DOI:10.19476/j.ysxb.1004.0609.2019.10.15
基于纳米划痕仪的单晶锗多次刻划力学特性实验
罗 良,杨晓京
(昆明理工大学 机电工程学院,昆明 650500)
摘 要:为深入理解单晶锗的纳米切削特性,提高纳米锗器件的光学表面质量,使用纳米划痕仪对单晶锗进行多次刻划实验研究,并测得其在刻划过程中的切削力、摩擦因数。利用扫描电子显微镜(SEM)观测沟槽的显微形貌及切屑堆积情况,使用原子力显微镜(AFM)检测其多次刻划过程中的弹性模量及表面粗糙度。结果表明:随着刻划次数的增多,切削力、摩擦因数,表面粗糙度均在逐渐增大,而弹性模量在逐渐变小,这些现象产生的根本原因是在刻划过程中位错的产生及单晶锗晶格遭到破坏引起的能量波动。此外,随着刻划次数的增加,沟槽两侧的切屑堆积越来越明显。
关键词:单晶锗;多次刻划;切削力;弹性模量
文章编号:1004-0609(2019)-10-2341-07 中图分类号: 文献标志码:A
红外光学材料在红外成像与制导技术中用于制造透镜、棱镜、窗口、滤光片、整流罩等,红外光学技术与微电子技术的结合,极大地推动了红外成像与红外制导技术的发展。单晶锗是红外光学硬脆材料的典型代表,是重要的红外材料,既可用于长波红外波段,又可用于中波红外波段。单晶锗的折射率大,有利于降低像差,对设计光学器件相当有利。在航空航天、军事设备等高科技领域有着重要的应用。
随着对切削加工精度和加工表面质量的要求不断提高的要求,超精密切削加工不断向纳米尺度拓展,即向纳米级、原子级精度发展,微纳米切削是超精密切削加工技术发展的前沿,是达到极限尺寸加工的重要手段[1]。到目前为止,对微纳米切削力学的研究还很不充分,特别是对于单晶锗红外光学硬脆材料微纳米切削力学理论的研究更是少之又少,在理论和技术等方面还需要进一步深入研究。
纳米划痕仪是测试材料力学性能的常用设备,不仅可以得到局部区域的硬度、弹性模量、摩擦因数等有关形变的宏观信息,还可以结合SEM、TEM和拉曼光谱等测试手段,对样品在纳米压痕和划痕测试中形成的切屑、位错、相变等微观形变机制进行讨论和分析[2-5]。与其他方法相比,通过纳米划痕仪来加工纳米沟槽可以更为简单快捷地来研究材料的力学性能,并且可以加工类似于硅、锗一类的硬脆材料,加工的尺度也可以从纳米级别跨度到微米级别。目前,已有很多学者利用纳米划痕仪对各种材料进行加工,大多集中在铝、硅及氧化物等表面[6-9]。近年来,有一些学者利用原子力显微镜对单晶硅进行多次刻划实验研究[10-16],然而利用这种方式对硬脆材料进行多次刻划加工时,会对原子力显微镜的探针造成极为严重的磨损,加工成本极高。也有一些学者使用纳米划痕仪通过取不同的载荷、切削速度及晶向,来研究其在单晶锗纳米切削过程中的切削特性[17-18]。然而至今却没有利用纳米划痕仪对单晶锗进行多次刻划的实验研究。
在实际切削过程中并不是总能一次就可以加工出所需要的表面形貌尺寸,实验更接近于微纳器件实际的加工过程。本文首次使用纳米划痕仪对单晶锗基体进行多次刻划实验研究,使用原子力显微镜分析了切削力、摩擦因数、弹性模量以及表面粗糙度在不同的刻划次数下的变化情况。为单晶锗微纳器件制造产业提供理论依据和实验基础。
1 实验
实验采用的基体材料为由合肥科晶技术公司制备的单晶锗片,晶面取向为(100),样品尺寸大小均为10 mm×10 mm×0.5 mm。样品的表面粗糙度小于5
,清洁度约1000级(超净工作室中制作),对样品进行单面抛光,将抛光面作为实验所用表面。在实验之前先对样品进行预处理,将样品放入丙酮和乙醇溶液中浸泡10 min进行去污,然后对样品表面进行预热。
实验所用的纳米划痕仪(NST),载荷范围为0.03 mN~1 N,载荷分辨率为0.02 μN,最大压入深度为600 μm,实验中采用圆弧曲率半径为2 μm的Berkovivh压头。
在真空的环境下采用聚焦离子束扫描电子显微镜(TESCANLYRA3 FEG-SEM/FIB)对单晶锗纳米划痕实验所得的样品的表面形貌进行观察。采用原子力显微镜(AFM)观察和测量单晶锗纳米沟槽的表面粗糙度及弹性模量信息。
在微纳米尺度下进行纳米刻划实验,对金刚石压头施加一定的法向载荷,使其压入单晶锗基体表面,并使装有试件的样品台沿切向方向水平匀速运动。图1所示为金刚石压头和试件表面滑动接触示意图。
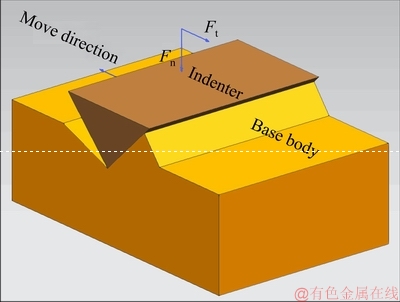
图1 金刚石压头和样品表面滑动示意图
Fig. 1 Schematic diagram of sliding contact between indenter and specimen
在单晶锗抛光面上刻划出6条长度均为200 μm的纳米沟槽。6条纳米沟槽的刻划次数分别为1、2、4、6、8、10次,施加的载荷均为20 mN,刻划速度均为200 μm/min。随着刻划次数的增加,压头进入工件表面的深度也逐渐变深,会发现试件表面的划痕呈沟槽状,沟槽的深度随刻划次数的增大而增大。
在刻划实验中,通过装有摩擦力传感器的纳米划痕仪可以测出在切削过程中的切削力及摩擦因数等参数随刻划距离、时间连续变化的数据。在不同的刻划次数下,绘制出切削力-位移曲线及摩擦因数-位移曲线。利用AFM测得每条纳米沟槽的弹性模量和表面粗糙度并绘制弹性模量-刻划次数曲线及表面粗糙度-刻划次数曲线。
2 实验结果与分析
2.1 对切削力及摩擦因数的影响
对切削力的研究是理解纳米切削机理的一个重要因素,它反映了材料的去除过程。图2所示为单晶锗在刻划速度为200 μm/min、载荷恒为20 mN、不同刻划次数时的切削力-位移曲线图。从图2可以看到,刻划次数对切削力的大小影响非常明显,随着刻划次数的增多,切削力也对应在增加。当刻划次数为1、2、4、6次时,切削力在0.4 mN附近反复波动,从第8次开始明显增长在0.7 mN附近波动,当刻划次数达到第10次时,切削力达到了0.9 mN。切削力的波动是由于单晶锗晶体中存在位错及在切削过程中单晶锗原子晶格遭到破坏而释放能量引起的。随着刻划次数的增多,切削的深度越来越深,单晶锗晶体的塑性变形也越来越明显,晶体对刀具滑移的阻力越来越大,单晶锗基体对变形的抗力不断的增加导致其切削力不断的增大。从位错理论的观点来看,随着塑性变形的进行,晶体中位错运动越来越困难。因为塑性变形所产生的内应力虽有利于位错的生长,但更不利于位错的运动致使切削力不断地增大。
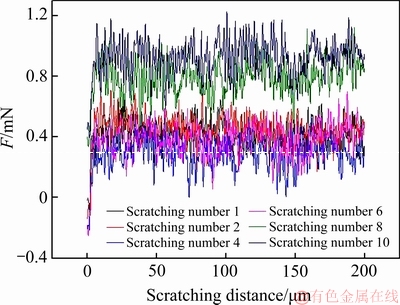
图2 不同刻划次数下切削力-刻划距离曲线
Fig. 2 Curves of cutting force-scratching distance under different scratching number
在微纳切削过程中的摩擦因数并非是恒定的,多次刻划会引起摩擦因数的变化,其计算公式如式(1)所示:
(1)
式中:η为摩擦因数;Ft为切向载荷;Fn为垂直载荷。
根据得到的切削力Ft,垂直载荷为20 mN,由公式计算出不同刻划次数下摩擦因数与划痕距离的关系曲线,其结果如图3所示。由图3可知,摩擦因数受刻划次数的影响规律与上述切削力一致。
为了能够清晰地看到不同刻划次数下纳米沟槽的表面形貌,使用扫描电子显微镜对沟槽进行观测,如图4所示,可以看到随着刻划次数的增加,沟槽的三维形貌尺寸在逐渐增大,同时沟槽两侧的切屑堆积越来越明显。

图3 不同刻划次数下摩擦因数-刻划距离曲线图
Fig. 3 Friction coefficient-scratching distance curves at different scratching number
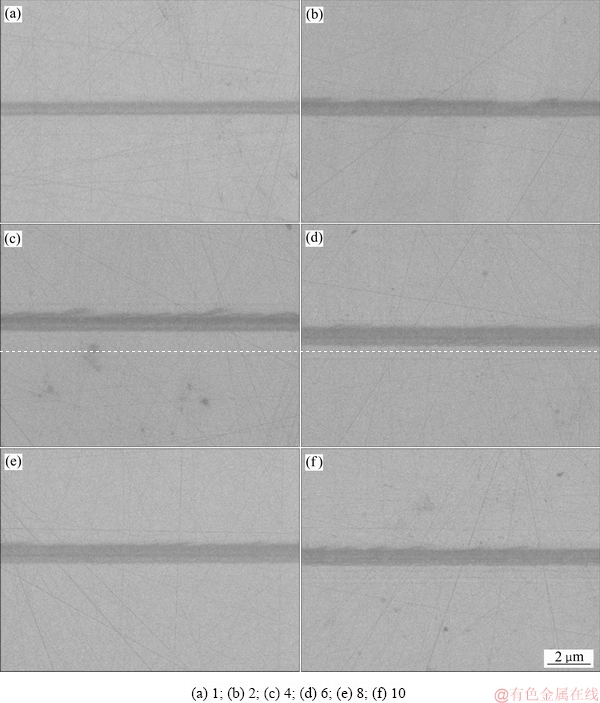
图4 不同刻划次数的纳米沟槽的SEM像(切削速度200 μm/min,垂直载荷为20 mN)
Fig. 4 SEM images of nanogrooves (200 μm) scratched at different scratching number (Scratching velocity 200 μm/min, normal forces 20 mN)
2.2 对弹性模量的影响
过去,材料的机械性质如弹性模量是通过不同的压印技术(Vickers或Hysitron)来进行测定的。在压入过程中通过一条被记录的载荷-位移曲线便可得到弹性模量信息。这些技术主要是用来研究薄膜的机械性质的。要获得定量的弹性模量,需要将AFM和压痕的力曲线实验数据与针尖-样品接触模型相拟合,根据不同的条件选择不同的模型。目前,常用的两种模型为JKR(Johnson, Kendall and Roberts)和DMT (Derjaguin-Muller-Toporov)模型[19-20]。其中,DMT模型适用于实验所用硬质的单晶锗材料,原子力显微镜探针半径较小的情况,因此,选择DMT模型进行测量,其测量原理如式(2)和式(3)所示:
(2)
式中:FDMT为作用在试件上的接触力;E为试件与针尖接触时的弹性模量;a为试件与针尖接触时的圆弧半径;R为针尖的圆弧半径;
为原子力显微镜探针悬臂的位移变量。
(3)
式中:Es为试件的弹性模量;Et为针尖的弹性模量;
为试件的泊松比;
为针尖的泊松比。
综合式(2)、(3)就可以求出被测材料的弹性模量。
图5所示为基于DMT模型的原子力显微镜测得的单晶锗纳米沟槽内部刻划次数与弹性模量的变化关系曲线。由图5可以看出,随着刻划次数的增加,弹性模量在逐渐减小。当对单晶锗抛光面刻划1次时,测得弹性模量值为257 GPa;第10次刻划时,测得弹性模量值为212 GPa,导致这种现象的原因是进行单晶锗基体的机械化学抛光生产时的加工变质层要大于纳米划痕仪刻划过后的加工变质层,且随着刻划次数的增加,加工变质层越来越小,因此,随着划痕次数的增加,其弹性模量在逐渐减小,最终会趋于稳定。此外,可以看出得到的弹性模量值要大于传统的纳米实验方法(Vickers)所得到的值,其原因是针尖的影响比如钝化和存在于最外层的氧化膜以及加工变质层的存在。
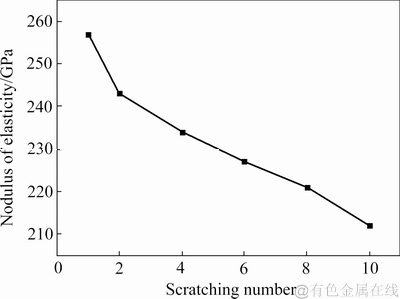
图5 弹性模量与刻划次数曲线
Fig. 5 Modulus of elasticity-scratching number curves
2.3 对表面粗糙度的影响
对单晶锗纳米沟槽进行加工时,刻划次数与沟槽表面粗糙度的实验关系曲线图如图6所示。
在微加工过程中刻划次数从1~10次变化时,沟槽的表面粗糙度在逐渐增大,即从刻划次数为1次时的Ra=0.376 nm到刻划次数为10次的Ra=1.623 nm。这是由于在金刚石压头划入单晶锗基体表面时,基体内部会产生位错,随着刻划次数的增加基体内部的位错越来越多产生位错堆积。此外,在刀具滑移过程中,单晶锗的晶格遭到破坏,释放出的能量会影响刀具与沟槽表面的接触稳定性。图7所示为不同刻划次数下的单晶锗加工表面AFM像。由图7可以看出,随着刻划次数的增加,单晶锗纳米沟槽的三维形貌尺寸在增加,表面光洁度也在下降,沟槽两侧的切屑堆积也越来越明显。
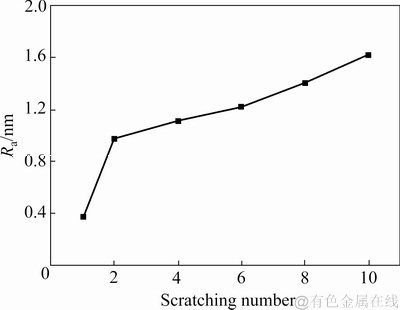
图6 表面粗糙度与刻划次数曲线图
Fig. 6 Surface roughness-scratching number curves
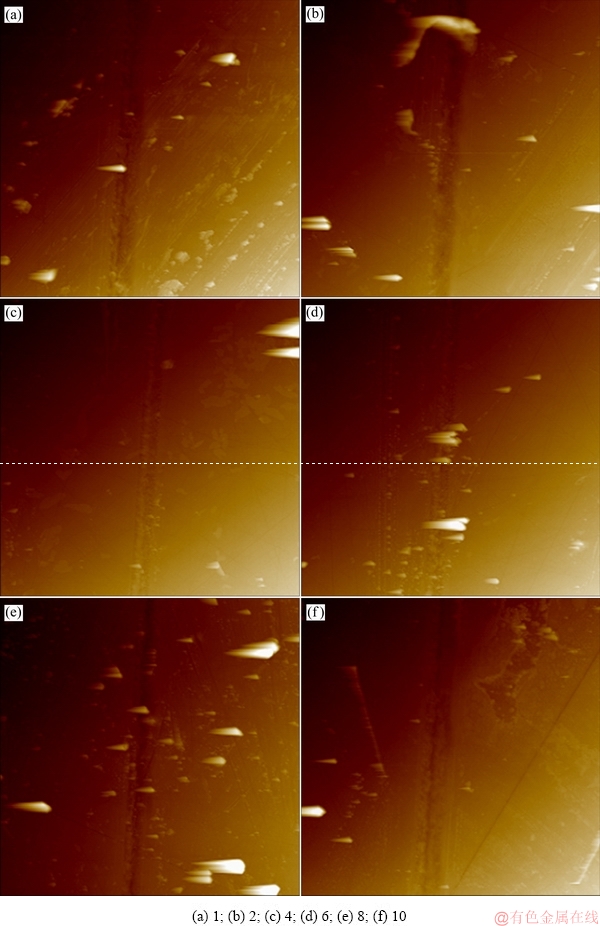
图7 不同刻划次数的纳米沟槽(200 μm) AFM像(切削速度为200 μm/min,垂直载荷为20 mN)
Fig. 7 AFM topographies of nanogrooves (200 μm) scratched at different number (Scratching velocity 200μm/min, normal forces 20 mN)
3 结论
1) 在单晶锗微纳切削过程中切削力及摩擦因数随着刻划次数的增加而增大,当刻划次数为1次时测得其切削力在0.4 mN附近波动,摩擦因数约为0.02;刻划次数为10次时,切削力增大到0.9 mN,摩擦因数约为0.045。切削力波动的根本原因是在刻划过程中单晶锗基体内部位错堆积及晶格破坏所引起的能量波动。
2) 利用原子力显微镜测得了在不同刻划次数下单晶锗纳米沟槽的弹性模量,弹性模量随着刻划次数的增大而减小,这是由于随着刻划次数的增多,单晶锗基体表面的加工变质层越来越小,此外,利用这种方法测得的弹性模量值要比传统的压痕方式得到的值要大,这是由于原子力显微镜的针尖圆弧半径较小,在划痕过程中产生了钝化及加工变质层的存在。
3) 随着刻划次数的增加,单晶锗已加工表面的粗糙度越来越大,第1次刻划时,其表面粗糙度为0.376 nm;第10次刻划时,表面粗糙度达到了1.623 nm。此外,随着刻划次数的增加,沟槽两侧的切屑堆积也越来越明显,单晶锗基体的塑性变形越来越明显。
REFERENCES
[1] 王国彪. 纳米制造前沿综述[M]. 北京: 科学出版社, 2009.
WANG Guo-biao. A review of the frontiers of nanofabrication[M]. Beijing: Science Press, 2009.
[2] WANG Yong-guang, CHEN Yao, ZHAO Dong, LU Xiao-long, LIU Wei-wei, QI Fei, CHEN Yang. Deformation mechanism of CrN/nitriding coated steel in wear and nano-scratch experiments under heavy loading conditions[J]. Applied Surface Science, 2018, 447(31): 100-106.
[3] CHEN L, PERSSON J, STAHL J E, ZHOU J M. Nano-scratching resistance of high-chromium white cast iron and its correlation with wear of cBN tool in machining[J]. Journal of Superhard Materials, 2017, 39(5): 365-372.
[4] LIU Xiao-ming, LIU Zhan-li, WEI Yue-guang. Ploughing friction and nanohardness dependent on the tip tilt in nano-scratch test for single crystal gold[J]. Computational Materials Science, 2015, 110: 54-61.
[5] Ballarrea J, López D A, Cavalieri A L. Frictional and adhesive behavior of organic–inorganic hybrid coatings on surgical grade stainless steel using nano-scratching technique[J]. Wear, 2009, 11/12: 1165-1170.
[6] Beake B D, Vishnyakov V M, Harris a J. Nano-scratch testing of (Ti,Fe)Nx thin films on silicon[J]. Surface & Coatings Technology, 2017, 309(15): 671-679.
[7] BEAKE B D, LISKIEWICZ T W, SMITH J F. Deformation of Si(100) in spherical contacts comparison of nano-fretting and nano-scratch tests with nano-indentation[J]. Surface & Coatings Technology, 2011, 7(25): 1921-1926.
[8] AMANOV A, SASAKI S, CHO I S. An investigation of the tribological and nano-scratch behaviors of Fe-Ni-Cr alloy sintered by direct metal laser sintering[J]. Materials and Design, 2013, 47: 386-394.
[9] HIGASHINO S, MIYAKE M, MATAMURA Y. Evaluation of the hardness and Young’s modulus of electrodeposited Al-W alloy films by nano-indentation[J]. Surface & Coatings Technology, 2017, 325(25): 346-351.
[10] GENG Yan-quan, BROUSSEAU E B. AFM tip-based nanomatching with increased cutting speed at the tool-workpiece interface[J]. Precision Engineering, 2018, 51: 536-544.
[11] GENG Yan-quan, YAN Yong-da. AFM tip-based mechanical nanomatchining of 3D micro and nano-structures via the control of the scratching trajectory[J]. Journal of Materials Processing Technology, 2017, 248: 236-248.
[12] GENG Yan-quan, YAN Yong-da. Depth prediction model of nano-grooves fabricated by AFM-based multi-passes scratching method[J]. Applied Surface Science, 2014, 313(15): 615-623.
[13] JIANG Xiao-hong, WU Guo-yun. Nanopattering on silicon surface using atomic force microscopy with diamond-like carbon(DLC)-coated Si probe[J]. Nanoscale Research Letters, 2011, 6: 518.
[14] DONG Zhu-xin, WEJINYA U C. Atomic force microscopy based repeatable surface nanomatchining for nanochannels on silicon substrates[J]. Applied Surface Science, 2012, 258(22): 8689-8695.
[15] VIEIRA L, LUCAS F L C. Scratch testing for micro- and nanoscale evaluation of tribocharging in DLC films containing silver nanoparticles using AFM and KPFM techniques[J]. Surface & Coatings Technology, 2014, 260(15): 205-213.
[16] WANG Z Q, TUNG S. Material removal model for AFM-based nanochannel fabrication[J]. Wear, 2012, 278/279(8): 71-76.
[17] LIU Yan-rong, YANG Xiao-jing, YANG Cheng-ming. Experimental research on mechanical characteristics in the process of nanoscale sliding contact[J]. Applied Mechanics and Materials, 2013, 275(77): 1769-1774.
[18] 杨晓京, 李 勇. 微纳米尺度单晶硅各向异性表面的切削特性[J]. 材料科学与工程学报, 2015, 563(4): 508-511.
YANG Xiao-jing, LI Yong. Cutting performance of single crystal silicon anisotropic surface in micro-nano scale[J]. Journal of Materials Science and Engineering, 2015, 563(4): 508-511.
[19] DERJAGUIN B V, MULLER V M, TOPOROV Y P. Effect of contact deformations on the adhesion of particles[J]. Journal of Colloid and Interface Science, 1975, 53: 314-326.
[20] PROKOPOVICH P, PERNI S. Comparison of JKR- and DMT-based multi-asperity adhesion model: Theory and experiment[J]. Colloids and Surfaces A: Physicochem Eng Aspects, 2011, 383: 95-101.
Mechanical properties experiment of monocrystalline germanium with multiple scratches based on nano scratch instrument
LUO Liang, YANG Xiao-jing
(Faculty of Mechanical and Electrical Engineering, Kunming University of Science and Technology, Kunming 650500, China)
Abstract: In order to understand the nanoscale cutting characteristics of single crystal germanium and improve the optical surface quality of the nanoscale germanium, the nanoscratch instrument was used to study the single crystal germanium, and the cutting force and friction coefficient in the process were measured. Scanning electron microscope (SEM) was used to observe the micromorphology and chip accumulation of the grooves. The elastic modulus and surface roughness were measured by atomic force microscopy (AFM). The results show that the cutting force, the friction coefficient and the surface roughness increase with the increase of the number of stroke, and the modulus of elasticity decreases gradually. The root cause of these phenomena is due to the dislocation in the etching process and the energy fluctuation caused by the destruction of the single crystal germanium lattice. In addition, with the increase of the number of chips, the accumulation of chips on both sides of the groove is more and more obvious.
Key words: single crystal germanium; multiple characterization; cutting force; elastic modulus
Foundation item: Projects(51765027, 51365021) supported by the National Natural Science Foundation of China
Received date: 2018-10-15; Accepted date: 2019-06-10
Corresponding author: YANG Xiao-jing; Tel: +86-13668718025; E-mail: xjyang@VIP.sina.com
(编辑 龙怀中)
基金项目:国家自然科学基金资助项目(51765027,51365021)
收稿日期:2018-10-15;修订日期:2019-06-10
通信作者:杨晓京,教授;电话:13668718025;E-mail:xjyang@VIP.sina.com