
Similar extrusion and mapping optimization of die cavity modeling for special-shaped products
QI Hong-yuan(齐红元), WANG Shuang-xin(王爽心), ZHU Heng-jun(朱衡君)
School of Mechanical and Electric Control Engineering, Beijing Jiaotong University, Beijing 100044, China
Received 8 October 2005; accepted 25 March 2006
Abstract:Aimed at the modeling issues in design and quick processing of extruding die for special-shaped products, with the help of Conformal Mapping theory, Conformal Mapping function is determined by the given method of numerical trigonometric interpolation. Three-dimensional forming problems are transformed into two-dimensional problems, and mathematical model of die cavity surface is established based on different kinds of vertical curve, as well as the mathematical model of plastic flow in extruding deformation of special-shaped products gets completed. By upper bound method, both vertical curves of die cavity and its parameters are optimized. Combining the optimized model with the latest NC technology, NC Program of die cavity and its CAM can be realized. Taking the similar extrusion of square-shaped products with arc radius as instance, both metal plastic similar extrusion and die cavity optimization are carried out.
Key words: extrusion; Conformal Mapping; forming; die cavity; special-shaped products
1 Introduction
For special-shaped products, similar extrusion is defined as the extruding deformation process which can make geometrical profile of metal arbitrary cross-section in deforming region be mutually similar to that of its original billet. During the metal forming, similar extrusion becomes non-axis-symmetrical three- dimensional problem due to the existence of tangent plastic flow, can not be simply described by two- dimensional theorem[1, 2]. In addition, on account of the difficulties in mathematics, related analysis was rarely reported, and no generalized expression of three- dimensional analysis exists[3, 4]. Consequently, not only similar extruding analysis but also its quick die processing was rarely achieved.
At present, with the help of Conformal Mapping theory, only using given mapping function to convert typical region into simple region[5, 6], some engineering problems can be solved. Conformal Mapping theory has been applied in mechanical vibration[7], electro- magnetics[8], hydromechanics[9] and plastic processing fields[10]. Analyzing the vibration of simple-supported plates with concentrated mass, the complicated plates region and its vibrating function can be described by unit dish region, then, its fundamental frequency can be determined[11].
In this paper, with the help of Conformal Mapping theory, applying numerical trigonometric interpolation approach, the mapping analysis function transforming irregular non-axis-symmetry cross-section into unit dish region is built up. Thus, the plastic flow of similar extrusion is translated into two-dimensional problem, then three-dimensional plastic flow gets analyzed. After the comparison among three popular vertical curves of die cavity, namely straight linetype, cubic-streamline linetype and convex linetype, both mathematical models of similar extrusion and optimal die cavity are generated. Consequently, the technical target of precise as well as quick CAD/CAM of die cavity surface can be achieved. Furthermore, taking the similar extrusion of square-shaped products with arc radius r as instance, its plastic flow field, die cavity modeling and parameters optimization are analyzed respectively.
2 Comformal Mapping of complicated region
By Conformal Mapping theory[12, 13], complicated region in Fig.1(b) can be mapped into unit dish region in Fig.1(a), mapping function of complex polynomial on complicated geometrical region can be described as
(
) (1)
In Eqn.(1), polynomial cn=an+ibn is complex coefficient, mapping function W should satisfy the following boundary conditions:
(2)
By Eqn.(2), Eqn.(1) can be described by complex trigonometric function as follows:
(3)
where ρ, θ are module and phase of arbitrary vector in Fig.1(a).
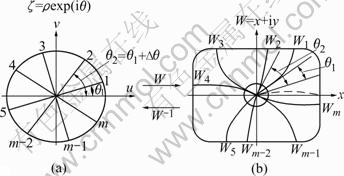
Fig.1 Conformal Mapping between complicated region and unit dish
As shown in Fig.1, suppose boundary points Wk=xk+iyk of complicated region W are interpolation points k∈N (positive integer), and xk and yk are real part value and imaginary value of Wk separately. By Conformal Mapping function W, mapping points of complex vector W1,W2, …,Wm are 1, 2, …, m respectively as shown in Fig.1(a). Assuming that the phasesθk∈[0, 2π] of complex vectors 1, 2, …, m are arithmetical progression, putting them into Eqn.(3), coordinate points value of interpolation points W1, W2, …, Wm can be obtained:
(4)
When m is large enough, the infinite interpolation points in Eqn.(3) can be replaced by finite interpolation points. From the orthogonal character of trigonometric function, the values of real part an and imaginary part bn of complex coefficients cn in progression function of item m∈N can be expressed as
(5)
In Eqn.(4), interpolation points W1,W2,…,Wm are unknown value satisfying boundary mapping conditions. They can be defined as odd interpolation points when not satisfying precision requirements. Adding new interpolation points between odd interpolation points, namely even points, then doing mutual iterative calculation between odd and even points, the interpolation points value and cn can be calculated under the condition of satisfying precision requirements. The above process determining Conformal Mapping function is named as trigonometric interpolation method.
3 Similar extrusion modeling
By Conformal Mapping theory, as shown in Fig.2(a), the geometrical profile on the cross-section of square- shaped billet(z=0 in Fig.3) can be described by Eqn.(3), we can get
It can map the cross-section region into unit dish region.
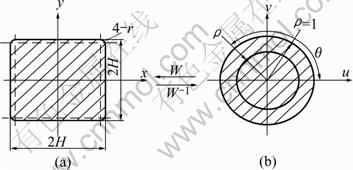
Fig.2 Conformal Mapping between square-shaped section and unit dish region
Fig.3(a) is the deforming body sketch of similar extrusion, which can be mapped into axis-symmetrical model (Fig.3(b)). As shown in Fig.3(a), taking the center of billet as origin to set up Cartesian coordinate system (x, y, z), the three-dimension analysis of deforming region function can be written as
(6)
As shown in Fig.3, Si is the cross-section area of square-shaped billet at die cavity inlet, and its profile arc radius is r.
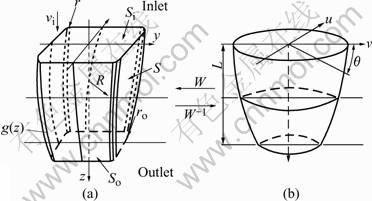
Fig.3 Mapping of square-shaped deforming region
Over plastic forming, the square-shaped products whose cross-section area So and arc radius ro are similar to the billet can be obtained. Suppose that the length of deforming region is L, and the linear ratio between Si and So is
,
in Eqn.(6) is the vertical interpolation function of die cavity. By the similar relationship between billet and product, arc radius ro can be gotten:
(7)
When ρ=1, Eqn.(6) becomes the parameter function of die cavity surface S(θ, ρ, z). Hence, die cavity modeling of similar extrusion can be carried out by the application of Conformal Mapping theory.
4 Vertical curve function g(z) of die cavity
Vertical function g(z) of die cavity is important in determining metal plastic flow field, die cavity modeling, and optimizing the length L of deforming region. In Fig.3, the geometrical boundary condition, which g(z) selects to satisfy the die cavity, is that the cross-section profiles at the inlet and the outlet should be the billet outer profiles and product outer profiles separately, namely
(8)
When die cavity belongs to linear linetype, the vertical curve function is
(9)
If the die cavity belongs to convex linetype, the vertical curve function becomes
(10)
When the die cavity belongs to cubic-streamline linetype, the vertical curve function should be
g(z)=Az3+Bz2+Cz+D
and this function should satisfy not only geometrical boundary conditions in Eqn.(8), but also the plastic flow conditions at the inlet and outlet of die cavity below:
(11)
Therefore
(12)
If
is obtained and united with Eqn.(6), the parameter function of three-dimensional die cavity surface can be described. Combining W with proportional mapping, the die cavity modeling of large compressing ratio extrusion can be achieved.
5 Plastic flow field of similar extrusion
It is assumed that the similar extrusion belongs to three-dimensional stable plastic flow field, in addition, as shown in Fig.3, we suppose that flow velocity vz along z-axis direction is even distribution on the arbitrary cross-section perpendicular to z-axis, thus, vz can be obtained from the character of flow pipe as follows:
(13)
where Sz is arbitrary cross-section area in deforming region; vi is axial direction velocity at the inlet of die.
Known from the stream function theory of metal plastic deformation, two three-dimensional plastic stream surface functions can be set up when ρ and θ in Eqn.(6) are constant. By total differential to both functions, velocity field of similar extrusion can be calculated:
(14)
Then, strain velocity field can be given from Eqn.(13) and Eqn.(14)[14] as follows:
(15)
6 Power and die cavity optimization
Both die cavity surface and plastic body function Eqn.(6) are defined by cn and L. The optimized die parameter L can be calculated from the upper bound method of plastic deformation, the general power dissipation function is
J*=Wi+W+Wf (16)
Metal deforming power dissipation Wi in deforming region is
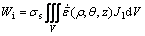
where
is equivalent strain ratio; σs is metal plastic yield stress; and V is metal’s volume in deforming region.
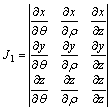
Power dissipation on the metal shearing section Si and So can be written as

where
are discontinuity velocity on sections Si and So respectively. Jacobi’s transformations of area differential unit on Si and So can be given by
Assuming m is the friction factor between metal and die, then power dissipation due to friction on the surface S is
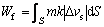
where ΔvS is tangent velocity between metal and die cavity surface S, then the transformations of area differential unit on the surface S is
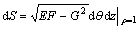
Here 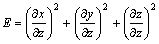
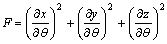

Now bringing velocity field of similar extrusion Eqn.(13), Eqn.(14) and strain velocity field Eqn.(15) into Eqn.(16), the general power dissipation can be described by
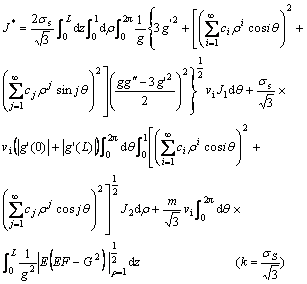
Suppose
(17)
where P is relative pressure ratio.
By the upper bound method, asking P for extremum to optimize parameter L, metal deforming velocity field, strain field and optimized parameter L can be obtained respectively.
7 Example
In Fig.2, square-shaped cross-section area is 2H×2H, geometrical center is (0, 0), arc radius is r, arc center is (a, b), then, geometrical boundary condition in the first quadrant can be given by
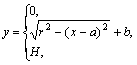
By numerical trigonometric interpolation method of Conformal Mapping, (accuracy of cn can be computed by normal convergence method[15], in this case, 32 interpolating points represent the infinite points of Eqn.(1) in the first quadrant), cn can be calculated as follows:
c2v+1=0.0, 1.076 649, 0.000 001, -0.102 780, -0.000 001, 0.038 262, 0.000 001, -0.018 425, -0.000 000, 0.009 608, 0.000 000, -0.005 148, -0.000 000, 0.002 991, -0.000 000, -0.002 930, 0.000 001
c2v=0 (v=1, 2, 3, ···, 16)
Both the similar extruding region function of square-shaped products and the function of die cavity can be given by bringing cn into Eqn.(6). General power function can be obtained from Eqns.(9)-(15) and (17), thus, under the same m and λ conditions, the optimized parameter L of die cavity with different arc radius r can be obtained.
As shown in Fig.4, the vertical curve function g(z) can be expressed by Eqn.(12) , when λ=0.85 and friction factor m=0.5, the optimized parameter L/H of die can be obtained by visual C++ program. Here, the optimized point L/H on each curve corresponds to the minimum point of curve P. Such as r=0.3 is corresponding to die optimized parameter L/H =1.52.
Under the same m and λ conditions, die optimized parameter L/H will change since arc radius r of billet is different. The optimized parameters are L/H=1.47 and L/H=1.42 corresponding to curves r=0.4 and r=0.5 separately. By analyzing general power dissipation, it can be concluded that, when arc radius becomes smaller, relative pressure ratio P will increase, and the die parameter L also tends to increase.
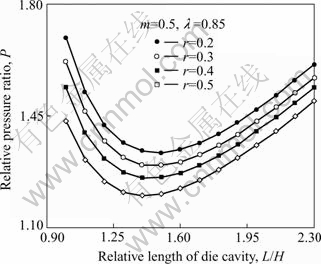
Fig.4 Optimized parameter L vs r
Over optimizing the die cavity of square-shaped similar extrusion, as shown in Figs.5(a) and (b), CAD drawing of cavity can be depicted separately when r=0.3 and r=0.5 under the conditions of m=0.5 and λ=0.85 by Eqn.(6). Combining die cavity surface function with the latest NC technology, both NC program of die cavity and its CAM[15] can be realized.
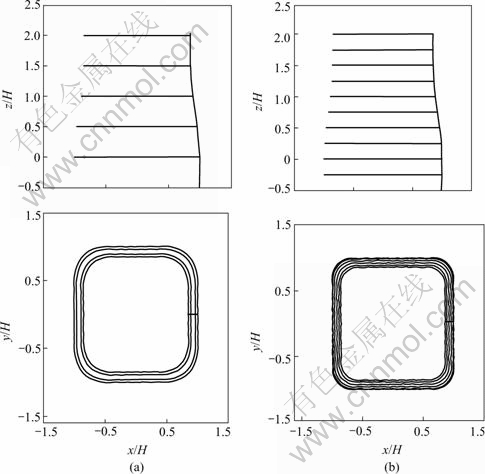
Fig.5 Optimized die cavities: (a) r=0.5; (b) r=0.3
Under the conditions λ=0.56 and m=0.30, three types of vertical curve of die cavity, namely straight linetype, cubic-streamline and convex, are compared. As shown in Fig.6, vertical curve is convex corresponding to the die parameters L/H=13.1, straight linetype corresponding to L/H=14.2, and cubic-streamline corresponding to L/H =17.2. The power dissipation shows decrease tendency, and optimized parameter L tends to increase due to the vertical curves changing from convex to linear and to cubic-streamline. It is demonstrated that material plastic flow is the flattest in cubic-streamline die. Thus, cubic-streamline die should be the first choice in ensuring the quality of extruding products under the available die cavity processing technology. By power analysis, it can be concluded that die cavity whose vertical curve is straight linetype is more optimal than that of convex.
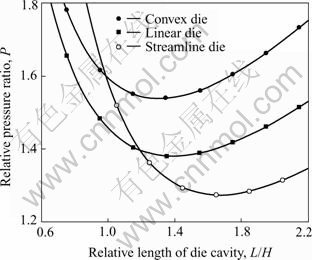
Fig.6 Optimized curve of die’s parameter L varying with vertical curve linetypes
8 Conclusions
1) By Conformal Mapping theory and numerical trigonometric interpolation methods, both the similar extrusion and mathematical model of die cavity surface are generated for special-shaped products.
2) Die cavity with three kinds of vertical curves are optimized by the upper bound method.
References
[1] KEUN K. An upper bound solution of tube drawing [J]. Journal of Materials Processing Technology, 1997, 63: 43-48.
[2] NAGPAL V. A simplified analysis of the lubricated shape extrusion [A]. Proceeding of 6th North American Manufacturing Research Conference NAMRC [C]. USA, 1978. 172-179.
[3] CHITKARA N R. Application of an upper bound method to off-centric extrusion of square section, analysis and experiments [J]. International Journal of Mechanical Sciences, 2000, 42: 321-344.
[4] CHO N S. Yang. Analysis of hydrofilm extrusion of elliptic shapes using perturbation method [J]. International Journal of Mechanical Sciences, 1984, 26(1): 1-19.
[5] TEPPATI V. Conformal-mapping design tools for coaxial couplers with complex cross section [J]. IEEE Transactions on Microwave Theory and Techniques, 2002, 50(10): 2339-2345.
[6] AMATORE C. Simulation of the double hemicylinder generator-collector assembly through conformal mapping technique [J]. Journal of Electroanalytical Chemistry, 2003, 553(Suppl): 49-61.
[7] RAJALINGHAM C. Axi-symmetric vibration of circular plates and its analog in elliptical plates using characteristic orthogonal polynomials [J]. Journal of sound and vibration, 1993, 161: 109-118.
[8] ZOU Ji-bin. Magnetic Circuit and Magnetic Field [M]. Harbin: Harbin Institute of Technology Press, 1998. 32-40.
[9] WU Guo-chuan. Tandem Blade Cascade [M]. Beijing: National Defence Industry Press, 1996. 83.
[10] QI Hong-yuan ZHU Heng-jun. Conformal mapping modeling of metal plastic deformation and die cavity in special-shaped extrusion [J]. Trans Nonferrous Met Soc China, 2002, 12(5): 858-861.
[11] QI Hong-yuan. Conformal analysis of fundamental frequency of vibration of simple-supported elastic ellipse-plates with concentrated substance [J]. Journal of Central South University of Technology, 2005, 12(Suppl.2): 269-273.
[12] WEN Guo-chun. Conformal Mapping and Boundary Problem [M]. Beijing: Higher Education Press, 1985.
[13] YAVUZ N. Conformal Field Theory [M]. Cambridge Massachusetts Perseus Pub, 2000.
[14] ZHAO Zhi-ye. Theory Basis of Metal Stress Process [M]. Beijing: Metallurgical Industry Press, 1989.
[15] QI Hong-yuan, ZHU Heng-jun. Chinese Postdoctoral Science Foundation ed. Proceeding of Chinese Postdoctoral Academic Conference[C]. Beijing: Science Press, 2001. 484-488.
Corresponding author: QI Hong-yuan; Tel: +86-13611009942; E-mail: qhy@jdxy.njtu.edu.cn
(Edited by PENG Chao-qun)