
Preparation of MgO whisker from magnesite tailings and its application
WANG Nan1, CHEN Min1, LI Yue-yuan1, NI Hong-wei2
1. School of Materials and Metallurgy, Northeastern University, Shenyang 110819, China;
2. Key Laboratory for Ferrous Metallurgy and Resources Utilization of Ministry of Education,
Wuhan University of Science and Technology, Wuhan 430081, China
Received 30 October 2010; accepted 27 May 2011
Abstract: Magnesium carbonate whisker as precursor was prepared from the low-grade magnesite tailings by the route of calcination, hydration, carbonation and thermal decomposition, and then MgO whisker was prepared by calcining the precursor. In addition, the effect of MgO whisker addition on sintering and thermal shock resistance of refractory was also investigated. The results show that the thermal decomposition product is MgCO3·3H2O and its morphology is remarkably influenced by the types of additives, and magnesium carbonate whisker with the length of 10-60 μm and length-diameter ratio of 10-20 is successfully prepared when a type of soluble magnesium salt is added. MgO whisker with the length of 10-40 μm is derived from precursor with the heating rate of 1 °C/min. The thermal shock resistance of refractory is significantly improved by the addition of MgO whisker due to its effect on binding and preventing crack expanding, and the proper amount of whisker addition is around 3%.
Key words: MgO whisker; precursor; magnesium carbonate whisker; refractory; thermal shock resistance
1 Introduction
China is abundant in magnesite resource which is also used as important raw materials for the production of basic refractories applied in the metallurgical industries. As for the mining and utilization of magnesite, the utilization ratio of low-grade magnesite tailing is low in China, which not only limits the effective and comprehensive utilization of magnesite resource, but also causes land occupation and environmental issues. In addition, most magnesite resources are mainly used for the production of magnesia refractory with low value-added products. Therefore, much more effective utilization of magnesite resource and the development of high value-added products are generally preferred [1-2].
As one of the high value-added products, MgO whisker is usually prepared by calcination of magnesium carbonate whisker [3-6], and the magnesium carbonate whisker is often prepared by co-precipitation technology through the reaction of soluble magnesium salts with carbonate salts in water solution [7-10]. For example, magnesium carbonate whisker could be prepared through the reaction of MgCl2 with (NH4)2CO3 in water solution, but the generated by-product of NH4Cl causes unavoidable environmental impact. Therefore, considering the development of low-cost and environmentally friendly technology, magnesium carbonate whisker was prepared by a novel method using magnesite tailings as starting materials, and further MgO whisker was prepared by using the prepared magnesium carbonate whisker as precursor. In addition, the effect of MgO whisker addition on the sintering and thermal shock resistance of MgO refractory was also investigated.
2 Experimental
2.1 Materials
The starting materials were the magnesite tailings from Dashiqiao of Liaoning province (particle size<40 mm), with MgO content of 46.56% (mass fraction). Reagent grade potassium dihydrogen phosphate (KH2PO4) and ammonium carbonate((NH4)2CO3), and a type of soluble magnesium salt were used as additives for preparation of magnesium carbonate whisker during thermal decomposition process. The light magnesium carbonate was used for preparation of MgO clinker.
2.2 Experimental procedures
Magnesite tailings, with chemical composition shown in Table 1, were firstly fired at 850 °C to obtain light burnt MgO, then mixed with water under stirring and CO2 gas bubbling to realize hydration and carbonation. Consequently, magnesium bicarbonate (Mg(HCO3)2) solution was obtained after resting and filtration. Then Mg(HCO3)2 solution was heated at 40-80 °C with stirring and different types of additives added. After filtration, the obtained precipitation product was dried at 120 °C for 24 h to get magnesium carbonate whiskers. The chemical composition of the prepared magnesium carbonate whisker was evaluated by fluorometric analysis and thermal gravity analysis (TGA), and the phase composition was characterized by X-ray diffraction (XRD). The morphology of the prepared magnesium carbonate whisker was observed by scanning electron microscopy (SEM).
Then the prepared magnesium carbonate whisker was calcinated under 600 °C for 2 h to get MgO whisker, and the sintering property and thermal shock resistance of MgO refractory with addition of the prepared MgO whisker were investigated. The apparent porosity of the refractory was measured by immersion method in kerosene under vacuum using Archimedes’ way, and the thermal shock resistance was evaluated by counting the cycling times of the sintered MgO body by repeatedly soaking the sample at 1 300 °C and then quenching on water cooled steel plate until the sample ruptured.
Table 1 Chemical composition of magnesite (mass fraction, %)
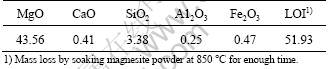
3 Results and discussion
3.1 Composition and morphology of thermal decomposition products
Figure 1 shows the XRD pattern of precipitated precursor after heating magnesium bicarbonate solution at 50 °C. It can be found that the obtained powder was well crystallized. By chemical and TGA analyses, it is known that the obtained precursor was MgCO3?3H2O. Chemical analysis of the prepared powder after heating at 850 °C showed that the content of MgCO3 was more than 99.6%, indicating that the obtained product has a high purity due to the effective separation of magnesium bicarbonate solution from gangue and other insoluble components in the magnesite tailings. Thus, it is considered that the present method for the preparation of MgCO3?3H2O powder can achieve an effective utilization of low-grade magnesite tailings. In addition, the filter cake after carbonation and solid-liquid separation could be reused for the hydration and carbonation processes, which is favorable to promote the yield ratio of magnesite.
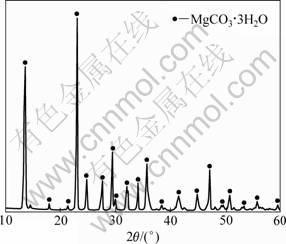
Fig. 1 XRD pattern of thermal decomposition product
Figure 2 shows the SEM images of the MgCO3·3H2O crystals with different types of additives. Without any addition, the mixtures of flaky and rod-like MgCO3·3H2O crystals were obtained, with the length of 15 μm. When potassium dihydrogen phosphate was added, petal shaped MgCO3·3H2O crystals were formed. Spherical magnesium carbonated ones were obtained with the addition of ammonium carbonate. While soluble magnesium salt was added, MgCO3·3H2O whiskers with the length of 20-60 μm and aspect ratio of 10-20 were obtained. According to the previous studies, it is known that the crystal formation in solution were dependent on the pH value and supersaturation degree [11-13]. When different types of additives were added in the present work, the pH values of the solution were changed to different levels, as shown in Fig. 3. Thus, it is considered that the influence of different types of additives on morphology of the precursor in the present work is due to their effects on pH value and solubility of Mg(HCO3)2, and proper precipitation conditions were obtained when the soluble magnesium salt was added.
3.2 Effect of heating rate on morphology of MgO whisker
Figure 4 indicates the morphology of MgO derived from calcination of precursor. It is observed that the MgCO3·3H2O whisker had pulverized when the heating rate was 5 °C/min. This is considered that the whisker precursor could not keep its original morphology for shrinkage during calcination process at a rapid heating rate. While the temperature was elevated at a lower heating rate (1 °C/min), the decomposition reaction of magnesium carbonate whisker was conducted at a lower rate which contributed to the transformation from magnesium carbonate whisker to magnesia whisker, and the maintenance of the one-dimensional morphology of MgCO3·3H2O whisker. As a result, magnesia whisker with the length of 10-40 μm was obtained.
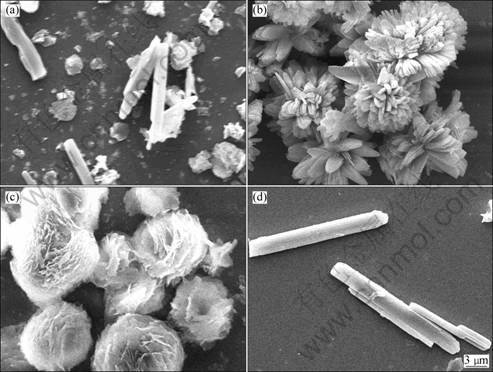
Fig. 2 Effects of additive types on crystal morphology: (a) Without additive; (b) KH2PO4; (c) (NH4)2CO3; (d) Soluble magnesium salt
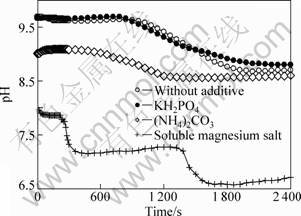
Fig. 3 Effect of additive types on pH values of solutions
3.3 Effect of MgO whisker addition on sintering and thermal shock resistance
Figure 5 shows the effect of MgO whisker addition on the densification of MgO clinker fired at 1 600 °C. It is observed that the small amount addition of whisker slightly increased the apparent porosities. It was 4.7% for the sample without addition, and increased to 5.7% while 1% MgO whisker was added, and further addition from 3% to 5% had little more effect. The influence of whisker addition on porosity is considered due to the effect of the whisker on restraining the movement of MgO grain boundaries during sintering process [14].
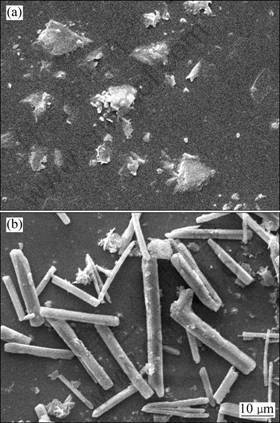
Fig. 4 SEM images of calcined products at different heating rates: (a) 5 °C/min; (b) 1 °C/min
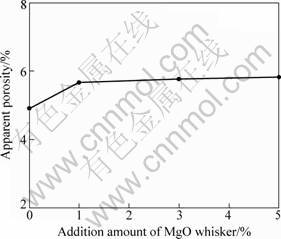
Fig. 5 Change of apparent porosity of MgO clinker with MgO whisker addition
Figure 6 shows the effect of whisker addition on the cycling time of thermal shock resistance of MgO clinker. It is observed that the thermal shock resistance of refractory was significantly improved by the addition of magnesia whisker. With addition of 3% MgO whisker, the thermal shock resistance time was significantly increased from 11 to 18 s. According to the fatigue fracture mechanism of bristle materials, the thermal shock resistance was influenced by the compactness, particle shape and microstructure [15-16]. In the present study, it is considered that the improvement of thermal shock resistance of the refractory was not for the slight decrease of compactness, but due to the effect of MgO whisker on binding and preventing of crack expanding. Less effect with further 5% addition is considered due to the poor dispersion effect of the whiskers. Therefore, it is considered that the proper amount of whisker addition should be around 3%.
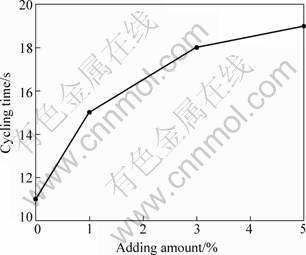
Fig. 6 Effect of whisker addition amount on thermal shock cycling time of MgO clinker
4 Conclusions
1) MgO whisker with the length of 10-40 μm was prepared by the route of hydration and carbonation- thermal decomposition-second calcination by using magnesite tailings as starting material.
2) Addition of MgO whisker slightly influences the densification of MgO clinker owing to the effect on hindering MgO growth.
3) The thermal shock resistance of refractory is significantly improved by the addition of MgO whisker due to its effect on binding and preventing crack expanding. When 3% MgO whiskers are added, the thermal shock resistance is significantly improved, but further increment of addition shows less effect due to the poor dispersion effect, and thus the proper amount of whisker addition is considered to be around 3%.
References
[1] ZHANG Xin-ye. Ways of improving utilization level of magnesite resource in China [J]. Conservation and Utilization of Mineral Resources, 2008(4): 23-25. (in Chinese)
[2] ZHANG Guo-dong, YUAN Zheng-he, YOU Jie-gang. Developing strategy of magnesite and magnesia-based refractories industry of Liaoning province [J]. Refractories, 2008, 42(3): 219-222. (in Chinese)
[3] WANG X L, XUE D F. Direct observation of the shape evolution of MgO whiskers
in a solution system [J]. Materials Letters, 2006, 60(9): 3160-3164.
[4] KIM B M, CHO Y K, YOON S Y, STEVEN R, PARK H C. Mullite whiskers derived from kaolin [J]. Ceramics International, 2009, 35(2): 579-583.
[5] ZHANG Li-li, LIU Jia-xiang, LI Min. Effect of different pyrogenation conditions on crystal morphology of basic magnesium carbonate [J]. Journal of the Chinese Ceramic Society, 2008, 36(9): 1310-1314. (in Chinese)
[6] HAHN R, BRUNNER J G, KUNZE J, SCHMUKI P, VIRTANEN S. A novel approach for the formation of Mg(OH)2/MgO nanowhiskers on magnesium: Rapid anodization in chloride containing solutions [J]. Electrochemistry Communications, 2008, 10(2): 288-292.
[7] KLOPROGGE J T, MARTENS W N, NOTHDURET L, DUONG L V, WEBB G E. Low temperature synthesis and characterization of nesquehonite [J]. Journal of Materials Science Letters, 2003, 22(11): 825-829.
[8] HE Y L, WANG J K, DENG H Y, YIN Q X, GONG J B. Comparison of different methods to prepare MgO whiskers [J]. Ceramics International, 2008, 34(6): 1399-1403.
[9] CHEN Rui, LUO Kang-bi, LI Hu-ping, TAN Yan-xia. Application of whiskers in the materials [J]. Science & Technology in Chemical Industry, 2007, 15(6): 58-61. (in Chinese)
[10] LI Jun, YANG Bin, WANG Jin-xiang, ZHONG Xiang-chong. Sintering behavior, microstructure and mechanical properties of MgO-ZrO2 materials [J]. Refractories, 1996, 30(2): 69-73. (in Chinese)
[11] YOSHIO O, SABURO I, TETSUSHI I, TOSHIHIRO K, YOSHIHIRO A. Preparation condition for aragonite whisker by carbonation process [J]. Journal of the Ceramic Society of Japan, 1996, 104(3): 196-200.
[12] GUO Jin-huo, HAN Yue-xin. Study on crystallization process of calcium carbonate whiskers [J]. Mining and Metallurgical Engineering, 1999, 19(4): 58-60. (in Chinese)
[13] OTA Y, INUI S, IWASHITA T, KASUGA T, ABE Y. Preparation conditions for aragonite whiskers by carbonation process [J]. Journal of the Ceramic Society of Japan, 1996, 104(3): 196-200.
[14] CHEN M, WANG N, YU J K, YAMAGUCHI A. Preparation of slaking resistant CaO aggregate from lightweight CaCO3 with oxide addition [J]. Materials letters, 2007, 61(1): 45-49.
[15] ROSSI R C, COST J R, JANOWSKI K R. Influence of the shape of dispersed particles on the elastic behavior of composite materials [J]. Journal of the American Ceramic Society, 1972, 55(5): 234-237.
[16] HASSLEMAN D P H, ZDANIEWSKI W A. Thermal stress resistance parameters for brittle materials subjected to thermal stress fatigue [J]. Journal of the American Ceramic Society, 1978, 61(7-8): 375.
利用菱镁矿尾矿制备氧化镁晶须及其应用
王 楠1,陈 敏1,李月圆1,倪红卫2
1. 东北大学 材料与冶金学院,沈阳 110819;
2. 武汉科技大学 钢铁冶金及资源利用省部共建教育部重点实验室,武汉430081
摘 要:以菱镁矿尾矿为原料,通过原料煅烧、水化碳酸化、热解工艺制得碳酸镁晶须作为前驱体,再通过二次煅烧制备氧化镁晶须,并考察添加氧化镁晶须对氧化镁耐火材料烧结和抗热震性能的影响。结果表明:在重镁水热解过程中,添加剂种类对热解产物碳酸镁的形貌具有重要影响,当添加一种可溶性镁盐时,可获得长度10-60 μm、长径比10-20的碳酸镁晶须;当升温速率为1 °C/min时,前驱体可完整地转变为长度为10-40 μm的氧化镁晶须;将氧化镁晶须添加至氧化镁耐火材料中,由于氧化镁晶须的钉扎作用而防止材料裂纹扩展,显著地提高了耐火材料的抗热震性,氧化镁晶须的适宜添加量为3%。
关键词:氧化镁晶须;前驱体;碳酸镁晶须;耐火材料;抗热震性
(Edited by LI Xiang-qun)
Foundation item: Projects (50874130, 50974034) supported by the National Natural Science Foundation of China; Project (FMRU2008K01) supported by the Open Research Fund of Key Laboratory for Ferrous Metallurgy and Resources Utilization of Ministry of Education, Wuhan University of Science and Technology, China
Corresponding author: WANG Nan; Tel: +86-24-83682241; E-mail: wangnan@mail.neu.edu.cn
DOI: 10.1016/S1003-6326(11)60973-4