
Electrochemical characteristics and surface morphology in non-chromate chemical conversion coating for Zn-electroplated steel sheets
Masazumi OKIDO1, Ryoichi ICHINO1, Seok-Ki JANG2, Seong-Jong KIM2
1. Graduate School of Engineering, Nagoya University, Furo-cho, Chikusa-ku, Nagoya 464-8603, Japan;
2. Division of Marine Engineering, Mokpo Maritime University, Mokpo City, Jeonnam 530-729, Korea
Received 2 March 2009; accepted 30 May 2009
Abstract: The corrosion protection property and morphology of colloidal silica conversion films as an alternative to chemical conversion coating(CCC) films were examined. The corrosion behavior was investigated in 3%NaCl solution using electrochemical techniques. Corrosion was implied by the appearance of red rust on the specimen surface. The results show that in 3%NaCl solution, red rust appears at 15-20, 55-70, and 75-85 d on Zn-electroplated steel, colloidal silica conversion-coated specimens, and chemical conversion-coated, specimens, respectively. In the salt spray test, the colloidal silica film provides better corrosion protection than CCC film, i.e., red rust appears at 96 h on the Zn-electroplated steel sheet, at 432 h on the CCC films, and at 888 h on silica conversion coating.
Key words: colloidal silica conversion film, corrosion salt spray test, rust
1 Introduction
With the heightened awareness of the need to protect terrestrial environments, strict regulations have been enacted governing the discharge of harmful matter that might cause environmental pollution. The regulations governing chrome, especially Cr6+, are strict. According to the pollutant release and transfer resister system and the environmental contaminant discharge movement quantitative register, the amount of Cr6+ used must be decreased. Since some countries have limited the amount of Cr6+ used to 5 g per automobile after the year 2002, automobile manufactures hope to use chrome-free conversion, which does not use Cr6+, in new designs[1]. In addition, to conserve resources and energy, it is necessary to develop a new surface finishing method to solve these problems[2]. Therefore, a new non- chromate-type chemical conversion coating method was studied in this work. The impact of environment on Zn electroplated steel sheets coated with colloidal silica was considered.
2 Experimental
The Zn-electroplated steel sheets used for chemical conversion coating were cleaned with acetone at 298 K, and the zinc surface was activated using 2% (mass fraction) nitric acid solution. After cleaning with water, the specimen was immersed in the chemical conversion coating solution for 90 s with agitation. Then, it was washed with water, and dried with warm air at 353 K for 5 min. The corrosive solution used was 500 mL of 3% (mass fraction) NaCl solution. The impedance experiment used the bipolar method with a counter and working electrodes. Measurements were made at an applied voltage of 10 mV over a frequency range from 10 kHz to 10 mHz, at 10 points per decade (per column). The salt spray test was conducted in the condition of 5% (mass fraction) NaCl, Ph=6.5-7.2, 308 K. The corrosive solution was 3% NaCl, pH 6.5-7.2. The presence of rust was defined with the ratio of corroded area to specimen area.
3 Results and discussion
Fig.1 compared the effect of using sulfuric, hydrochloric, and nitric acids to adjust the pH value of the chemical conversion coating solution containing sulfuric acid titanium. No microcrack was seen in the coatings when the pH was adjusted with sulfuric or hydrochloric acid; but it is seen with nitric acid. This is thought to occur because the nitric acid ion is a strong oxidizer. It is thought that bonds like Si—O—Zn form between the coating and the Zn-electroplated steel sheet. This involves dehydration and condensation involving Si—OH and HO—Zn and HOO—Zn bonds. In addition, when zinc is immersed in nitric acid, the zinc surface dissolves readily and is very reactive[3].
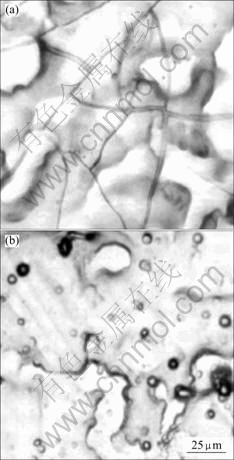
Fig.1 Surface morphologies of silica coating formed from colloidal silica solution containing Ti(SO4)2 adjusted with different solutions to pH 2: (a) HNO3; (b) H2SO4
Fig.2 shows the surface morphologies of the silica film formed from colloidal silica solution containing Ti(SO4)2 observed using optical microscopy. The pH value of the silica conversion solution was varied from 2 to 5. A chemical conversion coating film was produced only at pH 2. At pH 4.0-4.5, the chemical conversion coating solution became white and turbid. It is thought that the addition of the sulfuric acid titanium changed the nature of the colloidal silica solution.
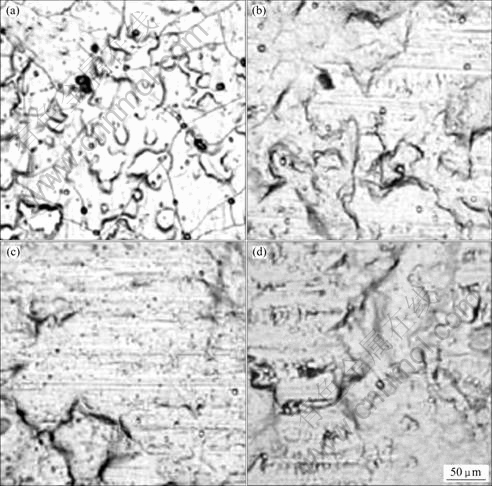
Fig.2 Surface morphologies of silica coating formed from colloidal silica solution with Ti(SO4)2: (a) pH 2; (b) pH 3; (c) pH 4; (d) pH 5
Fig.3 shows the FT-IR spectra of different silica conversion solutions. In general, FT-IR spectra are used to analyze organic compounds, and have been used to interpret the structures of thin films formed by the sol-gel method[4-7]. Peaks due to Si—O—Si resulting from the colloidal silica were seen near 800, 1074 and 1 238 cm-1. The broad peaks near 1 635 and 3 441 cm-1 are OH- in the film. A peak near 970 cm-1 was seen with the solution containing sulfuric acid titanium (c), and was due to Si—O—Ti[8]. By comparing the films formed from solutions (a) with (c), the spectrum of solution (b), which contains succinic acid, had a sharp peak near 1 238 cm-1. This is thought to be due to Si—O—C, which causes peaks at 1 130-1 250 cm-1[4]. Succinic acid was added to buffer the solution against an increase in pH due to local reactions. However, the succinic acid was absorbed during the chemical conversion process. In addition, the Ti in the chemical conversion coating solution exists as Ti4+. It is thought that the Si-O- on the silica surface combines with Ti4+[9].
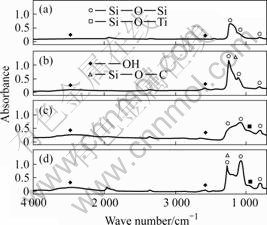
Fig.3 FT-IR spectra for different silica conversion solutions: (a) Colloidal silica; (b) Colloidal silica+C2H4(COOH)2; (c) Colloidal silica+Ti(SO4)2; (d) Silica conversion solution
Fig.4 presents the changes in the corrosion resistance exposed to 3%NaCl with time. The impedance locus consisted of high- and low-frequency loops. The shape did not change with the duration of chemical conversion treatment or immersion in the corrosive solution, although the magnitude changed. Charge transfer resistance Rct was calculated from the semicircle on the high frequency side of the impedance locus. In addition the entire surface of the specimen was covers with white rust (zinc hydroxide). Red rust first occurred on the Zn-electroplated, silica-coated, and chemical conversion-coated specimens at 15-20, 55-70, and 75-85 d, respectively. Moreover, with the CCC, immediately after immersion in the corrosive solution, pitting corrosion occurred in some regions and not in others. The progression of corrosion was slower in specimens without pitting corrosion. Once pitting corrosion occurs, corrosion resistance recovers with the generation of Zn products. The marked corrosion in the regions where pitting corrosion occurs is thought to affect the time at which red rust appears.
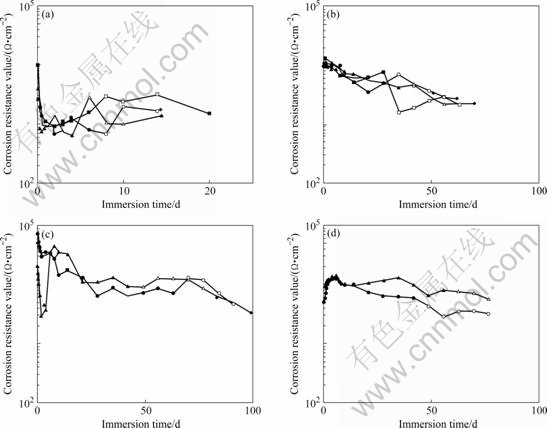
Fig.4 Corrosion resistance value (Rct) with immersion time in 3% NaCl: (a) Zn-electroplated; (b) Colloidal silica-coated; (c) Chemical conversion-coated; (d) Silica-coated with PVA
Fig.5 shows the change in the open circuit potential in 3% NaCl at 303 K, which was measured at the same time as the corrosion resistance using the alternative current impedance method. With time, the potential of the specimen increased gradually from -0.8 to -0.9 V, and zinc hydroxide covered the entire surface of the specimen as the potential rose. For the chromate chemical conversion coating, the effect depended on pitting corrosion (Fig.5(c)). In the specimen with pitting corrosion, the potential started rising 20 d after immersion, and the entire specimen was covered with zinc hydroxide after 50 d.
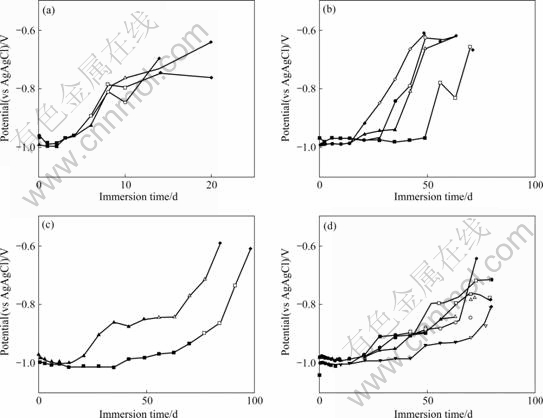
Fig.5 Open circuit potential with immersion time in 3% NaCl at 303 K: (a) Zn-electroplated coating; (b) Silica conversion coating; (c) CCC; (d) (Silica+polyvinyl alcohol) coating
Conversely, it took about 70 d for specimen without pitting corrosion. The time until red rust formed on the Zn-electroplated, silica chemical conversion coated, and chemical conversion coating with PVA was 15-20, 50-70, and 75-85 d, respectivel
Fig.6 displays the surface morphologies after subjecting each coating to the salt spray test. Within 24 h, white rust formed on the Zn-electroplated steel, and red rust covered the specimen at 96 h. The other specimens corroded more gradually. With the CCC, very little white rust was seen at 24 h. This is thought to be due to the self-recovery of the CCC. Furthermore, after 96 h the corrosion was advanced in some specimens. After 200 h, the effect of the silica coating was opposite to that of the CCC. Red rust formed on the CCC and silica coating after 18 and 37 d, respectively. When PVA was added to the silica solution, this took 60 d. It is thought that corrosion occurs more quickly with the CCC due to the presence of advanced pitting corrosion. When zinc metal is soaked in chromate solution, the zinc dissolves. Chromic acid ions are reduced near the zinc as hydrogen ions are generated with the dissolution reaction. This causes the pH near the zinc surface to increase. The chromate coating (Cr(OH)3?Cr(OH)?CrO4) that forms is an insoluble double salt of chromium hydroxide. The CrO4 component, which forms the chromate coating, has the characteristic of self-recovery [10]. However, the corrosion resistance decreases as the Cr6+ in the coating is depleted with self-recovery. Once pitting corrosion occurs, the corrosion resistance vanishes and the region where pitting corrosion occurs is highly corroded. There was a remarkable difference in the immersion experiment. In addition, white and red rust formed at different rates on the silica coating with and without PVA. The evaluation showed that the coating produced has an anti-corrosion barrier function, which is improved by a self-recovery characteristic, as that with chromate.
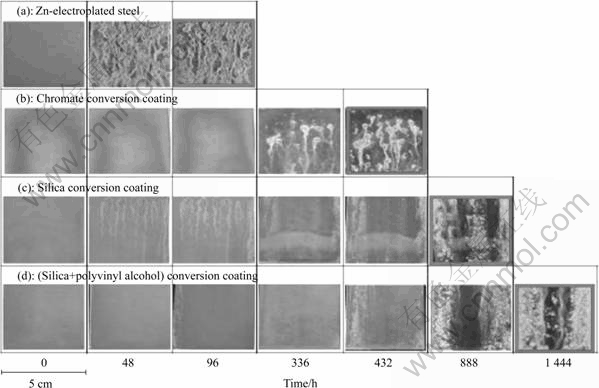
Fig.6 Surface morphologies in salt spray test
4 Conclusions
The formation of red rust on Zn-electroplated, silica-coated, and chemical conversion-coated specimens with PVA immersed in 3% NaCl takes 15-20, 55-70, and 75-85 d, respectively. In the salt spray test, the silica coating is more resistant to red rust formation than CCC, which is opposite to the electrochemical evaluation. Red rust formed after 18, 27, and 60 d on the chemical conversion-coated, silica-coated, and silica-coated with PVA specimens, respectively. Silica chemical conversion coating appears to have a high barrier function.
References
[1] BIBBER J W. A chromium-free conversion coating for aluminum [J]. Metal Finishing, 1993, 91: 46-47.
[2] UMEHARA H, TAKAYA M, KOJIMA Y. An investigation of the structure and corrosion resistance of a permanganate conversion coatings on AZ91 magnesium alloy [J]. Japan Journal of Light Metal, 2000, 50: 109-115.
[3] STILES D C, EDNEY E O. Dissolution of zinc into thin aqueous films as a function of residence time, acidic species, and pH [J]. Corrosion, 1989, 45: 896-901.
[4] PRIMEAU N, VAUTEY C, LANGLET M. The effect of thermal annealing on aerosol-gel deposited SiO2 films: A FTIR deconvolution study [J]. Thin Solid Films, 1997, 310: 47-56.
[5] PARLER C M, RITTER J A, AMIRIDIS M D. Infrared spectroscopic study of sol–gel derived mixed-metal oxides [J]. J Non-Cryst Solids, 2001, 279: 119-125.
[6] SECO A M, ALMEIDA R M. Densification of hybrid silica-titania sol–gel films studied by ellipsometry and FTIR [J]. Master Sci Eng B, 2000, 76: 193-199.
[7] ZHU Y, ONG P P. Evidence of photoluminescence related to subsurface Si-O-Si bonds in sputtered silicon nanoparticles [J]. Solid State Commum, 2000, 116: 427-429.
[8] Hu Chun, Wang Yi-zhong, Tang Hong-xia. Preparation and characterization of surface bond conjugated TiO2/SiO2 and photocatalysis for azo dyes [J]. Applied Catalysis B: Environmental, 2001, 30: 277-285.
[9] ALMEIDA R M. Spectroscopy and structure of sol-gel systems [J]. J Sol-Gel Sci Technol, 1998, 13: 51-59.
[10] KIM S J, HARA M, ICHINO R, OKIDO M, WADA N. Characterization of the silica conversion film formed on zinc-electroplated steel [J]. Materials Transactions, 2003, 44(4): 782-786.
Corresponding author: Seong-Jong KIM; Tel: +82-61-2407226; Fax; +82-61-2407201; E-mail: ksj@mmu.ac.kr
(Edited by ZHAO Jun)