网络首发时间: 2016-11-30 15:01
稀有金属 2018,42(03),252-258 DOI:10.13373/j.cnki.cjrm.xy16100019
石墨烯含量对铝基复合材料微观组织和力学性能的影响
李炯利 王旭东 武岳 曹振 郭建强 张海平
北京航空材料研究院北京市先进铝合金材料及应用工程技术研究中心
摘 要:
通过机械混合、低温球磨结合热挤压工艺制备了石墨烯增强铝基复合材料。通过透射电子显微镜 (TEM) 、能谱分析 (EDS) 和室温拉伸力学性能测试等手段, 对石墨烯纳米片添加量对铝基复合材料微观组织和力学性能的影响进行了研究。研究结果表明, 当石墨烯添加量为0.5% (质量分数) , 石墨烯基体沿着纳米晶铝的晶界均匀分布, 石墨烯/铝界面结合良好。当石墨烯含量大于1.0%时, 石墨烯在铝基体中分散性变差, 容易团聚形成夹杂, 使得石墨烯/铝界面结合变差。铝基复合材料的强度随着石墨烯添加量的增大先升高后降低。当石墨烯添加量为1.0%时, 复合材料的强度达到最大值 (抗拉248 MPa) , 与未添加石墨烯的纯铝相比, 抗拉强度提高了68.7%。石墨烯增强铝基复合材料的塑性随着石墨烯添加量的增大, 先保持不变而后急剧下降。当石墨烯添加量为0.5%, 复合材料塑性与纯铝塑性相当。当石墨烯添加量为1.0%, 延伸率为8.3%, 此时材料的强韧性匹配度较好。
关键词:
石墨烯;铝基复合材料;低温球磨;微观组织;力学性能;
中图分类号: TB333
作者简介:李炯利 (1985-) , 男, 山西繁峙人, 博士, 高级工程师, 研究方向:高性能铝基复合材料及其应用研究;电话:010-62496344;E-mail:ljlhpu123@163.com;
收稿日期:2016-10-15
基金:国家自然科学基金项目 (51404421) 资助;
Microstructure and Mechanical Properties of Aluminum-Matrix Composite with Different Graphene Contents
Li Jiongli Wang Xudong Wu Yue Cao Zhen Guo Jianqiang Zhang Haiping
Beijing Engineering Research Center of Advanced Aluminum Alloys and Applications, Beijing Institute of Aeronautical Materials
Abstract:
The combination of mechanical mixing, cryomilling and hot extrusion was employed for the fabrication of aluminum-matrix composite reinforced with graphene. Microstructure and mechanical properties were characterized by transmission electron microscopy (TEM) , electron dispersive spectroscopy (EDS) and static tensile tests to investigate the influence of graphene content on the microstructure and mechanical properties of aluminum-matrix composite. The results demonstrated that, with an addition of 0. 5% (mass fraction) graphene, the homogeneous distribution of graphene in the Al matrix as well as the clean metallurgical interfaces between aluminum and graphene were obtained. With an addition of 1. 0% graphene, however, the extent of the agglomeration of graphene increased, which in turn weakened the Al/Gr interface. As the content of graphene increased, the strength increased and then decreased. By incorporating 1. 0% graphene into aluminum matrix, the tensile strength reached its maximum (248 MPa) , increased by68. 7% compared with pure aluminum without graphene. When graphene content was above 1. 0%, however, this strengthening effect sharply dropped due to the clustering of graphene nanoflakes. The ductility maintained and then decreased with the content of graphene increasing. With 0. 5% graphene, both the elongation and area contraction of the composite did not decrease in comparison to pure aluminum. With the content of graphene reaching 1. 0%, the composite with a good combination of ductility (8. 3% tensile elongation) and strength (248 MPa) was successfully synthesized. Finally, some suggestions and the prospect on the aluminum-matrix composite reinforced with graphene were put forward.
Keyword:
graphene; aluminum-matrix composite; cryomilling; microstructure; mechanical properties;
Received: 2016-10-15
石墨烯是一种由碳原子构成的二维纳米材料, 呈单层片状结构 (厚度仅为几个纳米) 。由于其独特的二维蜂窝晶体结构和极高的键强度, 石墨烯是目前已知的世界上比强度最高、最坚硬的纳米材料 (断裂强度达130 GPa) [1], 甚至可以看作是二维的钻石。石墨烯也是迄今为止在实验室发现的比表面积最大 (2630 m2·g-1[2]) 、最薄 (厚度<5nm[3]) 的纳米材料。此外, 石墨烯特有的褶皱结构 (图1) , 使其在受力过程中存在一个褶皱舒展再断裂的过程, 因此石墨烯还具有良好的塑性和韧性[4]。得益于石墨烯的上述特性, 石墨烯在陶瓷材料[5,6]和高分子材料[7]中的添加被证明是一种提高材料强度同时保持材料塑性的有效手段, 但是, 石墨烯在金属铝及铝合金中的添加能否同样起到增强增韧的效果, 国内外学者也进行了尝试性的研究。
铝合金由于比强度高、成形性好和耐腐蚀性佳等优点, 在航空航天等领域获得了广泛应用[8]。近年来, 随着超声速飞行器使用要求和服役条件的不断提高, 航空航天领域对铝合金的性能提出了更高的要求[9]。然而, 通过传统的强化手段很难使铝合金的强度获得突破性的提高。利用石墨烯的高强度和良好的塑韧性优势, 并将其与传统铝合金复合, 能否使铝合金的性能进一步提升, 国内外学者也进行了相应的尝试。
石墨烯纳米片和铝合金粉体 (雾化) 在形貌、尺寸和密度等方面都存在着很大的差异 (表1) , 导致二者在材料复合时的相容性很差, 非金属的石墨烯和金属的铝在传统制备及成形工艺下也很难形成良好的界面结合。而对于金属基复合材料来说, 增强相在金属基体中的分布是否均匀、增强相是否发生团聚、界面结合是否紧密, 直接决定着复合材料性能的优劣。良好的界面结合可以使载荷在材料内部实现有效传递, 从而提高强度和韧性[10]。因此, 石墨烯在铝基体中的均匀分散如何实现, 以及石墨烯/铝的高质量界面结合如何获得, 是制备石墨烯增强铝基复合材料需要突破的关键技术。目前铝基复合材料的制备方法主要是熔融铸造法和粉末冶金法。采用传统熔融铸造法, 由于二者密度差异大, 石墨烯很难在铝液内部均匀分散, 此外, 二者在材料制备过程中还有可能发生高温界面反应, 生成Al4C3脆性相, 恶化材料性能。采用粉末冶金法, 则可使石墨烯纳米片和铝合金粉末在室温 (或更低的温度) 下实现均匀混合, 然后通过后续的压力加工来制备石墨烯增强铝基复合块体材料, 最大限度地抑制了传统熔融铸造法带来的高温界面反应。因此, 国内外学者大多采用的粉末冶金法, 将石墨烯引入到铝基体中, 来制备石墨烯增强铝基复合材料。
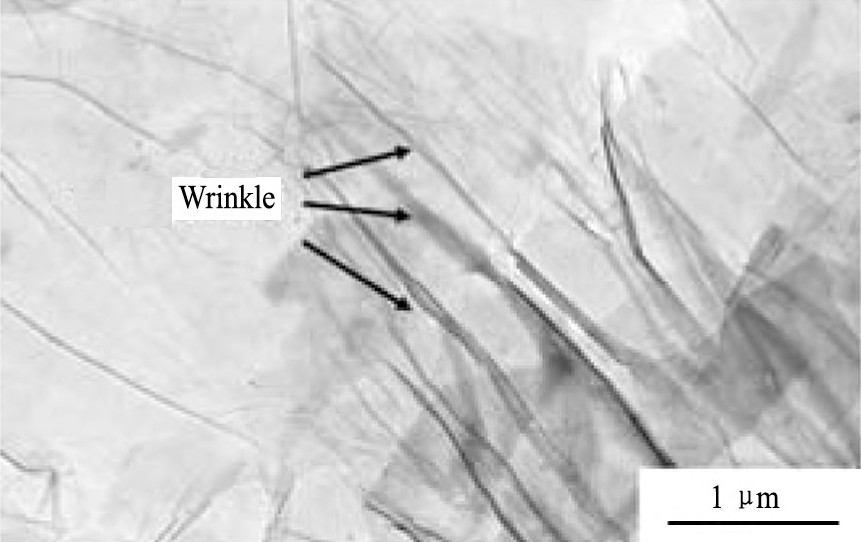
图1 石墨烯纳米片的透射电镜 (TEM) 照片Fig.1 TEM image of graphene nanoflakes
表1 石墨烯纳米片和铝合金粉体的差异Table 1 Difference between graphene nanoflakes and alu-minum powers 下载原图
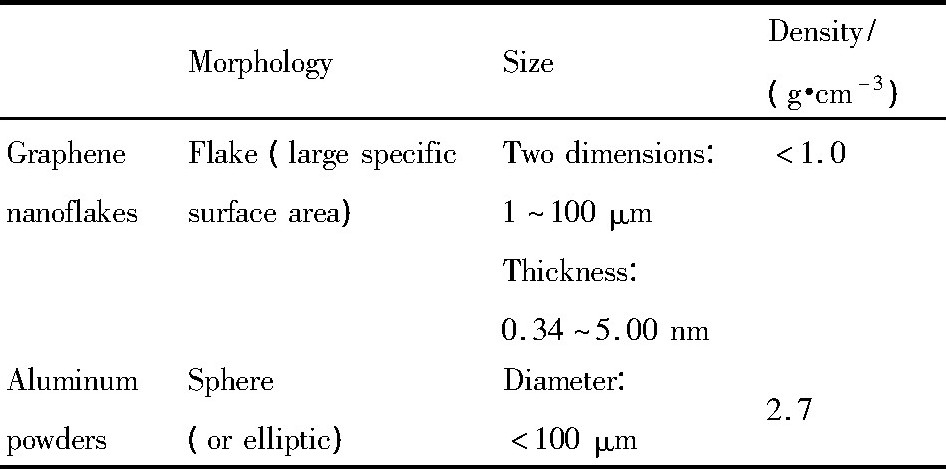
表1 石墨烯纳米片和铝合金粉体的差异Table 1 Difference between graphene nanoflakes and alu-minum powers
2011年Bartolucci等[11]通过机械球磨、热等静压和挤压的方法, 将质量分数为0.1%的石墨烯纳米片添加到了纯铝基体中, 制备成了石墨烯/铝复合材料。但是, 经测定, 材料的力学性能并没有得到提升。通过微观组织观察和XRD分析, 作者认为由于研究中采用的石墨烯 (氧化还原法制备) 存在着大量缺陷, 导致石墨烯和铝在材料制备过程中发生了界面反应, 生成Al4C3中间化合物 (有害相) , 进而降低了材料的强度和硬度[11]。因此, Bartolucci等的研究结果并不能反映石墨烯 (结构完整无缺陷) 增强铝基复合材料的本征性能。随后, 2014年Yan等[4]通过粉末冶金的方法, 将高品质且结构完整的石墨烯纳米片 (0.5%) 成功添加到铝合金 (Al-1.5Mg-3.9Cu) 中制备成石墨烯/铝复合材料, 与未添加石墨烯的铝合金相比, 材料的屈服强度提高50%, 塑性却未见明显降低。这一试验结果有力地证明了石墨烯不仅可以增强增韧陶瓷材料和高分子材料, 而且还是铝基复合材料的一种理想的增强相。
在以上两组石墨烯增强铝基复合材料的制备试验中, 石墨烯的添加量均小于0.5%。随着石墨烯含量的增大 (>0.5%) , 石墨烯在铝中的增强增韧效果是持续提升, 抑或是降低失效, 是一个值得探讨的问题。但是, 目前关于“铝基复合材料中石墨烯的极限添加量”的研究鲜有报道。为了计算铝基体中石墨烯的最适添加量, 基本假设如下: (1) 铝基体的晶粒都为等轴晶; (2) 石墨烯沿铝晶界均匀分布; (3) 每一个铝晶粒都被石墨烯均匀包裹。基于以上假设, 在石墨烯/铝复合材料中石墨烯的表面积等于铝晶粒的表面积, 可表达为式 (1)

式中, m为石墨烯/铝复合材料的质量;ω为复合材料中石墨烯的质量分数;ρ为铝 (或铝合金) 的密度;r为铝晶粒的半径;A为1 g单层石墨烯的面积, 取2630 m2[2];n为石墨烯的碳原子层数。由式 (1) 可得出, 石墨烯/铝复合材料中石墨烯层数、铝晶粒尺寸与石墨烯的极限添加量的关系, 见表2。
由表2数据可知, 当石墨烯的层数为10[3], 铝晶粒细至直径为200 nm (纳米晶) 时, 石墨烯的极限添加量可达4%。由于石墨烯的比表面积较大, 传统粉末冶金法很难使如此高质量分数的石墨烯纳米片 (4%) 均匀地分散到晶粒达到纳米级别 (100~200 nm) 的铝基体中。针对这一技术难点, 采用一种新颖有效的制备工艺来实现石墨烯在纳米晶铝中的均匀分散以及石墨烯/铝的高质量界面结合, 就显得十分必要。近年来出现的低温球磨粉末冶金工艺[12]和传统的粉末冶金法相比, 在改善增强相的分散及界面结合方面有明显的优势。文献[12]表明, 纳米B4C陶瓷颗粒和纯铝粉末的混合粉体经过低温球磨, 不仅实现了纳米B4C颗粒在铝基体中的均匀分散, 还可将纳米B4C颗粒包覆在铝内部, 形成高质量的界面结合。石墨烯与纳米B4C颗粒都属于典型的纳米材料, 因此, 可以尝试通过低温球磨技术来实现石墨烯纳米片在铝中的均匀分布、获得高质量的石墨烯/铝界面。本研究拟借助低温球磨工艺, 将高质量分数的石墨烯引入到铝基体中, 并通过压力加工制备成石墨烯铝基复合材料, 从而探究不同石墨烯含量对铝基复合材料微观组织和力学性能的影响。
表2 石墨烯层数、铝晶粒尺寸与石墨烯极限添加量的关系Table 2 Relationship of graphene layers, aluminum grain size and addition of graphene 下载原图
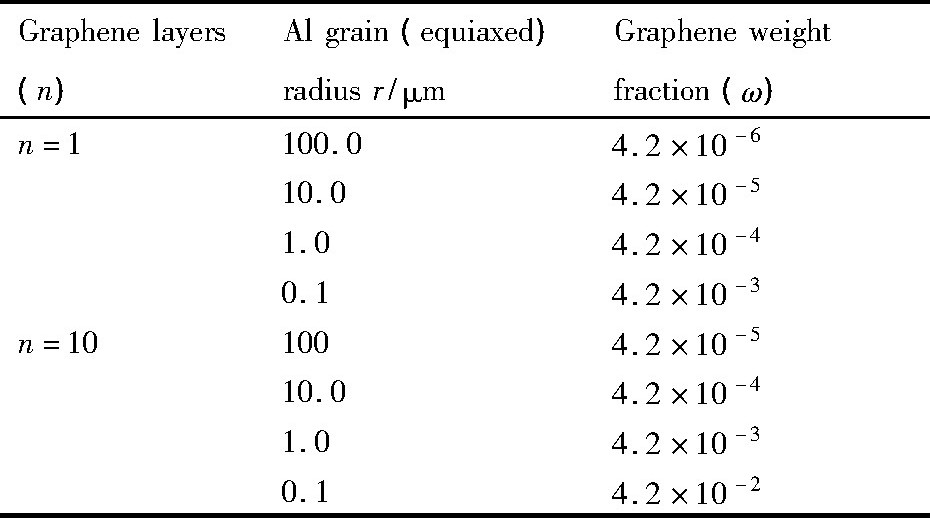
表2 石墨烯层数、铝晶粒尺寸与石墨烯极限添加量的关系Table 2 Relationship of graphene layers, aluminum grain size and addition of graphene
1实验
1.1材料
考虑到纯铝的包容性强, 在评价和分析材料的增强效果及增强机制时, 可以排除合金元素带来的干扰 (固溶强化、析出相强化等) 。因此, 在本研究中选取纯铝作为石墨烯增强铝基复合材料的基体材料。纯铝雾化粉体的平均粒度约为70μm, 基本化学成分及含量见表3。图2为纯铝雾化粉体的金相 (OM) 照片和扫描电镜 (SEM) 照片。由图2可知, 纯铝粉体的平均晶粒尺寸约为15~20μm (图2 (a) ) , 典型形貌较为规则, 大体呈近似球状 (图2 (b) ) 。
表3 纯铝雾化粉体的化学成分Table 3Chemical compositions of as-atomized aluminum powders (%, mass fraction) 下载原图

表3 纯铝雾化粉体的化学成分Table 3Chemical compositions of as-atomized aluminum powders (%, mass fraction)
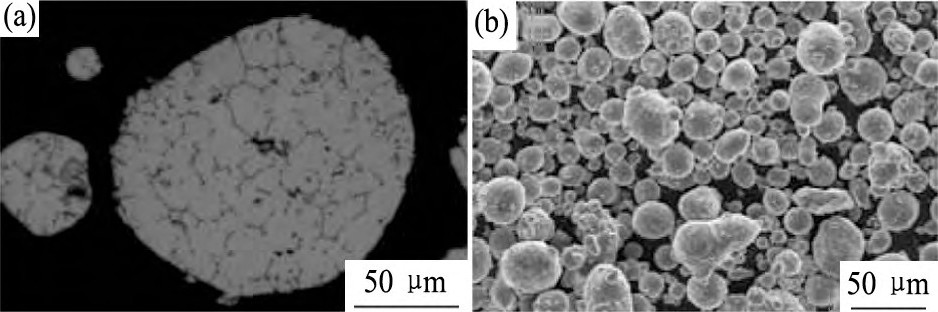
图2 纯铝雾化粉体的金相组织和颗粒形貌Fig.2 Microstructure and particle morphology of gas-atomized aluminum powder
(a) OM image; (b) SEM image
图3为石墨烯纳米片的SEM照片和透射电镜 (TEM) 照片。石墨烯纳米片具有较大的比表面积, 在二维方向和厚度方向上的尺寸相差较大, 如图3 (a) 所示。另外, 石墨烯纳米片还具有独特的褶皱结构, 如图3 (b) 所示。
1.2方法
首先将纯铝雾化粉体和石墨烯纳米片 (5组试验, 质量分数分别为0%, 0.5%, 1.0%, 1.5%, 2.0%) 在V型混粉机 (转速17 r·min-1) 中混合24 h, 得到石墨烯/铝混合粉体。然后将上述混合粉体、磨球和硬脂酸同时置于搅拌式球磨机中, 充入液氮, 待液氮浸没全部磨球时开始球磨, 搅拌轴转速为180r·min-1。磨球材质为轴承钢, 球料比为40∶1。有关低温球磨制备工艺的详细介绍见文献[13]。
低温球磨2 h后取出石墨烯/铝粉末, 并置于惰性气体保护箱中, 待其温度恢复至室温后装入铝合金包套内。将铝合金包套进行真空除气, 除气温度为300℃, 当真空度达到2.0×10-3Pa时开始计时, 保温2 h。除气结束后, 将包套焊合密封, 并在立式挤压机 (吨位250 t) 上进行热挤压 (温度300℃, 挤压比17.6∶1.0) , 制备成直径15 mm的石墨烯增强铝基复合材料杆材。
1.3表征手段
采用JEOL JEM-2100型透射电镜观察石墨烯增强铝基复合材料的微观组织, 在垂直于挤压方向取横向TEM试样, 加速电压为200 k V;通过JE-OL JEM-2100型透射电镜配备的INCA能谱仪 (EDS) 来定性评价石墨烯在铝基体中的均匀分布情况。拉伸试样沿挤压方向截取, 加工成标距区直径为d 5 mm的拉伸试棒, 拉伸试验在Instron 5887万能材料试验机上进行, 固定位移速率为1mm·min-1, 拉伸性能取3次试验的平均值。
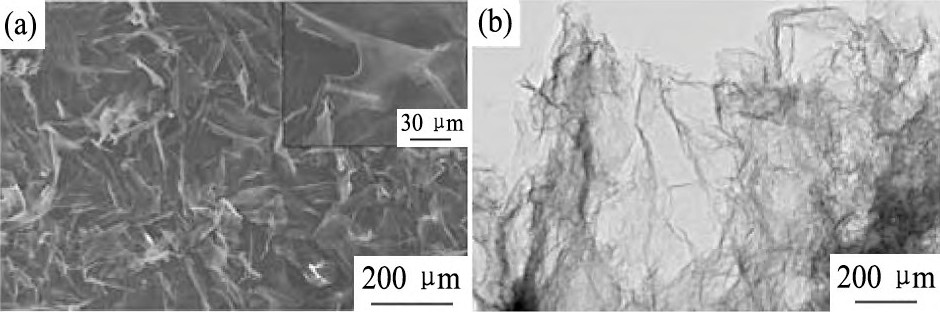
图3 石墨烯纳米片的典型形貌及微观组织Fig.3 Morphology and microstructure of graphene
(a) SEM image; (c) TEM image
2结果与讨论
2.1石墨烯含量对铝基复合材料微观组织的影响
图4为所制备的石墨烯铝基复合材料 (0.5%Gr) 微观组织的TEM照片。基体铝的平均晶粒尺寸达到纳米级别 (~200 nm) , 且石墨烯沿着纳米晶铝的晶界均匀弥散分布, 未发现明显石墨烯团聚现象, 如图4 (a) 所示。通过高分辨透射电镜照片 (图4 (b) ) 还可观察到, 石墨烯/铝之间界面纯净, 无杂质、孔隙等缺陷, 且未在界面处发现Al4C3中间化合物等有害相, 说明增强相石墨烯和基体铝间基本达到了原子尺度的冶金结合。值得注意的是, 均匀分布在铝基体中的石墨烯厚度为3~4nm, 约为10个碳原子层的厚度 (单层碳原子的厚度为0.335 nm[3]) , 仍属于石墨烯范畴[14]。
图5为石墨烯含量为1.0%的铝基复合材料微观组织的透射电镜照片和能谱图。在石墨烯铝基复合材料的微观组织中发现有带宽约为50 nm的亮灰色条带状组织沿基体铝晶界呈连续或半连续分布, 如图5 (a) 所示。通过透射电镜自带的能谱仪对上述带状组织附近区域的Al元素和C元素的分布进行了面扫描 (图5 (b) 和 (c) ) , 结果证明图5 (a) 中存在的条带状组织是由于石墨烯的团聚造成的。说明当石墨烯含量为1.0%时, 高质量分数的石墨烯在铝基体中分散性变差, 容易团聚形成大尺寸夹杂, 使得石墨烯/铝界面结合变差。基于以上实验结果, 可以推断当石墨烯含量超过1.0%时, 石墨烯在铝基体中的分散将会变得越来越困难, 石墨烯的团聚将越来越严重, 石墨烯和铝间的界面结合强度也会越来越弱。
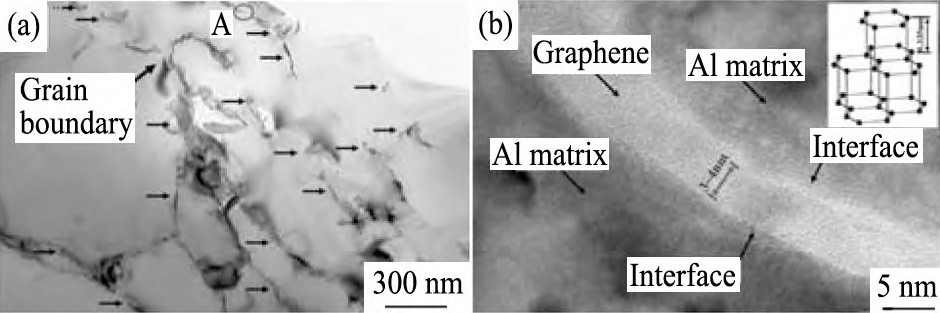
图4 石墨烯铝基复合材料 (0.5%Gr) 的微观组织Fig.4 TEM images of Al/Gr composite reinforced with 0.5%graphene
(a) Bright-field TEM image (transverse) ; (b) HRTEM image of area“A”shown in (a)
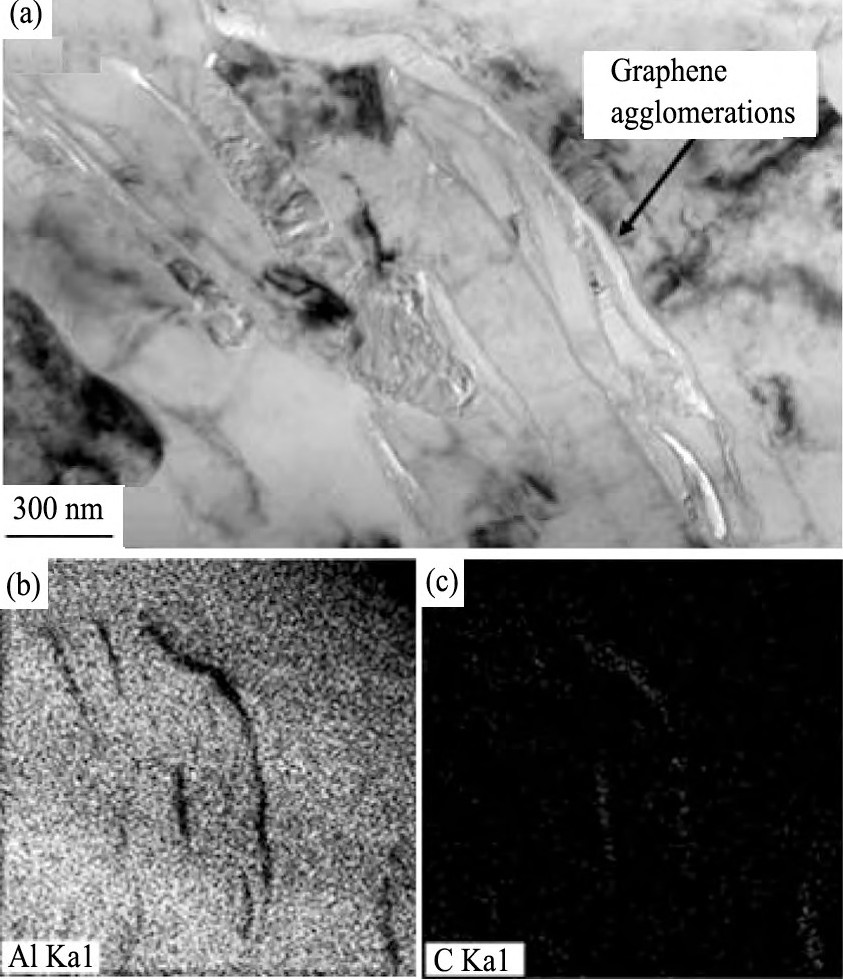
图5 石墨烯铝基复合材料 (1.0%Gr) 的微观组织Fig.5TEM and EDS images of Al/Gr composite reinforced with 1.0%graphene
(a) Bright-field TEM image showing graphene agglomerations (transverse) ; (b) Corresponding EDS mapping for Al element; (c) Corresponding EDS mapping for C element
2.2石墨烯含量对铝基复合材料力学性能的影响
图6为石墨烯铝基复合材料 (石墨烯质量分数分别为0%, 0.5%, 1.0%) 的应力-应变曲线。由图6可知, 石墨烯的添加带来材料强度的显著提升。例如, 当石墨烯添加量为0.5%时, 铝基复合材料与纯铝相比, 屈服强度和抗拉强度分别提高了8.8%和17.7%。这种增强效果归因于以下几个因素。首先, 超高强度 (130 GPa) 和纳米尺度 (3~4nm) 的石墨烯在基体铝晶界上均匀弥散分布 (图4 (a) ) , 作为一种有效的增强相, 对铝基复合材料带来显著的强化效果。同时, 石墨烯纳米片以及其他纳米弥散相 (如Al N[15]和Al2O3[16]) , 通过钉扎晶界, 起到抑制晶粒长大和稳定晶粒尺寸的作用, 在一定程度上维持了纳米晶铝基体带来的细晶强化效果。此外, 石墨烯与铝基体间高质量的界面结合 (图4 (b) ) , 使得载荷可从铝基体有效地传递到高强度的石墨烯 (130 GPa) [1], 从而进一步提升复合材料的强度。
由图6可知, 石墨烯铝基复合材料的塑性随着石墨烯含量的增加先维持不变, 而后降低。当石墨烯添加量为0.5%时, 铝基复合材料的断后伸长率和断面收缩率与未添加石墨烯的纯铝相比, 未见降低。分析认为, 石墨烯特有的二维蜂窝和褶皱结构 (图3 (b) ) , 使其在受力过程中存在一个褶皱舒展平铺的过程, 对铝基复合材料的塑性和韧性的保持有一定的贡献[4], 因此铝基体中适量 (≤0.5%) 石墨烯的添加不会带来由于增强相的引入而导致塑性降低的现象, 而这一现象在传统金属基复合材料中是普遍存在的。当石墨烯添加量从0.5%增加到1.0%时, 铝基复合材料的塑性大幅下降, 断后伸长率从19.9降至8.3%。分析认为, 随着石墨烯添加量的增加, 石墨烯在铝基体中分散变得越来越困难。当石墨烯的含量增加至1.0%时, 微观组织中出现了石墨烯的团聚 (图5) , 形成大尺寸的夹杂缺陷, 使得石墨烯/铝界面结合变差, 从而导致材料的塑性韧性降低。值得注意的是, 当石墨烯添加量从0.5%增加到1.0%时, 石墨烯铝基复合材料的强度未见降低, 这与材料塑性的变化规律正好相反。这一发现与文献[17]报道的结果一致。有限的增强相团聚在一定程度上对金属基复合材料的强度有一定贡献[17]。
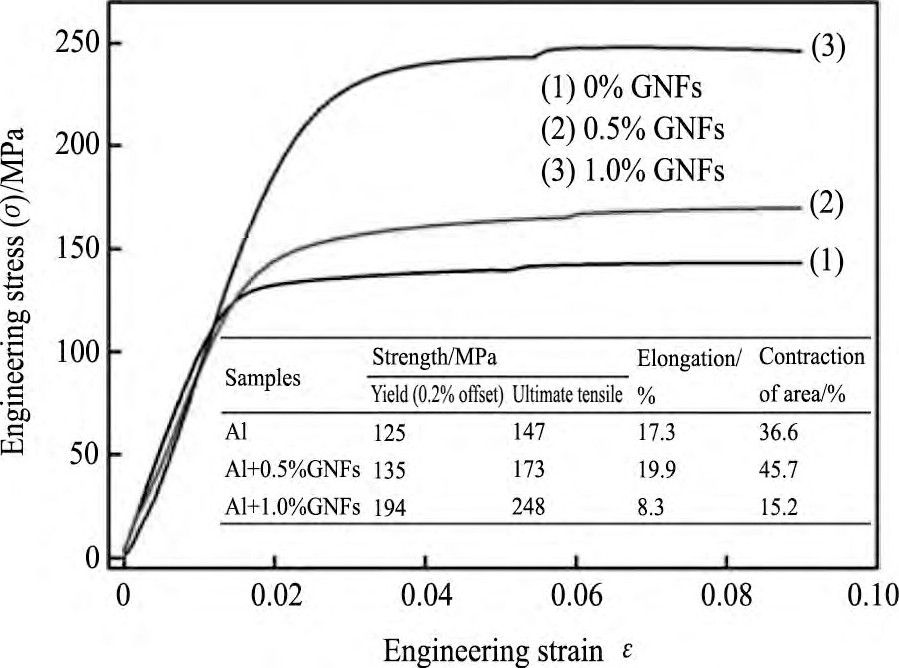
图6 石墨烯铝基复合材料的应力应变曲线Fig.6Engineering stress-strain curves and tensile properties of composite samples reinforced with 0%, 0.5%, 1.0%graphene at room temperature
图7为石墨烯铝基复合材料室温拉伸力学性能随石墨烯添加量的变化曲线。随着石墨烯添加量的增大, 铝基复合材料的强度先升高后降低。当石墨烯添加量为1.0% (质量分数) 时, 复合材料的强度 (抗拉248 MPa) 达到最大值, 与未添加石墨烯的纯铝相比, 抗拉强度提高了68.7%;与传统变形纯铝 (1050) 相比, 抗拉强度提高至300%。石墨烯铝基复合材料的塑性随着石墨烯添加量的增大, 先保持不变而后急剧下降。当石墨烯添加量为0.5%时, 复合材料塑性与纯铝塑性相当。随着石墨烯含量的增大, 石墨烯在铝中的分散变得越来越困难。当石墨烯添加量为1.0%, 延伸率降至8.3%, 但仍在可接受范围之内 (通常情况下, 满足工程应用需求的金属结构材料的断后伸长率要求至少为7%~8%) [18], 材料的强韧性匹配度较好。当石墨烯含量大于1.0%时, 石墨烯在铝基体中分散性变差, 容易团聚形成夹杂, 使得石墨烯/铝界面结合变差, 材料的强度和塑性都同时降低。
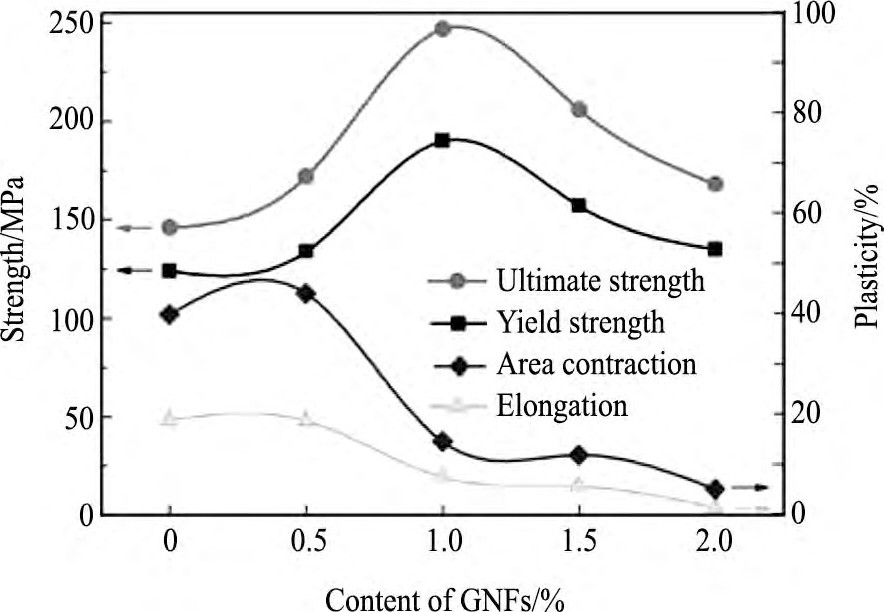
图7 石墨烯添加量对铝基复合材料力学性能的影响Fig.7Tensile properties of bulk nanostructured Al/Gr com-posite verse weight fraction (0%~2.0%) of graphene at room temperature
上述实验结果表明, 石墨烯的最适添加量为1% (此时材料的强韧性匹配度较好) , 远小于理论值4% (见式 (1) , 石墨烯的层数为10, 铝晶粒直径200 nm) 。分析认为, 理论计算和实验结果的差异主要由以下几方面造成: (1) 石墨烯的层数不可能全部为10层; (2) 石墨烯不可能非常完美地沿着基体铝晶界均匀分布, 将每一个铝晶粒均匀包覆; (3) 铝晶粒的形貌不可能全部为等轴球状, 晶粒尺寸也不可能全部达到纳米级别。以上理论计算和实验结果在一定程度上对石墨烯增强铝基复合材料研制过程中石墨烯含量的选择, 有一定指导和借鉴意义。
纳米材料因其独特的结构和优异的性能, 正在越来越多地吸引着研究人员的目光。石墨烯独特的二维纳米特性改变了传统的零维 (如陶瓷颗粒) 和一维 (如碳纤维) 的增强理论, 为材料设计增加了新的研究思路。石墨烯在铝中的添加及其带来的强韧化效果, 为铝合金/铝基复合材料 (尤其是纳米晶铝) 的增强增韧提供了新的工艺手段。可以预见, 石墨烯增强铝基复合材料是未来高性能铝/铝基复合材料的发展趋势之一。但是采用粉末冶金法制备石墨烯增强铝基复合材料的工艺复杂, 成本较高, 工程化难度较大, 不适合大规模的工业生产;采用熔融铸造法虽然可以实现石墨烯增强铝基复合材料的大规模工业化生产, 但是如果将石墨烯不做任何处理直接加入到铝液中, 则会在最终得到的铸锭中观察到严重的缺陷 (气孔、石墨烯团聚等) , 恶化材料性能。未来可通过先进的低温球磨技术结合热挤压技术制备出石墨烯在铝基体中均匀分布且界面结合良好的“石墨烯/铝”复合材料挤压丝材, 将其作为“石墨烯/铝”的中间合金, 最终将石墨烯以“石墨烯/铝”中间合金的形式添加到熔融的铝液中, 最大程度地改善石墨烯在铝液中的分散均匀性, 从而使得采用熔融铸造法来实现石墨烯增强铝基复合材料的工业化生产成为可能。
3结论
1.通过机械混合、低温球磨结合热挤压工艺制备了石墨烯增强铝基复合材料。当石墨烯添加量为0.5%, 石墨烯沿着基体铝的晶界均匀弥散分布, 且石墨烯/铝界面纯净, 无杂质、孔隙等缺陷, 基本达到了原子尺度的冶金结合。当石墨烯含量大于1.0%时, 石墨烯在铝基体中分散性变差, 易团聚形成夹杂, 使得石墨烯/铝界面结合变差。
2.随着石墨烯添加量的增大, 石墨烯铝基复合材料的强度先升高后降低。当石墨烯添加量为1.0%时, 复合材料的强度 (抗拉248 MPa) 达到最大值, 与未添加石墨烯的纯铝相比, 抗拉强度提高了68.7%。
3.石墨烯铝基复合材料的塑性随着石墨烯添加量的增大, 先保持不变而后急剧下降。当石墨烯添加量为0.5%, 复合材料塑性与纯铝塑性相当。随着石墨烯含量的增大, 石墨烯在铝中的分散变得越来越困难。
4.当石墨烯添加量为1.0%, 抗拉强度达248MPa, 延伸率为8.3%, 石墨烯铝基复合材料的强韧性匹配度较好。
参考文献
[1] Lee C G, Wei X D, Kysar J W, Hone J.Measurement of the elastic properties and intrinsic strength on monolayer graphene[J].Science, 2008, 321 (18) :385.
[2] Ruoff R S.Preparation and characterization of graphene oxide paper[J].Nature, 2007, 448:457.
[3] Novoselov K S, Geim A K, Morozov S V.Electric field effect in atomically thin carbon films[J].Science, 2004, 306:666.
[4] Yan S J, Dai S L, Zhang X Y.Investigating aluminum alloy reinforced by graphene nanoflakes[J].Material Science and Engineering A, 2014, 612:440.
[5] Liu J, Yan H X, Jiang K.Mechanical properties of graphene platelet-reinforced alumina ceramic composites[J].Cerm.Int., 2013, 39 (6) :6215.
[6] Liu J, Yan H X, Reece M J.Toughening of zirconia/alumina composites by the addition of graphene platelets[J].Journal of the European Ceramic Society, 2012, 32:4185.
[7] Liang J J, Huang Y, Zhang L.Molecular-level dispersion of graphene into poly (vinyl alcohol) and effective reinforcement of their nanocomposites[J].Advanced Functional Materials, 2009, 19 (14) :2297.
[8] Williams J C, Starke E A.Progress in structural materials for aerospace systems[J].Acta Mater., 2003, 51:5775.
[9] Li J L, Zhang K, Xiong Y C.Advanced in research on nanocrystalline Al-Mg alloys with high performance[J].Journal of Materials Engineering, 2013, 11:75. (李炯利, 张坤, 熊艳才.高性能纳米晶Al-Mg合金的研究进展[J].材料工程, 2013, 11:75.)
[10] Ye J C, He J H, Schoenung J M.Cryomilling for the fabrication of a particulate B4C reinforced Al nanocomposite:partⅠ.Effects of process conditions on structure[J].Metall.Mater.Trans.A, 2006, 37:3099.
[11] Bartolucci S F, Paras J, Rafiee M A.Graphene-aluminum nanocomposites[J].Material Science and Engineering A, 2011, 528:7933.
[12] Li J L, Wang X D, Wang S H, Zhang X F, Wang S Q, Xiong Y C.Morphology and microstructure of nanocrystalline aluminum-based composite powder reinforced with nanometric B4C particles[J].Chinese Journal of Rare Metals, 2016, 40 (6) :521. (李炯利, 王旭东, 王少华, 张显峰, 王胜强, 熊艳才.纳米B4C颗粒增强纳米晶铝基复合材料的粉体形貌及微观组织[J].稀有金属, 2016, 40 (6) :521.)
[13] Li J L, Li S S, Fan Z Z, Li W, Xiong Y C.A super high strength bulk nanocrystalline Al prepared via cryomilling[J].The Chinese Journal of Nonferrous Metals, 2013, 23 (5) :1182. (李炯利, 厉沙沙, 樊振中, 李伟, 熊艳才.低温球磨制备超高强度块体纳米晶纯铝[J].中国有色金属学报, 2013, 23 (5) :1182.)
[14] Geim A K, Novoselov K S.The rise of graphene[J].Nature Materials, 2007, 6:183.
[15] Li Y, Liu W, Ortalan V, Li W F, Zhang Z, Vogt R, Browning N D, Lavernia E J, Schoenung J M.HRTEM and EELS study of aluminum nitride in nanostructured Al 5083/B4C processed via cryomilling[J].Acta Mater., 2010, 58:1732.
[16] Han B Q, Lee Z, Nutt S R, Lavernia E J, Mohamed F A.Mechanical properties of an ultrafine-grained Al-7.5 pct Mg alloy[J].Metall.Mater.Trans.A, 2003, 34:603.
[17] Kang Y C, Chan S L.Tensile properties of nanometric Al2O3particulate-reinforced aluminum matrix composites[J].Materials Chemistry and Physics, 2004, 85:438.
[18] Han B Q, Lee Z, Witkin D, Nutt S, Lavernia E J.Deformation behavior of bimodal nanostructured 5083 Al alloys[J].Metall.Mater.Trans.A, 2005, 36:957.