J. Cent. South Univ. (2016) 23: 1839-1846
DOI: 10.1007/s11771-016-3238-2

Correlation between microstructural features and tensile strength for friction welded joints of AA-7005 aluminum alloy
Seyyed Mostafa Tahsini1, Ayyub Halvaee1, Hamed Khosravi2
1. School of Metallurgy and Materials Engineering, College of Engineering, University of Tehran, Tehran, Iran;
2. Department of Materials Engineering, Faculty of Engineering, University of Sistan and Baluchestan, Zahedan, Iran
Central South University Press and Springer-Verlag Berlin Heidelberg 2016
Abstract: Similar friction welded joints of AA-7005 aluminum rods were fabricated using different combinations of process parameters such as friction pressure (1.0, 1.5 and 2.0 MPa) and friction time (10, 15 and 20 s). Interfacial microstructure and formation of intermetallic compounds at the joint interface were evaluated via scanning electron microscopy (SEM) equipped with energy dispersive spectrum (EDS), and optical microscopy (OM). Microstructural observations reveal the formation of intermetallic phases during the welding process which cannot be extruded from the interface. Theses phases influence the tensile strength of the resultant joints. From the tensile characteristics viewpoint, the greatest tensile strength value of 365 MPa is obtained at 1.5 MPa and 15 s. Finally, the role of microstructural features on tensile strength of resultant joints is discussed.
Key words: friction welding; AA-7005 aluminum alloy; microstructure; intermetallics; tensile strength
1 Introduction
Highly alloyed 7XXX series of aluminum alloys are wieldy used in aerospace structures where some properties such as lightness, specific stiffness and high specific strength are very critical factors [1]. However, joining and welding of these alloys are very difficult via fusion welding processes [2]. The main drawback associated with the fusion welding of 7XXX aluminum alloys is their high susceptibility to weld solidification cracking [3]. Friction welding (FW) is a promising candidate for welding and joining of these alloys. This process is a solid phase pressure welding technique where no actual melting of the parent metals occurs. Rubbing the two faces of pieces being welded (a moving workpiece and a stationary component) to each other creates sufficient frictional heat at the interface between them. As soon as the joining surfaces are sufficiently plasticized by the frictional heat, the relative motion is stopped and the pressure on the stationary component is increased until the joining established. During the welding process, surface oxides and contaminates are eliminated from the surfaces of workpieces (called as flash process), providing a suitable condition for an efficient bonding between the atoms. On the other hand, no surface cleaning stage is needed prior to welding in this method. Moreover, this process prevents from forming of porosity, shrinkage and thermal stresses which are observable in fusion methods [4-5].
Although FW is considered as a solid state welding technique, in some conditions, it is possible to form a thin molten film on the joint surface causing segregation of alloying elements in heat affected zone (HAZ). Microstructural characteristics often determine the final properties of resultant welds. Therefore, process parameters such as frictional time, frictional pressure, rotational speed, forging time and forging pressure have a profound influence on the final mechanical properties of the joints [3, 6-9].
Some studies have been conducted on the friction welding of various engineering alloys. For instance, OZDEMIR et al [10] investigated the effect of rotational speed on the interface properties of friction welded joints between AISI 304l and 4340 steels and reported that the tensile strength of joints increased by increasing the rotational speed. SAHIN [11] investigated the effect of friction time and friction pressure on the microstructural properties and welding strengths of the joints using AISI 304 parts. KALUC and TABAN [12] jointed a medium C45 (AISI 1040) carbon steel and powder metallurgically produced tool steel 1.3344PM (AISI M3:2) using friction welding. CHANDER et al [13] studied continuous drive friction welding of austenitic AISI 304 and AISI 4140 steels. They reported that tensile strength and impact toughness increased by increasing the rotational speed up to 1500 r/min and decreased afterwards. FAUZI et al [14] investigated the microstructure and mechanical properties of alumina-6061 aluminum alloy joined by friction welding and observed that rotational speed of 2500 r/min can produce a very good joint and microhardness as compared to the other experimental rotational speeds. The microstructure and mechanical properties of rotary friction welded titanium alloys studied by AVINASH et al [15].
To the best of our knowledge, no research work has been reported on the friction welding of AA-7005 aluminum alloys. This work has attempted to experimentally describe the microstructural characteristics and tensile strength of similar friction welded joints of AA-7005 aluminum alloys. The aims of the present study are to investigate (1) the friction weldability of AA-7005 aluminum alloys and (2) influence of varying process parameters (friction time and friction pressure) on microstructure and tensile strength of the friction welded joints of this alloy.
2 Experimental
AA-7005 aluminum alloy rods with diameter of 20 mm were used in this work. The chemical composition of this alloy is listed in Table 1. The geometry and dimensions of the parts used in the friction welding experiments are shown in Fig. 1.
A friction welding set-up was designed based on the continuous drive welding machines. The rotating workpiece is driven by a 3.5 kW electric motor having a maximum rotational speed of 3600 r/min. The rotational speed of the electric motor was varied and controlled by an inverter. The time was recorded by a chronometer and pressure was measured by an analog pressure gauge.
The friction welding parameters are listed in Table 2. In the present research, rotational speed, forging pressure and forging time were kept constant and various friction time and friction pressures were employed.
To study the microstructure in the welded zone, samples were sectioned from the friction welded joints transverse to the welding direction. These samples were subjected to standard metallographic procedures, and etched in Keller’s etching reagent (2 mL HF, 3 mL HCl, 5 mL HNO3, and 90 mL H2O) for 15 s. Microstructural investigations were carried out using Camscan MV2300 scanning electron microscope (SEM) equipped with an energy dispersive spectrometer (EDS), and Olympus- BH2UMA optical microscope (OM). The average grain size in different regions was obtained using image analyzer software.
Table 1 Chemical composition of AA-7005 aluminum alloy (mass fraction, %)

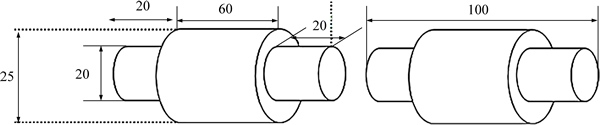
Fig. 1 Geometry and dimensions of parts used for friction welding (Unit: mm)
Table 2 Friction welding process parameters
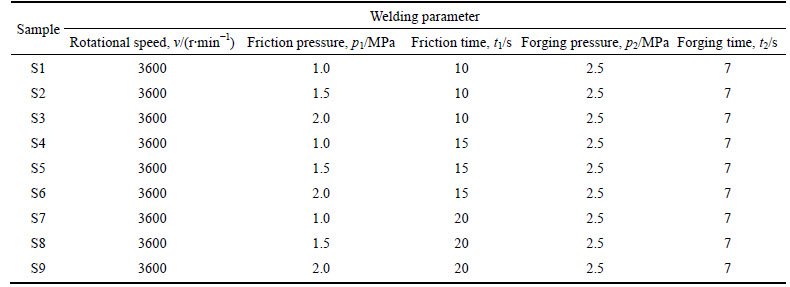
Tensile samples in triplicate with the dimensions shown in Fig. 2 were machined perpendicular to the welding direction (according to ASTM E 8 M) and exposed to tensile test on a universal testing machine (Zwick/Roell Z100). Tensile test was carried out at room temperature with a constant crosshead speed of 3 mm/min.
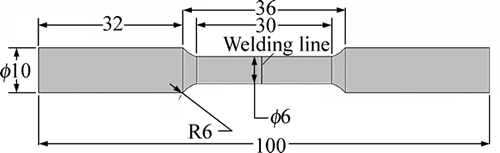
Fig. 2 Position and dimensions of tensile sample (Unit: mm)
3 Results and discussion
OM micrographs of AA-7005 aluminum alloy at two different magnifications are shown in Figs. 3(a) and (b). Figure 3(c) illustrates the XRD pattern of this alloy. The starting alloy has coarse grain with the mean size of 125 μm. From the XRD pattern, different phases of α-Al solid solution, Mg2Si, θ(CuAl2), MgZn2, and Al2CuMg are detected in the microstructure of AA-7005 aluminum alloy.
The macrographic image of friction welded joint, presented in Fig. 4, shows a considerable amount of surface flash, indicating the adequate generation of frictional heat together with explosion of oxide scales and other contaminants in the joint region. In FW process, heat dissipation on the stationary side is not as effective as on the rotating side. For this reason, more extensive plastic deformation could occur on the stationary side, leading to a larger amount of flash formation.
The optical microstructure for the friction welded joint produced at 1.5 MPa-15 s (sample S5) is shown in Fig. 5. Regarding to this figure, the microstructure can be broken up into three main regions: (1) dynamically recrystallized (DRX) zone, where the material is able to accommodate the plastic strain through dynamic recovery of the microstructure, (2) thermo-mechanically affected zone (TMAZ), where the degree of plastic deformation is mainly accommodated by an increase in the dislocation density of the matrix grains to a certain value, and (3) heat affected zone (HAZ) or undeformed zone (UDZ), characterized by a partial reversion of the precipitates present in the base metal matrix. The joint microstructures generated by employing other FW parameters are similar to the one shown in Fig. 5.Figure 6 shows the microstructure of the joint for sample S5 at a higher magnification, revealing the presence of coarser grains in the stationary side. In FW process, the base material is exposed to heavy plastic deformation at high temperatures close to its melting point [16]. In vicinity of joining region, the temperature cycle is different for the stationary and rotating samples. Because the rotating sample loses its heat continually through convection currents, it experiences a higher cooling rate leading to the formation of finer grains in the rotating side.
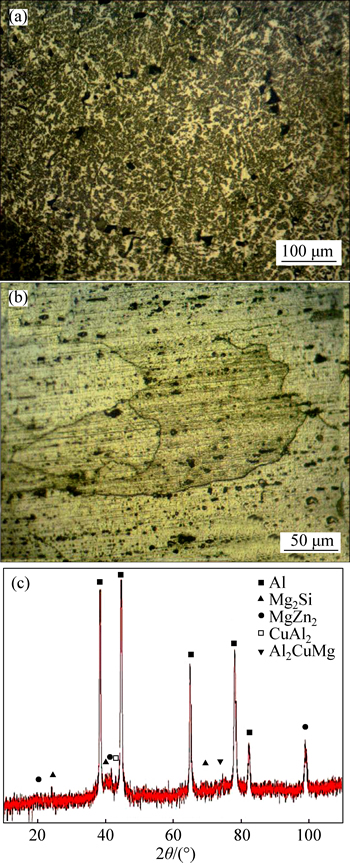
Fig. 3 OM micrographs of AA-7005 aluminum alloy at low magnification (a), high magnification (b), and XRD pattern of this alloy (c)
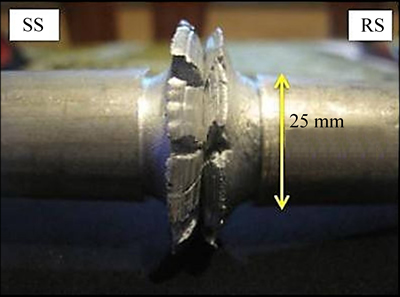
Fig. 4 Macrographic image of friction welded joint for sample S5 (SS-stationary side, RS-rotating side)
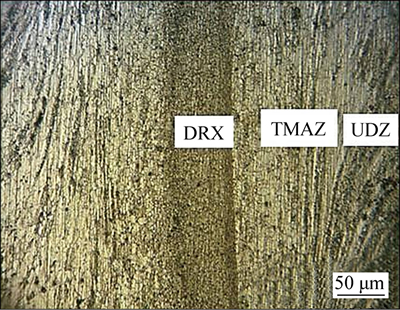
Fig. 5 OM micrograph from joint region of sample S5
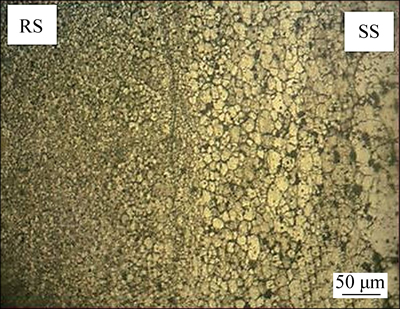
Fig. 6 OM micrograph from joint region of sample S5 at a higher magnification
OM micrographs taken from different regions of friction welded joint produced at 1.5 MPa-15 s are depicted in Fig. 7. At different regions of DRX, TMAZ and UDZ, indicated in Fig. 7, the grain sizes are 6.9, 4.1 and 11.3 μm, respectively. Based on the results, finer grain structures are observed in the TMAZ and DRX regions compared to the UDZ region. Also, the DRX region consists of coarser grains when compared to the TMAZ region. The formation of finer equiaxed grains in the TMAZ and DRX regions is due to the combination of severe plastic deformation and high frictional heating which promotes dynamic recrystallization in these regions [17]. However, in the DRX region, full dynamic recrystallization together with subsequent grain growth occurs. It should be mentioned that after the welding process, no coarse grains are observable in the DRX region; however, the size of the new grains formed in this region is a little larger than the newly formed grain size in the TMAZ. The presence of coarser grains in the UDZ compared to other regions is mainly related to the heat conduction from interface toward the base metal leading to the grain growth in this region.
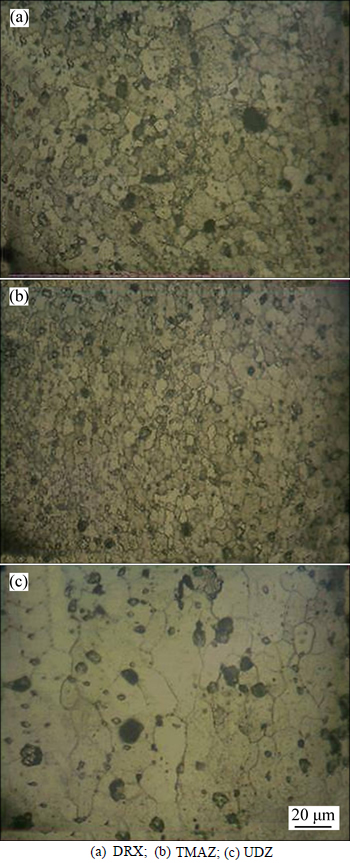
Fig. 7 OM micrographs from different regions of friction welded joint for sample S5 at stationary side:
The average results of tensile strength measurement in transverse orientation of friction welded joints are given in Table 3. Compared to the starting material with average tensile strength of 393 MPa, for all of the samples, reduction in the joint tensile strength is observed. The observed decrease can be attributed to the coarsening and dissolution of the strengthening precipitates during the weld thermal cycle [18]. It is evident from Table 3 that the joint tensile strength is significantly affected by varying the friction time and friction pressure. At a fixed friction pressure, by increasing the friction time from 10 to 20 s, joint tensile strength is firstly increased and then declined. On the other hand, at a fixed friction time, when the friction pressure is increased from 1.0 to 2.0 MPa, joint tensile strength is also firstly increased and afterwards decreased.The joint fabricated using a combination of friction pressure of 1.5 MPa and friction time of 15 s (sample S5) exhibits a higher tensile strength compared to the other joints. For this sample, tensile strength of the joint is obtained of 365 MPa. Joint produced under this condition gets a tensile strength of 92.9% of that of base metal. Simultaneous increase in the friction time and friction pressure from 10 s-1.0 MPa to 15 s-1.5 MPa leads to the increase of joint tensile strength by 13%. When the both of friction time and friction pressure are short (i.e. 10 s and 1.0 MPa), due to nonsufficient temperature and plastic deformation, unbounded regions could result. Figure 8 shows the presence of discontinuity in transverse cross section of joint for sample S1. As it can be seen in this figure, the observed defect has been created in the center of the joint and junction in other regions has completely formed. This means that during the FW process, the center of joint experiences a lower temperature than other regions.
Table 3 Results of tensile test
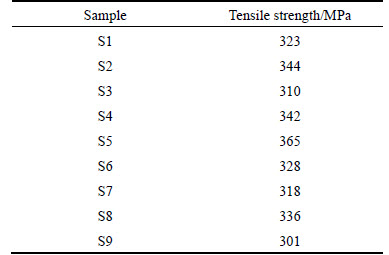
SEM image taken from the fracture surface of sample S1 is given in Fig. 9(a), while Fig. 9(b) represents the EDS pattern of the particles present in the joint microstructure of this sample. It seems that these inclusions are formed during the friction applying and could not get out from the interface when forging pressure has been applied. According to the results obtained by XRD (Fig. 10), intermetallic phases such as FeAl2 and MgSiO4 exist in the fracture surface of sample S1. These brittle compounds prevent perfect joining of two surfaces to be jointed.
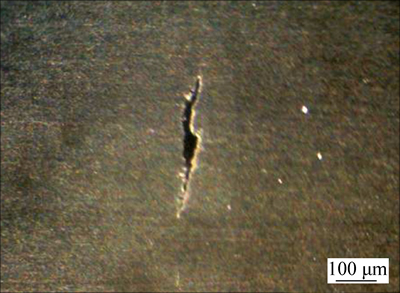
Fig. 8 Presence of discontinuity in transverse cross section of joint for sample S1
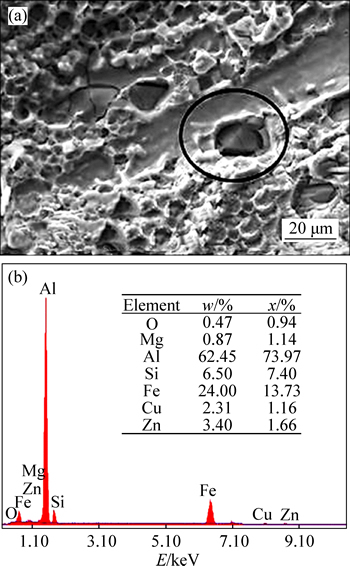
Fig. 9 SEM image from fracture surface of sample S1 (a) and EDS pattern from marked region (b)
On the other hand, if the friction time and friction pressure are simultaneously held high (i.e. 20 s and 2.0 MPa), localized fusion may occur in the joint region and also a broad HAZ with coarser grains is formed as a result of increased temperature in this region.Figures 11(a) and (b) represent SEM photographs of the joint region in sample S9, revealing the accumulation of particles at the end of TMAZ. The EDS pattern of these particles is shown in Fig. 11(c). Also, it can be seen that the joint region is not uniform due to the extreme deformation in this sample. The high temperature created in the interface region of this sample causes the localized fusion. This implies that segregation and accumulation of alloying elements as intermetallic phases takes place in the interface during solidification stage, which will lead to an increased probability in the formation of weak regions and consequently poor joint tensile strength is obtained.
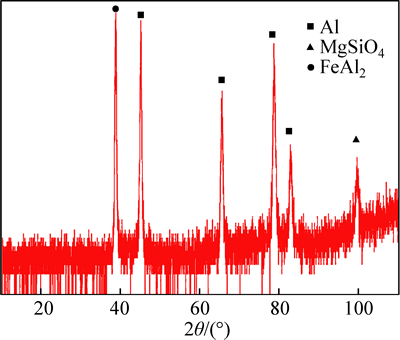
Fig. 10 XRD pattern from fracture surface of sample S1
Figure 12 illustrates the SEM images of joint interface for sample S5 with the highest joint tensile strength. From this figure, it can be seen that the joining in this sample is free from defects and a perfect joint has been obtained. Regarding to Fig. 12(b), nearly uniform distribution of white phases in the matrix is observable. An EDS analysis was carried out in order to evaluate these phases that formed in the welded joint. The EDS pattern taken from the white phase (Fig. 13) shows the formation of aggregation of compounds of Si, Al, and Fe.
Figure 14 shows the SEM observations from the tensile fracture surface of base metal, sample S1, and sample S5. The ductile dimples with different size and depth are observable on the fracture surface of the base metal (Fig. 14(a)). In fact, in this sample, failure is governed by coalescence of microvoids. This indicates a ductile fracture mode. Figure 14(b) shows the fracture surface of the sample S1 jointed at 1.0 MPa-10 s, which is characterized by transgranular cleavage and intergranular fracture. The presence of cleavage facets on the fracture surface of this sample together with observed intergranular fracture indicates that the joint has failed through brittle fracture. Intergranular fracture is due to the presence of the brittle secondary precipitates (FeAl2 and MgSiO4) at the grain boundaries (as indicated in Fig. 9). On the contrary, the fracture surface of sample S5 jointed at 1.5 MPa-15 s shows mixed brittle (region A) and ductile (region B) features, as indicated in Fig. 14(c).
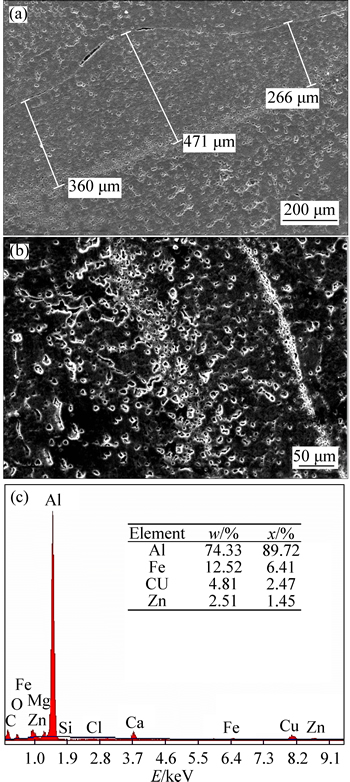
Fig. 11 SEM images from joint interface of sample S9 in manner uneched (a), etched (b) state, and EDS pattern from dispersed particles (c)
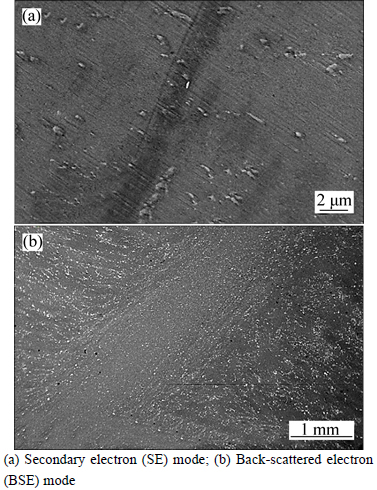
Fig. 12 SEM images of joint interface for sample S5:
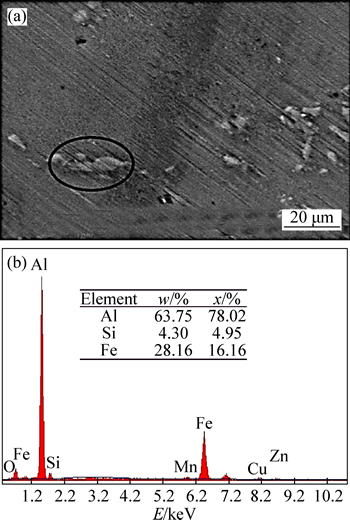
Fig. 13 EDS pattern from white phases present in joint region of sample S5
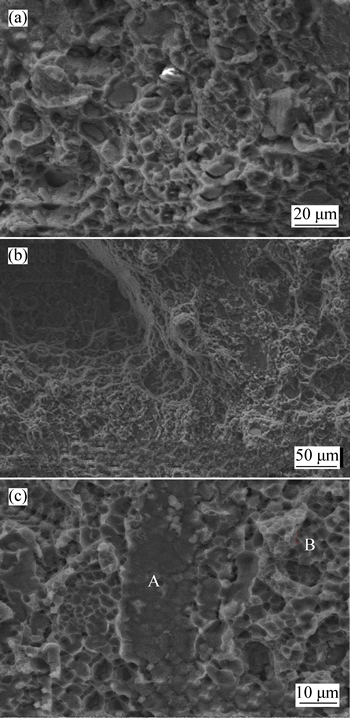
Fig. 14 SEM fractographs of base metal (a), sample S1 (1.0 MPa, 10 s) (b), and sample S5 (1.5 MPa, 15 s) (c)
4 Conclusions
In the present work, AA-7005 aluminum rods were jointed successfully by friction welding (FW). The effect of friction time (10, 15 and 20 s) and friction pressure (1.0, 1.5 and 2.0 MPa) on the microstructural characteristics and joint tensile strength of welded samples was investigated. The conclusions drawn from the results can be summarized as follows:
1) During the FW process, the rotating sample experiences a higher cooling rate compared to the stationary sample. This leads to the formation of finer microstructure in rotating side.
2) The value of tensile strength in joint is increased to a maximum value and then declined by increasing both of the friction time and friction pressure.
3) That sample jointed with the friction time of 15 s and friction pressure of 1.5 MPa exhibits a higher joint tensile strength compared to the other samples. Joint produced under this condition gets a tensile strength of 92.9% of that of base metal.
4) Using the friction time of 20 s and friction pressure of 2.0 MPa, due to the accumulation of alloying elements as intermetallic phases in the interface region, the friction welded joint shows a poor tensile strength.
References
[1] AZIMI A, FALLAHDOOST H, NEJADSEYFI O. Microstructure, mechanical and tribological behavior of hot-pressed mechanically alloyed Al-Zn-Mg-Cu powders [J]. Materials and Design, 2015, 75: 1-8.
[2] PALANIVEL R, MATHEWS P K, MURUGAN N. Optimization of process parameters to maximize ultimate tensile strength of friction stir welded dissimilar aluminum alloys using response surface methodology [J]. Journal of Central South University, 2013, 20: 2929-2938.
[3] MISHRA R S, MA Z Y. Friction stir welding and processing [J]. Materials Science and Engineering R: Reports, 2005, 50: 1-78.
[4] GHOLAMI S, EMADODDIN E, TAJALLY M, BORHANI E. Friction stir processing of 7075 aluminum alloy and subsequent aging treatment [J]. Transactions of Nonferrous Metals Society of China, 2015, 19: 2847-2855.
[5] LI D, YANG X, CUI L, HE F, ZHANG X. Investigation of stationary shoulder friction stir welding of aluminum alloy 7075-T651 [J]. Journal of Materials Processing Technology, 2015, 222: 391-398.
[6] MERCAN S, AYDIN S, OZDEMIR N. Effect of welding parameters on the fatigue properties of dissimilar AISI 2205-AISI 1020 joined by friction welding [J]. International Journal of Fatigue, 2015, 81: 78-90.
[7] HAKAN A, MEHMET T, ADEM K. Effect of friction pressure on the properties of friction welded MA956 iron based super alloy [J]. Materials and Design, 2007, 28: 948-953.
[8] SAHIN M. Joining of aluminum and copper materials with friction welding [J]. Advanced Manufacturing Technology, 2010, 49: 527-534.
[9] SAHIN M. Joining of stainless-steel and aluminum materials by friction welding [J]. The International Journal of Advanced Manufacturing Technology, 2009, 41: 487-497.
[10] OZDEMIR N, SARSYLMAZ F, HASCALYK A. Effect of rotational speed on the interface properties of friction-welded AISI 304L to 4340 steel [J]. Materials and Design, 2007, 28: 301-307.
[11] SAHIN M. Evaluation of the joint-interface properties of austenitic-stainless steels (AISI 304) joined by friction welding [J]. Materials and Design, 2007, 28: 2244-2250.
[12] KALUC E, TABAN E. Study of weld zone of friction welded C45/1.3344PM dissimilar steel joints [C]// International Conference on Design, Fabrication and Economy of Welded Structures. Miscolc, Hungary, 2008: 469-475.
[13] CHANDERA G S, REDDY G M, RAO A V. Influence of rotational speed on microstructure and mechanical properties of dissimilar metal AISI 304-AISI 4140 continuous drive friction welds [J]. Journal of Iron and Steel Research, International, 2012, 19: 64-73.
[14] FAUZI M N A, UDAY M B, ZUHAILAWATI H, ISMAIL A B. Microstructure and mechanical properties of alumina-6061 aluminum alloy joined by friction welding [J]. Materials and Design, 2010, 31: 670-676.
[15] AVINASH M, CHAITANYA V K, DHANANJAY K G, SARALA U, MURALIDHARA B K. Microstructure and mechanical behavior of rotary friction welded titanium alloys [J]. Proceedings of World Academy of Science, Engineering and Technology, 2007, 1: 124-126.
[16] DEBROY T, BHADESHIA H K D H. Friction stir welding of dissimilar alloys-a perspective [J]. Science and Technology of Welding and Joining, 2010, 15: 266-270.
[17] MA Z Y, MISHRA R S. Development of ultrafine-grained microstructure and low temperature (0.48Tm) superplasticity in friction stir processed Al-Mg-Zr [J]. Scripta Materialia, 2005, 53: 75-80.
[18] SHARMA C, DWIVEDI D K, KUMAR P. Effect of welding parameters on microstructure and mechanical properties of friction stir welded joints of AA7039 aluminum alloy [J]. Materials and Design, 2012, 36: 379-390.
(Edited by YANG Bing)
Received date: 2015-06-18; Accepted date: 2015-10-31
Corresponding author: Hamed Khosravi; Tel: +98-9151177285; E-mail: hkhosravi@mail.kntu.ac.ir