Trans. Nonferrous Met. Soc. China 23(2013) 2686-2691
Size effects on plastic deformation behavior in micro radial compression of pure copper
Li-dong CHENG1, Chuan-jie WANG2, Chun-ju WANG2, Bin GUO2, Zhen-long WANG1
1. School of Mechatronics Engineering, Harbin Institute of Technology, Harbin 150001, China;
2. School of Materials Science and Engineering, Harbin Institute of Technology, Harbin 150001, China
Received 10 July 2012; accepted 26 May 2013
Abstract: Micro radial compression tests were carried out on cylindrical specimens of pure copper polycrystals with different grain sizes. Experimental results indicated that phenomena of decreasing forming force, increasing scatter of forming force and more irregular surface topography occurred with the increase of grain size. A modified surface model based on dislocations pile-up in surface layer grains, and a flow stress scattering formulation based on standard deviation and grain size distribution were proposed to analyze size effects on forming force in micro compression. The inhomogeneous deformation of surface layer grains was discussed by the main deformation manner of rotation. A good agreement with the experimental results was achieved.
Key words: micro-forming; size effects; radial compression; inhomogeneous deformation; scatter of forming force
1 Introduction
A growing demand on micro metal components is mainly driven by the quick development of micro electro mechanical systems (MEMS) and micro system technology (MST). Some commercial micro metal parts such as connector pins, miniature screws, contact springs, chip leadframes and IC-sockets have been widely applied to micro electronics [1,2]. However, kinds of disadvantages restrict these micro manufacturing methods widely applied to industry, such as micro machining, micro-EDM, micro-electrochemical machining and LIGA-process [3]. Micro-forming is a promising technology in manufacturing micro metal parts, because it offers many attractive virtues, such as higher production rates, better material integrity, less waste and lower manufacturing costs. However, when material parameters keep constant, some challenges, like size effects, occur during the scaling down of components dimensions. The traditional material deformation thesis cannot be applied directly to micro scale deformation. A great deal of investigation has been carried out by the former researchers. GEIGER et al [4-7] did some experimental researches on size effects of flow stress in micro upsetting deformation, and they proposed a surface model to interpret the phenomena. Size effects also occur in micro sheet axial-stretching deformation, and flow stress decreases with the decreasing specimen thickness, excluding that grain size is bigger than specimen thickness [8-10].
EICHENHUELLER et al [11] studied the deformation behavior in micro forming at elevated temperature, and indicated that elevated temperatures are suitable for enlarging the forming limits and minimizing size effects in micro forming. WANG et al [12] and CHAN et al [13,14] did some work on the size effects of flow stress and scattering in micro upsetting deformation.
et al [15] developed a mesoscopic model based on the intergranular interactional and Hall-Petch relationship to analyze the mechanism of size effects. SHEN and YU [16] proposed a composite model to simulate the size effects on the reduction of flow stress in micro-forming. CHAN et al [13] introduced a novel method based on the experimental results and composite model to analyze the effect of material microstructure characterizations on deformation behavior and scattering of flow stress. Comprehensive review on development of size effects investigations in micro forming was presented in Refs. [1,17-20]. These studies before were focused on the decreasing of flow stress in micro- forming. However, few researches have been done to analyze the mechanical of scattering flow stress.
In this study, effects of grain size on plastic flow, forming force and its scattering were studied by micro upsetting deformation of cylindrical specimens. A modified surface model based on piling up of dislocations in surface layer grains and a flow stress scattering model based on standard deviation and grain size distribution were proposed to analyze the mechanism of size effects in micro upsetting deformation. The inhomogeneous deformation in the surface layer grains was discussed by the main deformation manner of rotation.
2 Experimental
The dimensions of T2 copper cylindrical specimen were d1.0 mm × 5.0 mm to obtain the plain strain condition. The samples were annealed at temperatures ranging from 400 °C to 800 °C, and the grain sizes were in the range of 11.5-121 μm, and the ratio of sample diameter to grain size λ was in the range of 8-97. The annealing parameters and the obtained grain sizes are shown in Table 1, and the microstructures of treated materials are shown in Fig. 1. The lubricant graphite was applied to minimizing the friction size effect in experiment. The experiment was carried out at room temperature with a strain rate of
=0.0025 s-1 and a compression ratio of 50%.
Table 1 Heat treatment process and obtained grain sizes after annealing
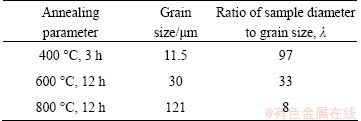
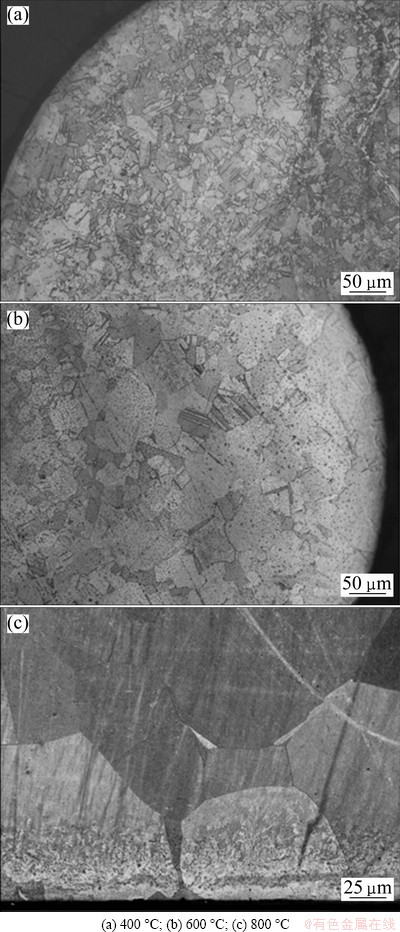
Fig. 1 SEM images of specimens treated at different temperatures
3 Results and discussion
3.1 Influence of grain size on forming force
In traditional crystalline metal forming, material mechanical behavior is dependent on grain size and can be formulated by relationship among yielding stress σs, friction stress in lattice σ0, grain size d and material constant K which represents the grain boundary effect strength on the crystal mechanical behavior, that is, Hall-Petch relationship:
(1)
However, the surface layer grains dominate the deformation with the reduction of specimen size or the increasing of grain size. Dislocations moving through the grains pile up at grain boundaries but not at the free surface during plastic deformation. It results in less being hardened for surface layer grains than for the internal grains. The material constant Ks of surface layer grain is smaller than Ki of the internal layer grains based on dislocations piling-up, as shown in Fig. 2. Based on the surface model [6], the flow stress can be expressed as
σs=αsσs-s+αiσs-i (2)
where αs and αi represent the shares of surface and inner face layer grains in the cross section of micro parts.
αs+αi=1 (3)
Substituting Eq. (1) with Ks and Ki and Eq. (3) into Eq. (2), a modified surface model which denotes the whole mechanical behavior of micro metal parts considering the Hall-Petch relationship and piling up of dislocations is constructed.
(4)
where σs-i, d and D (Fig. 3) are flow stress of internal layer grains (equals polycrystalline), average grain size and specimen diameter, respectively.
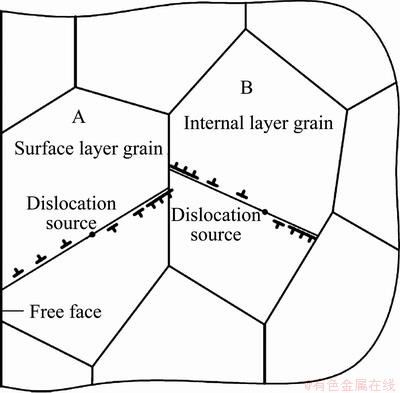
Fig. 2 Dislocation piling-up model
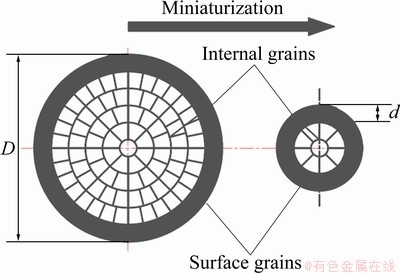
Fig. 3 Ratio of surface grains to total grains
The first term in the right of Eq. (4) is equal to flow stress in macro metal forming, and the second term represents the effect of surface grains on the integrated mechanical property. When D
d, the term [1-(1-2d/D)2] approaches to zero, which means that the surface layer grains affecting term almost has nothing on the whole material mechanical behavior, Eq. (4) can be simplified as σs=σs-i. This is accordant with the traditional continuous material model. However, with increasing of grain size d or decreasing of specimen size D, the term [1-(1-2d/D)2] ranges from 0 to 1. The surface grains affecting term has a negative effect on the whole material properties, which means that σs is smaller than σs-i. Accordingly, the reduction of forming force in micro metal forming occurs, just as shown in Fig. 4. When D=2d, just only two grains situate in the specimen section, the term [1-(1-2d/D)2] equals 1, then Eq. (4) is simplified to
(5)
There are no internal grains in the specimen. This is consistent with the former hypothesis of surface model.
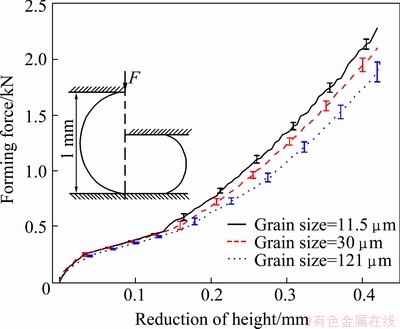
Fig. 4 Forming force and scatter in micro upsetting
From Fig. 4, an increasing trend of forming force scattering is observed with the increasing of grain size. It is a representative phenomenon in micro-forming. The scatter mainly results from inhomogeneous distributions of grain size and orientation with decreasing of grain amount in a sample. The effect of distributions of grain size and orientation on the flow stress can be expressed as
(6)
(7)
where fi and di are the fraction and grain size of the ith grain; n is the total number of grains in a sample; MTaylor and τc are mean Taylor factor and critical resolved shear stress.
It is clear that flow stress is also related to the distributions of grain size and orientation especially for several grains in the sample. To analyze the distributions of grain size and orientation for several grains located in the sample, the 11.5 μm grain sized sample was applied, as shown in Fig. 5. The comparison of distribution of grain size and orientation are shown in Fig. 6 and Fig. 7. It can be seen that the grain size distribution with a large number of grains is smooth and like normal distribution, the grain size distribution with several grains is fluctuated severely. The grain orientation and distribution also give a similar tendency when there are several grains located in the sample. With the increasing of grain size or decreasing of sample size, the effect of distributions of grain size and orientation becomes stronger, and the scatter of forming force increases.
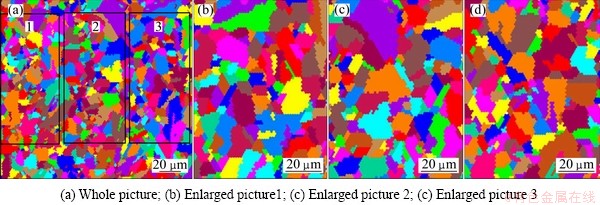
Fig. 5 Grain size distribution

Fig. 6 Grain size distribution

Fig. 7 Taylor factor distribution
3.2 Influence of grain size on plastic flow
The topography exhibiting in the specimen surface is shown in Fig. 8. With the increasing of grain size, the scraggly topography exhibiting in the specimen surface tends to be more distinct, which results from inhomogeneous deformation of surface grains. Grains in surface layer are less restricted because for one or two free boundaries during deformation, rotation is easier than slipping. As for samples with grain size of 11.5 μm, large height reduction does not cause scraggly topography, as shown in Fig. 9. This implies that the scraggly topography on the sample surface will not appear at whatever strain when grain size is comparable small to the sample size (e.g. D/d=97), and the scraggly topography appears on the sample surface when the ratio of sample size to grain size is comparable small (e.g. D/d=8) at a proper strain. To analyze the inhomogeneous deformation in details, the microstructure and grain orientation distribution maps of deformed samples are obtained as shown in Fig. 10.
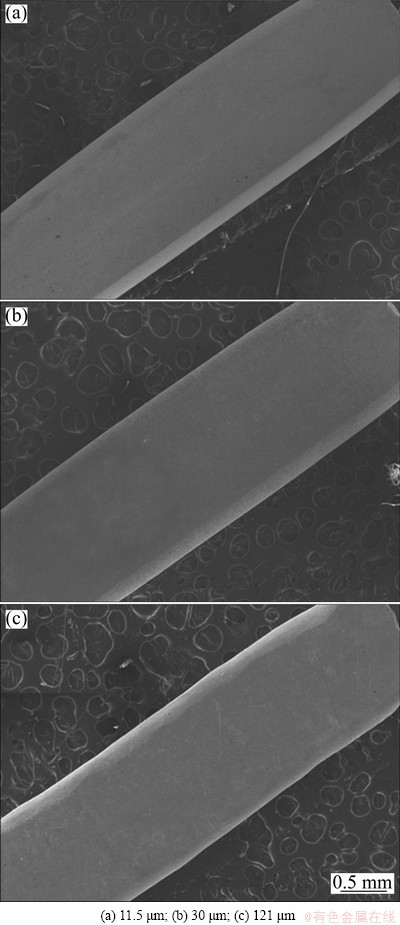
Fig. 8 SEM images of micro deformed specimens with different grain sizes
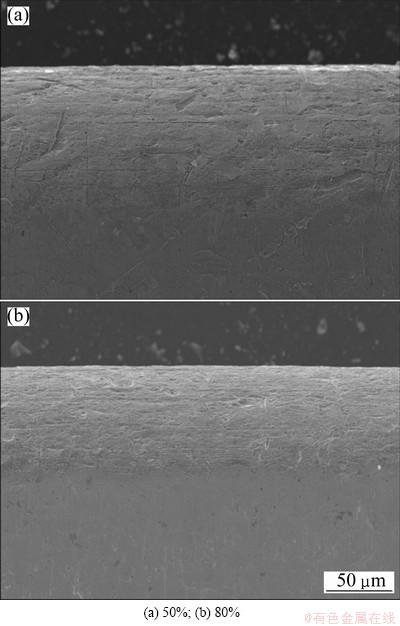
Fig. 9 Surface topographies of samples at different height reduction
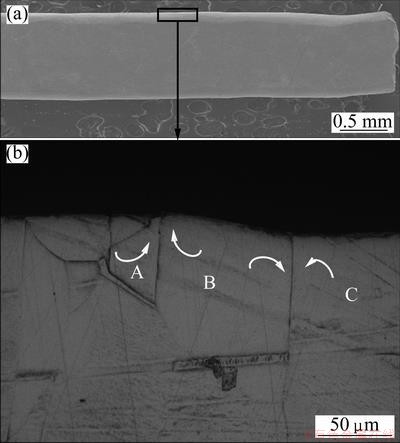
Fig. 10 Microstructures of deformed part (d=121 μm)
Inhomogeneous deformation is related with the orientation, distribution of grains located in the plastic deformation field for metal forming. For polycrystalline metal forming, grains mainly underg two deformations: rotation and slipping. The grain boundaries, through rotation and gliding, play a very important role in harmonizing intergranular deformation, but less deformation occurs in the grain boundaries. So, rotation dominates the deformation and results in some changes of micro topography on the surface. With the miniaturization of specimens or increase of grain size in micro forming, intergranular inhomogeneous deformation increases compared to specimens with a larger number of grains in macro metal forming.
4 Conclusions
Micro radial upsetting of copper was carried out at room temperature. With the increase of grain size, size effects appeared, such as decreasing of forming force, increasing of scatter of forming force and also more heterogeneous deformation in the specimen surface. Then, a modified surface model based on surface layer model and considering Hall-Petch relationship and dislocations pile-up in surface layer grains was proposed to interpret the decreasing of forming force successfully. Also, an analytical model of explaining the forming force scattering based on the Hall-Petch relationship and standard deviation formulation was introduced. They are good agreement with the experimental results. Surface layer grains prefer rotation to slipping because of less restriction than internal layer grains. So, a scraggly topography on the surface occurs. This research also indicates that it is necessary to consider the properties of every single grain. The reason is that every single grain plays an important role in deformation behavior of specimen with the increase of grain size or the decrease of specimen dimensions in micro forming.
References
[1] GEIGER M, KLEINER M, ECKSTEIN R. Microforming [J]. CIRP Annals-Manufacturing Technology, 2001, 50(2): 445-462.
[2] VOLLERTSEN F, SCHULZE NIEHOFF H, HU Z. State of the art in micro forming [J]. International Journal of Machine Tools and Manufacture, 2006, 46(11): 1172-1179.
[3] QIN Y. Micro-manufacturing engineering and technology [M]. Oxford: Elsevier Publishers, 2010: 8-13.
[4] GEIGER M, MESSNER A, ENGEL U. Production of microparts— size effects in bulk metal forming, similarity theory [J]. Production Engineering, 1997, 4(1): 55-58.
[5] GEIGER M, MESSNER A, ENGEL U, KALS R, VOLLERTSEN F. Design of micro-forming processes fundamentals, material dada and friction behavior [C]//Proceeding of the 9th International Cold Forging Conference. Solihull: FMJ International Publishers, 1995: 155-164.
[6] TIESLER N, ENGEL U, GEIGER M. Basic research on cold forging of microparts [C]//Proceeding of the 7th ICTP. 2002: 379-384.
[7] ENGEL U, ECKSTEIN R. Microforming-from basic research to its realization [J]. Journal of Materials Processing Technology, 2002, 125-126: 35-44.
[8] KALS T A, ECKSTEIN R. Miniaturization in sheet metal forming [J]. Journal of Materials Processing Technology, 2000, 103(1): 95-101.
[9] RAULEA L V, GOIJAERTS A M, GOVAERT L E, BAAIJENS F P T. Size effects in the processing of thin metal sheets [J]. Journal of Materials Processing Technology, 2001, 115(1): 44-48.
[10] GAU J T, PRINCIPE C, WANG J. An experimental study on size effects on flow stress and formability of aluminum and brass for microforming [J]. Journal of Materials Processing Technology, 2007, 184(1): 42-46.
[11] EICHENHUELLER B, EGERER E, ENGEL U. Microforming at elevated temperature-forming and material behaviour [J]. International Journal of Advanced Manufacturing Technology, 2007, 33(1): 119-124.
[12] WANG C J, GUO B, SHAN D B, SUN L N. Effects of specimen size on flow stress of micro rod specimen [J]. Transactions of Nonferrous Metals Society of China, 2009, 19(s2): s511-s515.
[13] CHAN W L, FU M W, LU J, LIU J G. Modeling of the grain size effect on the micro deformation behavior in micro-forming of pure copper [J]. Materials Science and Engineering A, 2010, 527(24): 6638-6648.
[14] CHAN W L, FU M W, LU J. The size effect on micro deformation behaviour in micro-scale plastic deformation [J]. Materials and Design, 2010, 32(1): 198-206.
[15]
S, ENGEL U, GEIGER M. FE-simulation of microforming processes applying a mesoscopic model [J]. International Journal of Machine Tools and Manufacture, 2006, 46(11): 1222-1226.
[16] SHEN Y, YU H P. Construction of a composite model of decreasing flow stress scale effect [J]. Journal of Materials Processing Technology, 2009, 209(17): 5845-5850.
[17] VOLLERTSEN F. Categories of size effects [J]. Production Engineering, 2008, 2(4): 377-383.
[18] GEIGER M, VOLLERTSEN F, KALS R. Fundamentals on the manufacturing of sheet metal microparts [J]. ClRP Annals- Manufacturing Technology, 1996, 45(1): 277-282.
[19] JESWIET J, GEIGER M, ENGEL U, KLEINER M, SCHIKORRA M, DUFLOU J, NEUGEBAUER R, BARIANI P, BRUSCHI S. Metal forming progress since 2000 [J]. CIRP Journal of Manufacturing Science and Technology, 2008, 1(1): 2-17.
[20] VOLLERTSEN F. Size effects in micro forming [J]. Key Engineering Materials, 2011, 473: 3-12.
纯铜径向微压缩塑性变形行为尺寸效应
程利东1,王传杰2,王春举2,郭 斌2,王振龙1
1. 哈尔滨工业大学 机电工程学院,哈尔滨 150001;
2. 哈尔滨工业大学 材料科学与工程学院,哈尔滨 150001
摘 要:对不同晶粒尺寸的纯铜多晶体圆柱试样,开展径向微压缩试样。实验结果表明,随着晶粒尺寸的增大,成形力减弱,分散性增大,并出现不规则表面。提出了基于表层晶粒位错堆积的修正表层模型和基于标准偏差理论和晶粒尺寸分布的流动应力波动性公式,分析了微压缩变形中的成形力尺寸效应。从表层晶粒以旋转为主要变形模式的角度,讨论了表层晶粒非均匀塑性变形。与实验结果吻合很好。
关键词:微成形;尺寸效应;径向压缩;非均匀变形;成形力分散性
(Edited by Hua YANG)
Foundation item: Project (51375113) supported by the National Natural Science Foundation of China
Corresponding author: Chun-ju WANG; Tel: +86-451-86418640; +86-15124527811; E-mail: cjwang1978@hit.edu.cn
DOI: 10.1016/S1003-6326(13)62785-5