文章编号:1004-0609(2009)04-0619-04
激光-TIG复合熔注制备WCp/Al复合材料层的微观组织
李福泉,魏连峰,李俐群,陈彦宾
(哈尔滨工业大学 现代焊接生产技术国家重点实验室,哈尔滨 150001)
摘 要:采用激光-TIG复合熔注工艺,在铝合金表面制备WCp/Al表面复合材料层。通过优化激光功率、TIG电流、扫描速度和送粉率等工艺参数,可以获得0.5~4.3 mm厚的表面复合材料层。采用XRD、SEM、EDS等手段对表面颗粒强化层的微观组织和成分进行研究。结果表明:熔注层基体的微观组织为过共晶组织;熔注层不同位置的过共晶相具有不同的形貌,熔池上部主要为含有十字花状、鱼骨状、蝶状先共晶相(W1-xAlx)Cy的过共晶组织,而底部的先共晶相呈现块状形态。
关键词:颗粒增强复合材料;铝合金;WC;激光-TIG复合;显微组织
中图分类号:TG174.4 文献标识码: A
Microstructures of WCp/Al metal matrix composites layer produced by hybrid laser-TIG melt injection
LI Fu-quan, WEI Lian-feng, LI Li-qun, CHEN Yan-bin
(State Key Laboratory of Advanced Welding Production Technology, Harbin Institute of Technology, Harbin 150001, China)
Abstract: In order to overcome the difficulties of laser melt injection (LMI) on aluminum alloys, which include high reflection of laser on aluminum, oxide film and high heat conductivity of aluminum alloy, the hybrid laser-TIG melt injection (HLTMI) was developed. WCp/Al composite layer was prepared on the surface of aluminum. Through optimization of process parameters of HLTMI, such as laser power, TIG current, scanning velocity and powder feeding rate, the MMC layers with different thicknesses ranging from 0.5 mm to 4.3 mm can be achieved. The microstructure and composition of the coatings were analyzed by means of XRD, SEM and EDS. The results show that the microstructures of MMCs layer presents a hypereutectic structure. The hypereutectic phases at different locations exhibit different shapes: the hypereutectic phase (W1-xAlx)Cy at the upside of the layer represents cross shape, fishbone-like or papilionaceous, while the preeutectic phase at the bottom of the layer exhibits massive structure.
Key words: particulate metal matrix composite; aluminum alloy; WC; hybrid laser-TIG; microstructure
铝合金具有密度小、热膨胀系数低、比刚度高、比强度高和易成型加工等优异性能。但铝合金耐磨性差极易产生塑性变形,限制了铝合金的应用。颗粒增强金属基复合材料(MMC) 可以将硬质颗粒的高强度、高硬度、高熔点和金属基体的良好韧性结合起来,近年来发展迅猛并逐渐成为材料改性领域中的研究热点,尤其在耐磨环境下具有良好的应用前景[1-4]。增强颗粒的存在形式是非连续,因之被称为颗粒增强复合材料(PMMC)。很早就有许多相关方面的研究和著作,其中大多都是在铝基体上进行实验的,结果显示PMMC与常规材料相比都有着显著优势[5-7]。但是,昂贵的成本限制了它的进一步应用和推广;但是机械零件失效一般都发生在工作面(表面),因此,表面复合材料层显示了巨大的优势[8]。
激光熔注技术(Laser melt injection)制备颗粒增强表面复合材料层是近年来研究的热点,国内外已经有了很多相关的文献和报道[9-12]。但基体材料大多为钢铁或钛合金,对铝合金的研究较少且不够深入和系统。铝合金表面有致密的氧化膜,另外,它对激光反射较高且热导率很高,利用激光熔注在其表面制备复合材料层有较大的困难。VREELING等[13] 采用YAG激光功率2 kW,预热300 ℃以上时才能实现SiC对Al 的表面熔注。当温度低于300 ℃时,颗粒无法进入熔池。进一步研究发现,这与铝对激光反射率高、表面存在氧化膜且导热率高有关。预热温度较低时,氧化膜阻止颗粒进入熔池;温度较高时,氧化膜破裂,粉末成功进入熔池。本文作者针对铝合金激光熔注所存在的问题,借鉴焊接过程中的激光-TIG复合焊接技 术[14-16],开发了激光-TIG复合熔注的新工艺,并对熔注层微观组织做进一步研究。
1 实验
试验采用2219铝合金,试样尺寸为120 mm×50 mm×5 mm。其主要成分见表1,热处理状态为T87;金相组织如图1所示。2219铝合金中的基体相为α(Al) ,根据资料可以判断[17],图1中褐色相(图中A所示)为α(Al)和CuAl2 的二元共晶,黑色大块的(图中B所示)为(FeMn)Al6。而颜色较浅(图中C所示)的相为CuAl2 相。
表1 2219铝合金的化学成分
Table 1 Chemical compositions of aluminum alloy 2219 (mass fraction,%)

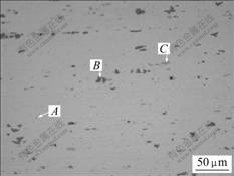
图1 2219铝合金母材金相组织
Fig.1 Metallograph of aluminum alloy 2219 substrate
熔注前对试样表面进行打磨,然后用丙酮清洗试样,去除油污,最后再对试样进行化学清洗以去除氧化膜,具体步骤为:在40~60 ℃的6%~10%氢氧化钠水溶液碱洗7 min;然后清水冲洗;接着放入30%硝酸中3 min进行中和光化;最后取出后清水冲洗,干燥风干。
试验采用的铸造WC 陶瓷颗粒为立方晶系硬质颗粒,是制造硬质合金的主要材料,具有很高的显微硬度,常用于制备耐磨涂层。注入粉末的粒度为0.075~0.150 mm,粉末的SEM像如图2所示,其组成包括WC相和W2C相。
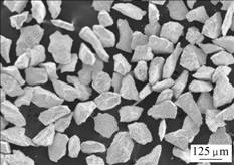
图2 WC 粉末的SEM 像
Fig.2 SEM image of WC powders
本实验是在3 kW轴流射频激励扩散冷却CO2激光器下进行的,配用CNC系统工作台。采用PEL-1A送粉器进行同步送粉,焊机所用型号为WX-300TIG。所采用的实验系统如图3所示,可将WC颗粒注入到铝合金表面所形成的熔池中。采用以下工艺参数,可在铝合金表面获得良好的颗粒增强的复合材料层:激光功率(P)1.0~1.5 kW,TIG电流(I)40~100 A,扫描速
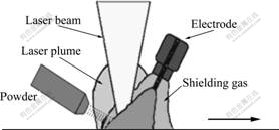
图3 实验系统示意图
Fig.3 Schematic diagram of experimental system
度(v)0.2~0.4 m/min,载气流量(L1)600~800 L/h,TIG保护气流量(L2)240~450 L/h,送粉角(α)30?~50?,TIG倾角(β)60?~80?,送粉率(M)120~150 mg/s。激光采用负离焦的方式以保证光斑直径在3~4 mm左右。通过对参数的合理调节,可在铝合金表面制备厚度为0.5~4.3 mm的复合材料层,颗粒注入深度可根据需要通过工艺参数匹配来控制。
对所获得的激光熔注层,采用JSM-5600LV型扫描电镜(SEM)进行显微组织观察与分析,用Link ISIS300型能谱仪器(EDX)检测熔注层元素分布,用D/max-2500型X射线衍射仪(XRD)分析熔注层的相组成。
2 结果与分析
对于激光-TIG复合熔注的新工艺,之所以不需要预热即可在铝合金表面获得良好的熔注效果,取决于交流TIG电源作用。一方面,在TIG电弧热源辅助激光热源进行加热形成熔池,铝合金液态熔池对激光的反射率低于固态金属,由于电弧的作用,激光束能够直接辐射到液态熔池表面,增大吸收率,增加铝合金熔池存在的时间。另一方面,由于电弧的“阴极雾化”作用,采用交流TIG电弧的负半周可有效清理铝合金表面氧化膜。而TIG电弧的正半周的存在,则避免了电弧的钨极被过度加热引起烧损。这种激光-TIG复合熔注特殊的工艺特点,必然对其所形成的熔注层的组织性能产生明显的影响。
2.1 熔注层的宏观形貌
熔注层厚度与宽度随着热输入的增加而增大,单独对TIG电流和激光功率考察时发现不同的规律,图4(a)所示为P=1.1 kW、M=125 mg/s、v=0.2 m/min时得到的熔注层厚度随TIG电流变化关系,图4(b)所示为I=50 A、M=135 mg/s、v=0.3 m/min时熔注层厚度随激光功率的变化关系。从图4(b)中可以看出,熔注层厚度随电流的增加是单调增加的;但随着激光功率的增加熔注层的厚度先是逐渐递增而后又有所下降,在2 kW处出现转折。出现这种现象的主要原因在于铝合金含有较多的合金元素,熔注过程中会产生很大的等离子体,而激光功率对等离子体的影响要强于TIG电流的作用,特别是正离焦的时候,激光的焦点在工件上方,很容易把上方气体“点燃”,形成很高的等离子体;等离子体罩在熔池上方,对颗粒注入熔池产生十分不利的影响。因此,实验中采用负离焦方式,并将激光控制在1~2 kW范围之内。
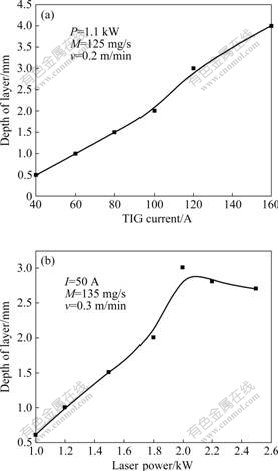
图4 TIG电流、激光功率对熔注层厚度的影响
Fig.4 Influences of TIG current (a) and laser power (b) on thickness of HLTMI layer
本实验通过调节工艺参数在铝合金表面获得了良好的复合材料层,并且通过工艺参数的调节,控制热输入与送粉率以及扫描速度之间的匹配,得到不同厚度(0.5~4.3 mm)的复合材料层。用软件Image-pro plus对熔注层颗粒体积分数进行了分析。在电弧电流为70~90 A、激光功率为1.2~1.5 kW、送粉率为130~140 mg/s、扫描速度为0.3~0.4 m/min时所获得的熔注层的颗粒体积分数为0.3~0.45。
图5所示为不同工艺参数下获得的复合材料层。尽管WC的密度比铝液的要大,WC颗粒在熔注过程中有下沉的趋势,但激光熔池中温度梯度和溶质梯度所引起的Marangoni流会促进WC颗粒位置重排,抑制其于熔池底部聚集。两者的共同作用对WC在激光熔池中的分布产生影响。图6所示为熔注层水平截面颗粒分布的SEM像,所采用的工艺参数为:TIG电流80 A,激光功率1.5 kW,送粉率145 mg/s,扫描速度0.35 m/min。由图6可以看到,水平截面颗粒分布较为均匀。
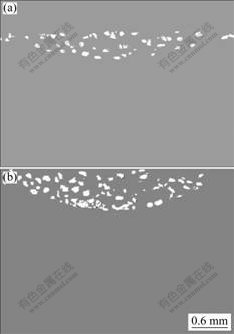
图5 不同工艺参数下获得的熔注层SEM形貌
Fig.5 SEM morphologies of HLTMI layer prepared at different parameters: (a) I=40 A, P=1 kW, M=120 mg/s, v=0.2 m/min; (b) I=70 A, P=1.2 kW, M=135 mg/s, v=0.3 m/min
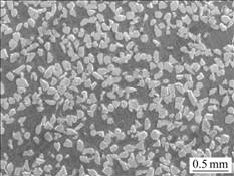
图6 熔注层水平截面的SEM形貌
Fig.6 SEM morphology of horizontal cross-section of HLTMI layer
2.2 注入颗粒的微观形貌
图7(a)~(c)所示分别为熔注层不同位置颗粒形貌的SEM像。所采用的工艺参数为TIG电流80 A,激光功率1.5 kW,送粉率145 mg/s,扫描速度0.2 m/min。可以明显看到位于熔注层下部的WC 颗粒熔化较多,颗粒的形状已经变得圆滑;而熔池上部颗粒WC 颗粒表面熔化较少,大多保留原来的棱角状。

图7 熔注层不同位置的颗粒SEM像
Fig.7 SEM morphologies of particles at different locations of HLTMI layer: (a) Upper location of HLTMI layer; (b) Middle location of HLTMI layer; (c) Bottom location of HLTMI layer
由于熔池的温度比WC的熔点(2 860 ℃)低很多,因此,WC 颗粒表层熔化甚至完全熔化主要是受到激光束的辐照,颗粒进入熔池后基本不再继续熔化。而位于熔注层上部的WC 颗粒,由喷嘴喷出到进入熔池前的飞行过程中,大部分粒子已不经受光束辐照,至少已经不再受到光束中心的辐照加热,主要是从熔池后部进入熔池,因而颗粒表面熔化较少,仍能保留原来的棱角状。而位于熔注层下部的颗粒自喷嘴送出后,进入熔池前的飞行过程中,经受电弧和光束的辐照,激光束的中心温度可以达到3 000 ℃以上甚至更高,WC 表层发生较多的熔化,在固态WC 周围形成液态WC 薄层。
2.3 WC颗粒间基体组织
熔注过程中,WC 颗粒会被复合热源加热到较高的温度,进入熔池后,高温下W原子和C原子将不断向基体溶解和扩散,与Al等元素发生反应,反应产物将在很大程度上影响熔注层的组织结构。图8所示为 熔注层的基体组织SEM像。由于复合热源作用下,熔池温度场处于一种十分复杂的状态,因此,熔池凝固后熔注层中各区域的组织形貌差别也很大。由于TIG电弧能量作用空间较宽,复合热源对颗粒的加热作用明显强于单激光熔注工艺,所以,复合熔注过程中颗粒的熔化相对严重;另外,采用TIG/激光复合的方法进行熔注时,颗粒在复杂的温度场和流场中下沉,将会受到熔池中液态金属表面张力、颗粒与液铝相对运动所产生的相互作用力等的作用。当颗粒在复合热源作用下急剧熔化进入熔池后,会在熔池上部遗留了大量的液态WC,并在熔池中与合金元素发生了复杂的反应。高温下W原子和C原子不断向基体溶解和扩散,熔池成分很不均匀,熔池中存在许多W 原子富集区,在较高的温度下,W、C和Al的生成相从液相中析出。这种碳化物相成分复杂,结晶时的长大方式不同于WC、W2C那样结晶为块状先共晶相,而是随着温度的下降和元素的不断扩散,在液相中逐渐长大为蝶状、鱼骨状、十字花状的过共晶树枝晶。图9所示为对应的复合熔注层的XRD谱,可以看出熔注层主要由α(Al)、W2C、WC和(W1-xAlx)Cy等相组成,其中α(Al)、W2C和WC为主要的相。借助能谱分析(EDS)和X射线衍射分析(XRD)对熔注层的先共晶相进行研究,先共晶相(W1-xAlx)Cy的成分较为复杂,选取多个蝶状、鱼骨状、十字花状的相进行EDS分析,发现成分变化很大。以图8(a)中A和B两点为例,其中A点的能谱分析结果为60.2 W、35.2C和4.6Al(摩尔分数,%),形状相似的B点的能谱分析结果为50.4 W、26.7C和22.9Al。经分析发现其偏差远大于能谱分析的误差范围。对W、Al二元相图进一步分析发现,W和Al可以形成许多不同成分的相W1-xAlx(x=0.10, 0.25, 0.50)。因此,(W1-xAlx)Cy的产生原因可以解释如下:在高温下,W原子和C原子不断向基体溶解和扩散,W与Al先行反应析出W1-xAlx,熔池内部W原子和C原子的分布很不均匀,进而形成不同的W、Al二元相,对应着不同 x 的值;这些相在结晶长大过程中,不断与C元素反应生成(W1-xAlx)Cy。这与文献[18]所述情况类似,W、C和Al三元化合物的衍射峰的位置也对应得很好,表明该相就是W、C和Al所生成的复杂碳化物(W1-xAlx)Cy。在较低的温度下,基体枝晶与枝晶间细小的条状共晶化合物连生结晶为共晶组织。因此熔注层上部组织形貌为(W1-xAlx)Cy先共晶相+共晶组织(α(Al)与Al2Cu的共晶),如图8(a)所示。
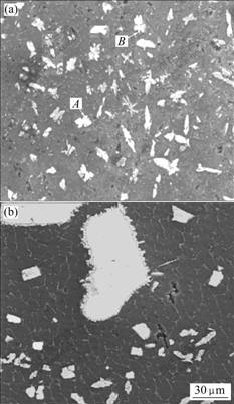
图8 复合熔注层中基体组织的SEM像
Fig.8 SEM images of substrate at different locations of HLTMI layer: (a) Upper side of layer; (b) Bottom side of layer
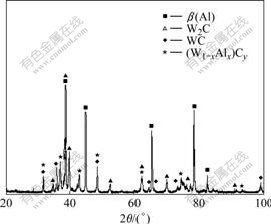
图9 复合熔注层XRD谱
Fig.9 XRD pattern of HLTMI layer
图8(b)所示为熔池底部基体组织形貌的SEM像。熔池底部由于受基体的激冷作用,因此,与熔池中上部相比,温度比较低,W原子和C原子来不及充分溶解和扩散,也没有时间与其它元素的充分反应。在熔池底部,钨的碳化物以自己的长大方式先行结晶长大,因此,在熔池底部也可以看到典型的过共晶组织形貌:块状先共晶相(钨碳化合物)+α(Al)与Al2Cu共晶。
3 结论
1) 采用激光-TIG复合熔注工艺在铝合金表面制备了颗粒增强复合材料层。通过优化激光功率、TIG电流、扫描速度和送粉率等工艺参数,获得了0.5~4.3 mm厚的表面复合材料层。
2) 由于受到复合热源辐照加热的影响,熔注层中颗粒从上部到下部颗粒表面被熔化的程度依次增加,随着深度的增加颗粒边缘逐渐趋于圆滑。熔注层的主要相组成为α(Al)、W2C、WC和(W1-xAlx)Cy。
3) 熔注层复杂的成分和冷却过程造就了复杂的组织形貌:熔池上部主要为含有十字花状、鱼骨状、蝶状先共晶相(W1-xAlx)Cy的过共晶组织,而底部的先共晶相则呈现块状形态。
REFERENCES
[1] 赵敏海, 刘爱国, 郭面焕. WC颗粒增强耐磨材料的研究现状[J]. 焊接, 2006, 11: 26-30.
ZHAO Min-hai, LIU Ai-guo, GUO Mian-huan. Research on WC reinforced metal matrix composite[J]. Welding & Joining, 2006, 11: 26-30.
[2] 许 斌, 项 东. 碳化钨颗粒增强表面复合材料的研究进展[J]. 铸造技术, 2002, 23(6): 362-364.
XU Bin, XIANG Dong. Survey of surface composites strengthened casting by WC articles[J]. Foundry Technology, 2002, 23(6): 362-364.
[3] 湛永钟, 张国定, 蔡宏伟. 颗粒增强金属基复合材料的干摩擦性能与磨损机理[J]. 材料科学与工程学报, 2003, 21(5): 748-752.
ZHAN Yong-zhong, ZHANG Guo-ding, CAI Hong-wei. Tribological properties and wear mechanisms of particulate reinforced metal matrix composites[J]. Journal of Materials Science & Engineering, 2003, 21(5): 748-752.
[4] BERTRAND Y P, SMUROV I. Laser cladding of wear resistant metal matrix composite coatings[J]. Thin Solid Films, 2004, 453/454: 133-138.
[5] MCDANELS D L. Analysis of stress–strain, fracture, and ductility behavior of aluminum matrix composites containing discontinuous silicon carbide reinforcement[J]. Met Trans, 1985, 16(6): 1105–1115.
[6] IBRAHIM A, MOHAMED F A, LAVERNIA E J. Particulate reinforced metal matrix composites—A review[J]. J Mater Sci 1991, 26(5): 1137-1156.
[7] LLOYD D J. Particle reinforced aluminum and magnesium matrix composites[J]. Intern Mater Rev, 1994, 39(1): 1-23.
[8] MIRACLE D B. Metal matrix composites–From science to technological significance[J]. Composites Science and Technology, 2005, 65(15/16): 2526-2540.
[9] PEI Y T, OCELIK V, De HOSSON J T M. SiCp/Ti6Al4V functionally graded materials produced by laser melt injection[J]. Acta Materialia, 2002, 50(8): 2035-2051.
[10] VREELING J A, OCELIK V, DE HOSSON J T M. Ti-6Al-4V strengthened by laser melt injection of WCp particles[J]. Acta Materialia, 2002, 50(19): 4913-4924.
[11] PEI Y T, OCELIK V, DE HOSSON J T M. Interfacial adhesion of laser clad functionally graded materials[J]. Mater Sci Eng A, 2003, 342(1/2): 192-200.
[12] LIU D J, LI L Q, LI F Q, CHEN Y C. WCp/Fe metal matrix composites produced by laser melt injection[J]. Surface & Coatings Technology, 2008, 202(9): 1771-1777.
[13] VREELING J A, OCELIK V, PEI Y T. Laser melt injection in aluminum alloys: On the role of the oxide skin[J]. Acta Mater, 2000, 48(17): 4225-4233.
[14] STEEN W M. Arc augmented laser processing of materials[J]. J Appl Phys, 1980, 51(11): 5636-5641.
[15] DILTHEY U, LUEDER F, WIESCHEMANN A. Technical and economical advantages by synergies in laser arc hybrid welding [J]. Welding in the World, 1999, 43(4): 141-152.
[16] DIEBOLD P, ALBRIGHT C E. Laser-GTA welding of aluminum alloy 5052[J]. Welding Journal, 1984, 63(6): 18-24.
[17] 孟庆国, 方洪渊, 徐文立, 姬书得. 2219铝合金双丝焊热影响区组织及力学性能[J]. 焊接学报, 2006, 27(3): 9-12.
MENG Qing-guo, FANG Hong-yuan, XU Wen-li, JI Shu-de. Microstructure and mechanical properties of 2219 Al-alloy heat-affected zone with twin wire welding[J]. Transactions of the China Welding Institution, 2006, 27(3): 9-12
[18] YAN J M, MA X F, ZHAO W, TANG H G, ZHU C J. Synthesis crystal structure and density of (W1-xAlx)C[J]. Journal of Solid State Chemistry, 2004, 177(7): 2265–2270.
收稿日期:2008-06-17;修订日期:2008-11-27
通讯作者:李福泉,讲师,博士;电话:0451-86415506;传真:0451-86415374;E-mail: lifuquan@hit.edu.cn
(编辑 何学锋)