
pH value in simulated occluded corrosion cell for magnesium alloys
ZENG Rong-chang(曾荣昌)1, CHEN Jun(陈君)1, KE Wei(柯伟)2,
Han En-hou(韩恩厚)2, W. Dietzel3
1. School of Materials Science and Engineering, Chongqing Institute of Technology, Chongqing 400050, China;
2. Environmental Corrosion Center, Institute of Metals Research,
Chinese Academy of Sciences, Shenyang 110016, China;
3. GKSS Research Centre Geesthacht GmbH, Geesthacht 21502, Germany
Received 15 July 2007; accepted 10 September 2007
Abstract: Corrosion of magnesium alloys is an important issue for their applications in automobile and aerospace industry. pH values as a function of time in two types of simulated occluded corrosion cells (OCC) for magnesium alloys AZ80 and AM60 were measured. The influence of mass ratio of solution to material or liquid to solid ratio (L/S ratio), initial pH value and chemical compositions of solutions on pH value in OCC was discussed. The experimental results show that pH value for magnesium alloys increases gradually or rapidly in Occ, depending on L/S ratio, initial pH value of solution and chloride ions concentration etc, and then reaches up to 10.5-10.6 and finally stabilizes at the level. The onset in the pH value time curve corresponds to the precipitate of magnesium hydroxide according to the theoretical calculation.
Key words: magnesium alloy; pH value; corrosion; occluded corrosion cell; free corrosion potential
1 Introduction
A growing interest on magnesium alloys has attracted applications in automotive, aerospace and 3C (computer, communication, consumer electronics) industry as well as bioengineering. Corrosion is an important concern for designers and engineers due to the activity of magnesium. Although the corrosion mechanism of magnesium and its alloys have been discussed in the previous studies, the environment in corrosion pits, however, is sparsely investigated[1-3]. It is demonstrated that most of the attack on magnesium alloys takes place in the form of pitting at the initial stage. The corrosion pit is also an initiation of stress corrosion cracking and corrosion fatigue.
Corrosion mechanism of magnesium alloys is quite different from the well-known knowledge dealing with corrosion on steel and aluminium. For instance, it is known that acidification of steel and aluminium occurs in occluded corrosion cells(OCC), pH values of iron and aluminium are 2.70-4.71 and 3.50, respectively[8-10]. SEDRIKS et al[11], however, have reported that pH value of AZ61 in solution after 10 min is stabilized at 11.9. And SONG et al[12] have found that the alkalinization effect caused by corroding magnesium results in an increase in pH value of the SBF to over 9 in about 10 h and finally to a relative stable value of 10.5. And SONG[13] has also observed that a small piece of corroding Mg coupon (1 cm3) can lead to an increase in pH value of 250 mL neutral Hank solution to 10 in 15 h. Therefore, scientific corrosion information, to well understand the mechanism of a corrosion pit or a crack tip, can be obtained through a simulated OCC. It is observed that the shape of corrosion pits of magnesium alloys is hemispherical[14]. And oxygen does not join the electrochemical reactions of magnesium with environment[1-2]. Hence, it is possible to measure the pH value through a simulated OCC. In the present work, pH value in simulated OCC and corrosion mechanisms of magnesium alloys were investigated.
2 experimental
The materials used in this study were the as-extruded and as-cast magnesium alloys Am60 (5.60%-6.40% Al, 0.26%-0.50% Mn, Mg balance). It is very difficult to measure pH value directly in a corrosion pit or a crack tip. Hence, two types of simulated OCC were designed and shown in Fig.1. Type Ⅰ OCC was simulated by using a small container (10 mL) that can contain several small pieces (1 cm×1 cm×1 cm) of magnesium alloy coupons. The mass ratio of solution(liquid) to material(solid) is called L/S ratio. Coupons with 1.44, 2.88 and 4.32 g were separately immersed in 6 mL 3.5% NaCl solution,corresponding to an L/S ratio of 4.2, 2.1 and 1.4, respectively. Type ⅡOCC was the modified one, which was more similar to an actual corrosion pit or a crack tip, simulated by drilling a 25 mm deep hole with a diameter of 16 mm, in addition to a 3.5 mm deep sharp tip with an angle of 118? (shown in Fig.1), in an AM60 ingot.

Fig.1 Schematics of two types of simulated OCC: (a) Type Ⅰ; (b) Type Ⅱ
The solutions applied included NaCl solution, distilled water and Hank’s solution (NaCl 8.0 g/L, KCl 0.4 g/L, CaCl2 0.14 g/L, NaHCO3 0.35 g/L, C6H6O6 1.0 g/L, MgCl2?6H2O 0.1 g/L, MgSO4?7H2O 0.06 g/L, KH2PO4 0.06 g/L and Na2HPO4?12H2O 0.06 g/L). A PHS-25 type pH meter was used to measure the pH value in a simulated cell. All the solutions were prepared by using reagent grade agents and distilled water.
Potential measurement was performed by using an EG & G model 273 potentiostat. Three-electrode system was applied: the working electrode with an exposed surface area of 2.84 cm2; a saturated calomel electrode (SCE) and a platinum plate, used as reference electrode and auxiliary electrode, respectively.
3 Results
3.1 Influence of L/S ratio
the dependence of pH values of Mg alloys in Type I simulated OCC for as-extruded AM60 with various L/S ratios on the immersion time is shown in Fig.2. As can be seen, the pH values increase with increasing time and finally maintain at a relatively stable value of 10.5-10.6. The increase rate depends on the L/S ratio. The smaller the L/S ratio the shorter, the time for pH value to reach up to 10.5. This indicates that alkalinization occurs rapidly in the simulated occ, depending on the L/S ratio.
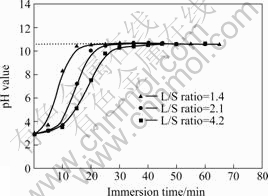
Fig.2 pH values for various L/S ratios as function of immersion time for as-extruded AM60 in 3.5% NaCl solution
3.2 Influence of initial pH value of solution
Fig.3 displays pH values as a function of time for the solutions with initial pH values of 3 and 7. In Type Ⅰ simulated OCC, the pH value increases faster in the solution with an initial pH value of 3 than in that of 7. In spite of different incipient pH values of solutions, their pH values augment up to 10.5 at an approximate time.
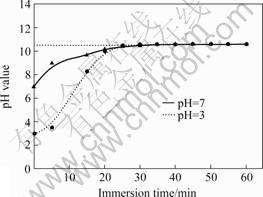
Fig.3 pH value as function of immersion time for as-extruded AM60 alloy in 3.5% NaCl solutions with initial pH values of 3 and 7(L/S ratio=1.4)
3.3 Influence of chloride ions
Fig.4 exhibits the pH value as a function of time for as-cast AM60 alloy in Type II simulated corrosion cells with 3.5% NaCl solution, distilled water and Hank’s solution. It is obvious that pH value rises faster than in 3.5% NaCl solution in distilled water and Hank’s solution. In 3.5% NaCl solution, pH value reaches up to over 10 in 2 min and maintains between 10.5 and 10.8 after then, whereas its value gives rise to 10 in more than 24 min in distilled water and Hank’s solution, and fluctuates between 10.5 and 10.8. More serious pitting attack with hydrogen bubble evolution is observed in Type Ⅱ simulated cells in 3.5% NaCl solution, rather than in distilled water and Hank’s solution. There is no distinct difference for the pH value between distilled water and Hank’s solution. This implies that chloride ion accelerates the alkalinization effect of magnesium alloy in simulated OCC, whereas Ca2+,
,
and
ions in Hank’s solution might to some degree suppress the detrimental impact of Cl- ion.
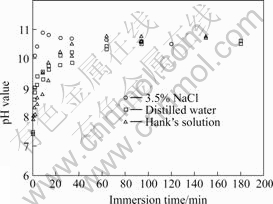
Fig.4 pH values as function of time for AM60 alloy in 3.5% NaCl solution, distilled water and Hank’s solution
Influence of the mass fraction of chloride ion on pH values for as-cast AM60 alloy is demonstrated in Fig.5. In the beginning phase, the mass fraction of chloride ions has a slight effect on the increasing rate of pH value. But in the final phase, there is no obvious difference among the three solutions.
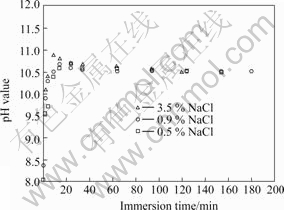
Fig.5 Influence of mass fraction of chloride ion on pH value for AM60 alloy
3.4 Influence of free corrosion potential
To better understand the reason resulting in the change of pH value, the free corrosion potential (Ecorr) and pH value for as-extruded AM60 alloy are measured simultaneously in a corrosion cell with 325 mL 3.5% NaCl solution. The result in Fig.6 exhibits that at the initial stage, Ecorr increases quickly, then decreases gradually, and finally fluctuates between -1.638 and -1.617 V. In the meantime, pH value rises continuously and then tends to become steady at 9.43 after 300 min.
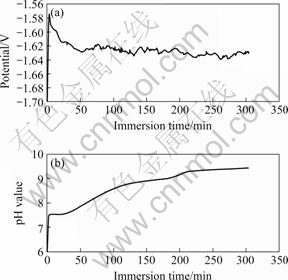
Fig.6 Free corrosion potential (a) and pH value (b) vs immersion time for AM60 alloy in 3.5% NaCl solution
From the corroded sample, several corrosion pits are observed in Fig.7. The upward light lines (indicated by a white arrow in Fig.7) originating at corrosion pits result from hydrogen evolution erasing the surface. The film breakdown and pitting attack around intermetallic particles lead to a decrease in Ecorr and an increase in pH value.
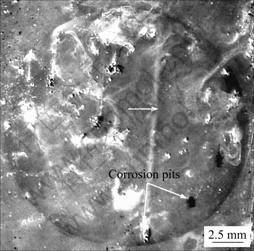
Fig.7 Corrosion morphology of AM60 alloy after 5 h immersion in 3.5% NaCl solution
4 Discussion
The onset on pH value vs immersion time curve represents the time when magnesium ion is saturated and magnesium hydroxide starts to precipitate on the surface. This can be theoretically calculated as follows.
General chemical reactions in corrosion of magnesium alloys are
Mg2++2H2O=Mg(OH)2+2H2 (1)
Mg(OH)2=Mg2++2OH- (2)
Equilibrium constant K in Eqn.(2) is
lgK=lg[Mg2+]+2lg[OH-] (3)
[OH-]?[H+]=10-14 (4)
Insertion of Eqn.(3) into Eqn.(4) yields
lg[Mg2+]=28+lgK-2pH (5)
According to Ref.[11],
K=10-11.05 (6)
Insertion of Eqn.(6) into Eqn.(5) yields
lg[Mg2+]=16.95-2pH (7)
For the solution saturated with Mg2+ ion [15],
[Mg2+]=10-3.90 (8)
Insertion of Eqn.(8) into Eqn.(7) yields
pH =10.43.
The indicates the pH value when Mg2+ ion is saturated. This theoretical value is in pronounced agreement with the measured value.
Eqn.(7) follows
(9)
Eqn.(9) shows that the slope
(pH) of the curves can express corrosion rate of magnesium and its alloys before the saturation of Mg2+ ion.
5 Conclusions
1) The alkalinization occurs rapidly in the simulated occ, depending on the L/S ratio, initial pH value of solution and the concentration of chloride ion.
2) pH value in a simulated OCC remains within a stable range of 10.5-10.7, regardless of the initial pH value in the acidic or neutral solution.
3) The onset of pH value as a function of time corresponds to Mg (OH)2 precipitate in the light of the theoretical calculation.
4) The increase in pH value results from the film breakdown and pitting attack on magnesium alloy AM60.
Acknowledgement
The authors would like to thank Guangling Magnesium Industry Science and Technology Co. Ltd. for providing the tested materials.
References
[1] MAKER G L, KRUGER J. Corrosion of magnesium [J]. Int Mater Rev, 1993, 38: 138-153.
[2] SONG G, ATRENS A. Corrosion mechanisms of magnesium alloy [J]. Adv Eng Mater, 1999, 1: 11-33.
[3] ZENG Rong-chang, ZHANG Jin, HUANG Wei-jiu, DIETZEL W, KAINER K U, BLAEERT C, K E W. Review of studies on corrosion of magnesium alloys [J]. Trans Nonferrous Met Soc China, 2006, 16(S): 763-770.
[4] SONG G, BOWLES A L, JOHN D H. Corrosion resistance of aged die cast magnesium alloy AZ91D [J]. Mater Sci Eng A, 2004, A366: 74-86.
[5] SONG G. Recent progress in corrosion and protection of magnesium alloys [J]. Adv Eng Mater, 2005, 7: 563-586.
[6] SONG G L, ATRENS A, WU X L, ZHANG B. Corrosion behavior of AZ21, AZ501 and AZ91 in sodium chloride [J]. Corros Sci, 1998, 40: 1769-1791.
[7] LUNDER O, AUNE T KR NISANCIOGLU K. The Role of Mg17Al12 phase in corrosion of Mg alloys AZ91 [J]. Corrosion, 1989, 45(9): 741-747.
[8] CHU Wu-yang, QIAO Li-Jie, CHEN Qi-zhi, GAO Ke-wei. Fracture and environmental fracture [M]. Beijing: Science Press, 2000: 178. (in Chinese)
[9] YANG Wu. Local corrosion of metals [M]. Beijing: Chemical Industry Press, 1997: 53. (in Chinese)
[10] POURBAIX M. The electrochemical basis for localized corrosion [M]. Houston: NACE, 1971: 12-33.
[11] SEDRIKS A J, GREEN A S, NOVAK D L. On the chemistry of the solution at tips of stress corrosion cracks in Al alloys [J]. Corrosion, 1971, 27(5): 198-201.
[12] SONG G, SONG S. A possible biodegradable magnesium implant material [J]. Adv Eng Mater, 2007, 9(4): 298-302.
[13] SONG G. Control of biodegradation of biocompatible magnesium alloys [J]. Corros Sci, 2007, 49: 1696-1701.
[14] ZENG R C, HAN E H, KE W J. Corrosion of artificial aged magnesium alloy AZ80 in 3.5% NaCl solutions [J]. Mater Sci & Technol, 2007, 23(3): 353-358.
[15] YANG Xi-zhen, YANG Wu. Electrochemistry and thermodynamics of metal corrosion: potential-pH diagram and its applications [M]. Beijing: Chemical Industry Press, 1991: 13. (in Chinese)
Foundation item: Projects (200413BA4002, 8655) supported by the Natural Science Foundation of Chongqing Municipal Science Commission, China; Project (KJ050604) supported by the Technology Commission and the Science and Technology foundation of Chongqing Municipal Education Commission, China
Corresponding author: ZENG Rong-chang; Tel: +86-23-68665616; E-mail: rczeng2001@yahoo.com.cn
(Edited by CHEN Wei-ping)