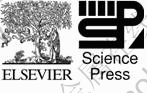
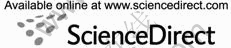
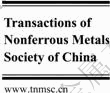
Trans. Nonferrous Met. Soc. China 22(2012) 1092-1095
Influence of spiral crystal selector on crystal orientation of single crystal superalloy
ZHANG Ru-lin1, CHEN Li-na1, LI Chong-he1, WANG Ning2, LU Xiong-gang1, REN Zhong-ming1
1. Shanghai Key Laboratory of Modern Metallurgy and Materials Processing,
Shanghai University, Shanghai 200072, China;
2. Baoshan Iron & Steel Co., Ltd., Shanghai 201900, China
Received 23 September 2011; accepted 5 January 2012
Abstract: To increase efficiency and improve performance, reducing cost and emissions, advanced single crystal Ni-based superalloys are required in aerospace propulsion and power generating gas turbines. With the development of alloy, significant improvements in casting techniques have been achieved by introducing the directionally solidified (DS) casting process followed by single crystal (SX) technique. The deviation of preferred orientation of single crystal superalloys is one of the most important defects in casting. In directional solidification equipment with high temperature gradient, single crystal specimens of DZ417G alloy were prepared successfully by the modified Bridgeman method with spiral grain selector. The orientation was investigated by means of X-ray diffraction (XRD) and electron backscattered diffraction (EBSD).The results show that the crystal selector with a smaller angle can effectively reduce the deviation of preferred orientation.
Key words: nickel-base superalloy; directional solidification; single crystal superalloy; crystal orientation; spiral grain selector
1 Introduction
Aero-engine turbine blades sit in the severe environment behind the combustor and rotate at high speed in order to extract energy from the high temperature gas stream. The need to achieve increased efficiency and performance, while reducing cost and emissions, in aerospace propulsion and power generating gas turbines requires advanced single crystal Ni-based superalloys [1-3]. With the development of alloy, significant improvements in casting techniques have been achieved over the last 30 years by introducing the directionally solidified (DS) casting process followed by single crystal (SX) technique [4]. However, newer generation single crystal alloys exhibit increased levels of solidification segregation which leads to the formation of casting defects. The transition from DS to SX was achieved by introducing a crystal selector which consists of two parts, a starter block referring to the grain orientation optimization and a spiral part to ensure that only one grain can eventually survive and grow into the blade.
Recently, it was found that the mechanical properties of the Ni-based superalloys are not isotropic [5]. For instance, blades with [001] crystal index have higher temperature creep strength compared with those with [011] or [111] index. During the growth of grains, the preferred growth direction is known to be [001]. The goal of single crystal casting is to align the [001] single crystals along the length of the turbine blade. However, this unidirectional process does not always assemble such turbine blades. The deviation of preferred orientation of single crystal superalloys from [001] often happens and it becomes one of the most important defects. In general, the product with less 10° deviation of preferred orientation is judged to be well oriented [6]. A process model is described, which is based upon a thermal analysis of the heat transfer occurring in a commercial casting furnace, and a cellular-automaton model for competitive dendrite growth [7,8]. But there are several reports about the experiment. In order to get a smaller deviation of preferred orientation, the angle of the crystal selector and the length of the spiral part were studied by experiment.
2 Experimental
Experiment was carried out in a home-made vacuum directional solidification furnace [9]. The schematic is shown in Fig. 1. In the experiment, the DZ417G alloy was used, with composition (mass fraction, %): C 0.18, Cr 8.96, Mo 3.08, Co 9.72, V 0.86, B 0.015, A1 5.41, Ti 4.50, Fe 0.23, P 0.002, S 0.002, Si 0.04, Mn 0.05 and the balance Ni. The shell mold which contained six ingots was made of the corundum. The six ingots were divided into two groups. Each group had three ingots with different angles (30°, 45° and 60°) of the selector. The difference between two groups was the length of the crystal selector: one was 15 mm and the other was 30 mm. The melt of alloy was heated and hold at 1 520 °C and the withdrawing rate was 1.5 mm/min. The macro-corrosion reagent was H2O2 (1.5 mL) + HCl (5 mL, 36.5%). Electron backscattered diffraction (EBSD) and X-ray diffraction (XRD) were used to detect the grain orientation.
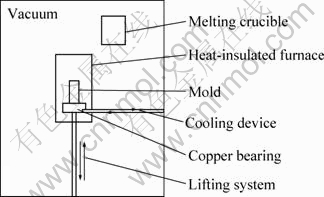
Fig. 1 Schematic of vacuum unidirectional solidification furnace
3 Result and discussion
The ingots were eroded by the macro-corrosion reagent for the macro-structure analysis and their macro-structure is shown in Fig. 2. The grain orientation was measured by EBSD and XRD. In order to facilitate the study, the ingots were marked from No. 1 to No. 6. The length of crystal selector of samples 1, 2 and 3 was 30 mm, and the length of samples 4, 5 and 6 was 15 mm. The angle of the selector for samples No.1 and 4 was 30°, No. 2 and 5 was 45°, No. 3 and 6 was 60°. All ingots were metallurgical single crystals and no grain boundary on surface could be found, as shown in Fig. 2.
The pole figures of samples for XRD analysis are shown in Fig. 3. It is found that not all of the ingots are physical single crystals, the Sample 4 has two grains and samples 3 and 5 have polycrystalline trend. HU et al [10] suggested that, only when the length of grain selection device is longer than 20 mm, the selector can play the role in the crystal selection and the unwanted grains can be eliminated. The length of spiral part of samples 4, 5 and 6 is 15 mm. It is shorter than the length suggested by HU et al (20 mm) [10], so the polycrystal and polycrystalline trend happened. In order to obtain the single crystal, the crystal selector with different angles needs an optimum length of the spiral part which is related to the angle of grain selector.
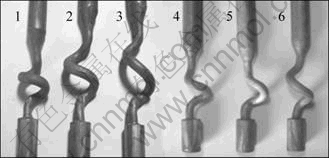
Fig. 2 Macro pictures of ingots after corrosion
In spiral geometries [11], when the angle of grain selector (α) is small, there is a little chance that the grain selection would take place in the channel of selector. In this case, almost all grains disappear at the wall of grain selector. On the other hand, when α is large, the grain selection may take place in the channel; however, the selector can not efficiently eliminate the badly oriented grains at the wall of the grain selector and guarantee the existence of only one grain. In this study, the angles used are 30°, 45° and 60°, which are not too large or too small. So, we can prepare single crystals in the three angles.
But all the single crystals that we got have a deviation of preferred orientation. The inverse pole figures of ingots obtained by EBSD are shown in Fig. 4. After calculation, the angles deviated from preferred orientation [001] are listed in Table 1. Only Sample 1, which had a deviation of preferred orientation [001] less than 10°, was judged to be well oriented.
Almost all the simulations show the spiral grain selector can quickly but randomly select one grain with no optimization on the grain orientations [12-15]. But it needs a large amount of experiments to prove. Our present experiments find that there may be some relation between the angle and the grain orientations.
In conclusion, there is an appropriate angle of grain selector to get optimal orientation. From the result, we can see that the crystal selector with a smaller angle can effectively reduce the deviation of preferred orientation. In this study, the appropriate angle of grain selector is around 30°.
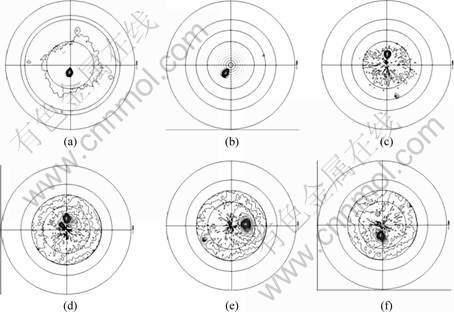
Fig. 3 Pole figures of six ingots: (a) Sample 1; (b) Sample 2; (c) Sample 3; (d) Sample 4; (e) Sample 5; (f) Sample 6
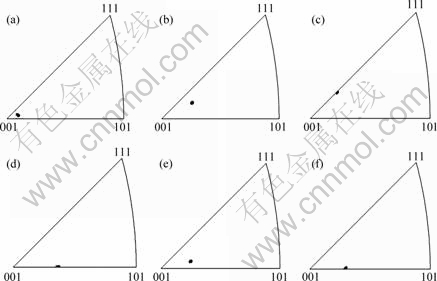
Fig. 4 Inverse pole figures of six ingots: (a) Sample 1; (b) Sample 2; (c) Sample 3; (d) Sample 4; (e) Sample 5; (f) Sample 6
Table 1 Angle deviated from preferred orientation [001] of samples 1-6
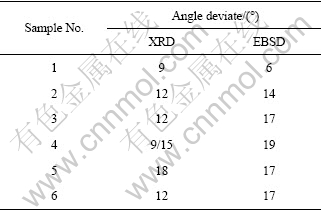
4 Conclusions
1) The spiral of the crystal selector possesses the great influence on crystal orientation of single crystal blade prepared by the high rapid solidification.
2) In order to obtain the single crystal with a smaller deviation of preferred orientation, the length of the spiral part must be longer than 20 mm and the optimum length is related to the angle of grain selector.
3) The crystal selector with a smaller angle can effectively reduce the deviation of preferred orientation. The appropriate angle of grain selector to get optimal orientation is found to be around 30°.
References
[1] CARONA P, TASADDUP K. Evolution of Ni-based superalloys for single crystal gas turbine blade applications [J]. Aerospace Science and Technology, 1999, 3(8): 513-523.
[2] VERON M, BRECHET Y, LOUCHET F. Directional coarsening of Ni-based superalloys: Computer simulation at the mesoscopic level [J]. Acta Materialia, 1996, 44(9): 3633-3641.
[3] FURRER D, FECHT H. Ni-based superalloys for turbine discs [J]. Metals and Materials Society, 1999, 51(1): 14-17.
[4] SEO S M, KIM I S, LEE J H, JO C Y, MIYAHARA H, OGI K. Grain structure and texture evolutions during single crystal casting of the Ni-base superalloy CMSX-4 [J]. Met Mater Int, 2009, 15(3): 391-398.
[5] DONG H B. Analysis of grain selection during directional solidification of gas turbine blades[J]. Proceedings of the World Congress on Engineering, 2007, 2(4): 978-988.
[6] ESAKA H, SHINOZUKA K, TAMURA M. Analysis of single crystal casting process taking into account the shape of pigtail [J]. Materials Science and Engineering A, 2005, 413-414(15): 151-155.
[7] GANDIN C A, RAPPAZ M. A coupled finite element-cellular automaton model for the prediction of dendritic grain structures in solidification processes [J]. Acta Metallurgica et Materialia, 1994, 42(7): 2233-2246.
[8] GANDIN C A, RAPPAZ M, TINTILLIER R. Three-dimensional probabilistic simulation of solidification grain structures: Application to superalloy precision castings [J]. Metallurgical and Materials Transactions A, 1993, 24(2): 467-479.
[9] LI Chong-he, GUO Zi-ming, ZHU Ming, LU Xiong-gang, YE Xiao-su, ZHAI Qi-jie. Preparation of single crystal of TiNi alloy and its shape memory performance [C]//LENG Jin-song, ASUNDI A K, ECKE W. 2nd International Conference on Smart Materials and Nanotechnology in Engineering. Weihai: Proc of SPIE, 2009.
[10] FU Heng-zhi, GUO Jing-jie, LIU Lin, LI Jin-shan. Directional solidification and processing of advanced materials [M]. Beijing: Science Press, 2008: 538. (in Chinese)
[11] CARTER P, COX D C, GANDIN C A, REED R C. Process modeling of grain selection during the solidification of single crystal superalloy castings [J]. Materials Science and Engineering A, 2000, 280: 233-246.
[12] DAI H J, GEBELIN J C, NEWELL M, REED R C, D’SOUZA N, BROWN P D, DONG H B. Grain selection during solidification in spiral grain selector [C]//REED R C, GREEN K A, CARON P, GABB T P, FAHRMANN M G, HURON E S, WOODARD S A. Superalloys, 2008. TMS: 367-372.
[13] DAI H J, GEBELIN J C, REED R C, D’SOUZA N, BROWN P D, DONG H B. Effect of spiral shape on grain selection during casting of single crystal turbine blades [J]. International Journal of Cast Metals Research, 2009, 22(1-4): 54-57.
[14] PAN Dong, XU Qing-yan, LIU Bai-cheng, LI Jia-rong, YUAN Hai-long, JIN Hai-peng. Modeling of grain selection during directional solidification of single crystal superalloy turbine blade castings [J]. Metals and Materials Society, 2010, 62(5): 30-34.
[15] RAPPAZ M, GANDIN C A, DESBIOLLES J L, THEVOZ P. Prediction of grain structures in various solidification processes [J]. Metallurgical and Materials Transactions A, 1996, 27(3): 695-705.
螺旋选晶器对单晶高温合金晶粒取向的影响
张如林1,陈丽娜1,李重河1,王 宁2,鲁雄刚1,任忠鸣1
1. 上海大学 上海市现代冶金及材料制备重点实验室,上海 200072;
2. 宝山钢铁股份有限公司,上海 201900
摘 要:对于航天推进和发电燃气轮机,为了实现更高的效率和性能并同时降低成本和排放,需要发展先进的镍基单晶高温合金。随着合金的发展,合金的铸造技术已经从定向凝固(DS)发展到单晶(SX)。单晶取向与择优取向的偏差已经成为单晶高温合金最重要的铸造缺陷之一。在自行设计的高温度梯度定向凝固装置中,采用改进的Bridgeman法,用螺旋选晶器拉制出DZ417G合金的单晶。使用XRD和EBSD对其取向进行分析研究。 结果表明:较小角度的螺旋选晶器可以有效地减少单晶取向与择优取向的偏差。
关键词:镍基高温合金;定向凝固;单晶高温合金;晶粒取向;螺旋选晶器
(Edited by YANG Hua)
Foundation item: Project (51074105) supported by the National Natural Science Foundation of China; Projects (08DZ1130100, 10520706400) supported by the Science and Technology Commission of Shanghai Municipality, China; Project (2007CB613606) supported by the National Basic Research Program of China
Corresponding author: LI Chong-he; Tel: +86-21-56332934; E-mail: chli@staff.shu.edu.cn
DOI: 10.1016/S1003-6326(11)61288-0