
Surface nanocrystallization of 7A04 aluminium alloy induced by circulation rolling plastic deformation
YE Hui-qiong(叶惠琼), FAN Xin-min(樊新民)
Department of Materials Science and Engineering, Nanjing University of Science and Technology, Nanjing 210094, China
Received 10 April 2006; accepted 25 April 2006
Abstract: The surface nanocrystalline microstructures of 7A04 aluminium alloy was obtained by means of circulation rolling plastic deformation(CRPD), the grain refinement behavior and the hardness variation were examined. X-ray diffraction(XRD) and transmission electron microscopy(TEM) were applied to characterize the microstructure of the surface layer. The experimental evidences show that, after the CRPD treatment, the mean grain size in the surface layer is about 50 nm. The microhardness of the nanostructured surface layers is enhanced significantly after CRPD compared with that of the matrix, which can be attributed primarily to the grain refinement. The microhardness at the top surface can reach about HV0.05335, while the value of the matrix is HV0.05160 or so. The surface hardening effect is obtained obviously. Besides, the thermal stability of nanocrystalline layer was investigated. The results of the XRD analysis and the microhardness measurement show that the nanocrystalline layer has better thermal-stability than the matrix. And the DSC measurement shows that the synthesis of nanostructured surface layer has influence on the phase transformation of 7A04 aluminum alloy.
Key words: surface nanocrystallization; 7A04 aluminium alloy; hardness; grain refinement; thermal stability
1 Introduction
The mechanical properties of engineering materials can be improved by refining their microstructures. It is known that most failures of engineering materials are very sensitive to the structure and properties of material surface, and in most cases, the material failures occur on the surface. Therefore, optimization of surface structure and properties may effectively improve the global behavior of material. Surface nanocrystallization is a new topic proposed in recent years, which is known as one of the important methods to modify surface physical, chemical and mechanical properties and prolong the use life of machinery parts[1]. Recently, nanocrystallization structure of surface layers was successfully achieved on different metallic materials via severe plastic deformation using ultrasonic shot peening[2-4], high- energy shot peening(HESP)[5,6], surface mechanical attrition treatment(SMA)[7-9], wire-brushing[10] and circulation rolling plastic deformation (CRPD)[11, 12], etc.
In this work, the nanostructured surface layer on 7A04Al alloy was induced by the circulation rolling plastic deformation(CRPD). The microstructure evolution was characterized by different techniques, and the change of mechanical properties after the CRPD treatment was analyzed. Meanwhile, the thermal stability of nanocrystalline layer was studied.
2 Experimental
The material used in this work was 7A04 aluminium alloy, which contains 6.43% Zn, 2.12% Mg, 1.84% Cu, 0.35% Fe, 0.22% Si, 0.33% Mn (mass fraction) and balance Al. The material was prepared by the solution treatment, and then the aging was carried out at 120 ℃ for 3 h and 160 ℃ for 3 h.
The samples were treated by CRPD methods in vacuum for 80, 160 and 240 min, respectively. After the CRPD treatment, the annealing treatment and the DSC measurement were carried out to study the thermal stability of nanocrystalline layer. The annealing temperatures were 200, 300, 400 and 500 ℃, respectively.
The microstructure evolution of samples was characterized by different techniques. The structure of the sample surface was studied using X-ray diffraction (XRD) with Cu Kα radiation in X-ray diffractometer. The average grain size was obtained from XRD line broadening in terms of the Scherrer and Wilson equation. The morphologies of cross-section and surface layer of the samples after the CRPD treatment were examined using optical microscope and the JEOL-2000EM transmission electron microscopy(TEM), respectively. The thin foil samples for TEM observations were cut from the 7A04 aluminium alloy surface by an electro-spark discharge machine, and then grinded into about 150 μm, at last, thinned by ion milling .
Sample discs for DSC with diameter of 5 mm and thickness of 0.5 mm were prepared before and after CRPD treatment. The DSC measurement was taken in a Shimadzu DSC-50 apparatus. High purity aluminum was used as reference. The experiments were carried out at the heating rate of 20 ℃/min from 75 to 500 ℃ under a nitrogen atmosphere.
3 Results and discussion
3.1 XRD analyses of surface layer
Fig.1 shows the XRD patterns of 7A04 Al alloy specimens treated for different time. The Bragg- diffractional peak in the treated samples becomes broader than that in the original sample, which may be attributed to grain refinement, microtrain and instrument broadening. From Fig.1, it can be seen that, at and after 80 min treatment, the main Bragg peaks of 7A04 broaden obviously, and the grain size decreases to nanoscale about 65 nm at 160 min treatment based on the broadening of peaks. With the increase of the treating time, the intensity of the peaks decreases. But when the treating time reaches up to 160 min, the grain size doesn’t change or changes slightly.
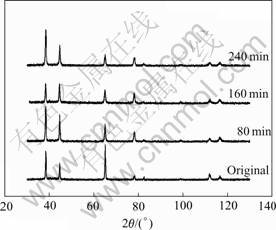
Fig.1 XRD patterns of samples treated for different time
3.2 Micrograph of surface layer
The metallograph on the cross-section of the sample after CRPD treatment for 80 min is shown in Fig.2. The plastic deformation evidences can be observed at depth of about 200 μm from the top surface, which can be referred to as the deformation region. The plastic flows in the deformation region are found along one direction, which indicates that repeated mechanical loads acted on material surface are statistically concentrated in some special directions.
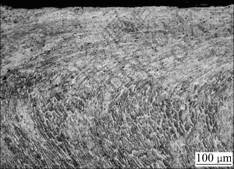
Fig.2 Metallograph of cross-section of sample treated for 80 min
The top CRPD surface layer of the samples treated for 160 min was observed by TEM. The results are shown in Fig.3. According to the TEM images, the mean grain size could be measured. The average grain size on the top surface layer treated for 160 min already is refined to about 50 nm. The grain size determined from TEM observation is evidently smaller than that obtained from the XRD calculation. It might be due to the fact that XRD results average the structure information at a certain depth of about 10 μm from the surface to the matrix that the X-ray can reach, while the TEM sample is a very thin film (less than 1μm thick) on the sample surface. And from Fig.3, from both the bright and the dark field images, it can be seen that the shape of the nanocrystallized grains is roughly equiaxed.
3.3 Microhardness gradient distribution along depth of layer
Microhardness from the surface to matrix was measured, and the results are shown in Fig.4. From Fig.4, the curve shows that the microhardness descends gradually from surface to matrix, and the slope coefficient becomes small with the distance increasing from the surface. Microhardness of the top surface increases with the treating time prolonging, but when the surface is treated for 240 min, the microhardness becomes a little small compared with that of treated for 160 min. The microhardness of the top surface can reach HV 335 after being treated for 160 min. The value is
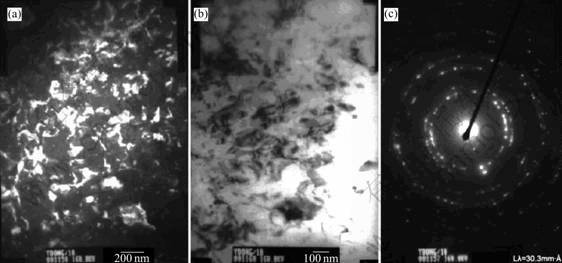
Fig.3 TEM images and selected area electron diffraction patterns of top surface layer after CRPD treatment for 160 min: (a) Dark field image; (b) Bright field image; (c) SAED pattern
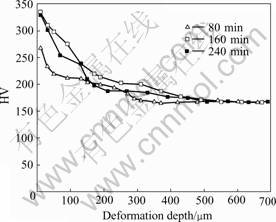
Fig.4 Microhardness distribution along surface depth
much higher than that of the matrix. Thereby, the surface hardening effect has been obtained obviously. The microhardness reduces significantly from the top surface to the depth of about 200 μm. Beyond 200 μm, the hardness changes slightly until 400 μm in depth.
Over 400 μm in depth, the hardness is the same as that of the matrix. Combined with the analyses results of microstructure, it may be concluded that the grain refinement or the working hardening is mostly contributed to the increase of the hardness from the top surface layer at the depth of 400 μm.
3.4 Thermal stability of nanocrystalline layer
The samples after CRPD treated for 160 min were annealed at 200, 300, 400 and 500 ℃, respectively, for 30 min to investigate the thermal stability of the surface nanocrystalline layer.
XRD analyses were carried out after annealing at different temperatures, and the result is shown in Fig.5. From Fig.5, it can be observed that the broadening of the Bragg-diffractional peak decreases after annealing. When the annealing temperature reach 400 and 500 ℃, the Bragg-diffractional peak in the treated samples does not change or changes slightly. The diffraction peaks at 40.42?, 41.32? and 44.56? of the samples annealing at 200℃ and 300℃ are attributed to MgZn2 because the growth of grain may be prevented.
Fig.6 shows the microhardness after annealing at different temperatures. It can be seen that the hardness of the samples decreases significantly with the increase of the temperature. But the hardness of the plastic deformation region is still higher than that of the matrix. Until annealing at 400 ℃ and 500 ℃, there is no evident difference between the plastic deformation region and the matrix, and the microhardness decreases to very low value. When annealing at 200 ℃, the hardness of the sample changes slightly and is very close to that of the sample treated for 160 min. But when the temperature reaches up to 300 ℃, the hardness descends obviously. This may be due to the dissolution of MgZn2 phase or because the grain size has grown and the microtrain has disappeared. According to the results of XRD analyses and the hardness measurement, it can be concluded that the nanocrystalline layer of 7A04 Al alloy has better thermal stability than the matrix.
The phase transformation of the nanocrystalline layer through the DSC measurement of the samples before and after CRPD treatment. The results are shown in Fig.7. The curve a in Fig.7 shows the DSC scan of the sample before CRPD treatment. The thermograph shows a endothermic peak at about 473 K. According to the present study, the endothermic peak can be interpreted by the dissolution reaction of unstable η′(MgZn2), which
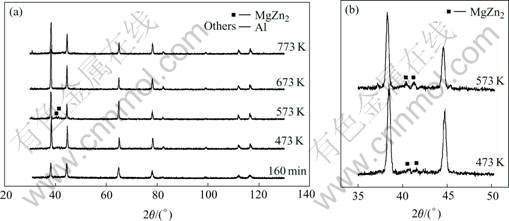
Fig.5 XRD patterns of annealing samples treated for 160 min: (a) XRD patterns of samples annealed at different temperatures; (b) Partial view of XRD patterns
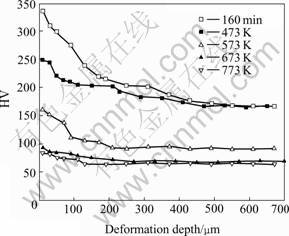
Fig.6 Microhardness distribution along deformation depth after annealing

Fig.7 DSC thermogram of samples before(a) and after(b) CRPD treatment
agrees with the past research. In the early studies[13, 14], it was concluded that the η′ precipitates were the predominant constituent in the samples of 7A04 Al alloy
in the state of progressively aging. In addition, the DSC curve a shows that the start dissolution temperature of the precipitations is about 380K. The curve b in Fig.7 shows the thermograph of the sample treated by CRPD. From the curves, it can be found that, after the CRPD treatment, there is no endothermic peak at about 473 K. The interpretation of the results may be invited by the grain refinement or the microtrain. Because the endothermic heat might be offset by the heat release from the microtrain. The peak might be delayed to higher temperature or disappears. The results show that the synthesis of a nanostructured surface layer has influence on the phase transformation.
4 Conclusions
1) Nanocrystalline structure is obtained successfully in the surface layer of the 7A04 aluminum alloy by means of the CRPD treatment. The average grain size of the surface layer is about 50 nm at the top surface layer and increases gradually with the depth increasing. The plastic deformation region is about 300 μm.
2) The microhardness of the nanostructured surface layers is enhanced significantly after CRPD treatment compared with that of the initial sample. The microhardness can reach about HV0.05335 at the top surface, while the value of the matrix is HV0.05160 or so. Therefore, the surface hardening effect is obtained obviously.
3) According to the results of the XRD analysis and the microhardness measurement of the samples after annealing, it can be concluded that the nanocrystalline layer of 7A04 Al alloy has better thermal stability than the matrix. And the DSC measurement shows that the synthesis of a nanostructured surface layer has influence on the phase transformation of the 7A04 aluminum alloy.
References
[1] LU K, LU J. Surface nanocrystallization (SNC) of metallic materials: presentation of the concept behind a new approach[J]. J Mater Sci Tech, 1999,15: 193-197.
[2] LIU G, LU J, LU K. Surface nanocrystallization of 316L stainless steel induced by ultrasonic shot peening [J]. Mater Sci Eng, 2000, A286: 92-95.
[3] WU X, TAO N, HONG Y, XU B, LU J, LU K. Microstructure and evolution of mechanically-induced ultrafine grain in surface layer of Al-alloy subjected to USSP [J]. Acta Mater, 2002, 50: 2075-2084.
[4] TAO N R, SUI M L, LU J, LU K. Surface nanocrystallization of iron induced by ultrasonic shot peening [J]. Nanostruct Mater, 1999,11(4): 433-440.
[5] LIU G, WANG S C, LOU X F, LU J, LU K. Low carbon steel with nanostructured surface layer induced by high-energy shot peening [J]. Scripta Mater, 2001, 44: 1791-1795.
[6] CHEN Chun-huan, REN Rui-ming, ZHAO Xiu-juan, ZHANG Yu-jun. Surface nanostructures in commercial pure Ti induced by high energy shot peening [J]. Trans Nonferrous Met Soc China, 2004, 14(2): 215-218.
[7] WANG Z B, TAO N R, LI S, LIU G, LU J, LU K. Effect of surface nanocrystallization on friction and wear properties in low carbon steel [J]. Mater Sci Eng A, 2003, A352: 144-149.
[8] TAO N R, WANG Z B, TONG W P, SUI M L, LU J, LU K. An investigation of surface nanocrystallization mechanism in Fe induced by surface mechanical attrition treatment [J]. Acta Mater, 2002, 50: 4603-4616.
[9] WANG Hong-bin, WU Xiao-chun, XU Ling-yun. Thermal stability of nanocrystalline layer prepared by surface mechanical attrition in 0Cr18Ni9Ti stainless steel [J]. Trans Nonferrous Met Soc China, 2004, 14(2): 210-214.
[10] Sato M, Tsuji N, Minamino Y, KOIZUMI Y. Formation of nanocrystalline surface layers in various metallic materials by near surface severe plastic deformation [J]. Sci Technol Adv Mater, 2004, 5: 145-152.
[11] FAN Xin-min, ZHU Lin, HUANG Jie-wen. Surface nanocrystalli- zation of Ti6Al4V induced by circulation rolling plastic deformation [J]. Trans Nonferrous Met Soc China, 2004, 14(s2): 190-192.
[12] FAN Xin-min, ZHOU Bo-sen, ZHU Lin, HUANG Jie-wen. Surface nanocrystallization of low carbon steel induced by circulation rolling plastic deformation [J]. Material Science Forum, 2005, 475-479: 133-136.
[13] ZHANG Bao-chang. The Nonferrous Metals and its Heat Treating [M]. Xi’an: Northwestern Polytechnical University Press, 1993.(in Chinese)
[14] Xie g s, Zeng t, Ding h. DSC and TEM study of ultra high strength aluminum alloy [J]. Acta Metallurgica Sinica, 2004, 17(4): 554-559.
(Edited by LI Yan-hong)
Corresponding author: FAN Xin-min; Tel: +86-25-84315617-802; E-mail: zxsysiam@mail.njust.edu.cn