Synthesis of LiCoxNi1-xO2 cathode materials from electrolysis Co-Ni alloys
YE Mao(叶 茂)1, WEI Jin-ping(魏进平)1, CAO Xiao-yan(曹晓燕)2,
ZHAI Jin-ling(翟金玲)1, WANG Xiao-yu(王晓宇)1, SUN Xin(孙 欣)1, YAN Jie(阎 杰)1
(1. Institute of New Energy Material Chemistry, Nankai University, Tianjin 300071, China;
2. College of Chemistry and Chemical Engineering, Ocean University of China,Qingdao 266003, China)
Abstract: The LiCoxNi1-xO2 (x=0.2, 0.5 and 0.8) cathode materials were synthesized by sintering the mixtures of lithium salt and CoxNi1-x(OH)2 (x=0.2, 0.5 and 0.8) which were achieved from corresponding CoxNi1-x alloys by electrolysis technique. The structure and electrochemical characteristics of the obtained LiCoxNi1-xO2 were studied by XRD, SEM, PSCA and charge-discharge cycling test. The results show that the electrochemical capacities of the LiCoxNi1-xO2 (x=0.2, 0.5 and 0.8) materials are improved with the increase of the Ni content. The electrochemical performance of LiCo0.2Ni0.8O2 made in oxygen atmosphere has higher charge-discharge capacity and better cycleability compared with the one made in air atmosphere.
Key words: cathode materials; electrolysis; LiCoxNi1-xO2; Co-Ni alloys CLC number: TM912.9
Document code: A
1 INTRODUCTION
Lithium ion battery is considered the most promising energy storage device at present because of its high discharge voltage, long cyclic lifetime and lower self-discharge rate[1]. The cathode materials being used now are usually LiCoO2, LiNiO2 and their derivatives with ordered layered structure like α-NaFeO2[2]. Among the materials, LiCoO2 is the one used most widely in commercial products, because its preparation is simple and convenient, and the electrochemical performance is fairly good compared with the others[3]. LiNiO2 is another cathode material candidate and also attracts much attention due to its low cost and the possibility of larger capacity than LiCoO2 in practice (LiCoO2, 140mA·h/g; LiNiO2, 200mA·h/g)[4]. But it is well known that the property of LiNiO2 strongly depends on the stoichiometry and structure while the preparation is difficult[5-9]. Moreover, the cyclic stability of the LiNiO2 electrode is not good, because LiNiO2 may decompose and release O2 during charging, which causes unsafe problems for lithium ion battery, especially at elevated temperatures[10-12].
Since the structures of LiCoO2 and LiNiO2 are similar, which are helpful to form a solid solution in the overall composition domain[13], the compound LiCoxNi1-xO2 was studied extensively[14-19]. Their performances seem much better than those of LiNiO2 and LiCoO2, such as the thermal stability and capacity density. The capacity density in practice is about 180mA·h/g. The XAFS analysis results show that the oxidation of the Ni ion in Li1-x(Ni0.5Co0.5)O2 occurs immediately when the cell is charged, then stops at x of 0.5, whereas the oxidation of Co continues slowly until x of 0.8[20]. Therefore, the material is identified as one of the most promising cathode materials in lithium ion battery[15-17].
In this paper, cathode materials LiCoxNi1-xO2 (x=0.2, 0.5, 0.8) were synthesized by means of high-temperature solid-state reactions from relevant reactants CoxNi1-x(OH)2 (x=0.2, 0.5, 0.8) which were prepared from CoxNi1-x alloy by electrolysis method. Since cobalt and nickel have similar character and form an intergrowth in the mine, the cobalt and nickel were first mined as Co-Ni alloy, then the alloy was electrolyzed to get pure metal or corresponding salt. So the advantages of this method are: 1) the raw material is not a Ni-Co salt but Ni-Co alloy, so the cost is reduced; 2) the electrolyte can be recycled, which does little pollution to the environment.
2 EXPERIMENTAL
High purity metals with stoichiometrical ratios of Co to Ni(0.2∶0.8; 0.5∶0.5; 0.8∶0.2) were arc-melted in vacuum to get the CoxNi1-x alloy. The CoxNi1-x alloy was galvanostatically electrolyzed in 100g/L NaCl solution, then the electrolysis product was rinsed by water to remove Cl- anion, dried at 80℃ to obtain corresponding CoxNi1-x(OH)2. The CoxNi1-x(OH)2 (x=0.2, 0.5, 0.8) were mixed with LiOH (AR grade) by stoichiometric ratio 1∶1.05. The mixtures were ground in an agate mortar and pre-heated at 600℃ for 6h, then quenched to the room temperature and grounded again, followed by heat-treating in the range of 700-800℃ for 12h to get the LiCoxNi1-xO2 (x=0.2, 0.5 and 0.8). The structures of CoxNi1-x alloys and CoxNi1-x(OH)2 were determined by XRD (D-max/2500 Rigaku, Cu Kα radiation). The particle morphology of the powders was observed by a scanning electron microscopy (SEM, Hitachi S-3500N). The compositions of CoxNi1-x alloys and CoxNi1-x(OH)2 were determined by atomic absorption spectrometry(AAS).
Positive electrode for the electrochemical test was fabricated with active material, acetylene black as conducting additive and PTFE as binder mixed together in mass ratio of 80∶15∶5. Then the electrodes were dried at 120℃ for 24h. The coin cells for test were assembled in the Ar-filled glove box with the prepared positive electrode and lithium foil as the negative electrode,1mol/L LiPF6/EC (ethylene carbonate)+DEC (diethylene carbonate) (1∶1, volume ratio) as the electrolyte (Battery-grade, Merck Germany), and Celgard 2400 (polypropylene) films as the separator. The charged-discharged cycling was galvanostatically performed between 4.2-3.0V at a current of 30mA/g. To study the diffusion coefficient of Li+ through the electrodes, potential step chronoamperometry measurements were performed using a Solartron 1287 potentiostat.
3 RESULTS AND DISCUSSION
3.1 Preparation of CoxNi1-x(OH)2 and LiCoxNi1-xO2
The mechanism of electrochemical preparation for CoxNi1-x(OH)2 can be expressed as
Anodic reaction:
Co→CO2++2e, Ni→Ni2++2e(1)
Cathodic reaction:
2H2O+2e→H2↑+2OH-(2)
pH value of the solution near cathode increased during the electrolysis process, and the precipitation of Ni2+, CO2+ with OH- took place:
xCO2++(1-x)Ni2++2OH-→ CoxNi1-x(OH)2↓(3)
After being rinsed and dried, the Co-Ni hydroxide precipitation was mixed with LiOH by molar ratio of Li to CoxNi1-x of 1.05/1.00. The mixture was calcined to obtain the cathode material LiCoxNi1-xO2. The contents of Ni and Co in the alloys and the electrolysis products are listed in Table 1. As can be seen, the ratio of Ni to Co in the CoxNi1-x(OH)2 keeps accordant with that in the alloys, which means the preparation method is convenient.
Table 1 Molar ratio of Co to Ni in CoxNi1-x alloy and CoxNi1-x(OH)2
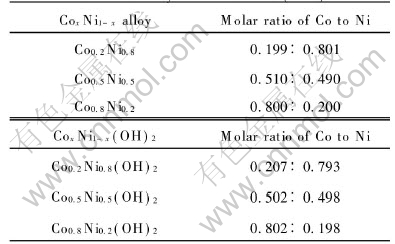
The XRD characterizations of Co, Ni and the CoxNi1-x alloy were investigated. All the XRD peaks for Co0.2Ni0.8 alloy are indexed as a single phase with a Ni fcc structure, indicating that the Ni and Co can be co-melted completely to form a solid solution alloy. Meanwhile, Co0.5Ni0.5 and Co0.8Ni0.2 alloys have the identical crystalline phase with a Co hexagonal structure. Fig.1 shows the XRD patterns of CoxNi1-x(OH)2 (x=0.2, 0.5 and 0.8) obtained by electrolysis of their corresponding CoxNi1-x(x=0.2, 0.5 and 0.8) alloys. It is found that the peaks of Co0.2Ni0.8(OH)2 can be assigned to β-Ni(OH)2 with a hexagonal structure, while Co0.5Ni0.5(OH)2 and Co0.8Ni0.2(OH)2 are detected to mainly have β-Co(OH)2 structure with a little Ni(OH)2·0.75H2O. Therefore, it can be concluded that the hydroxide precipitate can be obtained by electrolysis of Ni-Co alloy, and the structure of the hydroxide depends on the main element content in their corresponding alloys.
XRD patterns of the resulting oxides LiCoxNi1-xO2 are illustrated in Fig.2, which show a hexagonal structure with good crystallizability. Taking the pattern of LiCo0.2Ni0.8O2 as an example, the diffraction intensity of (003) plane (2θ=18.8°) is the strongest, the intensity ratio of I003/I104 is about 1.7857, whereas the intensity ratio of I003/I006 is near 25. Therefore, the structure of LiCo0.2Ni0.8O2 can be approved as the layered α-NaFeO2[14]. Moreover, as seen in Table 2, the values of a and c decrease, and the ratio of c/a is raised with the increasing Co content. In addition, the particle size distribution is homogeneous from SEM images as shown in Fig.3.
3.2 Electrochemical performance
In the galvanostatic charge-discharge cycling
Table 2 Crystallographic parameters of LiCoxNi1-xO2 cathode materials synthesized in different atmospheres
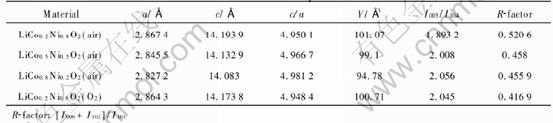
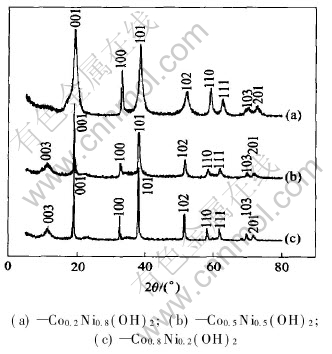
Fig.1 XRD patterns of CoxNi1-x(OH)2
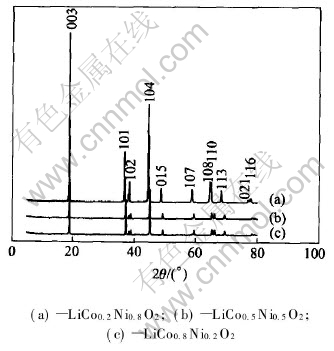
Fig.2 XRD patterns of LiCoxNi1-xO2 cathode materials
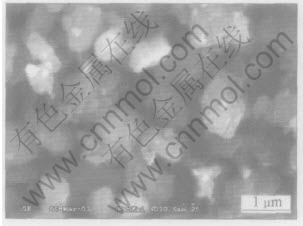
Fig.3 SEM images of LiCo0.2Ni0.8O2 synthesized in air atmosphere
test, the first charge/discharge capacity of the LiCoxNi1-xO2 (x=0.2, 0.5 and 0.8) cathode is 199/156, 180/146 and 168/146 (mA·h/g), respectively. After 20 charge/discharge cycles, the charge/discharge capacity of the LiCoxNi1-xO2 (x=0.2, 0.5 and 0.8) cathode is 150/146, 142/138 and 130/127 (mA·h/g), respectively. Its clear that the LiCo0.2Ni0.8O2 cathode material exhibits highest electrochemical charge/discharge capacity and best cycle stability. The higher Ni content in the oxide is beneficial to increasing discharge capacity and improving cycle stability of the electrodes.
In order to investigate the effect of the atmosphere during heat-treatment on the properties of LiCoxNi1-xO2, LiCo0.2Ni0.8O2 was prepared under air and oxygen flow respectively. The crystallographic parameters of LiCo0.2Ni0.8O2 cathode synthesized in different atmosphere are shown in Table 2. Compared with the LiCo0.2Ni0.8O2 prepared in air, the ratio of I003/I004 is higher and R-factor ([I006+I102]/I101) is lower for the material prepared in O2, which means that the crystallizability of the latter is better[21]. Fig.4 shows the charge-discharge cycle performance of LiCo0.2Ni0.8O2 cathode synthesized in different atmospheres. The capacity of the LiCo0.2Ni0.8O2 prepared in O2 atmosphere at the first charge-discharge cycle is 224mA·h/g for charging and 175mA·h/g for discharging, thus the efficiency is 78.1%. The charging/discharging capacity decreases gradually down to 170/164 (mA·h/g) after 40 cycles. The reversible capacity of the oxide made in air is relatively lower, and the reversibility seems stable for both samples.
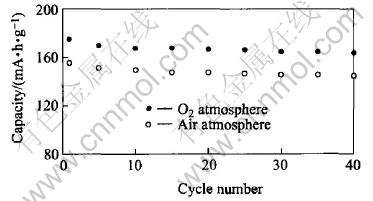
Fig.4 Charge-discharge cycle performance of LiCo0.2Ni0.8O2 cathode synthesized in air and O2 atmosphere at current rate of 0.2C
The diffusion coefficients D of Li+ in the LiCo0.2Ni0.8O2 cathode prepared in different atmospheres were studied by PSCA (potential step chronoamperometry) method in the potential step of 4.100V and 4.105V, as shown in Fig.5. It can be seen that the materials particle size is only about 1μm, the amount of PTFE binder is little, and the oxide powders can contact with each other very well. So the diffusion coefficient D can be calculated from the Cottrell region according to the follow formula[22]:
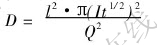
where Q is the total charge capacity involved in the potential step, l is the diffusion length which is considered a half of the average size of the particle. The diffusion coefficient D of Li+ in LiCo0.2-Ni0.8O2 cathode synthesized in air and O2 atmosphere is calculated to be 0.78×10-12cm2/s and 1.69×10-12cm2/s, respectively. After 40 charge-discharge cycles, the value of D for the latter reduces to be 1.36×10-12cm2/s. Obviously, the D values for the material prepared in O2 are larger than the one prepared in air atmosphere, indicating that the reaction polarization of the material synthesized in O2 atmosphere is lower and Li+ diffusion efficiency is higher. After 40 cycles, the diffusion coefficient of Li+ in the LiCo0.2Ni0.8O2 synthesized in O2 atmosphere can still be kept at a fairly high value, which means that the speed of Li+ insert/desert is still rapid.
Therefore, the atmosphere for preparing the oxide from the electrolysis product is important. Oxygen is favorable for the oxides preparation, because it is somewhat difficult for Ni2+ to be oxidized to Ni3+[23], while oxygen can promote the transformation and reduce the content of Ni2+ in the resulting oxide[24]. Based on the results of Rietveld refinement, some Ni2+ exists at Li+ site in LiNiO2[9]. As some nonstoichiometric LiNiO2 can be formed and there are several phase transitions during the charging-discharging process, the electrochemical capacity fading of the electrode will be serious. Based on the results, Ni2+ can be oxidized to Ni3+ in the material prepared in O2 atmosphere, so the content of Ni2+ can be reduced evidently[24], and the electrochemical properties are improved.
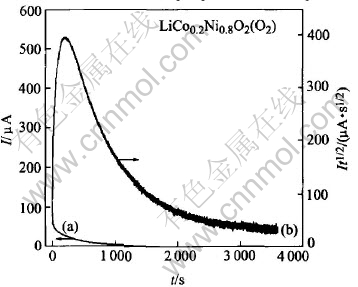
Fig.5 Relationship between I-t(a) and It1/2-t (b) of LiCo0.2Ni0.8O2 cathode synthesized in O2 atmosphere before charge-discharge cycle
4 CONCLUSIONS
A new method was investigated to prepare the cathode materials LiCoxNi1-xO2(x=0.2, 0.5 and 0.8) from the reactant Co1-xNix(OH)2 by electrolysis of CoxNi1-x alloy. Co1-xNix(OH)2 can be conveniently attained by electrolysis of corresponding alloy in the same stoichiometry. This method is more economical with less pollution compared with conventional method. The electrochemical performance of LiCoxNi1-xO2 (x=0.2, 0.5 and 0.8) materials is improved with the increase of the Ni content. Among them the LiCo0.2Ni0.8O2 exhibits the highest capacity and the best cycleability. The atmosphere in sintering process plays an important role in the performance of the cathode material. Compared with that sintered in air atmosphere, LiCo0.2Ni0.8O2 with better crystallizability, electrochemical character and higher Li+ diffusion rate can be achieved in oxygen atmosphere.
REFERENCES
[1]Scrosati B. Challenge of portable power[J]. Nature, 1995, 373: 557-558.
[2]Koksbang R, Barker J, Shi H, et al. Cathode materials for lithium rocking chair batteries[J]. Solid State Ionics, 1996, 84: 1-21.
[3]Ohzuku T, Uedo A. Solid-state redox reactions of LiCoO2 (R3m) for four-volt secondary lithium cells[J]. J Electrochem Soc, 1994, 141: 2972-2978.
[4]Arai H, Okada S, Sakurai Y, et al. Reversibility of LiNiO2 cathode[J]. Solid State Ionics, 1997, 95: 275-282.
[5]Ohzuku T, Uedo A, Nagayama M. Electrochemistry and structural chemistry of LiNiO2 (R3m) for 4 volt secondary lithium cells[J]. J Electrochem Soc, 1993, 140:1862-1870.
[6]Morales J, Pérez-Vicente C, Tirado J L. Cation distribution and chemical deintercalation of Li1-xNi1+xO2[J]. Mat Res Bull, 1990, 25: 623-630.
[7]Moshtev R V, Zlatilova P, Manev V, et al. The LiNiO2 solid solution as a cathode material for rechargeable lithium batteries[J]. J Power Sources, 1995, 54: 329-333.
[8]Rougier A, Graviereau P, Delmas C. Optimization of the composition of the Li1-zNi1+zO2 electrode materials: structural, magnetic, and electrochemical studies[J]. J Electrochem Soc, 1996, 143: 1168-1175.
[9]Peres J P, Delmas C, Rougie A, et al. The relationship between the composition of lithium nickel oxide and the loss of reversibility during the first cycle[J]. J Phys Chem Solids, 1996, 57: 1057-1060.
[10]Biensan P, Simon B, Pérès J P, et al. On safety of lithium-ion cells[J]. J Power Sources, 1999, 82: 906-912.
[11]Arai H, Okada S, Sakurai Y, et al. Thermal behavior of Li1yNiO2 and the decomposition mechanism[J]. Solid State Ionics, 1998, 109: 295-302.
[12]Broussely M, Bieusan P, Simon B. Lithium insertion into host materials: the key to success for Li ion batteries[J]. Electrochim Acta, 1999, 45: 3-22.
[13]Delmas C, Ménétrier M, Crognennec L, et al. An overview of the Li(Ni,M)O2 systems: syntheses, structures and properties[J]. Electrochim Acta, 1999, 45: 243-253.
[14]Li W, Currie J C. Morphology effects on the electrochemical performance of LiNi1-xCoxO2[J]. J Electrochem Soc, 1997, 144: 2773-2780.
[15]Cho J, Jung H S, Park Y C, et al. Electrochemical properties and thermal stability of LiaNi1-xCOxO2 cathode materials[J]. J Electrochem Soc, 2000, 147: 15-20.
[16]Ritehie A G, Giwa C O, Lee J C, et al. Future cathode materials for lithium rechargeable batteries[J]. J Power Sources, 1999, 80: 98-102.
[17]Kostecki R, McLarnon F. Degradation of LiNi0.8-Co0.2O2 cathode surfaces in high-power lithium-ion batteries[J]. Electrochem Solid State Lett, 2002, 5: A164-A166.
[18]Broussely M. Recent developments on lithium ion batteries at SAFT[J]. J Power Sources, 1999, 81: 140-143.
[19]Venkatraman S, Shin Y, Manthiram A. Phase relationships and structural and chemical stabilities of charged Li1-xCoO2 and Li1-xNi0.85Co0.15O2 cathodes[J]. Electrochem Solid State Lett, 2003, 6: A9-A12.
[20]Nakagome N T. In situ transmission X-ray absorption fine structure analysis of the Li deintercalation process in Li(Ni0.5Co0.5)O2[J]. Electrochem Solid State Lett, 1998, 1: 259-262.
[21]Fey G T K, Chen J G, Subramanian V, et al. Preparation and electrochemical properties of Zn-doped LiNi0.8Co0.2O2[J]. J Power Sources, 2002, 112: 384-394.
[22]Aurbach D, Levi M D, Levi E, et al. Common electroanalytical behavior of Li intercalation processes into graphite and transition metal oxides[J]. J Electrochem Soc, 1998, 145: 3024-3033.
[23]Barbonx P, Tarascon J M, Shokovhi F K. The use of acetates as precursors for the low-temperature synthesis of LiMn2O4 and LiCoO2 intercalation compounds[J]. J Solid State Chem, 1994, 94: 185-196.
[24]Kanno R, Kubo H, Kawamoto Y, et al. Phase relationship and lithium deintercalation in lithium nickel oxides[J]. J Solid State Chem, 1994, 110: 216-225.
(Edited by LI Xiang-qun)
Foundation item: Project (2002CB211800) supported by the National Key Fundmental Research and Development Program of China
Received date: 2004-11-08; Accepted date:2005-01-05
Correspondence: YAN Jie, Professor; Tel: +86-22-23503623; E-mail: yanjie@nankai.edu.cn