
Microstructure and properties of unleaded free-cutting brass containing stibium
XIAO Lai-rong(肖来荣)1,2, SHU Xue-peng(舒学鹏) 1,2, YI Dan-qing(易丹青)1,2,
ZHANG Xi-min(张喜民) 1,2, QIN Jing-li(覃静丽) 1,2, HU Jia-rui(胡加瑞) 1,2
1.School of Materials Science and Engineering, Central South University, Changsha 410083, China;
2.The Key Laboratory of Non-ferrous Metals, Materials Science and Engineering, Ministry of Education,Changsha 410083; China
Received 15 July 2007; accepted 10 September 2007
Abstract: A new environmental friendly cutting brass containing stibium instead of lead was produced by casting and rolling. The microstructure was observed and the mechanical, dezincification and cutting properties were studied. The results show that the white particles distribute in both grains and grain boundaries, and the particles are mainly intermetallics containing stibium. The tensile strength, yield strength and elongation percentage of half-hard Sb-brass is 461.72 MPa, 213.3 MPa and 15.67%, respectively. Corresponding to HPb59-1 by the size as well as appearance of the chips and the mechanism of free-cutting, the cutting property of unleaded free-cutting Sb-brass is excellent. The unleaded Sb-brass has excellent dezincification corrosion resistance, and the average depth of longitudinal section is about 295.4 μm, while the average depth of lateral section is about 214.7 μm, and it is feasible to develop a new unleaded free-cutting Sb-brass.
Key words: nonleaded; free-cutting brass; stibium; microstructure; property
1 Introduction
Because of the excellent cutting property and wear-resisting property, lead brass has been applied in various fields, such as electronic equipment connectors, device components, water pipes of water system, water faucet, valves, pipe connections and hydraulic valves used in automobile, fire control and airplane, but Pb is a kind of element harmful to environment and human being[1-2]. In recent years, with the rising of people’s environment protection consciousness, many bans of limiting the use of Pb-brass were promulgated, and it will be facing strict limits and challenges, so it will be a great subject facing to the world metal material manufactures to develop newly unleaded brass[3-5].
Up to now, many research patents of new technology of unleaded brass have been promulgated in internal and overseas[6-8]. Pb is replaced by Bi and Si in alloys, and it can reach ideal practice purpose. It mainly can be divided into Cu-Zn-Bi and Cu-Zn- Si[9-12], as well as some adding carbon, magnesium, tellurium, and it can reach the purpose of nonleaded. But all those systems may have the disadvantage of high price, complex technology and weak cutting property[13]. In this experiment we mainly considered to add some Sb to replace Pb in brass, and also added some Ce and Ti to improve the integrated properties.
2 Experimental
2.1 Alloy preparation
The crude material were 2# electrolysis copper, pure Zn and pure Sb, as well as some Ce and Ti. The ingots were melt in the line-frequency furnace, Cu and Ti was added at the temperature of the melting point of Cu, and Zn and Ce was added at lower temperature about 450 ℃, So it can reduce the melting loss of low-melting point metal. The casts were cuboid with the size about 50 mm×20 mm×90 mm, then after uniform heat treatment, the cast ingots were rolled into less 2 mm thickness sheets. The composition of alloy is listed in Table 1.
Table 1 composition of alloy(mass fraction, %)

2.2 Properties measurement
Stretch experiment at room-temperature was carried out on CSS44100 multifunction material electronic tester, and the strength of extension and the elongation percentage were tested. Also the Rockwell hardness was tested in 69-1 optical hardness-testing device. Using NEOPHOT221 OM, Sernir 200 SEM and Gensis60 EDS to observe the microstructure; making tensile samples and dezincification corrosion samples and the cutting test were carried out in the CW6163A horizontal plain lathe, through the analysis of the cutting force and the cuttings, we can check its cutting property.
3 Results and discussion
3.1 Microstructure
Figs.1 and 2 show the micrographs of ingot before and after uniform heat treatment, respectively. It can be seen from Fig.1 that the alloy cast structure mainly consists of α phase and β phase clearly, and the hoar zones is α phase, the dingy zone is β phase. The ingot alloy microstructure has many fir-tree crystals and the size of crystals are non-homogeneous, and mainly is the lath-shaped, also its directionality is very poor, in some zones there are a few thin equiaxed grains, maybe it was caused by the non-adequate distribution of the grain refiner in the smelting. From Fig.2 we can see that there is no bulky fir-tree crystal and compared to its ingot structure, the crystal grains have become into nub and spherical grains, also in some places there still has the lath-shaped crystal. The content of β phase is increased after uniform heat treatment, because of its high temperature plastic property, it make the structure foundation of rolling. Also both in Figs.1 and 2 there are some spotted state educts in α phase and the phase boundaries between α phase and β phase, and after uniform heat treatment, the spotted state educts increase apparently.
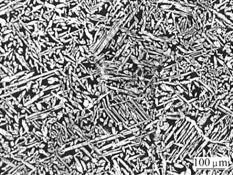
Fig.1 Ingot micrographs of unleaded Sb-brass
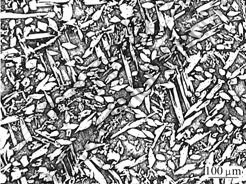
Fig.2 Micrographs of unleaded Sb-brass after uniform heat treatment
Figs.3 and 4 show the SEM micrographs of alloy ingot before and after uniform heat treatment respectively. There are many white spotted state educts in SEM micrographs, and it mainly exists in α phase as well as phase boundaries between α phase and β phase, there are also fewer in β phase, and the diameter of those white spherical educts is less than 1 μm. In order to identify those phases, choosing some points in different position to do EDS analysis, and point A and F is the white educt in α phase, while points B and G is the educt in phase boundary between α phase and β phase, points C and H is the white educt in β phase, D and E is the small zones in α phase and β phase respectively, and detailed EDS datas are listed in Table 2.
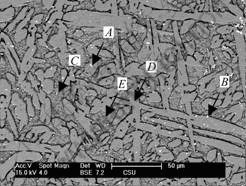
Fig.3 Ingot SEM micrographs of unleaded Sb-brass

Fig.4 SEM micrographs of unleaded Sb-brass after uniform heat treatment
Table 2 EDS results of Sb-brass at different position(mole fraction, %)

From the data in Table 2 we can see that there are no dissociative Sb both in α phase and β phase, and Sb mainly exists as compounds, judged by its pattern, distribution and elements percentage composition, we can consider it as Cu-Zn-Sb-Ce compound. Reported in Refs.[14-15], Sb is formed to sosoloid with Zn priory in alloy and gathered in grain boundaries; while Ce and Sb can form high melting-point intermetallic compound hard-fragile phase, and it can control the degree of softening and embrittlement of alloy effectively. It will improve the property of cutting to make those particles containing Sb uniform distribution.
Figs.5 and 6 show the alloy micrographs of longitudinal section and lateral section after rolling respectively. It can be seen from Fig.5 that the grains have been stretched along the rolling direction after rolling, it formed visible fibrous tissue, and the fibrous tissue was broken in a certain extent, so it shows that the dynamic recovery phenomenon occurs in the course of rolling, but the dynamic recrystallization phenomenon does not occur and the stretched structure is reserved. From Fig.6 we can see that α phase and β phase distribute exiguously and homogenously and it further validates that it does not appear obvious dynamic recrystallization phenomenon in the course of rolling. Figs.7 and 8 show the alloy SEM micrographs of longitudinal section and lateral section after rolling respectively. In the same way, choosing some points in
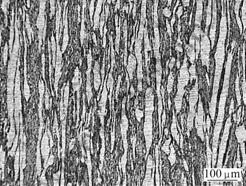
Fig.5 Longitudinal section micrographs of unleaded Sb-brass after rolling
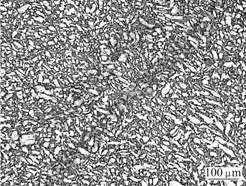
Fig.6 Lateral section micrographs of unleaded Sb-brass after rolling
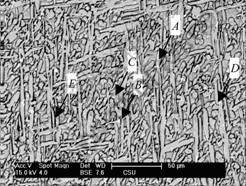
Fig.7 Longitudinal section SEM micrographs of unleaded Sb-brass after rolling

Fig.8 Lateral section SEM micrographs of unleaded Sb-brass after rolling
different position to do EDS analysis, and point A is the white educt in α phase, while point B is the educt in phase boundary between α phase and β phase, point C is the white educt in β phase, D and E is small zones in α phase and β phase respective, and detailed EDS data are listed in Table 3.
From those data in Table 3 we can see that the compound is accordant with those in Fig.4 and it is Cu-Zn-Sb-Ce compound. It will improve the property of cutting to make those particles contain Sb uniform distribution.
Table 3 EDS results of Sb-brass at different positions(mole fraction, %)
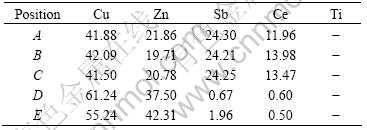
3.2 Mechanical property of alloy
The mainly mechanical property of alloy is listed in Table 4.
Table 4 Mechanical properties of unleaded free-cutting Sb-brass
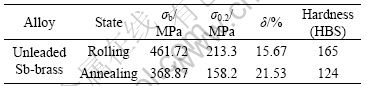
Elongation percentage and contraction of cross area is most important index judging the plasticity of materials. It can be seen from Table 4 that the elongation percentage of lead-unleaded Sb-brass reaches 15.67%, and we can judge it good basically.
The tensile strength of half-hard HPb59-1 is about 470-550 MPa, while the yield strength is about 350 MPa and its elongation percentage is greater than 7%. See Table 4, the ensile strength of unleaded Sb-brass in this experiment can reach 461.72 MPa and its elongation percentage is 15.67%, while the yield strength is only 213.3 MPa. The tensile strength is less than HPb59-1, while the yield strength is greatly descended. The reason is as follows[16]: although it has some solution effect with adding Sb and also can increase the strength of alloy, but because of the brittleness of Sb(the Sb compound is brittle too), it restricts the increasing of strength in a certain extent. The impurity is easily gathered at grain boundaries and segregated, and it appears some brittle compound in grains, all those factors will descend the strength of alloy. After annealing, the strength descends obvious and the elongation percentage increases in a certain extent; the hardness of alloy is higher than HPb59-1, and it accords with the request of experiment.
3.3 Dezincification corrosion resistance
The dezincification corrosion experiment was followed the standard of GB10119-88 in constant temperature water bath. The samples were placed in a beaker with standard measured solution of 1.0% CuC12 vertically(the amount of solution is direct proportion with the superficial area of samples and every 100 mm2 exposed areas with 250 mL solution), the water temperature is (75±1)℃, and the corrosion time is 24 h. After corrosion, cutting off the sample along the middle, and sampling, after polishing, in NEOPHOT221 microscope the depth of corrosion was measured. After measuring many couple samples, the average depth of longitudinal section is about 295.4 μm, while the average depth of lateral section is about 214.7 μm. It is better than HPb59-1, the possible reasons are as follows: the nature chemical stability of Sb is excellent and distributes dispersedly in alloy structure with compound, so it prevents the further corrosion of Zn in a certain extent[17]; on the other hand, Ce and Ti can refine the grains and purify the grain boundaries, reducing the corrosion rate in a certain extent and increasing the dezincification corrosion resistance.

Fig.9 Longitudinal section dezincification corrosion micrographs of unleaded Sb-brass after rolling
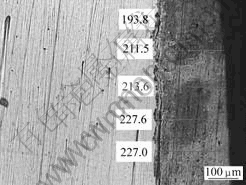
Fig.10 Lateral section dezincification corrosion micrographs of unleaded Sb-brass after rolling
3.4 Cutting test
Because of the restricting of experiment conditions, the sheets after rolling cannot be done the cutting test, so we re-melt following the same ratio of mixture and cast round bars. After extruding we do the cutting test in CW6163A plain lathe using the straightening samples of φ14-16 round bars, the cutter material is Ys8, the way of cutter is turning excircle for 1 mm, and the rotational speed of main shaft is 407 r/min.
The cuttings of unleaded Sb-brass and HPb59-1 were showed in Fig.11(a) and (b) respectively. Both cuttings are tiny, and the cuttings of HPb59-1 are slightness, just like short needle, while the cuttings of unleaded Sb-brass like fragmental and its inner surface is smooth; The cutting course of unleaded Sb-brass was stable and fluctuation was slightly, the cutting surface was smooth and the roughness of surface was very small, and we can consider it is better than HPb59-1 basically.
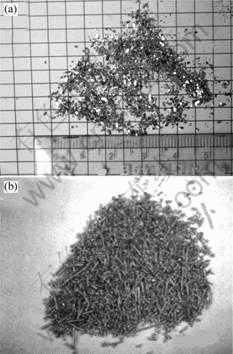
Fig.11 Cuttings of alloy: (a) Cuttings of Sb-brass; (b) Cuttings of HPb59-1
In HPb59-1, Pb is dissociative and is not dissolved in brass, there is plenty of Pb particles in the line of contact with cutter, and those dispersed Pb particles play an important role in crushing cuttings, decreasing the bonding and welding together cuttings to the cutter, so it can crush the cuttings and decrease the size of cuttings. Because of the lower melting temperature of Pb(the melting temperature of Pb is 327.5 ℃), accordingly it will melt instantaneously in local while the cutter touched the work pieces. It is helpful to modify the shape of cuttings and plays the role in smoothing the cutter and keeps the cutter tartness[18], so its cutting property is good.
The second-phase particles containing Sb in unleaded Sb-brass are easily to be brushed under the effect of shearing stress when touching with the cutter, and the stress concentration, easily to form the cracks and expand. It will crush the cuttings and prevent the discontiguous growth of cuttings. It finally decreases the size of cuttings and increases the cutting property of unleaded Sb-brass[16].
4 Conclusions
1) There are white precipitated phase both in α phase and β phase, it is mainly compound containing Sb.
2) The ensile strength of unleaded Sb-brass reaches 461.72 MPa and its elongation percentage is 15.67%, while the yield strength is only 213.3 MPa, the total mechanical property can be considered excellent.
3) The dezincification corrosion resistance of un- leaded Sb-brass is excellent, and the average depth of longitudinal section is about 295.4 μm, while the average depth of lateral section is about 214.7 μm, and the real mechanism needs to do further research.
4) Judging by the size of cuttings and the analysis the mechanism of easily cutting, cutting property of nonleaded free-cutting brass containing stibium is excellent, and it is feasible to develop a new unleaded Sb-brass.
References
[1] EI-SHERIF R M,ISMAIL K M, BADAWY W A. Effect of Zn and Pb as alloying elements on the electrochemical behavior of brass in NaC1 solutions[J]. Electrochimic Acta, 2004, 49(28): 5139-5l50.
[2] KARALEKAS P C, CRAUN G F Jr. Lead and other trace metals in drink water in the Boston metropolitan area[J]. J New England Water Works Assoe, 1976, 90: 160-172.
[3] JANG Y H, KIM S S, KIM I S. Effect of alloying elements on elevated temperature tensile ductility of Bi added, Pb-free brass[J]. Journal of the Korean Institute of Metals and Materials, 2004, 42(7): 537-542.
[4] YOU S J, CHOI Y S, KIM J G. Stress corrosion cracking properties of environmentally friendly unleaded brasses containing bismuth in Mattsson’s solution[J]. Mater Sci Eng A, 2003, 345(122): 207-214.
[5] NAKANO A, HIGASHIIRIKI K, ROCHMAN N T. Removal of lead from brass scrap by compound-separation method[J]. Journal of the Japan Institute of Metals, 2005, 69(2): 198-201.
[6] MYERSON A S. Treating brass components to eliminate leachable lead: US, 6191210[P]. 2001.
[7] HISASHI T, KEIICHIRO O, YOSHITO S. Lead-free copper base alloy material: JP, 2000-169919[P]. 2000.
[8] GUO Jun-hua, HE You-qi, SHI Hang-xing. Unleaded easy-cutting brass: CN, 200310109162.0[P]. 2003. (in Chinese)
[9] DOWNEY J P. Reducing lead leachate in brass plumbing components: US, 5454876[P]. 1995.
[10] JOE S L. Leaching of lead from brass plumbing fixtures: US, 5707421[P]. 1998.
[11] HIROYUKI T. Lead-free, free-cutting brass alloy material and production method thereof: JP, 2003-277855[P]. 2003.
[12] PANG Jin-shan, XIAO Yin-xin. Study of nonleaded easy-cutting brass[J]. Journal of Guangdong University of Technology, 2001. 18(13): 63-66. (in Chinese)
[13] HUANG Jin-song, PENG Chao-qun, ZHANG Si-qi, HUANG Bo-yun. Unleaded free-cutting brass alloy[J]. The Chinese Journal of Nonferrous Metals, 2006,16(9): 1486-1493. (in Chinese)
[14] ISMAIL K M, RABAB M. Effect of Zn and Pb contents on the electrochemical behavior of brass alloys in chloride-free neutral sulfate solutions[J]. Electrochimica Acta, 2004, 49: 5151–5160.
[15] ZHANG Ming, XIE Xiao, CAI Zi-hua, MENG Xian-qi. The new environmental protection lead-free easy-cutting lower Bi, Sb brass and its manufacturing method: CN, 200510050425.4[P]. 2005. (in Chinese)
[16] ZHANG Ming, ZHANG Si-qi, CAI Zi-hua. Unleaded free-cutting brass alloy: CN, 200410015836.5[P]. 2004. (in Chinese)
[17] CHATAIN D, WYNBLATT P, ROHRER G S. Anisotropic phenomena at interfaces in bismuth-saturated copper[J]. Scripta Materialia, 2004, 50(5): 565-569.
[18] WANG Zhu-tang, TIAN Rong-zhang. The directory of copper alloy and treatment[M]. Changsha: Central South University Press, 2002. (in Chinese)
(Edited by YANG Hua)
Foundation item: Projects (2006BRE03B02) supported by the Key Project of 11th Five-Year Plan of China
Corresponding author: XIAO Lai-rong; Tel: +86-731-8830137; E-mail: xiaoxiaox@vip.sina.com