DOI: 10.11817/j.issn.1672-7207.2021.05.021
基于切削理论的数字钻探参数与岩石单轴抗压强度关系研究
江贝1,马凤林1,王琦1, 2,刘悦2, 3,李术才2,何满潮1,魏华勇1
(1. 中国矿业大学 (北京) 深部岩土力学与地下工程国家重点实验室,北京,100083;
2. 山东大学 岩土与结构工程研究中心,山东 济南,250061;
3. 山东高速集团有限公司,山东 济南,250100)
摘要:为实现岩石力学参数的现场实时测试,利用数字钻探技术准确获取岩石单轴抗压强度,考虑钻进过程中岩石碎屑对切削荷载的影响,建立基于岩石碎屑区的切削力学模型。基于该模型得到数字钻探参数与碎屑区边界压力(碎屑压力)的关系式,结合数字钻探试验结果建立数字钻探参数与岩石单轴抗压强度关系模型(DP-σc模型),将该模型应用于岩石单轴抗压强度的随钻测试,并验证基于DP-σc模型实时获取岩石单轴抗压强度的有效性。研究结果表明:通过随钻测试反演得到的岩石单轴抗压强度与室内单轴压缩试验结果差异率平均值小于5%,建立的DP-σc模型应用于岩石单轴抗压强度的随钻测试是合理、有效的。
关键词:钻探参数;岩石碎屑区;碎屑压力;单轴抗压强度;随钻测试
中图分类号:TU45 文献标志码:A
文章编号:1672-7207(2021)05-1601-09
Research of relationship between digital drilling parameters and rock uniaxial compressive strength based on cutting theory
JIANG Bei1, MA Fenglin1, WANG Qi1, 2, LIU Yue2, 3, LI Shucai2, HE Manchao1, WEI Huayong1
(1. State Key Laboratory for Geo-mechanics and Deep Underground Engineering, China University of Mining & Technology(Beijing), Beijing 100083, China;
2. Research Center of Geotechnical and Structural Engineering, Shandong University, Jinan 250061, China;
3. Shandong Hi-Speed Group Co. Ltd., Jinan 250100, China)
Abstract: In order to realize the real-time testing of rock mechanics parameters and accurately obtain rock uniaxial compressive strength by using digital drilling technology, the cutting mechanics model based on rock crushing zone was established, considering the influence of rock crushing zone on cutting load during drilling. The relationship between digital drilling parameters and rock crushing zone boundary pressure(crushing pressure) was obtained. Combined with the digital drilling test results, the relationship model of digital drilling parameters and rock uniaxial compressive strength (DP-σc model) was obtained, which was applied to the drilling measurement of rock uniaxial compressive strength. Based on this, the validity of drilling measurement of rock uniaxial compressive strength based on DP-σc model was verified. The results show that the average difference rate of rock uniaxial compressive strength obtained by drilling test and uniaxial compression test is less than 5%. The DP-σc model is effective and reasonable when it is applied in the drilling measurement of rock uniaxial compressive strength.
Key words: drilling parameters; rock crushing zone; crushing pressure; uniaxial compressive strength; drilling measurement
近年来,我国地下工程迅速发展,规模逐步增大,受复杂地质条件的影响,地下工程灾害频发[1-3]。围岩分级是地下工程施工的基础,为减少工程灾害的发生,需根据围岩分级对支护参数进行设计和优化,以增强围岩稳定性控制。岩石单轴抗压强度是反映岩体性质的重要力学参数,其准确获取对于围岩分级和围岩支护参数设计具有重要意义。目前,最常用的单轴抗压强度测试方法为室内单轴压缩试验,但该方法试验步骤复杂、成本高,无法对破碎围岩进行有效测试,且测试结果无法反映围岩取芯前未经扰动的应力状态[4-6]。现场测试方法可实时获取岩石力学参数,点荷载法是现场测试岩石强度的主要方法之一,但在测试过程中,试件在点荷载的作用下发生拉应力诱导的劈裂破坏,破坏机制与岩石压缩破坏机制不同,导致不同种类岩石的点荷载强度与单轴抗压强度的转换系数明显不同,故该测试方法的精度较低,无法完全应用在实际工程中[7-9]。数字钻探技术是一种对钻进过程中数字钻探参数准确控制和监测的技术,数字钻探参数包括钻速、转速、切削扭矩、钻进压力等,在钻进过程中,数字钻探测试系统对部分参数进行定量控制和监测[10-13]。大量现场和室内数字钻探试验结果表明,数字钻探参数与岩石力学参数密切相关[14-16],该研究结果为岩石力学参数的测试提供了新思路。KAHRAMAN等[17]通过对部分数字钻探参数与岩石单轴抗压强度关系的定性研究,建立了钻进速度与岩石单轴抗压强度的经验公式;HUANG等[18-19]基于钻进试验建立了不同的预测模型,用于预测不同类型岩石的单轴抗压强度;YASAR等[20]对试验数据进行统计分析,提出了钻速和钻速比能与岩石单轴抗压强度的经验公式。以上研究过程均假设钻头切削刃与被切削岩块直接接触。LIU等[21-22]通过室内试验研究岩石切削过程,发现钻头切削岩石过程中切削刃与被切削岩石之间存在粉末状碎屑区即岩石碎屑区。WANG等[23-24]进行了室内试验和理论分析,研究岩石碎屑对钻头切削荷载的影响,证明岩石碎屑区改变了切削力的大小和钻头荷载的传递方向,对岩石力学参数与钻头切削力的研究具有重要影响,在岩石切削研究中不可忽略。国内外学者大多通过室内试验分析了岩石碎屑的形成过程与分布规律,XUE等[24-25]引入岩石碎屑区的概念建立岩石切削力学模型,提出了切削力与岩石力学参数的关系式,但未将其用于获取岩石单轴抗压强度。为更加真实地考虑岩石碎屑对切削荷载的影响,本文作者建立基于岩石碎屑区的切削力学模型,计算数字钻探参数与碎屑区边界压力σ0(以下简称碎屑压力)的关系式,基于室内试验结果建立岩石单轴抗压强度与σ0的关系,从而得到数字钻探参数DP(drilling parameter)与岩石单轴抗压强度关系模型(DP-σc模型),将该模型应用于岩石单轴抗压强度的随钻测试,并验证基于DP-σc模型实时获取岩石单轴抗压强度的有效性。
1 数字钻探参数与碎屑压力理论分析
1.1 岩石切削力学模型建立
本文作者团队自主研发了具有3列切削刃的金刚石复合片(polycrystalline diamond compact,PDC)钻头,该钻头切削刃的金刚石复合片形状为方形,其形状和受力特征不会因钻进过程中切削刃的磨损而改变,因此,可减少切削刃磨损对试验数据的影响。对该钻头切削岩石过程进行分析,建立岩石切削力学模型,研究切削刃与岩石之间的相互作用,如图1所示。在岩石切削过程中,切削刃绕钻头轴线旋转,对接触岩石进行切削,切削刃前方岩石首先破碎产生粉末状岩屑,由于切削刃具有一定的倾角,破碎岩屑在切削刃与岩石之间被挤压形成岩石碎屑区。
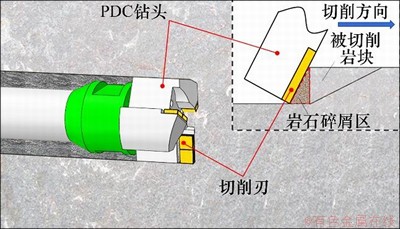
图1 钻头切削岩石过程示意图
Fig. 1 Schematic diagram of rock cutting by drill bit
为对钻头切削岩石过程进行受力分析,计算数字钻探参数与碎屑压力的关系式,根据岩石的切削破坏特征,建立岩石切削力学模型时依据以下假设:
1) 钻头单列切削刃旋转1周的钻进距离远比切削刃与岩石的接触长度小,因此,钻头周期性切削岩石的过程可简化为线性过程;
2) 根据PRYHOROVSKA等[26]的研究,岩石切削过程中旋转运动和线性运动本质相似,故可将钻头切削岩石问题转化为求解平面应变问题;
3) 钻头切削力远比切削破坏的岩石重力大,因此,本文不考虑岩石重力对切削过程的影响。
取钻头的1列切削刃建立岩石切削力学模型,如图2所示,沿钻头旋转方向的切向建立x轴,沿钻进方向建立y轴。图2中,α为切削刃倾角;Fc为钻头切削刃对被切削岩块的作用力;γ为钻头切削角,表示作用力Fc与切削刃法线方向的夹角;Fb为切削刃底部对原岩的作用力;δ为作用力Fb与竖直方向的夹角,同时也为切削刃底部与原岩之间的摩擦角;d为钻头的切削深度;Fc与Fb分别由x和y这2个方向的分力组成;其中
为岩石切削力,
为切削刃底部与原岩之间的摩擦力,
为Fb在y轴的分力;σ0为碎屑区边界压力;f0为岩石碎屑区与岩石之间的摩擦力。
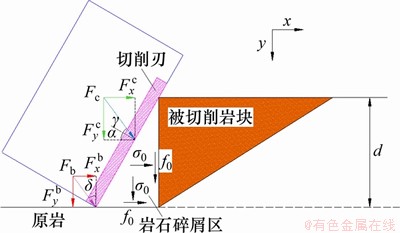
图2 岩石切削力学模型
Fig. 2 Mechanical model of rock cutting
1.2 碎屑压力分析
为研究数字钻探参数与碎屑压力的关系,对岩石切削过程进行受力分析。钻头切削刃的作用力如图2所示,
和
与钻头钻进压力有关,满足以下关系:
(1)
(2)
定义岩石碎屑区对岩石的压应力σ0为碎屑区边界压力,经计算可知:
(3)
式中:f0为岩石碎屑区与岩石之间的摩擦力;
,为岩石碎屑区与岩石之间的摩擦因数;
为摩擦角。
以岩石碎屑区为研究对象进行受力分析,建立平衡方程:
(4)
(5)
PDC钻头在钻进过程中产生的钻进压力FN由
和
共同组成,满足:
(6)
将式(6)与式(2)、式(5)进一步联立得
(7)
式中:
;v为钻头的钻进速度;N为钻头转速;m为切削刃列数;L1,L2和L3分别为3列切削刃的长度。
在岩石切削过程中,
对钻头中心产生扭矩Mc,用于钻头切削岩石;
对钻头中心产生扭矩Mf,用于克服钻头与原岩之间的摩擦力。
图3所示为PDC钻头和单列切削刃示意图,设切削刃上任一位置距钻头中心的距离为r,任一微段长度为dr,则任一微段上的力对钻头中心产生的扭矩
为
(8)
式中:
为岩石切削力
对钻头中心产生的扭矩;
为切削刃底部与原岩石之间的摩擦力
对钻头中心产生的扭矩。
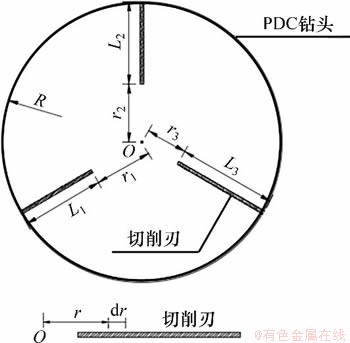
图3 PDC钻头和单列切削刃示意图
Fig. 3 Schematic diagram of PDC drill bit and cutting edge
将切削刃任一微段产生的扭矩dM沿切削刃长度方向积分,得到该切削刃对钻头中心产生的扭矩,3列切削刃产生的扭矩之和即为切削扭矩M:

(9)
将式(4)、式(7)代入式(9),可得数字钻探参数与碎屑压力的关系式为

(10)
进一步反推式(10)可得碎屑压力为

(11)
以上理论分析得到了数字钻探参数与碎屑压力的关系式。为建立数字钻探参数与岩石单轴抗压强度关系模型(DP-σc模型),需通过数字钻探试验获取数字钻探参数,计算得到具体的碎屑压力σ0,将σ0与单轴压缩试验获取的岩石单轴抗压强度σc进行拟合,建立σ0与σc的关系,从而得到DP-σc模型。
2 数字钻探试验
2.1 试验设备
为研究岩石单轴抗压强度σc与碎屑压力σ0的关系,利用本文作者团队自主研发的室内岩石钻探测试系统对不同强度的砂岩和砂浆试件进行数字钻探试验。该系统配备了符合岩石切削力学模型的PDC钻头,包括钻进系统、加载系统、压力室装置及监测控制系统,同时对钻进过程中的数字钻探参数进行控制、监测与分析,如图4所示,钻进主体装置整体长×宽×高为1 750 mm×2 350 mm×4 335 mm,钻杆推力范围为0~50 kN,计算σ0所需的钻头具体参数如表1所示。
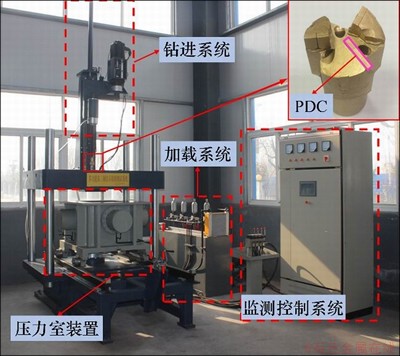
图4 岩石钻探测试系统与PDC钻头
Fig. 4 Rock drilling test system and PDC drill bit
表1 PDC钻头尺寸参数
Table 1 Dimension parameters of PDC drill bit mm

2.2 试验方案
2.2.1 试件及配比方案
试验选用的砂岩和砂浆试件共36组,试件长×宽×高为150 mm×150 mm×230 mm。砂岩试件共8组(S1~S8),为补充试验数据以提高试验结果的准确性,配制了7种不同等级强度的砂浆试件共28组(J1~J28)。不同强度砂浆试件的配合比如表2所示,其中强度等级为M15及以下的水泥砂浆,水泥强度等级为32.5;强度等级超过M15的水泥砂浆,水泥强度等级为42.5。
表2 不同砂浆强度配合比
Table 2 Mortar ratio of different strength grades
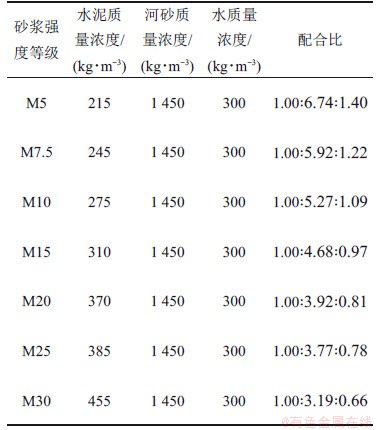
2.2.2 钻探与取芯方案
利用室内岩石钻探测试系统对各试件进行数字钻探试验,采用控制钻速v和转速N,监测扭矩M和钻进压力FN的钻探模式,钻进深度为110 mm,各试件设定的v和N方案如表3所示。
表3 钻进方案
Table 3 Drilling schemes
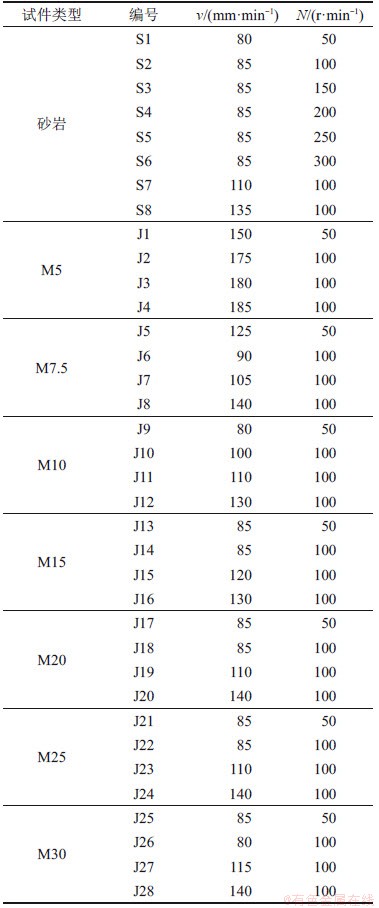
对钻进后试件进行取芯,制作标准岩芯试件,进行单轴压缩试验获取试件的单轴抗压强度,取芯后的试件如图5所示。
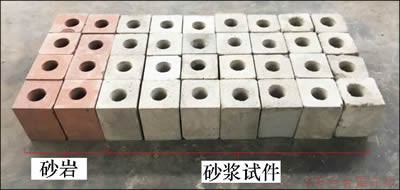
图5 取芯后试件
Fig. 5 Specimens after coring
2.3 试验结果与理论计算分析
2.3.1 试验结果分析
根据试验方案对各试件开展数字钻探试验,获取钻探过程中的数字钻探参数,以方案S5为例,v设定为85 mm/min,N设定为250 r/min,试验监测M和FN随钻进深度Dh的变化曲线分别如图6和图7所示。
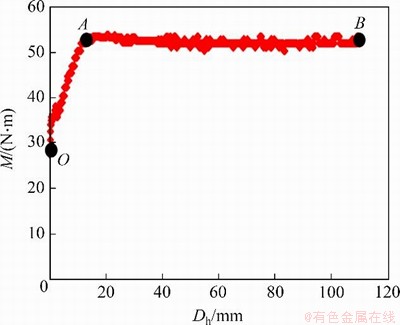
图6 扭矩M随钻进深度Dh的变化
Fig. 6 Variations of torque M versus drilling depth Dh
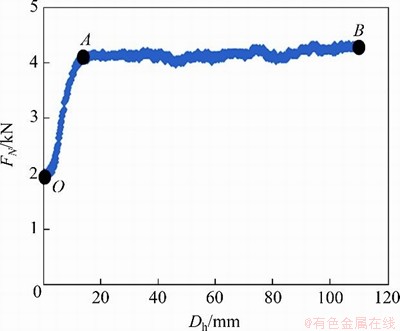
图7 钻进压力FN随钻进深度Dh的变化
Fig. 7 Variations of drilling pressure FN versus drilling depth Dh
由图6和图7可知:M与FN随Dh的变化规律相似,结合变化曲线分析,PDC钻头切削岩石的过程主要分为以下2个阶段。
1) 上升阶段(OA段):当钻头与岩石表面接触时,由于钻进过程中的切削力、摩擦力和钻进压力迅速增大,M和FN在极小的Dh内急剧上升。
2) 稳定阶段(AB段):钻头钻进岩石一定深度后,M和FN达到钻进所需的扭矩和钻进压力,故随钻头推进,M和FN不再上升,由于岩石试件材料的不均匀性,M和FN在小范围内上下波动,整体趋于稳定,直至试验结束。
在钻头与岩石接触前,由于钻探测试系统部件之间的摩擦,钻头空转会产生稳定的初始扭矩,M和FN存在一定的初始值。各方案扭矩M和钻进压力FN的试验值取值方法相同,以M为例进行说明:试件接触岩石前的初始扭矩用MI表示,稳定阶段扭矩的平均值用MS表示,试件扭矩试验值为M=MS-MI。以方案S5的试验数据为例,MI=24 MPa,MS=52 MPa,则M=MS-MI=28 MPa。
2.3.2 理论计算与室内试验结果关系分析
在36组试验方案中随机选取30组,对其试验结果进行计算分析,PDC钻头的几何参数见表1;根据已有研究成果[27-28],PDC钻头切削角γ与切削刃倾角α有关,本文所选钻头的倾角α为15°,对应切削角γ取值为18°,钻头底部摩擦角δ取值为12°;岩屑破碎区摩擦角
可由式(1)反推得到;v和N选用每个方案的实际值,将上述参数以及扭矩M、钻进压力FN代入式(11),可求得碎屑压力σ0,如表4所示。
表4 室内试验及理论分析结果
Table 4 Results of digital drilling tests and theoretical analysis
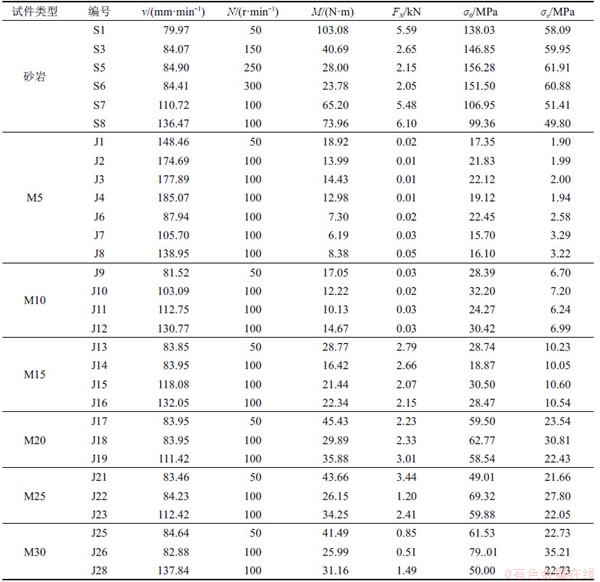
将各试件理论分析得到的碎屑压力σ0与单轴压缩试验得到的岩石单轴抗压强度σc进行统计分析,进一步建立数字钻探参数与单轴抗压强度关系模型(DP-σc模型)。
3 DP-σc模型
3.1 DP-σc模型建立
基于表4中30组试件的试验及理论分析数据,绘制σ0-σc散点图,并对数据进行拟合,确定σc与σ0之间的关系,如图8所示。由图8可知:σc与σ0呈非线性关系,且σc随σ0的增大而增大,最佳拟合曲线的拟合度
,表明分析数据离散性较低,且拟合度较高。
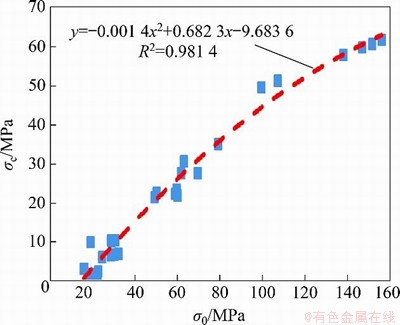
图8 岩石单轴抗压强度σc与碎屑压力σ0关系分析
Fig. 8 Analysis of relation between rock uniaxial compressive strength σc and rock cutting strength σ0
基于σ0-σc的最优拟合曲线,可得到岩石单轴抗压强度σc与碎屑压力σ0的关系式为
(12)
联立式(12)与式(11),可得DP-σc模型:

(13)
式中:
,定义为切削系数。
3.2 DP-σc模型应用效果
基于试验数据建立的DP-σc模型可应用于岩石单轴抗压强度的随钻测试,即:将钻探过程中的数字钻探参数(v,N,FN和M)以及所用钻头的几何参数代入式(13),求解岩石单轴抗压强度。
根据表4以外的6组试验数据,对DP-σc模型应用于岩石单轴抗压强度随钻测试的有效性进行验证,各试件钻进过程中的数字钻探参数v,N,M和FN以及通过单轴压缩试验获得的σc见表5。
为定量评估通过DP-σc模型计算得到的岩石单轴抗压强度理论值与通过室内单轴压缩试验获取的岩石单轴抗压强度试验值的差异,建立差异率λ,其计算方式如下:
(14)
式中:T
为通过DP-σc模型计算得到的岩石单轴抗压强度理论值;E
为通过室内单轴压缩试验获取的岩石单轴抗压强度试验值。
表5 用于DP-σc模型验证的相关数据
Table 5 Relevant data for verification of DP-σc model
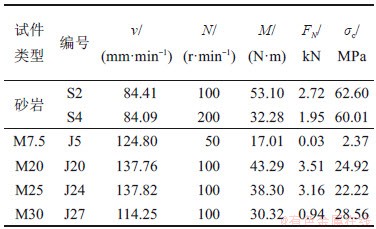
由图9可知:T
与E
的差异率较小,所选6组验证方案的差异率均在9%以内,且平均值为4.06%,证明了本文建立的DP-σc模型应用于岩石单轴抗压强度随钻测试是合理、有效的。基于本文对数字钻探参数与岩石单轴抗压强度的研究,针对不同类型岩石进一步开展数字钻探试验和单轴压缩试验,可建立适用于各类岩体的DP-σc模型,应用于各类工程岩体单轴抗压强度的现场测试。
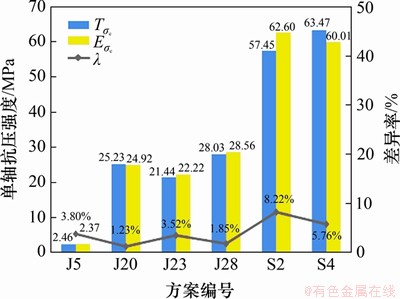
图9 单轴抗压强度理论值与试验值对比
Fig. 9 Comparisons of theoretical value and experimental value of uniaxial compressive strength
4 结论
1) 考虑岩石碎屑区对切削荷载的影响,建立了基于岩石碎屑区的切削力学模型,得到了数字钻探参数与碎屑压力σ0的关系式。
2) 利用室内岩石钻探测试系统对岩石试件进行数字钻探试验,获取数字钻探参数,计算得到碎屑压力σ0,对σ0与单轴压缩试验测得的单轴抗压强度σc进行拟合,建立了σ0与σc的关系,得到了DP-σc模型。
3) 通过DP-σc模型计算得到的T
与单轴压缩试验测定的E
差异率平均值为4.06%,证明了本文建立的DP-σc模型应用于岩石单轴抗压强度的随钻测试是合理、有效的。
参考文献:
[1] 何满潮, 谢和平, 彭苏萍, 等. 深部开采岩体力学研究[J]. 岩石力学与工程学报, 2005, 24(16): 2803-2813.
HE Manchao, XIE Heping, PENG Suping, et al. Study on rock mechanics in deep mining engineering[J]. Chinese Journal of Rock Mechanics and Engineering, 2005, 24(16): 2803-2813.
[2] WANG Qi, JIANG Bei, PAN Rui, et al. Failure mechanism of surrounding rock with high stress and confined concrete support system[J]. International Journal of Rock Mechanics and Mining Sciences, 2018, 102: 89-100.
[3] 饶军应, 傅鹤林, 刘运思, 等. 管状填充性椭圆形溶洞的围岩应力弹性解析分析[J]. 中南大学学报(自然科学版), 2015, 46(7): 2605-2612.
RAO Junying, FU Helin, LIU Yunsi, et al. Stress analysis of rocks surrounding a tubular filled elliptical Karst cave with complex function of elastic mechanics[J]. Journal of Central South University(Science and Technology), 2015, 46(7): 2605-2612.
[4] PINCUS H J. Round one-longitudinal and transverse pulse velocities, unconfined compressive strength, uniaxial elastic modulus, and splitting tensile strength[J]. Geotechnical Testing Journal, 1993, 16(1): 138-163.
[5] CERYAN N. Application of support vector machines and relevance vector machines in predicting uniaxial compressive strength of volcanic rocks[J]. Journal of African Earth Sciences, 2014, 100: 634-644.
[6] 傅鹤林, 张加兵, 伍毅敏, 等. 低温冻结条件下板岩破坏类型及单轴抗压强度试验研究[J]. 中南大学学报(自然科学版), 2017, 48(11): 3051-3059.
FU Helin, ZHANG Jiabing, WU Yimin, et al. Experimental study of failure forms and uniaxial compressive strength for slate under low temperature[J]. Journal of Central South University(Science and Technology), 2017, 48(11): 3051-3059.
[7] KAHRAMAN S. The determination of uniaxial compressive strength from point load strength for pyroclastic rocks[J]. Engineering Geology, 2014, 170: 33-42.
[8] SINGHT N, KAINTHOLA A, VENKATESH A. Correlation between point load index and uniaxial compressive strength for different rock types[J]. Rock Mechanics and Rock Engineering, 2012, 45(2): 259-264.
[9] 郭曼丽. 试论岩石点荷载试验的适用性[J]. 岩土力学, 2003, 24(3): 488-489.
GUO Manli. Discussion on adaptability of point load test of rocks[J]. Rock and Soil Mechanics, 2003, 24(3): 488-489.
[10] CHEN Jian, YUE Zhongqi. Ground characterization using breaking-action-based zoning analysis of rotary-percussive instrumented drilling[J]. International Journal of Rock Mechanics and Mining Sciences, 2015, 75: 33-43.
[11] 王琦, 高红科, 蒋振华, 等. 地下工程围岩数字钻探测试系统研发与应用[J]. 岩石力学与工程学报, 2020, 39(2): 301-310.
WANG Qi, GAO Hongke, JIANG Zhenhua, et al. Development and application of a surrounding rock digital drilling test system of underground engineering[J]. Chinese Journal of Rock Mechanics and Engineering, 2020, 39(2): 301-310.
[12] YANG W W, YUE Z Q, THAML G. Automatic monitoring of inserting or retrieving SPT sampler in drillhole[J]. Geotechnical Testing Journal, 2012, 35(3): 420-436.
[13] KOVALYSHEN Y. Self-excited axial vibrations of a drilling assembly: modeling and experimental investigation[C]// Proceedings of the 47th US Rock Mechanics/Geomechanics Symposium. San Francisco, USA: Curiran Associates Inc, 2013: 23-26.
[14] AALIZAD S A, RASHIDINEJAD F. Prediction of penetration rate of rotary-percussive drilling using artificial neural networks-a case study[J]. Archives of Mining Science, 2012, 57(3): 715-728.
[15] van WYK G, ELS D N J, AKDOGAN G, et al. Discrete element simulation of tribological interactions in rock cutting[J]. International Journal of Rock Mechanics and Mining Sciences, 2014, 65: 8-19.
[16] 岳中琦. 钻孔过程监测(DPM)对工程岩体质量评价方法的完善与提升[J]. 岩石力学与工程学报, 2014, 33(10): 1977-1996.
YUE Zhongqi. Drilling process monitoring for refining and upgrading rock mass quality classification methods[J]. Chinese Journal of Rock Mechanics and Engineering, 2014, 33(10): 1977-1996.
[17] KAHRAMAN S, BILGIN N, FERIDUNOGLU C. Dominant rock properties affecting the penetration rate of percussive drills[J]. International Journal of Rock Mechanics and Mining Sciences, 2003, 40(5): 711-723.
[18] HUANG S L, WANG Z W. The mechanics of diamond core drilling of rocks[J]. International Journal of Rock Mechanics and Mining Sciences, 1997, 34(3/4): 612.
[19] MONJEZI M, KHOSHALAN H A, RAZIFARD M. A neuro-genetic network for predicting uniaxial compressive strength of rocks[J]. Geotechnical and Geological Engineering, 2012, 30(4): 1053-1062.
[20] YASAR E, RANJITH P G, VIETE D R. An experimental investigation into the drilling and physico-mechanical properties of a rock-like brittle material[J]. Journal of Petroleum Science and Engineering, 2011, 76(3/4): 185-193.
[21] LIU Weiji, ZHU Xiaohua. Experimental study of the force response and chip formation in rock cutting[J]. Arabian Journal of Geosciences, 2019, 12: 457-468.
[22] CHENG Zhen, SHENG Mao, LI Gensheng,et al. Cracks imaging in linear cutting tests with a PDC cutter: characteristics and development sequence of cracks in the rock[J]. Journal of Petroleum Science and Engineering, 2019, 179: 1151-1158.
[23] WANG Fuzeng, LIU Shuying, GUO Ziyu,et al. Analysis of cutting forces and chip formation in milling of marble[J]. The International Journal of Advanced Manufacturing Technology, 2020, 108(9/10): 2907-2916.
[24] XUE Jing, XIA Yimin, JI Zhiyong. Soft rock cutting mechanics model of TBM cutter and experimental research[C]// Intelligent Robotics & Applications, Second International Conference. Icira, Singapore: ICIRA, 2009: 383-391.
[25] CHE Demeng, ZHU Wule, EHMANN K F. Chipping and crushing mechanisms in orthogonal rock cutting[J]. International Journal of Mechanical Sciences, 2016, 119: 224-236.
[26] PRYHOROVSKA T O, CHAPLINSKIY S S, KUDRIAVTSEV I O. Finite element modelling of rock mass cutting by cutters for PDC drill bits[J]. Petroleum Exploration and Development, 2015, 42(6): 888-892.
[27] HUANG H, LECAMPION B, DETOURNAY E. Discrete element modeling of tool-rock interaction I: rock cutting[J]. International Journal for Numerical and Analytical Methods in Geomechanics, 2013, 37(13): 1913-1929.
[28] YAHIAOUI M, PARIS J Y, DELBE K, et al. Independent analyses of cutting and friction forces applied on a single polycrystalline diamond compact cutter[J]. International Journal of Rock Mechanics and Mining Sciences, 2016, 85: 20-26.
(编辑 刘锦伟)
收稿日期: 2020 -07 -30; 修回日期: 2020 -09 -15
基金项目(Foundation item):国家自然科学基金资助项目(42077267,52074164,51874188);国家重大科研仪器研制项目(51927807);山东省重大科技创新工程项目(2019SDZY04);山东省高等学校青创科技支持计划项目(2019KJG013) (Projects(42077267, 52074164, 51874188) supported by the National Natural Science Foundation of China; Project(51927807) supported by the Program of National Major Scientific Research Equipment; Project(2019SDZY04) supported by the Major Scientific and Technological Innovation Project of Shandong Province; Project(2019KJG013) supported by the Shandong Province Higher Educational Youth Innovation Science and Technology Program)
通信作者:王琦,博士,教授,从事复杂条件地下工程围岩破坏机理及控制技术研究;E-mail:chinawangqi@163.com
引用格式: 江贝, 马凤林, 王琦, 等. 基于切削理论的数字钻探参数与岩石单轴抗压强度关系研究[J]. 中南大学学报(自然科学版), 2021, 52(5): 1601-1609.
Citation: JIANG Bei, MA Fenglin, WANG Qi, et al. Research of relationship between digital drilling parameters and rock uniaxial compressive strength based on cutting theory[J]. Journal of Central South University(Science and Technology), 2021, 52(5): 1601-1609.