Trans. Nonferrous Met. Soc. China 25(2015) 1194-1199
Effects of TaC on microstructure and mechanical properties of coarse grained WC-9Co cemented carbides
Wei SU, Ye-xi SUN, Hai-lin YANG, Xian-qi ZHANG, Jian-ming RUAN
Powder Metallurgy Research Institute, Central South University, Changsha 410083, China
Received 31 March 2014; accepted 27 October 2014
Abstract: Coarse grained WC-9Co cemented carbides with 0-1.0% TaC (mass fraction) were fabricated by HIP-sintering and gas quenching. The effects of TaC on the microstructures and mechanical properties were investigated using scanning electron microscopy (SEM), energy dispersive X-ray analysis (EDS), X-ray diffractometry (XRD) and mechanical properties tests. The results show that the maximum values of hardness and strength are HV 1124 and 2466 MPa respectively when 0.4% TaC is added. When the content of TaC is more than 0.6%, the grain size of WC is no longer affected by the amount of TaC, and (W,Ta)C occurs as well. Moreover, the strength and fracture toughness increase and the (Ta+W) content decreases with the increase of TaC content. The dependence of (Ta+W) content on the mechanical properties indicates that (Ta+W) content in Co should be decreased as low as possible to improve the mechanical properties of coarse grained WC-TaC-9Co cemented carbides with the microstructure of WC+γ two phase regions.
Key words: coarse grained WC–9Co cemented carbides; TaC; Ta content; W content
1 Introduction
WC-Co cemented carbide consists of hard phase WC embedded in ductile phase Co, which is prepared usually by a powder metallurgy and liquid phase sintering methodology [1-3]. Coarse grained WC-Co cemented carbide is widely employed in mining and drilling due to the perfect combination of thermal conductivity, toughness and shock resistance [4-6]. However, the disadvantages of coarse grained WC-Co over fine grained WC-Co are inferior hardness, wear resistance and strength [7]. A wide range of properties can be obtained via adjusting the volume fraction and the grain size of WC phase. In other words, the hardness can increase with increasing of WC volume fraction and/or decreasing of WC grain size, while the fracture toughness can increase with increasing of Co content and/or WC grain size. Thus, coarse grained WC-Co cemented carbides with 5%-10% Co (mass fraction) are a promising material offering a very good balance of wear resistance and fracture resistance [8].
Sintering temperature of the coarse grained WC-Co cemented carbide is generally 20-50 °C higher than that of the fine grained WC-Co cemented carbide for its lower surface energy of initial powder and lower Co content. However, the increase of temperature means that the abnormal grain growth is easier to occur [9-12]. Therefore, a small amount of other transition metal carbides as grain inhibitors are added to inhibit the growth of WC grain, consequently improving the microstructure homogeneity and mechanical properties of WC-Co cemented carbide [12-19]. Generally, the order of overall inhibition effectiveness is VC>Cr3C2> NbC>TaC>TiC. However, VC results in the embrittle- ment of WC-Co cemented carbide, Cr3C2 is not suitable for using in high temperature conditions, TiC has the worst inhibition effectiveness. It seems that NbC and TaC are the best grain inhibitors for coarse grained WC-Co cemented carbides as their high melting temperature and low thermal expansion. In comparison to TaC, NbC is more hostile in the densification of WC-Co cemented carbides.
MAHMOODAN et al [14] demonstrated that nano grained WC-10Co cemented carbide with 0.6% TaC (mass fraction) addition obtains the maximum hardness and the intermediate fracture toughness. SOLEIMANPOUR et al [15] reported that the transverse rupture strength (TRS) continues to increase and fracture toughness shows an opposite trend in WC–10Co cemented carbide within 0–2% (Ta,Nb)C addition. However, neither of them mentioned the influence of TaC addition on Ta and W contents in Co and the dependence of Ta and W content in Co on the mechanical properties of WC-Co cemented carbide. It was put forward by CHA et al [20] that the fracture toughness was proportional to C content in Co. In other words, fracture toughness decreases with the increase of W content because of the inverse relationship between C and W content. How Ta content varies with increasing TaC addition and whether the variation of Ta content affects W content are well worth studying. In addition, it is necessary to explore whether the variation of Ta and W content influences the mechanical properties of WC–Co cemented carbides.
The mechanical properties of WC-Co are affected by the HCP/FCC ratio of Co phase [20]. If HCP Co and FCC Co co-exist, it is difficult to determinate the dependence of Ta and W content in Co on the mechanical properties of WC-Co cemented carbides. The transformation temperature of FCC Co to HCP Co decreases with decreasing Co content in WC-Co cemented carbide [16]. In other words, the lower the Co content, the higher the FCC/HCP ratio of Co phase. Combining with quenching process, the transformation of FCC Co to HCP Co could be suppressed completely for WC-Co cemented carbides with low Co content [16]. Nevertheless, Co content should be as much as possible to discern accurately the variation of Ta content because of the limited solubility of TaC in Co.
In the present work, six sets of coarse grained WC-TaC-9Co cemented carbides with only FCC Co phase were fabricated by HIP–sintering and gas quenching. The effects of TaC addition on microstructures and mechanical properties of coarse grained WC-9Co were investigated. The influence of the variation of Ta, W content on mechanical properties was discussed as well.
2 Experimental
2.1 Preparation of WC-TaC-9Co alloys
WC (total carbon: 6.14%), Co and TaC (total carbon: 6.21%) with particle sizes of 20.2, 1.0 and 0.87 μm, respectively, were used as starting materials. Six sets of WC-TaC-9Co powders were weighted with the nominal compositions of the alloys shown in Table 1. Six powder mixtures were milled separately in a ball mill (36 h, ethyl alcohol, mass ratio of ball to powder of 3.5:1) with 1.8% paraffin. Subsequently, the milled powders were dried in the vacuum oven at 100 °C for 2 h, and granulated by passing through a 180 μm sieve.
Table 1 Nominal compositions of six alloys (mass fraction, %)
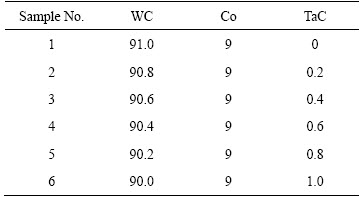
The compacts were pressed under a uniaxial pressure of 200 MPa. Dewaxing and pre-sintering of green compacts were carried out in a separated cycle in flowing hydrogen. Six sets of samples were fabricated by HIP–sintering at 1450 °C and 5 MPa. The holding time was 100 min. When temperature dropped to 1250 °C, Ar was inflated to rapidly cool the alloys and to suppress the transformation from FCC Co to HCP Co during cooling.
2.2 Characterization
The as-sintered alloys were sectioned, ground, polished and then etched for 2 min with Murakami solution. Microstructures were observed by a scanning electron microscope (SEM, JSM-6360LV, Joel). The mean WC grain sizes were measured by the linear intercept method. The relative densities of the sintered alloys were measured by the Archimedes method. The hardness was measured by HTV-PHS30 tester with 300 N load. Fracture toughness test and transverse rupture test were conducted using a three-point bending instrument based on Instron3369 according to ASTM E1290 and ISO 3327, respectively. The ZDHC40 coercive meter and the magnetic saturation induction tester were used to determinate coercivity and magnetic saturation (Ms) of the as-sintered alloys, respectively.
Ta and W contents in Co of the six alloys were discerned by a scanning electron microscope (Quanta250, FEG) equipped with EDS Genesis software. However, EDS analysis was hard to detect accurately the variation of Ta and W contents in Co via a metallographic structure of WC-Co because of the interference of WC grain [6]. To investigate the effect of Ta and W contents on Co binder phase, the selective electrolysis corrosion was conducted in the DF1700S adjustable DC current power unit to corrode WC phase and to reserve Co phase. The composition of the electrolyte was 4 mol/L NaOH, 3% C4H6O6 and 2% NaClO4 [6]. In addition, the identification of Co phase structure was determined by X-ray diffractometer (D/max 2550, Rigaku).
3 Results and discussion
3.1 Microstructures of WC-TaC-9Co alloys
Figure 1 shows the backscattered electron (BSE) images of the microstructures of WC-TaC-9Co alloys sintered at 1450 °C. When TaC addition is less than 0.4%, abnormal growth of WC grains is observed obviously and these abnormal grain sizes are close to 20 μm. When TaC addition is more than 0.4%, abnormal WC grains disappear. However, grey (Ta,W)C appears and the amount of grey (Ta,W) C increases with increasing TaC content.
Densities, grain sizes and coercivities of the alloys are listed in Table 2. The densities of alloys change slightly in the range of 14.49-14.56 g/cm3 with the addition of TaC. It can be seen from Table 2 that coercivity initially increases from 2.1 kA/m to 3.2 kA/m, and then keeps around 3.2 kA/m with the increase of TaC addition. The higher the coercivity, the smaller the WC grains size. The variation trend of coercivity is consistent with the observation of WC-TaC-9Co microstructures. In other words, TaC addition does not further inhibit the growth of WC grains when TaC is more than 0.6%.
The growth of WC grains is far less certain during sintering because of the differences in the size and lattice distortion of WC particles [21,22]. As shown in Fig. 1, the addition of TaC is deemed to tolerate more uncertainty of WC grain growth [21] and to eliminate the abnormal growth of WC grains. Although Ta segregation in WC/WC boundary is only supported by ab calculation, Ta segregation in WC/Co boundary has been verified by experiments [23]. Therefore, TaC addition could reduce interface energy of WC-Co sintering system and inhibit the growth of WC grains through segregation [10,12]. In addition, a portion of TaC addition is consumed for dissolving in Co. Thus, (Ta,W)C occurs when the amount of TaC addition outweighs the total sum of the segregated TaC and the dissolved TaC.
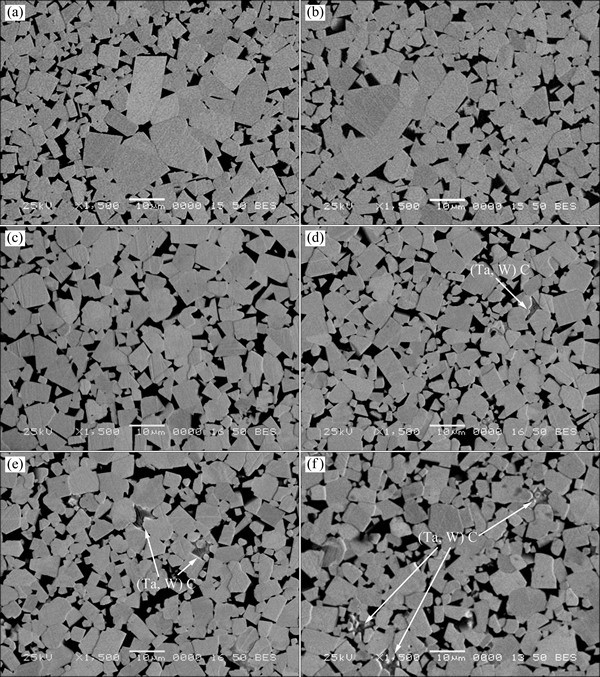
Fig. 1 Backscattered electron SEM images of WC-9Co with 0 (a), 0.2% (b), 0.4% (c), 0.6% (d), 0.8% (e) and 1.0% (f) TaC addition
Table 2 Porosities, densities, grain sizes and coercivities of WC–TaC–9Co alloys
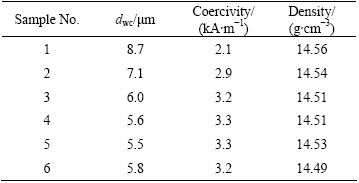
3.2 Mechanical properties of WC-TaC-9Co alloys
Figure 2 shows the X-ray diffraction patterns of Co phase in WC-9Co alloys. No HCP Co is detected and only FCC Co is found. In this case, the effects of Co phase structure on the mechanical properties of WC-TaC-Co alloys could be eliminated.
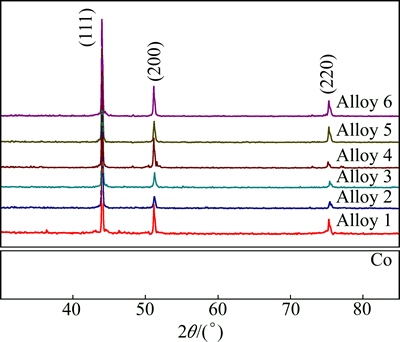
Fig. 2 XRD patterns of Co phase in WC-9Co alloys
Figure 3 shows that the mechanical properties of WC-TaC-9Co alloys vary with the amounts of TaC addition. When 0.4% TaC is added, hardness and TRS increase from HV 927, 1952 MPa for Alloy 1 to HV 1124, 2466 MPa for Alloy 3, respectively. Meanwhile, fracture toughness decreases from 22.35 MPa·m1/2 to 19.12 MPa·m1/2 correspondingly. The results conform to Hall-Petch relation and the inverse proportional relation between fracture toughness and hardness [7]. TRS and fracture toughness of Alloy 4 (WC+γ+(W,Ta)C) are lower than those of Alloy 3 (WC+γ), which demonstrates that (W,Ta)C could deteriorate TRS and fracture toughness for its brittleness. When TaC is more than 0.6%, TRS and fracture toughness slightly increase with increasing TaC content, which seems to be contradictory with the observation of microstructures.
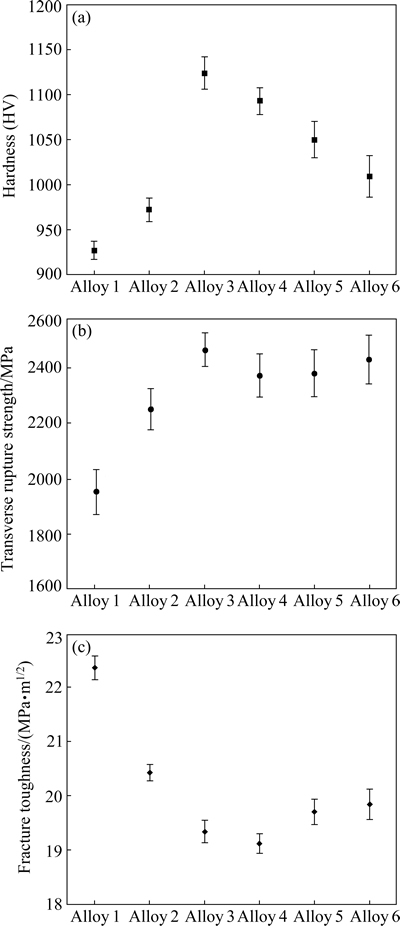
Fig. 3 Dependence of hardness (a), TRS (b), and fracture toughness (c) on TaC addition in WC-9Co alloys
3.3 W and Ta content in Co binder phase
Figure 4 shows the morphology of Co phase and corresponding EDS analysis of Alloy 1 after the selective electrolysis corrosion of WC phase. Five micro-areas were selected to conduct EDS analysis in every alloy. The average results of map analysis of W and Ta contents are summarized in Table 3. It can be seen from Table 3 that W content decreases from 8.51% to 4.19%, while Ta content initially increases to 3.09% and then decreases to 2.30% with the increase of TaC addition. Although EDS is a semi-quantitative analysis, it can present the variation tendency of Ta and W contents in Co binder phase. Compared Alloy 4 with Alloy 3, it could be concluded that Ta content reaches the maximum value with the occurrence of (W,Ta)C. With the further increase of TaC addition, Ta content decreases and (W,Ta)C content increases. It seems that the growth of (W,Ta)C consumes Ta and W in Co binder phase. Consequently, Ta and W contents in Co binder phase decrease with the increase of (W,Ta)C.
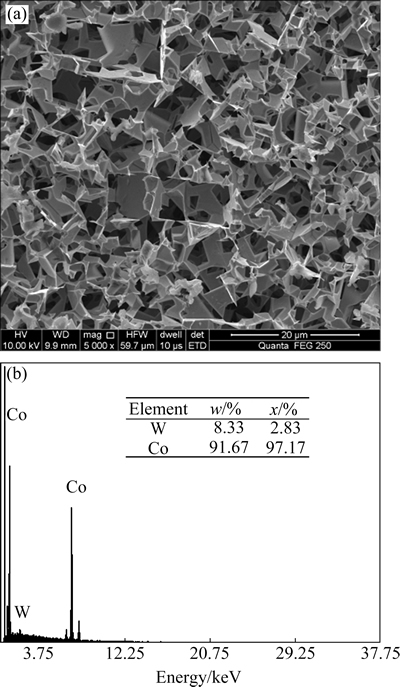
Fig. 4 SEM morophology of Co phase by selective corrosion of WC phases (a) and EDS result (b) derived from Alloy 1
Table 3 W and Ta contents in Co binder phase and magnetic saturation of alloys
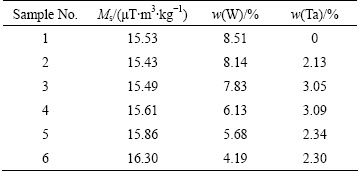
Combining Fig. 3 and Table 3, it shows that TRS and fracture toughness increase while (Ta+W) content decreases with more than 0.6% TaC addition. It can be concluded that the decrease of (Ta+W) content contributes to the increase of TRS and fracture toughness. In other words, the adverse effect of brittle (W,Ta) C on TRS and fracture toughness can be eliminated by the decrease of (Ta+W) content. As for coarse grained WC-Co alloys, load is undertaken basically by hard phase WC and (W,Ta)C during hardness test. Thus, hardness is more susceptible to (W,Ta)C for hardness of (W,Ta)C is lower than that of WC [14]. In other words, the more the (W,Ta)C phase, the lower the hardness.
4 Conclusions
1) TaC addition could inhibit the growth of WC grain, eliminate the abnormal WC grain and decrease the size of WC grain for coarse grained WC-9Co cemented carbides. When TaC addition is over 0.4%, WC grain size does not further decrease, while (Ta,W)C occurs and increases with increasing TaC addition. The amount of TaC addition could influence the W and Ta content in Co binder phase. W content decreases with the increase of TaC addition. When the content TaC is 0.6%, the maximum of Ta content (3.09%) is obtained in coarse grained WC-9Co cemented carbide.
2) The variation of W and Ta contents and WC grain size influence the mechanical properties of coarse grained WC-9Co cemented carbide. When TaC is less than 0.4%, TRS and hardness significantly increase with increasing TaC addition, while fracture toughness decreases with decreasing WC grain size. The best comprehensive mechanical properties are obtained in coarse grained WC-0.4TaC-9Co with HV 1124, TRS 2466 MPa, fracture toughness 19.34 MPa·m1/2 and grain size 6.0 μm. When TaC is more than 0.6%, strength and fracture toughness increase, while (Ta+W) content in Co decreases with increasing TaC addition.
3) The dependence of the mechanical properties on W and Ta contents indicates that the decrease of (Ta+W) content in Co is conducive to improving strength and fracture toughness of WC-TaC-9Co cemented carbides with WC+γ+(W,Ta)C phases. Therefore, it may be an effective way to improve the mechanical properties that (Ta+W) content in Co maintains at a low value for coarse grained WC-TaC-9Co cemented carbides with the microstructure of WC+γ two phase regions.
References
[1] MAHMOODAN M, ALLAKBARZADEH H, GHOLAMIPOUR R. Sintering of WC-10%Co nano powders containing TaC and VC grain growth inhibitors [J]. Transactions of Nonferrous Metals Society of China, 2011, 21(5): 1080-1084.
[2] BAO Rui, YI Jian-hong, PENG Yuan-dong, ZHANG Hao-ze. Effects of microwave sintering temperature and soaking time on microstructure of WC-8Co [J]. Transactions of Nonferrous Metals Society of China, 2013, 23(2): 372-376.
[3] HIROKO M, SOTOMI I, NORIYASU O, KENICHI M, SYO K, SHINGO K. Effect of stress ratio on fatigue lifetime and crack growth behavior of WC-Co cemented carbide [J]. Transactions of Nonferrous Metals Society of China, 2014, 24(s1): s14-s19.
[4] REN X Y, MIAO H Zh, PENG Zh J. A review of cemented carbides for rock drilling: An old but still tough challenge in geo–engineering [J]. International Journal of Refractory Metals & Hard Materials, 2013, 39: 61-77.
[5] BESTE U, JACOBSON S. A new view of the deterioration and wear of WC/Co cemented carbide rock drill buttons [J]. Wear, 2008, 264: 1129-1141.
[6] ZHANG L, XIE M W, CHENG X, NAN Q, WANG Zh, FENG Y P. Micro characteristics of binder phases in WC-Co cemented carbides with Cr-V and Cr-V-RE additives [J]. International Journal of Refractory Metals & Hard Materials, 2013, 36: 211-219.
[7] O'QUIGLEY D G F, LUYCKXA S, JAMESB M N. New results on the relationship between hardness and fracture toughness of WC-Co hardmetal [J]. Materials Science and Engineering A, 1996, 209: 228-230.
[8] BESTE U, JACOBSON S, HOGMARK S. Rock penetration into cemented carbide drill buttons during rock drilling [J]. Wear, 2008, 264: 1142-1151.
[9] SHATOV A V, PONOMAREV S S, FIRSTOV S A, WARREN R. The contiguity of carbide crystals of different shapes in cemented carbides [J]. International Journal of Refractory Metals & Hard Materials, 2006, 24: 61-74.
[10] GILLE G, SZESNY B, DREYER K, VAN DEN BERG H, SCHMIDT J, GESTRICH T, LEITNER G. Submicron and ultrafine grained hardmetals for microdrills and metal cutting inserts [J]. International Journal of Refractory Metals & Hard Materials, 2002, 20: 3-22.
[11] SOMMER M, SCHUBERT W D, ERICH Z, WARBICHLER P. On the formation of very large WC crystals during sintering of ultrafine WC-Co alloys [J]. International Journal of Refractory Metals & Hard Materials, 2002, 20: 41-50.
[12] MORTON C W, WILLS D J, STJERNBERG K. The temperature ranges for maximum effectiveness of grain growth inhibitors in WC-Co alloys [J]. International Journal of Refractory Metals & Hard Materials, 2005, 23: 287-293.
[13] HUANG S G, LIU R L, LI L, VAN DER BIEST O, VLEUGELS J. NbC as grain growth inhibitor and carbide in WC-Co hardmetals [J]. International Journal of Refractory Metals & Hard Materials, 2008, 26: 389-395.
[14] MAHMOODAN M, ALLAKBARZADEH H, GHOLAMIPOUR R. Microstructural and mechanical characterization of high energy ball milled and sintered WC-10wt%Co-xTaC nano powders [J]. International Journal of Refractory Metals & Hard Materials, 2009, 27: 801-805.
[15] SOLEIMANPOUR A M, ABACHI P, SIMCHI A. Microstructure and mechanical properties of WC-10Co cemented carbide containing VC or (Ta, Nb) C and fracture toughness evaluation using different models [J]. International Journal of Refractory Metals & Hard Materials, 2012, 31: 141-146.
[16] UPADHYAYA G S. Materials Science of cemented carbides—an overview [J]. Materials and Design, 2001, 22: 483-489.
[17] XIAO D H, HE Y H, LUO W H, SONG M. Effect of VC and NbC additions on microstructure and properties of ultrafine WC-10Co cemented carbides [J]. Transactions of Nonferrous Metals Society of China, 2009, 19(6): 1520-1525.
[18] ZHANG Li, CHENG Shu, CHENG Xin, WU Hou-ping, MA Y, XIONG Xiang-jun. Effects of cubic carbides and La additions on WC grain morphology, hardness and toughness of WC-Co alloys [J]. Transactions of Nonferrous Metals Society of China, 2012, 22(7): 1680-1685.
[19] OBADELE B A, OLUBAMBI P A, JOHNSON O T. Effects of TiC addition on properties of laser particle deposited WC-Co-Cr and WC-Ni coatings [J]. Transactions of Nonferrous Metals Society of China, 2013, 23(12): 3634-3642.
[20] CHA S I, HONG S H, HA G H, KIM B K. Mechanical properties of WC–10Co cemented carbides sintered from nanocrystalline spray conversion processed powders [J]. International Journal of Refractory Metals & Hard Materials, 2001, 19: 397-403.
[21] SCHUBERT W D, BOCK A, LUX B. General aspects and limits of conventional ultrafine WC powder manufacture and hard metal production [J]. International Journal of Refractory Metals & Hard Materials, 1995, 13: 281-296.
[22] GILLE G, BREDTHAUER J, GRIES B, MENDE B, HEINRICH W. Advanced and new grades of WC and binder powder—their properties and application [J]. International Journal of Refractory Metals & Hard Materials, 2000, 18: 87-102.
[23] WEIDOW J,
H O. Grain and phase boundary segregation in WC-Co with TiC, ZrC, NbC or TaC additions [J]. International Journal of Refractory Metals & Hard Materials, 2011, 29: 38-43.
TaC含量对WC-9Co粗晶硬质合金显微组织和力学性能的影响
苏 伟,孙业熙,杨海林,张贤其,阮建明
中南大学 粉末冶金研究院,长沙 410083
摘 要:采用热等静压烧结和气淬工艺制备6种不同TaC含量的WC-9Co粗晶硬质合金。利用扫描电镜,能谱仪、X射线衍射等方法研究TaC含量对WC-9Co粗晶硬质合金显微组织、Co中Ta和W含量的影响,并对合金的力学性能进行测试和比较。结果表明:当TaC添加量为0.4%时,WC晶粒生长被明显抑制,WC-9Co的硬度和强度达到最大值,分别为HV 1124和2466 MPa。当TaC添加量超过0.6%时,WC晶粒不再进一步减小,合金显微组织中出现(W,Ta)C相;而且随着TaC含量的增加,合金的强度和韧性提高,同时Co中的(Ta+W)含量下降。这表明,对于具有正常WC+γ组织的粗晶WC-TaC-9Co合金,降低Co中的(Ta+W)含量有利于提高其力学性能。
关键词:粗晶WC-9Co硬质合金;TaC;Ta含量;W含量
(Edited by Yun-bin HE)
Foundation item: Project (2013zzts025) supported by the Fundamental Research Funds for the Central Universities of China
Corresponding author: Jian-ming RUAN, Tel/Fax: +86-731-88836827; E-mail: jianming@csu.edu.cn
DOI: 10.1016/S1003-6326(15)63715-3