J. Cent. South Univ. Technol. (2011) 18: 960-965
DOI: 10.1007/s11771-011-0787-2
Effect of annealing on microstructure and properties of Si3N4-AlN composite ceramics
XU Peng(徐鹏)1, 2, YANG Jian(杨建)1, QIU Tai(丘泰)1, CHEN Xing(陈兴)1
1. College of Materials Science and Engineering, Nanjing University of Technology, Nanjing 210009, China;
2. Beijing Sinoma Synthetic Crystals Co. Ltd., Beijing 100018, China
? Central South University Press and Springer-Verlag Berlin Heidelberg 2011
Abstract: Aiming at developing novel microwave-transparent ceramics with low dielectric loss, high thermal conductivity and high strength, Si3N4-AlN (30%, mass fraction) composite ceramics with La2O3 as sintering additive were prepared by hot-pressing at 1 800 °C and subsequently annealed at 1 450 °C and 1 850 °C for 2 h and 4 h, respectively. The materials were characterized by XRD and SEM. The effect of annealing process on the phase composition, sintering performance, microstructure, bending strength, dielectric loss and thermal conductivity of the materials was investigated. The results showed that both annealing at 1 850 °C and 1 450 °C promoted the phase transformation of α-Si3N4 to β-Si3N4. After annealing at 1 850 °C, grain growth to a certain extent occurred in the materials. Especially, the elongated β-Si3N4 grains showed a slight increase in diameter from 0.2 μm to 0.6 μm approximately and a decrease in aspect ratio. As a result, as the annealing time increased to 4 h, the bending strength declined from 456 MPa to 390 MPa, whereas the dielectric loss decreased to 2.15×10-3 and the thermal conductivity increased to 16.3 W/(m?K) gradually. When annealed at 1 450 °C, increasing the annealing time to 4 h significantly promoted the crystallization of glassy phase to La2Si6N8O3 phase in the materials, which led to the increase in bending strength to 619 MPa and thermal conductivity to 15.9 W/(m·K), respectively, and simultaneously the decrease in dielectric loss to 1.53×10-3.
Key words: Si3N4-AlN composite; annealing; La2O3; bending strength; thermal conductivity; dielectric loss
1 Introduction
Microwave-transparent ceramics (MTC) are the special materials employed as output windows of traveling wave tube (TWT) in the field of microwave communication. Commonly, in order to perform the functions, besides low dielectric loss (tan δ) and high thermal conductivity, excellent mechanical strength and thermal shock resistance are also exactly required for MTC to release the heat caused by dielectric loss in time and prevent the thermal breakdown. Recently, with the increment of output power, broadening of wave band and development of microwave technology, a higher mechanical property of MTC is desired in response to the miniaturization design of output windows.
Aluminum nitride (AlN) has been an excellent candidate for microwave-transparent ceramics due to its high thermal conductivity and low tan δ [1]. However, AlN possesses relatively low mechanical strength, which limits its applications to high-power output windows. Silicon nitride (β-Si3N4) is a familiar advanced ceramics considered for structural applications on engine components and wear parts owing to its excellent mechanical properties at both room and elevated temperatures, good resistance to thermal shock and chemical attack. However, recent investigations have indicated that a thermal conductivity of 100- 155 W/(m·K) or even more could be obtained for the β-Si3N4 ceramics [2-3]. Moreover, the Si3N4 ceramics with low dielectric loss of less than 5×10-4 at 10 GHz, which is suitable for use as output windows, has been prepared by TAJIMA et al [4]. These works suggest a potential application of Si3N4 as microwave-transparent ceramics. Therefore, by combining the excellent properties of AlN and Si3N4, Si3N4-AlN composite ceramics might be a novel microwave-transparent ceramics with low dielectric loss, high thermal conductivity, high strength and thermal shock resistance, which are being investigated by the authors. In our previous work, Si3N4-AlN (30%, mass fraction) composite ceramics with a high bending strength of 456 MPa has been successfully prepared by selecting La2O3 as the sintering additive. However, the materials exhibit a relatively low thermal conductivity and high dielectric loss which are believed to be caused by the relatively large amount of glassy phase existing in the materials [5].
As has been revealed by the literatures [6-11], annealing is an effective route to increase the thermal conductivity and decrease tan δ of AlN and Si3N4 ceramics by accelerating the grain growth, eliminating glassy phase and making them distribute in tri-crystal junctions. In this work, Si3N4-AlN composite ceramics were prepared by hot-pressing using 6% (mass fraction) La2O3 as the sintering additive and the effects of annealing process on the phase composition, sintering performance, microstructure, bending strength, dielectric loss and thermal conductivity of the materials were investigated.
2 Experimental
Commercial α-Si3N4 (α-phase content >93%, average particle size 0.5 μm, oxygen content <2.0%) and AlN (purity >98.6%, average particle size 0.5 μm) powders were selected as the starting materials. In all specimens, the mass ratio of Si3N4 to AlN is fixed at 7:3, and 6% (mass fraction) La2O3 (purity >99.9%) was added as the sintering additive. After ball-milling in ethanol for 6 h, the slurry was dried and sieved. Then, the mixed powders were placed into a graphite mold coated with BN and hot-pressed at 1 800 °C for 2 h under a pressure of 30 MPa in N2 atmosphere, followed by annealing at 1 450 °C and 1 850 °C for 2 h and 4 h, respectively.
The densities of the sintered specimens were determined by the Archimedes method, and the phase identification of the specimens was performed by X-ray diffractometry (ARL X’TRA, Switzerland) with Cu Kα radiation. The specimens were cut, ground and polished into strips with dimensions of 3 mm×4 mm×40 mm and the three point bending method was applied to measure the room temperature bending strength using a span of 30 mm with a crosshead speed of 0.5 mm/min. The microstructures of the specimens were investigated by SEM (JSM-5900, JEOL, Japan). Prior to observation by SEM, heat-etching at 1 700 °C in N2 atmosphere was conducted for the polished specimens.
The thermal conductivity was determined by the laser-flash method (LFA447, Netzsch, German) with billet dimensions of d12.7 mm×2.5 mm. The dielectric loss (tan δ) was measured at 1 MHz by the perturbation method using a cavity resonator and a vector network analyzer (HP-4294A).
3 Results and discussion
3.1 Phase composition and density
Figure 1 shows the XRD patterns of the specimens with different annealing processes. Both β-Si3N4 and AlN were identified as the main phases in all the specimens, which indicates that Si3N4-AlN composite ceramics have been prepared. Lanthanum melilites (La2Si6N8O3) also appeared as the intergranular phase in the materials. The formation of La2Si6N8O3 could be explained by the reaction between La2O3 and Si3N4 as follows:
La2O3+2Si3N4=La2Si6N8O3 (1)
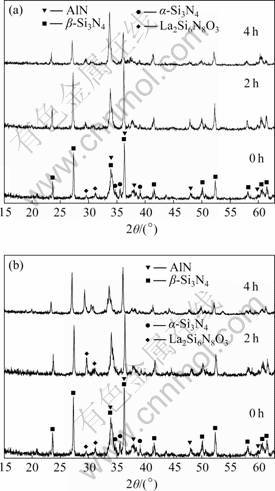
Fig.1 XRD patterns of Si3N4-AlN composite ceramics with different annealing times: (a) Annealed at 1 850 °C; (b) Annealed at 1 450 °C
For the unannealed specimen, a small amount of α-Si3N4 was also found, which suggests an incomplete transformation of Si3N4 from α-phase to β-phase. For the annealed samples, the α-Si3N4 disappeared gradually with increasing the annealing time, which indicates that the annealing promotes the phase transformation of α-Si3N4 to β-Si3N4. For the samples annealed at 1 450 °C, the content of La2Si6N8O3 increased gradually with increasing the annealing time. Therefore, a conclusion could be drawn that increasing the annealing time at 1 450 °C resulted in more La2Si6N8O3 crystallized from the glassy phase.
Table 1 lists the bulk densities and apparent porosities of the Si3N4-AlN composite ceramics with different annealing processes. As can be seen, all the samples show relatively high density (apparent porosity <0.3%), which suggests that the annealing process has no influence on the densities of the materials.
Table 1 Bulk density and apparent porosity of Si3N4-AlN composite ceramics with different annealing processes
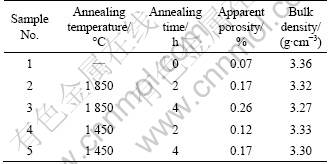
3.2 Microstructure
The SEI micrographs of the Si3N4-AlN composite ceramics with different annealing times at 1 850 °C and 1 450 °C are shown in Fig.2 and Fig.3, respectively. All the specimens showed a similar microstructure which mainly consists of elongated β-Si3N4 grains and equiaxial AlN grains. In the meantime, a number of pores distributing between the grains were also observed as a result of hot-etching, which indicates a certain content of glassy phase existing in the materials. As can be seen in Fig.2, as the annealing time increased to 4 h, the elongated β-Si3N4 grains showed an invariant length and a slight increase in diameter from 0.2 μm to 0.6 μm approximately. The average grain size of AlN also increased from 0.2 μm to 0.8 μm. The grain growth will result in the decrease in volume fraction of two-grain junction per unit volume in the materials. For the samples annealed at 1 450 °C, there was no obvious grain growth like the samples annealed at 1 850 °C. However, the content of pores decreased and simultaneously the amount of equiaxial grains increased dramatically as the annealing time increased. So a conclusion could be drawn that the annealing at 1 450 °C significantly facilitated the crystallization of glassy phase to equiaxial La2Si6N8O3 crystalline phase,which is in agreement with the XRD results.
3.3 Bending strength
Figure 4 shows the bending strengths of Si3N4-AlN composite ceramics with different annealing processes. It can be seen that the unannealed Si3N4-AlN composite ceramic exhibited a high room-temperature strength of 456 MPa, which is reasonably owing to the β-Si3N4 matrix. When annealed at 1 850 °C, with the increase of annealing time, the bending strength decreased to 390 MPa gradually, which could be attributed to the radial growth and the decrease in aspect ratio of β-Si3N4 grains. Whereas, for the samples annealed at 1 450 °C, the case was quite the contrary. The increase of annealing time showed a positive effect on the bending strength of the materials, which increased from 456 MPa to 619 MPa. As there is no variation in the aspect ratio of the elongated β-Si3N4 grains, the increase of bending strength could be explained by the crystallization of glassy phase to La2Si6N8O3, which was promoted by extended annealing time. Figure 5 shows the SEI micrograph of the fracture surface of Si3N4-AlN composite ceramics annealed at 1 450 °C for 4 h. It can be seen that intergranular fracture was the leading fracture manner due to the weak bonding between the grains and the glassy phase. Therefore, with the increase of annealing time, more glassy phase crystallized. The decrease of glassy phase content contributes to the dramatical improvement in the bending strength of the materials.
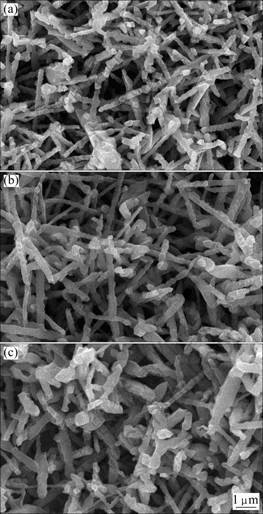
Fig.2 SEI micrographs of etched surfaces of Si3N4-AlN composite ceramics with various annealing times at 1 850 °C: (a) 0 h; (b) 2 h; (c) 4 h
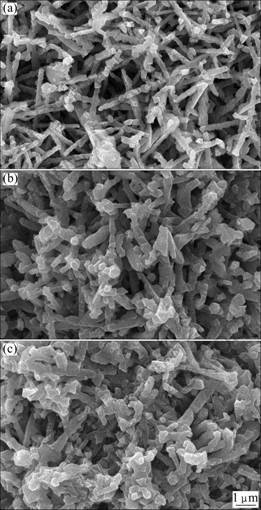
Fig.3 SEI micrographs of etched surfaces of Si3N4-AlN composite ceramics with various annealing times at 1 450 °C: (a) 0 h; (b) 2 h; (c) 4 h
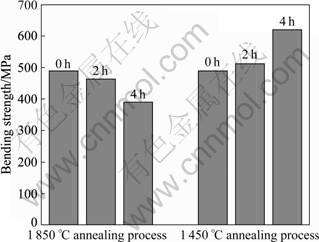
Fig.4 Bending strengths of Si3N4-AlN composite ceramics with different annealing processes
3.4 Dielectric loss
Figure 6 demonstrates the relationship between the dielectric loss (tan δ) of Si3N4-AlN composite ceramics and the annealing process. In general, annealing can effectively promote the grain growth and development, reducing the lattice defects and residual stresses in crystals, which is favorable to the decrease of dielectric loss. It can be seen that when annealed at 1 850 °C, the dielectric loss of the samples decreased from 4.55×10-3 to 2.15×10-3 with increasing annealing time, which could be explained from the further grain growth and the reduction of various defects in the materials. For the case of 1 450 °C, the annealing time also showed the same effect on the dielectric loss of the materials, which reached the minimum value of 1.53×10-3 with the annealing time of 4 h. As there is no obvious variation in grain size, the significant decrease in tan δ was believed to be associated with the crystallization process of the glassy phase. Generally, the glassy phase shows a much higher dielectric loss than the corresponding crystalline phase owing to the disordered distribution of atoms. For example, the tan δ of Y-Al-Si-O-N glass ((1-2)×10-2 [13]) is an order of magnitude higher than that of the crystalline phase ((2.0-2.5)×10-3 [14]). Therefore, it is reasonable to suppose that the case is similar for the La-Al-Si-O-N system although there is no exact data reported at present. As both AlN and Si3N4 crystals have very low tan δ, the glassy phase contributes to the majority of tan δ of the materials despite their small content. Thus, the decrease of glassy phase resulted from the extended annealing time leads to the significant decrease in tan δ.
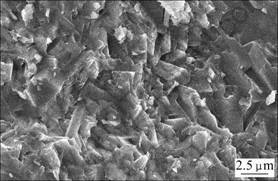
Fig.5 SEI micrograph of fracture surface of Si3N4-AlN composite ceramics annealed for 4 h at 1 450 °C
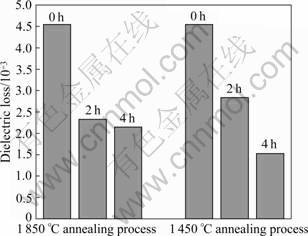
Fig.6 Dielectric losses of Si3N4-AlN composite ceramics with different annealing processes
3.5 Thermal conductivity
The effect of annealing process on the thermal conductivity of the Si3N4-AlN composite ceramics is shown in Fig.7. Both the annealing at 1 850 °C and 1 450 °C played a positive effect on the thermal conductivity of the materials, which increased to 16.3 W/(m·K) and 15.9 W/(m·K) as the annealing time increased to 4h, respectively. As is well known, the phonon thermal conduction mechanism is obeyed for non-metal materials such as AlN and Si3N4 ceramics. According to GOLDSMID et al’s theory [15], the thermal conductivities of both Si3N4 and AlN are governed by the phonon scattering at grain boundaries and are proportional to the square root of the grain size (λ∝D1/2, λ: thermal conductivity, D: grain diameter) up to its intrinsic value. Considering the very low thermal conductivity of the glassy phase, the improvement in thermal conductivity of the materials annealed at two different temperatures can be explained by the variation in grain size and the amount of glassy phase. As has been analyzed above, annealing leads to the grain growth and the migration of glassy phase toward tri-crystal junctions. At the same time, the amount of glassy phase decreases significantly due to its crystallization during the annealing process. All these will improve the reciprocal contact among the Si3N4 and AlN grains with high intrinsic thermal conductivity, which thereby increases the thermal conductivity of the composites. However, for all that, the thermal conductivity of the as-prepared Si3N4-AlN composite ceramics is still much lower than that of pure AlN and Si3N4 ceramics, and the function of annealing is not remarkable. Such a low thermal conductivity is believed to be caused by the small grain size and relatively large amount of oxygen existing in crystal lattice. Promoting the grain growth is a key factor to improve the thermal conductivity of the materials, which can be achieved by further prolonging the annealing time or using some coarse raw material powder as crystal seeds.

Fig.7 Thermal conductivities of Si3N4-AlN composite ceramics with different annealing processes
4 Conclusions
1) The annealing of the as-prepared Si3N4-AlN (30%, mass fraction) composite ceramics at 1 850 °C and 1 450 °C promoted the phase transformation of α-Si3N4 to β-Si3N4. For the samples annealed at 1 450 °C, increasing the annealing time resulted in more La2Si6N8O3 crystallized from the glassy phase.
2) After the annealing at 1 850 °C, grain growth to a certain extent occurred in the materials. Especially, the elongated β-Si3N4 grains showed a slight increase in diameter from 0.2 μm to 0.6 μm approximately and a decrease in aspect ratio. As a result, as the annealing time increased to 4 h, the bending strength declined from 456 MPa to 390 MPa, whereas the dielectric loss decreased to 2.15×10-3 and the thermal conductivity increased to 16.3 W/(m·K) gradually.
3) When annealed at 1 450 °C, increasing the annealing time to 4 h significantly promoted the crystallization of glassy phase to La2Si6N8O3 phase in the materials, which led to the increase in bending strength to 619 MPa and thermal conductivity to 15.9 W/(m·K), respectively, and simultaneously the decrease in dielectric loss to 1.53×10-3.
References
[1] SLACK G A, TANZILLI R A, POHL R O, VANDERSANDE J W. The intrinsic thermal conductivity of AlN [J]. Journal of Physics and Chemistry Solids, 1987, 48(7): 641-47.
[2] WATARI K, HIRAO K, TORIYAMA M, ISHIZAKI K. Effect of grain size on the thermal conductivity of Si3N4 [J]. Journal of the American Ceramic Society, 1999, 82(3): 777-779.
[3] HIRAO K, WATARI K, BRITO M E, TORIYAMA M, KANIAKI S. High thermal conductivity in silicon nitride with anisotropic microstructure [J]. Journal of the American Ceramic Society, 1996, 79(9): 2485-2488.
[4] TAJIMA K, UCHIMURA H, TANAKA K, KOHSAKA S, MARUYAMA H. Dielectric material having a low dielectric loss factor for high-frequency use: US Patent 5885916 [P]. 1997-03-23.
[5] XU Peng, YANG Jian, QIU Tai. Effect of La2O3 additive on microstructure and properties of Si3N4-AlN composite ceramics [M/OL]// JIANG Dong-liang, ZENG Yu-ping, SINGH M, HEINRICH J. Ceramic Materials and Components for Energy and Environmental Applications. Hoboken, USA: John Wiley & Sons, 2010.
[6] MIYAZAKI H, YOSHIZAWA Y, HIRAO K. Effect of crystallization of intergranular glassy phases on the dielectric properties of silicon nitride ceramics [J]. Materials Science and Engineering B, 2008, 148(1/2/3): 257-260.
[7] KUME S, YASUOKA M, OMURA N, WATARI K. Annealing effect on dielectric property of AlN ceramics [J]. Journal of the European Ceramic Society, 2006, 26(10/11): 1831-1834.
[8] ANGEL D P, MARIA I O, PILAR M. Effect of microstructure on the thermal conductivity of hot-pressed silicon nitride materials [J]. Journal of the American Ceramic Society, 2002, 85(1): 200-206.
[9] FURUYA K, MUNAKATA F, MATSUO K, AKIMUNE Y, YE J, OKADA A. Microstructural control of 6-silicon nitride ceramics to improve thermal conductivity [J]. Journal of Thermal Analysis and Calorimetry, 2002, 69(3): 873-879.
[10] WASANAPIARNPONG T, WADA S, IMAI M, YANO T. Thermal conductivity improvement by heat-treatment in Si3N4 ceramics using SiO2-MgO-Y2O3 additive system [J]. Key Engineering Materials, 2007, 352: 233-238.
[11] KUME S, YASUOKA M, OMURA N, WATARI K. Effects of annealing on dielectric loss and microstructure of aluminum nitride ceramics [J]. Journal of the American Ceramic Society, 2005, 88(11): 3229-3231.
[12] PARK M K, KIM H N, LEE K S, BAEK S S, KANG E S, BAEK Y K, KIM D K. Effect of microstructure on dielectric properties of Si3N4 at microwave frequency [J]. Key Engineering Materials, 2005, 287: 247-252.
[13] OHNO H. Dielectric and electrical design consideration of ceramics for fusion devices [J]. Journal of Nuclear Materials, 1991, 179/180/181: 60-63.
[14] THORP J S, SHARIF R I. Dielectric properties of some hot-pressed nitrogen ceramics [J]. Journal of Materials Science, 1977, 12(11): 2274-2280.
[15] GOLDSMID H J, PENN A W. Boundary scattering of phonons in solid solutions [J]. Physics Letters A, 1968, 27(8): 523-524.
(Edited by PENG Chao-qun)
Foundation item: Project(50872052) supported by the National Natural Science Foundation of China; Project(2009AA05Z313) supported by the National High Technology Research and Development Program of China; Project supported by the Commission of Science, Technology and Industry for National Defence, China
Received date: 2010-05-24; Accepted date: 2010-11-02
Corresponding author: YANG Jian, Associate professor, PhD; Tel: +86-25-83587262; E-mail: yangjian1976@163.com