
Effect of process parameters on density of magnesium alloy parts by low-pressure expendable pattern casting
LI Ji-qiang(李继强), FAN Zi-tian(樊自田), DONG Xuan-pu(董选普)
State Key Laboratory of Material Processing and Die and Mould Technology
Huazhong University of Science and Technology, Wuhan 430074, China
Received 15 July 2007; accepted 10 September 2007
Abstract: The combination of magnesium alloys with the low-pressure expendable pattern casting (LP-EPC) process would bright future for application of magnesium alloys. The researches are focused on the effect of process parameters on the internal casting quality of magnesium alloy parts. AZ91D magnesium alloy castings were produced for different combinations of the LP-EPC process parameters. Specifically, pouring temperature, vacuum, filling velocity and coupling action of these factors were manipulated to observe their effect on the casting porosity and density distribution. The results indicate that the pouring temperature with LP-EPC process is lower than it in gravity casting. The selected process parameters, such as vacuum, filling velocity and coupled modes of them, must ensure melt metal flowing front profile exhibiting smooth and convex shape. The optimal process parameters for the castings are pouring temperature 983-1 023 K, vacuum 0.02-0.03 MPa, filling velocity 60-95 mm/s, and simultaneous filling with sucking.
Key words: magnesium alloy; low-pressure expendable pattern casting; process parameters; density
1 Introduction
The production and utilization of magnesium alloy has seen a dramatic increase in the last decade because of its huge potential in the automobile industry for increased fuel efficiency via vehicle mass reduction[1-3]. Magnesium alloy components are usually fabricated by various casting processes because of low formability near room temperature. The applicable methods are high-pressure die-casting and all kinds of gravity casting such as sand, permanent and semi-permanent mould casting. Other relevant production technologies are squeezing casting, semi-solid casting and rapid solidification[4-5]. The high-pressure die-casting dominates among the casting methods used worldwide. However, entrapped gas pores as a result of high fill-up-rate make the casting impossible for heat treatments, and the presence of bands of porosity and segregation in die-casting has a significant effect on the mechanical properties[6-7]. Furthermore, the complicated and expensive production equipment also restricts its application. In order to exploit the benefits of magnesium alloy, it is necessary to develop alternative processing that can effectively produce complex, high-precision casting with good mechanical properties at low expense.
The lost foam casting (LFC) processing or evaporative casting processing is a low-cost technique for manufacturing complicated and near-net-shape castings[8]. In the LFC process molten metal is poured into a foam pattern that has been coated with refractory material and surrounded with unbounded sand. The pattern evaporates and molten metal takes place of the pattern, and the metal solidifies in the shape of the pattern. The LFC process can offer advantages and significant savings over traditional green sand casting by producing castings with lower dimensional tolerances and complex geometries, eliminating or reducing machining and assembly operation, and providing cleaner and quieter working conditions. However, the LFC processing of magnesium alloys faces critical challenges due to the high chemical reactivity of magnesium itself and low latent heat compared with aluminum alloys[9].
In order to avoid defects in magnesium castings associated with the conventional lost foam process, a novel lost foam process has been specially developed, in which a low pressure is introduced for counter gravity filling[10-12]. Therefore, laminar flow and fully eliminating turbulence are achieved during mould filling. This processing will reduce the exposure time in air for magnesium alloy melt and overcome the fill problems for magnesium alloy in conventional EPC process.
As a newly developed casting process, there are few open documents to describe its characteristics and little information to guide us in practice. Therefore, in this work the authors aim at the effect of process parameters on the internal casting quality of magnesium alloy parts and investigating the optimal processing parameters for low-pressure EPC process to produce magnesium alloy castings without any defects.
2 Experimental
2.1 Experimental parameters
The Low-pressure EPC Process parameters were varied with the view to manipulating the mass fraction of the liquid-EPS residue generated during mold filling. The main studied parameters and their respective levels are summarized in Table 1.
Table 1 Experimental conditions used in experiment
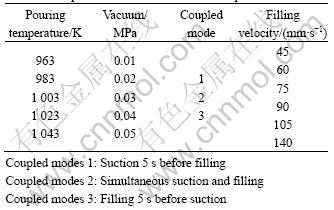
2.2 Expendable pattern and coating
The experimental casting pattern and its gating system were prepared using the most widely used expandable polystyrene (EPS) board by a hot wire cutter, which had a bulk density of 0. 020 g/cm3. In these tests, foam pattern is shown in Fig.1.
The glued clusters were coated with specially confected refractory slurries with Baume 45. Then the coated clusters were put into an oven to dry for 24 h at 50 ℃. The clusters were coated and dried twice or even more times until the coating thickness reached 0. 5 mm.
2. 3 Molding, melting and pouring
The coated patterns were placed into an top-open steel flask with a plenum chamber on its base, and subsequently filling dry silica sand (40-70 size) to enclose the coated pattern and then compacting the dry sand using a three-dimension compaction table. After the coated pattern was properly embedded and packed with dry sand, a plastic film of 0. 1 mm in thickness was used to cover the open-top of the flask.
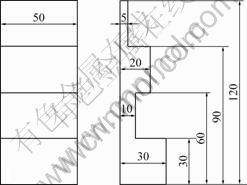
Fig.1 Experimental foam patterns
AZ91D magnesium alloy ingots were melted and superheated in the resistance furnace. The melt temperature was measured with a chormel-alumel thermocouple. When the alloy began to melt, a mixture gas of 0.2%-0.5% sulphur hexafluoride (SF6) in nitrogen was flowed to the melt surface to protect magnesium alloy from oxidizing and burning. Once the melt was heated to 1 013 K, 0.5% grain refiner was added to the melt whilst continuously stirring the melt for 5 to 8 min for a uniform distribution of the grain refiner. After settling down and deslagging, the flask with coated EPS pattern was positioned on the top of furnace and vacuum was applied to the flask for fixing the dry sand. Then the filling procedure began to operate through a mold-filling control system.
2. 4 Measurement
In order to assess the casting homogeneity, casting density was determined by the Archimedes Principle. Sample specific gravity was obtained from Eqn.(1). A electronic analytical balance was used to measure the mass of the casting samples with an accuracy of 0.001 g. A 0.14 mm thick thread was used to suspend casting specimens in a cup filled with water. Care was taken to prevent the specimens from touching the walls of the cup. Further more, image analysis of metallographic samples was carried out to quantify the combined (gas and solidification shrinkage) porosity levels.
(1)
where mair is mass of sample in air; ms/w is mass of sample (suspended on a thread in a cup of water), cup and water; mc/w is mass of cup and water.
3 Results and discussion
Casting parameters affecting the relative amount of the EPS pyrolysis products in the casting cavity were seen to have a statistically significant effect on the casting porosity. Fig.2 presents the average casting density for the respective casting conditions. When the process parameters are 1 003 K pouring temperature, 0.03 MPa vacuum, 75 mm/s filling velocity with simultaneous suction and filling, the density of castings is the maximal.
If think about the measurement error of experiments and the goal of LP-EPC process adapting to different casting, we can conclude that the optimal process parameters for the castings are 983-1 023 K pouring temperature, 0.02-0.03 MPa vacuum, 60-95 mm/s filling velocity with simultaneous suction and filling. And the density of castings is changed from 1.796 g/cm3 to 1.807 g/cm3, which agrees with the standard value (1.810 g/cm3)[13]. In casting process, lower values of the process parameters value were used for the thicker walled parts, and higher values of the process parameters were applied to thin-walled and complicated parts so as to gain perfect casting. Fig.3 displays the casting with low-pressure lost foam casting process. It was found that the casting production resulted in a major mass reduction of gating system without impairing quality.
3.1 Effect of pouring temperature on density
Generally, the pouring temperature of gravity lost foam casting process would higher 30-50 ℃ than sand casting. However, excessive pouring temperature not only aggrandizes energy consumption but also deteriorates molten magnesium alloy oxidation and inspiration. Moreover, excessive pouring temperature will induce more pyrolysis products and lead to shrinkage porosity (as Fig.4(a)), cavity or sand penetration defects, which decrease the casting density. The pouring temperature of melt magnesium alloys in low-pressure lost foam casting process is not needed to be too high, which provides adequate heat energy to ensure complete foam pyrolysis and full filling is enough. In fact, the castings can display good surface quality and approach the theoretical density of 1.810 g/cm3 using lower pouring temperature, such as 1 003 K pouring temperature (as Fig.4(b)).
3.2 Effect of vacuum on the density
The vacuum could improve the rigidity of the dry sand mould of EPC to overcome mould expansion or collapsion. Furthermore, vacuum sucking could also increase the filling pressure differential, the foam pyrolysis product escaped rate and molten metal filling velocity[14-15]. The application of higher vacuum established a pressure gradient at the metal-mold interface, which caused the liquid metal front to change its profile from convex to concave (Fig.5)[16-17]. This change of the metal front profile was possibly an additional factor which attributed to the entrapment of the liquid-EPS residue in the casting. Due to the concave profile, the liquid metal advanced preferentially along the mold walls and the liquid-EPS products possibly agglomerated in the center regions, thus likely remaining entrapped in the solidified casting (as Fig.6).
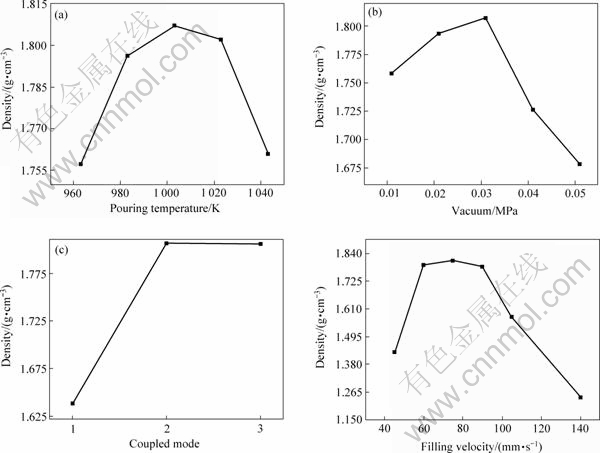
Fig.2 Average casting density with different parameters
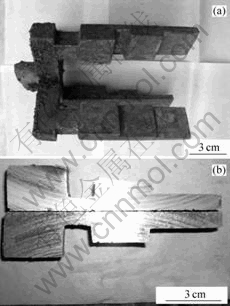
Fig.3 Castings produced by LP-EPC process (983 K, 0.02 MPa, 90 mm/s and simultaneous suction and filling): (a) Macroscopic; (b) Cross section
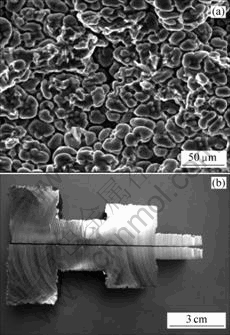
Fig.4 Effect of pouring temperature on casting: (a) Porosity defects, 1 043 K; (b) Cross section, 1 003 K
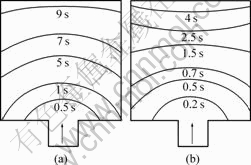
Fig.5 Metal front profile with different vacuums: (a) Low-vacuum; (b) High-vacuum
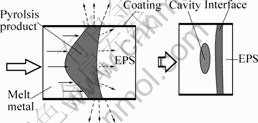
Fig.6 Mode of liquid-EPS products entrapped in casting
3.3 Effect of coupled modes on density
The reasonable matching of the gas pressure in crucible and the vacuum degree in sand box plays an important role in the filling quality of the LP-EPC process. As Fig.2(c) shows, the casting has lower density when we use vacuum sucking and mould filling. The reason is that the vacuum field in sand box firstly established and liquid metal advanced preferentially along the mold walls, which induced the liquid-EPS products possibly agglomerated in the melt metal (Fig.7(a)). However, when mould filling comes before vacuum sucking or simultaneous performs, the melt metal of flowing front would move smoothly and its profile is not concave (Figs.7(b)-(c)). The cast parts would obtain internal compact structure and perfect exterior surface. The experimental results also indicated that the castings would consume more metal on sprue or gate if we use coupled modes 3. By comparing all of the effect factors, it is indicated that the optimal coupled mode is simultaneous suction and filling.
3.4 Effect of filling velocity on density
The reasonable filling velocity of melt metal is a main difficult problem in the LP-EPC process. Generally, too low filling velocity would lead to misrun defects or incomplete filling, such as 45 mm/s. As the filling velocity of metal increases, the density of casting also increases and reach maximum when the filling velocity of metal is 75 mm/s. The misrun or other pyrolysis defect is not easy to occur in the castings. If the filling velocity is re-raised (less than 105 mm/s), the metal-foam interface exhibits smooth and convex shape. As the filling velocity is too high, for example 140 mm/s, the melt metal of flowing front would not move smoothly and cause the liquid metal to change its flowage from laminar current to turbulent current, even jet current (as Fig.8)[18-19]. A lot of pore defects would be found at the inner and top end of castings. This is not surprising, because when the filling velocity is too high and there isn’t sufficient time for the liquid polymer to be removed through the coating layer, the pyrolysis products of the foam pattern would be pushed ahead of the metal front, some pyrolysis products would also be engulfed in the molt metal to form pore defects.
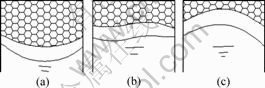
Fig.7 Metal front profiles with different coupled modes
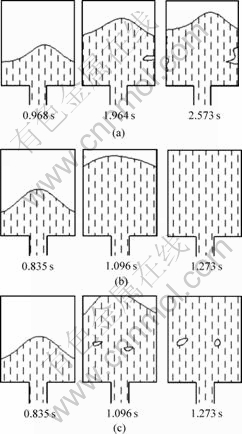
Fig.8 Metal front profiles at different filling velocities: (a) Low filling velocity; (b) Middle filling velocity; (c) High filling velocity
4 Conclusion
1) The temperature with LP-EPC process is lower than it in gravity casting. In order to obtain perfect casting, the vacuum, filling velocity and coupled modes of them, must ensure metal front profile exhibiting smooth and convex shape.
2) The optimal process parameters for the castings are pouring temperature 983-1 023 K, vacuum 0.02-0.03 MPa, filling velocity 60-95 mm/s and simultaneous filling with sucking. Either less or higher than the casting parameters would lead to density decreasing.
References
[1] MORDIKE B L, EBERT T. Magnesium properties-application- potential[J]. Material Science and Engineering, 2001, A302(1): 37-45.
[2] KANEKO T, SUZUKI M. Automotive applications of magnesium alloys[J]. Materials Science Forum, 2003, 419-422(1): 67-72.
[3] COLE G S. Issues that influence magnesium’s use in the automotive industry [J]. Materials Science Forum, 2003, 419-422 (1): 43-50.
[4] FRIEDRICH H E, MORDIKE B L. Magnesium technology[M]. Germany: Springer, 2005.
[5] KLEINER S, BEFFORT O, WAHLEN A, UGGOWITZER P J. Microstructures and mechanical properties of squeeze cast and semi-solid cast Mg-Al alloys[J]. Journal of Light Metals, 2002, 2(4): 277-280.
[6] DAHLE A K, SANNES S, JOHN D H St, WESTENGEN H. Formation of defect s bands in high pressure die cast magnesium alloys[J]. Journal of Light Metals, 2001, 1(2): 99-103.
[7] DAHLE A K, LEE Y C, NAVE M D, MCDONALD S D. Development of the as-cast macrostructure in magnesium-aluminum alloys[J]. Journal of Light Metals, 2001, 1(1): 61-72.
[8] MARTLATT M, WWEISS D J, HRYN J N. Developments in lost foam casting of magnesium[J]. AFS Transactions, 2003(111): 1053-1060
[9] WU He-bao, FAN Zi-tian, HUANG Nai-yu, DONG Xuan-pu, TIAN Xue-feng. Process optimization for AZ91 Mg-alloy low-pressure EPC process[J]. Journal Wuhan University of Technology, 2005, 20(2): 42-44.
[10] THOMSON J P, XU S, SADAYAPPAN M. Low pressure casting of magnesium alloy AZ91 and AM50[J]. AFS Transactions, 2004(112): 985-994.
[11] BAST J, AISURADSE M, HAHN T. Advantages of low-pressure lost foam casting process[J]. AFS Transactions, 2004(112): 1131-1142.
[12] FAN Z T, JI S. Low pressure lost foam process for casting magnesium alloys[J]. Materials Science and Technology, 2005, 21(6): 727-734.
[13] AVEDESIAN M M, BAKER H. Magnesium and magnesium alloys—ASM specialty handbook[M]. Ohio: ASM International, 1999.
[14] BICHLER L, RAVINDRAN C. Effect of vacuum and selected LFC process parameters on mold filling of AZ91E casting[J]. AFS Transactions, 2006(114): 921-943.
[15] LIU Zi-li, HU Jing-yu, WANG Qu-dong, DING Wen-jiang, ZHU Yan-ping, LU Yi-zhen, CHEN Wen-zhou. Evaluation of the effect of vacuum on mold filling in the magnesium EPC process[J]. Journal of Materials Processing Technology, 2002(120): 94-100.
[16] FAN Zi-tian, WU He-bao, LI Ji-qiang, ZHANG Da-fu, DONG Xuan-pu, HUANG Nai-yu. Characteristics and practices of the low pressure-expendable pattern casting process for magnesium alloy[J]. Special Casting and Nonferrous Alloys, 2006, 26(1): 39-42.
[17] TIAN Xue-feng, FAN Zi-tian, HUANG Nai-yu. Study on mold filling in AZ91 alloy LFC process[J]. Journal of Materials and Metallurgy, 2006, 5(3): 226-230.
[18] WU H B, FAN Z T, HUANG N Y, DONG X P, TIAN X F. Mold-filling characteristics of AZ91 magnesium alloy in the low-pressure expendable pattern casting process[J]. Journal of Materials Engineer and Performance, 2005, 14(1): 132-135.
[19] WU He-bao. Study on mold filling and solidification of magnesium alloy in lost foam casting process under controllable pressure[D]. Wuhan: Huazhong University of Science and Technology, 2005.
Foundation item: Projects (50275058) supported by the National Natural Science Foundation of China
Corresponding author: LI Ji-qiang; Tel: +86-27-87543876; E-mail: andy050302@yahoo.com.cn
(Edited by CHEN Ai-hua)