
Direct electroless Ni-P deposition on AM50 magnesium alloy from sulfate bath
LI Guang-yu(李光玉), NIU Li-yuan(牛丽媛), JIANG Zhong-hao(江中浩),
GU Chang-dong(谷长栋), LIAN Jian-she(连建设)
Key Laboratory of Automobile Materials, Ministry of Education,
College of Materials Science and Engineering, Jilin University, Changchun 130025, China
Received 20 April 2006; accepted 30 June 2006
Abstract: A bright electroless Ni-P deposition on AM50 magnesium alloy in a sulfate plating bath was proposed by using direct plating process with non-chromate pretreatment. The electroless Ni-P plating on AM50 magnesium alloy has an admirable appearance and good adhesion. The results indicate that the electroless Ni-P deposition with non-chromate pretreatment has better adhesion than that of zinc immersion coating. Anodic polarization curves indicate that the electroless Ni-P deposition obtained from the sulfate bath has similar corrosion-resistance to that obtained from basic nickel carbonate bath. The deposition process generates less pollutant by a non-chromate plating bath and is suitable for the magnesium alloys manufacture because of its low cost. The hardness of the electroless Ni-P plated AM50 is about HV 720.6 and HV 969.7 after heat treatments at 180 ℃ for 2 h. The wear resistance of Ni-P plated magnesium alloy specimens is about 5 to 9 times as high as that of bare magnesium alloys.
Key words: magnesium alloy; AM50; Ni-P deposition; salt spray, adhesion
1 Introduction
In order to decrease fuel consumption and improve human ecology, reducing vehicle mass through application of lightweight materials is attractive [1-4]. Magnesium is the lightest structural metal with the highest specific strength. However, magnesium alloys application has been limited due to the undesirable properties including poor corrosion and wear resistances of magnesium alloys. The effective way to prevent corrosion of magnesium is to coat the base material. Thus, formation of a rustproof coating on the surface of the magnesium alloy is necessary in practical utilization and relevant studies have been developed quickly in recent years [5-10].
Electroless deposition technique of Ni-P alloy coatings has been a well-known commercial process that has found numerous applications in many fields due to the excellent properties of the coatings, such as high corrosion-resistant, high wear-resistant, good lubricity, high hardness and acceptable ductility [11-17].
As for electroplating on the magnesium alloy, there are two kinds of process used for plating on magnesium and magnesium alloys: direct electroless nickel plating and zinc immersion. It can be noted that in many previous reports on the electroless plating on magnesium alloys [18, 19], the nickel ions were provided by basic nickel carbonate in the plating bath. The pretreatment of electroless Ni-P deposition on magnesium alloys is discussed in relative reports, in which chromate is used in acid pickling.
However, basic nickel carbonate is not easy to dissolve and expensive. In this paper, the electroless Ni-P deposition on AM50 magnesium alloy was undertaken from a sulfate nickel plating bath[17].
One object of the investigation is to develop a pretr- eatment method for treating magnesium alloys before electroless Ni-P plating, which can produce an admirable appearance and good adhesion for the further Ni-P plating. Another object is to investigate a direct method for treating magnesium alloys, which generates less pollutant by using a non-chromate plating bath and suit- able for the magnesium alloys manufacture.
2 Experimental
The substrate material used in this study was AM50 die cast magnesium alloy with the specimen size of 50 mm×50 mm×3 mm. The chemical compositions of the alloy are given in Table 1.
Table 1 Compositions of AM50 magnesium alloy(mass fract- ion, %)

The samples were abraded with No.2000 SiC paper before the pretreatment processes. The procedure and bath composition for obtaining electroless Ni-P deposit- ion on AM50 magnesium alloy are given in Table 2.
Table 2 Procedure and bath composition of electroless Ni-P plaiting on AM50 magnesium alloy
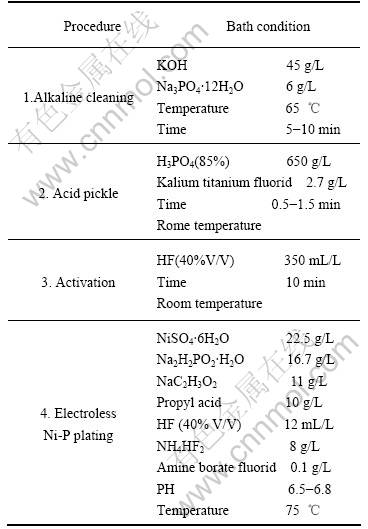
In Table 2 the non-chromate pretreatment process is used in the test. The samples were first degreased (Step1 in Table 2) and rinsed in de-ionized water to remove all alkali. Then pickling of the AM50 sample in the acid bath (Step2 in Table 2) was used to remove oxide layers or other chemical coatings of the sample surface and supply the surface for better mechanical adhesion of the electroless Ni-P deposition on AM50 magnesium alloy. Furthermore, activation (Step3 in Table 2) was used to the AM50 sample. The pretreatment process without chromate in Step2 and Step3 were employed to replace the traditional zinc immersion process.
The coating surface were observed using SEM (JSM-5310, Japan Electronics). The compositions of phosphate coatings were analyzed using XRD (D/max- 2500PC, Cu Ka).
The adhesion test on the electroless Ni-P deposition with thickness 10-20 mm on AM50 was undertaken. Before test two or more crossed beelines on the surface of samples were scored using the knife (ISO 2409 code) [20]. The nick must be scored to the substrate. Then the appearance of the electroless Ni-P deposition sample was employed to estimate the adhesion properties.
The hardness of magnesium alloy before and after electroless deposition was evaluated using an HXD-1000 microhardness tester with Vickers indenter, at a load of 1 N and duration of 15 s. The coated samples were rotated in sand/water for measurement of wear resistance [15]. The rotation speed was kept constant at 300 r/min and the wear effect was measured in terms of mass loss expressed in milligrams. The samples were measured within the thickness of the coating without reaching to the base metal.
3 Results and discussion
3.1 Microstructure of electroless deposition on AM50 magnesium alloy
SEM micrograph of the electroless Ni-P deposition on AM50 magnesium alloy is shown in Fig.1. It is seen that the dense and microhole-less ‘conglobulation’ micr- ostructures was deposited on the magnesium alloy.
Fig.2 shows the cross-section of the electroless Ni-P
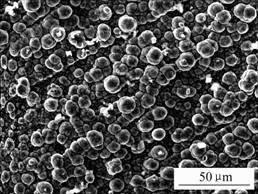
Fig.1 SEM micrograph of Ni-P depositions on AM50 magnesium alloy
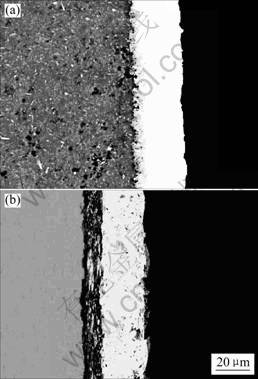
Fig.2 Morphologies of cross-section of electroless Ni-P deposition on AM50 magnesium alloy with different pretreatment process: (a) Non-chromate pretreatment; (b) Zinc immersion
deposition on AM50 with different pretreatment before plating. In Fig.2 (a) it can be seen that the non-chromate pretreatment and activation provides AM50 magnesium alloy surface many pits to act as sites for mechanical interlocking to improve the adhesion of electroless Ni-P deposition on the substrate[17].
In comparison, the cross-section of the electoless Ni-P deposition on AM50 with the zinc immersion is shown in Fig.2 (b). The zinc immersion layer between the electroless Ni-P coating and AM50 magnesium alloy can be clearly seen. The zinc coating is adhered by immersion method and has a distinct interface without interlocking to the matrix.
The electroless Ni-P deposition on AM50 magnesium alloy with non-chromate pretreatment is glazed and has admirable appearance. But the electroless Ni-P deposition with zinc immersion pretreatment is slight dull and appears a little bit coarse. That is because the electroless Ni-P deposition forms directly on the surface of AM50 magnesium alloy and could get bright appearance on the polished AM50 magnesium alloy.
The phosphor content in electroless Ni-P deposition on AM50 magnesium alloy is 11.4%. The XRD pattern of electroless Ni-P on AM50 magnesium alloy is show in Fig.3. There is a bread-shaped peak (where 2θ=45?). It is the characteristic peaks of the mixture of amorphous and crystal Ni3P.

Fig.3 XRD patterns of electroless Ni-P on AM 50
3.2 Properties of electroless deposition on AM50 magnesium alloy
Table 3 shows the adhesion results. The edge of the cuts on the electroless deposition with non-chromate pretreatment is completely smooth and none of peeling or breaking-off. Therefore, it leads to a better adhesion because of the interlocking microstructure (Fig.2 (a)). By comparison, there is a bit of breaking-off of Ni-P deposition with zinc immersion pretreatment at the intersections of the cuts.
Table 3 Adhesion characteristic results of electroless Ni-P deposition with different pretreatment on AM50 magnesium alloy
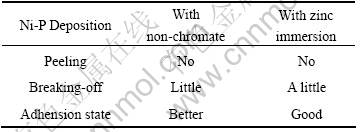
Accordingly, in consideration of adhesion properties, the non-chromate pretreatment can be used as the pretreatment before electroless Ni-P deposition, in place of zinc immersion coating.
The challenge to obtaining depositions on magnesium alloy is that it can’t form easily in acidic plating baths because the magnesium alloy tends to be rust. In the tests it was found that the magnesium alloy did not erode in pH 6.5-6.8 plating baths (adjusted by ammonia). Anodic polarization of the AM50 magnesium alloy and 20 μm electroless Ni-P deposition obtained from sulfate bath of pH 5.8, sulfate bath of pH 6.7 and basic nickel carbonate bath are shown in Fig.4. The corrosion potential Ecorr of AM50 is -2.116 mV. It is seen that for the Ni-P coating, when bath pH increases from 5.8 to 6.7, the corrosion potential Ecorr moves from -0.916 mV to -0.636 mV. Therefore, the increase of corrosion potential Ecorr to positive direction could be attributed to the decrease of H+ ion in the bath. Moreover, it is seen that the Ni-P coating from the basic nickel carbonate bath observed similar corrosion potentials (-0.621 mV) to that from the sulfate bath with pH=6.7, therefore, they should have the similar anticorrosion per- formance.
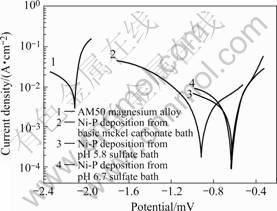
Fig.4 Anodic polarization curves of Ni-P layers from different baths compared with substrate in 3%NaCl solution
AM50 specimens were plated 20 μm electroless Ni-P deposition. The hardness is 118.6 HV before plating. The hardness of the electroless Ni-P plated sample is average HV 720.6 and HV 969.7 after heat treatments at 180 ℃ for 2 h.
The wear resistance of the specimens was compared by measuring the mass lose when specimens were rotated in sand/water mixture. Fig.5 shows the relation
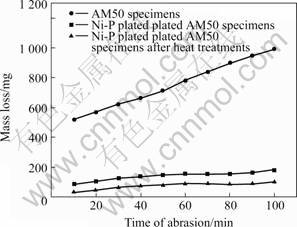
Fig.5 Relation between time of abrasion and mass loss for Ni-P platings, in comparison with substrate
between time of abrasion and mass loss of the specimens in the test. It indicates that the mass loss of Ni-P plated specimens is much lower than bare magnesium alloy specimens. The wear resistant of Ni-P plated magnesium alloy specimens is 3 to 7 times as high as that of bare magnesium alloys parts. After heat treatment at 180 ℃ for 2 h, the Ni-P plated magnesium alloy specimens are 5 to 9 times as high as that of AM50 magnesium alloys.
4 Conclusions
1) The non-chromate pretreatment was used to obtain bright and better-adhered Ni-P deposition on the AM50 magnesium alloy.
2) The Ni-P deposition on the AM50 alloy with non-chromate pretreatment obtained from pH 6.7 sulfate bath has similar corrosion-resistance to that from basic nickel carbonate bath, and they exhibits better antico- rrosion property than the Ni-P deposition on the AM50 alloy with non-chromate pretreatment obtained from pH 5.8 sulfate bath.
3) The wear resistant of Ni-P plated magnesium alloy specimens is about 5 to 9 times as high as that of bare magnesium alloys parts.
References
[1] IGNAT S, SALLAMAND P, GREVEY D, LAMBERTIN M. Magnesium alloys laser (Nd:YAG) cladding and alloying with side injection of aluminium powder [J]. Appl Surf Sci, 2004, 225: 124-134.
[2] WATARI H, DAVEY K, RASGADO M T, HAGA T IZWA S. Semi-solid manufacturing process of magnesium alloys by twin-roll casting [J]. J Mater Process Tech, 2004, 155-156: 1662-1667.
[3] Retallick W B, Brady M P, Hurnphrey D L. A phosphoric acid surface treatment for improved oxidation resistance of gamma titanium aluminides [J]. Intermetallics, 1998, 6: 335-337.
[4] ROSALBINO F, ANGELINI E, DE NEGRI S, SACCONE A, DELFINO S. Effect of erbium addition on the corrosion behaviour of Mg-Al alloys [J]. Intermetallics, 2005, 13: 55-60.
[5] HAWKE D, ALBRIGHT D L. A phosphate-permanganate conversion coating for magnesium [J]. Met Finish, 1995, 93(10): 34-38.
[6] UMEHARA H, TAKAYA M, TERAUCHI S. Chrome-free surface treatments for magnesium alloy [J]. Surf Coat Technol, 2003, l69-170: 666-669.
[7] HAN E H, ZHOU W Q, SHAN D Y, KE W. Corrosion and protection of magnesium alloy AZ31D by a new conversion coating [J]. Mater Sci Forum, 2003, 419(4): 879-883.
[8] KOUISNI L, AZZI M, ZERTOUBI M, DALARD F, MAXIMOVITCH S. Phosphate coatings on magnesium alloy AM60 (Part 1): Study of the formation and the growth of zinc phosphate films [J]. Surf Coat Technol, 2004, 185(1): 58-67.
[9] KOUISNI L, AZZI M, DALARD F, MAXIMOVITCH S. Phosphate coatings on magnesium alloy AM60(Part 2): Electrochemical behaviour in borate buffer solution [J]. Surf Coat Technol, 2005, 192(2-3): 239-246.
[10] NIU L Y, JIANG Z H, LI G Y, GU C D, LIAN J S. A study and app1ication of zinc phosphate coating on AZ91D magnesium alloy [J]. Surf Coat Technol, 2006, 200, 3021-3026.
[11] GAO Y, ZHENG Z J, ZHU M, LUO C P. Corrosion resistance of electrolessly deposited Ni-P and Ni-W-P alloys with various structures [J]. Mater Sci Eng A, 2004, A381: 98-103.
[12] YAN H. New Techniques in Electroless Nickel and Composite Plating[M]. Beijing: National Defense Industry Press, 2001. 1.
[13] HUO H Y, LI Y, WANG F H. Corrosion of AZ91D magnesium alloy with a chemical conversion coating and electroless nickel layer [J]. Corros Sci, 2004, 46(6): 1467-1477.
[14] AMBAT R, ZHOU W. Electroless nickel-plating on AZ91D magnesium alloy: effect of substrate microstructure and plating parameters [J]. Surf Coat Technol, 2004, 179(2-3): 124-134.
[15] ABDEL HAMID Z, ABOU ELKHAIR M T. Development of electroless nickel–phosphorous composite deposits for wear resistance of 6061 aluminum alloy [J]. Mater Lett, 2002, 57(3): 720-726.
[16] GU C D, LIAN J S, LI G Y, MU L Y, JIANG Z H. High corrosion-resistant Ni-P/Ni/Ni-P multilayer coatings on steel [J]. Surf Coat Technol, 2005, 197: 61-67.
[17] GU C D, LIAN J S, LI G Y, NIU L Y, JIANG Z H. Electroless Ni-P plating on AZ91D magnesium alloy from a sulfate solution [J]. J Alloy Compd, 2005, 391: 104-109.
[18] SHARMA A K, SURESH M R, BHOJRAJ H, NARAYANAMURTHY H, SAHU R E. Electroless nickel plating on magnesium alloy [J]. Met Finish, 1998, 96(3): 10-18.
[19] ASTM Standard Designation B, 480-88. Standard Guide for Prep- aration of Magnesium and Magnesium Alloys for Electroplating[S].
[20] ISO Standards 2409-1992. Paints and Varnishes-Cross-Cut Test[S].
(Edited by HE Xue-feng)
Foundation item: Project (2004CB619301) supported by the Foundation of National Key Basic Research and Development Program; Project supported by the 985 Project of Jilin University, China
Corresponding author: LIAN Jian-she; Tel: +86-431-5095875; E-mail: lianjs@ jlu.edu.cn