
Thermal explosion synthesis of aluminum matrix composites reinforced with TiC-TiB2 ceramic particulates
ZOU Bing-lin(邹兵林), SHEN Ping(沈平), JIANG Qi-chuan(姜启川)
Key Laboratory of Automobile Materials, Department of Materials Science and Engineering, Jilin University, Changchun 130025, China
Received 15 July 2007; accepted 10 September 2007
Abstract: In situ TiC-TiB2 diphase ceramic reinforced aluminum metal matrix composites were successfully fabricated via thermal explosion (TE) reaction in the Al-Ti-B4C system. Using DTA and XRD analyses, the combustion reaction characteristic was examined. The results show that Al serves not only as a diluent but also as a reaction participant, affecting the reaction process and its final products. Combining with the DTA and the TE temperature-time curves, the ignition temperature is estimated to be about 970 K. With increasing Al content, the adiabatic combustion temperature is lowered and the sizes of the TiC and TiB2 particulates decrease. When the Al content in the reactants is more than 50%, Al3Ti intermediate phase is detected in the synthesized products. SEM observations reveal that the nearly spherical TiC particles and hexagonal or rectangular TiB2 particles distribute relatively uniformly in the Al matrix.
Key words: TiC; TiB2; metal matrix composites; thermal explosion; microstructure
1 Introduction
Titanium carbide (TiC) and titanium boride (TiB2) are intriguing ceramics because of their unique combination of properties such as low density, high melting point, high hardness, excellent wear resistance and good chemical stability at high temperatures. Therefore, they are widely used as the reinforcements in aluminum metal matrix composites (MMCs)[1-2]. The TiC and/or TiB2 reinforced aluminum MMCs have a wide range of applications in the automobile, aerospace, civil engineering and military areas when high specific strength and modulus as well as good wear resistance are required[3]. Over the past decades, the aluminum MMCs reinforced with TiC or TiB2 particulates fabricated by in situ processes have been extensively studied. For instance, TEE et al[4] fabricated the in situ TiB2 reinforced aluminum MMCs by stir-casting technique using an Al-Ti-B system, and KERTI[5] fabricated the TiC reinforced aluminum MMCs by the addition of elemental carbon to the molten Al-Ti alloys. However, the literature on the aluminum MMCs reinforced with in situ TiC-TiB2 diphase ceramics is limited. TiC-TiB2 composites possess superior properties such as enhanced fracture toughness and bending strength compared with the constituent ceramic components[6]. Therefore, the study on the TiC-TiB2 diphase ceramic reinforced aluminum MMCs is very important.
Compared with traditional methods such as powder metallurgy, thermal explosion (TE) synthesis technique has the advantages of lower processing cost, higher energy and time efficiency and higher purity of products[7]. In this study, we investigated the TE synthesis reaction of the preform consisting of Al, Ti and B4C powders and aimed at fabricating in situ TiC-TiB2 reinforced aluminum MMCs.
2 Experimental
The starting materials were commercial powders of Al (98.0% in purity, ~29 μm), Ti (99.5% in purity, ~50 μm) and B4C (≥95% in purity, ~3.5 μm). The main impurities in the B4C powders were dissociative boron and carbon together with <1% Fe2O3. The powders were proportioned for Ti and B4C in a molar ratio of 3?1 and Al of 40%, 50% and 60% of the total mass. After homogeneous mixing, the powders were pressed into d 22 mm×15 mm cylindrical compacts with relative densities of (65±2)%.
In order to investigate the TE reaction characteristic, (40±5) mg powder mixtures of 50%Al-Ti-B4C held in an alumina crucible were heated to different temperatures in a DTA apparatus (Rigaku-8150, Japan) at a rate of 20 K/min under a flowing argon gas (flow rate 40 L/min). After the DTA experiments, the samples were crushed into powders and analyzed for their phase constitution by X-ray diffraction (XRD, Rigaku D/Max 2500PC, Japan).
The green compact was placed in an electric resistance furnace. The furnace was evacuated, backfilled with argon and then heated. When the TE reaction was triggered, the power was turned off. The temperature in close to the center of the compacts was measured by W-5% Re/W-26% Re thermocouples and the signals were recorded and processed by a data acquisition system using an acquisition speed of 50 ms/point. Microstructures and phase constitution of the TE reaction products were investigated by scanning electron microscopy (SEM, JSM-6310LV, Japan) and XRD (Rigaku D/Max 2500PC, Japan).
3 Results and discussion
3.1 Differential thermal analysis (DTA)
In order to investigate the TE reaction characteristics of the TiC and TiB2 formation in the Al-Ti-B4C system, the powder mixtures of (40±5) mg of 50%Al-Ti-B4C were heated upon to 1 473 K at a rate of 20 K/min in the DTA apparatus. The DTA curve and XRD patterns are shown in Fig.1. As shown in Fig.1 (a), there exists an endothermic peak at temperature of 935 K, corresponding to the melting of aluminum. With the further increase in temperature, two exothermic peaks at temperatures of 1 030 K and 1 207 K, respectively, appear. In order to clarify the nature of the exothermic reaction at 1 030 K, an interrupted experiment was conducted for the powders heated upon to 1 050 K and then halted. As shown Fig.1 (b), Al3Ti is detected in the resultant products at temperature 1 050 K, which suggests that the first exothermic peak at 1 030 K corresponds to the exothermic reaction Al+Ti→Al3Ti. Also, it can be seen that TiC and TiB2 appear in the reaction products at temperature of 1 473 K and the Al peak intensifies while Al3Ti peak weakens as the temperature increases from 1 050 K to 1 473 K, which implies that the second exothermic peak at 1 207 K corresponds to the exothermic reaction Al3Ti+B4C→TiC+TiB2+Al. In this case, the aluminum powder plays two important roles in the DTA reaction, namely, a reaction participant and a diluent.

Fig.1 DTA curve (a) of Al-Ti-B4C powder mixtures containing 50% Al and XRD patterns (b) for 50% Al-Ti-B4C samples heated at 1 050 K and 1 473 K, respectively
3.2 Temperature—time profile and adiabatic combustion temperature during TE reaction
When the compacts were heated in the electric resistance furnace, the temperatures of the compacts were measured. Fig.2 shows the typical temperature—time curve for the 50%Al-Ti-B4C compact. The heating rate of the electric resistance furnace is about 16 K/min as calculated by the slope of curve during the heating period. The zigzag flat in the temperature—time curve might correspond to the melting of aluminum, which is well in agreement with the endothermic peak in Fig.1 (a). After the aluminum in the compact is completely melted, the temperature of the compact increases rapidly and abruptly from 972 K (ignition temperature, Tig) to 2 318 K (combustion temperature, Tc). It is interesting to note that Tig in the TE reaction is slightly lower than that in the DTA reaction(Fig.1(a)), which may be caused by the disparity in the processing conditions, heating rate and green density of the reactants.
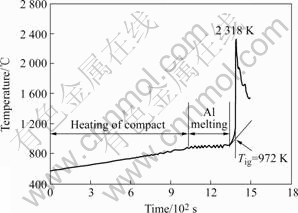
Fig.2 Temperature—time curve for 50%Al-Ti-B4C compact
Assuming that: 1) the initiating temperature (T0) of the TE reaction is equal to Tig (970 K), 2) the products of the TE reaction consist of Al, TiC and TiB2 and 3) no eutectic transformation (TiC+TiB2óLiquid[8]) occurs in the resultant TiC and TiB2 phases, the adiabatic temperature (Tad) can be calculated using thermodynamic data[9] according to the following equation as [10]:
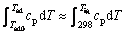
where cp is the specific heat capacity of the products, Tad0 is the adiabatic temperature calculated for T0 = 298 K and Tad is the adiabatic temperature for T0 = Tig. The value of Tad0 has been calculated in our previous paper[11] and the calculated results of Tad in the present study are listed in Table 1. It can be seen that Tad decreases with increasing aluminum content. The actual Tc (2 318 K) for the 50%Al-Ti-B4C compact is smaller than Tad (2 590 K) because of heat loss and the incomplete transition of the Al3Ti intermediate phase to the TiC and TiB2 products(Fig.3(b)).
Table 1 Calculated adiabatic temperatures with different Al contents at T0=970 K
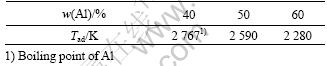
3.3 Synthesized products
Fig.3 shows the XRD results of the TE reaction products. As indicated, the reaction products for the sample with 40% Al content consist of TiC, TiB2 and Al while for the samples with 50% and 60% Al contents, a small amount of Al3Ti is detected in the products besides the aforementioned primary phases. It has been known that Al3Ti is the intermediate phase in the reaction based on the DTA and its corresponding XRD results. It is reasonable to deduce that the Al3Ti phase might also be the intermediate phase in the TE reaction, as inferred from the remnant Al3Ti phase in the samples with 50% and 60% Al content in the reactants. The presence of the remnant Al3Ti phase is attributed to the lower combustion temperature and the longer atomic diffusion distance when the Al content increases.
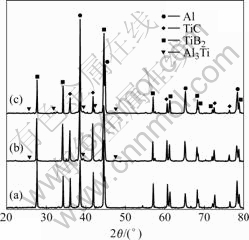
Fig.3 XRD patterns of TE reaction products for Al-Ti-B4C compacts containing 40%Al (a), 50%Al (b) and 60%Al (c), respectively
The microstructures of the samples with the Al contents of 40% and 60% in the reactants are presented in Fig.4, which shows the morphology and distribution of the TiC and TiB2 reinforcements produced in situ in the Al matrix. The nearly round particulates are TiC and the hexagonal or rectangular particulates are TiB2. It has been reported that TiC is in spherical shapes in the SHS products of the Al-Ti-C system[12] and TiB2 is in hexagonal or rectangular shapes in the SHS products of the Al-Ti-B system[13]. The size of these reinforcements decreases from about 4 μm to about 1 μm with the increase of the Al content from 40% to 60%. The decrease of the particle size is attributed to the decrease in the combustion temperature because the crystal growth rate is an exponential function of the combustion temperature[14]. On the other hand, the increase of liquid aluminum surrounding the ceramic particles gives rise to the increased diffusion path, reduces the driving force for the ceramic particle growth, and prevents the sintering among ceramic particles to form larger particulates. It can be seen from Fig.4 that the in situ TiC and TiB2 particles are distributed relatively uniformly in the Al matrix.
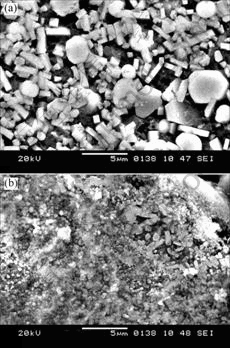
Fig.4 Microstructures of TE reaction products for Al-Ti-B4C compacts with Al contents of 40% (a) and 60% (b), respectively
4 Conclusions
1) It is feasible to fabricate the aluminum matrix composites reinforced with in situ TiC-TiB2 diphase ceramics via the TE reaction synthesis of compacts consisting of Al, Ti and B4C powders.
2) The TE reactions proceed just after the melting of Al, and the ignition temperature for the samples with 40%-60% Al in the reactants is about 970K. The aluminum reactant serves not only as a diluent but also as a reaction participant and Al3Ti is the intermediate phase in the reaction process.
3) With increasing Al content, the adiabatic combustion temperature and the sizes of the TiC and TiB2 particulates decrease obviously. Nearly spherical TiC particulates and hexagonal or rectangular TiB2 particulates distribute relatively uniformly in the Al matrix.
References
[1] TJONG S C, WANG G S. Synthesis and low cycle fatigue behavior of in-situ Al-based composite reinforced with submicron TiB2 and TiC particulates[J]. Adv Eng Mater, 2004, 6(12): 964-968.
[2] LI P J, KANDALOVA E G, NIKITIN V I. In situ synthesis of Al-TiC in aluminum melt[J]. Mater Lett, 2005, 59: 2545-2548.
[3] HUNT W H, HERLING D R. Aluminum metal matrix composite[J]. Adv Mater Proc, 2004: 39-42.
[4] TEE K L, LU L, LAI M O. Synthesis of in situ Al-TiB2 composites using stir cast rout[J]. Comp Struc, 1999, 47: 589-593.
[5] KERTI I. Production of TiC reinforced-aluminum composites with the addition of elemental carbon[J]. Mater Lett, 2005, 59: 3795-3800.
[6] UPADHYA K, YANG J M, HOFFMAN W P. Materials for ultrahigh temperature structural applications[J]. Am Ceram Soc Bull, 1997, 76(12): 51-56.
[7] CAPALDI M J, SAIDI A, WOOD J V. Reaction synthesis of TiC and Fe-TiC composites[J]. ISIJ Inter, 1997, 37(2): 188-193.
[8] GUSEV A I. Phase equilibria in the ternary system titanium- boron-carbon: the sections TiCy-TiB2 and B4Cy-TiB2[J]. J Solid State Chem, 1997, 133(1): 205-210.
[9] LIANG Y J, CHE Y C. Handbook of thermodynamic data of inorganics[M]. Shenyang: Northeastern University Press, 1993. (in Chinese)
[10] HOLT J B, MUNIR Z A. Combustion synthesis of titanium carbide: theory and experiment[J]. J Mater Sci, 1986, 21: 251-259.
[11] ZOU B L, SHEN Ping, JIANG Q C. Reaction synthesis of TiC-TiB2/Al composites from an Al-Ti-B4C system[J]. J Mater Sci, 2007. (accepted)
[12] JIANG Q C, LI X L, WANG H Y. Fabrication of TiC particulate reinforced magnesium matrix composites[J]. Scripta Mater, 2003, 48(6): 713-717.
[13] WANG H Y, JIANG Q C, ZHAO Y Q, ZHAO F, MA B X, WANG Y. Fabrication of TiB2 and TiB2-TiC particulates reinforced magnesium matrix composites[J]. Mater Sci Eng A, 2004, 372(1/2): 109-114.
[14] LEE W C, CHUNG S L. Ignition phenomena and reaction mechanism of the self-propagating high-temperature synthesis reaction in the titanium-carbon-aluminum system[J]. J Am Ceram Soc, 1997, 80(1): 53-61.
Foundation item: Project(50531030) supported by the National Natural Science Foundation of China; projects(2005CCA00300, 2006AA03Z566) supported by the Ministry of Science and Technology of China; project supported by the 985-Automotive Engineering of Jilin University
Corresponding author: JIANG Qi-chuan; Tel/fax: +86-431-85094699; E-mail: jqc@jlu.edu.cn
(Edited by YUAN Sai-qian)