DOI: 10.11817/j.ysxb.1004.0609.2021-37816
5182-O铝合金板材自冲铆接工艺参数对接头组织和性能的影响
毛晓东,刘庆永,李 利,谷宁杰,傅 垒,赵丕植
(中铝材料应用研究院有限公司,北京 102209)
摘 要:在D、F两种底模作用下,采用4种长度的铆钉(5.0 mm、5.5 mm、6.0 mm和6.5 mm)对5182-O铝合金板材1.5 mm+1.5 mm组合接头进行自冲铆接试验,对接头剖切面进行关键特征值测量,利用EBSD、硬度测试及拉伸试验对接头的组织和强度、吸能进行了研究;并基于5182-O板材在不同应变速率下的本构模型及Johnson-Cook损伤模型,建立自冲铆接成形过程模型,并与试验结果进行对比验证。结果表明:随着铆钉长度的增加,接头的强度、吸能呈先提高后降低的变化趋势,铆钉长度为6.0 mm时,接头性能最佳;在相同铆钉长度下,D组接头力学性能明显高于F组,原因是D组接头板材变形程度明显大于F组,加工硬化程度更高。利用DEFORM-2D软件对自冲铆接成形过程进行模拟,仿真结果与真实试验误差在15%以内,验证了模型的准确性。
关键词:5182-O铝合金;自冲铆接;力学性能;电子背散射衍射;变形组织
文章编号:1004-0609(2021)-05-1239-14 中图分类号:TG146.2 文献标志码:A
引文格式:毛晓东, 刘庆永, 李 利, 等. 5182-O铝合金板材自冲铆接工艺参数对接头组织和性能的影响[J]. 中国有色金属学报, 2021, 31(5): 1239-1252. DOI: 10.11817/j.ysxb.1004.0609.2021-37816
MAO Xiao-dong, LIU Qing-yong, LI Li, et al. Effect of technologicalparameters on microstructure and properties of self-piercing riveting joints of 5182-O aluminum alloy sheets[J]. The Chinese Journal of Nonferrous Metals, 2021, 31(5): 1239-1252. DOI: 10.11817/j.ysxb.1004.0609.2021-37816
随着汽车工业技术的不断发展,对汽车的经济性提出了更高的要求,这使得汽车制造商更加重视车辆轻量化技术的研究,轻型材料(如铝合金)的应用是减轻车身质量的一种有效方法[1]。然而,许多轻型材料的焊接性能并不理想,甚至无法焊接,给材料的连接工艺带来了巨大挑战[2-3]。因此,板材自冲铆接技术为轻型薄板材料的连接提供了一种解决办法。图1所示为自冲铆接工艺过程示意图[4-5],整个过程分为压紧、冲裁、扩展和冲铆完成四个阶段。
目前自冲铆接技术广泛应用在铝合金、钢铝混合接头的连接,是一种可靠的板材连接技术。针对该技术,国内外研究学者进行了一系列大量研究,主要集中在铆接工艺和接头性能的试验和模拟仿真等方面。MA等[6]通过对不同铆模比组合研究,研究铆钉和模具尺寸对铝合金6061-T6铆接性能的影响;HAN等[7]系统研究了涂层对铝合金与钢板自穿刺铆接接头质量和性能的影响;JEONG等[8]通过对铝合金板材本身强度对自冲铆接强度影响规律研究,表明自冲铆接接头强度随着板材本身强度的提高而明显提高;李晓静等[9]针对自冲铆接技术,研究了不同规格铆钉对不同厚度异种板材连接性能的影响;庄蔚敏等[10]通过对5754铝合金及Q235钢铝异质自冲铆接头的剥离性能研究,并基于MMC失效准则,利用LS-DYNA建立了钢铝异种材料自冲铆接有限元失效模型;邓成江等[11]开展了自冲铆接头失效机理研究,发现接头失效与材料力学性能、材料厚度及摩擦条件有关。
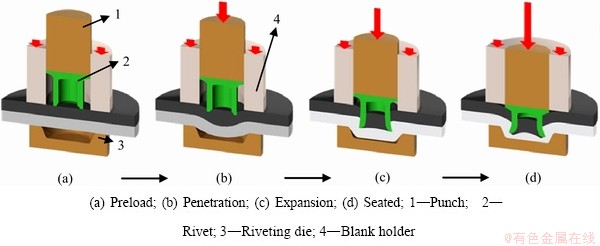
图1 自冲铆接工艺过程示意图
Fig. 1 Diagram of process of self-piercing riveting
随着铝合金材料在车身上的应用越来越广 泛,国内外科研机构及汽车制造商对自冲铆接技术的研究也越来越深入,但对于铆钉参数、底模参数对接头性能的影响规律及铆接过程材料的变形行为研究缺乏,对成形接头缺少相应的质量分析方 法[12-14]。本文以5182-O态1.5 mm厚度的铝合金板材为研究对象,系统开展铆钉长度及底模类型对接头性能影响规律的研究,深入分析冲铆过程母材的变形行为;并采用DEFORM-2D软件,基于不同应变速率下的材料本构模型及Johnson-Cook损伤模型,建立自冲铆接成形仿真模型,并将关键几何参数与真实试验值进行比较,验证模型的准确性,实现自冲铆接成形工艺的仿真预测。
1 实验
1.1 试验材料及铆接方法
试验材料为5182-O铝合金板材,上下板厚度均为1.5 mm,其化学成分及力学性能如表1、2所示。待铆接板材规格为120 mm×40 mm×1.5 mm(厚度),选择德国bollholf公司生产的镀锌钢铆钉,直径为d 5.3 mm,硬度为(41±2)HRC,根据板材厚度,铆钉长度选择5 mm、5.5 mm、6.0 mm以及6.5 mm四种规格;底模选择如图2所示的D和F两种类型。
自冲铆接设备(型号:SWX-DSF2019)采用行程控制,试验中调整冲头行程,保证铆钉压入板材后钉帽与上板材平齐;保压2 s后释放,可保证铆接质量的稳定;铆接速度设置为60 mm/s。
表1 5182-O铝合金化学成分
Table 1 Chemical components of 5182-O aluminum alloy

表2 5182-O铝合金力学性能
Table 2 Mechanical properties of 5182-O aluminum alloy

1.2 组织及性能评价方法
试样铆接完成后,将铆接接头沿铆钉子午面切取样品,经砂纸打磨、机械抛光后用体式显微镜观察接头横断面的宏观形貌,并测量接头的关键几何尺寸,主要有钉脚张开值D、自锁值u、钉头高度h及底厚值s,如图3所示,用于评价接头质量的合格性。
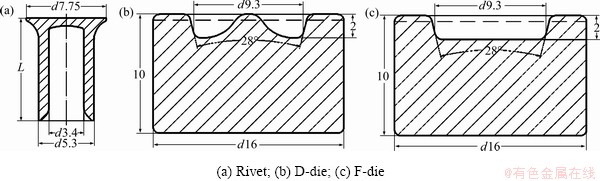
图2 铆钉、底模剖面图
Fig. 2 Cross-section draw of rivet and dies (Unit: mm)

图3 自冲铆接头关键几何尺寸
Fig. 3 Key geometric dimensions of self-piercing riveting

图4 力学性能试样及十字拉伸模具
Fig. 4 Specimen for mechanical properties and die of cross drawing
采用显微维氏硬度仪对接头剖切面不同位置的显微硬度进行测量;采用如图4所示的两种接头试样,分别测试接头的抗剪强度和抗拉强度,测试速度为10 mm/min,记录接头的失效载荷以及最大载荷处的失效位移,用于评价接头的力学性能;采用扫描电子显微镜对接头失效处的断口进行显微观察。将抛光后的接头横断面试样在体积分数为10%的高氯酸无水乙醇溶液中进行电解抛光,抛光液温度0~5 ℃,抛光电压20 V,抛光时间20 s;采用带有电子背散射衍射(EBSD)探头的TESCAN MIR3场发射扫描电子显微镜进行电子背散射衍射试验,测试电压20 kV,标定步长0.9 μm,利用软件HKL Channel 5对采集的数据进行处理。
2 结果与讨论
2.1 截面形貌
图5所示为两种底模作用下不同铆钉长度自冲铆接头横断面宏观形貌,并测量了接头关键几何参数。由图5可以看出,各组接头横断面均呈轴对称分布,未产生开裂、自锁破坏等缺陷。这表明在相同的驱动设备参数参数下,各组接头钉头高度均控制在0.3~0.5 mm之间,钉脚未刺穿下板材,外观质量良好。
图6所示为两种底模接头钉脚张开值D与自锁值u随铆钉长度的变化规律,可以看出,对于D型底模,随着铆钉长度L的增加,钉脚张开值D与自锁值u逐渐增大;当铆钉长度增大到6.5 mm时(见图5(d)),铆钉管脚发生了一定程度的弯曲变形,这是由于铆钉长度过长,铆接过程中在冲头和底模的作用下发生剧烈的挤压作用而发生变形失稳。对于F型底模,随着铆钉长度L的增加,钉脚张开值D逐渐增大,而自锁值u呈先增加后减小的变化;当铆钉长度为6.0 mm(见图5(g))时,自锁值达到最大;继续增加铆钉长度后,自锁值大幅减小,并且铆钉管脚与下板结合处产生了缝隙,表明当铆钉过长时,钉脚的张开未形成有效的机械自锁,降低了接头质量。从图6中还可以发现,两种接头的钉脚张开值D与自锁值u呈明显的正相关,表明铆接过程中钉脚的张开程度对接头质量影响较大。

图5 不同铆钉长度下接头的横断面形貌
Fig. 5 Specimens for mechanical properties and die of cross drawing
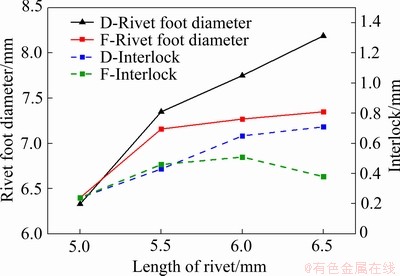
图6 横断面关键几何尺寸
Fig. 6 Key geometric dimensions of all cross sections
2.2 力学性能
自冲铆接接头的力学性能主要涉及最大剪切力、最大抗拉力以及相应条件下的失效吸能值。采用图4所示的力学性能试样对不同参数下的接头力学性能进行测试,进行5组重复试验并取平均值,相应的载荷-位移曲线如图7所示。通过对比可以看出,不同底模的接头在弹性失效阶段表现出显著差异,对于D型底模,在弹性阶段,不同铆钉长度的接头失效曲线接近重合,表明接头自锁质量良好;而对于F型底模,在弹性失效阶段,不同长度的铆钉接头表现出较大差异,随着铆钉长度提高,曲线斜率呈先增大后减小的变化趋势,表明F型底模对钉长因素敏感性较高,当铆钉长度较小时,接头自锁质量较差。
将以上各组接头的失效载荷及失效吸能值进行对比分析,如图8所示。对于两种类型底模接头,接头的剪切失效载荷随着铆钉长度的增加呈先增加后减小的变化规律,当铆钉长度L=6.0 mm时,两组接头剪切失效载荷均达到最大值,分别为6918 N和5425 N;接头的抗拉失效载荷则呈现先提高后趋于稳定的变化规律,当铆钉长度L=6.0 mm时,两组接头抗拉失效载荷达到较高水平,分别为3034 N和2568 N,接头性能较好。从图中还可以看出,D型底模接头的失效载荷与失效吸能值均明显高于F组,说明D型底模有利于提高铆钉张角而形成更好的机械自锁结构,提高接头力学性能。
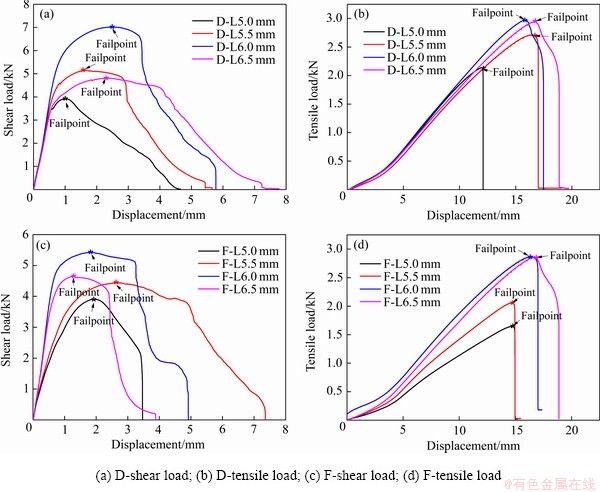
图7 接头载荷-位移曲线
Fig. 7 Load-displacement curves of joints
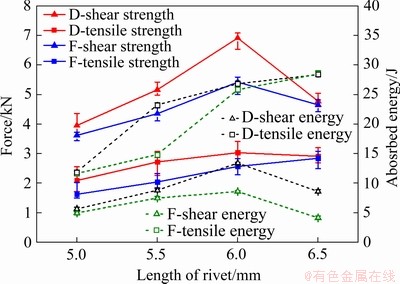
图8 接头力学性能
Fig. 8 Mechanical properties of joints
图9所示为两组底模不同参数下接头的失效形式。结果表明,对于D型底模,当铆钉长度为5.0 mm时,接头的剪切失效为自锁结构破坏,铆钉从下板脱落,上下板未撕裂;接头的抗拉失效表现为铆钉从下板拉出;当铆钉长度提高到5.5 mm时,接头同样发生相同的破坏形式,此时上板材被轻微撕裂;当铆钉长度继续增加到6.0 mm时,剪切接头的破坏发生在上板从钉帽出拉脱撕裂,自锁结构未破坏,抗拉接头同样发生钉帽从上板拉出,下层自锁结构未破坏,说明此时接头成形质量较好,自锁强度较大;当继续增加铆钉长度到6.5 mm时,剪切接头发生组合失效,自锁结构破坏并将下板撕裂,上板发生撕裂破坏,这是由于铆钉过长使得下板剩余厚度较小,在剪切作用下铆钉产生一定程度的翻转将下板剩余厚度撕裂,加速了自锁结构的破坏,使接头强度明显降低。
对于F型底模,接头的失效规律表现出与D型底模相同的变化趋势,随着铆钉长度的提高,接头的失效位置逐渐从接头的机械自锁结构破坏变为钉帽从上板脱落、上板材被撕裂。
2.3 硬度
力学性能研究结果表明,两组底模下,当铆钉规格为d 5.3 mm×6.0 mm时,接头性能均最佳。对两种底模下接头的母材硬度进行测试,测试位置如图10所示。结果显示,接头处上下板材硬度大致呈“M”型分布,且以铆钉中轴线呈轴对称分布。原始板材硬度约为75HV,铆接过程中接头处板材由于变形产生了不同程度的加工硬化。在铆钉临近位置(上板:±2、±3;下板:±3、±4)硬度值最大,最高可达139HV;这是由于板材在铆钉刺穿过程中受到剧烈的剪切作用而产生应变硬化。从图10中还可以明显看出,在铆钉管脚内部,D型底模接头的上下板硬度明显高于F型,这是由于铆接过程中受D型底模凸锥的挤压作用,滞留在管脚内部的母材受到强烈的挤压作用而产生形变硬化,使硬度值明显上升。

图9 接头失效形式
Fig. 9 Failure mode of joints

图10 硬度测试位置示意图
Fig. 10 Schematic diagram of hardness test locations
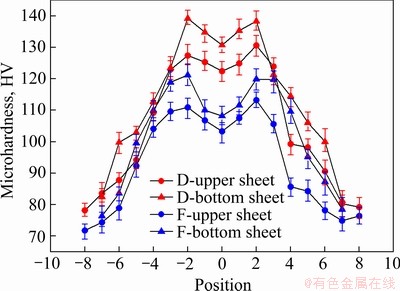
图11 接头的硬度值
Fig. 11 Hardness values of joints
2.4 显微组织
自冲铆接工艺在铆钉刺穿上板材并与下板形成自锁结构的过程中,与铆钉附近位置的板材发生剧烈的剪切作用,同时承受底模的挤压作用,导致接头处板材的力学性能和组织发生变化。选择铆钉规格为d 5.3 mm×6.0 mm、D和F两种底模接头,对上下板材不同位置进行EBSD测试,选择接头处典型的六个位置进行组织观察,分别是:上板铆钉外侧区(Ⅰ1)、上板铆钉内侧区(Ⅰ2)、上板铆钉中间区(Ⅰ3);下板铆钉外侧区(Ⅱ1)、下板铆钉内侧区(Ⅱ2)和下板铆钉中间区(Ⅱ3),如图12所示。
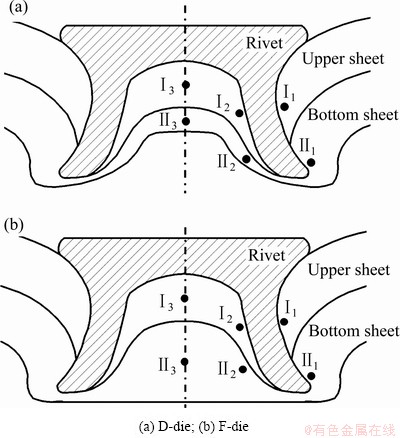
图12 显微组织测试位置示意图
Fig. 12 Schematic diagrams of testing positions for microstructure
图13(a)所示为5182-O原始板材晶粒取向分布图,图中黑色细线代表低角度晶界(Low angle grain boundaries,LAGBs,2°~15°),黑色粗线代表高角度晶界(High angle grain boundaries,HAGBs,>15°)。可以看出,5182-O原始板材为完全再结晶组织,晶粒成等轴状分布,晶粒大小约20~30 μm。从图13(b)中的{111}极图可以看出,原始母材主要为{001}
Cube再结晶织构。由晶界统计分布图13(c)可以看出,组织中主要为高角度再结晶晶界,HAGBs约为89.2%,LAGBs约为10.8%。
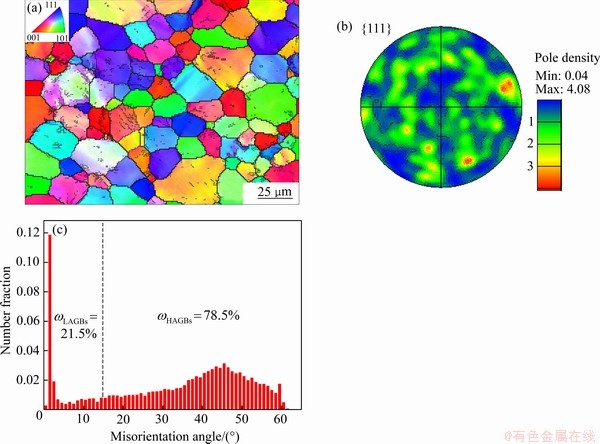
图13 原始母材晶粒取向分布图、{111}极图及晶界统计分布图
Fig. 13 Orientation distribution map (a), {111} pole figure (b) and misorientation angle distributions of initial sheet (c)
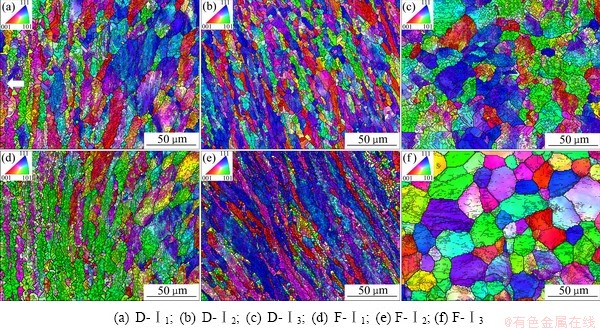
图14 上板变形区晶粒取向分布图
Fig. 14 Orientation distribution maps in deformation zones of upper sheets
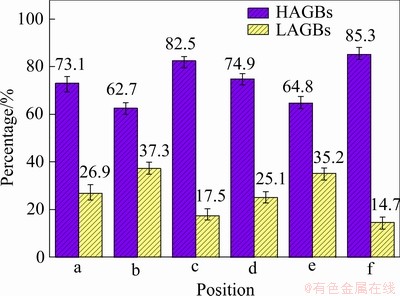
图15 上板变形区晶界比例图
Fig. 15 Grain boundaries ratio statistical chart in deformation zones of upper sheets
图14所示为两组底模接头上板铆接变形区组织形貌。从晶粒取向分布图可以明显看出,相比于母材,剪切变形区(见图14(a)和(b)、(d)和(e))组织由最初的等轴晶变为细长的变形组织,晶粒拉长、破碎,且越接近铆钉侧,晶粒越细长。两组底模下铆钉中心位置(见图14(c)和(f))主要受不同程度的垂直压力而发生一定程度的变形,D型底模由于凸锥的作用导致上板压缩变形程度较大,晶粒更扁平;从晶粒取向分布图中还可以看出,两组接头变形区晶粒内部出现了大量低角度晶界。将上板变形区不同位置高低角度晶界比例进行统计,如图15所示。结果表明,两组接头的Ⅰ2区ω(LAGBs)比例最大,分别达到了37.3%和35.2%,Ⅰ1次之,Ⅰ3最小,表明Ⅰ2区板材受铆钉剪切以及内腔挤压的双重作用,晶粒内部产生大量的位错和亚结构(见图14中黑色细线),使得ω(LAGBs)显著提高[15-18];而Ⅰ1区主要受铆钉的剪切作用,产生的位错和亚结构较少,晶粒也相对粗大;Ⅰ3区板材在铆接过程中主要受下板与铆钉内腔的挤压作用而发生轻微变形,晶粒未发生破碎,只在晶粒内部产生了亚结构,ω(LAGBs)较原始板材有少量提高;对比两组底模下的Ⅰ3区(见图14(c)和(f)),可以明显看出,由于D型底模凸锥的挤压作用,上板Ⅰ3区产生较大变形,产生的位错和亚结构显著增多,相比F型底模产生了较大的形变硬化作用。
图16所示为两组底模接头下板材变形位置晶粒取向分布图。在铆钉外侧剪切变形区Ⅱ1(见图16(a)和(d)),下板材组织沿铆接变形方向被轻微拉长,晶粒内部出现大量低角度晶界;在铆钉内侧剪切变形区Ⅱ2,板材受铆钉钉脚的剪切和内腔的挤压作用,晶粒显著拉长,并产生破碎;而在铆钉中心位置Ⅱ3区,下板材在铆接过程受到底模的挤压作用而变形,晶粒内部产生了大量亚结构。由图17晶界种类统计图中可以发现,变形区不同位置低角度晶界百分比相对原始板材均有不同程度的提高,且随着变形程度的提高,低角度晶界百分比呈逐渐提高的趋势,这是由于铆接过程的剪切应变和底模的挤压作用,晶粒发生了变形、拉长甚至破碎,产生了位错和亚结构,导致低角度晶界百分含量提高。
3 5182-O自冲铆接成形有限元分析
自冲铆接成形模型涉及板材、铆钉、冲头、压边圈与底模等,建立如图18(a)所示的3D几何模型,并基于自冲铆接工艺的对称性,利用DEFORM软件建立5182-O铝合金板材自冲铆接成形1/2对称2D模型,如图18(b)所示。根据上述研究结果,对于5182-O板材1.5 mm+1.5 mm厚度组合接头,采用d 5.3 mm×6.0 mm规格铆钉,在两种底模作用下的铆接成形过程进行仿真分析,研究其变形过程,并与真实试验结果进行对比,验证模型的准确性。

图16 下板变形区晶粒取向分布图
Fig. 16 Orientation distribution maps in deformation zones of bottom sheets
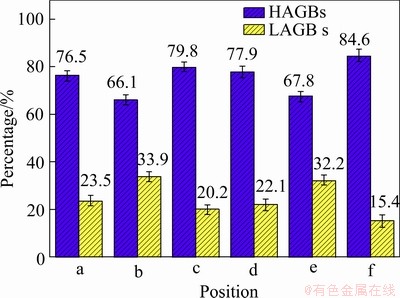
图17 下板变形区晶界比例图
Fig. 17 Grain boundaries ratio statistical chart in deformation zones of bottom sheets
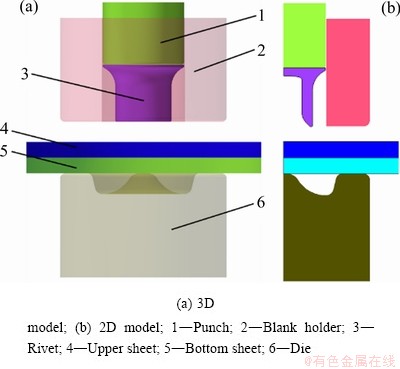
图18 自冲铆接几何模型
Fig. 18 Geometric model of self-piercing riveting
3.1 材料本构关系
依据国家标准《GBT 228—2002 金属材料室温拉伸试验方法》,对5182-O板材进行不同速度单向拉伸试验,获得材料基于不同加载速率下多应变率水平的力学特性,确定5182-O在不同应变速率下的本构模型。试验结果如图19所示。结果表明,5182-O板材应变率效应不明显,在真应变在0.1以下阶段,不同应变速率下的硬化曲线相近;随着应变速率的提高下,材料的断后伸长率明显提高。
3.2 材料损伤模型
在实际工程中,材料的受力情况通常比较复杂,变形常常不只是简单的拉、压、扭转等基本变形。而是两种或两种以上基本变形的组合,其应力状态为复杂应力状态。
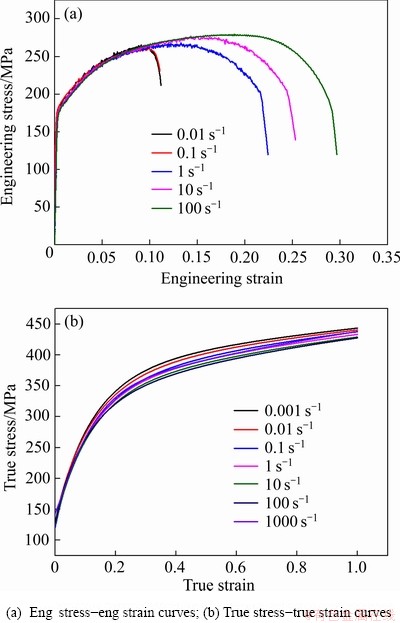
图19 5182-O应力-应变曲线
Fig. 19 Stress-strain curves of 5182-O sheet
材料所受应力状态不同时,材料内产生的塑性变形及应力集中程度将不同,材料断裂机理也将发生变化,通常以应力三轴度(Stress triaxiality)η作为复杂应力状态参数,即静水压力p与Mises等效应力q比值的负数,见式(1)。
(1)
Johnson-Cook损伤模型是以应变为标准的失效准则[19-20],但该模型的失效应变除了是应力三轴度、应变率的函数,也是温度的函数,由特定的公式表达,参见式(2)。其中d1、d2和d3是考虑了失效应变受应力三轴度影响的参数;d4为考虑了失效应变受应变率影响的参数;d5则是考虑了失效应变受温度变化影响的参数。其中d3与原公式有所不同,带有一个负号,主要是考虑到大多数材料的失效应变伴随着应力三轴度的增长而降低。自冲铆接过程可视为温度恒定,并且采用准静态拉伸,d4与d5均为0,因此公式可简化为式(3)的形式。
(2)
(3)
3.3 失效参数的确定
采用准静态穿孔、缺口等试验获得5182-O铝合金板材在不同应力状态下的力学性能及失效参数,如图20所示。通过仿真模拟结果与试验结果进行验证,两者吻合良好,如图21所示。
3.4 结果分析
图22所示为两种底模作用下板材的应变结果。可以发现,对于D型底模,在铆接过程中收到凸台的挤压作用而使铆钉内下板材发生剧烈变形,产生较大塑性应变,为变形最大位置;而对于F型底模,板材的最大应变点发生在上板切断位置。
对铆接成形后的接头,测量钉脚直径(D)、自锁量(u)以及底部厚度(s),并与实际接头进行对比,如表3所示。结果表明,对于D型底模,钉脚直径D、自锁量u以及底部厚度s的模拟值与实际值之间的误差分别为14.2%、4.9%和5.7%;F型底模,钉脚直径D、自锁量u以及底部厚度s的模拟值与实际值之间的误差分别为2.4%、10.9%和8.0%,模拟结果与试验值之间的相对误差均在15%以内,满足工程设计精确度要求。
两种底模模拟接头的关键几何参数与实际接头接近,误差均控制在15%以内,从而验证了仿真结果的正确性与可靠性,其对铆接工艺选择及铆钉、底模的选择设计具有重要的指导意义。

图20 穿孔、缺口试样几何尺寸
Fig. 20 Geometric dimensions of perforated (a) and notched (b) specimens (Unit: mm)

图21 5182-O板材失效模型
Fig. 21 Failure models of 5182-Osheet
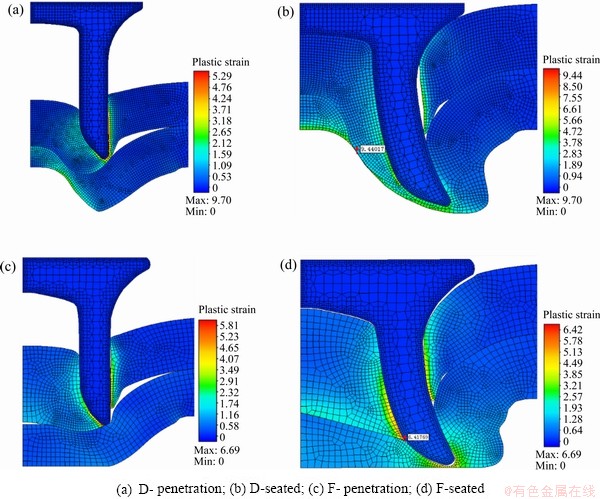
图22 两种底模下5182-O板材自冲铆接过程应变云图
Fig. 22 Strain contours of 5182-O sheet under two kinds of bottom dies during self-piercing riveting process
表3 模拟与实际对比
Table3 Comparison of simulated and actual results

4 结论
1) 对5182-O态1.5 mm+1.5 mm板材接头组合,随着铆钉长度的增加,接头的强度及吸能呈先提高后降低的变化趋势;当铆钉长度为6.0 mm时,接头强度及吸能最佳;接头的失效方式逐渐从机械自锁结构破坏变为钉帽从上板脱落、上板材被撕裂;在相同铆钉长度下,D型底模接头的钉脚张开值及自锁值较F组大,有利于提高接头的强度及吸量。
2) 铆接接头变形区上下板硬度大致呈“M”型分布,越靠近铆钉位置,剪切作用越强烈,硬度值较原始板材显著提高,最大可达139HV;D型底模由于凸锥的挤压作用,铆钉内部变形区板材硬度显著高于F型底模,有利于提高强度及吸量。
3) 铆接接头变形区上下板材受到铆钉强烈的剪切作用,板材组织由最初的等轴晶变为细长的变形组织,晶粒发生拉长、破碎,产生不同程度的位错和亚结构,使得低角度晶界比例提高;D型底模铆钉内部挤压变形区板材的低角度晶界比例明显大于F组,加工硬化程度更高。
4) 采用拉伸及缺口试验获得了5182-O态铝合金板材的本构模型及失效参数,并基于Johnson- Cook损伤模型成功建立了两种底模下的自冲铆接成形模型,接头关键几何参数与真实试验误差在15%以内,从而验证了模型的准确性,为实际工艺选择提供理论支撑。
REFERENCES
[1] 高 阳. 汽车轻量化技术方案及应用实例[J]. 汽车工程学报, 2018, 8(1): 1-9.
GAO Yang. Technical schemes and implementation examples of automobile lightweight[J]. Journal of Automotive Engineering, 2018, 8(1): 1-9.
[2] 李 报, 陈思杰, 赵丕峰. 汽车轻量化先进焊接技术研究进展[J]. 热加工工艺, 2018, 47(3): 13-17, 22.
LI Bao, CHEN Si-jie, ZHAO Pi-feng. Research progress of advanced welding technology for automobile lightweight[J]. Hot Working Technology, 2018, 47(3): 13-17, 22.
[3] 陈晓辉, 钟志平, 陆 辛. 车用铝合金连接技术的研究进展与应用[J]. 热加工工艺, 2016, 45(11): 5-8.
CHEN Xiao-hui, ZHONG Zhi-ping, LU Xin. Research progress and application of joining technology of aluminum alloy for automobile[J]. Hot Working Technology, 2016, 45(11): 5-8.
[4] HUANG H, DU D, CHANG B H, et al. Distortion analysis for self-piercing riveting of aluminium alloy sheets[J]. Science and Technology of Welding & Joining, 2007, 12(1): 73-78.
[5] 万淑敏, HU S Jack, 李双义, 等. 半空心自冲铆接的工艺参数及铆接质量判定[J]. 天津大学学报, 2007, 40(4): 494-498.
WAN Shu-min, HU S Jack, LI Shuang-yi, et al. Process parameters and joint evaluation of self-piercing riveting with half-hollow rivets[J]. Journal of Tianjin University, 2007, 40(4): 494-498.
[6] MA Y W, LOU M, LI Y B, et al. Effect of rivet and die on self-piercing rivetability of AA6061-T6 and mild steel CR4 of different gauges[J]. Journal of Materials Processing Technology, 2018, 251: 282-294.
[7] HAN L, CHRYSANTHOU A. Evaluation of quality and behaviour of self-piercing riveted aluminium to high strength low alloy sheets with different surface coatings[J]. Materials & Design, 2008, 29(2): 458-468.
[8] JEONG T, KIM M, HUN R, et al. Joint quality study of self-piercing riveted aluminum and steel joints depending on the thickness and strength of base metal[J]. Journal of Welding and Joining, 2019, 37(3): 212-219.
[9] 李晓静, 李双义, 张连洪, 等. 自冲铆接工艺的研究及改进措施[J]. 天津理工大学学报, 2005, 21(5): 61-64.
LI Xiao-jing, LI Shuang-yi, ZHANG Lian-hong, et al. Study of technology of self-piercing riveting and improved approach[J]. Journal of Tianjin University of Technology, 2005, 21(5): 61-64
[10] 庄蔚敏, 刘 洋, 王鹏跃, 等. 钢铝异质自冲铆接头剥离失效仿真[J]. 吉林大学学报(工学版), 2019, 49(6): 1826-1835.
ZHUANG Wei-min, LIU Yang, WANG Peng-yue, et al. Simulation on peeling failure of self-piercing riveted joints in steel and aluminum alloy dissimilar sheets[J]. Journal of Jilin University(Engineering and Technology Edition), 2019, 49(6): 1826-1835.
[11] 邓成江, 何晓聪, 邢保英, 等. 基于试验的自冲铆接头失效机理分析[J]. 热加工工艺, 2013, 42(17): 220-223.
DENG Cheng-jiang, HE Xiao-cong, XING Bao-ying, et al. Analysis on failure mechanism of self-piercing riveted joints based on tests[J]. Hot Working Technology, 2013, 42(17): 220-223.
[12] 万淑敏, 胡仕新, 张连洪, 等. 模具工艺参数对自冲铆接工艺过程及铆接质量的影响[J]. 机械设计, 2008, 25(4): 62-65.
WAN Shu-min, HU Shi-xin, ZHANG Lian-hong, et al. Influence of die process parameters on the process and quality of self-piercing riveting[J]. Journal of Machine Design, 2008, 25(4): 62-65.
[13] 黄舒彦. 铝钢异种金属自冲铆接工艺与质量评价研究[D]. 上海: 上海交通大学, 2011.
HUANG Shu-yan. Process and quality evaluation research on self-piercing riveting for dissimilar metal aluminum/steel[D]. Shanghai: Shanghai Jiao Tong University, 2011.
[14] HOANG N H, LANGSETH M. Aluminium self-piercing rivet's failure: Testing and numerical analyses[J]. Applied Mechanics & Materials, 2014, 541/542: 1355-1359.
[15] 茹祥坤, 刘延光, 夏 爽, 等. 形变及热处理对白铜B10合金晶界特征分布的影响[J]. 中国有色金属学报, 2013, 23(8): 2176-2181.
RU Xiang-kun, LIU Yan-guang, XIA Shuang, et al. Effect of deformation and heat-treatment on grain boundary distribution character of cupronickel B10 alloy[J]. The Chinese Journal of Nonferrous Metals, 2013, 23(8): 2176-2181.
[16] 廖荣跃, 叶凌英, 陈明安, 等. 7B04铝合金超塑性变形的组织演变与变形机理[J]. 中南大学学报(自然科学版), 2018, 49(12): 2931-2938.
LIAO Rong-yue, YE Ling-ying, CHEN Ming-an, et al. Microstructure evolution and deformation mechanism of 7B04 aluminum alloy under superplastic deformation[J]. Journal of Central South University(Science and Technology), 2018, 49(12): 2931-2938.
[17] XIA Shuang, ZHOU Bang-xin, CHEN Wen-jue. Grain cluster microstructure and grain boundary character distribution in alloy 690[J]. Metallurgical and Materials Transactions A, 2009, 40(12): 3016.
[18] 张成行, 曹 宇, 曹玲飞, 等. 异种铝合金搅拌摩擦焊接头的显微组织、力学及腐蚀性能[J]. 中国有色金属学报, 2019, 29(10): 2255-2265.
ZHANG Cheng-hang, CAO Yu, CAO Ling-fei, et al. Microstructure, mechanical and corrosion properties of dissimilar friction stir welded aluminum alloys joints[J]. The Chinese Journal of Nonferrous Metals, 2019, 29(10): 2255-2265.
[19] 季玉辉. 基于Johnson-Cook模型的硬物损伤数值模拟研究[D]. 南京: 南京航空航天大学, 2009.
JI Yu-hui. Numerical simulation of hard-body foreign object damage based on Johnson-Cook model[D]. Nanjing: Nanjing University of Aeronautics and Astronautics, 2009.
[20] 朱 浩. 车用铝合金变形损伤和断裂机理研究与材料表征及有限元模拟[D]. 兰州: 兰州理工大学, 2008.
ZHU Hao. Study on deformation damage and fracture mechanism and materials characterization for alumimum automotive with FEM simulation[D]. Lanzhou University of Technology, 2008.
Effects of technological parameters on microstructure and properties of self-piercing riveting joints of 5182-O aluminum alloy sheets
MAO Xiao-dong, LIU Qing-yong, LI Li, GU Ning-jie, YANG Hao, FU Lei, ZHAO Pi-zhi
(CHINALCO Materials and Application Research Institute, Beijing 102209, China)
Abstract: Under the actions of D-die and F-die, four lengths of rivets (5.0 mm, 5.5 mm, 6.0 mm and 6.5 mm) were used to conduct self-piercing riveting tests on the joints of 1.5 mm+1.5 mm 5182-O aluminum alloy plates. The key characteristic values were measured on the profiles of the joints. The microstructure and mechanical properties of the joints were studied by using EBSD, hardness tests and tensile tests. Based on the constitutive models of 5182-O plates under different strain rates and the Johnson-Cook damage model, the forming process of self-piercing riveting was established and the simulation results were compared with the experimental results for verification. The results show that the mechanical properties of the joints increase firstly and then decrease with the increase of rivet length. When the length is 6.0mm, the mechanical properties of the joints are optimum. Under the same length of rivet, the mechanical properties of joints in group D are significantly higher than those in group F. The degree of deformation in group D is obviously higher than that in group F, resulting in higher work-hardening capacity. Software DEFORM-2D was adopted to establish the forming model of self-piercing riveting. The simulation results show an error of less than 15%, compared with the results by experiment, which verifies the accuracy of the model.
Key words: 5182-O aluminum alloy; self-piercing riveting; mechanical properties; EBSD; deformation microstructure
Foundation item: Project(TC180A6MR) supported by the National New Material Production and Application Demonstration Platform of China
Received date: 2020-07-22; Accepted date: 2020-12-04
Corresponding author: MAO Xiao-dong; Tel: +86-10-66600113; E-mail: Maoxiaodong@cmari.com
(编辑 何学锋)
基金项目:国家新材料生产应用示范平台资助项目(TC180A6MR)
收稿日期:2020-07-22;修订日期:2020-12-04
通信作者:毛晓东,工程师,硕士;电话:010-66600113;E-mail:Maoxiaodong@cmari.com