
Recovery of valuable metals from anode material of hydrogen-nickel battery
WU Fang(吴 芳), XU Sheng-ming(徐盛明), LI Lin-yan(李林艳),
CHEN Song-zhe(陈崧哲), XU Gang(徐 刚), XU Jing-ming(徐景明)
Institute of Nuclear and New Energy Technology, Tsinghua University, Beijing 100084, China
Received 8 May 2006; accepted 11 November 2008
Abstract: Simultaneous recovery of rare earth, nickel and cobalt resources from the anode material of hydrogen-nickel battery was performed through a hydrometallurgical process. Most of rare earth elements are separated from nickel and cobalt in the form of sulfates when the anode material is firstly leached with sulfuric acid. Then, the precipitated rare earth sulfates are dissolved with sodium hydroxide to form rare earth hydroxides. The rare earth element, zinc and manganese ions in the lixivium are also separated from nickel and cobalt by using PC-88A extractant system, and the organic phase loaded rare earth is stripped with hydrochloric acid. By neutralizing the stripping solution with rare earth hydroxide, the rare earth chloride is obtained. Under the suitable leaching conditions of sulfuric acid 3 mol/L, leaching time 4 h and temperature 95 ℃, 94.5% of rare earth in the anode material is transformed into the sulfate precipitates, and the leaching ratios of nickel and cobalt can approach 99.5%. When the pH value of the extractive system is controlled in the range of 3.0-3.5, the rare earth elements in the lixivium can be extracted completely into the organic phase, and the stripping recovery of the rare earth can reach 98% in the extraction stage. The total recoveries of rare earth, nickel and cobalt are 98.9%, 98.4% and 98.5%, respectively.
Key words: solid waste materials; hydrogen-nickel battery; recovery; rare earth
1 Introduction
With the escalating of competitive capability for secondary batteries in the international market, China has become the base of processing and exporting batteries. In 2003, the battery output is nearly half that of the whole world, in which the hydrogen-nickel batteries reach up to 0.56 billion[1]. The output of hydrogen-nickel batteries is steadily rising due to their low cost, quick charging capability, long cycling life, no memory effect, less pollution, wide temperature range, good security, etc. It is estimated that the hydrogen-nickel batteries will occupy 29% of the international battery market till 2010 [2]. The hydrogen-nickel battery contains 30% Ni, 4% Co and about 10% rare earth elements. It is investigated that one hydrogen-nickel battery weighs about 25 g. Thus, there exists 7 500 t of nickel, 1 000 t of cobalt, and 2 500 t of rare earth elements in one billion tonnes of disabled hydrogen-nickel batteries. According to the average price of London Metal Exchange(LME) Market, the value is about 1.5 billion RMB. Meanwhile, the spent secondary batteries are forbidden to be abandoned randomly. Therefore, the recovery of the miniature secondary batteries, such as the hydrogen-nickel battery, has received much attention[3-4].
Since the hydrogen-nickel battery was commercialized in 1993, the recovery and utilization of the valuable metals in the spent hydrogen-nickel battery have been studied. ZHANG et al[5-6] had succeeded in recovering the mixed rare earth elements, cobalt and nickel, by a solvent extraction with 25% D2EHPA in kerosene, followed by selective precipitation with oxalic acid. TZANETAKIS and SCOTT[2,7] used D2EHPA to extract and separate the rare earth elements after leaching by hydrochloric acid; WANG et al[8] regenerated the hydrogen-storage alloy of the hydrogen-nickel battery, of which the electrochemical capability could be renewed. TENORIO and ESPINOSA[9] used ore-dressing method to recover the nickel-based alloy from the hydrogen- nickel battery. The major processes for the recovery of rare earth from the leaching solution, however, include solvent extraction at a low pH value[5-6], and precipitation of rare earth sulfate mixed salt[10-11]. In this work, the leaching processes of the three kinds of anode are compared. At the same time, a novel flow for the recovery of rare earth is proposed to investigate the influences of various factors on the recovery and separation of rare earth in the process of leaching and extraction, in which the lixivium concentration is settled at 100 g/L in order to meet the needs of industrialization.
2 Experimental
2.1 Starting materials
The anode scraps of hydrogen-nickel battery were provided by a battery company, and its composition is displayed in Table 1. From Table 1, it can be seen that three kinds of anodes contain similar mixed rare earth materials[10].
Table 1 Composition of spent anode material (mass fraction, %)

2.2 Experimental procedure
2.2.1 Acid-leaching
Because the hydrogen-nickel battery contains a great deal of nickel and cobalt with high value, the recovery of nickel and cobalt must be considered in the process of rare earth recovering. Previous researches on the recovery of the anode material of hydrogen-nickel battery have established the recovering flow for the spent anode material of hydrogen-nickel battery, in which sulfuric acid was used as leaching agent. In this work, sulfuric acid was also chosen as the leaching agent. Because the solubility of rare earth sulfate is low, high concentration of sulfuric acid can lead to the precipitation of rare earth sulfates. High solid-to-liquid ratio was adopted in the design of the recovery flow [6,11] to control the concentration of rare earth in the range of 2.5-3.5 g/L. The rare earth was recovered in subsequent extraction procedure. The concentration of nickel in the solution was too low to recover. Other researchers[10] used sodium sulfate to deposit the rare earth. As a result, the separation of rare earth and nickel, cobalt was realized in the leaching stage. In order to deposit rare earth completely, the dosage of sodium sulfate was three times of the theoretical value. In this case, a great deal of sodium ion entered nickel sulfate solution. It was shown that the Na+ concentration would exceed 20 g/L when the Ni2+ concentration reached 100 g/L.
Na+ is difficult to be removed in the subsequent purification of nickel sulfate[12]. In this study, we made use of the low solubility of rare earth sulfate to separate most rare earth elements (from nickel and cobalt). Small part of rare earth entering into the solution was separated and recovered in the subsequent extraction. The lixivium and filter residue were separated after leaching. The filter residue was mainly composed of the sulphate precipitation and a little amount of organic adhesive. It was transformed to rare earth hydroxide after alkalization, and then was neutralized by hydrochloric acid to form rare earth chloride which was concentrated to produce rare earth chloride crystals.
2.2.2 Solvent extraction
PC-88A is an excellent extractant for rare earth whose organic phase is composed of 20% PC-88A+80% kerosene. The solvent extraction was carried out in mixer-settler, in which the capacity of mixing chamber and 30-stage clarifying chamber are 200 L and 600 L, respectively, and the mixing speed is 80 r/min. The model of the mixer-settler is shown in Fig.1.

Fig.1 Model of mixer-settler: (1)-(4) Nickel making soap; (5)-(12) Extraction; (13)-(16) Washing; (17)-(22) Counter-extraction of Zn and Mn; (23)-(28) Counter-extraction of rare earth; (29)-(30) Pure water washing of organic phase; (1) Organic phase, 20% PC-88A+80% kerosene, and saponification ratio of sodium hydroxide, 70%; (2) Nickel sulfate solution, 50 g/L, pH=6; (3) Lixivium; (4) Washing solution, 0.1 mol/L H2SO4; (5) Back-extractant for Zn2+, Mn2+, 2 mol/L HCl; (6) Back-extractant for rare earth element, 4 mol/L HCl; (7) Washing solution for organic phase, pure water; (8) Export of regenerated organic phase; (9) Export of washing water for organic phase; (10) Export of rare earth counter-extract; (11) Export of back-extractant for impurity of Zn2+ and Mn2+; (12) Export of raffinate of nickel sulfate NiSO4 and cobalt sulfate CoSO4; (13) Export of nickel soap solution
2.2.3 Recovery of rare earth
The rare earth sulfate deposited in the leaching process was transformed into rare earth hydroxide after alkalization. High concentrated HCl remaining in the back-extract could neutralize rare earth hydroxide to form rare earth chloride. The reaction is
RE2(SO4)3+NaOH=RE(OH)3+Na2SO4 (1)
RE(OH)3+HCl=RECl3+H2O (2)
The rare earth chloride was concentrated and crystallized to form crystalline rare earth chloride, and the flow chart of rare earth recovering is shown in Fig.2.
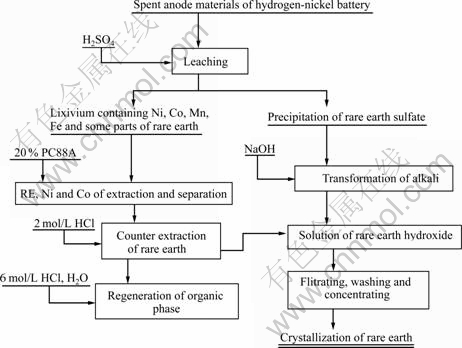
Fig.2 Flowchart of rare earth recovering
2.3 Analysis
The analysis of total amount of rare earth, lanthanum and other rear earth elements was performed according to GB/T14635.1—93, XB/T606.4—95 and GB/T12690—90, respectively[13]. The macro-analysis of cobalt was carried out on a 722 spectrophotometer, and the analysis of trace cobalt and other metal-ion was carried on a NITACHI Z-8230 atomic absorption spectro-
meter. The element remaining in the organic phase after extraction was back-extracted by HCl and then was analyzed. pH values were measured with HM-30S pH meter.
3 Results and discussion
3.1 Leaching of spent anode materials of hydrogen- nickel battery
3.1.1 Mechanical separation of steel band
The foaming nickel exists in the form of metal state and it is recovered after leaching. Because the porous copper network does not dissolve in dilute sulfuric acid, the leached material can be separated easily from it, when the copper network anode is leached with sulfuric acid. In this study, wet rotary mill was used to mechanically separate alloy powder from the steel band base. The experimental results are displayed in Table 2.
Table 2 Separation effect of nickel plating steel band by using rotary mill

From Table 2, it can be seen that the recovery ratio of alloy powder can reach 99.5% through the mechanical separation of the steel band. The separated nickel plating steel band can be recovered in the production of stainless steel.
3.1.2 Influence of temperature on leaching
Experimental conditions are as follows: H2SO4 3 mol/L, leaching time 4 h and fixed solid-to-liquid ratio in which the completely leached nickel maintains about at 100 g/L. The influence of leaching temperature is displayed in Fig.3.
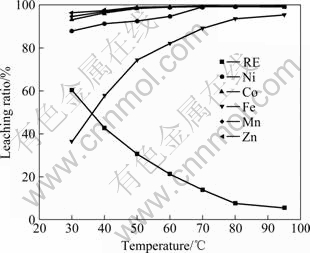
Fig.3 Leaching results at different temperature
From Fig.3, it can be seen that the leaching ratio of rare earth reduces with the rising of temperature due to the formation of rare earth sulphates, and the leaching ratios of Mn and Zn almost keep constant at different temperature. The leaching ratios of Ni, Co and Fe increase with the rising of temperature, and can approach 99.5% at 95 ℃. The composition of lixivium at the different temperatures is displayed in Table 3.
Table 3 Composition of lixivium at different temperatures
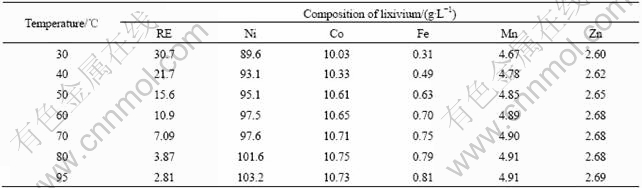
The rare earth elements in the spent anode material of hydrogen-nickel battery are mainly light rare earth, such as La, Ce, Pr and Nd, and the solubilities[14] of their sulfates reduce obviously with the rising of temperature, which are listed in Table 4.
Table 4 Solubility of rare earth sulfates
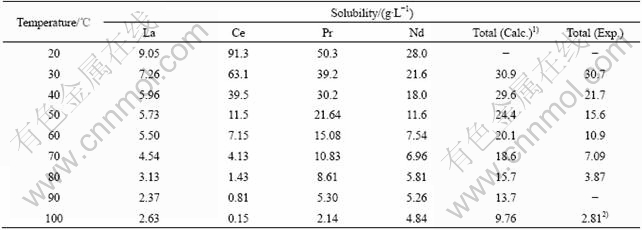
Note: 1) Assumed condition: rare earth in anode is leached fully, and when concentration of nickel in solution is 100 g/L, concentrations of leached rare earth elements are La 25.63 g/L, Ce 1.78 g/L, Pr 5.33 g/L, Nd 16.50 g/L, respectively; 2) Measured concentration at 95 ℃.
From Table 4, it can be seen that the solubility of rare earth in the actual lixivium is less than the calculated value. At high temperature, this difference becomes much obvious, which is mainly due to the large ion strength and common-ion effect originated from SO42-. Therefore, the leaching should be carried out at above 95 ℃. The extract was hot-filtered and the dreg was washed with hot water. Fe was removed from the lixivium to be less than 50 mg/L with the yellow natojarosite method before extraction. In this case, the recovery ratios of rare earth, nickel and cobalt are all higher than 99.5%.
3.2 Extraction
After filtration, nickel and cobalt together with
5.5% rare earth were recovered and separated by extraction. The impurities, such as Mn2+ and Zn2+ were separated in counter extraction. The nickel and cobalt sulfate solutions were purified while the rare earth was recovered, and CoSO4 and NiSO4 in the raffinate could be recovered by separating.
3.2.1 Nickel-saponification
Because the extraction by using PC-88A as extractant would produce H+, it is necessary that PC-88A is treated with NaOH to saponify PC-88A before extraction. Na-PC-88A would bring about additional Na+. So, nickel was used to saponify PC-88A. The reaction is
2NaX+NiSO4=NiX2+Na2SO4
(X=ROP(R)(O)O-, R=C4H9CH(C2H5)CH2) (3)
The nickel-saponification was carried out in 50 g/L NiSO4 solution at pH 6, and the saponification ratio is about 60%.
3.2.2 Extraction and separation for rare earth, nickel, and cobalt
The extracting pH1/2 values of PC-88A in sulfuric acid (pH1/2 is the pH value at which 50% metals are extracted) are[15] 1.0, 1.2, 2.5, 3.5, 4.2 and 5.6 for RE3+, Fe3+, Zn2+, Mn2+, Co2+ and Ni2+, respectively. Therefore, The separation of rare earth from other elements can be realized by controlling the equilibrium pH value. After eight-stage fractional extraction, the influence of pH value on the extraction ratio of all kinds of elements is displayed in Fig.4.
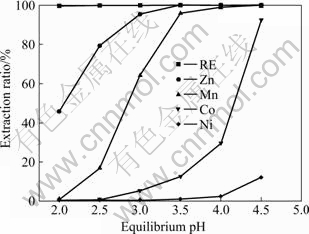
Fig.4 Influence of pH value on extraction ratio of all kinds of elements
From Fig.4, it can be seen that the extraction and separation of rare earth, cobalt and nickel only need less than four-stage extraction. But eight-stage extraction was used in order to separate Mn2+ from Co2+ effectively. When the equilibrium pH value is in the range of 3.0-3.5, all the rare earth elements enter into the organic phase along with Zn2+ and Mn2+ etc, at which the extraction ratios of Co2+ and Ni2+ are less than 13% and 1%, respectively.
3.2.3 Scrubbing of nickel and cobalt in organic phase
Little cobalt and nickel co-extracted into organic phase can be easily eluted with 0.2 mol/L H2SO4. Through four-stage washing, Ni2+ and Co2+ in organic phase are removed to below 0.05 g/L at the flowing ratio (organic phase to water phase) of 20?1.
3.2.4 Stripping of Zn2+ and Mn2+
Compared with the rare earth, the impurities, Zn and Mn are stripped easily. If there is six-stage stripping with 2 mol/L HCl, much rare earth will be stripped, in which the stripping solution does not circulate and the pH values of every stage in extraction tank are controlled by flowing ratio. The stripping extractant (2 mol/L HCl) of Zn2+ and Mn2+ in the 22nd stage enters into the exit of the raffinate of Zn2+ and Mn2+ in the 17th stage. The pH value is controlled to rise gradually to 2 in the 17th stage, at which the rare earth re-enters into the organic phase. At the exit of the 17th stage, the concentrations of Zn2+, Mn2+ and RE3+ in the stripping solution are 5.91, 10.82 and 0.01 g/L, respectively. The stripping ratios of Zn2+ and Mn2+ are 96.3% and 99.5%, respectively, and the recovery ratio of rare earth is 99.0%.
3.2.5 Stripping of rare earth
The rare earths were stripped through six stages with 4 mol/L HCl. The stripping solution was recycled to keep the acidity invariable to enrich the rare earth. And when the rare earth was enriched to 200-250 g/L, the stripping solution is refreshed. After rare earth enriching, the stripping solution contains RE3+ 250 g/L, Zn2+ 6.32 g/L, Mn2+ 1.96 g/L, Fe3+ 0.68 g/L, and the recovery ratio of rare earth is 99.5%.
3.2.6 Recovery of raffinate
The recovered substance in the five-stage settling tank is the intermixture of NiSO4 and CoSO4 with high quality, in which the Ni2+ and Co2+ contents are 98.04% and 10.20%, respectively, and the contents of Mn2+, Zn2+, Fe3+, RE3+ and Na+ are less than 0.05%, 0.001%, 0.001%, 0.001% and 1.35%, respectively. High-quality crystals of NiSO4 and CoSO4 are obtained after separation and enrichment due to the Na+-free flow. The recovery ratios of nickel and cobalt are more than 99.0%. If the Fe-removing is taken into account, the general recovery ratios of nickel and cobalt are 98.4% and 98.5%, respectively.
3.3 Recovery of rare earth
The precipitation of rare earth sulfate after leaching is transformed into rare earth hydroxide through alkalization. The solubilities of the rare earth hydroxide are very low, and they are 1.0×10-19, 1.5×10-20, 2.7× 10-20, 1.9×10-21 and 6.8×10-22 for La, Ce, Pr, Nd and Sm, respectively. The rare earth hydroxide can be precipitated completely by only 1.1 times the theoretical addition of NaOH. The precipitating recovery of rare earth in this stage is 94.5%, and 5.39% of the others can be recovered in the following extracting stages.
There is much HCl remaining in the batch-extracted solution of rare earth. A proper amount of HC1 is recruited to neutralize the rare earth hydroxide, resulting in the rare earth chloride with concentration in the range of 250-300 g/L. On account of the loss during filtration caused by the entrain mainly originated from the organic adhesive, the recovery of rare earth is 99.0%. Then, the rare earth chloride is heated and concentrated to 450-500 g/L, and crystallized by cooling, and 98.9% of rare earth in the form of chlorides can be recovered in the recycling of the anode materials of hydrogen-nickel battery.
4 Conclusions
1) The hydrometallurgical flow was designed to recover the rare earth, nickel and cobalt simultaneously from the anode material of hydrogen-nickel battery. The recovery procedure includes: the leaching of the anode with sulfuric acid; the separation of most rare earth from nickel and cobalt in the form of rare earth sulfates; the neutralization of rare earth sulphate; the separation of rare earth, Zn2+ and Mn2+ in the lixivium from nickel and cobalt by using PC-88A and kerosene as extractant; and the stripping of rare earth with HCl.
2) When recovering the anode material of hydrogen-nickel battery with nickel-plating steel band as carrier, the wet ball-milling method is used to separate the alloy powder and the steel band. And the foaming nickel and copper network anodes can be recovered directly.
3) In the recovery process of rare earth, the leaching solid-to-liquid ratio is controlled as the nickel concentration reaches about 100 g/L for the convenience of industry recovery. The detailed leaching condition is as follows: 3 mol/L H2SO4, 4 h leaching time and 95 ℃. Under such condition, 94.5% of rare earth elements are transformed into the rare earth sulfate precipitates, and the leaching ratios of Ni and Co can approach 99.5%. The organic phase in the extraction is the mixture of 20% PC-88A and kerosene saponified by nickel. If the pH value is controlled in the range of 3.0-3.5, the rare earth would enter into the organic phase completely. The recovery ratio of the rare earth is 98% in the extraction stage by using 4 mol/L HCl as stripping extractant.
4) The total recovery ratios of rare earth, nickel and cobalt are 98.9%, 98.4% and 98.5%, respectively.
References
[1] The special report of Chinese battery industry association [J]. Battery Industry, 2004, 9(2): 109-110. (in Chinese)
[2] TZANETAKIS N, SCOTT K. Recycling of nickel-metal hydride batteries: Dissolution and solvent extraction of metals [J]. Journal of Chemical Technology and Biotechnology, 2004, 79: 919-926.
[3] WU fang. The recovery of nickel and cobalt from the spent lithium-ion secondary batteries [J]. The Chinese Journal of Nonferrous Metals, 2004, 14(4): 697-701. (in Chinese)
[4] ZHU Jian-xin, YU Bo, NIE Yong-feng, LI Jin-hui. The review of regeneration technique in use of the spent cadmium-nickel batteries [J]. Battery Bimonthly, 2001, 31(5): 248-250. (in Chinese)
[5] ZHANG P W, YOKOYAMA T, ITABASHI O, WAKUI Y, SUZUKI T M, INOUE K. Hydrometallurgical process for recovery of metal values from spent nickel-metal hydride secondary batteries [J]. Hydrometallurgy, 1998, 50: 61-75.
[6] ZHANG P W, YOKOYAMA T, ITABASHI O, WAKUI Y, SUZUKI T M, INOUE K. Recovery of metal values form spent nickel-metal hydride rechargeable batteries [J]. Journal of Power Sources, 1999, 77: 116-122.
[7] TZANETAKIS N, SCOTT K. Recycling of nickel-metal hydride batteries: Electrochemical deposition of cobalt and nickel [J]. Journal of Chemical Technology and Biotechnology, 2004, 79: 927-934.
[8] WANG R, YAN J, ZHOU Z, GAO X P, SONG D Y, ZHOU Z X. Regeneration of hydrogen storage alloy in spent nickel–metal hydride batteries [J]. Journal of Alloys and Compounds, 2002, 336: 237-241.
[9] TENORIO J A S, ESPINOSA D C R. Recovery of Ni-based alloys from spent NiMH batteries [J]. Journal of Power Sources, 2002, 108: 70-73.
[10] XU Li-yang, CHEN Zhi-chuan. The technics studies of recovery of rare earth in the cathode plate of hydrogen-nickel battery [J]. The Chinese Journal of Rare Earths, 2003, 21(1): 66-70. (in Chinese)
[11] PIETRELLI L, BELLOMO B, FONTANA D, MONTEREALI M R. Rare earths recovery from NiMH spent batteries [J]. Hydrometallurgy, 2002, 66: 135-139.
[12] ZHANG Li-ming. The practice of improving the production quality of nickel sulfate [J]. Mining & Metallurgy of Nonferrous Metals, 1996(5): 38-40. (in Chinese)
[13] ZHU Yu-hua. ’95 complete compilation for rare earth standards [M]. Beijing: Metallurgical Industry Press, 1995. (in Chinese)
[14] XU Guang-qian. Rare earths [M]. 2nd ed. Beijing: Metallurgical Industry Press, 2002. (in Chinese)
[15] WANG Jia-ding, CHEN Jia-yong. The handbook of solvent extraction [M]. Beijing: Chemical Industry Press, 2001: 442-445. (in Chinese)
Foundation item: Projects(50674060, 50734005) supported by the National Natural Science Foundation of China; Projects(20051070103, 2008B030302014) supported by the Development of Science and Technology of Guangdong Province, China; Project(2008BAC46B03) supported by the National Key Technology R&D Program
Corresponding author: XU Sheng-ming; Tel: +86-10-62773585; Fax: +86-10-62771150; E-mail: smxu@tsinghua.edu.cn
DOI: 10.1016/S1003-6326(08)60297-6
(Edited by YANG Bing)