锗废渣掺量对水泥及膏体水化凝结的影响规律
王洪江1,李辉1,吴爱祥1,焦华喆1,肖云涛1,严庆文2
(1. 北京科技大学 土木与环境工程学院,北京,100083;
2. 云南驰宏锌锗股份有限公司,云南 曲靖,655011)
摘要:研究锗废渣掺入水泥及膏体后对其水化凝结规律的影响。将锗废渣以不同比例掺入水泥,经研究发现锗废渣不同掺量可以对水泥水化凝结起到调节作用。在此基础上,将尾砂和锗废渣以不同比例配制成膏体,发现锗废渣对膏体凝结起到了促凝的作用,而且掺量越大,效果越明显。经分析认为,锗废渣的掺入使水化反应生成更多的钙矾石,从而降低尾砂中Zn2+对膏体的缓凝作用。这为进一步研究将锗废渣掺入膏体调节膏体凝结时间提供理论依据。
关键词:锗废渣;缓凝;促凝;水化凝结规律
中图分类号:TQ172.9 文献标志码:A 文章编号:1672-7207(2013)02-0743-06
Hydraulic condensing rules for cement and paste mixed with different proportions of germanium waste
WANG Hongjiang1, LI Hui1, WU Aixiang1, JIAO Huazhe1, XIAO Yuntao1, YAN Qingwen2
(1. School of Civil and Environmental Engineering, University of Science and Technology Beijing, Beijing 100083, China;
2. Yunnan Chihong Zn and Ge Company Ltd, Qujing 655011, China)
Abstract: The hydraulic condensing rules after the cement and paste mixed with germanium waste were studied. Firstly different proportions of germanium waste mixed with cement were used, then it was found that different proportions of germanium waste can be regulatory role on hydraulic condensation. On the basis of the current industrial parameters, according to the different proportions of tailings and germanium waste made into paste, it is found that the germanium waste plays a promoting function of condensation, and the greater the mixed quantity, the greater the effect is. Experiment shows that with the germanium adding to paste with more ettringite to generate Zn2+ is reduced within tailing to paste of the slow effect. This provides the theory basis adjust setting time for paste which is mixed with germanium waste.
Key words: germanium waste; retarding; procoagulant; hydraulic condensing rules
云南某铅锌矿年产30 t铅锌矿伴生金属锗资源综合利用项目目前正在顺利进行,项目建成后,使公司产业链得到了延展,并使公司成为了全国最大规模的锗生产基地。然而在锗生产过程中的大量残液呈酸性,需要采用生石灰进行中和处理[1-2],处理后的残渣的二次处理又成为新的问题[3-4],即残渣处理要求高,而且不能对环境造成污染。为此,考虑将锗废渣作为充填骨料充填入采场是十分必要的。本文作者将不同比例的锗废渣掺入到水泥后进行泌水率[5]和凝结时间(初凝和终凝)测定,然后从泌水率和水化凝结过程分析造成水泥凝结时间差异的原因。在此基础上,根据现行工业参数将尾砂与锗废渣按照不同比例配制成膏体,测定锗废渣掺量不同情况下膏体的凝结时间,并从水化机理角度对锗废渣不同掺量情况下造成膏体凝结时间变化的原因进行解释。同时通过将Zn(NO3)2和Na2SO4掺入到膏体中,证实尾砂中Zn2+对膏体凝结具有明显的调节作用,也为进一步解释锗废渣对膏体水化凝结的促凝作用机理提供理论依据。
1 原材料
(1) 水泥。强度等级为32.5R型普通硅酸盐水泥。密度为3.05 g/cm3,容重为1.10 g/cm3,粒级组成如图1所示。
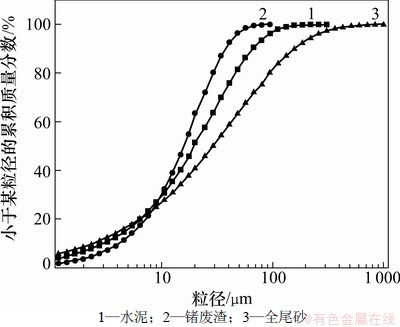
图1 水泥、锗废渣和尾砂粒级组成曲线
Fig.1 Grain level curves of cement, waste of Ge and tailling
(2) 锗废渣。此锗废渣是用生石灰对提炼锗后的废液进行中和处理而得到的废渣,虽称为锗废渣,但是其化学成分中锗的含量非常低(见表1)。锗废渣为灰白色,通过XRD分析结果可以判断,锗废渣的主要化学成分为CaSO4(见图2)。其密度为2.37 g/cm3;平均粒径为29.63 μm,小于20 μm粒径含量高达50%(其粒级组成如图1所示)。
不同晶体经X线作用后产生特有的衍射峰,而非晶质体则无衍射峰,通过锗废渣的X线衍射可以看到衍射峰位置内出现一个较高的峰位,这个峰的高低可以表明晶体的多少[6]。由图2可以看出:锗废渣的主要化学成分为CaSO4,但是其是否含有结晶水还有待于进一步分析。
表1 锗废渣元素化学成分(质量分数)
Table 1 Chemical composition of Ge waste residue %

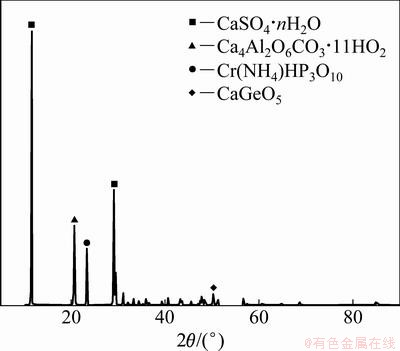
图2 锗废渣的XRD谱
Fig.2 XRD pattern of waste of Ge
(3) 全尾砂。其密度为2.75 g/cm3,容重为1.75 g/cm3,孔隙率为36.36%;平均粒径为75.59 μm,中值粒径为34.95 μm,小于20 μm的颗粒累计含量占37.20%(粒级组成如图1所示);其化学组成及矿物组成分别见表2和表3。
表2 全尾砂化学成分(质量分数)
Table 2 Chemical composition of tailings %

表3 全尾砂矿物组成(质量分数)
Table 3 Mineral composition of tailings %
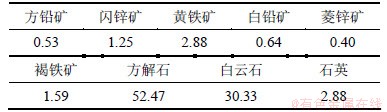
由图1可以看出:在配制膏体的3种配料中,锗废渣的粒度最细,其次为水泥,最后为全尾砂。即将造成锗废渣掺量越多,其整体粒度越细,需水量也将随之增加。
2 实验原理与方案
2.1 实验原理
(1) 泌水率测定。泌水率反映了浆体的析水性能,实际上也是浆体的保水性能。用量杯盛入一定量的浆体,测其浆体质量,并换算出其中清水的含量;在量杯表面铺两层纱布,纱布大小与量杯口同大,然后将滤纸放在纱布表面,测定在60 min内浆体泌出的清水质量,泌出清水与浆体内清水总量之比即为泌水率P。其计算公式如下:

式中:P为浆体泌水率,%;m0为泌出清水质量,g;m为浆体中原总清水量,g。
(2) 凝结时间测定。根据GB/T 1346—2001《水泥净浆标准稠度用水量、凝结时间、安全性验证方法》规定,采用标准法维卡仪对不同锗废渣添加比例的水泥浆体进行初凝和终凝时间的测定;依据砂浆测试仪的操作规程,测定膏体凝结时间。
2.2 实验方案
(1) 锗废渣掺量对水泥浆体凝结时间的影响。将锗废渣在烤箱中烘干后,分别按0,5%,10%,15%,20%和25%的质量比例掺入到水泥中进行实验。选择水灰比为0.30,即加水量为水泥和锗废渣总质量的30%,然后分别测定其锗废渣不同掺量情况下浆体的泌水率和凝结时间,同时将锗废渣掺比为0,10%和20%的试样在其加水后3 h(水化反应开始后3 h)用无水乙醇终止其水化反应,然后将其试样烘干研磨后进行X线衍射实验,分析其水化凝结过程。
(2) 锗废渣掺量对膏体凝结时间的影响。采用未烘干锗废渣,根据现行工业参数,配制4组不同配比的料浆。料浆配比质量分数为80%,灰砂比(即水泥与骨料质量比)为1:8,全尾砂与锗废渣的质量比分别为7:1,6:2,5:3和4:4。测定不同尾废比情况下膏体的凝结时间。
(3) 锌离子对膏体凝结时间的影响。实验尾砂来自深锥进料尾砂。为除去尾砂中已存可溶性锌离子对实验的影响,先将尾砂多次浸泡清洗,在清洗过程中应尽量避免细粒级尾砂流失。将清洗干净后的尾砂烘干备用。
(4) 按照现行工业配比进行膏体配制,即膏体质量分数为80%,m(全尾砂):m(水淬渣):m(水泥)为7:1:1,其他物料全部采用现生产中实际采用的水淬渣、水泥等。实验分为5组,分析纯Zn(NO3)2按全尾砂总质量的0,0.01%,0.03%,0.06%,0.10%和0.50%添加。
(5) 硫酸根离子对膏体凝结时间的影响。按照现行工业配比进行膏体配制,实验分为6组,分析纯Na2SO4按充填干料总质量的0,1%,2%,3%,4%和5%添加。
3 结果与分析
锗废渣掺量对水泥凝结时间及泌水率的影响分别如图3和4所示。
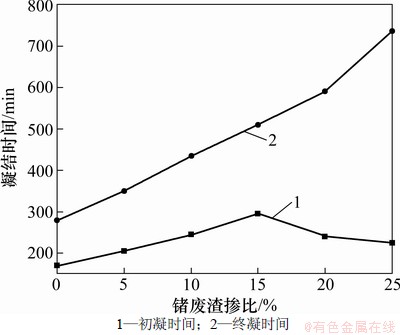
图3 锗废渣掺比对水泥浆体凝结时间的影响
Fig.3 Effect of Ge waste mixed on setting time
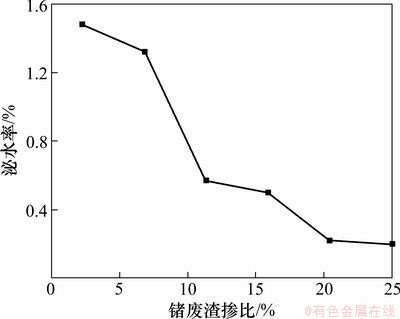
图4 锗废渣掺比对水泥浆体泌水率的影响
Fig.4 Effect of Ge waste mixed on bleeding rate
由图3可以看出:随着锗废渣掺量的不断增加,水泥浆体的初凝时间表现出先增加后降低的趋势,终凝时间则不断延长。分析原因主要是由于锗废渣中主要成分是石膏,而石膏是水泥工业的主要添加剂之一,其添加量可以控制水泥的凝结时间,在一定比例以下对水泥起到缓凝作用,超过一定的比例将造成水泥的快速凝结[7-8]。
初凝现象的水化过程分析:一方面,水泥加水后迅速发生水化反应,其中以C3A反应最快[9-10],同时锗废渣掺入后,引入大量的SO42-,其与C3A反应生成钙矾石,而钙矾石是一种难溶性物质,其将富集在C3A表面形成一层致密的膜,从而阻碍了C3A的快速水解;另一方面,根据卓斯(Tadros)等的延迟成核假设[11-12],当水泥中主要成分C3S与水接触后,在C3S表面有晶格缺陷的部位最先发生水解,使Ca2+和OH-进入溶液,造成C3S离子表面形成一个缺钙的富硅层,锗废渣作为一种高钙水化物质,其大量的Ca2+进入溶液,被钙表面吸附形成双电子层,并使其表面出现正电位。由于带正电位的C3S与溶液界面区存在高浓度的Ca2+,导致了C3S进一步水化受阻,即导致了影响水泥浆体初凝时间的诱导期变长。随后溶液中的Ca2+继续增多,当其达到一定饱和度时,开始以Ca(OH)2晶体的形式析出,从而C3S开始恢复正常并加速水化,双电子层也逐渐减弱或消失,此时诱导期基本结束,即达到水泥浆体的初凝。但是,锗废渣掺入量超过一定比例(15%),水化过程中的另一种作用开始加强。水泥加水后成为一种凝胶溶液,硅酸盐胶体带负电荷,通常情况下由于电性排斥力,使凝胶溶液具有一定稳定性,不容易结合成大颗粒,但是锗废渣掺入量较大时,引入了大量的Ca2+,其与硅酸盐胶体将发生电荷间的相互吸引,发生颗粒间的凝聚现象,使水泥出现速凝。
大多数研究都断定水泥正常的凝结受控于C3S的水化,加之其是水泥中的主要矿物成分,故常常作为水泥水化的模型[13]。C3S的水化产物为C—S—H凝胶和Ca(OH)2,而Ca(OH)2作为一种重要的水化产物,其在水化凝结过程中起着重要作用。图5所示为不同锗废渣掺比水泥浆体水化产物的XRD分析曲线。由图5可以看出:在相同水化反应条件下,通过XRD分析得到的Ca(OH)2的生成量存在很大差异,随着锗废渣掺入比例的提高,Ca(OH)2在水化过程中的量先是急剧下降,这将导致C3S的水化速度减慢,随后当其掺量达到一定比例(15%)后,水化过程中Ca(OH)2的量又逐渐增多,C3S的水化速度恢复正常。表明锗废渣的掺入对C3S的水化过程产生了影响,从而影响了水泥的水化凝结,在一定程度上,这将是导致水泥凝结时间变化的一个重要原因。
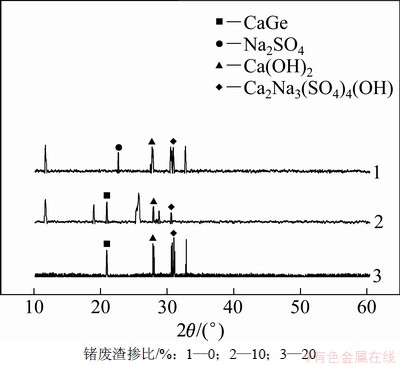
图5 不同锗废渣掺比水泥浆体水化产物的XRD谱
Fig.5 XRD patterns of hydration products with different mixed Ge wastes
终凝现象的水化过程分析:锗废渣(主要成分是石膏)对水泥浆体水化反应的影响主要发生在初凝阶段,其后C3A水化反应开始变慢,C3S与C2S开始正常参与水化反应,但是由于锗废渣颗粒组成较细,即比表面积较大,造成其颗粒表面的吸附作用增强,很多游离的水分子吸附在颗粒表面,即浆体的保水性增强,泌水率下降(见图4),而且锗废渣掺量越多,其含水量就越多,这样就会造成其终凝凝结时间的延迟。
锗废渣掺量对膏体凝结时间的影响如图6所示。由图6可知:在灰砂比为1:8、膏体质量分数为80%配比条件下,随着尾废比的不断降低,即锗废渣的添加量的不断增加,膏体的凝结时间则不断缩短。
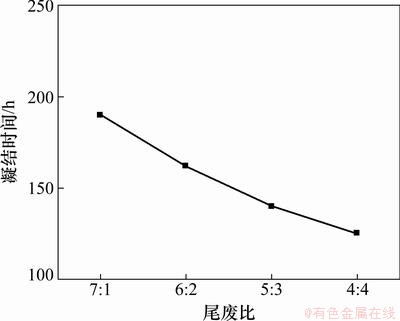
图6 膏体质量分数为80%和灰砂比为1:8条件下不同尾废比的膏体凝结时间
Fig.6 Paste setting time with different mixed Ge wastes at paste mass fraction of 80% and water ratio of 1:8
图7所示为硝酸锌添加量对膏体凝结时间的影响。由图7可以看出:硝酸锌对膏体的凝结时间具有明显的缓凝作用,当硝酸锌添加量为尾砂质量的0.06%,此时的凝结时间达到127 h,缓凝效果最强。而随着添加量超过一定量时,膏体的凝结时间反而有一定的缩短,硝酸锌的缓凝效果降低。所以,尾砂中一定浓度的锌离子是可以延迟膏体早期凝结,对膏体具有缓凝作用。
锗废渣对膏体促凝的水化过程分析:尾砂中由于含锌矿物(见表1和2)及选矿工艺过程(主要)不可避免的含有可溶性锌离子的存在,而根据硝酸锌添加量对膏体凝结时间的影响实验,分析可知:在一定含量范围内(0.06%)锌离子对膏体凝结起到了缓凝作用,而且其含量越多,缓凝效果越明显。
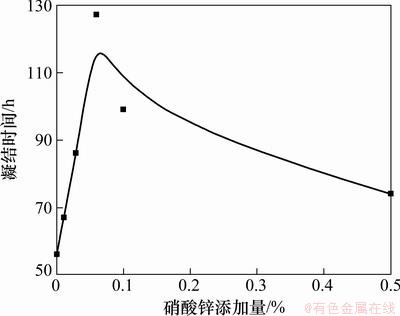
图7 硝酸锌添加量对膏体凝结时间的影响
Fig.7 Effect of Zn(NO3)2 content on paste setting time
锗废渣和尾砂掺入到膏体中,随着水化反应的进行,其可溶性离子不断溶解,离子浓度不断增加,其离子一部分参与水化反应生成了水化产物,另一部分则溶解在游离水中。在水泥水化初期(即初凝),一方面,溶液中的Zn2+与Ca2+及OH-作用生成不溶性水化产物Ca(Zn(OH)3)2·2H2O盖在水泥颗粒表面,阻碍水泥水化;另一方面,水化过程中其不溶性颗粒吸附在新相的晶胚上,降低了饱和溶液中晶胚的生成速度,阻碍了水泥水化及浆体初始结构的发展,从而表现出Zn2+对膏体的缓凝作用[14]。但是,锗废渣的掺入将使浆体中的Ca2+和SO42-大量增加,尤其是SO42-的引入,将促进C3A反应而生成钙矾石(Aft),而且其掺量越大,AFt的生成量越多,AFt的生成将伴随着体积的膨胀,即水化产物有利于冲破水泥粒子表面的覆盖层而使水化反应加速。在膏体体系中这两种作用同时进行着,但是伴随着锗废渣掺量的增加,SO42-的作用效果将越来越明显,即水泥的水化速度越来越快,表现出初凝时间的不断缩短。故随着锗废渣掺量的增加,膏体的凝结时间不断缩短。
图8所示为硫酸钠添加量对膏体凝结时间的影响。由图8可以看出:随着Na2SO4掺入比例的增加,膏体的凝结时间表现出先缩短后增加的趋势,其主要原因是随着SO42-掺入量的增加,其与C3A快速发生反应生成了AFt,并伴随着体积的膨胀,而且当Na2SO4掺入比例控制在4%左右时,其掺入量越多,效果越明显,即生成的AFt的量越多,水泥颗粒暴露的越充分,从而水化反应越迅速,凝结时间越快。进一步证明了SO42-对膏体的水化凝结是有利的,即掺入一定量锗废渣可以缩短膏体的凝结时间。
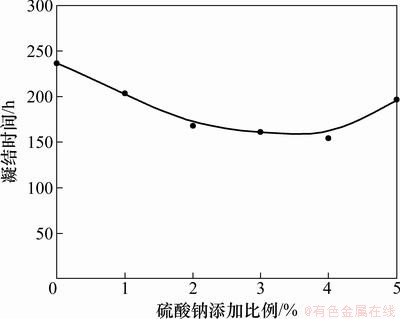
图8 硫酸钠添加量对膏体凝结时间的影响
Fig.8 Effect of Na2SO4 content on paste setting time
4 结论
(1) 锗废渣的粒度较细,当其中小于20 μm颗粒累积含量达到50%时,其掺入水泥后将造成浆体泌水率的降低,保水性增强,使浆体凝结时间延长,尤其是使终凝时间延长。
(2) 锗废渣掺入后对水泥浆体凝结时间起到了调节作用,当其掺量小于15%时对水泥起到缓凝作用,当其掺量大于15%时对浆体又起到促凝作用,其原因是锗废渣中CaSO4成分引起的。
(3) 锗废渣的掺入对膏体起到了一定的促凝作用,且随着掺量的增加,其促凝效果越明显,这主要是因为锗废渣掺入使水化反应生成了更多的AFt,从而降低了Zn2+对膏体的缓凝作用。
(4) 通过将Zn(NO3)2和Na2SO4以不同比例掺入到膏体中,证实了Zn2+对膏体凝结具有缓凝的作用,同时也为锗废渣对膏体凝结具有促凝作用的机理研究提供了依据。
参考文献:
[1] 王少龙, 李云昌. 锗蒸馏残液的环保处理工艺研究[J].稀有金属, 2007, 31(4): 581-584.
WANG Shaolong, LI Yunchang. Ge distillation of the residual liquid dealing with environmental protection technology research[J]. Rare Metal, 2007, 31(4): 581-584.
[2] 王恒金. 蒸锗残液残渣综合回收有价成分方案的探讨[J]. 云南冶金, 1988(5): 35-37.
WANG Hengjin. Ge steam residual liquid residue comprehensive recovery of valuable ingredients of the scheme are discussed[J]. Yunnan Metallurgy, 1988(5): 35-37.
[3] 王洪江, 罗恒. 火湿法联合工艺处理锗蒸馏残渣[J]. 广东有色金属学报, 2002(S1): 44-50.
WANG Hongjiang, LUO Heng. Fire wet joint processing Ge distillation residue[J]. Guangdong Non-ferrous Metal Journal, 2002(S1): 44-50.
[4] 王少龙, 雷霆, 张玉林, 等. 四氯化锗提纯工业研究进展[J]. 材料导报, 2006, 20(7): 35-37.
WANG Shaolong, LEI Ting, ZHANG Yunlin, et al. GeCl4 purification industrial research progress[J]. Materials Review, 2006, 20(7): 35-37.
[5] 王洪江, 王勇, 吴爱祥, 等. 从饱和率和泌水率角度探讨膏体新定义[J]. 武汉理工大学学报, 2011, 33(6): 85-89.
WANG Hongjiang, WANG Yong, WU Ai-xiang, et al. The paste new definition research from saturated rate and bleeding rate[J]. Journal of Wuhan University of Science and Technology, 2011, 33(6): 85-89.
[6] Bentz D P, Garboczi E J. Percolation of phase in a three-dimensional cement paste microstructural[J]. Cement and Concrete Research, 1991(2): 325-344.
[7] 张玉珍, 王政. 硬石膏复合缓凝剂对水泥的缓凝及增强作用[J]. 中国建材, 1995(1): 23-34.
ZHANG Yunzhen, WANG Zheng. Hard gesso composite retarder for cement and enhance coagulation slow role[J]. China Building Materials, 1995(1): 23-34.
[8] 盛广宏, 陈明, 程麟, 等. 硬石膏对硅酸盐水泥性能的影响[J]. 水泥工程, 2004(5): 8-11.
SHENG Guanghong, CHEN Ming, CHENG Lin, et al. Hard gesso to influence on the performance of the Portland cement[J]. Cement Engineering, 2004(5): 8-11.
[9] Krstulovic R, Dabic P. A conceptual model of the cement hydration process[J]. Cement and Concrete Research, 2000, 30(5): 693-698.
[10] 马振珠, 岳汉威, 宋晓岚. 水泥水化过程的机理、测试及影响因素[J]. 长沙大学学报, 2009, 23(2): 43-46.
MA Zhenzhu, YUE Hanwei, SONG Xiaolan. The mechanism of the cement hydration process, test and influencing factors[J]. Journal of Changsha University, 2009, 23(2): 43-46.
[11] 袁润章. 胶凝材料学[M]. 2版. 武汉: 武汉工业大学出版社, 2003: 93-130.
YUAN Runzhang. Cementitious material science[M]. 2nd ed. Wuhan: Wuhan Industrial University Press, 2003: 93-130.
[12] Lea F M. The chemistry of cement and concrete[M]. 3rd ed. California, Americam: Chemical Publishing Co Inc, 1970: 654-681.
[13] Bonavetti V L, Rahhal V F, Irassar E F. Studies on the carboaluminate formation in limestone filler-blended cements[J]. Cement and Concrete Research, 2001, 31(6): 853-859.
[14] 张莉. 化学外加剂对水泥水化历程的影响及其作用机理研究[D]. 武汉: 武汉理工大学材料科学与工程学院, 2004: 40-42.
ZHANG Li. Chemical additives to the influence of the cement hydration process and mechanism research[D]. Wuhan: Wuhan University of Technology. School of Materials Science and Engineering, 2004: 40-42.
(编辑 杨幼平)
收稿日期:2012-02-18;修回日期:2012-04-30
基金项目:国家自然科学基金重点资助项目(50934002);长江学者和创新团队发展计划项目(IRT0950)
通信作者:王洪江(1967-),男,河南三门峡人,硕士生导师,从事充填采矿、溶浸采矿及岩石力学研究;电话:15901196527;E-mail:wanghj@126.com