Trans. Nonferrous Met. Soc. China 27(2017) 1019-1025
Evolution of bonding interface in solid-liquid cast-rolling bonding of Cu/Al clad strip
Hua-gui HUANG, Yi-kang DONG, Meng YAN, Feng-shan DU
National Engineering Research Center for Equipment and Technology of Cold Strip Rolling, Yanshan University, Qinhuangdao 066004, China
Received 3 March 2016; accepted 18 September 2016
Abstract: Cu/Al clad strips are prepared using solid-liquid cast-rolling bonding (SLCRB) technique with a d160 mm × 150 mm twin-roll experimental caster. The extent of interfacial reactions, composition of the reaction products, and their micro-morphology evolution in the SLCRB process are investigated with scanning electron microscope (SEM), energy dispersive spectrometer (EDS), and X-ray diffraction (XRD). In the casting pool, initial aluminized coating is first generated on the copper strip surface, with the diffusion layer mainly consisting of α(Al)+CuAl2 and growing at high temperatures, with the maximum thickness of 10 μm. After sequent rolling below the kiss point, the diffusion layer is broken by severe elongation, which leads to an additional crack bond process with a fresh interface of virgin base metal. The average thickness is reduced from 10 to 5 μm. The reaction products, CuAl2, CuAl, and Cu9Al4, are dispersed along the rolling direction. Peeling and bending test results indicate that the fracture occurs in the aluminum substrate, and the morphology is a dimple pattern. No crack or separation is found at the bonding interface after 90°-180° bending. The presented method provides an economical way to fabricate Cu/Al clad strip directly.
Key words: Cu/Al clad strip; solid-liquid cast-rolling bonding; bonding interface; reaction diffusion; peeling test
1 Introduction
The Cu/Al clad strip has many advanced properties, such as high conductivity, light weight, and low price compared with pure copper or copper alloys. Accordingly, it has been widely used as power connectors, tapes, and other electric and heat conductive elements in electrical engineering and heat exchange field [1-3]. At present, several methods are used to produce clad strips, but roll bonding is always one of the effective and efficient processes because of its low cost and high productivity [4,5]. Significant efforts have been spent on improving bonding strength by optimizing the rolling and diffusion annealing heat treatment technology parameters [6-10]. However, time- consuming preparation is necessary for the strip components prior to the roll bonding process, and the total rolling reduction is always no less than 60%.
In recent years, combining the rapid solidification with roll bonding technology has enabled the application of a new short flow process based on twin-roll casting in bimetallic clad strip fabrication [11]. Cladding of Mg alloy with Al has been conducted with twin-roll casting process using melted Mg and solid Al strip by BAE et al [12]. The formability of the Al-Mg-Al cladded sheet could be improved by annealing and secondary rolling to reduce the thickness of the reaction zone. An experiment on twin-roll casting of aluminum-steel clad strips was conducted by GRYDIN et al [13], in which melted Al and solid steel strip were used. Results of deep-drawing and adhesive strength tests for the clad strips have proven the applicability of the strips for further plastic deformation processing. Moreover, with the 1050 aluminum alloy as matrix and mild steel wire as reinforcement element, the wire-inserted composite strip was fabricated using a twin-roll caster [14].
Brittle reactive products, such as CuAl2, are easily generated at the solid-liquid bonding interface between Cu and Al [15,16]. The thickness of the reactive diffusion layer even reaches 50-100 μm under high temperature for a long time [17], which easily weakens the bonding strength. Existing works mostly focus on the diffusion process without deformation or after deformation. The present work deals with a new solid-liquid cast-rolling bonding (SLCRB) technique.A concurrence of solid-liquid and solid-solid hot-roll bonding in SLCRB process exists, which uses solid copper strip and molten aluminum to fabricate Cu/Al clad strip directly with twin-roll caster. A study is also conducted on the bonding mechanism and micro- morphology evolution in the bonding interface.
2 Experimental
As shown in Fig. 1, the solid copper strip and molten aluminum are fed into the roll bite of the twin-roll caster simultaneously. Then, Cu/Al clad strip is fabricated by combining the rapid solidification with hot-roll bonding. The tension of the copper strip and contact angle θ can be controlled using a decoiler. The ladle, tundish, and delivery device ensure the continuity and stability of the feeding molten aluminum into the casting pool. The experiments are conducted on a d160 mm × 150 mm twin-roll experimental caster at National Engineering Research Center for Equipment and Technology of Cold Strip Rolling, Yanshan University, China. Table 1 lists the experimental parameters. The total thickness of Cu/Al clad strip is 2.0 mm, of which 0.5 mm for Cu and 1.5 mm for Al.
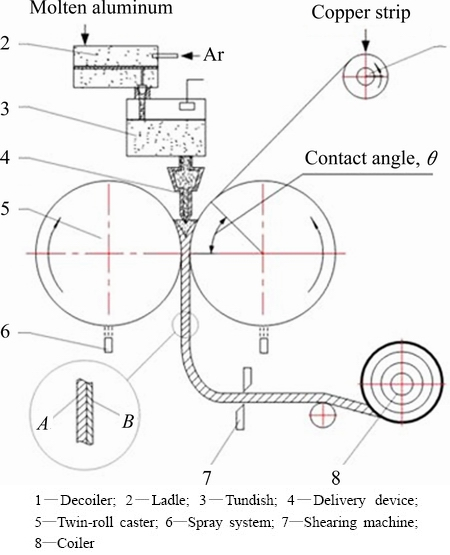
Fig. 1 Schematic diagram for SLCRB of Cu/Al clad strip
The bonding strength of prepared Cu/Al strip was measured by conducting a peeling test using an Instron 5848 tensile tester according to ASTM-D903-93. The test is carried out at room temperature with a peeling speed of 30 mm/min. And the SEM and XRD were applied to observing the micro-morphology evolution of the bonding interface along the rolling direction.
Table 1 Experimental parameters
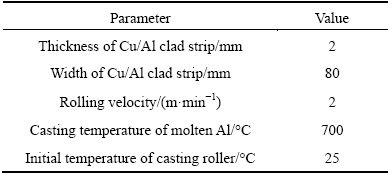
3 Results and discussion
3.1 Overview of cast-rolling bonding area
As shown in Fig. 2, the sliced samples of the workpiece in the cast-rolling bonding area are acquired through emergency stop and quick cooling, among which, a large hole caused by the discontinuity in molten aluminum feeding can be found in Sample 1. Some as-cast defects exist, such as small voids, in the casting pool of Samples 2, 3, and 4. Fortunately, these defects have been eliminated by the sequent rolling entirely below the kiss point, and the compactness of aluminum component is accordingly improved in the final clad strips.
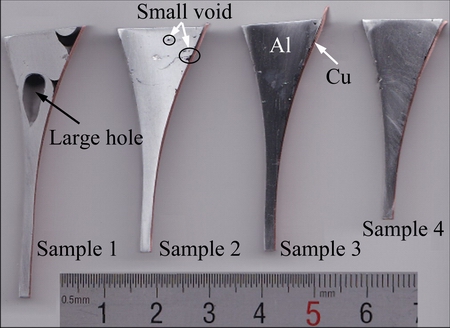
Fig. 2 Sliced samples of workpiece in cast-rolling bonding area
Figure 3 presents the macro-morphology evolution of the bonding interface along the cast-rolling area. In the casting pool, the molten aluminum contacts with copper strip without pressure and a gap can be found between the aluminum and cooper strip (Zone I). Below the kiss point of the cast-rolling area, hot-roll bonding is applied on the solid aluminum and copper strip, and the macro-morphology of bonding interface is obviously improved by severe deformation (Zones II, III and IV). At the exit of the caster, the thickness of copper strip is reduced to some extent (Zone IV).
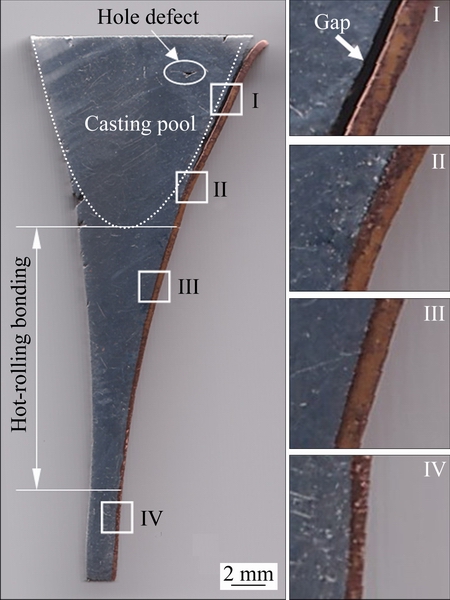
Fig. 3 Macro-morphology evolution of bonding interface
3.2 Micro-morphology of bonding interface
It is well known that the bonding strength depends on the thermodynamic condition at the bonding interface. However, the temperature and deformation distribution along the cast-rolling bonding interface are relatively different. Figure 4 shows the SEM images for Zones III and IV in Fig. 3. As shown in Fig. 4(a), many dents occur on the copper strip surface in zone III, which indicates that the deformation is not large enough to eliminate the scraping trace on the copper strip surface. Thus, the liquid aluminum is filled into the dent, and a thin solid aluminum shell is first generated, with the diffusion layer mainly consisting of α(Al)+CuAl2. It consists of three layers, from the aluminum to copper, lamellar (red arrow), cellulation (blue arrow), and bright lamellar (brown arrow) structures. However, in Zone IV, the exit of the caster, the bonding interface becomes smooth and uniform after large plastic deformation (Fig. 4(b)).
Table 2 presents the EDS analysis results for three points, A, B, and C (Fig. 4(b)), in the diffusion layer of Zone IV. The composition of the reaction products is indicated to be α(Al)+CuAl2, CuAl, and Cu9Al4 from the aluminum to the copper side, successively.
Linear SEM-EDS analysis was carried out for Zones III and IV in Fig. 3. Figure 5 presents the element distribution profiles of the interface. The composition platform in Fig. 5(a) shows that a precipitated phase exists from liquid in Zone III. The thickness of the diffusion layer is reduced from 10 (Fig. 5(a)) to 5 μm (Fig. 5(b)) by hot rolling in the cast-rolling area.
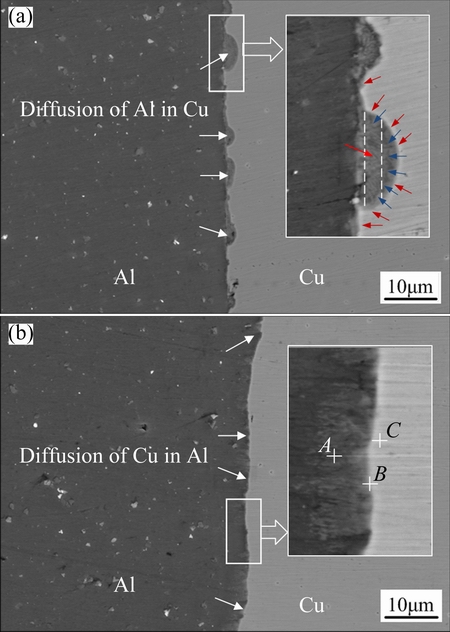
Fig. 4 SEM images of interface for Zones III (a) and IV (b)
Table 2 EDS analysis results of reactive products for bonding interface (in Fig. 4(b))
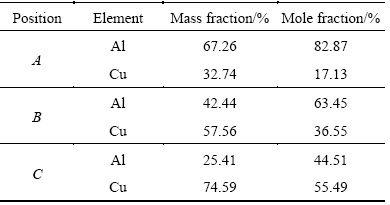
3.3 Peeling test of Cu/Al clad strip
With an average over five samples, the average peeling force is 97 N and the average peeling strength is 21.3 N/mm, which meets the industry requirement.
Investigating the micro-morphology on the bonding interface in the cast-rolling area requires further peeling test for Zones III and IV, and the SEM images of the peeled surface are shown in Figs. 6 and 7, respectively. As shown in Fig. 6(a), ductile fracture (red arrow) and brittle fracture (white arrow) coexist on the aluminum side of Zone III. However, for the aluminum side of Zone IV, the fracture mode was completely dimple (Fig. 7(a)). EDS analysis results indicate that the aluminum content is close to 100%, that is, the fracture is located at the aluminum substrate and the bonding strength is satisfactory.
Similar to the micro-morphology evolution rule on the aluminum side, the feature of ductile fracture is more apparent in Zone IV (Fig. 7(b)) than that in Zone III (Fig. 6(b)) on the copper side.
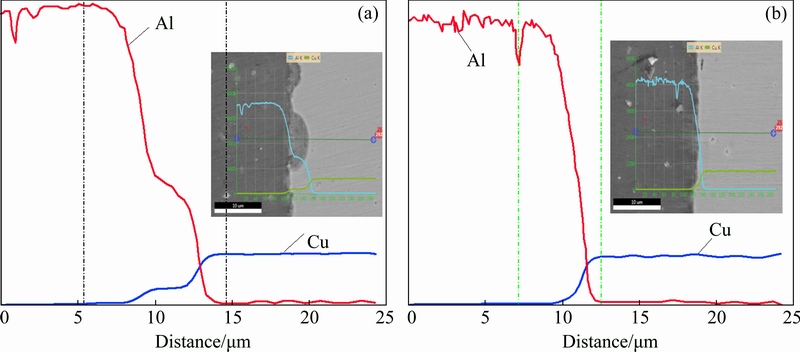
Fig. 5 Element distribution profiles of bonding interface for Zones III (a) and IV (b)
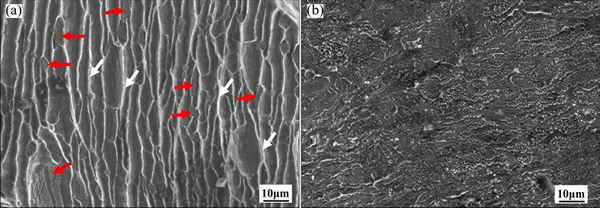
Fig. 6 SEM images of fracture surface of peeled-off strips Al (a) and Cu (b) for Zone III
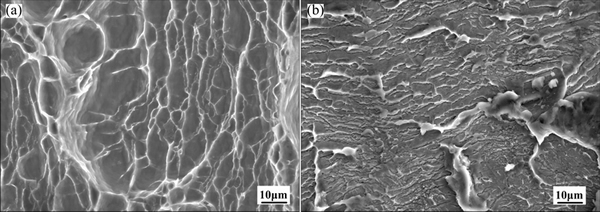
Fig. 7 SEM images of fracture surface of peeled-off strips Al (a) and Cu (b) for Zone IV
By using XRD, the composition of interfacial reaction products in Zone IV is presented in Fig. 8. A large amount of aluminum atoms are found on the peeled surface on the copper side, which further proves that the fracture is located at the aluminum substrate. Only α(Al)+CuAl2 is found on the aluminum side. In addition, Cu9Al4, CuAl2 and CuAl on the copper side are shown in descending order according to their contents. The distribution rule of reaction products is in accordance with that mentioned in Table 2. The above findings indicate that the bonding quality is gradually enhanced. Furthermore, the hot deformation in the cast-rolling area plays a leading role in bonding.
3.4 Bending test of Cu/Al clad strip
Bending tests were carried out to check the workability of Cu/Al clad strip for further processing. As shown in Fig. 9(a), Cu/Al clad strips with shinning surface and high bonding strength are prepared. However, some fracture defects exist (Fig. 9(b)) on the copper side as a result of the slip between the cast roller and thin copper strip. Figure 10 shows the bending results. No crack or separation is found on the bonding interface after 90°-180° bending. Therefore, the feasibility of SLCRB for Cu/Al clad strips and their formability are proven.
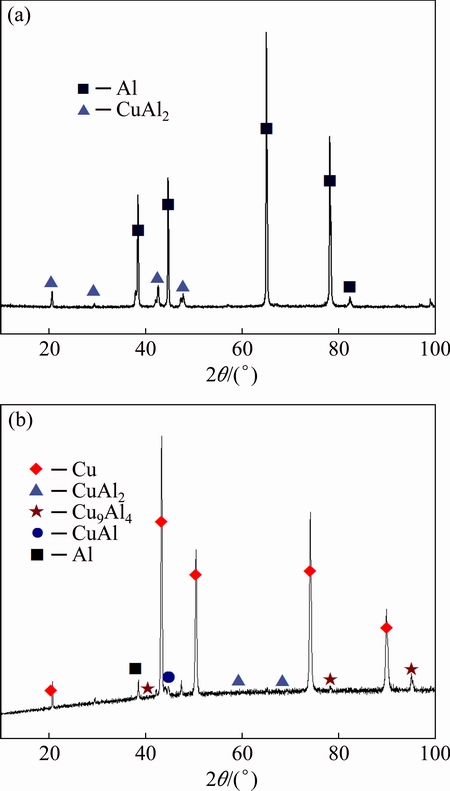
Fig. 8 XRD patterns from fracture surface of peeled-off strips Al (a) and Cu (b) for Zone IV
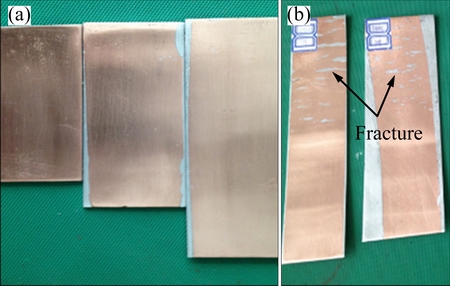
Fig. 9 Cu/Al clad strips with good quality (a) and defects (b)
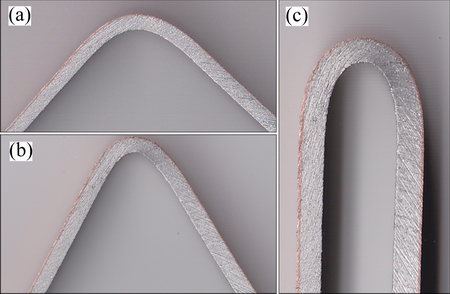
Fig. 10 Results of 90°(a), 130°(b) and 180°(c) bending
3.5 Bonding mechanism of SLCRB process
The above findings indicate that the matrix aluminum undergoes liquid, semi-solid, and solid states from the molten pool to the caster exit during the entire SLCRB process, and the Cu/Al clad strip is finally prepared. Accordingly, three different bonding mechanisms coexist at the Cu/Al bonding interface, namely, reactive diffusion at the liquid-solid interface, mechanical interlocking, and crack bonding at the solid-solid interface. The extent of interfacial reactions and composition of reaction products highly depend on the temperature and interactive force at the bonding interface. On the basis of this work and existing work [17-19], the evolution of the bonding interface and the distribution of the temperature and contact pressure in the cast-rolling area can be described in Fig. 11.
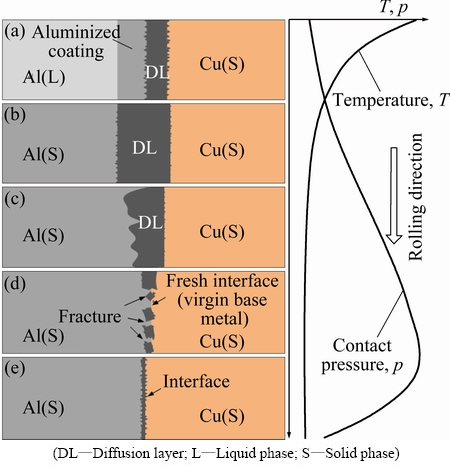
Fig. 11 Schematic diagram of evolution at bonding interface
During the first stage, molten aluminum contacts directly with the copper strip in the casting pool, and the initial aluminized coating is generated quickly on the copper strip surface (Fig. 11(a)). No deformation is applied at the bonding interface. However, according to the Cu-Al binary alloy phase diagram, reactive diffusion occurs between Cu and Al at high temperatures, and the copper-rich phase CuAl2 arises by the diffusion of aluminum atom into copper. The diffusion layer consisting of α(Al)+CuAl2, hence, forms and grows at the bonding interface.
The deformation begins to be applied at the bonding interface below the kiss point. However, this deformation is too small at the beginning of the solid-solid bonding stage, thereby creating a tendency for the diffusion layer to grow at high temperatures (Fig. 11(b)). With the increase of rolling reduction, the brittle diffusion layer is gradually crushed and even creates a discontinuity along the rolling direction under severe elongation deformation (Figs. 11(c) and (d)), thereby leading to crack bonding via extrusion of virgin base metals and high contact pressure at the fresh interface. Finally, reactive diffusion, mechanical interlocking, and crack bonding are combined to fulfill the metallurgical bonding in this stage, thereby creating a thin and uniform diffusion layer (Fig. 11(e)).
4 Conclusions
1) In accordance with different states of aluminum, reactive diffusion at Cu/Al solid-liquid interface, mechanical interlocking, and crack bonding in solid-solid interface coexist in the SLCRB process.
2) The reaction products at the bonding interface mainly consist of α(Al)+CuAl2, CuAl and Cu9Al4 from the aluminum to the copper side, successively. However, unlike the thick and brittle diffusion layer at the bonding interface of traditional solid-liquid compound casting, the diffusion layer is thin and uniform in the SLCRB process because of the short time spent at high temperature and the large rolling deformation applied at the bonding interface.
3) The average peel strength of the final Cu/Al clad strip is 97 N/mm, and the fracture occurs in the aluminum substrate. The high bonding strength and formability are proven via peeling and bending tests, respectively.
References
[1] LIU T, LIU P, WANG Q D. Research progress on copper/aluminum bimetal composite [J]. Materials Review, 2013, 27(10): 1-5.
[2] BYKOV A A. Bimetal production and applications [J]. Steel in Translation, 2011, 41(9): 778-786.
[3] ZHANG J Y, YAO J J, ZENG X Y, HAN Y Q, WU C J. Research process of copper cladding aluminum composites [J]. The Chinese Journal of Nonferrous Metals, 2014, 24(5): 275-1284. (in Chinese)
[4] KIM I K, HONG S I. Mechanochemical joining in cold roll-cladding of tri-layered Cu/Al/Cu composite and the interface cracking behavior [J]. Materials & Design, 2014, 57: 625-631.
[5] USCINOWICZ R. The effect of rolling direction on the creep process of Al-Cu bimetallic sheet [J]. Materials & Design, 2013, 49: 693-700.
[6] KIM I K, HONG S I. Effect of heat treatment on the bending behavior of tri-layered Cu/Al/Cu composite plates [J]. Materials & Design, 2013, 47: 590-598.
[7] CHEN C Y, CHEN H L, HWANG W S. Influence of interfacial structure development on the fracture mechanism and bond strength of aluminum/copper bimetal plate [J]. Materials Transactions, 2006, 47(4): 1232-1239.
[8] LI X B, ZU G Y, DING M M, MU Y L, WANG P. Interfacial microstructure and mechanical properties of Cu/Al clad sheet fabricated by asymmetrical roll bonding and annealing [J]. Materials Science and Engineering A, 2011, 529: 485-491.
[9] EIZADJOU M, MANESH H D, JANGHORBAN K. Mechanism of warm and cold roll bonding of aluminum alloy strips [J]. Materials & Design, 2009, 30: 4156-4161.
[10] SHENG L Y, YANG F, XI T F, LAI C, YE H Q. Influence of heat treatment on interface of Cu/Al bimetal composite fabricated by cold rolling [J]. Composites: Part B, 2011, 42(6): 1468-1473.
[11] HAGA T, MASAKAZU S, NAKAMURA R, YAMABAYASHI T, KUMAI S, WATARI H. Roll casting of three layers clad strip [J]. Key Engineering Materials, 2010, 443: 128-133.
[12] BAE J H, RAO A K P, KIM K H, KIM N J. Cladding of Mg alloy with Al by twin-roll casting [J]. Scripta Materialia, 2011, 64(9): 836-839.
[13] GRYDIN O, GERSTEIN G, NURNBERGER F, SCHAPER M, DANCHENKO V. Twin-roll casting of aluminum-steel clad strips [J]. Journal of Manufacturing Processes, 2013, 15(4): 501-507.
[14] HAGA T, TAKAHASHI K, WATARI H, KUMAI S. Casting of wire-inserted composite aluminum alloy strip using a twin roll caster [J]. Journal of Materials Processing Technology, 2007, 192-193: 108-113.
[15] TANAKA Y, KAJIHARA M, WATANABE Y. Growth behavior of compound layers during reactive diffusion between solid Cu and liquid Al [J]. Materials Science and Engineering A, 2007, 445-446: 355-363.
[16] WANG T M, CAO F, ZHOU P, KANG H J, CHEN Z N, FU Y A, XIAO T Q, HUANG W X, YUAN Q X. Study on diffusion behavior and microstructural evolution of Al/Cu bimetal interface by synchrotron X-ray radiography [J]. Journal of Alloys and Compounds, 2014, 616: 550-555.
[17] ZHANG H A, CHEN G. Fabrication of Cu/Al compound materials by solid-liquid bonding method and interface bonding mechanism [J]. The Chinese Journal of Nonferrous Metals, 2008, 18(3): 414-420. (in Chinese)
[18] XU B, TONG W P, LIU C Z, ZUO L, HE J C. Effects of high magnetic field on growth behavior of compound layers during reactive diffusion between solid Cu and liquid Al [J]. Journal of Materials Science & Technology, 2011, 27(9): 856-860.
[19] ZHANG J Y, ZENG X Y, HAN Y Q, YAO J J, WU C J. Formation mechanism of interface in copper cladding aluminum composites fabricated by core-filling continuous casting [J]. The Chinese Journal of Nonferrous Metals, 2014, 24(11): 2755-2761. (in Chinese).
Cu/Al复合带固-液铸轧复合界面演化
黄华贵,董伊康,燕 猛,杜凤山
燕山大学 国家冷轧板带装备及工艺工程技术研究中心,秦皇岛 066004
摘 要:利用固-液铸轧复合(简称SLCRB)技术,在d160 mm × 150 mm二辊实验铸轧机上制备Cu/Al复合带,并对其界面扩散层的反应程度、反应产物组成及显微组织演变规律进行SEM、EDS和XRD分析。结果表明,铸轧液相熔池内,液态铝液与铜带接触后在其表面形成初始渗铝层,界面成分主要为α(Al)+CuAl2,且扩散层厚度在高温下逐渐生长变厚,最厚处约为10 μm;进入低于kiss点的固相区后,扩散层在剧烈轧制延伸变形作用下破裂,界面两侧原始基材被挤出接触后形成新的复合界面,在铸轧出口处形成沿轧制方向弥散分布的CuAl2、CuAl和Cu9Al4,扩散层平均厚度由10 μm减薄至5 μm且较为均匀。剥离和折弯性能测试结果表明,所制备的Cu/Al复合带剥离断裂面出现在Al基体侧,断口呈显著韧性断裂,试件经90°~180°折弯后未出现界面撕裂现象。研究成果为高效短流程制备Cu/Al复合带提供了工艺基础。
关键词:Cu/Al 复合带;固-液铸轧复合;复合界面;反应扩散;剥离测试
(Edited by Wei-ping CHEN)
Foundation item: Project (51474189) supported by the National Natural Science Foundation of China; Project (QN2015214) supported by the Educational Commission of Hebei Province, China
Corresponding author: Hua-gui HUANG; Tel: +86-335-8077352; E-mail: hhg@ysu.eud.cn
DOI: 10.1016/S1003-6326(17)60119-5