
Temperature measurement based on radialization power for micro-hotplate
ZHANG Tong(张 彤), QI Qi(漆 奇), LIU Kui-xue(刘奎学),
LIU Li(刘 丽), ZHANG Lei(张 蕾), XU Bao-kun(徐宝琨)
College of Electronic Science and Engineering, Jilin University, Changchun 130012, China
Received 10 April 2006; accepted 25 April 2006
Abstract: A novel method to measure the temperature on the surface of micro-hotplate was presented. The tiny fiber probe and the optical power meter were employed to measure the sample radialization power. By means of comparing the relationship between the radialization power and the temperature, sample surface temperature can be discerned accurately. Such an approach has provided more accuracy than traditional temperature measurements. The experimental result based on this method is quite similar to that of simulation by the finite element analysis (FEA) software of Ansys in theory. This measurement is very useful for measuring temperature for these micro samples prone to be untouchable.
Key words: micro-hotplate; temperature; heat distributing; radialization power; optical power meter; fiber probe
1 Introduction
Gas sensors, one kind of chemical sensors, are widely used in the field of industry, agriculture, storage, domestic life and so on. General gas sensors are sintering structure and their power consumption is around 1.0-1.5 W[1, 2]. Such power consumption is considered too high to assemble a portable meter in the practical use. Consequently more and more researchers changed their interests and focused on the study of micro-structure gas sensors with low power consumption[3-7].
Micro-structure gas sensor, like most gas sensors, can work well only to be heated to a certain level (300-400 ℃ customarily)[8]. The effect of control temperature on the properties of functional materials composed of micro-structure were investigated experimentally[9], and the work temperature was numerically simulated under different loading environment[10]. Being one of the most important parts of micro-structure gas sensor, micro-hotplate provides the required quantity of heat for the sensitive thin-films in order to make it operational, and usually keeps its temperature at 300 ℃ or above[11, 12]. The size of micro-hotplate is catholically tiny. The design of micro-hotplate consists of heating field distribution design and structure design[13, 14]. The former is to accomplish lower power heating, uniform heating, speedy heating and rapid change temperature[15, 16]. Therefore, the temperature measurement for micro-hotplate is very significant and necessary.
Most of the conventional temperature measuring devices such as thermocouple and infrared thermoscope fail to measure temperature for the micro-hotplate we designed, because the micro-hotplate with an area that ranges from 0.2 mm×0.2 mm to 1 mm×1 mm is too minute. Although the thermocouple is widely used to measure temperature, the units of thermocouple are several square micrometers, being too large for micro-hotplate. On the other hand, thermocouple must contact the sample when it is used to measure temperature. When the hot micro-hotplate is contacted the cold thermocouple, some heat will be lost and the result is imprecise. The infrared thermoscope is another device to measure temperature, but the area of facula is also much larger than the field of the micro-hotplate. So how to measure the temperature on the surface of micro-hotplate is still an unsolved problem.
In the following experiments, we set up a system which is capable of measuring the temperature on the surface of the micro-hotplate in an untouched way. This system is helpful for micro area and untouched sample.
2 Experimental
2.1 Sample preparation
The resistance of gas sensors can change when they absorb different levels of ambient gas atmosphere concentration. The presented gas sensor with the total size of 5 mm×1.7 mm and the heater size of 1.25 mm×1 mm was fabricated on silicon substrate by semiconductor process, as shown in Fig.1 (a). This gas sensor comprises platinum heater and platinum signal electrode sandwiched between sensing material layer and SiO2 insulating layer on isolated <100> silicon substrate. The heater and signal electrode were designed on the same plane, not only to make the heating more uniform, but also to make the fabrication easier. This gas sensor was required to operate with a supply of 6 V and accordingly the heater was designed 80 Ω. In addition, the temperature distribution on the surface of substrate is analyzed and compared at different widths and spaces with the finite element analysis (FEA) tool[17]. When the widths of heater, signal electrode and space were presumed as 50 μm, 50 μm, 25 μm respectively, the simulation results illustrate that the heat distribution of this sensor is even. The final design layout is shown in Fig.1 (b). The black strip is the heater, and the two-separate-interdigitated electrode is the platinum signal electrode. Fig.1(c) shows the photograph of gas sensor taken through microscope. In the following experiments, we sample this micro-hotplate, which is the shown sensor without sensing layer.
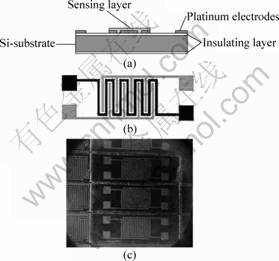
Fig.1 Schematic diagram of microstructure gas sensor:(a) Cross-section view; (b) Design layout; (c) Sample photo
2.2 Calibration curve
Any material has definite radialization power above 0 K, which is determined by its temperature and physical character. Our temperature measurement utilizes the relation between the temperature and the radialization power from the sample. The sample we designed is built on Si-substrate just like most micro-hotplates. The Si-chip which consist of many uncut micro-hotplates is chosen to get the calibration curve. This Si-chip is so large that the lost heating can be neglected, as a consequence, its temperature can be measured by thermoscope. In this system for calibration curve, the Si-chip, which is laid in the black box for heat insulation and ray insulation, is uniformly heated. Ni-Cr thermocouple is employed to measure the temperature, and optical power meter(JW3203R made in China)is to measure radialization power. This system is shown in Fig.2.
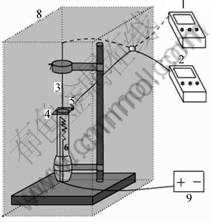
Fig.2 Schematic diagram of system for calibration curve between temperature and radialization: 1 Optical power meter; 2 Multimeter; 3 Fiber probe; 4 Sample platform; 5 Ni-Cr thermocouple; 6 Heater; 7 Hold set; 8 Black box; 9 DC power supply
2.3 Temperature measurement for micro-hotplate
Fig.3 shows the schematic diagram of the system for measuring the sample radialization power. Because the radialization power is only determined by physical character at a certain temperature, the temperature-radialization relation of the micro-hotplate is thoroughly the same as that of corresponding Si-chip. Accordingly, once the radialization power has been measured, we can get the temperature on micro-hotplate by comparing the calibration curve of Si-chip. In this system, the sample is laid in black box as well. Fiber probe with diameter ranging from 8 μm to 50 μm is available for different ranges of area. The appropriate diameter leads to adequate precision and enough radialization power. The diameter of 50 μm fiber probe is employed in our experiment based upon our design. The stabilized DC power supply with controllable voltage from 1 V to 15 V can display the voltage and the current
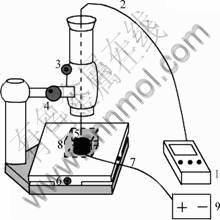
Fig.3 Schematic diagram of system for untouched fiber probe measuring radialization power on micro-hotplate: 1 Optical power meter; 2 Fiber probe; 3 Vertical position control for fiber; 4 Horizontal position control for fiber; 5 Sample platform; 6 x-direction position control for pedestal; 7 y-direction position control for pedestal; 8 Black box; 9 DC power supply
on its control panels, so the power consumption of the micro-hotplate can be computed. There is a position control button in this system for adjusting the position of the sample at the precision of micrometer. When the micro-hotplate is heated, the radialization power can be measured point-by-point with the space of several μm, and then the temperature distributing of entire surface of the micro-hotplate can be obtained.
3 Results and discussion
The Si-chip was delicately heated from indoor temperature to about 400 ℃ and then naturally cooled for measuring the calibration curve. The optical power meter provides four kinds of wavelengths (850, 980,1 310 and 1 550 nm) to be possible to choose. Fig.4 shows the results at these four wavelengths. The curve is almost horizontal below 250 ℃, but the radialization power apparently increases above 300 ℃. The curves of 850 nm and 980 nm have an interruption at about 280 ℃, and not very stable for 1 550 nm. Accordingly 1 310 nm is finally chosen in the experiment because of continuity and stability, so Fig.4(c) is considered to be the calibration curve.
Fig.5 shows the relationship between temperature and power consumption of this micro-hotplate. The temperature is the transformed result from Fig.4(c), and the power consumption is the calculated result based on voltage and current.
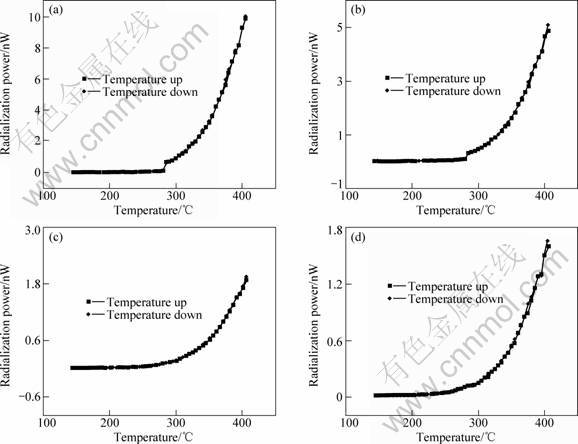
Fig.4 Thermal radialization results of micro-hotplate at different wavelengths: (a) 850 nm; (b) 980 nm; (c) 1 310 nm; (d) 1 550 nm
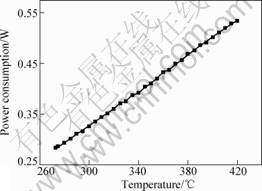
Fig.5 Power consumption of micro-hotplate, based on radializa-tion power at 1 310 nm
The back of micro-hotplate is chosen in order to reduce the complication in measuring the radialization point-by-point. Then the temperature distributing of the back of micro-hotplate can be displayed. The Si-substrate with the thickness of about 400 μm has high thermal conductivity and the temperature distributions of face and back are similar. Fig.6 (a) shows the contour-color fill (OriginPro software) based on the matrix of temperature data. The full sample thermal simulation has been carried out in order to investigate the temperature distributing of micro-hotplate and compare the result from experiment. A finite element model (ANSYS software) of the micro-hotplate structure was constructed using solid 70 with exact dimensions of the micro-hotplate to simulate the temperature distributing, and each kind of physics parameters used in the process of the FEA simulation and analysis is listed in Table 1. It can be seen from Fig.6 (b), the thermal simulation results for the micro-hotplate show that the central active area is a rectangle among points of (1.5, 0), (3.5, 0), (1.5, 1.6) and (3.5, 1.6) with the temperature about 330 ℃, and the difference in temperature between the center and the edge is about 40 ℃. These comply with the experimental results. The conspicuous difference between thermal simulation results and experimental results lies in the fact that the highest temperature area of micro-hotplate is the welding point in experiment, instead of the central active area. This is because the contact resistance of welding point affects the behavior of temperature distributing and results in the differences of simulation and experiment.
Table 1 Physics parameters used in process of FEA simulation and analysis
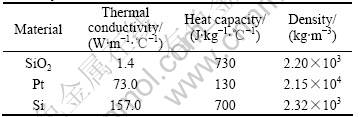
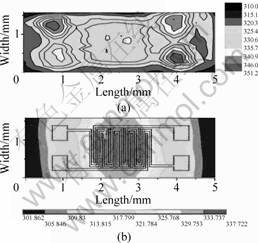
Fig.6 Comparison of measured (a) and simulated (b) temperature distribution of micro-hotplate
4 Conclusions
A novel untouched temperature measurement based on radialization power has been reported. The research results show that the experimental results are really the same as those obtained by simulation. Moreover, with the different fiber probes the range of measuring area can vary from 8 μm×8 μm to 50 μm×50 μm, and thus it can meet the requirements of micro-hotplate in experiment. Hence complication of the temperature measurement on micro-hotplate is reduced and the precision is enhanced. This measurement is very useful for measuring temperature for these micro samples prone to be untouchable.
References
[1] MEIXNER H, GERBLINGER J, LAMPE U, FLEISCHER M. Thin-film gas sensors based on semiconducting metal oxides[J]. Sensors and Actuators B, 1995, 23: 119-225.
[2] TETERYCZ H, KITA J, BAUER R, GOLONKA L, LICZNERSKI B, NITSCH K, WISNIEWSKI K. New design of an SnO2 gas sensor on low temperature cofiring ceramics[J]. Sensors and Actuators B, 1998, 47: 100-103.
[3] GARDNER J W. Microsensors Principles and Applications[M]. New York: Wiley Chicester, 1994. 331-337.
[4] LEE D S, LIM J W, LEE S M, HUH J S, LEE D D. Fabrication and characterization of micro-gas sensor for nitrogen oxides gas detection[J]. Sensors and Actuators B, 2000, 64: 31-36.
[5] ZEE F, JUDY J W. Micromachined polymer-based chemical gas sensor array[J]. Sensors and Actuators B, 2001, 72: 120-128.
[6] LEE S M, DYER D C, GARDNER J W. Design and optimization of a high-temperature silicon micro-hotplate for nanoporous palladium pellistors[J]. Microelectronics Journal, 2003, 34: 115-126.
[7] LE?N I, AMADOR R, KOHLHOF K. Evaluation of MUMPS polysilicon structures for thermal flow sensors[J]. Microelectronics Reliability, 2004, 44: 651-655.
[8] RETTING F, MOOS R. Ceramic meso hot-plates for gas sensors[J]. Sensors and Actuators B, 2004, 103: 91-97.
[9] ZHENG X J, ZHOU Y C, ZHONG H. Dependence of fracture toughness on annealing temperature in PZT thin films produced by metal organic decomposition[J]. Journal of Materials Research, 2003, 18(3): 578-584.
[10] ZHENG X J, ZHOU Y C, NIN M Z. Thermopiezoelectric response of a piezoelectric thin film PZT-6B deposited on MgO (100) substrate due to a continuous laser[J]. Int J Solid Structure, 2002, 39(15): 3935-3957.
[11] SEMANCIK S, CAVICCHI R E, WHEELER M C, TIFFANY J E, POIRIER G E, WALTON R M, SUEHLE J S, PANCHAPAKESAN B, DEVOE D L. Microhotplate platforms for chemical sensor research[J]. Sensors and Actuators B, 2001, 77: 579-591.
[12] SHARMA R K, CHAN P C H, TANG Zhen-an, YAN Gui-zhen, HSING I M, SIN J K O. Investigation of stability and reliability of tin oxide thin-film for integrated micro-machined gas sensor devices[J]. Sensors and Actuators B, 2001, 81: 9-6.
[13] YAN Gui-zhen, TANG Zhen-an, CHAN P C H, SIN J K O, HSING I M, WANG Yang-yuan. An experimental study on high-temperature metallization for micro-hotplate-based integrated gas sensors [J]. Sensors and Actuators B, 2002, 86: 1-11.
[14] CHUNG G S. Fabrication and characterization of micro-heaters with low-power consumption using SOI membrane and trench structures[J]. Sensors and Actuators A, 2004, 112: 55-60.
[15] FUNG S K H, TANG Zhen-an, CHAN P C H, SIN J K O, CHEUNG P W. Thermal analysis and design of a micro-hotplate for integrated gas-sensor applications[J]. Sensors and Actuators A, 1996, 54: 482-487.
[16] MOULTON T, ANANTHASURESH G K. Micromechanical devices with embedded electro-thermal-compliant actuation[J]. Sensors and Actuators A, 2001, 90: 38-48.
[17] ZHANG Tong, YANG Guang-li, LI Chun-ming, XU Bao-kun. Simulation and design of micro-hotplate of micro-structure gas sensor based on Si-substructure[J]. Measurement and Control Technology, 2004, 23(5): 12-13.(in Chinese)
(Edited by YANG You-ping)
Foundation item: Project (60104006) supported by the National Natural Science Foundation of China; Project(20030322) supported by the Science Technology Office of Jilin Province
Corresponding author: ZHANG Tong; Tel: +86-431-5168385; Fax: +86-431-8923907; E-mail: zhangtong@jlu.edu.cn