Trans. Nonferrous Met. Soc. China 23(2013) 964-969
Formability of AA5052/polyethylene/AA5052 sandwich sheets
Jian-guang LIU1,2, Wei XUE2
1. National Key Laboratory for Precision Hot Processing of Metals, Harbin Institute of Technology, Harbin 150001, China;
2. School of Materials Science and Engineering, Harbin Institute of Technology, Harbin 150001, China
Received 21 March 2012; accepted 18 July 2012
Abstract: The formability of AA5052/polyethylene/AA5052 sandwich sheets was experimentally studied. Three kinds of AA5052/polyethylene/AA5052 sandwich specimens with different thicknesses of core materials were prepared by the hot pressing adhesive method. Then, the uniaxial tensile tests were conducted to investigate the mechanical properties of AA5052/polyethylene/ AA5052 sandwich sheets, and the stretching tests were carried out to investigate the influences of polymer core thickness on the limit dome height of the sandwich sheet. The forming limit curves for three kinds of sandwich sheets were obtained. The experimental results show that the forming limit of the AA5052/polyethylene/AA5052 sandwich sheet is higher than that of the monolithic AA5052 sheet, and it increases with increasing the thickness of polyethylene core.
Key words: AA5052 aluminum alloy; sandwich sheets; polyethylene; formability; forming limit diagram
1 Introduction
With the gradual requirement of fuel savings and structural weight reduction in industries, lightweight materials and lightweight structures have gotten more and more applications. Over the past decades, metal- plastic sandwich sheets have generated a considerable interest as potential lightweight materials for structural parts [1]. Typically, a metalplastic sandwich sheet consists of two layers of metallic sheet as skin and a polymeric material as core. Three layers are glued together. The skin metallic materials are steel or aluminum alloy and the core polymeric material is polypropylene or polyethylene generally. Compared with monolithic metallic sheet, metal-plastic sandwich sheet offers lower density, higher specific flexural stiffness, better dent resistance and better sound and vibration damping characteristics [2-4]. Among various sandwich sheets, aluminum/plastic/aluminum sandwich sheets have generated a considerable interest as potential light weight and sound-deadening sheets for the body panels of high performance vehicles [5,6].
Although the aluminum/plastic/aluminum sandwich sheets have many advantages, however, the forming of these materials is very complicated due to the extremely large difference in mechanical properties between the polymer core and the skin sheet. The behaviors of the sandwich sheets are quite different from those of homogenous metallic sheets during the forming processes. The interface stress between skin sheet and core layer has a large influence on the deformation behavior of sandwich sheet [7]. Furthermore, the sliding and shearing occur between skin layers and hence affect the formability of the sandwich sheet [8-11]. In order to apply aluminum/plastic/aluminum sandwich sheets for automotive body panels, the formability of sandwich sheet must be investigated firstly. Over the past decades, many aluminum/plastic/aluminum sandwich sheets have been developed, such as AA5005/polypropylene/ AA5005 sandwich sheet, AA5182/polypropylene/ AA5182 sandwich sheet and AA3105/polypropylene/ AA3105. The formability of these sandwich sheets was investigated through experiments and numerical simulations, and some factors affecting the formability were also analyzed [12-16].
In the present study, a new AA5052/polyethylene/ AA5052 sandwich sheet was prepared, and the formability of AA5052/polyethylene/AA5052 sandwich sheets was investigated through experiments. Three kinds of AA5052/polyethylene/AA5052 sandwich specimens with different thicknesses of core materials were prepared by the hot pressing adhesive method. The uniaxial tensile tests were firstly conducted to have a better understanding of the mechanical properties of AA5052/polyethylene/AA5052 sandwich sheet. Then, the stretching tests were conducted for these sandwich sheets to investigate the influences of friction and polymer core thickness on the limit dome height of the sandwich sheet. Finally, the forming limit curves for these three kinds of sandwich sheets were obtained.
2 Preparation of sandwich sheets
A non-heat-treatable 5052-O aluminum alloy sheet with a thickness of 0.5 mm was used as skin materials of sandwich sheets. Table 1 shows the chemical composition of the AA5052-O skin sheet. A high density polyethylene was used as core materials of sandwich sheets. The strain—stress curves of AA5052-O skin sheet and polyethylene core materials are shown in Fig. 1.
Table 1 Chemical composition of AA5052-O aluminum alloy (mass fraction, %)

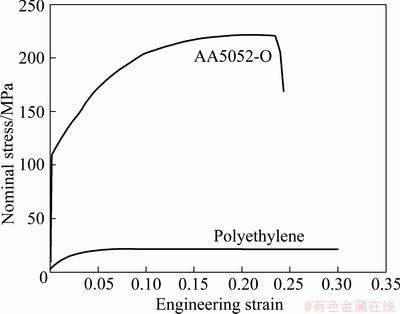
Fig. 1 Stress—strain curves of AA5052-O skin sheet and polyethylene core
The AA5052/polyethylene/AA5052 sandwich sheets were fabricated by the hot-pressing method. A hot-melt polyethylene adhesive film with a thickness of 0.05 mm was inserted between the AA5052 skin sheet and the polyethylene core to bond the core material and skin layers. The mould was placed into a pre-heated hot press with a thermocouple used to monitor the temperature of sandwich sheet. At 180 °C, the sandwich sheet was consolidated at a hydraulic plane hot pressure of 2 MPa for 7-10 min. Three kinds of sandwich sheets with core thicknesses of 0.5, 1.0 and 2.0 mm were prepared to investigate the influence of the thickness ratio on the formability of the sandwich sheet.
3 Tests for formability of sandwich sheets
3.1 Uniaxial tensile tests
The mechanical properties of sandwich sheets were determined through the tensile tests. The skin and core materials were cut in the required shapes directly and then bonded to the sandwich samples. A standard extensometer with a length of 25 mm was used to measure the strain accurately. An Instron 5569 material testing machine was used to perform the tensile tests on the sandwich specimens, and all the tests were conducted at a constant cross-head speed of 3 mm/min until fracture occurred.
According to Ref. [17], the stress—strain curves of the sandwich sheets can be predicted from those of the aluminum skin and the plastic core according to the rule of the mixture:
(1)
where ss is the flow stress of sandwich sheet, sf and sc are the flow stresses of skin sheet and plastic core, respectively, φf and φc are the volume fractions of skin sheet and plastic core, respectively.
Figure 2 shows the comparison of nominal stress—engineering strain curves of sandwich sheets determined by tensile tests and those calculated from the rule of the mixture. The results show that there are reasonably good agreements between the experimental and the calculated values, which indicates that the rule of the mixture can appropriately predict the tensile properties of the AA5052/ polyethylene/AA5052 sandwich sheet.
Table 2 lists the mechanical properties of AA5052-O skin sheet and sandwich sheets. The yield stress (YS), the ultimate tensile strength (UTS) and the elongation at fracture (Elf) are obtained from the stress—strain curves shown in Figs. 1 and 2. The elastic modulus of sandwich sheets is lower than that of the AA5052 skin sheet. The elongation of the sandwich sheet is higher than that of the monolithic AA5052-O sheet and increases with increasing the thickness of polyethylene core.
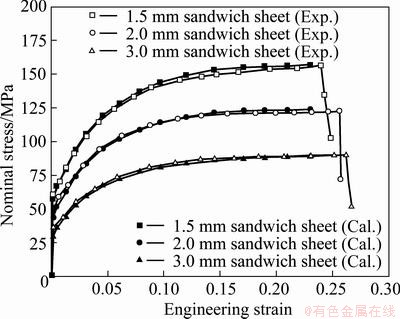
Fig. 2 Nominal stress—engineering strain curves of sandwich sheets
Table 2 Mechanical properties of AA5052-O skin sheet and sandwich sheets
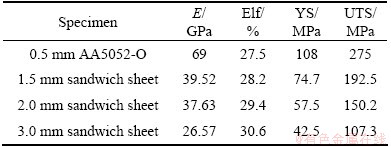
3.2 Formability tests
Hemispherical punch tests were conducted to investigate the formability of sandwich sheets. The diameters of the hemispherical punch and the die cavity are 90 and 95 mm, respectively. These tests were carried out on a universal testing machine. The punch stroke and load were obtained through the computer connected with the material testing machine. The cross-head speed was 3 mm/min for all tests. The main dimensions of the test samples are shown in Fig. 3. By changing the specimen geometry and lubrication conditions, various strain ratios of a deformed specimen formed. The specimens were prepared along the rolling direction. The arc-shaped specimens have widths of 20, 40, 60 and 80 mm, and the circle specimens have a diameter of 130 mm. The strain paths of the arc-shaped specimens were located in the negative minor strain region, which covered the region from the simple tension region to the plane strain region; and the strain paths of the circle specimens covered the plane strain region to the balanced biaxial stretch region. Two lubrication conditions were applied to the punch-stretch tests. The friction coefficient decreased in the order of dry and polytetrafluoroethene film. Each arc-shaped specimen had one specific strain path on the forming limit diagram (FLD) with the same lubricant (polytetrafluoroethene), and the circle specimens deformed with different lubricants (dry and polytetrafluoroethene) to obtain the biaxial stretch. The circle grids (each with a diameter of 2.0 mm) were printed on the surface of test samples to measure the strain of specimens after testing. The blanks were securely clamped in the holding die without excessive pull-in.
Figures 4 and 5 show the deformed specimens for AA5052-O skin sheet and three kinds of sandwich sheets. The localized fracture of the specimens took place in the center of the specimen for the arc-shaped specimens and deviated the dome center for the circle specimens. The deformed grids near the fracture were measured by using the strain analysis system ASAME so that the major strain and the minor strain can be determined.
4 Results and discussion
4.1 Punch load profile and limit dome height
Firstly, the forming load and limit dome heights were analyzed for the monolithic AA5052 sheet and three kinds of sandwich sheets. Table 3 lists the measured limit dome height (LDH) and limit punch load (LPL) in the hemispherical dome stretching test. It can be seen that the LDH and the LPL of the sandwich sheets and the monolithic AA5052-O sheet increase with improving the lubricant condition. At the same forming height, the punch load under polytetrafluoroethene lubricant condition is obviously lower than that under dry condition for the monolithic AA5052-O sheet. But for the sandwich sheets, the lubricant condition has not a significant effect on the punch load at the same forming height.
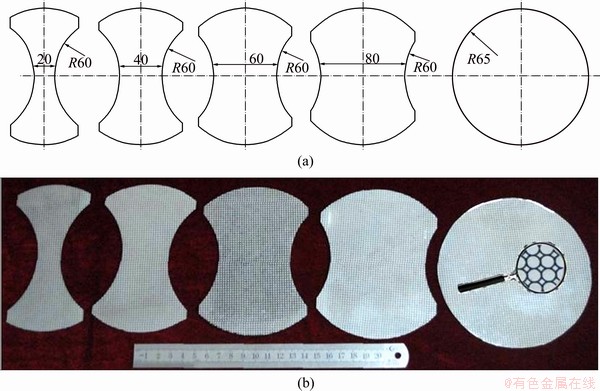
Fig. 3 Main dimensions (a) (Unit: mm) and experimental specimens (b) of test samples
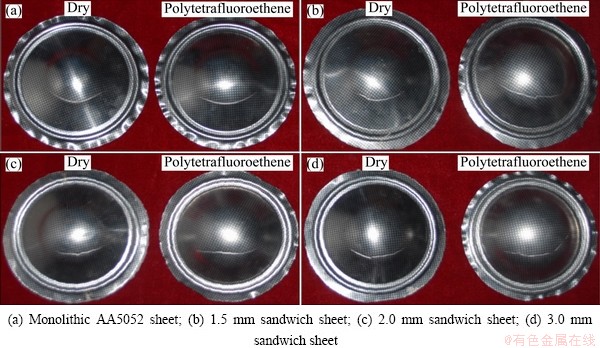
Fig. 4 Bulged specimens
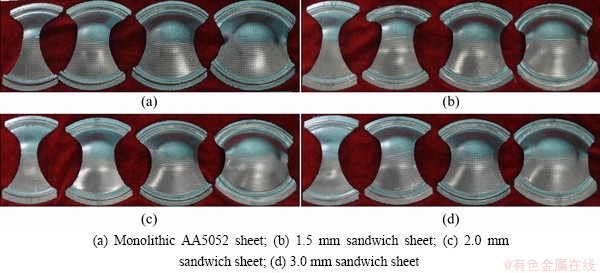
Fig. 5 Deformed shapes of arc-shaped test specimens
Table 3 Measured limit dome height (LDH) and limit punch load (LPL) in hemispherical dome stretching test
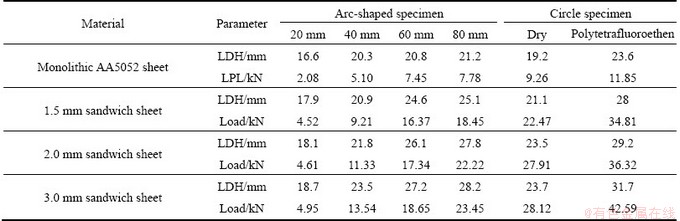
4.2 Strain distributions
The strain distributions of bulge specimens were measured by strain analysis system ASAME. Figure 6 compares the major strain distributions and the minor strain distributions of sandwich sheets and monolithic sheet under polytetrafluoroethene film lubricant. The maximum major strain points of all specimens deviate the center of specimen and the maximum minor strain points locate at the dome center for all bulged specimens. The maximum major strain and the maximum minor strain of sandwich sheets are higher than those of the monolithic sheet. With the increase of the thickness of core polymer, the limit strain of the sandwich sheet increases. Furthermore, the local necking point moves towards the dome center with increasing the thickness of core polymer.
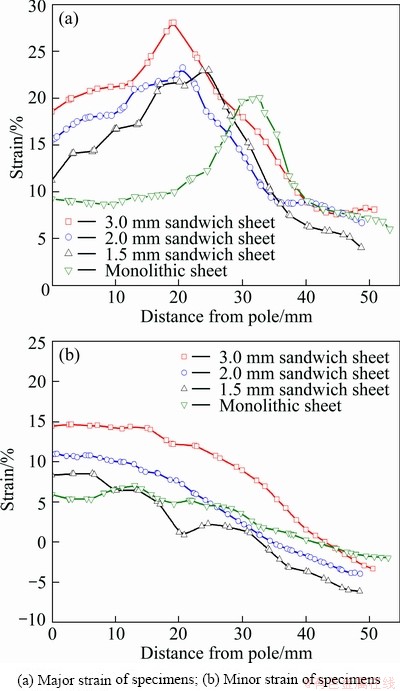
Fig. 6 Strain distributions of bulged specimens
Figure 7 shows the thickness strain distributions of bulged specimens under polytetrafluoroethene film lubricant. Overall, the strain of the sandwich sheets is larger than that of monolithic sheet and increases with increasing the thickness of core polymer. Furthermore, with increasing the thickness of core polymer, the maximum thinning point moves towards the dome center.
4.3 Forming limit diagram of sandwich sheets
Figure 8 shows the measured FLCs of AA5052-O skin sheet and three kinds of sandwich sheets. It can be seen that the FLCs of sandwich sheets are higher than that of the skin sheet. This result confirms that the formability of aluminum alloy-polymer sandwich sheet is higher than that of monolayer aluminum alloy sheet. Furthermore, the FLCs of the 2.0 mm sandwich sheet and the 3.0 mm sandwich sheet are far higher than that of the 1.5 mm sandwich sheet. The FLC of the 3.0 mm sandwich sheet is little higher than that of the 2.0 mm sandwich sheet. It can be concluded that the FLC of sandwich sheet increases with increasing the core thickness when the thickness of skin sheet is constant.
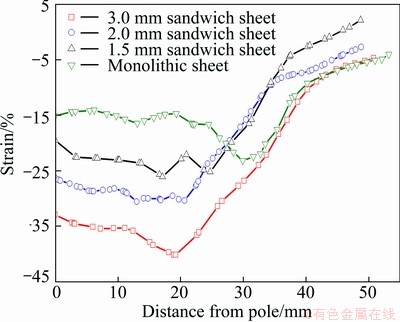
Fig. 7 Thickness strain distributions of bulged specimens under polytetrafluoroethene film lubricant
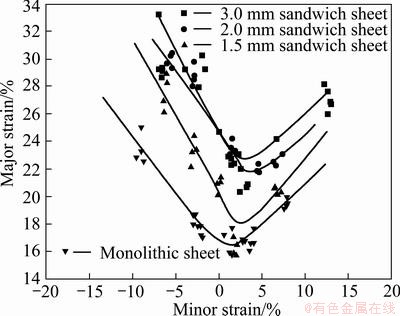
Fig. 8 Measured FLCs of AA5052-O monolithic sheet and sandwich sheets
5 Conclusions
1) The stress—strain curves of AA5052/ polyethylene/AA5052 sandwich sheets agree with the rule of the mixture and can be predicted by the combination of stress—strain curves of AA5052 and polyethylene.
2) The elongation at fracture of AA5052/ polyethylene/AA5052 sandwich sheet is higher than that of monolithic AA5052 sheet and increases with increasing the thickness of polyethylene core.
3) The limit dome height of AA5052/polyethylene/ AA5052 sandwich sheet is larger than that of monolithic AA5052 sheet. Increasing the thickness of the polyethylene core and improving the lubrication condition benefit the enhancement of the limiting dome height of the sandwich sheet.
4) Forming limits of AA5052/polyethylene/AA5052 are higher than those of monolithic AA5052 sheet. The formability of AA5052/polyethylene /AA5052 increases with increasing the thickness of the polyethylene core.
References
[1] Hayashi H, Nakagawa T. Recent trends in sheet metals and their formability in manufacturing automotive panels [J]. Journal of Materials Processing Technology, 1994, 46(3-4): 455-487.
[2] Miller W K. Metal-plastic laminates for vehicle weight reduction [C]//Proceedings of SAE International Congress. Detroit, 1980: 1-10.
[3] DiCello J A. Steel-polypropylene-steel laminate—A new weight reduction material [C]// Proceedings of SAE International Congress. Detroit, 1980: 11-15.
[4] Yao H, Chen C C, Liu S D, Li K P, Du C, Zhang L. Laminated steel forming modelling techniques and experimental verifications [C]// Proceedings of SAE International Congress. Detroit, 2003: 1-10.
[5] Veenstra E W. Aluminum-plastic-aluminum sandwich sheet for maximum weight reduction in body panels [C]// Proceedings of SAE International Congress. Detroit, 1993, 1-10.
[6] Kee J K, Rhee H M, Choi B I, Kim C W, Sung C W, Han C P, Kang K W, Won S T. Development of application technique of aluminum sandwich sheets for automotive hood [J]. International Journal of Precision Engineering and Manufacturing, 2009, 10(4): 71-75.
[7] Makinouchi A, Yoshida S, Ogawa H. Finite element simulation of bending process of steel-plastic laminate sheets [J]. Journal of the JSTP, 1988, 29(330): 755-760.
[8] Chen Ming-an, Zhang Xin-ming, Li Xue-qian, Cheng Fen-qiang, Lei Qiu-ling. Deformation analysis of the plastic core in steel- polypropylene-steel laminated sheet during the deep drawing process by finite element simulation [J]. Journal of Central South University of Technology: Natural Science, 2002, 33(4): 389. (in Chinese)
[9] Wang Yong, Chen Jun, Tang Bing-tao, Ruan Xue-yu. The drawing of laminated vibration damping steel sheet based on finite element simulation [J]. Journal of Shanghai Jiao tong University, 2007, 41(10): 1586-1589. (in Chinese)
[10] Huang Y M, Leu D K. Finite-element simulation of the bending process of steel/polymer/steel laminate sheets [J]. Journal of Materials Processing Technology, 1995, 52(2-4): 319-337.
[11] Link T D. Formability and performance of steel-plastic steel laminated sheet materials [C]//Proceedings of SAE International Congress. Detroit, 2001: 010079.
[12] Kim K J, Kim D, Choi S H, Chung K, Shin K S, Barlat F, Oh K H, Youn J R. Formability of AA5182/polypropylene/ AA5182 sandwich sheets [J]. Journal of Materials Processing Technology, 2003, 139(SPEC 1-3): s1-s7.
[13] Compston P, Cantwell W J, Cardew-Hall M J, Kalyanasundaram S, Mosse L. Comparison of surface strain for stamp formed aluminum and an aluminum-polypropylene laminate [J]. Journal of Materials Science, 2004, 39(19): 6087-6088.
[14] Weiss M, Dingle M E, Rolfe B F, Hodgson P D. The influence of temperature on the forming behavior of metal/polymer laminates in sheet metal forming [J]. Journal of Engineering Materials and Technology, 2007, 129(4): 530-537.
[15] Parsa M H, ahkami S N A, Ettehad M. Experimental and finite element study on the spring back of double curved aluminum/polypropylene/aluminum sandwich sheet [J]. Materials and Design, 2010, 31(9): 4174-4183.
[16] Parsa M H, Ettehad M, Matin P H, Ahkami S N A. Experimental and numerical determination of limiting drawing ratio of al3105-polypropylene-al3105 sandwich sheets [J]. Journal of Engineering Materials and Technology, 2010, 132(3): 03100401-03100411.
[17] Shin K S. Mechanical properties of aluminum/polypropylene/ aluminum sandwich sheets [J]. Metals and Materials International, 1999, 5(6): 613-618.
AA5052/聚乙烯/AA5052复合层板的成形性
刘建光1,2,薛 卫2
1. 哈尔滨工业大学 金属精密热加工国家级重点实验室,哈尔滨 150001;
2. 哈尔滨工业大学 材料科学与工程学院,哈尔滨 150001
摘 要:对AA5052/聚乙烯/AA5052复合层板成形性进行实验研究。采用热压粘结法制备3种中心层聚合物厚度不同的AA5052/聚乙烯/AA5052复合层板。对制备的复合层板进行拉伸实验,研究其力学性能。对3种聚合物复合层板进行刚性半球凸模胀形实验,研究中心层厚度对复合层板极限胀形高度的影响,得到3种复合层板成形极限曲线。研究结果表明:AA5052/聚乙烯/AA5052复合层板的成形极限高于单层AA5052铝合金板材的成形极限,并且随着聚乙烯层厚度的增加,复合层板成形极限提高。
关键词:AA5052铝合金;复合层板;聚乙烯;成形性;成形极限图
(Edited by Wei-ping CHEN)
Foundation item: Project (HIT.NSRIF.2009033) supported by the Scientific Research Foundation of Harbin Institute of Technology, China
Corresponding author: Jian-guang LIU; Tel/Fax: +86-451-86413365-19; E-mail: liujg@hit.edu.cn
DOI: 10.1016/S1003-6326(13)62553-4