

NaCl溶液腐蚀后304不锈钢的超声空蚀特征
陈杰,刘海霞,刘光磊,魏笑,邓濯,欧阳亚东
(江苏大学 材料科学与工程学院,江苏 镇江,212013)
摘要:对经NaCl溶液腐蚀后的304不锈钢进行符合ASTM G32标准的超声空蚀实验,从试样的质量损失、表面显微组织、表面形貌、表面粗糙度、显微硬度和残余应力等方面探究靶距和空蚀时间对空蚀的影响。研究结果表明:与未腐蚀试样相比,经NaCl溶液腐蚀后的304不锈钢的抗空蚀能力增强。在空蚀后期,疲劳损伤为空蚀破坏的主要原因,随着空蚀时间的延长,试样表面的裂纹增多,空蚀坑变深,但局部靶距的增加使表面整体的粗糙度在空蚀240 min后变化不明显。靶距对空蚀的影响明显大于空蚀时间的影响。当空蚀时间一定,靶距为0.4 mm时,试样的累积质量损失和表面粗糙度均达到最大,在该靶距条件下,加工硬化层厚度为250 μm,硬度最大值出现在距离空蚀表面50 μm处,而当靶距为0.6 mm时,残余应力达到最大。
关键词:304不锈钢;NaCl溶液;腐蚀;空蚀
中图分类号:TG178 文献标志码:A 开放科学(资源服务)标识码(OSID)
文章编号:1672-7207(2021)05-1436-10
Ultrasonic cavitation erosion behavior of 304 stainless steel after corrosion in NaCl solution
CHEN Jie, LIU Haixia, LIU Guanglei, WEI Xiao, DENG Zhuo, OUYANG Yadong
(School of Materials Science and Engineering, Jiangsu University, Zhenjiang 212013, China)
Abstract: An ultrasonic cavitation erosion experiment, which conforms to the ASTM G32 standard, was carried out on 304 stainless steel after corrosion in the NaCl solution. The effects of standoff distance and cavitation erosion time were described through mass loss, surface microstructure, surface morphology, surface roughness, microhardness and residual stress. The results show that the capability of resisting cavitation erosion of 304 stainless steel corroded in the NaCl solution is enhanced compared to that of non-corroded samples. In the later stage of cavitation erosion, fatigue damage is the main cause of cavitation damage .With the extension of cavitation erosion time, microcracks in the eroded surface increase and the depth of cavitation erosion pits increases as well, but the surface roughness varies insignificantly after cavitation erosion of 240 min due to the increase of local standoff distance. The effect of standoff distance on cavitation erosion is more remarkable than that of the cavitation erosion time. At certain cavitation erosion time, both the cumulative mass loss and the cumulative mass loss rate arrive at their maxima at a standoff distance of 0.4 mm. At this standoff distance, the thickness of the hardened layer reaches 250 μm, the maximum hardness arises at the depth of 50 μm, but the highest residual stress occurs at a standoff distance of 0.6 mm.
Key words: 304 stainless steel; NaCl solution; corrosion; cavitation erosion
空化是发生在液体内部的复杂相变现象。当液体内部局部静压强下降至某一临界值时,液体中的微小气核长大成为肉眼可见的空化泡。当空化泡迁移至高压区域时将发生溃灭,溃灭瞬间释放的巨大能量会对附近的固体壁面产生冲击作用,大量空化泡反复溃灭将导致固体壁面的破坏,即空蚀[1]。空蚀与液体介质的物理属性、系统运行参数等多种因素相关[2]。空蚀现象在以液体为工作介质的水力机械中最为常见,严重的空蚀会影响水力机械的运行效率和运行可靠性[3]。迄今为止,国内外已经在液体介质[4]、诱发空蚀的方法[5]、空蚀的评价方法[6-7]等方面开展对空蚀的研究。然而,空化的产生环境复杂且工程材料种类众多,仅从液体介质对空蚀的影响来看,很多已获得的研究结论仅对个例成立,很难得到普及,目前对于空蚀现象的理解并不充分。
已有研究证明腐蚀与空蚀之间存在着复杂的协同作用[8]。从机理层面,文献[5]分析了WC10Co-4Cr涂层在3.5% NaCl(质量分数)溶液中的空蚀行为,发现该涂层的抗空蚀能力取决于非晶相和WC晶粒。当NaCl质量分数降低至0.35%时,氧气泡能显著提高Ti在0.35% NaCl溶液中的抗空蚀能力[9]。在0.3%,3.0%和6.0% NaHCO3(质量分数)溶液中进行的铜合金空蚀对比实验表明,NaHCO3质量分数越高,空蚀程度越严重[10]。由此可见,腐蚀液与试样成分之间可能会发生化学反应,形成反应产物;反应产物与基体材料对空化作用的响应不同,加大了腐蚀与空蚀联合作用的研究难度。
不锈钢在流体机械和流体工程中被广泛应用,很多不锈钢制成的过流部件通常都运行于腐蚀-空蚀交替或并存的环境中[11-12]。在工作过程中,有些过流部件还面临着液体介质的更换问题。不锈钢对晶间腐蚀及应力腐蚀比较敏感,在Cl-环境中,不锈钢部件的缺陷处极易发生钝化膜破坏和由于局部酸化形成的点蚀,从而导致设备因穿孔而失效[13]。对304不锈钢进行的超声空蚀实验表明,其具有较强抗空蚀能力的原因之一在于奥氏体相对空蚀裂纹的发展有抑制作用[14]。目前,对于304不锈钢这一过流部件常见材料的腐蚀与空蚀联合作用机理尚未明确,且对于已经腐蚀表面的空蚀行为鲜见报道。
为探究304不锈钢在腐蚀与空蚀联合作用条件下的行为与机理,本文作者利用符合ASTM G32标准的超声空蚀实验台[15],借助较高浓度的NaCl溶液,对304不锈钢试样进行先腐蚀再空蚀的实验研究,考虑靶距和空蚀时间对空蚀结果的影响,并与未经腐蚀的304不锈钢试样进行相同实验条件下的空蚀结果对比,从质量损失、表面显微组织、形貌、粗糙度、显微硬度和残余应力等角度系统地分析304不锈钢腐蚀后的空蚀特征,为该材料抗空蚀性能的研究和工程应用提供支撑。
1 实验
1.1 实验材料与过程
将304不锈钢棒材加工制备成直径×长度为10 mm×8 mm的圆柱体试样,其化学成分如表1所示。将试样依次经400~2 000号砂纸打磨后抛光处理,然后在6% NaCl(质量分数)溶液中浸泡72 h。将浸泡后的试样经超声清洗后吹干,用精度为0.1 mg的Sartorius BSA124S分析天平多次称量试样的质量,取均值,随后对试样分别进行不同超声空蚀时间和靶距的2组实验,每组实验中采用5个试样进行平行实验。其中,第一组超声空蚀实验中,靶距为0.5 mm,超声时间分别设为15,30,60,120,240和360 min;第二组实验中,超声空蚀时间为180 min,靶距分别为0.2,0.4,0.6,0.8和1.0 mm。空蚀实验后,再次对试样进行多次称量取平均值,而后进行表征分析。
表1 304不锈钢的主要化学成分(质量分数)
Table 1 Main chemical compositions of 304 stainless steel %

1.2 实验装置
实验中采用的符合ASTM G32标准的超声空蚀实验装置,如图1所示。该装置的功率为500 W,超声频率为(27.4±0.3) kHz,超声变幅杆的振幅为(50±2.5) μm,工具头下端面直径为(15.9±0.05) mm,其浸入液面的深度为12.0 mm,试样上表面与工具头下端面间的间距(靶距)可以通过坐标机构进行调节。本实验采用的液体介质为蒸馏水,实验过程中,通过对冷却回路中循环水流量的控制将蒸馏水的温度保持在(25±0.5) °C。
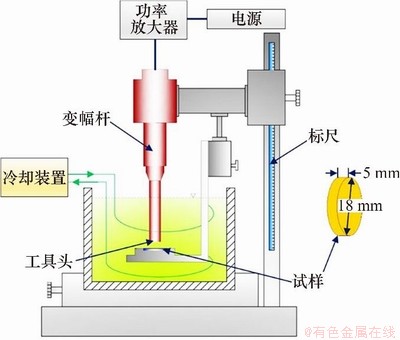
图1 超声空蚀装置示意图
Fig. 1 Schematic diagram of ultrasonic cavitation erosion device
1.3 表面参数测量
利用JSM-7001F型扫描电镜(SEM)观察空蚀后的试样表面形貌;通过X-350A型激光共聚焦显微镜观察试样表面三维形貌,并通过处理三维形貌数据计算试样的表面粗糙度;使用FM-ARS900全自动显微硬度计测量试样截面上的硬度分布,确定硬化层的深度;采用X射线应力测定仪测量试样表面的残余应力。
2 结果与讨论
2.1 空蚀时间的影响
2.1.1 空蚀累积质量损失与累积质量损失率
在试样表面附近,空化泡溃灭时产生的冲击波对试样表面造成持续的冲击载荷,致使试样表面出现材料剥落,引起试样质量损失。失重法是表征金属材料空蚀程度的常用方法[6]。试样的累积质量损失△m为[16]
(1)
式中:m0和m分别为试样空蚀前后的质量。
试样质量损失变化的速率为累积质量损失率ER:
(2)
式中:t为空蚀时间。
当靶距s为0.5 mm时,经腐蚀后空蚀的304不锈钢试样的累积质量损失和累积质量损失率随空蚀时间的变化如图2所示。从图2可以看出,随着空蚀时间的延长,
呈总体上升趋势。当空蚀时间为360 min时,试样的累积质量损失约2.1 mg。根据ER曲线,一般可以把试样的空蚀过程分为孕育、加速、稳定和衰减4个阶段[17]。从图2可见,对于腐蚀后再空蚀的试样,空蚀时间小于30 min时为空蚀孕育阶段,孕育期与材料的持久能力有关,该阶段空化泡破裂产生的冲击波的累积强度尚无法破坏材料表面的协调性,材料的损失并不明显,所以ER较小,且变化缓慢;当空蚀时间为30~120 min时,ER急剧增长,该时间段为空蚀的加速阶段;当空蚀时间为120~360 min时,ER平缓下降,空蚀的稳定期并不明显,主要呈现空蚀衰减阶段的特征。在空蚀后期,一方面,由于试样表面材料的不断剥落,超声振动头与产生的次表面距离增加,且材料剥落后形成的各向平面使得空泡溃灭对材料表面的应力集中分散,减轻了空泡溃灭对试样表面的影响,使得在质量损失不断增加的情况下ER缓慢减小;另一方面,由于空蚀时间较长,空泡的形成与扩散达到了动态平衡,蒸馏水能够在凹坑处稳定驻留,对空化泡溃灭的冲击形成缓冲作用,在一定程度上阻碍了空蚀的发展,这与文献[18-19]中对空蚀特性的研究结果一致。
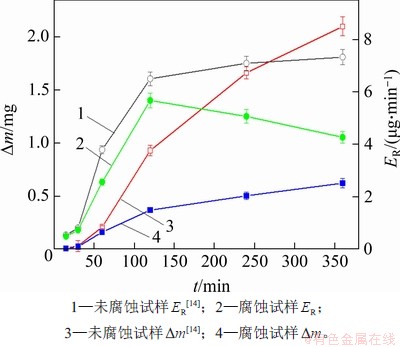
图2 累积质量损失和累积质量损失率随时间的变化(s=0.5 mm)
Fig. 2 Time-dependent cumulative mass loss and cumulative mass loss rate (s=0.5 mm)
文献[14]中获得的未经腐蚀的304不锈钢试样的超声空蚀结果见图2,该文献中所采用的实验装置和工况参数与本文的相同。通过对比可以看出,腐蚀后空蚀试样的累积质量损失明显小于未腐蚀试样的累积质量损失,且累积质量损失率也由于腐蚀作用而明显减小。结果表明,NaCl溶液的腐蚀作用使试样的抗空蚀能力增强。

图3 试样表面微观形貌随空蚀时间的变化(s=0.5 mm)
Fig. 3 Variation of surface morphology with cavitation erosion time (s=0.5 mm)
2.1.2 试样表面空蚀形貌
材料的微观组织变化是空蚀的另一个重要特征[20],空泡溃灭对材料表面的冲击决定了材料表面的破坏程度。采用SEM对空蚀后的304不锈钢试样表面进行微观观察,4个典型空蚀时刻的表面微观形貌如图3所示。空蚀前期,空泡溃灭反复作用于试样表面的时间短,试样表面协调性尚未被破坏,未出现明显的空蚀坑或裂纹,此时存在塑性变形,但并不明显,如图3(a)所示。当空蚀时间延长至120 min,试样表面的累积强度使晶粒发生不同程度的转动,晶界显现,试样表面凹凸不平严重;此外,在晶粒脊顶处和晶界处,材料表面因塑性变形速度和程度不一致,在局部凸起的应力集中部位产生了径向拉应力和颈缩,促进了表层的纵向开裂,产生的小规模破坏在空蚀后期成为疲劳损伤源,进一步加重材料的损伤与剥落,此时ER达到最大值(见图2)。当空蚀时间为240 min时,试样表面的晶界增多,组织结构被细化,晶界处的裂纹进一步扩展;同时,试样表面的裂纹明显增多。当空蚀时间延长至360 min时,材料的疲劳效应成为材料破坏的重要原因,此时,晶界处的滑移带变宽,滑移变形高度集中,在空泡溃灭的不断作用下,晶界处的应变积累到一定程度产生严重的应变,当金属塑性达到极限时,晶界处产生疲劳裂纹并在切应力的作用下迅速扩展汇聚,在此状态下,材料表面沿晶界发生了大规模的剥落。与文献[14]中未腐蚀而空蚀试样的表面形貌相比,图3中所示的空蚀发展相对滞后,空蚀由于腐蚀而得到抑制。这是由于腐蚀后试样表面形成的蚀坑在成为裂纹起源的同时,驻留住的稳定存在的蒸馏水具有“水垫”作用,对空泡溃灭产生的能量有缓冲作用。

图4 不同空蚀时间试样表面的轮廓图(s=0.5 mm)
Fig. 4 Profiles at different cavitation erosion time (s=0.5 mm)
2.1.3 空蚀试样的三维表面轮廓
采用X-350A型激光共聚焦显微镜对空蚀后的试样表面进行二维和三维轮廓观察,基于表面轮廓数据获得的空蚀坑的数量和尺寸可以作为评价材料表面空蚀程度的定量依据[21]。选取空蚀过程中3个典型的空蚀时间的测量结果如图4所示。图中,x和y分别为采样区域的横坐标和纵坐标。从图4可知:当空蚀时间为120 min时,试样表面的高低不平程度较轻,此时空蚀已进入发展阶段。当空蚀时间为240 min时,试样表面的粗糙程度加重,空蚀坑的数量明显增加,与图3(c)所示结果一致。当空蚀时间为360 min时,试样表面的材料剥落进一步加重,空蚀坑的尺寸增加,通过图4(d)和4(f)中的明暗程度可以判断,此时材料表面局部变形加重,但整体剥蚀尺寸趋于一致,试样表面的高度差较空蚀时间为240 min时变化并不明显,如图4(c)和4(e)所示。虽然试样表面上的不同区域与超声工具头的距离不同,会造成空蚀程度分布不均匀,但随着靶距小的区域内材料的进一步剥落,空泡破裂产生的冲击波到达试样表面的差异将逐步减弱,试样表面上的高度差随着空蚀时间的延长而减小。
除试样表面的三维轮廓外,材料表面的粗糙程度可以采用更为宏观的方式予以表达。基于激光共聚焦显微镜得到的表面高度计算均方根表面粗糙度Sa,用以对采样区域的表面粗糙程度进行表征。Sa的定义为
(3)
式中:Z(x,y)为借助激光共聚焦显微镜获得的高度;A为采样区域的面积。
图5所示为Sa随空蚀时间的变化曲线。从图5可以看出,当空蚀时间小于60 min时,试样表面粗糙度缓慢上升;当空蚀时间从60 min增加到 120 min时,试样表面在疲劳损伤源的基础上持续剥落,表面粗糙度快速上升;而后表面粗糙度变化不明显,且有下降的趋势,一直保持至空蚀时间为360 min时达到平衡。在空蚀后期,达到一定空蚀程度后,尽管试样表面材料随着空蚀时间延长继续剥离,但受加工硬化和空泡流体力学行为的影响,材料的剥离量和速度逐步减小,材料表面粗糙度变化不大,接近平衡状态。

图5 试样表面粗糙度随空蚀时间的变化(s=0.5 mm)
Fig. 5 Variation of surface roughness with cavitation erosion time (s=0.5 mm)
2.2 靶距对空蚀的影响
为考查靶距对空蚀的影响,选择空蚀时间为180 min的稳定期进行空蚀实验,靶距s分别为0.2,0.4,0.6,0.8和1.0 mm,对空蚀后试样的表面形貌、表面粗糙度、硬度、残余应力等进行综合分析。
2.2.1 累积质量损失
图6所示为超声空蚀时间为180 min时,空蚀试样的累积质量损失随靶距的变化。从图6可以看出,空蚀后试样的累积质量损失与靶距之间并不存在单调关系。当靶距为0.4 mm时,试样的累积质量损失约为1.3 mg,为5种靶距工况下的最大值。随着靶距从0.4 mm逐步增加,△m逐渐减小,当靶距为1.0 mm时,△m最小,约为0.9 mg。由此可见,靶距为0.4 mm时空蚀最为严重,此时,空泡完成了生长过程,并且在试样表面发生溃灭。靶距过小时,空化泡还未完全长大,空化泡溃灭释放的能量有限。靶距过大时,相当一部分空化泡在未到达试样表面时已经溃灭,提早释放了所携带的能量,未对试样表面构成严重破坏。

图6 空蚀试样的累积质量损失随靶距的变化(t=180 min)
Fig. 6 Cumulative mass loss of cavitation erosion samples at different standoff distances (t=180 min)
2.2.2 试样表面形貌
图7所示为试样在不同靶距条件下空蚀180 min后的微观形貌。304不锈钢为面心立方结构,塑性变形主要以滑移和孪生为主,靶距为0.2 mm时,试样表面出现明显的塑性变形和晶界汇聚,但由于空化泡到达试样表面时未完全长大,在试样表面能量累积有限,此时表面上未被破坏的区域明显。当靶距增加至0.4 mm时,绝大部分空泡溃灭产生的能量作用在试样表面,试样表面的塑性变形严重,蚀坑的数量最多,在此靶距条件下,由于空泡溃灭的能量已不能由滑移来释放,空蚀坑周围出现了细微裂纹,其中一些裂纹的尺寸较大,空蚀区域的面积增加,空蚀坑的深度变大,这是由于裂纹沿着晶界和蚀坑扩展并连接导致的。当靶距增加至0.6 mm时,与0.4 mm时相比,因部分空泡在达到试样表面前就已经溃灭,试样表面的破坏明显减弱,但塑性变形明显。此时,在有限的空化泡溃灭能量的冲击下,试样表面的材料剥落,小尺寸空蚀坑数量较多,蚀坑边缘也存在褶皱和裂纹,但与靶距为0.4 mm时相比,空蚀坑数量较少,尺寸较小。这与图6中靶距为0.4 mm和0.6 mm时试样的质量损失较大的情况相一致。随着靶距的增大,空泡溃灭时的位置与试样表面间的距离增加,空蚀效果逐步减弱,试样的表面以塑性变形为主,蚀坑数量减少,未被空蚀的区域明显增加,如图7(d)和(e)所示。

图7 不同靶距条件下试样表面的微观形貌(t=180 min)
Fig. 7 Surface morphology of samples at different standoff distances (t=180 min)
2.2.3 试样表面粗糙度
材料表面粗糙度的变化与空蚀损伤程度有关,图8所示为空蚀时间为180 min时,空蚀试样的表面粗糙度随靶距的变化情况。从图8可以看出,当靶距为0.4 mm时,试样的表面粗糙度最大,为4.03 μm。当靶距逐渐增加到1.0 mm时,试样表面粗糙度呈现阶梯式下降趋势。在整个变化过程中,当靶距为0.2 mm时,表面粗糙度最小。图8中的表面粗糙度变化情况与图7的结果相一致。可见,靶距对304不锈钢试样的表面粗糙度有显著的影响。

图8 不同靶距条件下的试样表面粗糙度(t=180 min)
Fig. 8 Surface roughness of samples at different standoff distances (t=180 min)
2.2.4 截面硬度分析
材料表面形貌的变化会引起表层显微硬度的改变。空化泡的溃灭在试样表面首先诱发塑性变形,塑性变形在空化过程中吸收空化产生的冲击载荷,在塑性变形的后期,试样表面被硬化,且硬化层存在于空蚀表面附近一定深度范围内。选取靶距为0.4 mm时的试样,采用全自动维氏显微硬度计,在试验载荷为3 N下保持15 s,测得的截面显微硬度的变化曲线如图9所示。从图9可知,距离空蚀表面50 μm处出现最大硬度,为317.69(HV)。随着取样深度的增加,显微硬度明显下降。在距空蚀表面250~350 μm时,硬度变化幅度较小,受到空化泡溃灭冲击的影响较弱。可以认为空泡破裂使得试样表层显微硬度大幅提升,且深度小于250 μm的材料层为硬化层,与传统的喷丸处理试样相比,硬化层深度略有提高[22]。随着空蚀的加剧,试样表面的材料不断剥落,即硬度大的材料层逐渐被去除,同时由于材料剥落导致的靶距增大,使得空化泡溃灭对新材料层的冲击减弱,截面显微硬度随着空蚀时间的延长而下降,最终达到基本稳定的状态。

图9 纵截面的显微硬度变化曲线(s=0.4 mm, t=180 min)
Fig. 9 Distribution of microhardness in cross section of the specimen (s=0.4 mm, t=180 min)
2.2.5 表面残余应力分析
空化泡溃灭对试样表面造成冲击,材料内部晶粒间相互挤压,位错逐渐堆积从而产生不均匀的塑性变形。当空化作用结束后,自试样表面一定深度内产生的自相平衡的内应力发生变化,即残余内应力。残余应力表征材料塑性变形程度,对裂纹扩展的影响很大,与试样表层的空蚀破坏程度有关,受空蚀工况参数影响,在外部应力作用下,残余应力的分布发生明显变化。不同靶距条件下的试样表面残余应力如图10所示。当表层材料体积膨胀时,由于受到基体的限制,会产生残余压应力,有利于材料硬度和疲劳性能的提高。当靶距增加时,试样表面的残余应力先迅速增加,而后减小。当靶距增加至0.6 mm时,残余应力增至最值,此时,试样表面的质量损失和最大粗糙度并非最大(如图6和图8所示),但试样内部应力比较集中,存在明显的加工硬化现象。虽然此时局部表面已经受到破坏,残余应力逐渐被释放,但空泡冲击造成的晶粒挤压和内部位错堆积在新的表面产生新的硬化层,残余应力达到最大值-465 MPa。此后,随着靶距的增加,空泡在达到试样表面前破裂,对试样表面的冲击减弱,虽然此时残余应力仍表现为压应力,但数值明显减小。
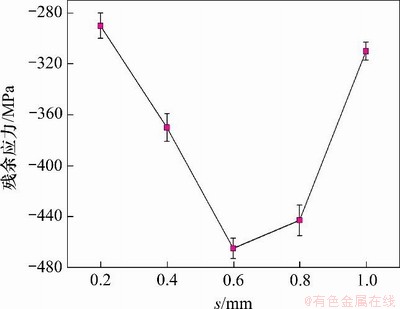
图10 残余应力随靶距的变化(t=180 min)
Fig. 10 Variation of residual stress with standoff distance (t=180 min)
3 结论
1) 与未被腐蚀的304不锈钢相比,先经NaCl溶液腐蚀再进行空蚀的304不锈钢的质量损失减少且空蚀发展相对滞后,空蚀由于腐蚀而受到抑制,材料的抗空蚀能力增强。
2) 经NaCl溶液腐蚀后,在空蚀前期试样表面呈现裂纹增多、空蚀坑变深的特征;到空蚀后期,空蚀稳定与衰减阶段的区分并不明显,空蚀呈现衰减趋势。
3) 当空蚀时间为180 min、靶距为0.4 mm时,腐蚀试样的表面粗糙度和其累积质量损失同时达到最大值,但试样表面的残余应力与靶距之间不存在单调变化关系,其最大值对应的靶距为0.6 mm。
参考文献:
[1] FRANC J P, MICHEL J M. Fundamentals of cavitation[M]. Dordrecht: Kluwer Academic Publishers, 2004: 265-271.
[2] CHANG S C, WENG W H, CHEN H C, et al. The cavitation erosion of Fe-Mn-Al alloys[J]. Wear, 1995, 181/182/183: 511-515.
[3] LAGUNA-CAMACHO J R, LEWIS R, VITE-TORRES M, et al. A study of cavitation erosion on engineering materials[J]. Wear, 2013, 301(1/2): 467-476.
[4] HOU Guoliang, ZHAO Xiaoqin, ZHOU Huidi, et al. Cavitation erosion of several oxy-fuel sprayed coatings tested in deionized water and artificial seawater[J]. Wear, 2014, 311(1/2): 81-92.
[5] HONG Sheng, WU Yuping, ZHANG Jianfeng, et al. Ultrasonic cavitation erosion of high-velocity oxygen-fuel (HVOF) sprayed near-nanostructured WC-10Co-4Cr coating in NaCl solution[J]. Ultrasonics Sonochemistry, 2015, 26: 87-92.
[6] 柳伟, 郑玉贵, 姚治铭, 等. 金属材料的空蚀研究进展[J]. 中国腐蚀与防护学报, 2001, 21(4): 250-255.
LIU Wei, ZHENG Yugui, YAO Zhiming, et al. Research progress on cavitation erosion of metallic materials[J]. Journal of Chinese Society for Corrosion and Protection, 2001, 21(4): 250-255.
[7] WANG Yan, LIU Jiangwei, KANG Nan, et al. Cavitation erosion of plasma-sprayed CoMoCrSi coatings[J]. Tribology International, 2016, 102: 429-435.
[8] KWOK C T, MAN H C, CHENG F T. Cavitation erosion and damage mechanisms of alloys with duplex structures[J]. Materials Science and Engineering: A, 1998, 242(1/2): 108-120.
[9] LI D G, WANG J D, CHEN D R, et al. Ultrasonic cavitation erosion of Ti in 0.35% NaCl solution with bubbling oxygen and nitrogen[J]. Ultrasonics Sonochemistry, 2015, 26: 99-110.
[10] LIU Haixia, CHEN Jinhao, SUN Jie, et al. Influence of the concentration of NaHCO3 solution on cavitation erosion of copper alloy[J]. Results in Physics, 2019, 13: 102145.
[11] TURNBULL A, RYAN M, WILLETTS A, et al. Corrosion and electrochemical behaviour of 316L stainless steel in acetic acid solutions[J]. Corrosion Science, 2003, 45(5): 1051-1072.
[12] ADELI M, GOLOZAR M A, RAEISSI K. Pitting corrosion of SAF2205 duplex stainless steel in acetic acid containing bromide and chloride[J]. Chemical Engineering Communications, 2010, 197(11): 1404-1416.
[13] 郝震, 戴恒彪, 李广州, 等. 304不锈钢在氯化钠介质中点蚀缓蚀剂的研究[J]. 表面技术, 2015, 44(4): 123-126.
HAO Zhen, DAI Hengbiao, LI Guangzhou, et al. Study on inhibitors for the pitting corrosion of 304 stainless steel in sodium chloride medium[J]. Surface Technology, 2015, 44(4): 123-126.
[14] 庄栋栋, 陈文博, 欧阳亚东, 等. 低碳钢与304不锈钢的超声空蚀机理对比研究[J]. 表面技术, 2019, 48(1): 225-233.
ZHUANG Dongdong, CHEN Wenbo, OUYANG Yadong, et al. Comparative investigation of ultrasonic cavitation erosion mechanism for low-carbon and 304 stainless steels[J]. Surface Technology, 2019, 48(1): 225-233.
[15] ASTM G32-10, Test method for cavitation erosion using vibratory apparatus[S].
[16] 张桃, 刘海霞, 康灿, 等. 铅黄铜合金在不同液体介质中的超声空蚀行为及机理[J]. 表面技术, 2018, 47(1): 109-115.
ZHANG Tao, LIU Haixia, KANG Can, et al. Ultrasonic cavitation erosion behavior and mechanism of Pb-brass alloy in different liquids[J]. Surface Technology, 2018, 47(1): 109-115.
[17] LIU Haixia, KANG Can, SOYAMA H. Experimental study of the influence of test chamber dimensions on aggressive intensity of the cavitating jet[J]. Journal of Testing and Evaluation, 2020, 48(5): 3588-3601.
[18] 白立新, 许唯临, 张法星, 等. 超声场中硬壁凹坑空化空蚀特性研究[J]. 中国科学(E辑: 技术科学), 2009, 39(6): 1122-1128.
BAI Lixin, XU Weilin, ZHANG Faxing, et al. Study on cavitation erosion characteristics of hard-wall pits in ultrasonic field[J]. Science in China(Series E: Technological Sciences), 2009, 39(6): 1122-1128.
[19] BAI Lixin, XU Weilin, TIAN Zhong, et al. A high-speed photographic study of ultrasonic cavitation near rigid boundary[J]. Journal of Hydrodynamics, Ser B, 2008, 20(5): 637-644.
[20] VERMA S, DUBEY P, SELOKAR A W, et al. Cavitation erosion behavior of nitrogen ion implanted 13Cr4Ni steel[J]. Transactions of the Indian Institute of Metals, 2017, 70(4): 957-965.
[21] TZANAKIS I, ESKIN D G, GEORGOULAS A, et al. Incubation pit analysis and calculation of the hydrodynamic impact pressure from the implosion of an acoustic cavitation bubble[J]. Ultrasonics Sonochemistry, 2014, 21(2): 866-878.
[22] 方博武. 受控喷丸与残余应力理论[M]. 济南: 山东科学技术出版社, 1991: 53-57.
FANG bowu. Controlled Shot Peening and Residual Stress Theory[M]. Jinan: Shandong Science & Technology Press, 1991: 53-57.
(编辑 赵俊)
收稿日期: 2020 -07 -13; 修回日期: 2020 -09 -24
基金项目(Foundation item):国家自然科学基金资助项目(51775251) (Project(51775251) supported by the National Natural Science Foundation of China)
通信作者:刘海霞,博士,教授,从事金属材料的空蚀机理研究;E-mail:liuhx@mail.ujs.edu.cn
DOI: 10.11817/j.issn.1672-7207.2021.05.005
引用格式: 陈杰, 刘海霞, 刘光磊, 等. NaCl溶液腐蚀后304不锈钢的超声空蚀特征[J]. 中南大学学报(自然科学版), 2021, 52(5): 1436-1445.
Citation: CHEN Jie, LIU Haixia, LIU Guanglei, et al. Ultrasonic cavitation erosion behavior of 304 stainless steel after corrosion in NaCl solution[J]. Journal of Central South University(Science and Technology), 2021, 52(5): 1436-1445.