DOI:10.19476/j.ysxb.1004.0609.2019.04.08
基于超声振动的镁合金双锥件颗粒介质成形工艺
曹秒艳1,房凯旋1,高明欣1,赵长财2
(1. 燕山大学 国家冷轧板带装备及工艺工程技术研究中心,秦皇岛 066004;
2. 燕山大学 先进锻压成形技术与科学教育部重点实验室,秦皇岛 066004)
摘 要:针对结构复杂且具有局部小特征的镁合金双锥件成形制造难的问题,提出一种超声振动辅助颗粒介质成形新工艺。基于有限元软件ABAQUS平台,从超声振动影响板材-模具及板材-介质之间摩擦因数的角度,建立AZ31B镁合金双锥形件的VGMF仿真模型,探讨不同振幅及压边间隙等工业参数对镁合金板材成形性能的影响。并运用有限元分析结果开展相应条件下的镁合金双锥形件VGMF相关试验,对模拟结果进行有效验证,证明该新工艺的适用性。结果表明:当压边间隙为1.25倍板厚时,板材具有较高的极限拉深比;超声振动能够有效降低成形力,改善壁厚均匀度,提高板料的成形极限,VGMF工艺为镁合金板材成形复杂截面零件提供新方法。
关键词:镁合金;双锥形件;超声振动;颗粒介质
文章编号:1004-0609(2019)-04-0726-07 中图分类号:TG386.43 文献标志码:A
轻量化是目前汽车、航空航天、军工等领域设计和开发的重要研究方向,镁合金、铝合金等轻量化材料的应用是实现产品轻量化的有效途径。镁合金具有密度低、比强度和比刚度高、阻尼性好、切削加工性和导热性优、电磁屏蔽能力强等优点,因此在汽车、航空航天、3C等领域应用广泛[1]。但由于镁合金具有独特的密排六方结构,滑移系较少,严重制约其室温成形性能的提高[2-3]。针对这一问题,国内外学者通过改变成形工艺条件和加载路径的方法,有效提高了镁合金板材的成形性能,扩大了应用范围[4-7]。其中,固体颗粒介质成形工艺[8]和超声振动辅助成形是两种各具特色的成形技术[9]。
固体颗粒介质成形工艺采用固体颗粒介质代替刚性凸模(或凹模)的作用,对金属板/管材进行成形,由于其耐高温、易于密封、绿色环保,成形质量好等优点,该工艺自提出后已经引起国内外的密切关注并得到了推广应用[10-13]。
超声振动塑性成形技术是指在传统金属塑性成形的基础上,对坯料或模具施加高频振动[14]。由于超声振动引起的表面效应和体积效应[15]能够有效降低工件的成形力、减小工件与模具间的摩擦、扩大金属塑形加工范围、提高产品表面质量,该技术在拉拔、冲压、挤压等工艺中得到广泛应用[16-17]。为了改善镁合金的成形性能,扩大其塑性成形加工范围,本文作者将超声振动加工技术与固体颗粒介质成形工艺相结合,提出超声振动辅助颗粒介质成形工艺(Vibration granules medium forming, VGMF),该工艺条件下,超声振动有望促进颗粒介质流动性和传力效果,同时可减小模具与板材摩擦,降低金属变形抗力,从而提高板材成形性能。本文以AZ31B镁合金板材拉深成形双锥形件为例,通过数值模拟与试验相结合的方法研究超声振动对镁合金板材颗粒介质成形的影响,对VGMF工艺进行探讨。
1 AZ31B镁合金双锥形件VGMF数值模拟
1.1 零件特征分析及有限元模型的建立
图1所示为研究的双锥形件示意图。双锥形件主要由6部分构成,由下自上依次为:凸缘、法兰圆角、锥壁、锥顶、平底及内凹底。成形该件的难点主要有两处:1) 锥顶及锥壁部分,因两部分的锥角不同,角度相差46°,这就使得成形过程相较于具有单一锥角零件的成形过程更为复杂,由法兰区域补料成形更为困难;2) 内凹底部分,该局部小特征由于底部壁厚减薄严重,因此与模具贴合过程中极易破裂。
采用商用有限元软件ABAQUS中建立镁合金颗粒介质拉深成形的数值仿真模型如图2所示,由于双锥形件为典型的回转体类零件,为降低计算成本,故建立1/4仿真模型进行分析。其中颗粒介质及板料为变形体,其余各部件均定义为刚体,同时,采用锥形冲头以增强颗粒介质的传力效果。颗粒的材料属性采用拓展的Drucker-Prager线性模型表达如表1所列。其中,β为颗粒材料的内摩擦角,K为三轴拉伸屈服应力与三轴压缩屈服应力之比,ψ为颗粒剪胀角,p为颗粒介质承受压力,εv 为颗粒体积压缩率。通过单向拉伸实验获得镁合金AZ31B的材料性能参数,并建立其材料模型[11],板材基本材料属性如表2所列。
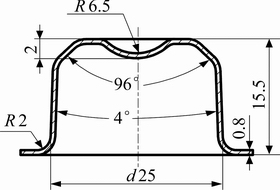
图1 双锥形零件示意图
Fig. 1 Schematic diagram of biconical parts (Unit: mm)
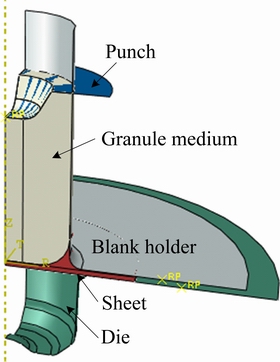
图2 仿真模型示意图
Fig. 2 Schematic diagram of simulation model
模拟分析中其边界条件为凹模和料筒固定,压头以恒定速率下压。由于在ABAQUS的瞬态动力学分析中,目前尚无法对超声振动下金属板材的体积效应进行直接精准的描述,因此本文仅从振动改变接触摩擦因数,进而影响拉深性能的角度对颗粒介质振动拉深成形进行仿真模拟。通过振动剪切摩擦[18]试验得到的各接触对间的摩擦因数如表3所列。
表1 固体颗粒介质材料模型参数
Table 1 Simulation parameters of solid granules

表2 镁合金AZ31B板材基本材料属性
Table 2 Basic material properties of magnesium alloy AZ31B plate
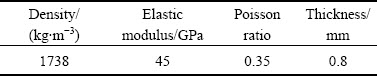
表3 不同条件下各接触对间的摩擦因数
Table 3 Friction coefficient between contact pairs under different conditions
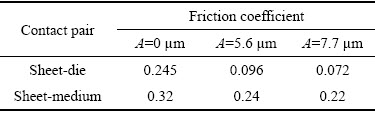
1.2 有限元模拟结果分析
选取厚度为0.8 mm的圆形坯料为研究对象,初始颗粒介质料高为20 mm,料筒直径为22 mm,板材成形温度θ=250 ℃,振幅分别为0 μm、5.6 μm、7.7 μm时的拉深仿真模型进行分析,研究压边间隙、振幅等成形参数对镁合金板材成形的影响。
1.2.1 压边间隙对成形的影响
对于圆锥形件,可将拉深比值定义为毛坯半径与锥形件平均中径之比。极限拉深比(Limited drawing ratio, LDR)主要用来衡量板材的最大可能变形程度,该值主要与板材材质、压边间隙、润滑等因素有关。压边间隙直接决定压边力的大小,从而影响板料的成形质量,选取合适的压边间隙对零件拉深成形至关重要。润滑的目的主要是减小板材与模具之间摩擦阻力,改善成形条件,超声振动辅助颗粒介质成形工艺中,超声振动改善了模具与板材之间的摩擦,有利于材料向模具中流动。
为了探讨不同压边间隙条件下,超声振动激励对镁合金板材颗粒介质拉深性能的影响,选取1.1t、1.25t和1.4t(其中t为板材坯料厚度) 3种不同压边间隙,模拟得到不同振动条件下的极限拉深比如图3所示。由图3可以看出,不管压边间隙大小如何,施加振动激励后,LDR均有显著提高,且在振幅7.7 μm达到最大值;LDR在振幅7.7 μm时的值比振幅5.6 μm时的稍有提高。
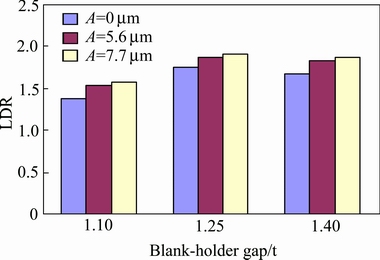
图3 不同压边间隙下极限拉深比
Fig. 3 LDR of different blank holder gap
相同振动条件下,压边间隙在1.2~1.3t的范围内板材均可顺利成形,1.3t时板材法兰区域出现轻微起皱;当压边间隙较小(1.1t)时会产生较大的压边力,板材容易拉裂;当压边间隙过大(1.4t)时会因为压边力较小导致法兰部分起皱,尤其成形后期起皱严重,阻碍板材进一步向凹模内流动。
1.2.2 振动对成形件壁厚影响
为考察超声振动对成形件壁厚的影响,选取压边间隙1.25t条件下,直径为43 mm的圆形坯料进行拉深成形仿真分析。提取成形件高度H=13.5 mm时,不同振动条件下成形件沿母线O-M-Q-T-P方向的壁厚分布曲线,如图4所示,此时成形件的锥壁段QT及锥顶部分已完全形成,开始成形内凹底部分。3种振幅下成形件壁厚曲线分布的走势基本一致,减薄最严重的区域同为底部中心O处。纵向来看,振幅为5.6 μm和7.7 μm时壁厚分布几乎无差异,但有无振动下成形件的壁厚分布曲线差别却很明显:施加超声振动后(A=5.6 μm或A=7.7 μm),成形件的壁厚更加均匀,底部壁厚减薄率有所减小,尤其是内凹底外缘至锥顶下边缘的MN段,壁厚相比无振动时整体提高了2.7%~4.3%;无振动时,最大壁厚减薄率约为22.8%,而施加超声振动后(A=5.6 μm或A=7.7 μm),壁厚最大减薄率约为12.5%;无振动时,锥壁上Q处壁厚减薄率为18.2%,该部位为成形中前期的破裂危险区域。出现这些变化的主要原因是:施加振动后,颗粒流动性增强,对金属板材的主动摩擦传力性能相应提高;另外,板材与凹模及压边圈间的摩擦力减小,有效地改善了板材自由变形区的主动摩擦保持效果及法兰圆角区域的坯料流动状况,改善了拉深成形过程。
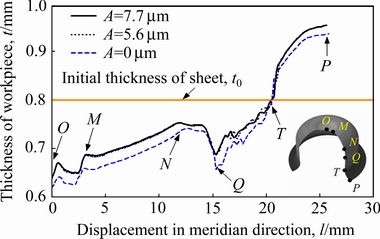
图4 不同振动条件下的成形件壁厚分布曲线
Fig. 4 Curve of wall thickness distribution of forming parts under different vibration conditions
1.2.3 模拟拉深成形力分析
图5所示为不同超声振幅条件下拉深成形力与压头行程的关系曲线。由图5可知:在压头行程小于6 mm时,有无振动情况下成形力的大小基本相同,这是因为拉深前期,因颗粒介质的压缩变形,使得此时压头经过介质作用于板料上的成形力较小,变形主要发生在处于双向拉应力状态的板材中心的自由变形区域,法兰及板材的大部分还未发生变形,振动的减摩作用还未体现出来。随着变形的进行,法兰部分板材开始流入凹模,振动作用使得板料与压边圈间的摩擦减小,即减摩作用逐渐增强,成形力小于无振动的情况,且差值随压头行程的进行,逐渐增大,最大可达1200 N。当压头行程(h)达到16 mm时,板料开始接触凹模底部中心,随着贴模成形的进行,颗粒介质内压急剧上升。此时板材法兰处补料效果降低,主要依赖板材自身延展逐步实现底部圆角等小特征的成形。
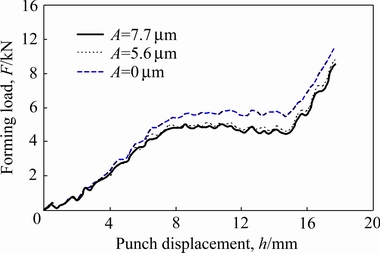
图5 不同振动条件下成形力变化曲线
Fig. 5 Curve of forming force under different vibration conditions
2 镁合金VGMF试验验证
2.1 镁合金双锥形件超声振动辅助颗粒介质成形试验装置及过程
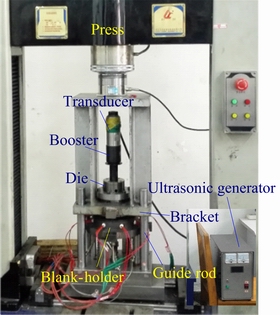
图6 试验原理及装置图
Fig. 6 Experiment schematic diagram and experiment setup
本试验所用的超声波发生器频率为20 kHz,试验前通过非接触式OptoMET数字型激光多普勒测振仪对不同档位下的模具振幅进行测量。镁合金双锥形件超声振动颗粒成形试验原理和设备装置图见图6。试验时,先将颗粒介质倒入料筒中,然后将抹有高温润滑剂的圆形坯料放置在压边圈上表面,压边圈内均布加热棒;支撑框上端通过螺栓连接在试验机的活动横梁上,底部连接着超声振子的凹模采用法兰固定于支撑框下端,活动横梁下行带动支撑框沿着导柱向下运动,直到凹模与压边圈上的坯料贴合;压边圈上设置有调整垫片,用于控制压边圈与凹模间压边间隙。然后开启加热装置,加热到目标温度,并保温5 min,启动超声波发生器,超声波通过换能器和变幅杆传递到凹模,使其产生纵向振动。压机开始下行,启动数据采集软件,随着凹模下行,坯料缓慢地流入凹模型腔中,同时压边圈也向下运动,压缩弹簧保证压边圈始终贴紧坯料并维持固定间隙值。拉深成形完成后,进行卸载,活动横梁回程带动支撑框向上运动,压边圈在弹簧的作用下恢复至初始位置。试验选用厚度为0.8 mm的AZ31B镁合金板,采用水基二硫化钼作为润滑剂,颗粒装料高度为20 mm。
2.2 试验结果分析
坯料直径D0=44 mm,在成形温度θ=250 ℃,振幅分别为0 μm、5.6 μm、7.7 μm时试验件对比如图7所示。由图7可看出,不施加振动时(A=0 μm),双锥形件在刚开始成形一小段锥壁段时即发生破裂,成形高度约为12.4 mm。断裂面向零件周向发展,宏观来看,断口不平整、较为粗糙,是因径向拉应力过大引起的典型断裂形式。当施加超声振动后(A=5.6 μm或A=7.7 μm),零件均可完全成形,成形件高度均可达到零件图所要求的15.5 mm。当振幅为5.6 μm时,零件凸缘部分分布较为均匀,成形件表面光滑;当振幅为7.7 μm时,零件底部锥形及内凹底均成形饱满,其工件法兰直径相比振幅5.6 μm时的小,说明随着振幅增加,板材变形时收料更为充分,壁厚更加均匀。
2.2.1 振动拉深试验成形力
图8所示为不同振幅下试验件成形力随压头行程的变化曲线。可以看出,施加超声振动后,底部贴模前拉深成形力峰值较无振动时大幅下降,振幅为5.6 μm时的成形力峰值下降了约26%,振幅为7.7 μm时的成形力峰值下降了约31.5%。而振幅为5.6 μm和7.7 μm时底部贴模前拉深阶段成形力峰值基本接近,待到底部内凹及圆角等局部特征贴模充型时,成形力急剧上升。综上说明超声振动的施加能够有效地降低成形力,提高零件的成形极限。

图7 不同振幅下试验件对比图
Fig. 7 Comparison of test pieces at different amplitudes
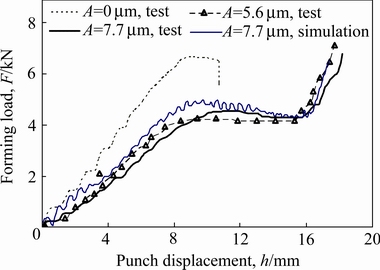
图8 不同振幅下试验件成形力变化曲线
Fig. 8 Curves of forming force of test parts under different amplitudes
图8中也给出了超声振幅为7.7 μm时拉深成形力的模拟变化曲线,对比发现,试验成形力比模拟值有所降低,这是由于本数值模拟中仅仅考虑了超声振动对于板材与模具及介质间的摩擦因数的影响,也即“表面效应”的作用,暂未考虑“体积效应”的影响。而超声振动之所以能有效降低成形力,究其原因是“体积效应”和“表面效应”共同作用的结果。“表面效应”的作用机理本质在于摩擦力的减小,在超声振动的作用下,模具与板料会产生瞬间分离,且摩擦矢量会发生周期性的改变,最终导致接触摩擦减小,成形力的下降。“体积效应”使材料在振动激励后出现“软化”现象,有学者认为是材料吸收超声振动能量后,其内部的微粒活性增强,温度升高,造成与晶体位错有关的热致软化[9]。
2.2.2 试验工件壁厚对比分析
为了更好地分析振幅在镁合金双锥件振动颗粒介质拉深成形中的影响,特选取坯料直径D0=43 mm,成形温度θ=250 ℃,振幅分别为0 μm、5.6 μm时的成形件进行壁厚测量,其中所选成形件均已完全成形,测量点的位置沿零件母线OA选取,测量结果与模拟结果曲线分布如图9所示。由图9可以看出,无振动时(A=0 μm),壁厚减薄最严重的位置为内凹底的边缘位置,如图上所示的B处;当振幅为5.6 μm时,壁厚减薄最严重的部位出现在底部中心O处。总体来看,试验值与模拟值的变化趋势基本一致,但模拟值整体上大于试验值,出现这种差异的原因可能包括:模拟主要是从“表面效应”角度对振动在成形中所起作用进行了一个近似表达,对“体积效应”模拟中未能体现;振动对颗粒介质的作用机理较为复杂,对其作用机理的探索研究还有待进一步深入。
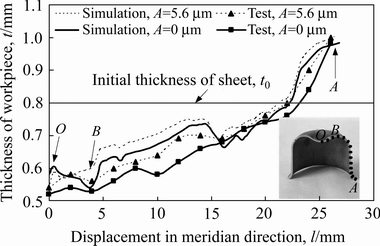
图9 不同振幅下零件壁厚分布情况
Fig. 9 Distribution of wall thickness at different amplitudes
3 结论
1) 以镁合金板料成形双锥形件为例,从振动影响摩擦因数进而影响拉深性能的角度对VGMF工艺进行仿真运算,通过仿真模拟和试验对比发现,相同成形条件下,施加超声振动后,成形件的壁厚更加均匀,成形极限有效提高。
2) 由于超声振动的减摩作用,使得板料与模具间的摩擦阻力减小,施加振幅为5.6 μm和7.7 μm的超声振动后,成形力显著降低,较无振动下条件下的成形力下降幅度分别为26%和31.5%;超声振动抑制了双锥形件底部圆角小特征部位在成形时的减薄和破裂趋势,使之工件局部小特征充型更加饱满,改善了板材的成形性能。
REFERENCES
[1] 李 超, 李彩霞, 赵 闪. 脉冲电流条件下工业态AZ31镁合金板材的气胀成形[J]. 中国有色金属学报, 2015, 25(3): 553-559.
LI Chao, LI Cai-xia, ZHAO Shan. Gas blow forming of commercial AZ31 magnesium assisted by pulse current[J]. The Chinese Journal of Nonferrous Metals, 2015, 25(3): 553-559.
[2] 郜 瑞, 温 彤, 季筱玮, 张文城. 镁合金板材拉深工艺的研究与进展[J]. 热加工工艺, 2012, 41(5): 30-32.
GAO Rui, WEN Tong, JI Xiao-wei, ZHANG Wen-cheng. Research and development of drawing technology for magnesium alloy[J]. Hot Working Technology, 2012, 41(5): 30-32.
[3] 申利权, 杨 旗, 靳 丽, 董 杰. AZ31B镁合金在高应变速率下的热压缩变形行为和微观组织演变[J]. 中国有色金属学报, 2014(9): 2195-2204.
SHEN Li-quan, YANG Qi, JIN Li, DONG Jie. Deformation behavior and microstructure transformation of AZ31B Mg alloy under high strain rate compression[J]. The Chinese Journal of Nonferrous Metals, 2014(9): 2195-2204.
[4] 张士宏, 宋广胜, 宋鸿武, 程 明. 镁合金板材温热变形机理及温热成形技术[J]. 机械工程学报, 2012, 48(18): 28-34.
ZHANG Shi-hong, SONG Guang-sheng, SONG Hong-wu, CHENG Ming. Deformation mechanism and warm forming technology for magnesium alloys sheets[J]. Journal of Mechanical Engineering, 2012, 48(18): 28-34.
[5] VIEHWEGER B, RICHTER G, DURING M, KARABET A, SVIRIDOV A, HARTMANN H, RICHTER U. Hydromechanisches tiefziehen und hochdruckblechumformung als verfahren zur herstellung komplexer bauteile aus magnesiumfeinblechen des typs AZ31B-0[J]. Materialwissenschaft Und Werkstofftechnik, 2004, 35(7): 440-446. (in German)
[6] LEE S, CHEN Y H, WANG J Y. Isothermal sheet formability of magnesium alloy AZ31 and AZ61[J]. Journal of Materials Processing Technology, 2002, 124: 19-24.
[7] Antoniswamy A R, Carpenter A J, Carter J T, Jr L G H, Taleff E M. Forming-limit diagrams for magnesium AZ31B and ZEK100 alloy sheets at elevated temperatures[J]. Journal of Materials Engineering & Performance, 2013, 22(11): 3389-3397.
[8] 赵长财, 李晓丹, 董国疆, 王银思. 板料固体颗粒介质成形新工艺及其数值模拟[J]. 机械工程学报, 2009, 45(6): 211-215.
ZHAO Chang-cai, LI Xiao-dan, DONG Guo-jiang, WANG Yin-si. Solid granules medium forming technology and its numerical simulation[J]. Journal of Mechanical Engineering, 2009, 45(6): 211-215.
[9] Wen Tong, Gao Rui, Chen Xia. Influence of high frequency vibration on deep drawing process of AZ31 sheet at room temperature[J]. Journal of Shanghai Jiao Tong University (Science), 2012, 17(4): 456-460.
[10] CHEN H, GUNER A, KHALIFA N B, TEKKAYA A E. Granular media-based tube press hardening[J]. Journal of Materials Processing Technology, 2016, 228: 145-159.
[11] CAO Miao-yan, ZHAO Chang-cai, DONG Guo-jiang, YANG Sheng-fu. Instability analysis on the free deformation zone in forming process of cylindrical parts with hot granule medium[J]. Transactions of Nonferrous Metals Society of China, 2016, 26(8): 2188-2196.
[12] GRUNER M, MERKLEIN M. Numerical simulation of hydro forming at elevated temperatures with granular material used as medium compared to the real part geometry[J]. International Journal of Material Forming, 2010, 3(1): 279-282.
[13] 李鹏亮, 张 志, 曾元松. 钛合金机头罩固体颗粒介质成形工艺研究[J]. 锻压技术, 2012, 37(5): 60-63.
LI Peng-liang, ZHANG Zhi, ZENG Yuan-song. Study on titanium alloy spinner based on solid granules medium forming[J]. Forging & Stamping Technology, 2012, 37(5): 60-63.
[14] 赵升吨, 李泳峄, 范淑琴. 超声振动塑性加工技术的现状分析[J]. 中国机械工程,2013, 24(6): 835-840.
ZHAO Sheng-dun, LI Yong-ze, FAN Shu-qin. Status analysis of plastic processing technology with ultrasonic vibration[J]. China Mechanical Engineering, 2013, 24(6): 835-840.
[15] Blaha F, Langenecker B. Elongation of zinc monocrystals under ultrasonic action[J]. Die Natur Wissenschafen, 1955, 42(20): 556-556. (in German)
[16] Pasierb A, Wojnar A. An experimental investigation of deep-drawing process of thin-walled products with utilization of ultrasonic vibrations[J]. Journal of Materials Processing Technology 1992, 34(1/4): 489-494.
[17] 谢 涛, 齐海群, 张 俊. 超声振动拉丝实验研究[J]. 中国机械工程, 2006, 17(3): 224-226.
XIE Tao, QI Hai-qun, ZHANG Jun. Experimental research on wire drawing with ultrasonic vibration[J]. China Mechanical Engineering, 2006, 17(3): 224-226.
[18] CAO Miao-yan, PENG Ya-xin, ZHAO Chang-cai, DONG Guo-jiang, DU Bing. Frictional characteristics of granular system under high pressure[J]. Journal of Central South University, 2016, 23(5):1132-1141.
Granular medium forming technology of magnesium alloy biconical parts based on ultrasonic vibration
CAO Miao-yan1, FANG Kai-xuan1, GAO Ming-xin1, ZHAO Chang-cai2
(1. National Engineering Research Center for Equipment and Technology of Cold Strip Rolling, Yanshan University, Qinhuangdao 066004, China;
2. Key Laboratory of Advanced Forging & Stamping Technology and Science, Ministry of Education of China, Yanshan University, Qinhuangdao 066004, China)
Abstract: The vibration granules medium forming (VGMF) was proposed to solve the manufacturing problem of a AZ31B magnesium alloy biconical specimen with some small local complex structures. The VGMF process simulation model of AZ31B magnesium alloy biconical parts was established with ABAQUS from the effect of vibration on the friction coefficients of sheet-die and sheet-medium, and the influences of different amplitudes and blank-holder gaps on magnesium alloy sheet forming properties were discussed. The accuracy of simulation results was proved by the VGMF test of AZ31B biconical parts, and the applicability of the new process was proven. The results show that the ultrasonic vibration can reduce the forming force, keep the uniformity of the thickness, and improve the forming limit of the sheet metal, and when the blank-holder gap is 1.25 times of sheet thickness, the magnesium alloy sheet has a higher limit drawing ratio (LDR). VGMF provides a new method for forming complex cross-section parts of magnesium alloy sheet.
Key words: magnesium alloy; biconical part; ultrasonic vibration; granules medium
Foundation item: Projects(51775480, 51305385) supported by the National Natural Science Foundation of China
Received date: 2017-11-21; Accepted date: 2018-02-08
Corresponding author: ZHAO Chang-cai; Tel: +86-18533511399; E-mail: zhao1964@ysu.edu.cn
(编辑 王 超)
基金项目:国家自然科学基金资助项目(51775480, 51305385).
收稿日期:2017-11-21;修订日期:2018-02-08
通信作者:赵长财,教授,博士;电话: 18533511399;E-mail:zhao1964@ysu.edu.cn