网络首发时间: 2016-08-23 16:15
稀有金属 2017,41(10),1143-1150 DOI:10.13373/j.cnki.cjrm.xy16050009
湿法冶金法从铅银渣中异步回收锌、铅银的试验研究
李国栋 林海 董颖博 王鑫 张悦
北京科技大学能源与环境工程学院
西北矿冶研究院
摘 要:
传统的湿法炼锌过程中, 在热酸浸出阶段会产生大量的铅银渣, 由于湿法冶炼的工艺特点, 锌精矿中的铅银金属矿物经过焙烧、浸出工序后几乎全部富集在铅银渣中。铅银渣矿虽含有较高品位的铅锌银, 但由于渣中矿物组成复杂, 有价矿物嵌布粒度较细且被脉石矿物和铁酸锌包裹等特点, 常规方法难以有效回收铅银渣中的有价金属, 造成了资源的浪费。采用湿法冶金的方法研究“酸性浸出-氯化浸出”的异步浸出工艺从铅银渣中浸出锌、铅银影响因素, 结果表明:以硫酸作为酸性浸出剂, 铅银渣在浸出时间80 min, 浸出浓度200 g·L-1, 初酸浓度为200 g·L-1, 浸出温度90℃的条件下进行酸性浸锌后, 以硫酸和氯化钠为氯化浸出剂, 将滤渣按照氯化钠浓度300 g·L-1, 浸出时间120 min, 浸出浓度200 g·L-1, 初酸浓度60 g·L-1, 浸出温度90℃的条件进行氯化浸出铅银, 最终可得到尾渣产率为51.84%, 尾渣中含锌0.21%, 含铅0.46%, 含银38.50 g·t-1, 锌、铅和银的浸出率分别为92.15%, 94.88%和93.24%的指标。
关键词:
铅银渣;异步浸出;酸性浸出;氯化浸出;
中图分类号: TF812;TF813;TF832
作者简介:李国栋 (1983-) , 男, 甘肃张掖人, 博士研究生, 研究方向:复杂难选矿选矿技术, E-mail:lgdabcd@163.com;;林海, 教授, 电话:010-62332526, E-mail:Linhai@ces.ustb.edu.cn;
收稿日期:2016-05-08
基金:国家科技部高技术研究发展计划项目 (2012AA062402) 资助;
Hydrometallurgy Asynchronous Recovery of Zinc, Lead and Silver from Pb-Ag Residue
Li Guodong Lin Hai Dong Yingbo Wang Xin Zhang Yue
School of Energy and Environmental Engineering, University of Science and Technology Beijing
Northwest Research Institute of Mining and Metallurgy
Abstract:
In traditional zinc hydrometallurgy process, a large amount of Pb-Ag residue was produced at high temperature acid leaching stage. Due to the characteristics of this process, most of the lead and silver metal in zinc concentrate remained in the Pb-Ag residue after roasting and acid leaching of zinc concentrate. Although Pb-Ag residue contained high grade of lead and silver, giving its complex mineral composition, relatively fine disseminated particle size of valuable minerals and that the valuable minerals encapsulated by gangue minerals and zinc ferrite, the recovery of valuable metals from Pb-Ag residue was difficult by conventional methods. Thus the method of wet metallurgy was adopted for the recovery of valuable metals from Pb-Ag residue. Asynchronous leaching process was studied by using acid-chlorination leaching to recover zinc, lead and silver. Test results showed that the yield rate of 51. 84% for tail residue was obtained with the process as follows. In the acid leaching stage, the conditions were that leaching concentration was 200 g·L-1, initial acid concentration was 200 g·L-1, leaching time was 80 min and temperature was 90 ℃; and in the chlorination leaching stage using the filter residue from the acid leaching, the conditions were that sodium chloride concentration was 300 g·L-1, leaching concentration was 200 g·L-1, initial acid concentration was 60 g·L-1, leaching time was 120 min and temperature was 90 ℃. Finally, the tail residue contained zinc 0. 21%, lead 0. 46%, silver 38. 50 g·t-1, with the leaching rates of 92. 15%, 94. 88%, 93. 24%, respectively.
Keyword:
Pb-Ag residue; asynchronous leaching; acid leaching; chlorination leaching;
Received: 2016-05-08
传统的湿法炼锌利用硫化锌和氧化锌, 通过焙烧-磨矿-酸浸-除杂-电积工艺回收锌金属[1], 在湿法炼锌的过程中会产出大量锌冶炼渣, 这些锌冶炼渣成分复杂且有价矿物含量较高, 特别是高温高酸浸出环节产出的铅银渣。由于湿法炼锌工艺的特点, 在冶炼过程中仅对锌等金属进行了回收, 而其中绝大部分的铅、银和少量的锌等有价金属都存在于铅银渣中未利用, 造成资源浪费[2,3], 并且大量的堆存会带来一系列的环境问题[4,5]。
湿法炼锌浸出渣处理处置是有色冶炼过程中的一个难题, 由于原料差异大, 价值及工艺方法不同, 产出渣的性质也截然不同[6]。目前, 浸出渣综合回收的方法主要有火法和湿法。火法回收主要以奥斯麦特法、回转窑挥发法、烟化炉挥发法等[7]。湿法回收主要以酸性浸出和碱性浸出, 常见的浸出剂有硫酸、盐酸、硝酸、氨水、碳酸盐、氯盐等[8,9,10,11]。通过对比常规的锌冶炼渣回收方法, 从能耗、可操作性以回收成本等方面考虑, 利用湿法冶金工艺无疑是最可靠的方法之一[12,13,14,15]。本文以西北某铅银冶炼厂高温高酸环节产出铅银渣为研究对象, 提出采用酸性浸出-氯化浸出的异步湿法冶金工艺从铅银渣中分别回收锌和铅银金属, 考虑到浸出过程的可操作性、浸出液的后续处理及浸出剂的成本, 选用硫酸作为酸性浸剂回收锌, 以氯化钠和硫酸作为氯化浸出剂浸出铅银。
1 矿石性质
试验所用矿样取自西北某铅锌冶炼厂, 为湿法炼锌过程中的铅银渣, 试样晾晒后利用对辊破碎机进行破碎、筛分、制样。试样的多元素分析见表1, 铅物相见表2, 锌物相见表3, 银物相见表4。
从表1的化学分析结果可以看出, 铅银渣中可供回收的有价金属元素有金、银、铅、锌等金属。表2~4的物相分析结果表明:锌主要以铁酸锌的形式赋存, 含量占54.48%, 其他以氧化锌和硫化锌;铅主要以氧化铅、硫酸铅为主, 含量高达80%以上, 此外还有少量的硫化铅和其他形式赋存的铅;银主要以难溶包裹银和硫化银、金属银的形式赋存, 此外还有少量的氧化银。
表1 铅银渣主要化学分析结果Table 1Multi-elementary analysis results of Pb-Ag resi-due (%, mass fraction) 下载原图
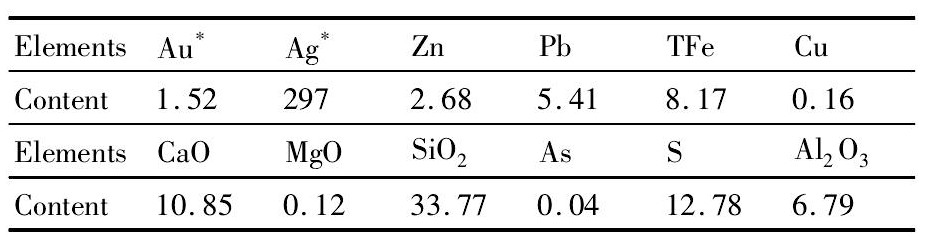
*:unit being g·L-1
表1 铅银渣主要化学分析结果Table 1Multi-elementary analysis results of Pb-Ag resi-due (%, mass fraction)
表2 铅物相分析结果Table 2 Analysis results of lead phase (%, mass fraction) 下载原图
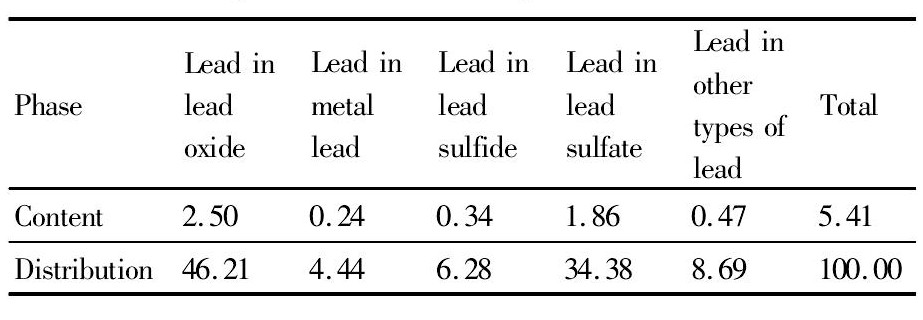
表2 铅物相分析结果Table 2 Analysis results of lead phase (%, mass fraction)
表3 锌物相分析结果Table 3 Analysis results of zinc phase (%, mass fraction) 下载原图
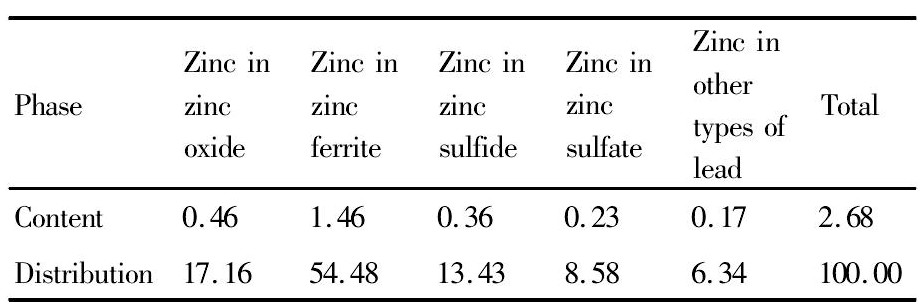
表3 锌物相分析结果Table 3 Analysis results of zinc phase (%, mass fraction)
表4 银物相分析结果Table 4 Analysis results of silver phase (%, mass fraction) 下载原图
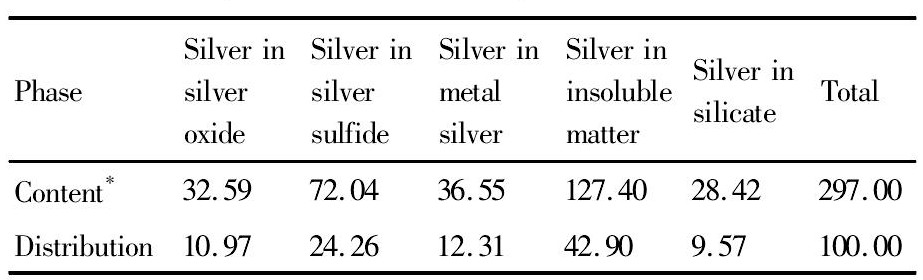
*:unit being g·L-1
表4 银物相分析结果Table 4 Analysis results of silver phase (%, mass fraction)
对铅银渣进行X射线衍射 (XRD) 分析、扫描电镜 (SEM) 及能谱 (EDS) 分析, 分析结果见图1和2。
图1和2的分析结果表明, 铅银渣的组成复杂, 有价金属矿物有硫酸铅、铁酸锌、金属银等, 脉石矿物主要以石英、氧化铁、硫酸钙等。有价金属矿物嵌布较细, 大部分的嵌布在10μm左右且部分的金属矿物以细粒级包裹在铁酸锌和脉石矿物中。部分金属矿物与脉石矿物解离不明显。
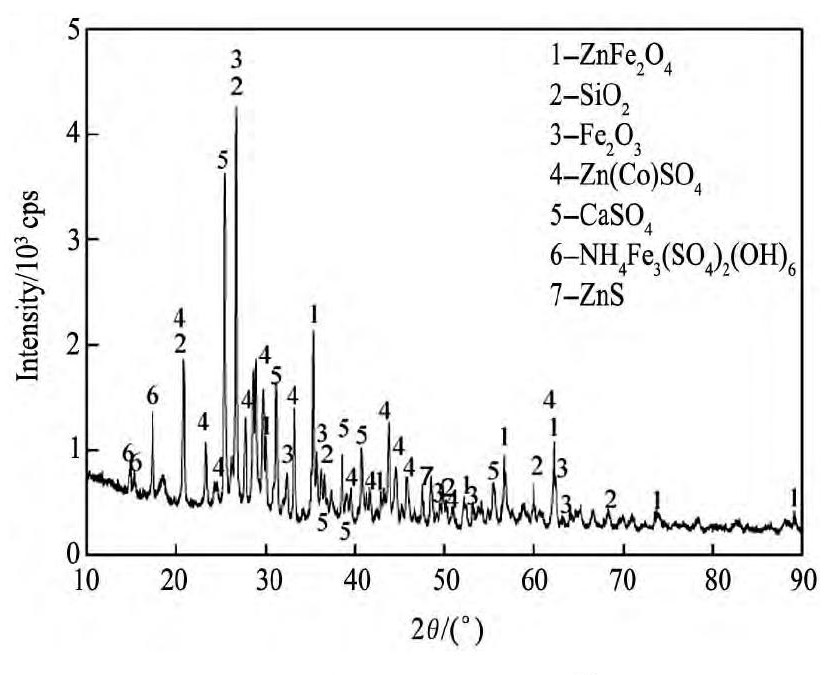
图1 铅银渣XRD图谱Fig.1 X-ray diffraction pattern of Pb-Ag residue
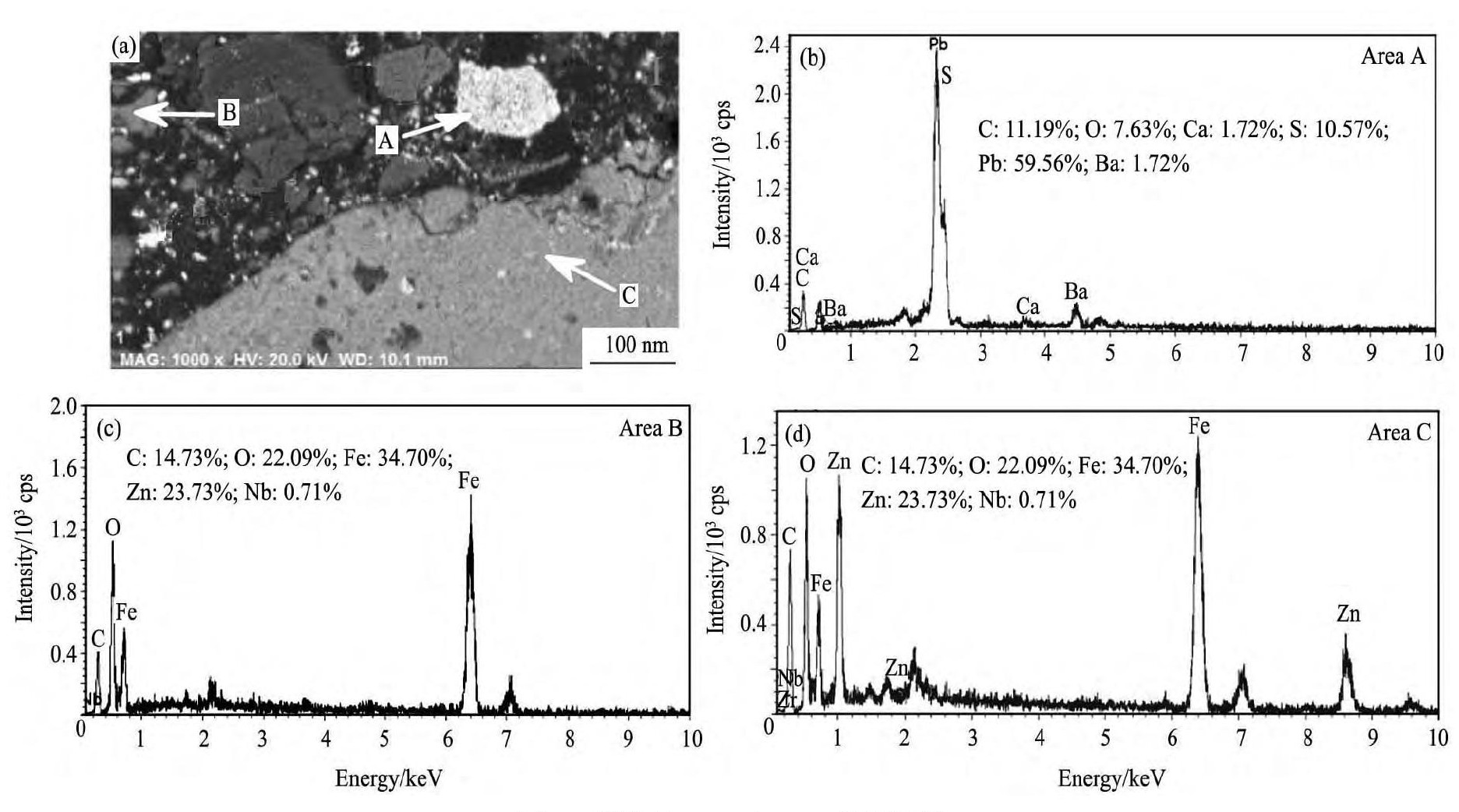
图2 铅银渣SEM和EDS分析图谱Fig.2 SEM image (a) and EDS analysis (b, c, d) of Pb-Ag residue
从铅银渣的矿石性质研究结果可知, 铅银渣中有价金属由于其赋存状态的特殊、嵌布粒度较细且铅银金属被其他矿物包裹的特性难以采用常规的浮选等工艺回收。
2 试验
2.1 方法
取200 g铅银渣置于500 ml烧杯中, 按照试验设定的浸出浓度加入去离子水, 在添加试验要求的浓硫酸后将烧杯放置在H04-1型磁力搅拌器中按照设定的温度和时间进行搅拌浸出锌, 待酸性浸出锌试验结束后, 过滤烘干, 称重后化验计算浸出结果。
取100 g上述最优条件下的酸性浸出渣, 置于500 ml烧杯中, 按照试验设定的浸出浓度加入去离子水, 在添加试验要求的浓硫酸和氯化钠后将烧杯放置在H04-1型磁力搅拌器中按照设定的温度和时间进行搅拌浸出铅和银, 待氯化浸出锌试验结束后, 过滤烘干, 称重后化验并计算浸出结果。在浸出过程中, 在固定时间内补加一定量的去离子水以保证浸出浓度固定。浸出结果的计算是以浸出渣及铅银渣中铅锌银的含量计算的。
2.2 试剂
试验中所用的硫酸和氯化钠均为分析纯。
3 铅锌银浸出基本原理
3.1 锌的浸出
铅银渣的的锌主要以铁酸锌、硫化锌和氧化锌形式存在, 铁酸锌发生的溶解溶液如下:

根据方程 (1) 的热力学数据计算[16], 可知铁酸锌在常温环境下式可以溶解的, 但铁酸锌由于其特殊的锌铁尖晶石构造, 酸溶活化能为58520J·mol-1, 在65℃的弱酸环境很难溶解, 只有从动力学采取必要的手段:提高酸度, 升高浸出温度, 才可以提高铁酸锌的溶解度。
3.2 铅的浸出
铅主要是以硫酸铅和氧化铅的形式存在。在酸性条件下, 氧化铅溶于饱和氯化钠溶液, 按照以下的反应进行[17]:

硫酸铅按照以下反应溶解于饱和氯化钠溶液中生成氯化铅:

溶液中的氯化铅与饱和溶液中的氯化钠选厂络合物, 反应如下:

3.3 银的浸出
铅银渣中的银主要是以难溶包裹银、硫化银和少量的金属形式存在。在热酸浸出过程中, 包裹物被溶解, 内部的银才可以与氯化浸出剂接触到从而被溶解浸出。
在有氧化剂Fe3+存在的酸性环境中, 硫化银会被氧化, 银离子加入溶液并与溶液中的氯离子络合物, 生产络合物, 反应如下[18,19]:

单质银在酸性溶液中, 当有大量的Fe3+存在时, 且体系中αFe3+/αFe2+>2.0×10-10时单质银被溶解加入到溶液中:

上述方程式表明, 铅银渣中存在的3种含银矿物能够被有效的溶解[9], 从而达到浸出目的。
4 结果与讨论
4.1 酸性浸出锌试验
4.1.1 初酸浓度对锌浸出率的影响
由锌浸出原理可以, 提高锌的浸出率就是要提高铅银渣中铁酸锌的浸出率, 而铁酸锌的溶解必须在强酸高温环境中, 因此以硫酸作为锌浸出剂, 试验在浸出温度分别为60, 70, 80和90℃, 浸出时间80 min, 浸出浓度200 g·L-1的条件下, 考察了初酸浓度从100~220 g·L-1范围内变化对锌浸出率的影响。试验结果见图3。
从图3的试验结果可知, 不同温度下初始酸度对锌浸出率结果差异较大。在浸出温度为60℃情况下, 增加初始酸浓度, 锌的浸出率增幅很小。当提高浸出温度, 随着初始酸度的增加, 锌的浸出率也呈现出增加的趋势。在浸出温度80和90℃的条件下, 当初始酸度超过200 g·L-1, 锌的浸出率变化都不再明显。分析结果表明在低温条件下, 铁酸锌的溶解度较小, 锌的浸出率也低, 增加体系温度和初始酸度后, 铁酸锌的溶解度提高, 锌的浸出也就相应增加, 浸出结果与方程 (1) 的热力学分析结果相吻合[16]。在酸性浸出锌过程中, 应该在较高的温度环境中, 选择初酸浓度以200 g·L-1浸出锌为宜。
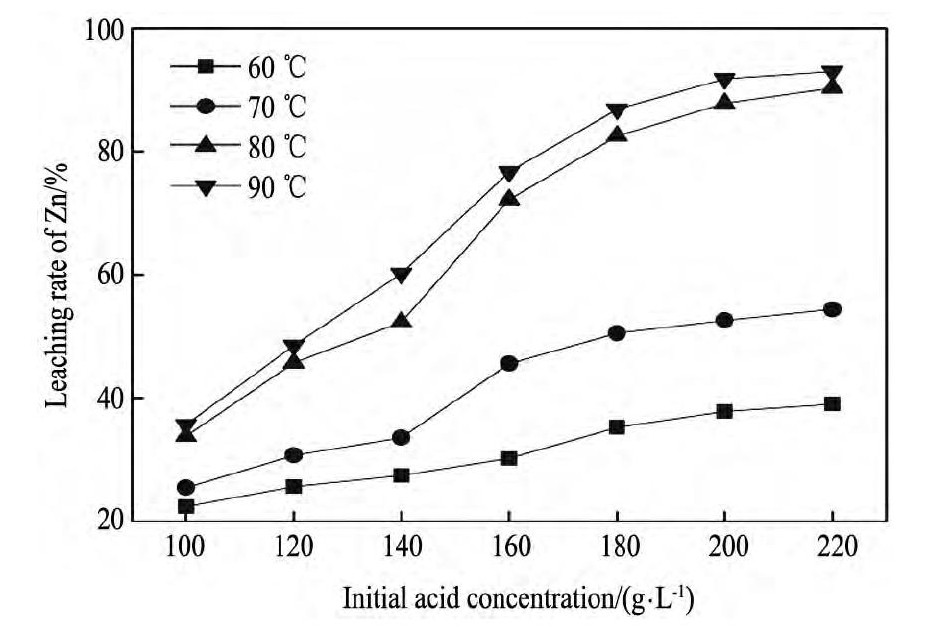
图3 初始酸度对锌浸出率的影响Fig.3 Leaching rate of Zn with different initial acid concentra-tions
4.1.2 浸出浓度 (固液比) 对锌浸出率的影响
初始酸度为200 g·L-1, 浸出时间100 min, 在浸出温度分别为70, 80和90℃的条件下, 研究了浸出浓度在100~300 g·L-1范围内变化对锌浸出率的影响。试验结果见图4。
结果表明, 在3种不同温度体系下锌的浸出率曲线都呈现出同一特征, 锌的浸出率随着浸出浓度的增加而降低, 这一浸出特点在高温体系下尤为明显。分析试验数据可知, 在温度为80和90℃浸出体系下, 当浸出浓度低于200 g·L-1时, 锌的浸出率分别达到87.84%和91.23%, 而浸出浓度超过200 g·L-1时, 锌的浸出率急剧下降, 原因是在酸性浸出体系中, 较低的浸出浓度更有利于浸出剂与物料之间的反应。从动力学角度来讲, 低的浸出浓度更有利于反应向右进行[20,21]。因此, 在酸性浸出锌时, 高温体系下的浸出浓度以200 g·L-1为宜。
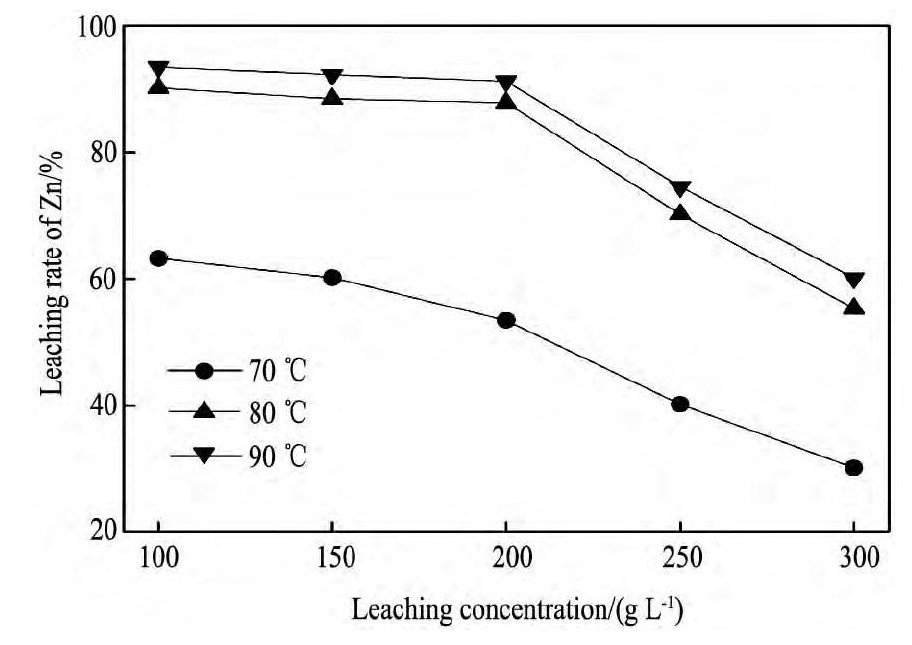
图4 浸出浓度对锌浸出率的影响Fig.4 Leaching rate of Zn with different leaching concentrations
4.1.3 浸出时间对锌浸出率的影响
浸出浓度为200 g·L-1, 初酸浓度为200 g·L-1的条件下, 在70, 80和90℃3种温度体系下, 考察了浸出时间在20~120 min范围变化, 对锌浸出率的影响。试验结果见图5。
结果显示, 在3种不同温度体系下锌的浸出率都是随着时间的增加而提高的。在90℃的温度体系下, 经过80 min的浸出, 锌的浸出率就可以达到91%以上, 再增加浸出时间, 锌的浸出率变化不明显;而在80℃的温度体系下, 80 min后锌的浸出率仅有87.25%, 经过120min的浸出, 锌的浸出率也可以达到91%以上;在70℃的温度体系下, 经过120 min的浸出, 锌的浸出率也仅有71.76%。随着浸出时间的增加, 铅银渣中的氧化铁被进一步的溶解, 浸出液中的Fe3+浓度提高, 并且少量的难以溶解的硫化锌溶解, 从而提高了锌的浸出率[21,22]。分析试验结果可知, 在相同的初始酸度条件下, 在较高的温度环境中, 较短的时间内锌的浸出率就可以达到最高值, 因此, 在酸性浸出锌的过程中, 选择90℃的温度体系下, 浸出80 min为宜。
4.2 氯化浸出铅银试验
4.2.1 氯化钠浓度对铅银浸出率的影响
在浸出时间90 min, 浸出温度80℃, 硫酸用量40g·L-1, 浸出浓度在250 g·L-1的条件下, 试验研究了氯化钠浓度在100~350 g·L-1范围内变化对铅银浸出结果的影响。试验结果见图6。
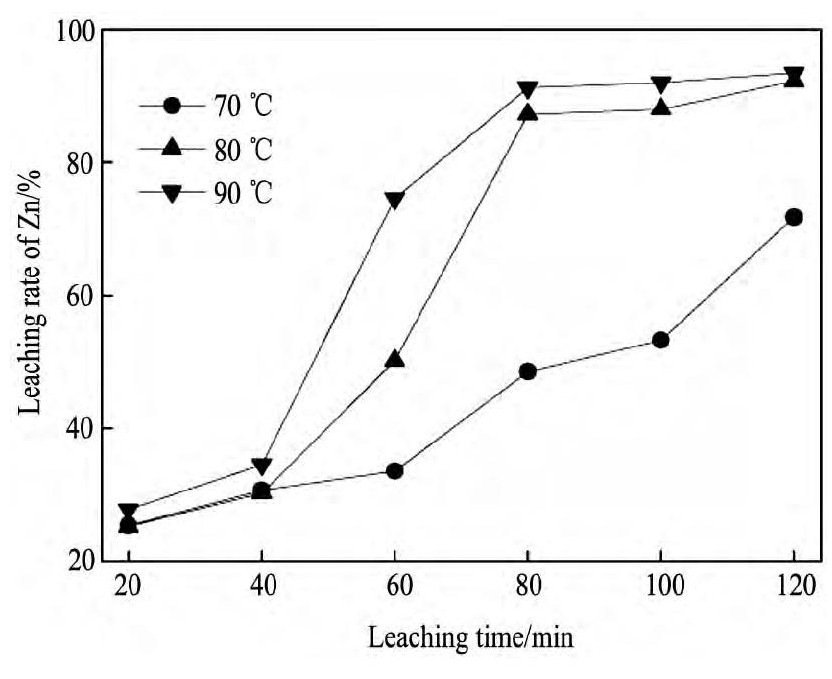
图5 浸出时间对锌浸出率的影响Fig.5 Leaching rate of Zn with different leaching time
从图6的试验结果可知, 氯化钠浓度对铅银浸出率影响十分显著。随着氯化钠浓度的增加, 铅银的浸出率都呈现持续增加的趋势, 当氯化钠浓度超过300 g·L-1时, 铅银的浸出率变化不再明显。由方程 (4) ~ (8) 可知, 溶液中氯离子的浓度, 决定了铅银的浸出率, 因此在溶液中较高的氯离子浓度是铅银高浸出率的前提[17,18]。因此选择氯化钠浓度以300 g·L-1为宜, 此时铅银的浸出率分别为90.22%和87.84%。
4.2.2 初酸浓度对铅银的浸出率影响
从铅银的浸出原理可以自, 在酸性条件下, 铅银可以很好地溶解于浸出体系中, 因此在浸出铅银时, 选择廉价易得氯化钠作为氯化浸出剂, 硫酸作为助浸剂。在浸出时间90 min, 浸出温度80℃, 氯化钠浓度为300 g·L-1, 浸出浓度在250 g·L-1的条件下, 试验研究了初酸浓度在0~100 g·L-1范围内变化对铅银浸出结果的影响。试验结果见图7。
结果表明, 当浸出体系中没有添加硫酸时, 铅银的浸出率都较低, 这主要是因为铅银在氯化浸出时, 都必须在酸性的环境中进行[18,19,20]。随硫酸添加量的增加, 铅锌的进率持续提高, 当初酸浓度达到60 g·L-1时, 铅银的浸出率分别达到92.25%和87.26%, 再提高初酸浓度, 铅银的浸出率变化不再明显。因此认为, 在氯化浸出时初酸浓度以60g·L-1为宜。
4.2.3 浸出浓度对铅银的浸出率影响
在浸出时间90 min, 浸出温度80℃, 氯化钠浓度为300g·L-1, 初酸浓度在60 g·t-1的条件下, 试验研究了浸出浓度在100~300 g·L-1范围内变化对铅银浸出结果的影响。试验结果表明在氯化浸出体系中, 低浸出浓度下更有利于铅银的浸出, 因此在氯化浸出铅银时, 浸出浓度以200 g·L-1为宜。
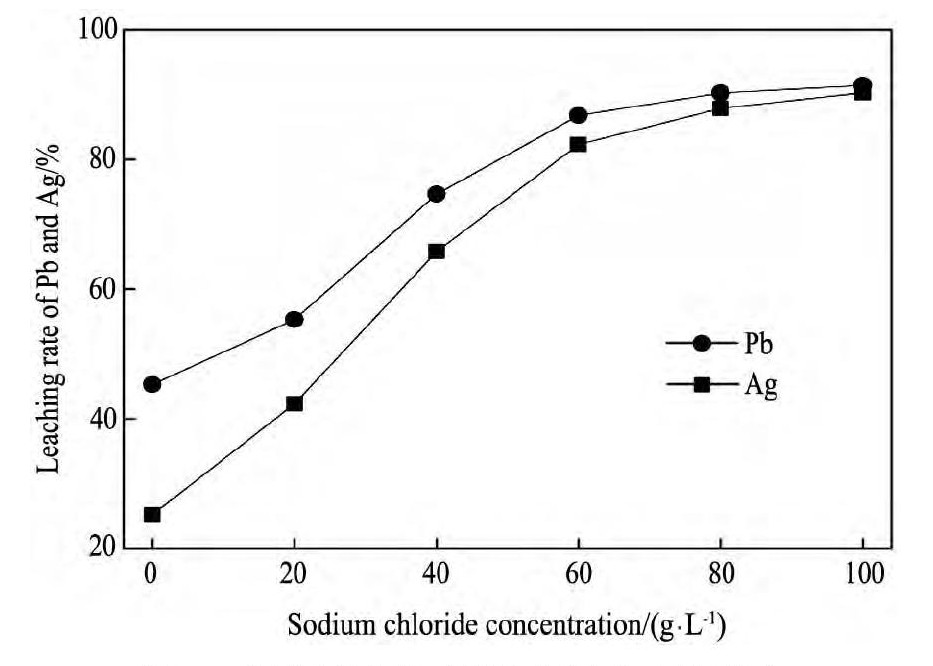
图6 氯化钠浓度对铅和银浸出率的影响Fig.6 Leaching rate of Pb and Ag with different sodium chlo-ride concentrations
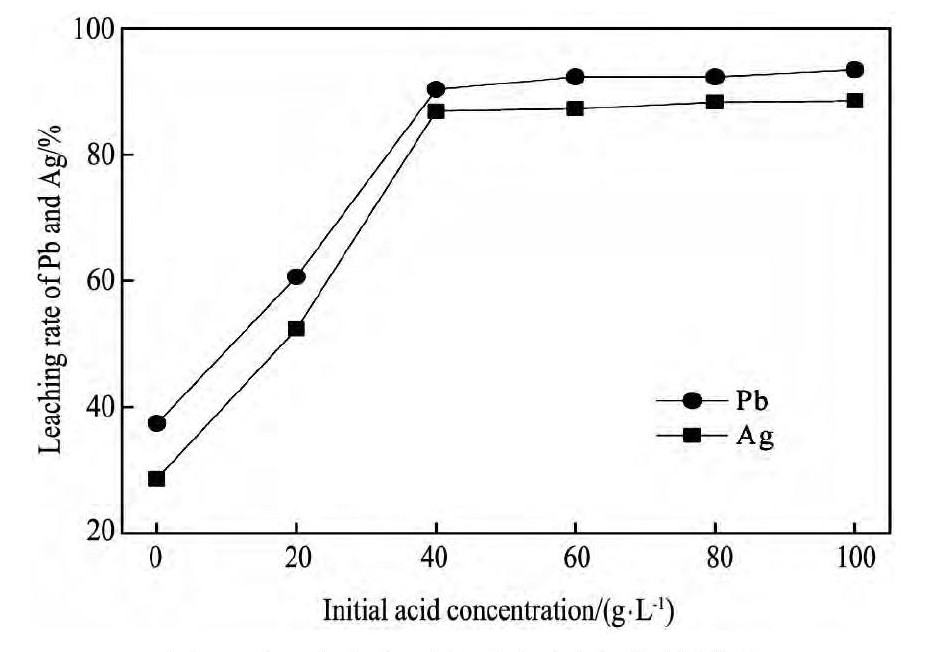
图7 初酸浓度对铅和银浸出率的影响Fig.7Leaching rate of Pb and Ag with different initial acid concentrations
4.2.4 浸出时间对铅银的浸出率影响
在浸出温度80℃, 氯化钠浓度为300 g·L-1, 初酸浓度在60 g·L-1, 浸出浓度200 g·L-1为的条件下, 试验研究了浸出时间在30~180 min范围内变化对铅银浸出结果的影响。试验结果表明在氯化浸出过程中, 铅的浸出率在90 min后浸出率已达到93.20%, 而银的浸出率在120 min后才达到最大值91.17%, 这主要是因为随着浸出时间的增加, 铅银渣中的含铁的矿物被溶解, 溶液中Fe3+浓度提高, 根据方程 (5) 和 (6) , Fe3+浓度更有利于银的浸出[14,21], 在氯化浸出时选择浸出时间为120 min为宜。
4.2.5 浸出温度对铅银的浸出率影响
在浸出时间120 min, 浸出浓度200 g·L-1, 氯化钠浓度为300 g·L-1, 初酸浓度在60 g·L-1的条件下, 试验研究了浸出温度在60~100℃范围内变化对铅银浸出结果的影响。试验结果见图8。
由图8的试验结果可知, 提高浸出温度更有利于银的浸出。随着浸出温度升高, 铅银的浸出率都呈上升趋势, 铅浸出率在80℃后变化不在明显;在温度达到90℃后银的浸出率变化才趋于缓和, 此时铅银的浸出率分别达到94.55%和93.23%。这是因为银离子与氯离子在溶液中形成银氯络合物的溶解度, 随着温度的升高而增加, 从而使银的浸出率增加[22]。综合考虑, 氯化浸出的温度以90℃为宜。
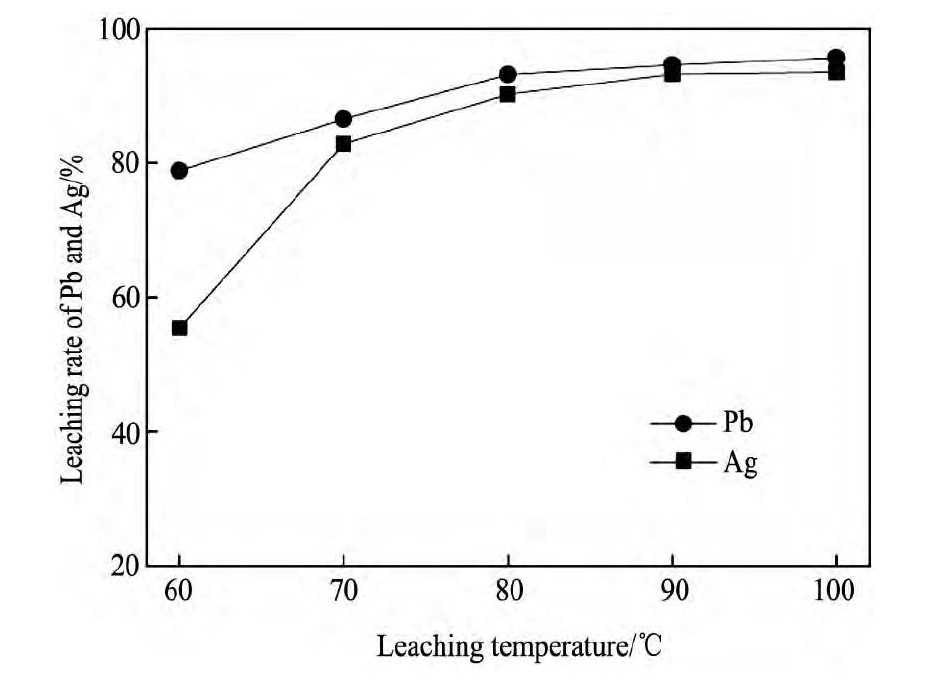
图8 浸出温度对铅和银浸出率的影响Fig.8 Leaching rate of Pb and Ag with different leaching tem-peratures
4.3 酸性浸出-氯化浸出验证试验
综合上述条件试验结果, 按照最佳工艺参数进行酸性浸出-氯化浸出验证试验, 取200铅银渣, 以浸出时间80 min, 浸出浓度200 g·L-1, 初酸浓度为200 g·L-1, 浸出温度90℃的条件下, 进行酸性浸出, 待浸出完成后过滤;将酸性浸出滤渣按照氯化钠浓度300 g·L-1, 浸出时间120 min, 浸出浓度200 g·L-1, 初酸浓度为60 g·L-1, 浸出温度90℃的条件下, 进行氯化浸出。酸性浸出-氯化浸出铅银渣数质量流程图见图9, 结果表明, 铅银渣经过酸性浸出-氯化浸出后锌、铅和银的浸出率分别为92.15%, 94.88%和93.24%, 尾渣产率为51.84%, 尾渣中含锌0.21%, 含铅0.46%, 含银38.50 g·t-1, 达到了综合回收利用铅银渣的目的。
5 结论
1.铅银渣含有较高的铅锌银, 通过铅锌银的浸出理论分析表明利用酸性浸出-氯化浸出的异步浸出工艺是可行的。
2.酸性浸出的较优工艺参数为浸出时间80 min, 浸出浓度200 g·L-1, 初酸浓度为200 g·L-1, 浸出温度90℃;氯化浸出较优工艺参数为氯化钠浓度300 g·L-1, 浸出时间120 min, 浸出浓度200 g·L-1, 初酸浓度60 g·L-1, 浸出温度90℃。
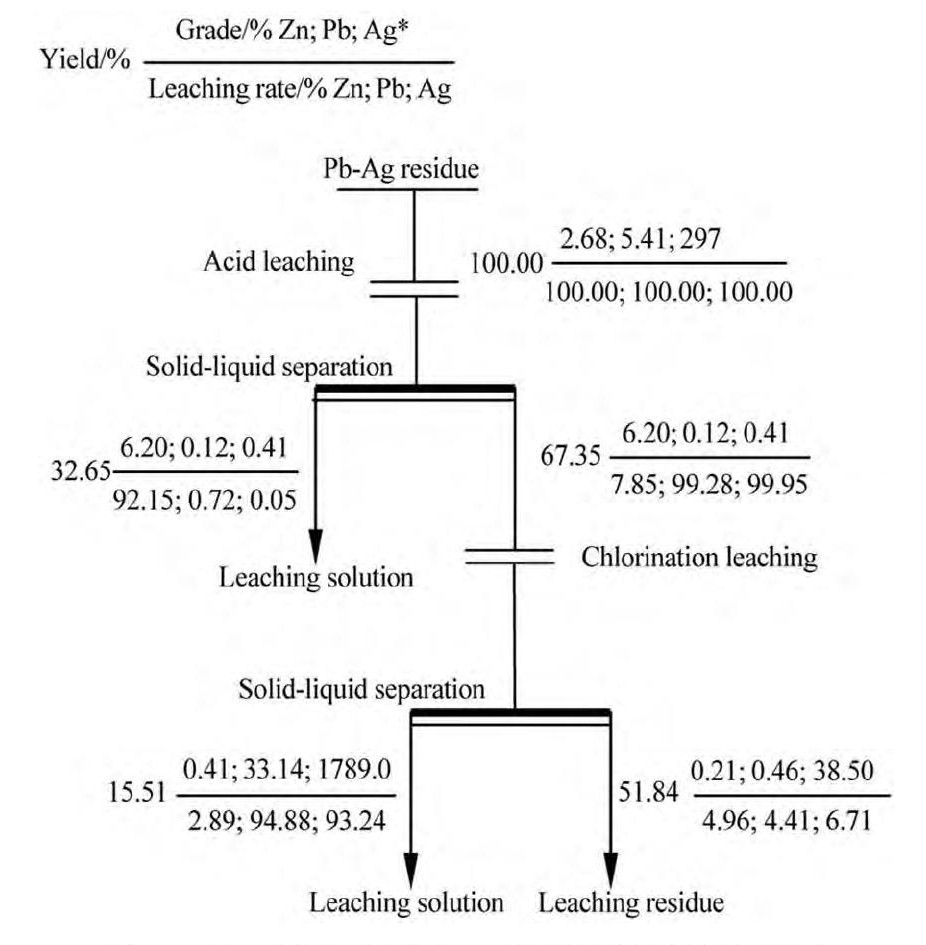
图9 酸性浸出-氯化浸出铅银渣数质量流程图Fig.9 Quantity-quality flow sheet of acid leaching-chlorination leaching on Pb-Ag residue
3.验证试验结果表明铅银渣经过酸性浸出-氯化浸出后尾渣产率为51.84%, 尾渣中含锌0.21%, 含铅0.46%, 含银38.50 g·t-1, 锌、铅和银的浸出率分别为92.15%, 94.88%和93.24%。
参考文献
[1] Antrekowitsch J.Hydrometallurgically recovering zinc from electric arc furnace dusts[J].Journal of Minerals, 2001, 53 (12) :26.
[2] Dutrizac J, Dinardo O.The co-precipitation of copper and zinc with lead jarosite[J].Hydrometallurgy, 1983, (11) :61.
[3] Luo W, Feng Q, Ou L, Zhang G, Chen Y.Kinetics of saprolitic laterite leaching by sulphuric acid at atmospheric pressure[J].Minerals Engineering, 2010, 23 (6) :458.
[4] Li C C, Xie F C, Ma Y, Cai T T, Li H Y, Huang Z Y, Yuan G Q.Multiple heavy metals extraction and recovery from hazardous electroplating sludge waste via ultrasonically enhanced two-stage acid leaching[J].Journal of Hazardous Materials, 2010, 178 (1) :823.
[5] Ozverdi A, Erdem M.Environmental risk assessment and stabilization/solidification of zinc extraction residue:I.Environmental risk assessment[J].Hydrometallurgy, 2010, 100 (3) :103.
[6] Li R G.Status and development of lead and zinc smelting process in China[J].China Nonferrous Metallurgy, 2012, 39 (6) :13. (李若贵.我国铅锌冶炼工艺现状及发展[J].中国有色冶金, 2012, 39 (6) :13)
[7] Liu H P.Processing technology overview zinc leaching slag[J].Yunnan Metallurgy, 2009, 38 (4) :34. (刘红萍.锌浸出渣处理工艺概述[J].云南冶金, 2009, 38 (4) :34.)
[8] Nagib S, Inoue K.Recovery of lead and zinc from fly ash generated from municipal incineration plants by means of acid and/or alkaline leaching[J].Hydrometallurgy, 2000, 56 (3) :269.
[9] Turan M D, Altundogan H S, Tümen F.Recovery of zinc and lead from zinc plant residue[J].Hydrometallurgy, 2004, 75 (1) :169.
[10] Julian M Steer, Anthony J Griffiths.Investigation of carboxylic acids and non-aqueous solvents for the selective leaching of zinc from blast furnace dust slurry[J].Hydrometallurgy, 2013, 140:34.
[12] Turan M D, Altundogan H S, Tümen F.Recovery of zinc and lead from zinc plant residue[J].Hydrometallurgy, 2004, 75 (1) :169.
[13] Leclerc N, Meux, Lecuire J M.Hydrometallurgical extraction of zinc ferrites[J].Hydrometallurgy, 2003, 70 (1-3) :175.
[14] Dutrizac J E.The leaching of silver sulfide in ferric ion media[J].Hydrometallurgy, 1994, (35) :275.
[15] A.Rusen A S, Sunkar Y A.Topkaya.Zinc and lead extraction frominkur leach residues by using hydrometallurgical method[J].Hydrometallurgy, 2008, (93) :45.
[16] Peng H L.Study on the behavior of zinc ferrite in conventional hydrometallurgical zinc production process[J].Hunan Nonferrous Metals, 2004, 20 (5) :20. (彭海良.常湿法炼锌中铁酸锌的行为研究[J].湖南有色金属, 2004, 20 (5) :20.)
[17] Zheng C Q, Deng S H, Zhang Z, Peng S F.A leaching mathematical model of zinc residue using Fe Cl3brine[J].Journal of Chendu University of Science and Technology, 1993, 68 (1) :8. (郑昌琼, 邓淑华, 张昭, 彭少方.氯盐法浸出锌渣的溶液化学模型[J].成都科技大学学报, 1993, 68 (1) :8.)
[18] Jin C S, Zhang Y A, Mou W Z, Zheng D L, Zeng Y, Jiang X L.Thermo-dynamics of gold chlorination leaching process[J].Chinese Journal of Rare Metals, 2012, 36 (1) :129. (金创石, 张廷安, 牟望重, 郑大录, 曾勇, 蒋孝丽.液氯化法浸金过程热力学[J].稀有金属, 2012, 36 (1) :129.)
[19] Luo W, Feng Q M, Ou L M, Zhang G F, Chen Y.Kinetics of saprolitic laterite leaching by sulphuric acid at atmospheric pressure[J].Minerals Engineering, 2010, 23 (6) :458.
[20] Turan M D, Altundogan H S, Tümen F.Recovery of zinc and lead from zinc plant residue[J].Hydrometallurgy, 2004, 75 (1) :169.
[21] Lu Y H, Shui C J.Leaching Ag2S with chlordes[J].Precious Metals, 1998, 19 (2) :23. (陆跃华, 水承静.硫化银的氯盐浸出[J].贵金属, 1998, 19 (2) :23.)
[22] Zhang Y H, Li Y, Ji T T, Shi W, Zhou C.Research on silver leaching with persulfate oxidation-chlorde salt[J].Metal Mine, 2011, 417 (3) :78. (张亚辉, 李妍, 季婷婷, 施维, 周超.过硫酸盐氧化-氯盐浸银研究[J].金属矿山, 2011, 417 (3) :78.)