文章编号:1004-0609(2015)-01-0211-09
机械活化-盐酸常压浸出钛铁矿的影响
伍 凌,陈嘉彬,钟胜奎,张晓萍,刘洁群
(苏州大学 沙钢钢铁学院,苏州 215021)
摘 要:采用机械活化-盐酸常压浸出法对钛铁矿进行了选择性浸出,研究机械活化对钛铁矿的结构、形貌、粒度及浸出效果的影响。结果表明,机械活化可以细化钛铁矿的粒径,增加颗粒表面的粗糙度,从而增大其比表面积;机械活化可以破坏钛铁矿晶粒的完整性,并产生大量晶格缺陷,使晶格膨胀,上述作用均能强化钛铁矿浸出。最优浸出条件为:盐酸质量分数20%,反应温度100 ℃,酸矿比1.2,钛铁矿活化时间2 h。最优条件下Ti和Fe的浸出率分别为1.07%和95.5%,最终Ti和Si富集在渣中,其他元素进入浸出液。将上述得到的富钛渣煅烧获得了品位高于90%的人造金红石。
关键词:钛铁矿;机械活化;盐酸;浸出
中图分类号:TF0 文献标志码:A
Effect of mechanical activation on hydrochloric acid leaching ilmenite at atomospheric pressure
WU Ling, CHEN Jia-bin, ZHONG Sheng-kui, ZHANG Xiao-ping, LIU Jie-qun
(School of Iron and Steel, Soochow University, Suzhou 215021, China)
Abstract: The elements of ilmenite were selectively leached by mechanical activation and hydrochloric acid leaching at atmospheric pressure, the effect of mechanical actuation on the microstructure, morphology, size and leaching results was studied. The results show that mechanical activation can refine the grain size and increase the surface roughness of ilmenite particles, which result in the increase of the specific surface area. The mechanical activation can also disrupt the integrity of ilmenite crystal grains, and induce the formation of a large number of lattice defects, which lead to the lattice expansion. All the above actions can strengthen the leaching of ilmenite. The optimal leaching conditions are as follows: hydrochloric acid of 20% in mass fraction, reaction temperature of 100 ℃, hydrochloric acid/ilmenite mass ratio of 1.2:1, and mechanical activation time of 2 h. Under the optimal conditions, the leaching ratios of Ti and Fe are 1.07% and 95.5%, respectively. As a result, Ti and Si are still in the slag, and the other elements are enriched in the lixivium. In addition, the synthetic rutile with the grade of over 90% is obtained by calcinating the above titanium-slag.
Key words: ilmenite; mechanical activation; hydrochloric acid; leaching
随着天然金红石资源的日渐枯竭,储量丰富的钛铁矿已成为钛工业的主要原料。然而,钛铁矿中钛的品位较低,直接冶炼流程长、产能低、三废量大,因此,需将其富集成高品位的富钛料,然后再进行冶炼[1-3]。目前报道的富集钛铁矿的方法中,一般都先将钛铁矿在高温下进行预氧化或(和)预还原处理,然后再浸出,将Ti和Fe等元素分离,从而达到富集的目的。如BALDERSON等[4]先将部分Fe(Ⅱ, Ⅲ) 还原成单质Fe,然后用酸浸出,从而使Fe与TiO2得到分离;郭宇峰等[5-6]先将Fe(Ⅱ, Ⅲ) 还原成单质Fe,然后在含氧的氯化铵溶液中将Fe进行锈蚀;SINHA[7]、HU等[8-9]和ZHU等[10]将钛铁矿弱氧化、还原后用盐酸浸出,使得Fe与TiO2得到分离。上述方法虽然能将钛铁分离,但都需要高温预处理,而且浸出通常在高温高压下进行,工艺流程复杂。近年来,许多研究者致力于机械活化-酸浸钛铁矿的研究,如SASIKUMAR等[11]研究了印度Orissa砂矿型钛铁矿的机械活化-硫酸浸出,CHEN[12]和WELHAM等[13]研究了澳大利亚砂矿型钛铁矿的机械活化-硫酸浸出,LI等[14]研究了攀枝花岩矿型钛铁矿的机械活化-硫酸常压浸出,上述方法工艺流程简单,但钛和铁同时被浸出,分离效果不理想。TAO等[15]用盐酸作浸出剂后,上述机械活化-浸出工艺使得钛和铁元素达到了较好的分离效果。
本研究采用机械活化-盐酸常压浸出法对钛铁矿进行浸出,在浸出前不需要高温氧化或还原处理,且浸出在常压下进行,浸出温度较低。主要研究了机械活化对钛铁矿的结构、形貌、粒度及浸出效果的影响。最终将Ti和Si富集在渣中,而Fe、Mg、Mn、Al和Ca等富集在浸出液中,将水解钛渣煅烧得到了品位高于90%的金红石型TiO2。
1 实验
1.1 实验原料
实验原料为攀枝花钢铁有限责任公司钛业分公司生产的钛精矿,矿粉粒度5~180 μm,矿粉的主要化学组成见表1。
表1 钛铁矿的化学组成
Table 1 Chemical composition of ilmenite (Mass fraction, %)
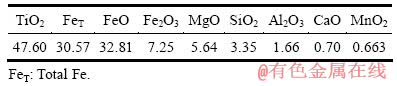
1.2 实验流程
1) 机械活化
机械活化的装置为变频行星式球磨机。按一定的球料比(不锈钢球与钛铁矿质量比分别取10:1、20:1、30:1和40:1)将钛铁矿粉置于不锈钢罐(500 mL)中,每个罐中装有直径为20、10和5 mm的不锈钢球,3种球的质量分别为250、200和50 g。设定球磨机转速为200 r/min,矿粉在空气气氛中活化一定的时间(15、30、60、120和180 min)后取出备用。
2) 浸出
取40 g活化后的钛铁矿粉置入三口烧瓶中,加入一定量(HCl与矿粉质量比分别为0.9:1、1.2:1、1.5:1和1.8:1)不同质量分数(15 %、20 %、25 %和30 %)的盐酸,然后将三口烧瓶密封,迅速加热至指定温度(80、90、100和110 ℃),浸出一定时间(15、30、60、120和180 min)后立即冷却、过滤,检测滤液中各元素的含量;将滤饼用5%盐酸洗涤3次后在100 ℃下干燥12 h,研磨均匀,将样品在空气中于800 ℃下煅烧4 h得人造金红石。
1.3 样品的物理化学表征
采用重铬酸钾滴定法测定浸出液中的铁含量,用硫酸高铁铵滴定法测定浸出渣中的钛含量。采用电感耦合等离子体原子发射光谱(ICP-AES, IRIS intrepid XSP, Thermo Electron Corporation)测定样品中杂质元素的含量。
采用Rigaku Ultima Ⅵ X射线衍射仪测定样品的物相,采用JEOL公司的JSM6380扫描电镜观察样品的形貌,采用Mastersizer 2000激光粒度测定仪测定样品的粒度。
2 结果与讨论
2.1 预实验-球料比的选择
图1所示为钛铁矿以不同的球料比活化2 h后的SEM像。由图1可知,当球料比为10:1时,钛铁矿的粒度相对较粗,且表面光滑,没有达到很好的球磨效果。球料比为20:1时,钛铁矿的颗粒细小均匀,表面粗糙。而当球料比为30:1及以上时,钛铁矿的颗粒反而变大,活化效果变差,这是由于球料比过高导致物料仅仅是填充在钢球之间的缝隙中,球磨时二者不能充分接触,因此达不到很好的球磨效果。
图2所示为钛铁矿以不同的球料比活化2 h后的粒径分布图。由图2可知,当球料比为20:1时,钛铁矿颗粒在细粒区(0.2~4 μm)的分布最多;而当球料比为30:1和40:1时,钛铁矿颗粒则主要分布在5~100 μm的粗粒区,球磨效果反而较差。因此,机械活化的最佳球料比为20:1左右。下文中机械活化的球料比均为20:1。
2.2 机械活化对钛铁矿结构的影响

图1 钛铁矿以不同的球料比活化2 h后的SEM像
Fig. 1 SEM images of ilmenite activated for 2 h with ball/ilmenite mass ratio of 10:1 (a), 20:1 (b), 30:1 (c) and 40:1 (d)
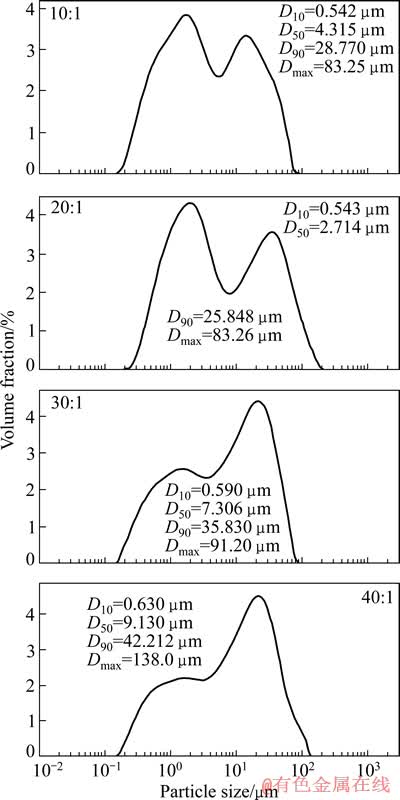
图2 钛铁矿以不同的球料比活化2 h后的粒径分布图
Fig. 2 Particle size distribution of ilmenite activated for 2 h with different ball/ilmenite ratio
图3所示为钛铁矿在活化不同时间后的XRD谱。由图3可知,未活化的钛铁矿衍射峰尖锐,除含有主物相FeTiO3(六方晶系,空间群R-3)外,还含有(Mg, Fe, Al)6(Si, Al)4O10(OH)8相,说明部分的Mg、Al、Si杂质是以晶态形式存在。而在机械活化后,各样品均显示出单一的FeTiO3相,杂相消失。由于Mg、Al、Si等杂质元素在常温下机械活化不可能全部进入FeTiO3的晶格,因此,杂相的消失是由其转变成无定形结构引起的。随着活化时间的延长,钛铁矿的衍射峰逐渐宽化,且峰强逐渐变弱,说明机械活化破坏了晶体的完整性,使得晶粒变细,且逐渐无定形化。
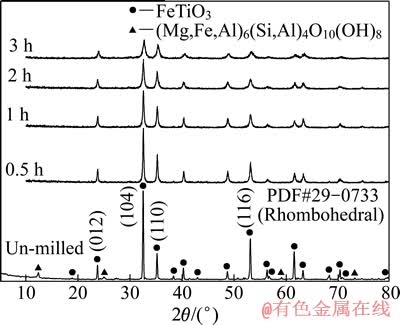
图3 钛铁矿在活化不同时间后的XRD谱
Fig. 3 XRD patterns of ilmenite activated for different times
为了进一步研究机械活化对钛铁矿结构的影响,对样品的晶格常数进行了精修,所得结果见图4。由图4可知,活化时间小于1 h时,机械活化主要造成晶格常数c变大,而a无明显变化(约增大0.0787%);而在2 h以后,晶格常数a和c均变大,且a的变化趋势反过来大于c。说明机械活化首先主要是沿c轴方向进行,继续延长时间则在a轴和c轴同时进行。
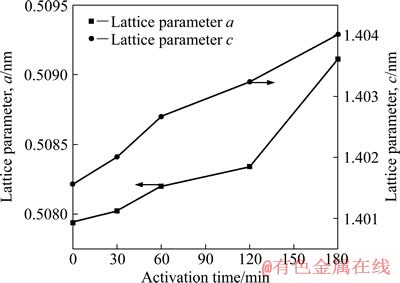
图4 钛铁矿的晶胞常数随活化时间的变化曲线
Fig. 4 Changing curves of lattice parameters of ilmenite with activation time
晶格膨胀可能是由于大量缺陷的产生而引起,另外若有Mg、Al、Mn等原子掺入到FeTiO3晶格中也能造成其晶格膨胀。
DUNCAN等[16]研究表明,未活化的钛铁矿在基面(0001)的浸出速度更快;而LI等[17]则发现经机械活化后的钛铁矿在c轴方向的应变点是浸出反应的表面活性点,强化浸出与钛铁矿在a轴方向的点阵应变关系不大。由此可见,机械活化后钛铁矿沿c轴的微小点阵应变就可能导致(0001)晶面族的浸出速度大大提高。因此,从图4中c轴的变化趋势可以预知,即便机械活化的时间较短也可大大强化钛铁矿的浸出速度。
2.3 机械活化对钛铁矿形貌的影响
图5所示为钛铁矿在活化不同时间后的SEM像。由图5可知,未活化的钛铁矿颗粒粗大(约100 μm)且表面光滑;活化15~30 min后的颗粒虽然变细至几个微米,但表面仍然很光滑;而活化60 min后颗粒的表面则变得粗糙,一直到120 min,钛铁矿的颗粒变得更加细小和粗糙,粗糙的表面有利于颗粒与浸出剂接触,从而强化浸出;但是,继续延长活化时间将导致颗粒团聚,如活化180 min时的钛铁矿就有明显的团聚现象。
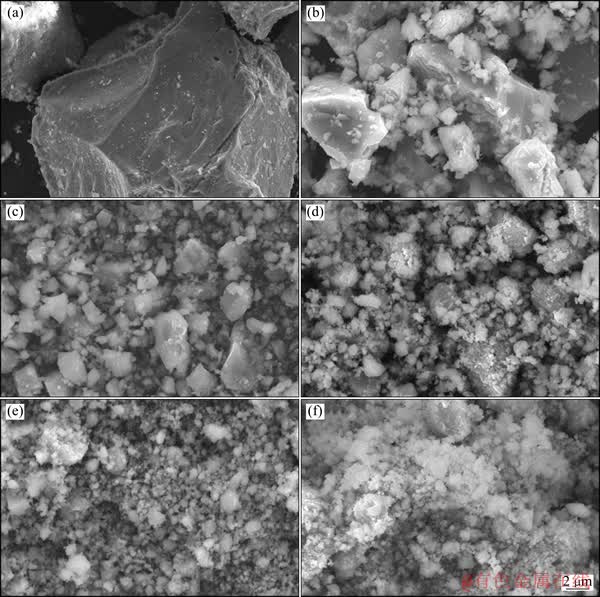
图5 钛铁矿在活化不同时间后的SEM像
Fig. 5 SEM images of ilmenite activated for 0 min (a), 15 min (b), 30 min (c), 60 min (d), 120 min (e) and 180 min (f)
2.4 机械活化对钛铁矿粒度及比表面积的影响
图6所示为钛铁矿在活化不同时间后的粒径分布图。由图6可知,未活化钛铁矿的粒径主要分布在20~180 μm之间,而活化之后钛铁矿的粒径则明显变细。活化30 min以上时,钛铁矿的粒径存在两个主要的分布区域,分别是0.2~4 μm的细粒区和4~80 μm粗粒区。从30~120 min,分布在细粒区的颗粒逐步增多。然而,在180 min时,细颗粒发生团聚,分布在粗粒区的颗粒反而增多,这与SEM的分析结果一致。
图7所示为钛铁矿的中值粒径和比表面积随活化时间的变化曲线。由图7可知,钛铁矿的中值粒径D50在最初30 min内急剧减小,然后随着活化时间的增加而缓慢减小,然而到180 min时又反而增大。另一方面,随着活化时间的延长,钛铁矿的比表面积一直增大,只是增大的趋势越来越平缓。未活化钛铁矿的比表面积仅为0.29 m2/g,活化120 min时急剧增大到8.79 m2/g,而在180 min时为9.72 m2/g。比表面积主要取决于颗粒的形貌和粒度。与活化120 min的钛铁矿相比,虽然活化180 min的钛铁矿具有更大的D50并且还存在明显的团聚,但其比表面积却大于前者,这与样品在超细粒区的颗粒分布有关,如活化120 min钛铁矿的D10=0.543 μm,而活化180分钟钛铁矿的D10=0.428 μm。比表面积的增大使得钛铁矿颗粒与浸出剂有更大的接触面积,从而可以强化浸出速度。
综上所述,从微观来说,机械活化可以细化钛铁矿的晶粒,并产生大量晶格缺陷,使其晶格膨胀;从宏观来说,机械活化可以减小钛铁矿的粒度,并增加颗粒表面的粗糙度,增大其比表面积。机械活化的上述作用均能使钛铁矿的浸出效率大大提高。另外,在最初的30 min内机械活化的效率最高,从形貌和粒度来考虑,最佳活化时间应为2 h左右。
2.5 机械活化对各元素浸出率的影响

图6 钛铁矿在活化不同时间后的粒径分布图
Fig. 6 Particle size distribution of ilmenite activated for different times

图7 钛铁矿的中值粒径(D50)和比表面积随活化时间的变化曲线
Fig. 7 Changing curves of medium diameter (D50) and specific surface area of ilmenite with activation time
研究机械活化对元素分离的影响时,所用球料比为20:1,盐酸的初始质量分数为20%,酸矿比为1.2,反应温度100 ℃,时间2 h。图8所示为活化时间对各元素浸出率的影响。由图8可知,当钛铁矿未经活化时,Fe、Mg、Al、Mn和Ca的浸出率均很低,约15%~20%;而Ti的浸出率则高达12.1%。当活化时间为0.5 h时,Fe、Mg、Al、Mn和Ca的浸出率迅速升高至91.2%、93.8%、92.8%、95.9%和93.3%,Ti的浸出率则迅速下降至2.12%,这是由于活化初期钛铁矿粒度迅速减小,比表面积迅速增大引起的。继续延长球磨时间,各元素的浸出率缓慢增加,如1 h时Fe、Mg、Al、Mn和Ca的浸出率为93.6%、97.2%、95.5%、98.2%和96.3%,Ti的浸出率为1.26%。活化时间从1 h增加到2 h时,仅有Fe的浸出率稍有增大(95.5%),Ti的浸出率稍有降低(1.07%),其它元素的浸出率无明显变化。而从2 h到3 h时,各元素的浸出率均没有明显变化。延长活化时间对元素浸出率的影响变小,这是由于活化后期钛铁矿的粒度和比表面积变化较小引起的。综上所述,将钛铁矿活化1 h即可基本达到元素分离的要求,但是为了获得品位更高的人造金红石,应将Ti和其他元素分离得越彻底越好,因此选择最佳活化时间为2 h左右。
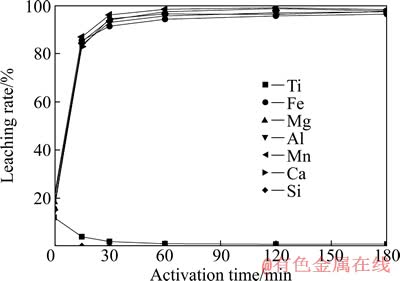
图8 活化时间对各元素浸出率的影响
Fig. 8 Effect of activation time on leaching rate of vatious elements
图9所示为活化不同时间钛铁矿所得浸出渣在800 ℃煅烧4 h后的XRD谱。由图9可知,钛铁矿未经活化时,所得浸出渣在煅烧后的主物相为Fe2TiO5,仅显示出少量金红石TiO2 的峰。然而在球磨0.5 h后,所得浸出渣在煅烧后的主物相变为金红石型TiO2,但仍存在少量Fe2TiO5的峰,说明浸出渣中还含有较多的Fe,这与元素分析的结果一致。当钛铁矿球磨1 h及以上时,所得浸出渣在煅烧后的物相均为单一的金红石型TiO2结构;没有显示出Si和Fe的相关物相,说明它们以无定形态存在或者含量太少导致无法检测出其衍射峰。
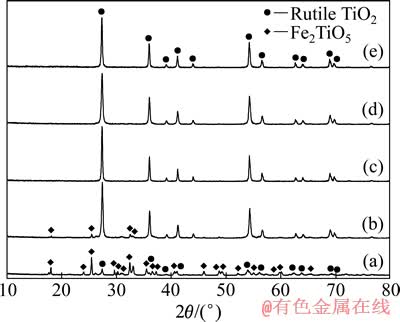
图9 活化不同时间的钛铁矿所得浸出渣在煅烧后的XRD谱
Fig. 9 XRD patterns of calcined slags obtained from ilmenite activated for 0 min (a), 15 min (b), 30 min (c), 60 min (d), 120 min (e) and 180 min (f)
2.6 浸出条件的优化
2.6.1 初始盐酸浓度和浸出时间对浸出的影响
研究初始盐酸浓度对浸出的影响时,以球磨2 h的钛铁矿为原料,浸出温度100 ℃,HCl和钛铁矿的质量比为1.2:1。图10所示为不同盐酸质量分数下Fe和Ti的浸出率随时间的变化图。由图10(a)可知,0~1 h时,各盐酸质量分数下Fe的浸出率均迅速增大,1 h之后,盐酸质量分数为15 %时Fe的浸出率缓慢增加,而盐酸质量分数为20%~30 %时Fe的浸出率增加很少,并在2 h后趋于稳定。由图(b)可知,Ti的浸出率随时间的变化趋势在各盐酸质量分数下相似,即0~1 h时迅速降低,1~2 h时缓慢降低,2 h之后趋于稳定;浸出时间相同时,Ti的浸出率随盐酸质量分数的升高而降低。表2所列为不同盐酸质量分数下浸出2 h所得浸出渣在800 ℃煅烧4 h后所得金红石的主要成分,由表可知,当盐酸质量分数高于20%时,浸出渣煅烧后所得金红石中TiO2的含量仅稍有升高。因此,从钛铁分离效果考虑,最优浸出时间为2 h左右,盐酸质量分数越高越好。但是,盐酸质量分数太高使得HCl易于挥发,会大大增加设备防腐的成本,同时高质量分数盐酸也难以循环利用。因此,在能保证钛铁分离效果的基础上,盐酸质量分数应越低越好。当盐酸质量分数为20%,浸出时间为2 h时,Fe的浸出率达95.5%,而Ti的浸出率仅为1.07%,达到了很好的分离效果,所得金红石中含TiO2 90.8%。因此,最佳的盐酸质量分数应为20%,最优浸出时间为2 h。
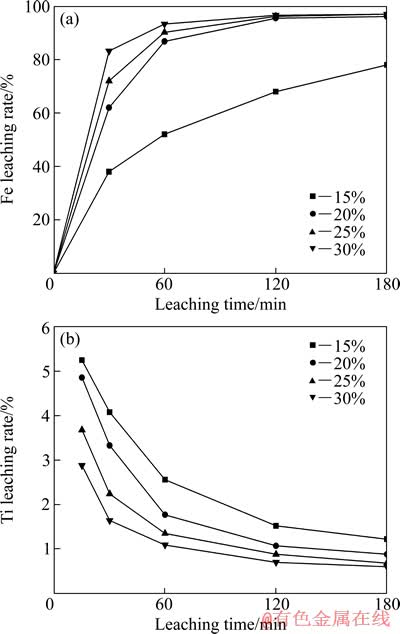
图10 盐酸质量分数和浸出时间对Fe和Ti浸出率的影响
Fig. 10 Effect of hydrochloric acid mass fraction and reaction time on leaching rate of Fe (a) and Ti (b)
表2 盐酸浓度对金红石主要成分的影响
Table 2 Effect of hydrochloric acid concentration on main chemical compositions of rutile

2.6.2 反应温度对浸出的影响
研究反应温度对浸出的影响时,以球磨2 h钛铁矿为原料,初始盐酸质量分数为20%,HCl和钛铁矿的质量比为1.2:1,浸出时间2 h。图11所示为不同反应温度下Fe和Ti的浸出率,相应浸出渣在800 ℃煅烧4 h后所得金红石的主要成分如表3。由图11可知,反应温度由80 ℃升高到100 ℃时,Fe的浸出率由78%迅速升高到95.5%;当继续升高温度到110 ℃时,Fe的浸出率变化较小(97.7%),所得金红石中TiO2的含量仅稍有增加(见表3)。另一方面,Ti在80、90、100和110 ℃时的浸出率分别为4.83%、2.47%、1.07%和0.72%,浸出率随着温度的升高而降低。升高温度有利于浸出反应的进行,因此 Fe的浸出率升高,但温度的升高同时有利于Ti的水解,因此,浸出液中Ti的含量减小。因此,温度越高Ti和Fe的分离效果越好,但考虑到能耗和高温下HCl的挥发,最佳反应温度应在100 ℃左右。
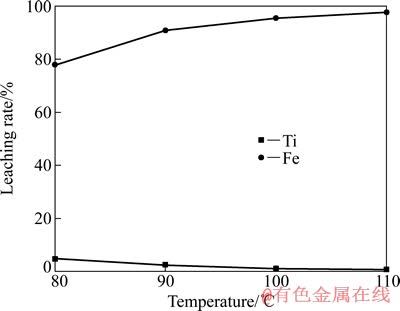
图11 反应温度对Ti和Fe浸出率的影响
Fig. 11 Effect of reaction temperature on leaching rate of Ti and Fe
表3 反应温度对金红石主要成分的影响
Table 3 Effect of reaction temperature on main chemical compositions of rutile
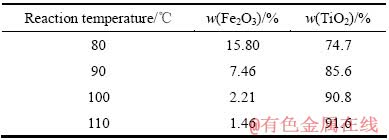
2.6.3 酸矿比对浸出的影响
研究酸矿比(HCl100%与钛铁矿的质量比)对浸出的影响时,以球磨2 h的钛铁矿为原料,初始盐酸质量分数为20%,反应温度100 ℃,时间2 h。图12所示为酸矿比对Ti和Fe浸出率的影响,相应浸出渣在800 ℃煅烧4 h后所得金红石的主要成分见表4。由图12可知,酸矿比为0.9时,Fe的浸出率仅为74.4%,而酸矿比为1.2时,其浸出率迅速升高至95.5%;继续增大酸矿比,Fe的浸出率缓慢增加。另一方面,Ti的浸出率也随着酸矿比的升高而缓慢升高,Ti在酸矿比0.9时的浸出率仅为0.9%,在酸矿比1.8时则增大到 2.32%。由表4可知,当酸矿比大于1.2时,所得金红石中TiO 2的含量仅稍有增加。考虑到Ti和Fe的分离效果、成本及废酸量等问题,最佳酸矿比为1.2左右。

图12 酸矿比对Ti和Fe浸出率的影响
Fig. 12 Effect of mass ratio of hydrochloric acid/ilmenite on leaching rates of Ti and Fe
表4 酸矿比对金红石主要成分的影响
Table 4 Effect of mass ratio of hydrochloric acid/ilmenite on main chemical compositions of rutile
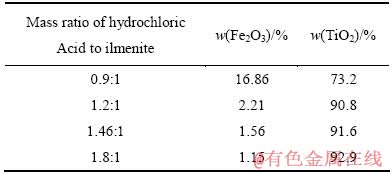
综上,机械活化-盐酸常压浸出钛铁矿的最优条件为:盐酸质量分数20%,反应温度100 ℃,酸矿比1.2,钛铁矿活化时间2 h。在此条件下,主元素Ti(浸出率1.07 %)和Fe(浸出率95.5 %)等元素得到了很好的分离,最终Ti和Si定向富集在渣中,Fe、Mg、Al、Mn和Ca等则定向富集在浸出液中。将该浸出渣在800℃煅烧4 h后得金红石型TiO2,其品位为90.8%,该品位已达到氯化法生产钛白或海绵钛的要求,但是其粒度较细(约1~5 μm),还需造粒(≥100 μm)后才能用于工业生产。
3 结论
1) 从微观来说,机械活化可细化钛铁矿的晶粒,并产生大量晶格缺陷,使其晶格膨胀;从宏观来说,机械活化可以减小钛铁矿的粒度,并增加颗粒表面的粗糙度,增大其比表面积。这些作用均能使钛铁矿的浸出效率大大提高。
2) 机械活化钛铁矿在最初的30 min内效率最高,最佳活化时间为2 h左右。
3) 最优浸出条件为:盐酸质量分数20%,反应温度100 ℃,酸矿比1.2,钛铁矿活化时间2 h。
4) 最终Ti和Si富集在渣中,其他元素进入浸出液。将所得富钛渣煅烧可得到品位高于90%的人造金红石。
REFERENCES
[1] 肖 玮, 鲁雄刚, 邹星礼, 李重河, 丁伟中. 富氢气基还原钛铁矿及其气相组分的耦合作用[J]. 中国有色金属学报, 2013, 23(12): 3423-3429.
XIAO Wei, LU Xiong-gang, ZOU Xin-li, LI Chong-he, DING Wei-zhong. Hydrogen-rich gas reduction of ilmenite and coupling reaction of gaseous compositions[J]. The Chinese Journal of Nonferrous Metals, 2013, 23(12): 3423-3429.
[2] JANSSEN A, PUTNIS A. Processes of oxidation and HCl-leaching of Tellnes ilmenite[J]. Hydrometallurgy, 2011, 109: 194-201.
[3] 危雪梅, 鲁雄刚, 肖 玮. 攀枝花预氧化钛精矿的H2还原行为[J]. 中南大学学报: 自然科学版, 2013, 23(11): 3248-3253.
WEI Xue-mei, LU Xiong-gang, XIAO Wei. Reduction behavior of Panzhihua pre-oxidized ilmenite by hydrogen[J]. Journal of Central South University: Science and Technology, 2013, 23(11): 3248-3253.
[4] BALDERSON G F, MACDONALD C A. Method for the production of synthetic rutile[P]. US Patent, 5885324, 1999.
[5] 郭宇峰, 游 高, 姜 涛, 邱冠周. 攀枝花钛铁矿固态还原行为[J]. 中国有色金属学报, 2010, 41(5): 1639-1644.
GUO Yu-feng, YOU Gao, JIANG Tao, QIU Guan-zhou. Solid-state reduction behavior of Panzhihua ilmenite[J]. The Chinese Journal of Nonferrous Metals, 2010, 41(5): 1639-1644.
[6] 郭宇峰, 刘 霞, 邱冠周, 姜 涛. 还原钛铁矿中金属铁锈蚀反应速率过程的强化[J]. 中南大学学报: 自然科学版, 2012, 43(3): 797-802.
GUO Yu-feng, LIU Xia, QIU Guan-zhou, JIANG Tao. Strengthening of metallic iron rust in reduced ilmenite[J]. Journal of Central South University: Science and Technology, 2012, 43(3): 797-802.
[7] SINHA H N. MURSO process for producing rutile substitute. In: Jaffe R I, Burte H M (Eds.), Titanium Science and Technology[M]. New York-London: Plenum Press, 1973: 233-244.
[8] ZHANG L, HU H, LIAO Z, CHEN Q, TAN J. Hydrochloric acid leaching behavior of different treated Panxi ilmenite concentrations[J]. Hydrometallurgy, 2011, 107: 40-47.
[9] TAN Ping, HU Hui-ping, ZHANG Li. Effects of mechanical activation and oxidation-reduction on hydrochloric acid leaching of Panxi ilmenite concentration[J]. Transactions of Nonferrous Metals Society of China, 2011, 21: 1414-1421.
[10] ZHU Q, ZHANG J, LI H. Influence of phase and microstructure on the rate of hydrochloric acid leaching in pretreated Panzhihua ilmenite[J]. Particulogy, 2014, 14: 83-90.
[11] SASIKUMAR C, RAO D S, SRIKANTH S, RAVIKUMAR B, MUKHOPADHYAY N K, MEHROTRA S P. Effect of mechanical activation on the kinetics of sulfuric acid leaching of beach sand ilmenite from Orissa, India[J]. Hydrometallurgy, 2004, 75: 189-204.
[12] CHEN Y. Low-temperature oxidation of ilmenite (FeTiO3) induced by high energy ball milling at room temperature[J]. J Alloy Compd, 1997, 257: 156-160.
[13] WELHAM N J, LLEWELLYN D J. Mechanical enhancement of the dissolution of ilmenite[J]. Miner Eng, 1998, 11: 827-841.
[14] LI C, LIANG B, GUO L H. Dissolution of mechanically activated Panzhihua ilmenites in dilute solutions of sulphuric acid[J]. Hydrometallurgy, 2007, 89: 1-10.
[15] TAO Tao, CHEN Qi-yuan, HU Hui-ping, YIN Z L, CHENG Ying. TiO2 nanoparticles prepared by hydrochloric acid leaching of mechanically activated and carbothermic reduced ilmenite[J]. Transactions of Nonferrous Metals Society of China, 2012, 22: 1232-1238.
[16] DUNCAN J F, METSON J B. Acid attack on New Zealand ilmenite Ⅰ: The mechanism of dissolution[J]. New Zeal J Sci, 1982, 25: 103-109.
[17] 李 春, 陈胜平, 吴子兵, 郭灵虹, 梁 斌. 机械活化方式对攀枝花钛铁矿浸出强化作用[J]. 化工学报, 2006, 57(4): 832-837.
LI Chun, CHEN Sheng-ping, WU Zi-bing, GUO Ling-hong, LIANG B. Enhancement effects of mechnically milling facilities on dissolution of Panzhihua ilmenite[J]. Journal of Chemical Industry and Engineering, 2006, 57(4): 832-837.
(编辑 何学锋)
基金项目:国家自然科学基金资助项目(51204114);江苏省自然科学基金资助项目(BK2012216);中国博士后科学基金资助项目(2013M540464, 2014T70543)
收稿日期:2014-05-07;修订日期:2014-10-17
通信作者:钟胜奎,教授,博士;电话:0512 67164815;E mail:zsk_suda@163.com