
Effect of extrusion processing parameters on microstructure and mechanical properties of as-extruded AZ31 sheets
JIANG Bin(蒋 斌)1, 2, GAO Liang(高 亮)1, 2, HUANG Guang-jie (黄光杰)1, 2,
DING Pei-dao(丁培道)1, WANG Jian(王 健)1, 2
1. National Engineering Research Center for Magnesium Alloys, Chongqing University, Chongqing 400044, China;
2. College of Materials Science and Engineering, Chongqing University, Chongqing 400045, China
Received 12 June 2008; accepted 5 September 2008
Abstract: The AZ31 sheets were prepared by extrusion. The effects of the extrusion processing parameters including the temperature, extrusion ratio, and structure of the extrusion die on the microstructure and mechanical properties of the as-extruded AZ31 sheets were investigated. The results show that the partial grains grow abnormally and the mechanical and anisotropic properties of the as-extruded AZ31 sheets have little change at the extrusion temperatures of 380-400 ℃ and the extrusion ratio of 13.3. With the increase of the extrusion ratio, the microstructure of the as-extruded AZ31 sheets by conventional die becomes finer and more uniform, and the elongation rate increases, but the strength decreases and its anisotropy becomes worse. Under the porthole die, finer and more uniform microstructure, higher mechanical properties and better anisotropy can be brought for the as-extruded AZ31 sheets. The extruded AZ31 sheets by the porthole die have better anneal process of 300℃ and 1 h.
Key words: AZ31 sheet; extrusion processing; microstructure; mechanical properties
1 Introduction
Conventional production process of magnesium alloy sheets takes many steps, including multi-hot rolling and multi-heat-treatment[1-7]. The as-extruded magnesium alloy sheets with 1-10 mm in thickness can be directly prepared by the conventional extrusion machine [8-13], which can save the expensive blooming mill, shorten the procedure and save cost. Meanwhile, the dynamic recrystallization during the hot extrusion can refine the grains of the as-extruded sheet. Therefore, the extrusion-rolling of the magnesium alloy sheets has attracted much attention. El-MORSY et al[8] reported that large reduction could be used for hot rolling of the as-extruded AZ61 sheet. HSIANG et al[9-10] used the fuzzy theory and the artificial neural network to predict deformation behaviors of sheets during the hot extrusion and optimize the extrusion parameters[11], and then the experimental effectiveness increased definitely. CHANG et al[12] investigated the effect of asymmetric hot extrusion on the AZ31 sheet and fine grains were obtained. ZHANG et al[13] investigated the effect of cross rolling on the microstructure of the as-extruded sheet and proper rolling parameters could bring fine grains for the sheet.
The as-extruded sheet has a great effect on the microstructure and the quality of the rolled sheet after extrusion[13]. In this work, the effects of extrusion processing parameters including temperature, extrusion ratio, and structure of the extrusion die on the microstructure and mechanical properties of the as-extruded AZ31 sheets were investigated in order to optimize the extrusion parameters and get a good quality sheet.
2 Experimental
Materials used in the research were commercial AZ31 ingots whose typical compositions were 2.8%-3.2%Al, 0.8%-1.2%Zn, 0.3%Mn, 0.01%Si, 0.01%Cu and Mg balance (in mass fraction). Before being extruded, the AZ31 ingots were milled and homogenized at 400 ℃ for 12 h. The conventional die and the porthole die were used in the experiment to optimize the structure of the extrusion die. The sizes of the ingots used for conventional die and the porthole die were d252 mm×600 mm and d160 mm×400 mm, respectively. The ingots and dies were heated in a box furnace at 380-400 ℃ for 3 h in order to make the temperature uniform. And then, the extrusion was conducted under the parameters listed in Table 1. After extrusion, the as-extruded sheet was cooled to room temperature in air.
The as-extruded sheet was annealed at different temperatures (300, 350 and 400 ℃) for 1 h. Microstructure was observed by optical microscopy. Mechanical properties of the sheets were tested according to the standard of ASTM. In order to get the anisotropic property of the sheets, the samples for the mechanical property test were cut along the extrusion direction, transverse direction and 45? direction, respectively.
3 Results and discussion
3.1 Effect of extrusion parameters on microstructure of as-extruded AZ31 sheets
When the extrusion ratio is 13.3, coarse and lath-like grains, shown in Fig.1, exist locally in the microstructure of the as-extruded AZ31 sheets under the conventional die and the different extrusion temperatures. Some coarser grains are merging the finer grains near them. At a higher deformation temperature, the growth of the grains will be easier[2]. Therefore, at the extrusion temperature of 400 ℃, the as-extruded AZ31 sheets under the conventional die have the microstructure with a worse uniformity. From Figs.1(a) and (c), it can be seen that the grains at the edge of the sheet are finer, which shows that the deformation during extrusion is very non-uniform.
Under the combination of the extrusion temperature of 400 ℃, the extrusion ratio of 33.2 and the conventional die, the microstructures of the as-extruded AZ31 sheets, shown in Fig.2, mainly consist of equiaxed and mixed grains with a size of 10-60 μm, and few grains are banded. The increase of extrusion ratio will cause the deformation to be increased and more uniform[14]. Thus, the microstructure under the ratio of 33.2 is more uniform.
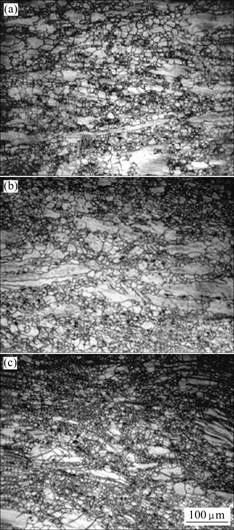
Fig.1 Microstructures of as-extruded AZ31 sheets under extrusion ratio of 13.3 by conventional die: (a) Center of sheet extruded at 380 ℃; (b) Center of sheet extruded at 400 ℃; (c) Edge of sheet extruded at 380 ℃
It is apt for a porthole die to produce a weld zone during the extrusion of the tube and the weld zone in the metal sheet or tube has an obvious bad effect on the properties[15]. Fig.3 shows that the weld zone does not exist in the as-extruded AZ31 sheets by the porthole die. The microstructure of the sheets consists of fine uniform equiaxed grains with the sizes of 20-40 μm and the difference
Table 1 Extrusion parameters used in experiment

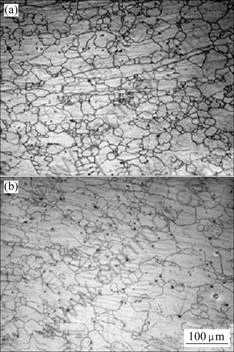
Fig.2 Microstructures of center (a) and edge (b) of as-extruded AZ31 sheets with extrusion ratio of 33.2 at extrusion temperature of 400 ℃ by conventional die
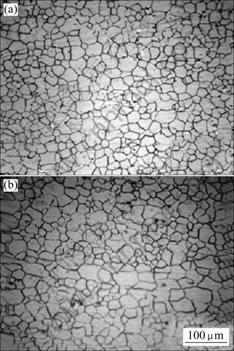
Fig.3 Microstructures of center (a) and edge (b) of as-extruded AZ31 sheets with extrusion ratio of 37.2 at extrusion temperature of 400 ℃ by porthole die
of the microstructure between the center and the edge is less. Thus, the porthole die used plays a better role. Because the porthole die can make the deformation of the metal more uniform[15], together with the uniform deformation resulting from the larger extrusion ratio, the grains of the as-extruded AZ31 sheets are finer and more uniform.
Therefore, in order to obtain the as-extruded AZ31 sheet with good microstructure, the porthole die and larger extrusion ratio are suggested.
3.2 Effect of annealing temperature on microstructure of as-extruded AZ31 sheets
Fig.4 shows the microstructure of the center of the as-extruded AZ31 sheets by using the porthole die after annealing. The grains of the as-extruded AZ31 sheets after annealing are coarser to some degree. With the increase of the annealing temperature, the average size of the grains increases in a small degree and the coarse grains exist locally. The better annealing temperature is 300 ℃ in order to obtain the fine uniform microstructure.
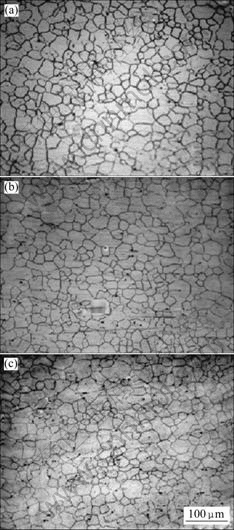
Fig.4 Microstructures of center of as-extruded AZ31 sheets with extrusion ratio of 37.2 at extrusion temperature of 400℃ by porthole die after being annealed at 300 ℃ (a), 350 ℃ (b), and 400 ℃ (c) for 1 h
3.3 Effect of extrusion parameters on mechanical properties of as-extruded AZ31 sheets
The mechanical properties of the as-extruded AZ31 sheets under different extrusion parameters are listed in Table 2. Under the conventional die, the extrusion temperatures of 380-400 ℃ have little effect on the mechanical properties because of the little difference of microstructure.
Table 2 Mechanical properties of as-extruded AZ31 sheets
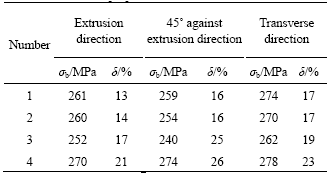
With the increase of the extrusion ratio, the elongation rate in the three directions of the as-extruded AZ31 sheets increases obviously because the microstructure evolved from non-uniform and coarse to uniform and fine, as shown in Figs.1-3. Meanwhile, under the conventional die, the strength of the as-extruded AZ31 sheets decreases and the anisotropy becomes stronger, which may result from the increase of inside stress and different texture characteristics of the as-extruded AZ31 sheets under different extrusion ratios[16]. Under the porthole die, the mechanical properties of the as-extruded AZ31 sheet are optimal and the anisotropies are better because of its finer and more uniform microstructure.
Table 3 lists the mechanical properties of No.4 as-extruded AZ31 sheet after annealing. The strength and elongation rate of No.4 as-extruded AZ31 sheet increase and their anisotropies improve at the annealing temperature of 300 ℃, resulting from the inside stress relief and the little change of microstructure. With the further increase of the annealing temperature, the strength
Table 3 Mechanical properties of No.4 as-extruded AZ31 sheet after annealing
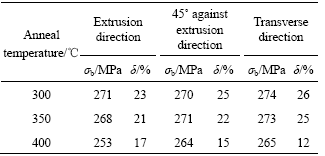
and elongation rate of No.4 as-extruded AZ31 sheet decrease and their anisotropies become worse because of the coarser and non-uniform microstructure.
4 Conclusions
1) When the extrusion temperature is 380-400 ℃ and the extrusion ratio is 13.3, the microstructure of the as-extruded AZ31 sheets by the conventional die is non-uniform and the mechanical properties and anisotropies have little change.
2) Under the conventional die, the increase of extrusion ratio causes the microstructure of the as-extruded AZ31 sheets to be finer and more uniform, the elongation rate to be increased, and the strength and the anisotropy to be decreased.
3) Applying the porthole die for the extrusion of the AZ31 sheet can make the grains further fine and uniform, increase the mechanical properties and improve the anisotropy of the mechanical properties. When the annealing temperature is 300 ℃, the as-extruded AZ31 sheet by the porthole die can obtain better mechanical properties and anisotropy.
References
[1] WANG L Y, FAN Y G, HUANG G J, HUANG G S, PAN F S, LIU Z H. Texture of AZ31B magnesium alloy sheets [J]. Chinese Journal of Materials Research, 2004, 18(5): 466-470. (in Chinese)
[2] WANG L Y, FAN Y G, HUANG G J, HUANG G S. Flow stress and softening behavior of wrought magnesium alloy AZ31B at elevated temperature [J]. Trans Nonferrous Met Soc China, 2003, 13(2): 335-338.
[3] JEONG H T, HA T K. Texture development in a warm rolled AZ31 magnesium alloy [J]. Journal of Materials Processing Technology, 2007(187/188): 559-561.
[4] KIM W J, LEE J B, KIM W Y, JEONG H T, JEONG H G. Microstructure and mechanical properties of Mg-Al-Zn alloy sheets severely deformed by asymmetrical rolling [J]. Scripta Materialia, 2007(56): 309-312.
[5] CHINO Y, SASSA K, KAMIYA A, MABUCHI M. Enhanced formability at elevated temperature of a cross-rolled magnesium alloy sheet [J]. Materials Science and Engineering A, 2006(441): 349-356.
[6] PE?REZ-PRADO M T, VALLE J A, RUANO O A. Achieving high strength in commercial Mg cast alloys through large strain rolling [J]. Materials Letters, 2005 (59): 3299-3303.
[7] J?GER A, LUK?C P, G?RTNEROV? V, BOHLEN J, KAINER K U. Tensile properties of hot rolled AZ31 Mg alloy sheets at elevated temperatures [J]. Journal of Alloys and Compounds, 2004(378): 184-187.
[8] EL-MORSY A, ISMAIL A, WALY M. Microstructural and mechanical properties evolution of magnesium AZ61 alloy processed through a combination of extrusion and thermomechanical processes [J]. Materials Science and Engineering A, 2008(486): 528-533.
[9] HSIANG S H, LIN Y W. Application of fuzzy theory to predict deformation behaviors of magnesium alloy sheets under hot extrusion [J]. Journal of Materials Processing Technology, 2008(201): 138-144.
[10] HSIANG S H, KUO J L. Application of ANN to the hot extrusion of magnesium alloy sheets [J]. International Journal of Advanced Manufacturing Technology, 2005, 25(3/4): 292-300.
[11] HSIANG S H, KUO J L. An investigation on the hot extrusion process of magnesium alloy sheet [J]. Journal of Materials Processing Technology, 2003(140): 6-12.
[12] CHANG L L, WANG Y N, ZHAO X, HUANG J C. Microstructure and mechanical properties in an AZ31 magnesium alloy sheet fabricated by asymmetric hot extrusion [J]. Materials Science and Engineering A, doi: 10.1016/j.msea. 2008.06.015.
[13] ZHANG Q L, HU Y X, WANG L L, SUN Y W, ZHOU Y L. Microstructure of magnesium alloy thin plate cross-rolled after extrusion [J]. Hot Working Technology, 2007, 36(9): 1-5.
[14] WANG L Y, HUANG G S, FAN Y G, HUANG G J. Grain refinement of wrought AZ31 magnesium alloy [J]. The Chinese Journal of Nonferrous Metals, 2003, 13(3): 594-598. (in Chinese)
[15] YANG X H, BAI W H, ZHANG M K. Optimization of geometric parameters of convergence chamber for continuous extrusion forming [J]. Journal of Harbin Institute of Technology, 2000, 32(5): 17-20. (in Chinese)
[16] QU J H, LI S J, ZHANG Z G, WANG F, ZUO L. Effect of extrusion and annealing technology on microstructure and texture of AZ31 magnesium alloy [J]. The Chinese Journal of Nonferrous Metals, 2007, 17(3): 434-440. (in Chinese)
(Edited by LI Xiang-qun)
Foundation item: Project(50604020) supported by the National Natural Science Foundation of China; Project(2007CB613706) supported by the National Basic Research Program of China; Project(3581) supported by the Natural Science Foundation project of CQ CSTC, China
Corresponding author: JIANG Bin; Tel: +86-23-65111140; E-mail: jiangbinrong@cqu.edu.cn