DOI: 10.11817/j.ysxb.1004.0609.2020-36358
铸造碳化钨颗粒增强PDC钻头胎体的三体磨损行为
胡 可1, 2,谢焕文1, 2,刘 辛1, 2,蔡一湘1, 2
(1. 广东省科学院 广东省材料与加工研究所,广州 510650;
2. 国家钛及稀有金属粉末冶金工程技术研究中心,广州 510650)
摘 要:采用无压浸渗工艺制备了铸造碳化钨颗粒增强PDC钻头胎体材料,胎体材料组织均匀,胎体中碳化钨颗粒完整,碳化钨颗粒与铜合金基体形成均匀扩散层。重点研究了PDC钻头胎体的三体磨料磨损行为和磨损机理。结果表明:铸造碳化钨颗粒形貌是影响PDC钻头胎体三体磨料磨损行为的主要因素。相对于破碎铸造碳化钨,球形碳化钨内部微裂纹少且无应力集中,具有耐磨增效作用,可显著提高PDC钻头胎体材料的三体磨损性能。球形碳化钨颗粒增强PDC钻头胎体的相对耐磨性是破碎碳化钨颗粒增强PDC钻头胎体的10倍。破碎碳化钨颗粒增强PDC钻头胎体的磨损表面呈现大量铜合金基体犁沟,多角状碳化钨颗粒被磨损变圆滑;而球形碳化钨颗粒增强PDC钻头胎体的磨损表面碳化钨颗粒突出林立,少量碳化钨颗粒被折断或发生破裂。
关键词:PDC钻头;铸造碳化钨;无压浸渗;三体磨料磨损
文章编号:1004-0609(2020)-02-0364-08 中图分类号:TD421.2 文献标志码:A
PDC(Polycrystalline diamond compact,聚晶金刚石复合片)钻头具有更高的安全性,可极大地提高钻井工作效率,降低钻井成本,已逐步取代牙轮钻头成为破岩主力,在油气勘探领域发挥着重要作用[1-2]。PDC钻头胎体的作用是包镶金刚石复合片并与钻头钢体牢固连接。胎体的硬度和耐磨性对金刚石钻头的性能至关重要,直接影响胎体对金刚石的包镶牢固程度以及金刚石能否及时出刃[3]。铸造碳化钨是WC和W2C两相的共晶产物,具有高硬度(高达2500~3100 HV)、高热稳定性、高耐磨性以及与金属润湿性良好等优点,被广泛添加至金属材料中以提高抗磨损性能[4-5]。PDC钻头胎体中通常添加有30%以上(质量分数)的铸造碳化钨做为增强相[6-7]。无压浸渗是PDC钻头胎体的常用制备技术。2003年以来,国外Hughes Christensen、Smith等钻头制造商推出的新型钻井PDC钻头多数是以铸造碳化钨颗粒与镍粉为骨架粉末,通过无压浸渗低熔点的铜合金而制成的[8]。采用铜合金做粘结金属可避免金刚石高温石墨化,同时与骨架材料和钢基体具有良好的润湿性和结合强度。胎体所用铸造碳化钨主要有不规则状的破碎铸造碳化钨和球形铸造碳化钨两种。目前钻头胎体的成分配方已臻成熟,应用多采用形状不规则的破碎铸造碳化钨颗粒做为PDC钻头胎体的主要骨架。然而,与破碎碳化钨相比,球形碳化钨具有碳含量波动小、共晶组织率高、共晶尺寸小、孔隙率低、硬度高以及耐磨性好等优点[4]。因此,近年已有相关研究和专利通过添加球形铸造碳化钨颗粒来改善胎体材料的性能[9-10]。李淑涛等[11]和邹黎明等[5]采用球形碳化钨粉末制备超硬耐磨耐蚀涂层,结果表明球形碳化钨的加入能有效提高机械零件的耐磨和耐蚀性能,延长使用寿命。谢焕文等[10]通过对比研究球形碳化钨与破碎碳化钨的粒度和含量对胎体组织与性能的影响发现球形碳化钨颗粒增强PDC钻头胎体材料的性能有显著提高,在石油钻采、海洋装备、地质矿山、工程机械等领域具有广阔的应用前景。
在油气勘探过程中,PDC 钻头在井底的工作条件恶劣,既承受各种复杂的交变载荷(如扭转振动、涡动以及各种耦合作用等),又受到岩石颗粒碎屑的冲刷磨损(海洋石油钻井时,更是受到液固两相流的冲刷和腐蚀)[12]。岩石颗粒、磨屑等覆盖在相互对磨的材料之间,形成摩擦第三体。因此,PDC钻头钻进过程中的磨损行为可看做是三体磨粒磨损(海洋钻井过程中,液相的冲刷和腐蚀导致钻头的磨损行为更为复杂,本文暂不考虑)。迄今,PDC钻头的磨损行为研究主要集中在PDC切削齿[13-14],而钻头胎体的磨损行为尤其是实际工况下的三体磨损行为却鲜有报道。为此,本文以铸造碳化钨颗粒混合镍粉作为骨架粉末,采用无压浸渗工艺制备PDC钻头胎体材料,在前期研究基础上重点研究PDC钻头胎体的三体磨损行为,探讨铸造碳化钨颗粒形貌及含量对钻头胎体材料的三体磨料磨损行为的影响,并揭示其磨损机理。
1 实验
1.1 PDC钻头胎体材料的制备
采用V型混料机将铸造碳化钨粉末和镍粉混合均匀制成骨架粉末,转速为40 r/min,混料时间为4 h。铸造碳化钨粉末由自贡长城硬面材料有限公司提供,分为不规则状的破碎铸造碳化钨与球形铸造碳化钨两种。镍粉采用高压水雾化法制备,呈近球形,其粒度小于38 μm。铸造碳化钨粉末的成分与性能如表1所示。原料粉末的微观形貌详见前期工作[10]。
采用无压浸渗工艺制备PDC钻头胎体材料。将骨架粉末装入石墨模具中,振实,并上置一定量的CuNi基合金粒作为粘结金属。将装好的石墨模具放入真空热处理炉中对试样进行浸渗处理,保温温度为1150 ℃,保温时间为1 h。整个升温、保温及冷却过程始终保持真空度低于20 Pa。保温结束后炉冷至室温后取出,并采用线切割制备相关样品以备组织分析和三体磨损性能测试。表2所示为PDC钻头胎体材料的编号、成分配方及密度。
采用阿基米德排水法测量各配方胎体材料的密度。采用JEOLJXA-8100型电子探针观察胎体材料的微观组织。采用HR-150A型洛氏硬度计测量胎体材料的洛氏硬度,金刚石洛氏压头型号为HRC-3,圆锥角
为120°,载荷为1.47 kN,顶端球面半径R为0.2 mm。硬度测试前试样测试面采用300#~2000#的SiC砂纸上进行研磨抛光处理,每个试样取6个点进行洛氏硬度测量,结果取其平均值。
1.2 三体磨损试验
采用MMH-5环块三体磨损试验机对胎体材料进行磨损试验,转速为30 r/min,试验载荷为6 kg。磨料为石英砂(主要成分SiO2),粒度为120~250 μm。每个试样预磨时间为120 min,预磨后每磨损30 min为一个阶段进行清洗称量。利用AL204型电子天平(精度0.01 mg)称量计算试样磨损前后的质量损失。由于各胎体材料所用原料及比例有所差异,造成各试样密度不相同,采用质量损失量不能科学地评价其耐磨性,故本文采用体积损失评价胎体材料的耐磨性能。体积损失量V=m/ρ,m为试样的质量损失量,ρ为试样密度。采用JEOLJXA-8100型电子探针观察胎体材料的磨损表面形貌。采用INCAPentaFET-x3能谱仪对磨损表面进行局部元素分析。采用Bruker DEKTAK XT探针式表面轮廓仪测量胎体材料的磨损表面3D轮廓和磨损面的表面粗糙度Ra。
表1 铸造碳化钨粉末的成分与性能
Table 1 Compositions and properties of cast tungsten carbide powders used in this study

表2 PDC钻头胎体材料的编号和成分配方及密度
Table 2 Specimen number, composition and density of prepared PDC drill bit matrix material

2 结果与讨论
2.1 胎体材料的微观组织
图1所示为胎体材料的微观组织。胎体材料中的铸造碳化钨颗粒基本都保持完整并均匀分布在铜基粘结相中。在相同的实验条件下,破碎铸造碳化钨颗粒增强胎体材料的碳化钨颗粒尖角处可见孔隙,如图1(a)和(b)所示。这主要是破碎碳化钨颗粒形状不规则,其作为骨架在浸渗前的孔隙不均匀、部分通道被阻断所致。此外,前期的能谱线扫描和XRD结果[10]显示:1) 镍与浸渍铜合金充分熔合并均匀分布在铜合金基体中;2) 铸造碳化钨颗粒在铜合金基体中发生局部溶解并形成均匀扩散层,但在碳化钨与铜合金基体的界面上未生成金属间化合物。碳化钨颗粒表面形成的扩散层有利于胎体中的铸造碳化钨与浸渍合金形成良好的结合,提高碳化钨与基体间的结合力和其对基体的强化作用,有利于胎体材料性能的提高。
2.2 胎体材料的硬度
胎体硬度可以作为衡量胎体耐磨性的一个比较直观的参考指标。一般来说,硬度越高,材料的耐磨性能越好[15]。但耐磨性受诸多因素的影响。图2所示为各配方胎体材料的洛氏硬度。随着碳化钨含量的增加,硬度计压头接触到碳化钨硬质点的几率增大,故铸造碳化钨含量为94%的胎体材料1#和3#的硬度高于碳化钨含量为87%的胎体材料2#和4#的硬度。此外,当铸造碳化钨含量相同时,碳化钨的颗粒形貌对胎体材料的影响很小,也即球形碳化钨颗粒增强胎体材料3#和4#的硬度分别与破碎碳化钨颗粒增强胎体材料1#和2#的相当。
2.3 胎体材料的三体磨损行为与磨损机理
胎体的耐磨性能是PDC钻头的重要性能指标之一,直接影响钻头的选择、钻进规程参数的确定、所用的操作技术以及所产生的经济指标[13]。图3所示为各配方胎体材料三体磨损2 h后的宏观形貌。破碎碳化钨颗粒增强胎体材料1#和2#的摩损面可见较深的犁沟,而球形碳化钨颗粒增强胎体3#和4#的磨损面则较为平整,在未受力的试样边缘处仍可见磨损实验前的抛光镜面光泽。
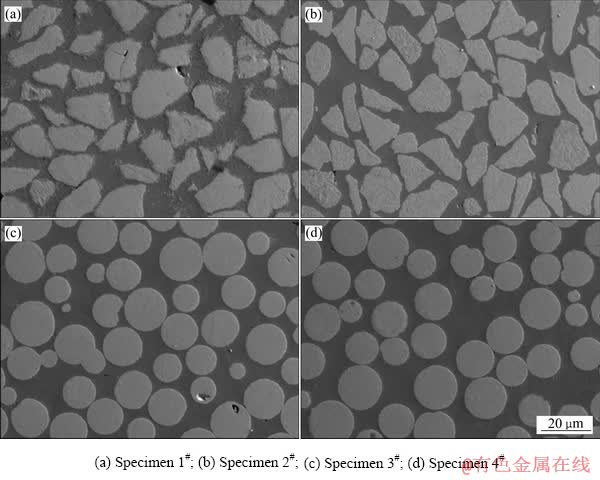
图1 铸造碳化钨颗粒增强PDC钻头胎体材料的微观组织
Fig. 1 Microstructures of cast tungsten carbide particles reinforced PDC drill bit matrix materials
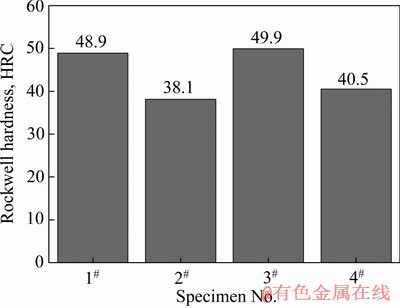
图2 胎体材料的洛氏硬度
Fig. 2 Rockwell hardness of PDC drill bit matrix materials
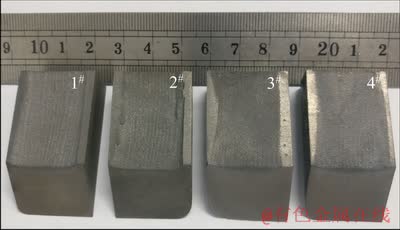
图3 胎体材料三体磨损后的宏观形貌
Fig. 3 Macro profiles of PDC drill bit matrix materials after three-body wear tests
图4(a)所示为胎体材料三体磨损过程中的体积磨损速率随时间的变化曲线。由图4(a)可知,30 min后,四种胎体材料的磨损速率基本维持稳定。但是,当铸造碳化钨的颗粒形貌相同时,增加铸造碳化钨颗粒的含量,高硬度的碳化钨颗粒增强了胎体的耐磨性能,因此胎体材料的磨损速率相应降低。同时可以看出,相对于破碎铸造碳化钨颗粒增强胎体材料1#和2#,球形铸造碳化钨颗粒增强胎体材料3#和4#的磨损速率显著降低。图4(b)所示为胎体材料三体磨损2 h后的总体积磨损量。胎体材料1#和2#(含破碎铸造碳化钨)与胎体材料3#和4#(含球形铸造碳化钨)的体积损失量相差10余倍,也即球形铸造碳化钨颗粒增强胎体材料3#和4#的耐磨性能远高于破碎铸造碳化钨颗粒增强胎体材料1#和2#的耐磨性。结合图2中胎体材料的硬度可知,当铸造碳化钨含量相同时胎体的硬度相当,但胎体的耐磨性能却相差甚远。因此,铸造碳化钨的颗粒形貌是影响胎体材料三体磨损性能的主要因素。此外,虽然球形铸造碳化钨与破碎铸造碳化钨的硬度相当(见表1),但球形碳化钨内部微裂纹少,且无应力集中,对提高胎体材料的耐磨性能同样具有促进作用。
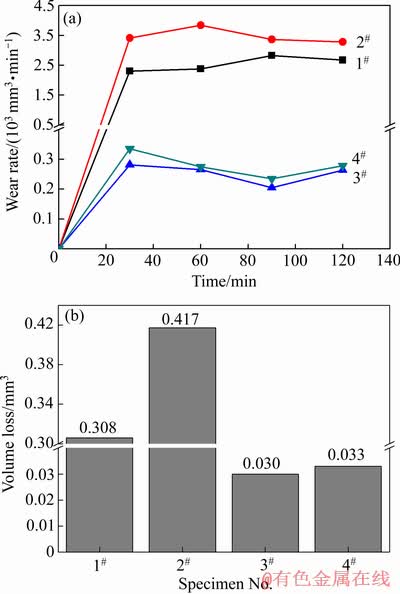
图4 胎体材料的三体磨损速率和磨损后的总体积磨损量
Fig. 4 Wear rate of PDC bit matrix materials vs wear time(a) and total wear volume of PDC bit matrix materials(b)
图5和6所示分别为胎体材料三体磨损后的表面磨损形貌和磨损表面局部区域EDS图谱(磨损时间为2 h)。图7所示为胎体材料磨损表面的3D轮廓图。由图7可知,经过2 h的三体磨料磨损后,铸造碳化钨颗粒表面均变得圆滑(见图5),磨损表面上碳化钨的位置均高于铜合金基体平面(见图5和7)。这说明铜合金基体最先被磨粒磨损,磨损到一定程度后凸起的碳化钨颗粒保护基体进一步被磨损,此时碳化钨颗粒承受磨粒磨损。更为重要的是,对比胎体材料1#和2#与3#和4#的微观磨损形貌发现,胎体材料1#和2#磨损表面相对平整且呈现大量的铜合金基体犁沟,部分铜合金更是“覆盖”在碳化钨颗粒表面;而胎体材料3#和4#的磨损表面则呈现碳化钨颗粒“峰峦林立”,少量碳化钨颗粒被折断或破裂。图8所示为胎体材料三体磨料磨损后磨损面的表面粗糙度。
当铸造碳化钨含量相同时(胎体材料1#和3#),不规则多角状碳化钨颗粒易破碎或剥离基体(见图5(a)和图7(a)),而“裸露”的球状碳化钨颗粒均匀分布在磨损表面,导致胎体材料1# 磨损后的表面粗糙度高于胎体材料3#的;而当碳化钨颗粒呈球状时,降低碳化钨含量,胎体中的铜合金基体含量增加,基体承受更多的磨损(见图5(d)和7(d)),从而导致胎体材料4#磨损后的表面粗糙度高于胎体材料3#的。胎体材料2#磨损后的表面粗糙度最低,其可能是破碎或剥离的碳化钨颗粒被“柔软”的铜合金基体覆盖或填充导致磨损相对平整所致(见图5(b)和7(b))。上述结果说明破碎碳化钨颗粒呈多角状,磨损过程中易破裂或从基体中剥落,对基体的支撑作用较差;而球形碳化钨颗粒硬度高、无尖角,在三体磨粒磨损过程中球体表面滑动摩擦因数小,与磨料的摩擦作用降低,因而不易破碎或从基体剥落,故球形碳化钨颗粒具有耐磨增效作用,进而显著提高PDC钻头胎体材料(3#和4#)的三体磨损性能。
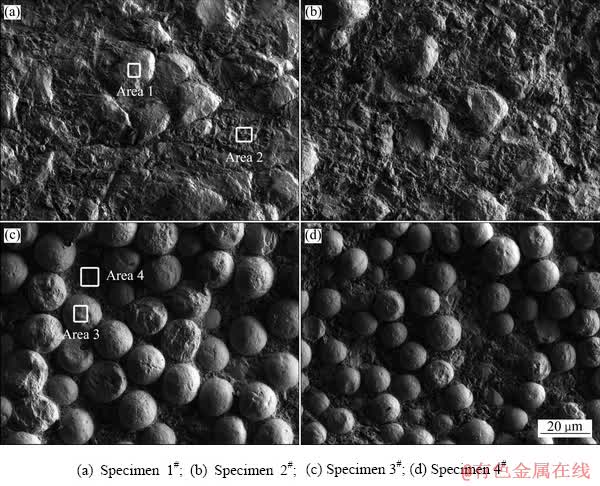
图5 胎体材料三体磨损后的表面磨损形貌
Fig. 5 Surface morphologies of PDC bit matrix materials worn by SiO2 slurries for 2 h
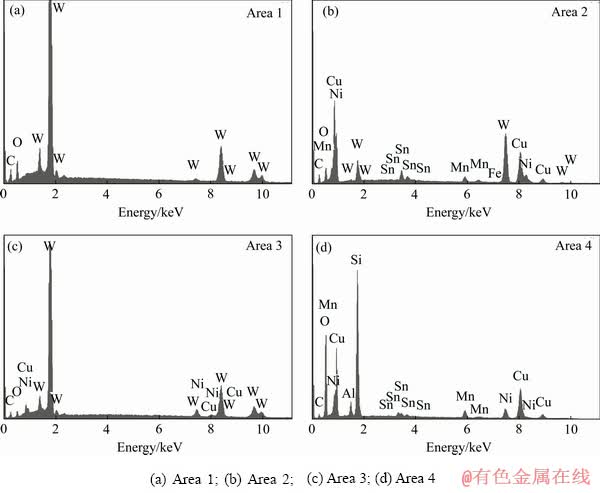
图6 胎体材料三体磨损后磨损表面局部区域的能谱图
Fig. 6 EDS patterns of local area (pointed out in Fig. 5) on worn surface of PDC bit matrix materials
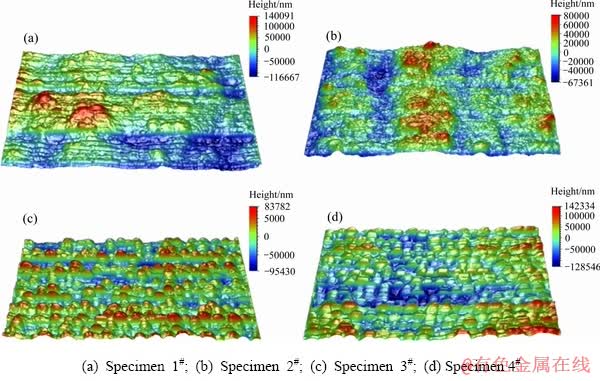
图7 胎体材料的磨损表面3D轮廓
Fig. 7 3D profiles of wear surfaces of PDC drill bit matrix materials

图8 胎体材料三体磨损后磨损面的表面粗糙度
Fig. 8 Roughness Ra of worn surfaces of PDC drill bit matrix materials after three-body wear tests
综上所述,球形铸造碳化钨颗粒增强PDC钻头胎体材料的三体磨料磨损过程及磨损机理可推测如下:
1)磨损初期,胎体材料中碳化钨颗粒与铜合金基体同时受到磨料的切削和磨损,因铜合金基体硬度低,最先被磨料切削、犁沟。
2)随着磨损过程继续进行,球形碳化钨颗粒抵抗磨料的切削和磨损,颗粒体积磨损量小(球形铸造碳化钨的硬度(大于HV2500)远高于石英砂的硬度(约HV1600)[16]。当材料硬度与磨料硬度之比Hm/Ha≥0.8 时,材料的磨损率随材料硬度的提高急剧下降[15]。铜合金基体大量磨损而下凹,碳化钨颗粒则突出于基体之上,突出“林立”的球形碳化钨颗粒可减少周围下凹的基体免受硬质磨料的进一步磨损,产生微观上的“阴影效应”(即磨损增效作用),而下凹的基体则反过来给予碳化钨颗粒良好的“支撑作用”,避免碳化钨颗粒的折断和剥落。
3)磨损后期,随着碳化钨颗粒周围铜合金基体的持续下凹,基体对碳化钨颗粒的支撑作用明显下降,而部分碳化钨颗粒则在磨料持续切削和疲劳磨损作用下发生折断或破碎;继续磨损,折断或破碎的碳化钨颗粒与铜合金基体“恢复”到同一水平状态,上述磨损过程重复直至碳化钨颗粒再折断或破碎。
3 结论
1) 铸造碳化钨颗粒增强PDC钻头胎体材料组织均匀,胎体中碳化钨颗粒完整,碳化钨颗粒与铜合金基体形成均匀扩散层。胎体材料的硬度几乎不受碳化钨颗粒形貌的影响。
2) 铸造碳化钨颗粒形貌是影响PDC钻头胎体三体磨料磨损行为的关键因素。相对于破碎铸造碳化钨,球形碳化钨内部微裂纹少且无应力集中,具有耐磨增效作用,可显著提高PDC钻头胎体材料的三体磨损性能。球形碳化钨颗粒增强PDC钻头胎体的相对耐磨性远优于破碎碳化钨颗粒增强PDC钻头胎体,前者的耐磨性能是后者的10倍。
3) 破碎碳化钨颗粒增强PDC钻头胎体的磨损表面平整,呈现大量铜合金基体犁沟,多角状碳化钨颗粒被磨损变圆滑;而球形碳化钨颗粒增强PDC钻头胎体的磨损表面碳化钨颗粒突出林立,少量碳化钨颗粒被折断或发生破裂。
REFERENCES
[1] 左汝强. 国际油气井钻头进展概述(三)— PDC钻头发展进程及当今态势[J]. 探矿工程(岩土钻掘工程), 2016, 43(3): 1-8.
ZUO Ru-qiang. International advancement of drilling bits for oil and gas well(3)—PDC bits progress and present trend (Ⅰ)[J]. Exploration Engineering (Rock & Soil Drilling and Tunneling), 2016, 43(3): 1-8.
[2] 赵永明, 谢德龙, 禹德洲, 方啸虎. 油气井金刚石钻头的现状及发展趋势[J].超硬材料工程, 2012, 24(5): 35-38.
ZHAO Yong-ming, XIE De-long, YU De-zhou, FANG Xiao-hu. Current situation and development trend of the diamond bits for oil and gas well[J]. Superhard Material Engineering, 2012, 24(5): 35-38.
[3] 张晓亮. 基于PRO/E软件的典型地质PDC钻头的应力分析[D]. 西安: 西安科技大学, 2009: 5-9.
ZHANG Xiao-liang. Analysis on the typical geological PDC bits’ stress based on PRO/E software[D]. Xi’an: Xi’an University of Science and Technology, 2009: 5-9.
[4] 佘建芳. 球形铸造碳化钨硬面材料生产新方法[J]. 硬质合金, 1998, 15(4): 241-245.
SHE Jian-fang. A new method for producing hard-facing material of spherical cast tungstencarbide[J]. Cemented Carbide, 1998, 15(4): 241-245.
[5] 邹黎明, 刘 辛, 王蕾, 谢焕文, 蔡一湘. 铸造碳化钨粉末物性对激光熔覆陶瓷颗粒增强Fe基复合材料耐磨性能的影响[J]. 稀有金属材料与工程, 2017, 46(4): 1126-1131.
ZOU Li-ming, LIU Xin, WANG Lei, XIE Huan-wen, CAI Yi-xiang. Effects of cast tungsten carbide powder on wear resistance of laser cladding ceramic particle reinforced iron matrix composite[J]. Rare Metal Materials and Engineering, 2017, 46(4): 1126-1131.
[6] 赵永明, 李 亮. 高强度低成本石油钻头胎体配方的研究[J]. 超硬材料工程, 2016, 28(3): 1-6.
ZHAO Yong-ming, LI Liang. Research of high-strength and low-cost formula of oil drill bit matrix[J]. Superhard Material Engineering, 2016, 28(3): 1-6.
[7] 丁华东, 浩宏奇, 金志浩. 金刚石钻头胎体材料设计新思路[J]. 西安交通大学学报, 1997, 31(4): 124-126.
DING Hua-dong, HAO Hong-qi, JIN Zhi-hao. A new material design method of diamond bit matrix[J]. Journal of Xi’an Jiaotong University, 1997, 31(4): 124-126.
[8] OHNO T, KARASAWA H, KOBAYASHI H. Cost reduction of polycrystalline diamond compact bits through improved durability[J]. Geothermics, 2002, 31(2): 245-262.
[9] 陈俊勇, 杨英祥, 赖建新, 温贵凡, 张力轩, 庞正光. 一种聚晶金刚石复合片钻头胎体粉及用其制造胎体的工艺: 中国, 201110433249.8[P]. 2012-06-13.
CHEN Jun-yong, YANG Ying-xiang, LAI Jian-xin, WEN Gui-fan, ZHANG Li-xuan, PAN Zheng-guang. Polycrystalline diamond compact (PDC) drillbit matrix powder and process for manufacturing matrix by using same: China, 201110433249.8[P]. 2012-06-13.
[10] 谢焕文, 刘 辛, 胡 可, 蔡一湘. 碳化钨粉末对PDC钻头胎体的组织与力学性能影响[J]. 复合材料学报, 2019, 36(5): 1235-1243.
XIE Huan-wen, LIU Xin, HU Ke, CAI Yi-xiang. Effect of cast tungsten carbide powders on microstructure and mechanical properties of the PDC bit matrix[J]. Acta Materiae Compositae Sinica, 2019, 36(5): 1235-1243.
[11] 李淑涛, 陈海䶮, 张根荣, 董丽华, 尹衍升. 深海石油钻采工具表面硬化材料研制[J]. 热喷涂技术, 2016, 8(2): 7-11, 59.
LI Shu-tao, CHEN Hai-yan, ZHANG Gen-rong, DONG Li-hua, YIN Yan-sheng. Hard facing materials of deep-sea oil drilling tools[J]. Thermal Spray Technology, 2016, 8(2): 7-11, 59.
[12] 王照智. 仿生耦合孕镶金刚石钻头耐磨增效机理研究[D]. 长春: 吉林大学, 2017: 111-129.
WANG Zhao-zhi. Study on the mechanism of wear resistance and efficiency increase of bionic coupling impregnated diamond bit[D]. Changchun: Jinlin University, 2017: 111-129.
[13] ERSOY A, WALLER M D. Wear characteristics of PDC pin and hybrid core bits in rock drilling[J]. Wear, 1995, 188(1/2): 150-165.
[14] 高明洋, 张 凯, 周 琴, 周辉峰, 刘宝林. 高温硬地层钻进中PDC钻头切削齿磨损研究[J]. 探矿工程(岩土钻掘工程), 2018, 45(10): 185-189.
GAO Ming-yang, ZHANG Kai, ZHOU Qin, ZHOU Hui-feng, LIU Bao-lin. Wear of PDC cutters in high temperature hard formation drilling[J]. Exploration Engineering (Rock & Soil Drilling and Tunneling), 2018, 45(10): 185-189.
[15] RICHARDSON R C D. The wear of metals by hard abrasives[J]. Wear, 1967, 10(4): 291-309.
[16] 郑开宏, 高义民, 陈 亮, 赵散梅, 李 林, 王 娟. 颗粒增强铁基复合材料的三体磨料磨损性能[J]. 摩擦学学报, 2012, 32(2): 176-182.
ZHENG Kai-hong, GAO Yi-min, CHEN Liang, ZHAO San-mei, LI Lin, WANG Juan. Three-body abrasive wear behavior of iron matrix composites reinforced with tungsten carbide particles[J]. Tribology, 2012, 32(2): 176-182.
Three-body abrasive wear behavior of PDC drill bit matrix reinforced by cast tungsten carbide particles
HU Ke1, 2, XIE Huan-wen1, 2, LIU Xin1, 2, CAI Yi-xiang1, 2
(1. Guangdong Institute of Materials and Processing, Guangdong Academy of Sciences, Guangzhou 510650, China;
2. National Engineering Research Center of Powder Metallurgy of Titanium&Rare Metals, Guangzhou 510650, China)
Abstract: Cast tungsten carbide particles reinforced PDC drill bit matrix was prepared by pressureless infiltration. The bit matrix showed a microstructure where the cast tungsten carbide particles were dispersed homogeneously in the Cu alloy. The tungsten carbide particles remained intact and formed a uniform diffusion layer with the Cu alloy matrix. The three-body abrasive wear behavior and wear mechanism of the PDC drill bit matrix were investigated. The results show that the morphology of cast tungsten carbide particles is the main factor affecting the three-body abrasive wear behavior of PDC drill bit matrix. Compared with the crushed cast tungsten carbide, fewer internal micro-cracks and no stress concentration are found in the spherical tungsten carbide, which has an increase effectiveness to resist wear and significantly improves the three-body wear performance of PDC drill bit matrix. The wear resistance of PDC drill bit matrix reinforced by spherical tungsten carbide particles is 10 times of that of PDC drill bit matrix reinforced by crushed tungsten carbide particles. The worn surface of the PDC drill bit matrix reinforced by crushed tungsten carbide particles shows furrowed Cu alloy with worn tungsten carbide particles. Whereas, on the worn surface of PDC drill bit matrix reinforced by spherical tungsten carbide particles, the tungsten carbide particles stand out and a small number of them are broken.
Key words: PDC drill bit; cast tungsten carbide; pressureless infiltration; three-body abrasive wear
Foundation item: Project(2011DFR50740) supported by the Special Program for International S&T Cooperation Projects of China; Project(2011A091102007) supported by the Special Program on Key Technology Research for Strategic Emerging Industries of Guangdong Province, China; Innovation Projects (2015B070701027, 2016B070701021) supported by the Program of Provincial Scientific Research Institutes in Guangdong Province, China; Projects(2018GDASCX-0963, 2018GDASCX-0117) supported by the GDAS’ Program of Science and Technology Development, China; Project(2017A070701029) supported by the Special Program for Collaborative Innovation and Facility Development of Guangdong Province, China; Major Project(201604046009) supported by the Program of Industry-University-Research Institute Collaboration of Guangzhou, China
Received date: 2019-02-22; Accepted date: 2019-07-26
Corresponding author: LIU Xin; Tel: +86-20-601086128; E-mail: shaneliu118@163.com
(编辑 何学锋)
基金项目:国家国际科技合作专项(2011DFR50740);广东省战略性新兴产业核心技术攻关专项(2011A091102007);广东省省属科研机构改革创新项目(2015B070701027,2016B070701021);广东省科学院实施创新驱动发展能力建设专项(2018GDASCX-0963,2018GDASCX-0117);广东省协同创新与平台环境建设专项(2017A070701029);广州市产学研协同创新重大专项(201604046009)
收稿日期:2019-02-22;修订日期:2019-07-26
通信作者:刘 辛,教授级高工,博士;电话:020-601086128;E-mail:shaneliu118@163.com