
Preparation of alumina-doped yttria-stabilized zirconia nanopowders by microwave-assisted peroxyl-complex coprecipitation
QI Liang(齐 亮), XU Ming-xia(徐明霞), TIAN Yu-ming(田玉明), ZHAO Jin-wei(赵今伟)
School of Materials Science and Engineering, Key Laboratory for Advanced Ceramics and Machining Technology of Ministry of Education, Tianjin University, Tianjin 300072, China
Received 10 April 2006; accepted 25 April 2006
Abstract: Alumina-doped yttria-stabilized zirconia (ADYSZ) nanopowders were prepared by microwave-assisted peroxyl-complex coprecipitation (MAPCC) using ZrOCl2·8H2O, Y2O3 and AlCl3·6H2O as starting materials, NH3·H2O as precipitant and H2O2 as complexant. The effects of adding H2O2 and microwave drying on the preparation and properties of ADYSZ were investigated. The precursors and nanopowders were studied by EDX, XRD, SEM and TEM techniques. The results show that the uniformity of component distribution within ADYSZ nanopowders is improved by adding appropriate dosage of H2O2. Complexing reaction between H2O2 and Zr4+ ion restrains the hydrolyzation and precipitation of Zr4+ ion. With the addition of H2O2, Al3+, Y3+ and Zr4+ ions can be precipitated synchronously in a relatively narrow range of pH value. H2O2 also improves the filterability of the wet precipitate. The highly hydrophilic precipitates can be quickly and effectively separated from aqueous solution. During microwave drying process, the moisture of wet precursors is selectively heated. Quick expansion of steam vapor within the wet colloidal particles causes the aggregations burst into numerous tiny lumps. Compared with oven drying, microwave drying can not only shorten drying time but also reduce aggregation intensity of the resultant ADYSZ nanopowders.
Key words: alumina-doping; yttria-stabilized zirconia; nanopowders; coprecipitation; hydrogen peroxide; microwave drying
1 Introduction
The widespread applications of various zirconia-based materials make zirconia a hotspot in materials science. In order to improve the physical and chemical properties of zirconia based-materials, many efforts including application of nano-scaled powders and adding different dopants to the matrix of zirconia-based materials have been made. Similarly, various approaches have been investigated to optimize the initial composition and synthesize monodisperse nanopowders with little aggregation.
Usually, substances like CaO[1], MgO[2], Y2O3[3] and CeO2[4] were chosen as additives and added to the matrix of zirconia-based compounds. In recent years, more and more scholars have begun to focus their interesting on the alumina-doped yttria-stabilized zirconia (ADYSZ) for the great advantages of accelerating sintering[5,6], enhancing fracture toughness[7] and retarding low temperature degradation[8] brought by the trace addition of Al2O3. However, in most of these studies, raw materials were either expensive commercial products or fabricated by ball-milling method, and the cost as well as the properties of this kind of raw material are not so ideal.
Various methods, including hydrolysis[9,10], sol-gel[11], precipitation[12] , hydrothermal method[13], have been applied to synthesize different kinds of ZrO2 nanopowders. Advantages and limitations of these methods were discussed in Ref.[14]. Among all kinds of methods, coprecipitation is the most common route to produce zirconia-based nanopowders. Compared with other synthesis methods, coprecipitation has many advantages such as simple requirement for synthesizing equipments, convenient manipulation. Nevertheless, the conventional coprecipitation method has the inherent disadvantage of inhomogeneity of resultant composition, especially when pH values of the precipitations of different initial ingredients are highly discrepant, efficiency is low in production and agglomeration is serious within resultant nanopowders. So, it is necessary to study an appropriate method to synthesize high performance zirconia-based nanopowders.
A novel modified coprecipitation method, called microwave-assisted peroxyl-complex coprecipitation (MAPCC), was put forward in this study. Effects of adding H2O2 and properties of alumina-doped yttria-stabilized zirconia (ADYSZ) nanopowders were investigated.
2 Experimental
The starting materials in the study were zirconium oxychloride octahydrate (ZrOCl2·8H2O, AR grade), yttrium oxide (Y2O3, AR grade) and aluminium chloride hexahydrate (AlCl3·6H2O, AR grade). Ammonia solution (NH3·H2O, 6 mol/L) and hydrogen dioxide solution (H2O2, 30%(mass fraction)) were used as precipitant and complexant, respectively.
Appropriate dosage of ZrOCl2·8H2O was dissolved in de-ionized water, and formed 0.5 mol/L Zr4+ solution. Subsequently, Y2O3 and AlCl3·6H2O were added to Zr4+ solution. The molar fraction of Y2O3 in initial composition of yttria-stabilized zirconia (YSZ) compound was designed as 3%. The mass fraction of alumina, which acted as a dopant of 3%Y2O3(molar fraction) stabilized ZrO2 (3YSZ) compound and was introduced by AlCl3·6H2O, ranging from 0 to 1.0% in 3YSZ matrix (0-1.0AD3YSZ). After the dissolution of starting materials, different dosages of H2O2, molar ratio of H2O2 to Zr4+ source ranging from 0 to 1.5, was dropwise added to the solution of starting materials with uninterrupted stirring of magnetic stirrer. With the addition of H2O2, pungent gas detected as chlorine (Cl2) was gradually released from the solution of starting materials. After aging for a short period, the amount of released Cl2 reduced and the 6 mol/L NH3·H2O was then dropwise added to the mixed solution with vigorous stirring. Simultaneously, the coprecipitation process began to proceed, and white flocculent precipitates were immediately generated from the mixed solution. The pH value of the reaction system was maintained about 8.5 during the whole course of reaction. This process is so-called peroxyl-complex coprecipitation (PCC). During the PCC process, the temperature of the reaction system was held at 40 ℃.
After aging for 1 h, till the pH value of the reaction system did not change, the resultant precipitates (aqueous precursors) were repeatedly washed with de-ionized water and filtered water. Filter cakes of the aqueous precursors, yielded from 0.5 mol ZrOCl2·8H2O and other corresponding additives, were dried in domestic microwave oven (Midea, 2.45 GHz, 320 W, 30 min) and traditional drying oven (80 ℃, 3 h), respectively. The dried precipitates made by different drying techniques were ball-milled and then calcined at 800 ℃ for 1 h. The whole process of PCC together with microwave drying was named after microwave-assisted peroxyl-complex coprecipitation (MAPCC).
The resultant ADYSZ nanopowders synthesized by MAPCC were uniaxially pressed at 120 MPa in a hard metal die with a diameter of 10 mm, and were cold isostatically pressed at 200 MPa, subsequently. The pressed pellets were sintered in air at different temperatures up to 1 500 ℃ for 2.5 h. The apparent density of the sintered pellets was measured by the ARCHIMEDE’s method, and the relative density was calculated using the theoretical density of 6.08 g/cm3.
To confirm the effect of H2O2 on the uniformity of component distribution, the compositional analysis of resultant ADYSZ nanopowders was done by using energy dispersive X-ray analysis (EDX, PHOENIX M/S EDAX, USA). The phase analysis of resultant ADYSZ nanopowders was done with X-ray diffractometer (XRD, PHILIPS PW 1 710, Netherlands) with Cu Kα radiation. Scanning electron microscopy (SEM, LEO 1530VP, Germany) was performed to observe the nature of agglomerates, surface morphology and approximate particle size in the resultant ADYSZ nanopowders exsiccated by different drying techniques. Finally, the mean size of resultant ADYSZ nanopowders was estimated from transmission electron microscopy (TEM, PHILIPS TECNAI F20, Netherlands).
3 Results and discussion
The XRD patterns of 0.3%(mass fraction) Al2O3-doped 3%(molar fraction) Y2O3-stabilized ZrO2 (0.3AD3YSZ) nanopowders, calcined at 800 ℃ for 1 h, synthesized by coprecipitation and PCC were shown in Fig. 1.

Fig.1 XRD patterns of 0.3AD3YSZ nanopowders synthesized by (a) coprecipitation and (b) PCC, calcined at 800 ℃ for 1 h
It can be found from Fig.1 that crystallinity of samples synthesized by PCC was better than that of samples synthesized by coprecipitation. Furthermore, characteristic reflections corresponding to monoclinic zirconia (m-ZrO2) could be found in Fig.1(a). Whereas, absence of either m-ZrO2 or other segregated substance was presented in Fig.1(b), and only reflections corresponding to tetragonal zirconia (t-ZrO2) were observed in Fig.1(b), which implied homogeneous component distribution within 0.3AD3YSZ nanopowders synthesized by PCC.
The EDX analysis results on 0.3AD3YSZ nanopowders synthesized by PCC confirm the presence of both yttrium and zirconium along with small amount of aluminum. By analyzing the EDX patterns, the atomic ratios of yttrium to zirconium and aluminum to zirconium collected from several stochastic points in 0.3AD3YSZ nanopowders samples synthesized by PCC were well kept within solid solution of initial composition, rather than those in 0.3AD3YSZ nanopowders samples synthesized by coprecipitation. The possible reasons for the improvement of compositional homogeneity brought by PCC were as follows: the complexing reaction between H2O2 and Zr4+ restrained the hydrolyzation and precipitation of Zr4+[15], with the addition of H2O2, the pH values for the precipitations of Al3+, Y3+ and Zr4+ ions were relatively proximate, and the three kinds of ions could be precipitated synchronously in a relative narrow range of pH value, which resulted in the synchronous precipitations of Al3+, Y3+ and Zr4+ ions. Finally, the synchronous precipitations led to a more homogeneous component distribution.
Simultaneously, H2O2 also improved the filterability of the wet precipitates. The experimental data for the effects of H2O2 on the consumption of NH3·H2O and filterability of aqueous precursors, yielded from 0.5 mol ZrOCl2·8H2O and other corresponding additives, were summarized in Table 1.
Table 1 Effects of H2O2 on consumption of NH3·H2O and filterability of aqueous precursors
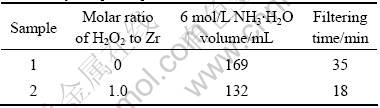
It can be seen from Table 1 that the addition of H2O2 to the initial solution of starting materials led to the consumption of NH3·H2O reduce and the filterability of aqueous precursors improve, the time for filtration was almost halved. GAO et al[16] reported that Zr4+ could react with H2O2 and generated a complex compound with ligands of —OH and —OOH. Consequently, it can be inferred from Table 1 that the ligands of —OH and —OOH derived from the complexing reaction within H2O2 and Zr4+ reduced the consumption of NH3·H2O and made the highly hydrophilic precipitates be quickly and effectively separated from aqueous solution.
Moreover, H2O2 is a strong oxidizer, with the addition of H2O2, the following reaction takes place within the solution of starting materials:
2Cl-+H2O2→Cl2↑+2OH- (1)
As the solubility of chlorine (Cl2) in de-ionized water was very little at room temperature, most of Cl- was easily removed using PCC method. KATO et al[17] reported that the secondary particle size of hydrous zirconia synthesized from ZrOCl2 solutions with the addition of metal chlorides increased as the number of Cl- ions in the solution increased. Hence, the conclusion can be drawn that PCC method can also effectively reduce the scale of powders.
Microwave drying has many advantages such as great efficiency, little thermal wastage, and so on. In comparative experiments, when wet precursors, which were yielded from 0.5 mol ZrOCl2·8H2O and other corresponding additives, were dried in oven at 80 ℃, it took 3 or 4 h to get the wet precursors thoroughly dried. However, the drying time shortened to about 30 min when microwave was performed.
To investigate the influence of different drying technique on the microstructure features of ADYSZ nanopowders, SEM was performed in this research. Fig.2 shows the microstructure features of ADYSZ nanopowders yielded from precursors which were dried by oven and microwave. It can be found that samples in
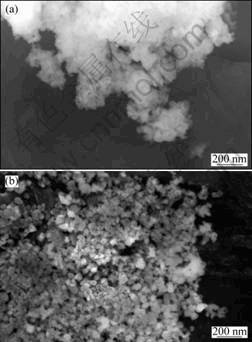
Fig.2 SEM photographs of ADYSZ nanopowders yielded from precursors synthesized by PCC, dried by (a) oven (80 ℃, 3 h) and (b) microwave (2.45 GHz, 320 W, 30 min), calcined at 800 ℃ for 1 h
Fig.2(a) comprise considerably densely agglomerated particles compared with samples in Fig.2(b), and the scale of each tiny lump of samples in Fig.2(a) is larger than that of samples in Fig.2(b). By contrasting the two photographs in Fig.2, it can be drawn that, compared with oven drying, the state of agglomeration within samples is greatly lightened by microwave drying.
Different drying mechanisms cause distinct contrast between Fig.2(a) and Fig.2(b). Microwave drying has the characteristic of volumetric heating, and this kind of heating is selective. During microwave drying process, the moisture of wet precursors is selectively heated by the microwave radiation. Because of the quick expansion caused by the acute evaporation of exterior and interior moisture, most aggregation within the wet colloidal particles burst into numerous tiny lumps. The microwave drying effectively avoided the condensation polymerization of hydroxyl groups induced by traditional oven drying. The burst model of microwave drying is demonstrated in Fig. 3.
Fig. 4 shows a TEM photograph of the resultant ADYSZ nanopowders consisted of hexagonally shaped particles and relatively uniform size distribution with diameters approximately 30 nm.
After sintering at 1 385 ℃ for 2.5 h, the relative
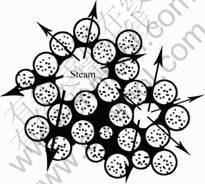
Fig. 3 Expansion effects caused by steam within wet colloidal particles during microwave drying process
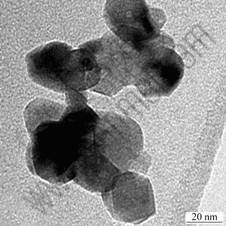
Fig.4 TEM photograph of ADYSZ nanopowders synthesized by MAPCC calcined at 800 ℃ for 1 h
density of the pressed pellets fabricated by 0.3AD3YSZ nanopowders reaches the maximum value of 98% of the theoretical density.
4 Conclusions
1) The addition of H2O2 in PCC route improves the filterability of the hydrous ADYSZ precursors and the uniformity of component distribution within resultant ADYSZ nanopowders. The reactions between H2O2 and Cl- made chlorine be easily removed. By adding H2O2, Al3+, Y3+ and Zr4+ can be precipitated synchronously in a relatively narrow range of pH value, which results in the improvement of compositional uniformity.
2) Microwave drying can effectively reduce the aggregation intensity and shorten the drying period. During microwave drying process, the moisture within the wet precipitates is selectively heated and turned into vapor, subsequently. Burst of the aggregate wet colloidal particles caused by the acute evaporation of exterior and interior moisture is considered the primary reason for avoiding aggregation.
3) ADYSZ nanopowders with homogeneous composition, low aggregation and narrow size distribution ranging around 30 nm can be synthesized by MAPCC method. The resultant ADYSZ nanopowders have good sintering activity. Compared with powders synthesized by other methods, 0.3AD3YSZ can be densely sintered at a relatively low temperature of
1 385℃. The relative density of the pressed pellets fabricated by the 0.3AD3YSZ reaches the maximum value of 98% of the theoretical density.
References
[1] GEORGE A M,VAIDYA M A, PHADNIS A B, MISHRA N C. Synthesis and structural characterization of calcia-stabilized tetragonal zirconia [J]. Journal of Materials Science, 1991, 26(15): 4194-4195.
[2] GARVIE R C, HANNINK R H J, PASCOE R T. Ceramic stell [J]. Nature (London), 1975, 258: 703-704.
[3] BOKHIMI X, MORALES A, GARCIA-RUIZ A, XIAO T D, CHEN H, STRUTT P R. Transformation of yttrium-doped hydrated zirconium into tetragonal and cubic nanocrystalline zirconia [J]. Journal of Solid State Chemistry, 1999, 142(2): 409-418.
[4] TSUKUMA K. Mechanical properties and thermal stability of CeO2 containing tetragonal zirconia polycrystals [J]. American Ceramic Society Bulletin, 1986, 65(10): 1386-1389.
[5] HODGSON S N B, CAWLEY J, CLUBLEY M. The role of Al2O3 impurities on the microstructure and properties of Y-TZP [J]. Journal of Materials Processing Technology, 1999, 92-93: 85-90.
[6] ROSS I M, RAINFORTH W M, McCOMB D W, SCOTT A J, BRYDSON R. The role of trace additions of alumina to yttria-tetragonal zirconia polycrystals(Y-TZP) [J]. Scripta Materialia, 2001, 45: 653-660.
[7] TEKELI S. The flexural strength, fracture toughness, hardness and densification behaviour of various amount of Al2O3-doped 8YSCZ/Al2O3 composites used as an electrolyte for solid oxide fuel cell [J]. Materials and Design, 2006, 27: 230-235.
[8] YANG C L, HSIANG H I, CHEN C C. Characteristics of yttria stabilized tetragonal zirconia powder used in optical fiber connector ferrule [J]. Ceramics International, 2005, 31: 297-303.
[9] MATSUI K, OHGAI M. Formation mechanism of hydrous-zirconia produced by hydrolysis of ZrOCl2 solutions [J]. Journal of the American Ceramic Society, 1997, 80(8): 1949-1956.
[10] MATSUI K, OHGAI M. Formation mechanism of hydrous-zirconia particles produced by hydrolysis of ZrOCl2 solutions: II [J]. Journal of the American Ceramic Society, 2000, 83(6): 1386-1392.
[11] ATKINSON A, SEGAL D L. Some recent developments in aqueous sol-gel processing [J]. Journal of Sol-gel Science and Technology, 1998, 13: 133-139.
[12] AVILA D M, MUCCILLO E N S. Influence of some variables of the precipitation process on the structural characteristics of fine zirconia powders [J]. Thermochimica Acta, 1995, 256: 391-398.
[13] PITICESCU R R,MONTY C, TALOI D, MOTOC A, AXINTE S. Hydrothermal synthesis of zirconia nanomaterials [J]. Journal of the European Ceramic Society, 2001, 21: 2057-2060.
[14] van de GRAAF M A C G, BURGGRAAF A J. Science and Technology of Zirconia Ⅱ: Advances in Ceramics, Vol. 12 [M]. Columbus: The American Ceramic Society, 1984: 744.
[15] MATSUDA Shin-ichi. New precipitation method [J]. Ceramics(in Japanese), 1999, 34(2): 84-88.
[16] GAO Yan-feng, MASUDA Y, OHTA H, K K. Room-temperature preparation of ZrO2 precursor thin film in an aqueous peroxozirconium-complex solution [J]. Chemistry of Materials, 2004, 16: 2615-2622.
[17] KATO E, EZOE M, KONDO M, MURASE Y, MATOBA K. Size control of ZrO2 aggregated particles by chloride-coexisted hydrolysis and sintering them [J]. Yogyo Kyokaishi, 1987, 95(10): 984-990.
(Edited by CHEN Can-hua)
Foundation item: Project(043182311) supported by the Key Program of Scientific and Technical Research of Tianjin
Corresponding author: XU Ming-xia; Tel: +86-22-27890489; Fax: +86-22-27404724; E-mail: xumingxia@tju.edu.cn