文章编号:1004-0609(2013)08-2118-07
海洋环境中7075-T6铝合金的氢渗透及应力腐蚀破裂
郑传波1,益 帼1,高延敏1,张 克2
(1. 江苏科技大学 材料科学与工程学院,镇江 212003;2. 中国石油天然气管道局 海洋工程分公司,廊坊 065000)
摘 要:采用D-S双电解池研究7075-T6铝合金的表观氢渗透系数,对表面镀镍厚度、充氢电流和循环次数对表观氢渗透系数的影响进行研究,进一步研究表面镀镍充氢试样的应力腐蚀敏感性。结果表明:表面镀镍厚度为220 nm时,钝化电流最为稳定,镀镍层厚度对氢渗透电流的影响主要体现在对氢原子的氧化能力和对铝合金基体的保护能力上。表观氢渗透系数随充氢电流增大有增大的趋势,主要与表面氢原子深度增大、深度梯度增大以及加速氢向铝合金的渗透相关。但是增大幅度表观氢渗透系数有减小的趋势,主要原因是由于氢的表面覆盖度增大后,大部分的氢原子开始结合为氢气而脱离铝合金表面。随着循环次数的增加,表观氢渗透系数也随之增大,主要原因是随着循环次数增加,铝合金内部的不可扩散氢深度趋于稳定,可扩散氢的渗透速度增大。SSRT实验分析和SEM电镜照片结果表明:随充氢时间的增长,SSRT敏感性增大,氢能够渗入铝合金内部,并使其脆性增大,且其脆性随着充氢时间延长而有所增大。
关键词:7075-T6铝合金;表观氢渗透系数;D-S双电解池; SSRT实验
中图分类号:P734;P755.3 文献标志码:A
Hydrogen permeation and stress corrosion cracking sensitivity of 7075-T6 Al alloy in marine environment
ZHENG Chuan-bo1, YI Guo1, GAO Yan-min1, ZHANG Ke2
(1. School of Materials Science and Engineering, Jiangsu University of Science and Technology, Zhenjiang 212003, China;
2. China Petroleum Pipeline Bureau Offshore Engineering Company, Langfang 065000, China)
Abstract: The apparent hydrogen diffusivity was studied by D-S double cell. The effect of thickness of plated Ni, charging current density and charging-uncharging cycles on apparent hydrogen diffusivity was studied. And the stress corrosion cracking (SCC) sensitivity of constant charging specimens was studied. The results show that the passivation current is steady while the thickness of plated Ni is 220 nm. The plated Ni can provide protection from pitting corrosion and catalysis effect on hydrogen. The apparent hydrogen diffusivity increases with the increase of charging current density. The surface hydrogen concentration increases with the increase of charging current density, and the concentration gradient also increases, the hydrogen permeation rate increases, while the increase trend becomes slow due to the surface coverage. The apparent hydrogen diffusivity increases with the increase of charging-uncharging cycles at the beginning, and then reaches a steady value due to the overflow of non-diffuse hydrogen and the increase of hydrogen permeation rate. And the SCC sensitivity of constant charging specimens increases with the increase of charging time.
Key words: 7075-T6 Al alloy; apparent hydrogen diffusivity; D-S double cell; SSRT experiment
金属材料的腐蚀过程常涉及氢的析出,氢进入金属材料内部后往往引起材料的脆断,造成灾难性后果。7075铝合金已广泛应用于航空航天领域,是一种高强度、低密度的材料。但是在其应用过程中容易受到环境影响而发生点蚀、应力腐蚀破裂、晶间腐蚀等多种形式的破坏。铝合金在盐溶液中的应力腐蚀破裂受到了研究者的关注,但是目前还没有形成对其机理的统一认识。研究表明,金属的氧化与氢离子的还原有关,且氧化电流与氢离子在点蚀或应力腐蚀裂纹附近的还原电流相互平衡,产生的氢离子将会渗透入金属并聚集在点蚀或应力腐蚀裂纹附近。近年来,有研究者提出了一种铝合金应力腐蚀破裂的氢脆和阳极溶解共同作用的机制。但是由于氢向铝合金的渗透电流测量较困难,这方面的研究也较少,所以尚缺少有关氢渗透入铝合金的有力证据。随着实验技术的进步及测量仪器精度的提高,近年来,这方面研究日益增多[1-7]。有研究表明,氢在不同系别的铝合金中的渗透系数从2×10-9到3×10-6 cm2/s。GEST[5]通过D-S双电解池测到3%NaCl中AA7075铝合金的氢渗透现象,并在对铝合金进行阴极阳极极化时测到氢渗透电流,但是测试方法较繁琐,不便于实验结果的重现。ONUCHUKWU 等[6]通过D-S双电解池对AA1060纯铝进行了研究。结果表明:铝在碱性环境中也可以发生氢渗透,且测得碱性环境中氢渗透系数为3×10-6 cm2/s。虽然对铝合金氢渗透的研究越来越多,但是关于铝合金的氢渗透系数还存在着比较大的分歧。这种分歧主要因为铝合金表面镀钯或镀镍时受到氧化膜和铝合金自身发生点蚀的影响。文献[4-5]中对铝合金表面镀镍或钯的工艺没有详细说明,实验的可重复性不高。另外,7×××系铝合金主要用于航空航天领域,在服役过程中,尤其是在沿海环境中容易发生局部腐蚀,给安全飞行带来极大隐患。国内外学者对其展开了大量研究以提高其耐蚀性能,但其应力腐蚀破裂机理一直不明确[7-11],本文作者主要从铝合金的氢渗透及其应力腐蚀破裂敏感性方面展开,研究氢渗入对其应力腐蚀破裂的影响。
本文作者旨在研究一种具有可重复性的D-S双电解池研究铝合金氢渗透系数的方法,主要通过简易的电化学镀镍工艺在铝合金表面镀镍,然后通过D-S双电解池研究其氢渗透行为,进一步采用慢应变速率拉伸实验(SSRT)研究其在海洋环境中充氢后的应力腐蚀敏感性。
1 实验
1.1 实验材料
实验材料采用7075-T6,将其加工成直径40 mm,厚度为5 mm的薄圆片。两面用800号砂纸逐级打磨。材料厚度对氢渗透电流有着直接的影响,材料厚度小于0.2 mm时,由于试样在加工过程中会形成表面划痕等原因,材料氢渗透电流比实际情况大[5]。当材料厚度大于0.3 mm时,氢渗透电流趋于一稳定值。用酒精和丙酮采用超声波清洗,以彻底去除试样表面的油污。试样双面镀镍,镀镍液组成为:250 g/L 硫酸镍[NiSO4·6H2O], 45 g/L 氯化镍[NiCl2·6H2O],40 g/L 硼酸[H3BO3]和0.2 g/L十二烷基硫酸钠[C12H25SO4Na],pH值为3。镀镍时,先用30 g/L磷酸钠,20 g/L碳酸钠10 mL/L的烷基酚聚氧乙烯醚除油,然后用氢氟酸、硝酸和水的体积比为1:1:1的溶液去除氧化膜,清洗时间60 s。最后采用上述镀镍液进行镀镍,先在镀镍电流密度3 mA/cm2时镀镍3 min,然后在镀镍电流密度1.5 mA/cm2时镀镍5 min。
1.2 氢渗透实验
传统的Devnathan-Stachurski(D-S)双电解池,试样夹在两个电解池中间,处理不好容易漏液,并且实验过程中换试样比较繁琐。本文作者采用改进的Devnathan-Stachurski双电解池技术测量7075铝合金在不同溶液中的氢渗透电流。改进的Devanathan- Stachurski双电解池实验装置如图1所示。该电解池是由作为双面电极的试样及其大小两个电解池构成,小电解池为阴极池,大电解池为阳极池。试样作为公用工作电极,与参比电极(Hg/HgO参比电极)、辅助电极(镍电极)一套三电极体系。阳极池为检测池,所用溶液为0.2 mol/L NaOH,用优级纯试剂与二次水配制。实验时,铝合金采用双面镀镍的方法,阳极池加入0.2 mol/L NaOH溶液(在0 mV vs HgO/Hg/0.2 mol/L NaOH极化电位下)钝化24 h以上,使背景电流密度小于0.1 μA/cm2;试样另一侧(即阴极侧)滴加0.2 mol/L NaOH溶液,开始充氢,记录不同条件下的氢渗透电流密度大小。试验时使用一台恒电位仪采集氢渗透电流密度,用计算机通过数据采集卡采集数据记录。阴极池一侧产生的氢原子渗透过金属薄片在阳极侧镀镍层的催化下被氧化为氢离子,用计算机通过数据采集器测得的氧化电流即为氢渗透电流。
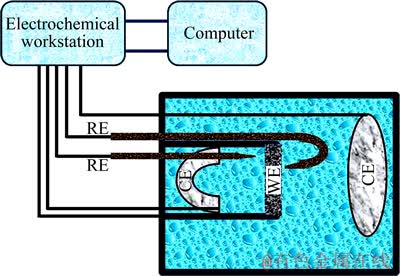
图1 实验装置示意图
Fig. 1 Schematic diagram of experimental set-up
1.3 慢应变速率拉伸实验
试样为圆棒状,表面采用镀镍处理,防止表面发生腐蚀。采用恒电流充氢不同时间后研究其应力腐蚀敏感性,充氢电流为-2 mA/cm2。实验时,在模拟海洋环境(3.5% NaCl)中充氢不同时间后,再放置在空气中拉伸,以便研究试样的应力腐蚀敏感性随充氢时间的关系。
2 结果与分析
2.1 镀镍层厚度对氢渗透系数的影响
镀镍层厚度根据法拉弟定律计算:
(1)
式中:M为镀层金属的摩尔质量;d为镀镍层厚度,I为镀镍电流,t为时间,d为密度,r为试样半径,n为电子数,F是法拉第常数。
根据镀镍时间和电流的不同,计算得到的镀镍层厚度,图2所示为不同镀镍层厚度时钝化电流密度随时间的变化。其中1的厚度约为150 nm,2的厚度为180 nm,3的厚度为220 nm。图3所示为不同镀镍厚度对氢渗透电流的影响。镀镍层厚度为220 nm时,钝化电流密度最为稳定。从图3中可知,镀镍层厚度增大,稳定氢渗透电流密度先增大,然后减小。但是镀镍层厚度为180 nm和220 nm时,稳定氢渗透电流密度相差不大。OUYANG等[12]研究发现未镀镍钢材也能检测到氢渗透电流,但是由于其氧化氢原子能力所限,所以氢渗透电流密度仅为镀镍钢板的10%。镍镀层做为氢原子氧化的催化剂,其厚度会对氢渗透电流密度产生一定影响,镀镍厚度太低时,铝合金表面未能被镍完全覆盖或者说镍氧化能力有限,渗透过的氢不能完全被氧化,氢渗透电流密度会变小,对结果产生负偏差。当镀镍层厚度增大时,铝合金表面的镍更加致密,会消除负偏差。但是镀镍层厚度太大的时候,又会对氢渗透电流密度产生正偏差,阻碍部分氢向材料的渗透。在本实验中,镍镀层为150 nm时稳定氢渗透电流密度约为1.5 μA/cm2时,镍不能完全氧化渗透过试样的氢原子。镍镀层厚度为180 nm和220 nm时的稳定氢渗透电流密度相差不大,表明镍镀层在180 nm时,已经能够完全氧化渗透过金属的氢原子。
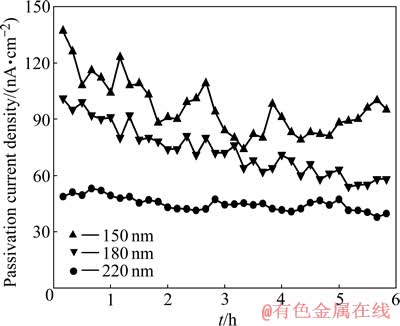
图2 不同镀镍厚度时钝化电流密度随时间的变化
Fig. 2 Change of passivation current with time at different plated Ni thickness

图3 不同镀镍厚度时氢渗透电流密度随时间的变化
Fig. 3 Change of hydrogen permeation current density with time at plated Ni thickness
根据Time-lag 法计算表观氢渗透系数:
(2)
式中:D为表观氢渗透系数,L为试样厚度,tL是氢渗透电流it= 0.63 i ∞时的时间。
计算所得的D值分别为2.1×10-7、3.5×10-7和3.2×10-7 cm2/s。表观氢渗透系数随镀镍层厚度增大先增大,然后减小。在DANIELSON等[5]的研究中发现,BRAUN等[13]的实验具有可重复性,用D-S双电解池研究了纯铝、7075-T6和AA2024-T3铝合金的氢渗透行为。采用喷溅法去除表面氧化膜,接着在表面喷溅5 μm Pd或者75%Pd+25%Ag(摩尔分数)(简称75Pd-25Ag)的薄膜。阳极侧是除氧的亚硝酸钠或0.5 mol/L乙酸钾的甲酰胺溶液,测得的氢渗透系数在1×10-7 cm2/s到6×10-7 cm2/s之间。本文作者计算得到的D值与BRAUN等[13]的研究结果处于一个数量级,说明本研究中试样处理和实验方法具有可靠性。
2.2 充氢电流对氢渗透系数的影响
镀镍层厚度为220 nm时,对不同充氢电流密度对氢渗透电流密度的影响进行研究,其结果如图4所示。根据时间滞后法(Time-lag 法)计算所得的D值分别为3.2×10-7、3.53×10-7和3.66×10-7 cm2/s。随充氢电流的增大,表观氢渗透系数有增加的趋势,但是增加的趋势变的缓慢,充氢电流为3 mA/cm2和5 mA/cm2时,表观氢渗透系数相对于充氢电流为2 mA/cm2时的增大幅度分别为10%和14%。
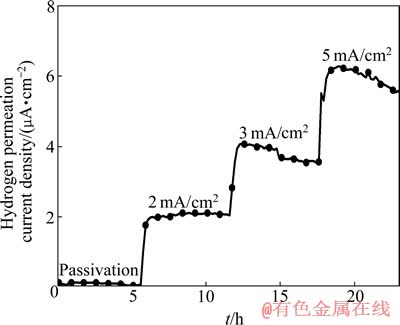
图4 不同充氢电流密度下氢渗透电流密度随时间的变化
Fig. 4 Change of hydrogen permeation current density with time under different charging current densities
氢渗透电流密度与表观氢浓度c0和D的关系可表示为
I ∞=c0DF/L (3)
式中:I ∞是稳态氢渗透电流,L是试样厚度。
由式(3)可知,氢渗透电流密度随着充氢电流增大主要有两方面的影响因素,一个是氢渗透系数的增大,另一个是表观氢浓度c0的增大。氢渗透系数对氢渗透电流密度增大的贡献值分别为10.3%和3.7%,说明表观氢渗透系数的增大不并不是氢渗透电流密度增大的主要原因。这与温度对氢渗透电流密度增大的影响有所不同[14],温度升高对氢渗透电流密度增大的主要原因是D的增大,随着温度升高,氢原子在充氢侧的吸附和吸收步骤加快。相反,使试样晶格发生扭曲所需的活化能开始增大。本研究中D的增大不明显,主要原因应该是表观氢浓度的增大。
根据下面公式计算了不同充氢电流密度下的表观氢浓度c0,
(4)
计算结果示于图5中。
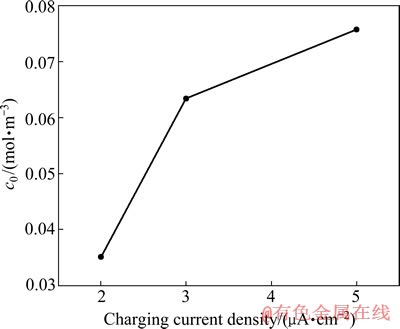
图5 表观氢浓度c0随充氢电流的变化
Fig. 5 Change of apparent surface hydrogen concentration with different charging current density
充氢电流密度从2 mA/cm2变为3 mA/cm2时,表观氢浓度变化较大;但当充氢电流密度3 mA/cm2增大到5 mA/cm2时,表观氢浓度变化有减小的趋势。充氢电流密度越大,试样表面的H原子浓度越高,试样表面和基体金属内部之间产生的浓度梯度越大。在这种梯度力的作用下,H原子向金属内部的扩散加剧,渗氢电流密度逐渐增大。但当充氢电流密度达到5 mA/cm2时,试样表面的氢原子有较大的部分开始互相结合成氢气而脱离试样表面,表面氢浓度开始趋于定值,有研究认为[15],氢首先是通过在电极表面的吸附形成单分子吸附层再参加电极反应,当氢原子浓度不够大时,被吸附在电极表面的氢原子覆盖度θ较小时,氢原子或大部分氢原子来不及结合为氢气,氢渗透电流密度随氢原子浓度的增大而增加,当氢原子浓度足够大,被吸附在电极表面氢原子浓度表面覆盖度θ较大时,氢原子的吸附和结合为氢气竞争机制开始起作用,导致吸附在试样表面的氢浓度趋于稳定[16]。
2.3 反复循环次数对氢渗透系数的影响
铝合金氢渗透电流的测试中,最主要存在两个问题,一个是铝合金表面氧化层[17]对氢渗透的阻碍作用和对电镀镍附着力的影响,另一个是镀镍层出现点蚀影响氢渗透电流的测定。铝合金表面氧化层的作用在电镀镍时已经去除。为测试反复循环后氢渗透电流的稳定性,采用充氢电流密度为2 mA/cm2,镀镍层厚度为220 nm为实验条件,对试样进行反复充放氢测试,所得到的稳定氢渗透电流值如图6所示。稳定氢渗透电流随循环次数的增加有增大的趋势,增大到一定值后变化平缓。根据Time-lag 法,计算表观氢渗透系数,得到图7所示的循环次数对氢渗透系数的影响。由图6可知,稳定氢渗透电流密度随循环次数的增加先增加然后趋于稳定,表观氢渗透系数变化也相似,先增大然后趋于稳定。氢原子进入金属后分为可扩散氢和不可扩散氢,可扩散氢会在浓度梯度下向检测池移动,最终扩散出金属被氧化;不可扩散的氢被定扎在金属内部无法移动。也就是说氢扩散进金属后,一部分被定扎为不可扩散氢,另一部分在浓度梯度作用下向检测池移动[18]。随着循环次数的增加,稳定氢渗透电流密度的变化说明在最初的循环中,铝合金内部的不可扩散氢尚未完全填满,这一点在表观氢渗透系数上也有体现,由图7中可知,表观氢渗透系数随循环次数增加,先增大后保持稳定值。根据公式(2),D与时间有关。在试验中发现,D增大的原因主要是tL变小导致,也就是氢向金属的渗透速度加快,主要原因跟以上分析相关,随着循环次数增加,不可扩散氢所占用的氢变少,大部分氢原子在浓度梯度作用下向检测池移动,达到tL的时间变小。

图6 充放电循环次数对稳定氢渗透电流密度J∞的影响
Fig. 6 Effect of charging-uncharging cycles on J∞

图7 充放电循环次数对表观氢渗透系数的影响
Fig. 7 Effect of charging-uncharging cycles on apparent hydrogen diffusivity
2.4 SSRT实验
图8所示为7075-T6铝合金在不同阴极充氢后的应力—应变曲线(充氢电流为-2 mA/cm2)。图9所示为对应的断口形貌。试样在海水环境中断裂伸长率有所下降,断裂时间减小,扫描电镜图相显示在空气中断口主要呈现韧窝,具有明显塑性断裂标志。充氢3 h后,试样断裂伸长率的减小不大,屈服应力有所增大,断口存在韧窝与少量河流花状样,表现出少量氢致断裂特征。随着充氢时间的增长,断裂伸长率进一步减小,充氢12 h和18 h后,断裂伸长率相关不大,但是18 h后,屈服应力有所下降。断口形貌中,12 h后的断口表现出较多的脆性断裂特征。18 h后的断口除表现出脆性断裂特征外,还有少量的类似氢化物的白斑出现,氢致断裂特征增多。结合氢渗透实验结果,氢在铝合金中的氢渗透率较小,充氢初期,氢渗入量较小,氢致脆性不太明显,随着充氢时间增长,氢渗入量增大,脆性增大。
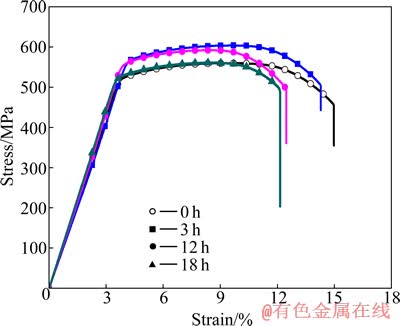
图8 7075-T6铝合金不同充氢时间的应力—应变曲线
Fig. 8 Strain—stress curves of 7075-T6 Al alloy after different charging times
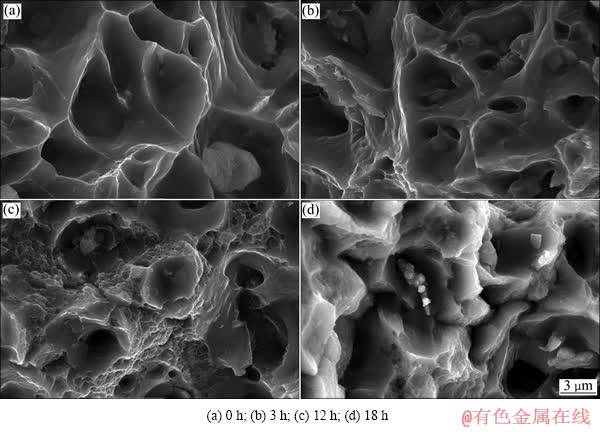
图9 7075-T6铝合合的断口形貌
Fig. 9 Fracture morphologies of 7075-T6 Al alloy
3 结论
1) 镀层厚度太小时,不足以全面覆盖铝合金表面,在检测池侧会发生铝和碱的反应,影响氢渗透系数测定;镀层厚度太大时,则会对氢原子的渗透造成阻碍作用,因此,最佳的镀层厚度为220 nm。
2) 充氢电流对表观氢渗透系数的影响主要在于表面氢浓度的变化,表面氢浓度除与充氢电流密度相关外,还与氢原子的表面覆盖率有关系。反复充放氢多次后,未在铝合金表面发现腐蚀,表明在220 nm镀镍层下,铝合金基体得到良好保护。表观氢渗透系数先增大后保持稳定,主要原因是由于铝合金内部不可扩散氢在经过几次循环后已经饱和,导致氢向检测池的渗透加速所致。
3) SSRT实验表明,氢能够向7075-T6铝合金渗透,发生一定程度上的脆化,脆性随着充氢时间增长而增大。
REFERENCES
[1] GEST R J, TROIANO A R. Stress corrosion and hydrogen embrittlement in aluminum alloys [J]. Corrosion, 1974, 30(8): 274-279.
[2] MUJIBUR RANHMAN A B M, KUMAR S, GERSON A R. Galvanic corrosion of laser weldments of AA6061 aluminium alloy [J]. Corrosion Science, 2007, 49(10): 4339-4351.
[3] 刘建华, 郝雪龙, 李松梅, 于 美. 新型含钪Al-Mg-Cu合金的抗应力腐蚀开裂特性[J]. 中国有色金属学报, 2010, 20(3): 415-419.
LIU Jian-hua, HAO Xue-long, LI Song-mei, YU Mei. Resistance to stress corrosion cracking of new Al-Mg-Cu alloy containing Sc [J]. The Chinese Journal of Nonferrous Metals, 2010, 20(3): 415-419.
[4] ADAMS T M, PAUL K, ANDREW D. Evaluation of oxidation and hydrogen permeation in Al-containing stainless steel alloys [J]. Materials Science & Engineering, 2006, 424(1): 33-39.
[5] GEST R J, TROIANO A R. Stress corrosion and hydrogen embrittle in an aluminum alloy[J]. Corrosion, 1974, 30(8): 274-280.
[6] ONUCHUKWU A I, TASATTI S. Hydrogen permeation into aluminum alloy 1060 as a result of corrosion in alkaline medium[J]. Basic Features of the Process, 1988, 33(10): 1425-1431.
[7] ZHENG Chuan-bo, YI Guo, GAO Yan-min. An electrochemical sensor for measuring hydrogen permeation behavior in atmospheric environment [J]. International Journal of Electrochemical Science, 2012, 7(10): 9518-9525.
[8] LEE E U, VASUDEVAN A K, GLINKA G. Environmental effects on low cycle fatigue of 2024-T351 and 7075-T651 aluminum alloys [J]. International Journal of Fatigue, 2009, 31(11/12): 1938-1942.
[9] PUIGGALI M, ZIELINSKI A, OLIVE JM, RENAULD E, DESJARDINS D, CID M. Effect of microstructure on stress corrosion cracking of an Al-Zn-Mg-Cu alloy [J]. Corrosion Science, 1998, 40(4/5): 805-819.
[10] KOTSIKOS G, SUTCLI J M, HOLROYD N J H. Hydrogen effects in the corrosion fatigue behavior of the white zone of 7xxx series aluminum alloy welds [J]. Corrosion Science, 2000, 42(1): 17-33.
[11] THAKUR C, BALASUBRAMANIAM R. Determination of hydrogen diffusivity in Al-Li-Cu-Mg alloys [J]. Journal of Materials Science Letters, 1996, 15(16): 1397-1399.
[12] OUYANG Y J, YU G, OU A L, XU W J. Double electrolyte sensor for monitoring hydrogen permeation rate in steels [J]. Corrosion Science, 2011, 53(6): 2247-2252.
[13] BRAUN R. Stress corrosion cracking behaviour of aluminium alloy sheet in an aqueous solution of 3%NaCl+0.3%H2O2[J]. Materials and Corrosion, 1994, 45(5): 255-263.
[14] ZHENG Chuan-bo, YI Guo. Temperature effect on hydrogen permeation of X56 steel [J]. Materials performance, 2011, 50(4): 72-76.
[15] ZHENG Chuan-bo, HUANG Yan-liang, HUO Chun-yong, Yu Qing. Hydrogen permeation behavior and corrosion monitoring of steel in cyclic wet-dry atmospheric environment [J]. Materials and Corrosion, 2007, 58(9): 716-720.
[16] 李国敏, 刘烈伟, 郑家棠. 碳钢在硫化氢及高压二氧化碳饱和的NaCl溶液中的腐蚀行为[J]. 中国腐蚀与防护学报, 2000, 20(4): 204-209.
LI Guo-min, LIU Lie-wei, ZHENG Jia-tang. Corrosion behavior of carbon steel in high pressure dioxide saturated NaCl solutions containing hydrogen sulfide [J]. Journal of Chinese Society for Corrosion and Protection, 2000, 20(4): 204-209.
[17] SCULLY J R, YOUNG G A, SMITH S W. Hydrogen solubility, diffusivity and trapping in high purity aluminum and selected Al-base alloys [J]. Materials Science Forum, 2000, 331/337: 1583-1600.
[18] QIAO Li-jie, HSIAO Chi-mei, CHU Wu-yang, CHEN Lian, LIU Shu-wang, ZOU Jun-jun. The concentration of hydrogen at crack tip of austenitic stainless steel after stress corrosion and polarization [J]. Scripta Metallurgica, 1988, 22(5): 627-630.
(编辑 李艳红)
基金项目:国家自然科学基金资助项目(51001055,51310105001);江苏高校优势学科建设资助项目
收稿日期:2012-05-25;修订日期:2013-05-20
通信作者:郑传波,副教授,博士;电话:0511-84401184;E-mail: chuanbo.zheng@gmail.com