文章编号:1004-0609(2012)05-1377-06
辅助磨擦对镍电铸层力学性能的影响
章 勇,朱增伟,朱 荻
(南京航空航天大学 机电工程学院,南京 210016)
摘 要:在磨擦辅助电铸镍过程中,通过改变游离微珠对电铸层表面的磨擦强弱,制备不同力学性能的镍电铸层。对所制备镍电铸层的表面形貌、织构等微观结构和显微硬度、抗拉强度及伸长率等性能进行测试和分析。结果表明:采用卧式放置的阴极能制得材料组织结构均匀的电铸层。且随着阴极表面线速度的提高,游离微珠对电铸层的整平作用和晶粒细化作用增强。在不同线速度下采用旋转阴极可以制备大范围力学性能的镍电铸层,其表面粗糙度为0.15~0.03 μm、硬度为185~410HV、抗拉强度为525~1 020 MPa、伸长率为24%~4%。
关键词:镍;电铸;力学性能;摩擦
中图分类号:TQ153.43 文献标志码:A
Effect of attrition on mechanical properties of electroformed nickel
ZHANG Yong, ZHU Zeng-wei, ZHU Di
(College of Mechanical and Electrical Engineering, Nanjing University of Aeronautics and Astronautics,Nanjing 210016, China)
Abstract: During the abrasive-assisted electroforming process of nickel, the electroformed nickel deposits with different mechanical properties were prepared by changing the friction strength of the free particles on the surface of the deposits. The morphology and texture of the deposits were studied, and the microhardness, tensile strength and elongation were also measured. The results show that the homogeneous microstructure of the deposits is obtained with the horizontal cathode. The surface smoothness is improved and the nickel crystal grain is refined with the increase of the linear velocity on the surface of the cathode. The electroformed nickel deposits can be obtained with a wide range of mechanical properties at different speeds of the rotating cathode. The surface roughness of the electroformed nickel deposits is in the range from 0.15 μm to 0.03 μm, the hardness is in the range from 185HV to 410HV, the tensile strength is in the range from 525 MPa to 1 020 MPa, and the elongation is in the range from 24% to 4%.
Key words: nickel; electroforming; mechanical performance; friction
电铸技术作为一种精密特种加工方法,应用于传统工艺难加工的零部件制造。镍是电铸工业中最常用的金属之一,已应用于精密模具、药型罩、火箭发动机推力室身部、超音速风洞喷管等的制造[1-4],这些零件对力学性能各有其不同的要求。因此,如何制备所需力学性能的电铸层是电铸工艺的关键问题。国内外许多研究者已对镍电铸层的制备进行了广泛的研究,Bell宇航公司研究了溶液成分、工艺参数对镍电铸层力学性能的影响,在采用压缩空气搅拌溶液的条件 下,得到了伸长率最高为23%、对应抗拉强度为435 MPa和抗拉强度最高793 MPa、对应伸长率为6%的电铸镍层;德国MBB公司在阴极电流密度为5 A/dm2的条件下制得了抗拉强度为549 MPa、伸长率为 18.5%的镍电铸层[5]。SAMPLE和KNAPP[6]制备了抗拉强度为766 MPa、伸长率为7%的镍电铸层。近年 来,对电沉积镍的研究主要采用脉冲电源[7-8]。
从上可以看出:电铸镍的性能受电沉积过程中诸多因素的影响,如冲液条件、溶液成分、电源和添加剂等。不同研究者制得的镍电铸层有差异,其力学性能大都在某一小范围内变化。而且传统的电铸工艺还存在如针孔、麻点、结瘤等缺陷,上述缺陷随着沉积时间的延长迅速恶化,使得沉积层表面质量变坏,材料的均匀性和力学性能较差[4, 9]。目前,比较常用的解决方法是在电铸液中加入添加剂或采用脉冲电源等,但这些方法在电铸加工中各有其缺点,如添加剂在电铸液中会不同程度地消耗、在长时间的电铸过程中很难控制其含量、电铸液的稳定性差、最终造成电铸层的质量降低、材料性能不均匀[10-13]。而采用脉冲电流则对电源的要求较高,且在对大型零部件的进行电铸时,脉冲电源应具有极高的峰值电流,这会带来新的困难。对于电铸层性能有严格要求的情况,以上方法往往难以适用。采用磨擦辅助电铸法可以改善电铸层的表面形貌,消除结瘤[14-15]。但在对某些大型复杂结构件进行电铸时,阴极采用立式放置方式会导致其不同部位所受摩擦不均匀,从而使得制得的电铸层材料不均匀。
为获得不同力学性能的镍电铸层,并改善电铸层的均匀性,本文作者利用磨擦辅助电铸成形技术,阴极采用卧式放置的方式进行电铸镍试验,研究不同阴极速度条件下制备的镍电铸层的力学性能,并探讨其作用机理。
1 实验原理及理论分析
在进行磨擦辅助电铸镍试验时,阴极采用卧式方式置于电铸槽中,试验装置如图1所示。在阴极和阳极筐之间,堆置不导电的耐磨游离微珠。电铸时,阴极以一定的速度旋转,阴极与游离微珠之间的相互磨擦和挤压,阻止了氢气泡和杂质在阴极表面的长期滞 留,从而避免在电铸层表面形成凹坑、针孔、麻点和结瘤等缺陷,实现阴极表面的整平。阴极的转动使得阴极周围的溶液能及时更新,强化了溶液的自然对流效果。游离微珠对阴极表面的覆盖和屏蔽,使得电极过程中电化学反应受到阻滞而引起极化,增强了电化学极化,从而提高了晶核的生成速度,能获得结晶细致的电铸层。同时,游离微珠对阴极表面的磨擦和挤压影响金属离子的放电和结晶过程,改变电铸层微观组织结构,从而改善电铸层的力学性能。
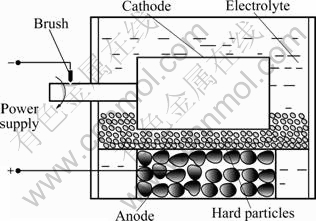
图1 试验装置示意图
Fig. 1 Schematic diagram of experimental apparatus
与立式放置的阴极相比,阴极采用卧式的方式放置,可使在电铸过程中阴极轴向同一高度位置上能够均匀地承受游离微珠的磨擦和挤压,从而保证整个阴极受到游离微珠的磨擦作用相同,以制得材料性能均匀的电铸层。
在电铸过程中,游离微珠和阴极表面之间包含摩擦、碰撞、挤压等复杂运动,为了简化分析,可对单个微珠在某一瞬间与阴极表面的作用状态进行分析。微珠与阴极表面的相对运动主要是滑动和滚动,且滚动摩擦力相对滑动摩擦力来说小得多,所以,分析滑动摩擦的作用即可。
由摩擦学可知,阴极表面位置i的摩擦力可由下式计算:
Fi=fWi (1)
式中:f为摩擦因数;Wi为位置i的载荷。
在一般滑动摩擦情况下,金属表面处于弹塑性接触状态,对于一般弹塑性接触状态的摩擦副,摩擦因数与载荷和滑动速度之间的关系如图2所示[16]。本实验中,电铸过程中游离微珠与阴极表面的摩擦可以看作是极小载荷(或中等载荷)及低速下的滑动摩擦,载荷Wi可以视为恒定值,这时摩擦因数f随着滑动速度v的增加而变大,而由Fi=fWi可知,摩擦力Fi随着速度v的增加而变大。由此可知,当阴极速度增加时,摩擦强度增加。
2 实验过程
采用氨基磺酸盐电铸液,其组成如下:氨基磺酸镍400 g/L、硼酸30 g/L、氯化镍15 g/L、pH=4,t=43 ℃。阳极为INCO公司生产的8~12 mm不含硫镍珠,并用阳极布包裹,以防止阳极泥的渗出。游离微珠采用直径为1~2 mm的陶瓷球,使用前用去离子水洗净后烘干。使用d 48 mm×80 mm的不锈钢圆柱外表面作为阴极,并屏蔽芯模两端面的非沉积区,芯模表面经抛光、弱浸蚀处理,再用去离子水洗净后入槽。电源采用直流稳压电源。电机选用普通调速电机,在不同的电机转速条件下,阴极电流密度均采用4 A/dm2,控制电沉积时间,将拉伸试件的电铸层厚度控制在0.75 mm左右。电铸结束后,取出芯模,经清洗、干燥后进行显微硬度测试,然后采用低速走丝电火花线切割机床,将电铸层连同芯模一起切割成拉伸试样,切割完后对电铸层进行脱模,洗净后进行拉伸试验。
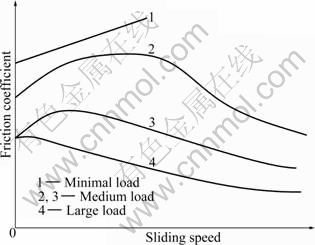
图2 摩擦因数与滑动速度的关系[16]
Fig. 2 Relationship between friction coefficient and sliding speed[16]
表面粗糙度测试:在Mahr GMBH粗糙度测试仪上测量电铸层的表面粗糙度。测量在脱模前进行,测量时用专门制作的夹具对带有电铸层的芯模进行定位,每个样件在不同部位测量6个点,取平均值。
电铸层的表面形貌测试:在HITACHI S3400N型扫描电子显微镜上进行。
电铸层的显微硬度测试:在HXS-1000A型数字式智能显微硬度计上进行。试验力为0.49 N,保荷时间10 s,每个试件在不同部位测量6个点,取平均值。
镍电铸层的抗拉强度、伸长率测试:在CSS-2202型电子万能试验机上进行拉伸试验,拉伸速率为0.4 mm/min。
3 结果与分析
图3所示为不同阴极速度下所制备的镍电铸层。图3(a)~(e)中阴极表面线速度分别为2.5、5、10、20和80 mm/s。从图3可以看出:在各个线速度下,电铸层表面均无针孔、无结瘤、平整和光滑,但是光亮度不同,光亮度随着线速度的提高逐渐增强。当线速度为2.5和5 mm/s时,电铸层表面平整光滑,但无明显的光亮感;当线速度为10 mm/s时,电铸层表面开始变得光亮;当线速度增加到20和80 mm/s时,光亮度明显增强。电铸层表面粗糙度变化如图4所示。从图4可以看出:随着线速度的提高,电铸层表面粗糙度呈下降趋势,当阴极线速度为80 mm/s时,表面粗糙度值最小,为0.03 μm,表明游离微珠的磨擦可以有效地阻止氢原子在阴极表面的吸附,从而避免形成针孔和麻点,抑制结瘤的生成。同时,游离微珠对沉积层有微磨削作用,摩擦强度的不同,对电铸层的整平作用不同。
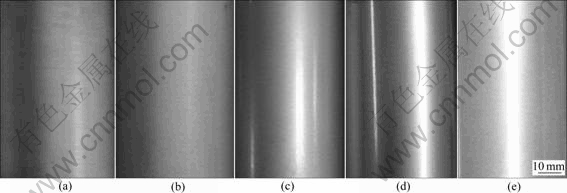
图3 不同阴极速度下的电铸镍外观
Fig. 3 Photos of electroformed nickel coatings at different cathode velocities: (a) 2.5 mm/s; (b) 5 mm/s; (c) 10 mm/s; (d) 20 mm/s; (e) 80 mm/s
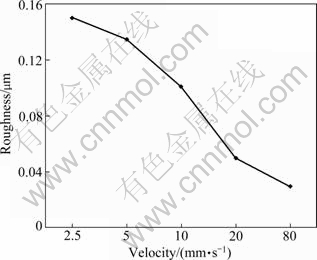
图4 阴极速度对电铸镍表面粗糙度的影响
Fig. 4 Effect of cathode velocity on surface roughness of electroformed nickel coatings
3.1 微观结构
图5所示为在不同速度条件下制备的电铸镍的SEM像。从图5可以看出:当阴极表面线速度为 2.5~10 mm/s时,随着线速度的提高,晶粒逐渐细化;当线速度小于20 mm/s时,电铸镍的晶粒尺寸较为粗大;而当线速度提高到80 mm/s时,晶粒尺寸明显细化,且表面有明显的磨擦痕迹。这表明在游离微珠辅助磨擦电铸镍过程中,游离微珠对阴极表面的磨擦和挤压作用能够细化晶粒,这种作用随着线速度的提高而加强。其次,纵观所有电铸镍试件的各个部位发现,同一试件不同部位的晶粒大小一致、材料的均匀性良好,表明卧式放置的阴极与游离微珠的磨擦均匀。
3.2 硬度
图6所示为镍电铸层的显微硬度随阴极表面速度的变化趋势。从图6可以看出:在一定线速度范围内,采用磨擦辅助电铸所制得的镍电铸层显微硬度随着阴极表面线速度的提高而增大。当阴极表面线速度为2.5~10 mm/s时,电铸镍的显微硬度提高较缓慢;当线速度提高到20 mm/s时,显微硬度迅速上升至305HV;当线速度为80 mm/s时,显微硬度最高,达到410HV。用磨擦辅助电铸技术所得电铸层的显微硬度提高的主要原因是游离微珠磨擦在电沉积过程中改变沉积层的组织结构,使晶粒细化。当电流密度一定时,阴极表面线速度的提高将强化磨擦作用,从而使电铸层的硬度相应提高。对同一电铸镍试件的不同部位进行硬度测试后发现,其硬度一致,说明电铸材料组织结构均匀。此外,当阴极电流密度增大时,相同线速度下游离微珠对阴极的磨擦作用被弱化,晶粒变大。
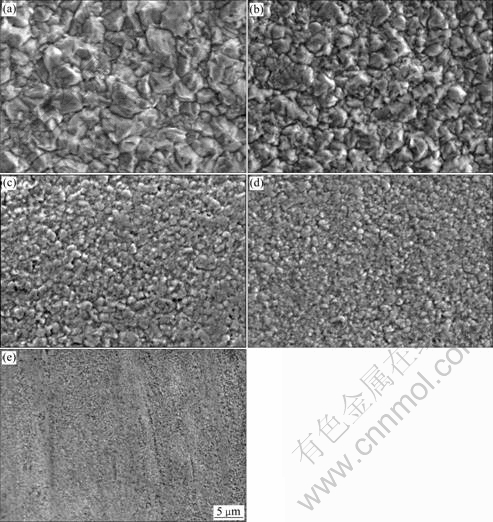
图5 不同速度下的电铸镍SEM像
Fig. 5 SEM images of electroformed nickel coatings at different velocities (a) 2.5 mm/s; (b) 5 mm/s; (c) 10 mm/s; (d) 20 mm/s; (e) 80 mm/s
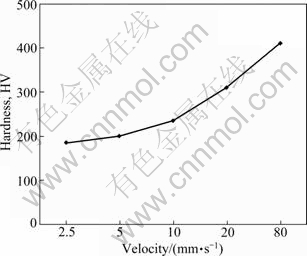
图6 阴极速度对电铸镍硬度的影响
Fig. 6 Effect of cathode velocity on hardness of electroformed nickel coatings
3.3 抗拉强度和伸长率
图7和8所示为阴极速度对电铸镍抗拉强度和伸长率的影响。由图7和8可以看出:电铸镍的抗拉强度随着阴极表面速度的增加而逐渐增加,而伸长率逐渐降低。当线速度为2.5~10 mm/s时,电铸镍的抗拉强度提高较缓慢,从490 MPa提高到635 MPa,此时伸长率相应地从24%下降到21%;当线速度提高到20 mm/s时,抗拉强度上升至810 MPa,伸长率急剧下降至10%;当线速度为80 mm/s时,抗拉强度最高达到1 020 MPa,此时伸长率为4%左右。其中,在阴极速度10 mm/s时,制得的镍电铸层的抗拉强度和伸长率分别为635 MPa和21%,比德国MBB公司生产的抗拉强度为549 MPa、伸长率为18.5%的镍电铸层,分别提高了15.7% 和13.5%。由实验结果可以看出,在其他速度条件下所制得的镍电铸层的性能也比传统的性能优异,这是因为在磨擦辅助电铸过程中,游离微珠对阴极表面的磨擦和挤压作用使电铸层更为致密和均匀。
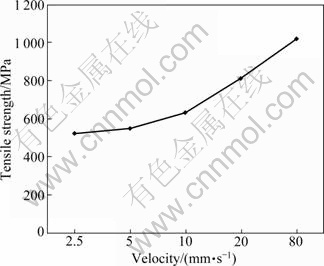
图7 阴极速度对电铸镍抗拉强度的影响
Fig. 7 Effect of cathode velocity on tensile strength of electroformed nickel coatings
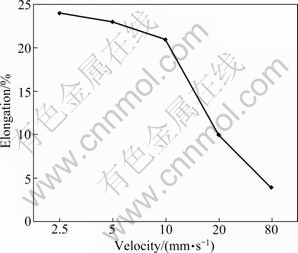
图8 阴极速度对电铸镍伸长率的影响
Fig. 8 Effect of cathode velocity on elongation of electroformed nickel coatings
对比电铸镍的组织结构可以认为,抗拉强度的提高是游离微珠磨擦所产生的细晶强化效应所致。当阴极表面线速度增大时,游离微珠的磨擦作用增强,引起电铸层的晶粒大小等组织结构的变化,使电铸层的强度也随之发生改变。显微硬度和抗拉强度随阴极表面速度的变化趋势与晶粒大小的变化趋势非常接近,当晶粒尺寸变小时,显微硬度和抗拉强度都增加。
4 结论
1) 在磨擦辅助电铸过程中,卧式放置的阴极有利于获得组织结构均匀的电铸层。阴极速度的变化对镍电铸层有不同程度的整平作用,且这种作用随着阴极速度的提高而增强,电铸层表面的光亮度也随之增加。
2) 游离微珠与阴极表面的磨擦对电铸层有明显的晶粒细化作用,电铸镍的晶粒随着阴极速度的增加而细化。
3) 采用磨擦辅助电铸技术可以获得性能优良的镍电铸层。当阴极电流密度为4 A/dm2、阴极速度为10 mm/s时,制得的镍电铸层的抗拉强度和伸长率分别为635 MPa和21%。在电流密度不变的条件下,随着游离微珠与阴极表面摩擦强度的增加,电铸镍的晶粒变小,显微硬度和抗拉强度增加,伸长率下降。
REFERENCES
[1] 陈钧武, 何士恒. 电铸原理与工艺[M]. 北京: 化学工业出版社, 2010: 5-7.
CHEN Jun-wu, HE Shi-heng. Mechanism and technology of electroforming [M]. Beijing: Chemical Industry Press, 2010: 5-7.
[2] 雷卫宁, 朱增伟, 陶 钢. 超细晶粒镍药型罩的精密电铸试验研究[J]. 中国机械工程, 2010, 21(3): 340-343.
LEI Wei-ning, ZHU Zeng-wei, TAO Gang. Experimental research on finer-grain electroformed nickel shaped charge liner [J]. China Mechanical Engineering, 2010, 21(3): 340-343.
[3] 李学磊, 朱增伟, 章 勇, 朱 栋, 朱 荻. 基于复杂型面薄壁零件成形的电铸试验研究[J]. 航空学报, 2010, 31(10): 2068-2074.
LI Xue-lei, ZHU Zeng-wei, ZHANG Yong, ZHU Dong, ZHU Di. Experimental research on electroforming of complex parts with thin wall [J]. Chinese Journal of Aeronautics, 2010, 31(10): 2068-2074.
[4] HART T, WATSON A. Electroforming [J]. Metal Finishing, 2000, 98(1): 388-399.
[5] MALONE G A. Investigation of electroforming techniques: Literature analysis report [R]. NASA-CR-134776. US NTIS, 1974: 76.
[6] SAMPLE C H, KNAPP B B. Physical and mechanical properties of electrodeposited nickel at elevated and sub-zero temperature [C]// Proceedings of Symposium on Electroforming. Philadelphia: ASTM-STP, 1962: 32-42.
[7] 许伟长, 戴品强. 电沉积微纳米镍的组织结构与力学性能[J]. 中国有色金属学报, 2009, 19(10): 1815-1821.
XU Wei-chang, DAI Pin-qiang. Microstructures and mechanical properties of electrodeposited microcrystalline and nano- crystalline Ni [J]. The Chinese Journal of Nonferrous Metals, 2009, 19(10): 1815-1821.
[8] 王 玉, 袁学韬, 俞宏英, 孙冬柏, 李辉勤. 脉冲电沉积工艺对镍镀层结构与硬度的影响[J]. 材料科学与工艺, 2010, 18(1): 89-95.
WANG Yu, YUAN Xue-tao, YU Hong-ying, SUN Dong-bai, LI Hui-qin. Influence of pulse parameters on the microstructure and microhardness of nickel electrodeposits [J]. Materials Science and Technology, 2010, 18(1): 89-95.
[9] MCGEOUGH J A, LEU M C, RAJURKAR K P, de SILVA A K M, LIU Q. Electroforming process and application to micro/macro manufacturing [J]. Annals of the CIRP, 2001, 50(2): 499-514.
[10] 刘仁志. 实用电铸技术[M]. 北京: 化学工业出版社, 2006: 211-213, 241-242.
LIU Ren-zhi. Electroforming technology [M]. Beijing: Chemical Industry Press, 2006: 211-213, 241-242.
[11] SILAIMANI S M, JOHN S. Review on recent advances in electroforming during the last decade [J]. Bulletin of Electrochemistry, 2001, 17(12): 553-560.
[12] 申俊杰, 田文怀, 王 雷, 冯传超, 杨 峰. 电铸液中添加剂含量与电铸镍晶体组织和性能的关系研究[J]. 兵器材料科学与工程, 2009, 32(1): 69-71.
SHEN Jun-jie, TIAN Wen-huai, WANG Lei, FENG Chuan-chao, YANG Feng. Research on relation between additive content in the electroforming solution and microstructure and mechanical properties of electroformed nickel [J]. Ordnance Material Science and Engineering, 2009, 32(1): 69-71.
[13] DIBARI G A. Nickel plating [J]. Plating Surf Finish, 2004, 91(8): 23-26.
[14] ZHU Di, ZHU Zeng-wei, QU Ning-song. Abrasive polishing assisted nickel electroforming process [J]. CIRP Annals— Manufacturing Technology, 2006, 55(1): 193-196.
[15] ZHU Zeng-wei, ZHU Di, QU Ning-song. Mechanical electro- deposition of bright nanocrystalline nickel [J]. Science in China Series E: Technological Sciences, 2008, 51(7): 911-920.
[16] 温诗铸, 黄 平. 摩擦学原理[M]. 第3版. 北京: 清华大学出版社, 2008: 241-245.
WEN Shi-zhu, HUANG Ping. Principles of tribology [M]. 3rd ed. Beijing: Tsinghua University Press, 2008: 241-245.
(编辑 陈卫萍)
基金项目:国家自然科学基金资助项目(50975143);航空科学基金资助项目(2009ZE52048);南京航空航天大学基本科研业务费专项科研项目(1005-XHA09009)
收稿日期:2011-07-20;修订日期:2011-12-10
通信作者:章 勇,博士研究生;电话:025-84895912;E-mail: zy6982@163.com