
Evaluation of thermal sprayed coating using ultrasonic inspection
by means of bottom echo back reflection
Toshifumi KUBOHORI, Toru ITO, Wahidullah WAHI, Yasuyuki INUI, Toshiro IKUTA
School of Science and Engineering, Kinki University, 3-4-1, Kowakae, Higashiosaka, Osaka, 577-8502, Japan
Received 18 June 2008; accepted 10 March 2009
Abstract: Thermal spraying technique is widely used in various mechanical parts as a surface reforming technique. However, as demand to maintain superior mechanical performance in harsh operating environment increases, the need for non-destructive evaluation method for thermal spray coating becomes more important. For this purpose, we thinned the thickness of the thermal sprayed coating by abrasion with blasting and used ultrasonic inspection by means of bottom echo reflection for effective measurement of abrasion quantity in thermal sprayed coating. The results obtained are summarized as follows. When the thickness of thermal sprayed coating becomes thin, the echo height increases. This is because thermal sprayed coatings absorb ultrasonic energy. Ultrasonic energy absorbed by Al2O3 is smaller compared with Fe-13Cr coating. Thermal sprayed coatings submerged in water have a lower echo height compared with air. As mentioned above, the thermal sprayed coating thickness can be estimated using ultrasonic inspection by means of bottom echo back reflection.
Key words: thermal sprayed coating; ultrasonic inspection; bottom echo back reflection
1 Introduction
Thermal spraying method consists of jetting molten or similarly heated particles at high speed against substrate surface in order to form a film coat. This technique is widely used as surface reforming technique to make a substrate corrosion-proof, abrasion-proof, heat-resistant and electrically insulated. Improvement of abrasion resistance is one of thermal sprayed coatings applications widely used in a large number of fields[1]. Thermal sprayed coating technology has made cutting in manufacturing achievable by using low class material as base material and applying only the necessary part with high class material coating. As demand to maintain superior mechanical performance in harsh operating environment increases, the need to have a thorough knowledge of abrasion state and mechanism in thermal sprayed coatings becomes more important. To achieve this objective, a reliable non-destructive method for evaluating thermal sprayed coating is needed. Ultrasonic inspection by means of bottom echo back reflection is a method where inspection can be made from the opposite side of subject. This method becomes more reliable as most of thermal sprayed coating surface is rough from abrasion, thus making inspection from the surface difficult. In applications such as fine powder transporting tube, which uses thermal sprayed coating to improve abrasion resistance inside the tube, inspection from the tube outside, is much practical.
In this study, we thinned the thickness of the thermal sprayed coating by abrasion with blasting and used ultrasonic inspection by means of bottom echo reflection for effective measurement of abrasion quantity in thermal sprayed coating. Based on the result, thermal sprayed coating thickness can be estimated.
2 Experimental
A micro-blasting machine (VMC-X30, Vaniman Ltd.) with white alumina (average particle diameter 120 μm) grit was used to abrade thermal sprayed coatings in the experiment.
After the abrasion process by blasting, the coatings thicknesses were measured using an ultrasonic flaw detector (DSL-104, Panametrix Co. Japan). To emulate the real conditions of thermal sprayed coating application environment, a few substances were used in the process. Fig.1 shows the schematic diagram of probe setting in the experiment and relation between attenuation and reflection of ultrasonic wave.
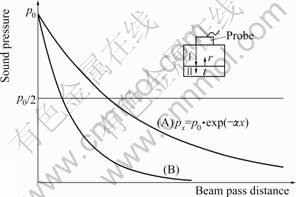
Fig.1 Probe setting and relationship between attenuation and reflection in ultrasonic wave
Generally, when sound waves propagate through a medium towards x direction, the attenuation state of sound pressure px can be expressed by Eq.(1), in the case of plane wave[2]:
px=p0?exp(-αx) (1)
where α is attenuation constant; x is the propagation distance of the sound wave; p0 is the sound pressure before entering medium; and px is the sound pressure after propagation into the medium in x direction. The attenuation constant α in Eq.(1) shows the degree of attenuation of ultrasonic wave energy produced as ultrasonic waves propagate through a medium. When ultrasonic waves hit perpendicularly against the border face, the waves are divided into reflecting components and passing components. The proportion of the two components is determined by acoustic impedance (Z) of the two media, which are in contact with each other at the face border. Supposing that only the sound pressure reflectance affects the reflected echo and that passing energy is absorbed by the medium II, which, in this case, refers to thermal sprayed coating, assumption can be made that ultrasonic wave energy is absorbed by thermal sprayed coating. This assumption is also supported by observation that echo height decreases as the film thickness increases.
Experimental test pieces were prepared by thermal spraying white alumina powder (Al2O3) and Fe-13Cr to a base material (SS400) with dimensions of 10 mm×10 mm×10 mm. The thickness was 250 ?m for alumina coating, and 200 ?m for Fe-13Cr. Before thermal spraying, the substrates were blasted with alumina to increase contact area.
3 Results and discussion
3.1 Relationship between surface roughness and echo height
In the experiment, abrasion quantity was measured by observing bottom echo of ultrasonic wave reflected from the coating and substrate surface. Therefore, it is necessary to investigate the influence of substrate surface roughness on echo height. Fig.2 shows the relationship between surface roughness(Rz) and echo height(H). As shown in Fig.2, there was no significant change in echo height when surface roughness was less than 350 ?m. However, echo height significantly dropped when surface roughness increased to more than 350 ?m. From this result, we can conclude that surface roughness of substrate and coating surface has no significant influence on echo height as long as the roughness is below 350 ?m.
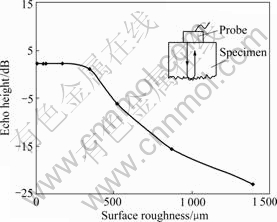
Fig.2 Relationship between surface roughness and echo height
3.2 Changes in coating thickness due to blasting time
Fig.3 shows the relationship between blasting time t and decrease in film thickness m for Al2O3 and Fe-13Cr coatings.
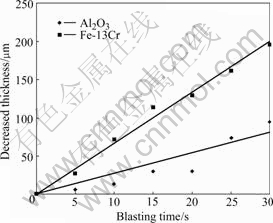
Fig.3 Relationship between coating thickness and blasting time
As shown in Fig.3, Al2O3 thermal sprayed coating has superior abrasion resistance to Fe-13Cr coating. This is because Fe-13Cr coating has a lower hardness of HRC 41.5 compared with Al2O3 coating with hardness of HRC 60.0.
3.3 Film thickness influence on echo height
In the experiment, we used bottom echo multi- reflection pattern to investigate characteristic for each material. Fig.4 shows bottom echo multi-reflection diagrams and the cross section morphologies for Al2O3 coatings. From this figure, the height of the first bottom echo increased when the coating thickness decreased. The same patterns were also observed in Fe-13Cr coatings.
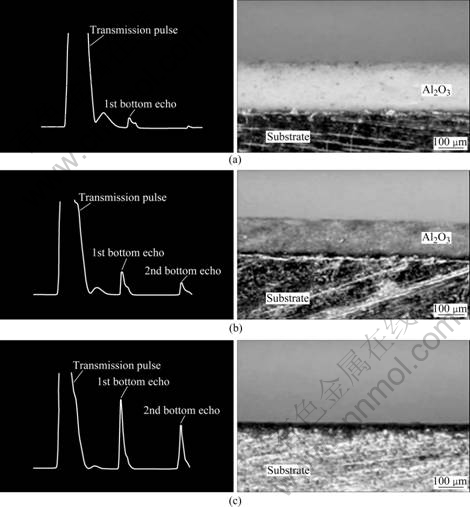
Fig.4 Bottom echo multi-reflection diagram and cross section morphologies for Al2O3 coatings: (a) t=0 s (a=250 μm); (b) t=5 s (a=240 μm); (c) a=0
Fig.5 shows the relationship between coating thickness(a) and echo height(H) for Al2O3 and Fe-13Cr measured in air and water.
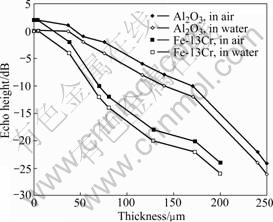
Fig.5 Relationship between coating thickness and echo height
From Fig.5, we can observe that echo height(H) becomes smaller as the coating thickness(a) increases. This is because when ultrasonic waves propagate, the waves are irradiated to medium surface and bottom face, which are parallel to each other at a speed unique to the medium. In the process, the energy is gradually attenuated by reflection at both ends of the base material faces and completely disappears.
Fig.5 also shows that Al2O3 has a higher value of H compared with Fe-13Cr coatings. This indicates that Fe-13Cr coatings absorbed higher ultrasonic wave than Al2O3 coatings. The conclusion is made by comparing acoustic impedance for each coating that corresponds directly to ultrasonic wave absorption. Acoustic impedance is 1.71 for Al2O3 and 4.53 for Fe-13Cr[2], which enables Fe-13Cr coatings to absorb more ultrasonic wave, thus resulting in the lower echo height.
3.4 Epoxy resin sealed coating thickness influence on echo height
Fig.6 shows relationship between echo height and coating thickness with blasting time(t) from epoxy resin sealed Al2O3 tested piece. Ultrasonic inspection was conducted by spreading contact substance on the epoxy resin sealed contact surface. Film thickness, a=0 mm, in Fig.6 indicates the border between thermal sprayed coating and epoxy resin seal. From this figure, we can observe that the amount of abrasion on the coating increased with the decrease in coating thickness proportional to blasting time (t).
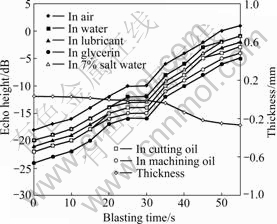
Fig.6 Relationship among echo height, coating thickness and blasting time
Fig.6 also shows that echo height became 2 dB lower when being measured in water. Echo height became lower by 7% in salt water, 14% in lubricating oil and 18% in machining oil. Echo height measured in glycerin dropped by as much as 6 dB, which proves that oily substances such as glycerin absorb greater amount of ultrasonic wave energy compared with other substances. From these results, it can be said that degree of abrasion can be measured accurately in atmosphere because of higher echo height and detecting sensitivity. In this experiment, coating thickness decrease rate for epoxy resin sealed coatings was smaller than that for unsealed coatings. Smaller rate can be attributed to comparative softness of sealing agent compared with thermal sprayed coatings, based on the basic characteristic of blasting that the harder the material, the greater the collision energy used for abrasion[3].
Table 1 lists the density of contact substances measured using Archimedean principle[4]. Based on Table 1 and Fig.6, acoustic impedances for atmosphere and contact substances other than glycerin are believed to be in the same value.
Table 1 Density of contact substances and thermal sprayed material
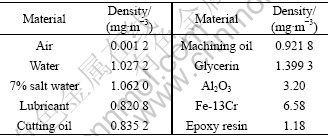
We make this assumption by comparing the density of atmosphere, which is very close to other contact substances except for glycerin. By roughly classifying substances density, we manage to establish relationship between impedance and density[5].
4 Conclusions
1) In this experiment, decrease in coating thickness makes echo height increased because thermal spray coating absorbs ultrasonic energy.
2) Ultrasonic energy absorbed by Al2O3 is smaller than that by Fe-13Cr sprayed coating.
3) Echo height measured in water is smaller by approximately 2 dB compared with atmosphere regardless of coating type.
4) In oily substances, echo height drops by approximately 2 dB compared with atmosphere because of larger impedance value for oily substances.
5) From this experiment, we can conclude that degree of wear can be effectively measured by observing changes in amplitude of ultrasonic wave echo reflected from bottom surface of a subject.
References
[1] Japan Thermal Spraying Society. Handbook of thermal spraying technology [M]. Tokyo: 1998: 82-83, 300, 349-356, 421, 576.
[2] Japan Society for the Promotion of Science. Ultrasonic material testing [M]. Tokyo: 1973: 30-31, 220, 303, 768.
[3] KUBOHORI T, YAMAMOTO Y, INUI Y, IKUTA T. Study on blasting—Effect of specimen temperature on blasting [J]. Journal of Japan Thermal Spraying Society, 2005, 42(1): 1-6.
[4] SERWAY R A. Physics for scientists and engineers [M]. 3rd ed. New York: Saunders College Publishing, 1992: 414.
[5] MINOWA Z. Density and concentration [M]. Tokyo: Corona Publishing Co., 1974: 131.
Corresponding author: Toshifumi KUBOHORI; Tel: +81-06-6721-2332; E-mail: kubohori@mech.kindai.ac.jp
DOI: 10.1016/S1003-6326(08)60391-X
(Edited by YANG Bing)