
Effect of particle size and agglomeration of TiO2 on synthesis and electrochemical properties of Li4Ti5O12
WU Le(伍乐), KAN Su-rong(阚素荣)?, LU Shi-gang(卢世刚),
ZHANG Xiang-jun(张向军), JIN Wei-hua(金维华)
General Research Institute for Nonferrous Metals, Beijing 100088, China
Received 15 July 2007; accepted 10 September 2007
Abstract: The effects of the initial condition of synthesis on electrochemical properties of Li4Ti5O12 were studied with the comparison among starting and final materials by SEM, XRD and electrochemical analysis methods. The influence of the solvents for mixing the starting material on the products was investigated. The results show that nano-sized Li4Ti5O12 powder obtained by nano-sized TiO2 with ethanolamine as solvent shows more excellent electrochemical performance. More than 95%, 91%, 85% and 71% of the nominal capacity is achieved respectively at 0.5C, 1C, 2C and 4C rate without excellent capacity fading after more than 30 cycles.
Key words: lithium titanate; Li4Ti5O12, nano-TiO2; solid-state synthesis
1 Introduction
The spinel lithium titanate has been extensively studied as a promising anode candidate presently[1-6]. Those researches show that Li4Ti5O12 can accommodate Li-ions during the charging without a noticeable change in the lattice parameter and does not react with electrolyte for its high potential plateau at around 1.55V versus Li/Li+. Consequently it offers excellent safe and cycle performance compared with carbonaceous materials used as anode active materials in commercial Li-ion batteries[7-8]. Moreover, the Li-ion diffusion coefficients, which is about 10 times higher than graphite, makes it more suitable as an negative electrode for high-power battery and electrochemical capacitors. However, the main drawback of Li4Ti5O12 is the poor electronic conductance[9-10], which reduces the high-rate ability of the electrode and accordingly limits its applications in some fields. Many researches indicated that fine particle-sized spinel Li4Ti5O12 exhibits more excellent rate ability with the higher number of lithium insertion sites and shorter length of Li-ion diffusion and electron transfer[11-13]. Consequently, there have been many studies focused on the synthesis of nano-sized Li4Ti5O12[14-16].
As most of the compounds of Li sources such as lithium hydroxide (LiOH?H2O) or lithium carbonate (Li2CO3) are discomposed or melted easily at a lower temperature while the titanate dioxide (TiO2) reacts in solid phase during the solid-state synthesis process of Li4Ti5O12. It is supposed that the particle size distribution of Li4Ti5O12 powder may mainly depend on the grain size of TiO2. In this study, the effect of the particle size of starting materials on the final material was discussed by the comparison of the raw material and products. The high-polar solvent ethanolamine was first used to disperse the nano-sized TiO2 during synthesis progress of Li4Ti5O12 compared with ethanol solvent.
2 Experimental
The Li4Ti5O12 powder was prepared by three methods. Method A[14]: stoichiometic amounts of Li2CO3 (1-5 μm, Xinjiang Research Institute of Non-ferrous Metals), micro-sized anatase TiO2(0.5-1.0 μm, Beijing Yili Fine Chemical Co.,Ltd.) and 10%(mass fraction) acetylene carbon black was mixed and milled for 30 h in agate jar at room temperature with ethanol as solvent. 8%(mass fraction) excess Li2CO3 was added to compensate for lithia volatilization during the high temperature heating. Method B is the same as method A but with nano-sized anatase TiO2 (20-25 nm, Hangzhou Wanjing New Material Co., Ltd.) instead of the micro-sized TiO2. Method C is the same as method B but with the ethanolamine instead of ethanol as solvent. The achieved slurries A and B were dried at 70 ℃ and the slurry C was dried at 180 ℃ to remove the solvent respectively. The resulting grey mixtures were preheated in a muffle furnace at 400 ℃ for 5 h in air and then sintered at 700 ℃ for 10 h, then cooled down to room temperature naturally to obtain the final powder. The above three products were named LTO-A, LTO-B and LTO-C corresponding to the method A, B and C, respectively.
The working electrode was prepared from a paste mixture of 83% Li4Ti5O12, 8% polyvinyldifluorin (PVDF) binder, and 9% carbon black with N-N Dimethyl Foramide(DMP) as solvent. The paste was coated on copper foils and then dried under vacuum at 100 ℃ to make a working electrode. The cell was assembled in drying chamber, which consisted of the working electrode, a metal Li electrode, porous separator (celgard 2400) and 1.0 mol/L LiPF6 ethylene carbonate (EC)/diethyl carbonate (DEC)(1?1) electrolyte. The initial open circuit voltage was about 3.1 V. The crystalline phase of the obtained Li4Ti5O12 powder was identified by powder X-ray diffraction(XRD) using PANalytical X'Pert PRO MPD diffraction system (Cu Kα, 40 kV, 40 mA).
The particle morphology and average particle size of the starting material and final products were observed by scanning electron microscope (SEM) using the Hitachi S-4800 FE-SEM.
The electrochemical performance of the half-cells was evaluated using a battery test system LAND CT2001A model (Wuhan Jinnuo Electronics Co., Ltd.). The charge and discharging voltage range is from 1.0 to 2.5 V.
3 Results and discussion
3.1 SEM analysis
The SEM images of Li2CO3 powder, Li4Ti5O12 powder and the gray mixture of Li2CO3, TiO2 and acetylene carbon black prepared by method C are shown in Fig.1. The particle size of Li2CO3 is 1-5 μm. While the Li4Ti5O12 powder size shown in Fig.1 is far smaller.
Fig.1 SEM images of Li2CO3(a); mixture of Li2CO3, TiO2 and acetylene carbon black prepared by method C(b); LTO-A(c); LTO-B(d); LTO-C(e)
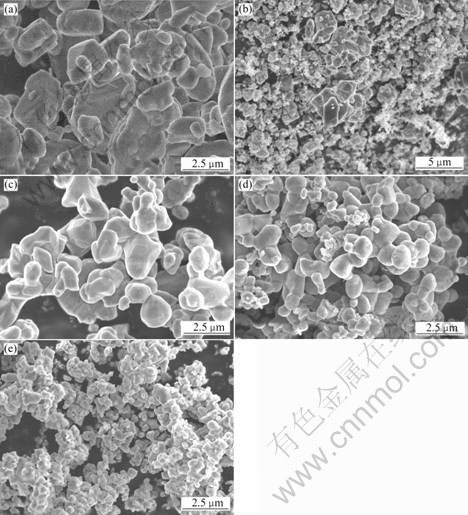
So it is supposed that there is no necessary relationship between them. Further more, the particle size of LTO-B(Fig.1(d)) and LTO-C(Fig.1(e)) synthesized by nano-sized TiO2 are less than LTO-A(Fig.1(a)) prepared by micro-sized TiO2. The results indicate that the particle size of Li4Ti5O12 is not dependent on the particle size distribution of Li sources but on that of Ti sources. The influence of the dispersion of TiO2 on the particle size of the final particles is also found. The nano-sized Li4Ti5O12 is achieved by using ethanolamine as solvent, as seen in Fig.1(e). That is because the ethanolamine as a high-polar solvent is more efficient to disperse the nano-sized TiO2 than ethanol and thus it can reduce the reunion of TiO2 and generate a more homogeneous precursor, and consequently reduce the particle size of the products. It appears that the particle size distribution of Li4Ti5O12 changes with that of TiO2.
3.2 XRD analysis
The XRD patterns of the Li-Ti-O phases shown in Fig.2 correlate well with that reported in the Refs.[17-19]. Single spinel phase Li4Ti5O12 is achieved with both methods B and C. While a weak diffraction peak appears at 2θ=27.4? in LTO-A , which indicate that the product prepared by method A contains a little amount of rutile phase TiO2. During the react process, as shown in Fig.3, the TiO2 powder, on one hand reacts with the near Li2CO3, on the other hand, transfers to the rutile phase and forms the impurity when they are not able to contact with Li2CO3. In our later studies, the peaks of rutile phase TiO2 disappear when the heating temperature is greater than 723 ℃ for the good contact of the reactants provided by the Li2CO3 salt fusion. But the particle size of the products also increases with the increasing temperature, which is in agreement with previous literatures[20]. While at the same heating temperature in methods B and C, no impurities were found in the products, which indicates that the nano-sized TiO2 and well mixed condition ensure good contact and complete reaction of the starting materials.
3.3 Electrochemical analysis
Fig.4 shows the charge-discharge curves of Li4Ti5O12 samples prepared by methods A, B and C with voltage range of 2.5-1.0 V. The samples exhibit discharge capacities of 148.1, 163.7 and 161.8 mA?h/g respectively at 0.1C rate, and the initial efficiencies of charge-discharge are all above 97%. The voltage plates of all samples are about 1.55 V (vs Li+/Li) with unapparent polarization, which is in agreement with literature values. The constant electrical potential is derived from the two-phase reversible reaction between Li4Ti5O12 and Li7Ti5O12 during the charge/discharge progress according to the following reaction[21]:
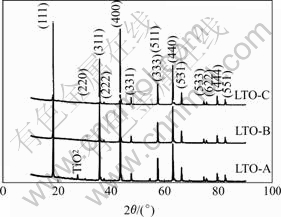
Fig.2 XRD patterns of Li4Ti5O12 prepared by methods A, B and C
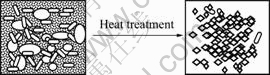
Fig.3 Schematic presentation of presence of impurity (
presents TiO2;
presents Li2CO3;
presents Li4Ti5O12; and black dots present acetylene carbon black)



The charge (de-intercalation) capacities of the half cells at different rate range from 0.1 to 4C are shown in Fig.5. As shown in Fig.5, sample LTO-A shows only 148.1 mA?h/g capacity, and only 70 mA?h/g is obtained at 4C for sample LTO-A corresponding to the existing impurity and large size. However, 161.3 mA?h/g and 163.8 mA?h/g are obtained for sample LTO-B and LTO-C respectively and there is no distinguished difference of the capacities at the low charge-discharge current between them. Furthermore, with the charge- discharge rate increasing, the difference between sample LTO-B and LTO-C become notable. More than 20 mA?h/g capacities are obtained for sample LTO-C than LTO-B though they have the similar XRD patterns. The reason should be the particle size distribution of Li4Ti5O12. Fine particle sized Li4Ti5O12 are more favorable to fast Li insertion/extraction. Sample LTO-C prepared by the nano-sized TiO2 as Ti source and with ethanolamine as solvent for mixing, shows about 71% capacity of the 0.1C capacity at 4C. There is almost no capacity fading after 30 cycles at different current. About 95%, 91%, 85% of the initial capacity are achieved at 0.5C, 1C and 2C respectively.
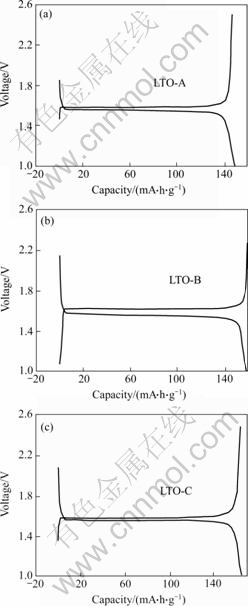
Fig.4 First charge and discharge curves of Li4Ti5O12/Li half cells at 0.1C rate
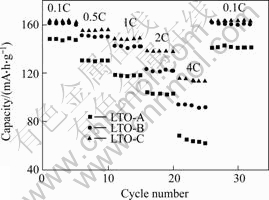
Fig.5 Charge (extraction) capacities in different rate as function of cycle number for cells shown in Fig.4
4 Conclusions
1) The particle size distribution of Li4Ti5O12 is more dependent on that of Ti sources than on that of Li sources.
2) Ethanolamine is more effective to reduce the agglomeration of nano-sized TiO2 than ethanol and subsequently the nano-sized Li4Ti5O12 is generated.
3.3) Nano-sized Li4Ti5O12 shows more excellent electrochemical performance than micro-sized ones, especially at high charge-discharge rate.
References
[1] LU W, BELHAROUA J, LIU K A. Electrochemical and thermal investigation of Li4/3Ti5/3O4 spinel[J]. J Electrochem Soc, 2007, 154(2): 114-118.
[2] RHO Y H, KANAMURA K. Preparation of Li4/3Ti5/5O4 Thin Film Electrodes by a PVP sol-gel coating method and their electrochemical properties[J]. J Electrochem Soc, 2004, 151(1): 106-110.
[3] CHRISTENSEN J, SRINIVASAN V, NEWMAN J. Optimization of lithium titanate electrodes for high-power cells[J]. J Electrochem Soc, 2006, 153(3): 560-565.
[4] TORU T, HIDEO Y, MASANORI Y. Mechanism of Li-doping into Li4Ti5O12 negative active material for Li-ion cells by new chemical method[J]. Journal of Power Sources, 2006, 162(2): 813-817.
[5] PROSINI P P, MANCINI R, PETRUCCI L, CONTINI V, BILLANO P. Li4Ti5O12 as anode in all-solid-state, plastic, lithium-ion batteries for low-power applications[J]. Solid State Ionics, 2001, 144(1/2): 185-192.
[6] DU P A, LAFORGUE A, SIMON P. Li4Ti5O12/poly(methyl) thiophene asymmetric hybrid electrochemical device[J]. Journal of Power Sources, 2004, 125(1): 95-102.
[7] JIANG J W, CHEN J, DAHN J R. Comparison of the reactions between Li7/3Ti5/3O4 or LiC6 and nonaqueous solvents or electrolytes using accelerating rate calorimetry[J]. J Electrochem Soc, 2004, 151(12): 2082-2087.
[8] YAO X L, XIE S, CHEN C H, WANG Q S, SUN J H, LI Y L, LU S X. Comparisons of graphite and spinel Li1.33Ti1.67O4 as anode materials for rechargeable lithium-ion batteries[J]. Electrochimica Acta, 2005, 50(20): 4076-4081.
[9] GUERFI A, CHAREST P, KINISHITA K, PERRIER M, ZAGHIB K. Nano electronically conductive titanium-spinel as lithium ion storage negative electrode[J]. Journal of Power Sources, 2004, 126(1/2): 163-168.
[10] CHEN C H, VAUGHEY J T, JANSEN A N, DEES D W, KAHAIAN A J, GOACHER K T, THACKERAY M M. Studies of Mg-substituted Li4-xMgxTi5O12 spinel electrodes (0x1) for lithium batteries[J]. J Electrochem Soc, 2001, 148(1): 102-104.
[11] WOLFENSTINE J, LEE U, ALLEN J L. Electrical conductivity and rate-capability of Li4Ti5O12 as a function of heat-treatment atmosphere[J]. Journal of Power Sources, 2006, 154(1): 287-289.
[12] KAVAN L, BRATZEL M. Facile synthesis of nanocrystalline Li4Ti5O12 (spinel) exhibiting fast Li insertion[J]. Electrochemical and Solid-State Letters, 2002, 5(2): 39-42.
[13] ALLEN J L, JOW T R, WOLFENSTINE J. Low temperature performance of nanophase Li4Ti5O12[J]. Journal of Power Sources, 2006, 159(2): 1340-1345.
[14] GUERFI A, SEVIGNY S, LAGACE M, HOVINGTON P. Nano-particle Li4Ti5O12 spinel as electrode for electrochemical generators[J]. Journal of Power Sources, 2003, 119/121: 88-94.
[15] KIM D H, AHN Y S, KIM J. Polyol-mediated synthesis of Li4Ti5O12 nanoparticle and its electrochemical properties[J]. Electrochemistry Communications, 2005, 7(12): 1340-1344.
[16] VENKATESWARLU M, CHEN C H, DO J S, LIN C W, CHOU T C, HWANG B J . Electrochemical properties of nano-sized Li4Ti5O12 powders synthesized by a sol-gel process and characterized by X-ray absorption spectroscopy[J]. Journal of Power Sources, 2005, 146(1/2): 204-208.
[17] OHZUKU T, UEDA A, YAMAMOTO N, IWAKOSHI Y. Factor affecting the capacity retention of lithium-ion cells[J]. Journal of Power Sources, 1995, 54(1): 99-102.
[18] ZAGHIB K, SIMONEAU M, ARMAND M, et al. Electrochemical study of Li4Ti5O12 as negative electrode for Li-ion polymer rechargeable batteries[J]. Journal of Power Sources, 1999, 81/82: 300-305.
[19] WANG G X, BRADHURST D H, DOU S X, et al. Spinel Li[Li1/3Ti5/3]O4 as an anode material for lithium ion batteries[J]. Journal of Power Sources, 1999, 83(1/2): 156-161.
[20] HAO Y J, LAI Q Y, XU Z H, LIU X Q, JI X Y. Synthesis by TEA sol-gel method and electrochemical properties of Li4Ti5O12 anode material for lithium-ion battery[J]. Solid State Ionics, 2005, 176(13/14): 1201-1206.
[21] SCHARNER S, WEPPNER W, SCHMID-BEURMANN P. Evidence of two-phase formation upon lithium insertion into the Li1.33Ti1.67O4 spinel[J]. J Electrochem Soc, 1999, 146(3): 857-861.
Corresponding author: KAN Su-rong; Tel: +86-10-82241309; E-mail: ksr8065@163.com
(Edited by ZHAO Jun)