Trans. Nonferrous Met. Soc. China 23(2013) 451-455
Synthesis and characterization of LiFePO4 coating with aluminum doped zinc oxide
Hao TANG1, Long TAN2, Jun XU1
1. Department of Materials Science, Fudan University, Shanghai 200433, China;
2. Felie Li-ion Battery Manufacture Co., Ltd., Wuxi 214028, China
Received 10 September 2012; accepted 18 December 2012
Abstract: Aluminum doped zinc oxide (AZO), as an electrically conductive material, was applied to coating on the surface of olivine-type LiFePO4 synthesized by solid-state method. The charge-discharge test results show that the rate performance and low-temperature performance of LiFePO4 are greatly improved by the surface treatment. Even at 20C rate, the discharge specific capacity of 100.9 mA·h/g was obtained by the AZO-coated LiFePO4 at room temperature. At -20 °C, the discharge specific capacity at 0.2C for un-coated LiFePO4 and the coated one are 50.3 mA·h/g and 119.4 mA·h/g, respectively. It should be attributed to the electrically conductive AZO-coating which increases the electronic conductivity of LiFePO4. Furthermore, the surface-coating increases the tap-density of LiFePO4. The results indicate that the AZO-coated LiFePO4 is a good candidate of cathode material for applying in lithium power batteries.
Key words: lithium ion battery; LiFePO4; coating; cathode material; aluminum doped zinc oxide
1 Introduction
Olivine-type LiFePO4, as a replacement of LiCoO2, has attracted attention since the significant report in 1997 by good enough [1] in which it was proposed to be used as cathode material for lithium ion batteries. It has the advantages of environment benign, inexpensive, thermal stable and good cycling stability [2-4]. However, its immanent disadvantages of low electronic conductivity and low diffusion rate of lithium ion during the charge-discharge process destroy the rate performance [5-7], and the capacity decreases rapidly even at moderate current density.
Many reports have discovered that the electrical performance of LiFePO4 can be improved by ion doping [8], carbon coating [9,10] and metal oxide coating [11-13]. Especially, coating carbon which is an electrically conductive material has been wildly applied in industry with advantages of facie, inexpensive and good effect to control the particle size of LiFePO4. However, the electrically conductive carbon reduces the tap-density of LiFePO4, which is being harmful to the energy density of the lithium ion battery [14]. Further- more, the low-temperature performance of carbon-coated LiFePO4 is also needed to be improved [11].
In this work, the electrically conductive material of aluminum doped zinc oxide(AZO) is firstly applied to coating on the surface of LiFePO4. It is reported that the insulated pure zinc oxide can be changed to be electrically conductive with doping appropriate metals such as indium, gallium and aluminum [15,16]. And the resistivity of the AZO film even can be decreased to 10-4 Ω·cm [16]. Besides, the solid density of zinc oxide (5.7 g/cm3) is even higher than that of the LiFePO4 (3.6 g/cm3). Therefore, both the electrochemical properties and tap density of LiFePO4 would be greatly improved by coating with the electrically conductive AZO. The low-temperature performance of the AZO- coated LiFePO4 powders is also investigated.
2 Experimental
LiFePO4 was synthesized by solid-state method using FeC2O4·2H2O, NH4H2PO4 and Li2CO3 as the raw materials. Stoichiometric FeC2O4·2H2O, NH4H2PO4 and Li2CO3 were full-mixed in isopropanol by ball milling for 2 h. Then the obtained slurry was dried at 80 °C. The resulted powders were calcined at 700 °C for 8 h in a purified N2 flow and the uncoated LiFePO4 was obtained, which is signed as Un-LFP.
C4H6ZnO4·2H2O and C8H12Al2O9·4H2O in the molar ratio of 43.7:1 were initially dissolved in distilled water. The Un-LFP was then added and the mixtures were stirred for 1 h in order to make the Un-LFP disperse homogeneously in the solution. The resultant solution was then dried at 120 °C to get the powder precursor. The powder precursor was calcined at 500 °C for 1 h in a purified N2 flow and the LiFePO4 coating with AZO was finally obtained (m(AZO):[m(LiFePO4)+ m(AZO)]=2%), signed as AZO-LFP.
All the reagents used in the experiment were of analytical purity and were used without further purification. Powder X-ray diffraction (XRD) analysis using Cu Kα radiation was employed to identify the crystalline phase of the prepared powder with a Bruker D8-advance (German) at room temperature in the range of 10°≤2θ≤70°. The morphology was investigated with a field emission scan electron microscope (SEM, S-4800, Japan). The tap-density meter (BT-300, Dandong Bettersize Instruments Ltd., China) was applied to measuring the tap-density of the prepared powder. The coin cells were assembled by using lithium foil as anode in an argon-filled glove box, the as-prepared powders mixed with 12% acetylene black and 8% PVDF as the cathode and 1 mol/L LiPF6 in a 1:1(V/V) mixture of ethylene carbonate (EC) and dimethylcarbonate(DMC) as the electrolyte, Celgard 2300 membrane as the cell separator. The charge-discharge cycle was performed in a voltage range of 2.0-3.8 V using the coin cells. All the electrical measurements were carried out by a battery testing system (Landet-5 V/10 mA, Landet Electronic Corporation, China) at room temperature.
3 Results and discussion
Figure 1 shows the XRD patterns of the Un-LFP and AZO-LFP powders. All diffraction lines can be index for the orthorhombic olive structure with pmnb space group (JCPDS card No. 40—1499) [11]. No peaks corresponding to AZO were observed, indicating that the low content of AZO compound cannot be detected by XRD. The lattice constants of the Un-LFP and AZO-LFP powders have been refined and tabulated in Table 1. It is consistent with that of the standard LiFePO4 and the results obtained in other reports [11,13]. The result also confirms that the surface modification with AZO did not cause the change in lattice constants. This indicates that the Al3+ and Zn2+ ions are adhere on the surface of the LiFePO4 powders as AZO coating rather than diffuse into LiFePO4 lattice. And more, the tap-densities of the Un-LFP and AZO-LFP powders were also measured and tabulated in Table 1. It is obvious that the tap density of LiFePO4 is improved by the AZO coating. The result is different from that of the carbon coating and is significant for applying in lithium power batteries.
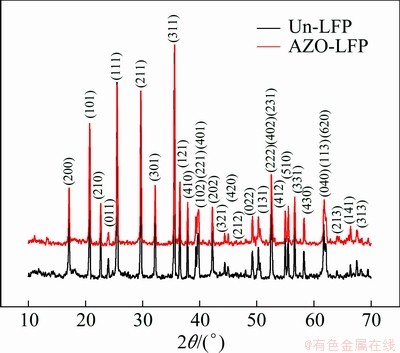
Fig. 1 XRD patterns of Un-LFP and AZO-LFP powders collected by steps of 0.02° in 10°≤2θ≤70°
Table 1 Calculated structure parameters and tap-densities of Un-LFP and AZO-LFP powders
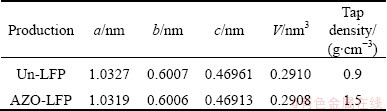
The SEM images of the Un-LFP and AZO-LFP powders are shown in Fig. 2. It can be clearly seen in Fig. 2(a) that the surface of Un-LFP powder is smooth with little sponge-like material coating on and between the particles. It can be attributed to the decomposition of
in FeC2O4·2H2O in purified N2 flow, which causes little carbon remain. As seen in Fig. 2(b), the surfaces of LiFePO4 particles are covered by some well-distributed nano-particles, which should be the AZO material. It proves that the AZO material has been successfully coated on the surface of LiFePO4, which is consistent with the XRD result mentioned above.
The initial charge-discharge curves of the Un-LFP and AZO-LFP powders tested at different current densities are shown in Fig. 3(a). The cells were firstly charged to 3.8 V at the constant current density, then charged until the charge current density decreased to 0.05C, and finally discharged to 2.0 V at the constant current density. All these curves have the smooth plateaus, indicating the well-crystallized structure of the both samples. The initial charge-discharge specific capacities of the Un-LFP powders at 0.1C and 1C are 156.3/150.3 mA·h/g and 145.5/130.9 mA·h/g, respectively. For the AZO-LFP powders, 165.8/160.1 mA·h/g and 158.1/148.0 mA·h/g were obtained at 0.1C
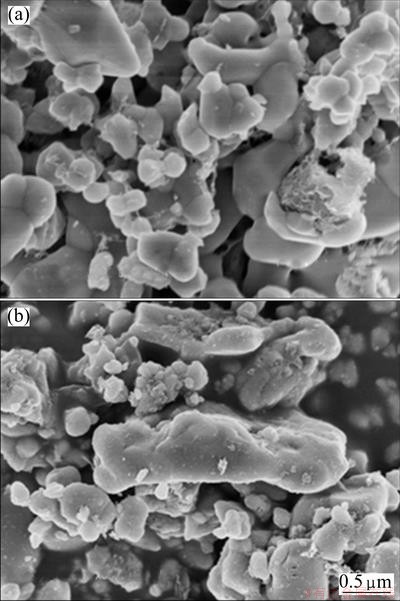
Fig. 2 SEM images of Un-LFP (a) and AZO-LFP powders (b)
and 1C, respectively. Furthermore, it is obvious that lower discharge plateau is obtained for the curves of the Un-LFP powders, which attributes to the more sever polarization caused by the poor electronic conductivity of LiFePO4 particles. The results well prove that the electrically conductive AZO coating increases the electronic conductivity of LiFePO4, and then improves the specific capacities especially at a high rate.
Figure 3(b) shows the cycle performance of the Un-LFP and AZO-LFP powders. Good results at 0.1C are obtained for the both samples. About 99.5% and 97.4% of the initial capacities are retained for the AZO-LFP and Un-LFP powders. When the current density is increased to 1C, 96.5% of the initial specific capacity is retained for the AZO-LFP powders, but only 91.3% for the Un-LFP powders. This result demonstrates that the AZO coating can improve the cycling stability of LiFePO4. This improvement is largely due to the presence of AZO which could impede the reaction between the cathode particles and electrolyte [10].
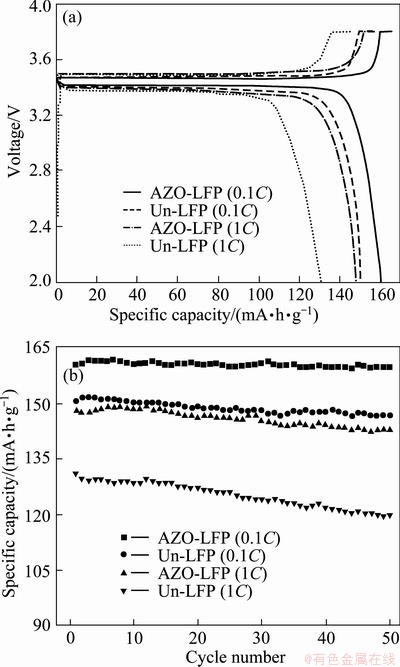
Fig. 3 Initial charge-discharge curves (a) and cycling properties (b) of Un-LFP and AZO-LFP powders tested at room temperature
To evaluate the rate capability of the Un-LFP and AZO-LFP, the discharge curves tested at different rates are shown in Fig. 4. For the Un-LFP (Fig. 4(a)), the discharged specific capacity decreases dramatically with increasing the discharge rate. When the rate increases to 5C, only 72.0 mA·h/g of the specific capacity is retained for the Un-LFP. However, good rate performance is obtained for AZO-LFP, as shown in Fig. 4(b). The discharge specific capacity can reach 100.9 mA·h/g even at 20C rate, indicating that the AZO-LFP is a good candidate of cathode material for lithium power batteries.
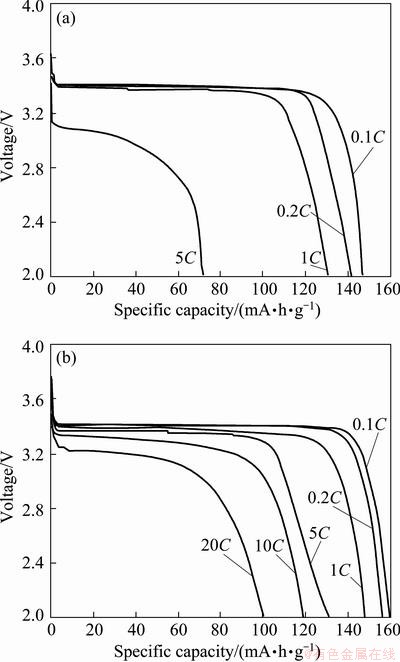
Fig. 4 Rate performance of Un-LFP (a) and AZO-LFP (b) powders at room temperature
Figure 5 displays the initial discharge curves of the Un-LFP and AZO-LFP (0.2C) tested at -20 °C. Apparently, the Un-LFP has a bad low-temperature performance shown in Fig. 5. After coating the AZO material, a smooth plateau appears in the discharged process and the specific capacity increases to 119.4 mA·h/g, which indicates that the reaction of Li ions extration/insertion and electron transfer can well proceed at -20 °C. It was reported that the surface reaction kinetics is slowed down with the drop of operation temperature [11]. The obtained results of AZO-LFP should be attributed to the surface treatment which increases the electrode kinetics at -20 °C. Moreover, the improved electrode kinetics can also be beneficial to the rate performance of LiFePO4, which is consistent with the result in Fig. 4.
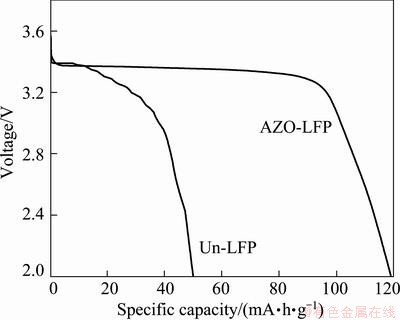
Fig. 5 Initial discharge curves of Un-LFP and AZO-LFP powders tested at -20°C
4 Conclusions
AZO was successfully coated on the surface of LiFePO4 synthesized by solid-state method. Discharge specific capacity of 100.9 mA·h/g can be retained by AZO-coated LiFePO4 testing in the current density of 20C at room temperature, whereas the un-coated LiFePO4 can only reach 72.0 mA·h/g even at 5C rate. At -20 °C, the discharge specific capacities at 0.2C for un-coated LiFePO4 and the coated one are 50.3 mA·h/g and 119.4 mA·h/g, respectively. The surface treatment of AZO-coating greatly improves the rate performance and low-temperature performance of LiFePO4, which indicates that the AZO-LFP is a good candidate of cathode material for lithium power batteries.
References
[1] PADHI A K, NANJUNDASWAMY K S, GOODENOUGH J B. Phospho-olivines as positive electrode materials for rechargeable lithium batteries [J]. J Electrochemical Society, 1997, 144(4): 1188-1194.
[2] YAMADA A, CHUNG S C, HINOKUMA K, YAMADA A, CHUNG S C, HINOKUMA K. Optimized LiFePO4 for lithium battery cathodes [J] . J Electrochem Soc A, 2001, 148(3): 224-229.
[3] PROSINI P P, PASQUALL M. Improved electrochemical performance of a LiFePO4 based composite cathode [J]. Electrochimica Acta, 2001, 46: 3517-3523.
[4] THACKERAY M. An unexpected conductor [J]. Nat Mater, 2002, 1: 81-82.
[5] ZHOU X, WANG F, ZHU Y, LIU Z. Graphene modified LiFePO4 cathode materials for high power lithium ion batteries [J]. J Mater Chem, 2011, 21(10): 3353-3358.
[6] CHEN Zhao-yong, ZHU Wei, ZHU Hua-li, ZHANG Jian-li, LI Qi-feng. Electrochemical performances of LiFePO4/C composites prepared by molten salt method [J]. Transactions of Nonferrous Metals Society of China, 2010, 20(5): 809-813.
[7] WU Ling, WANG Zhi-xing, LI Xin-hai, LI Ling-jun, GUO Hua-jun, ZHENG Jun-chao, WANG Xiao-juan. Electrochemical performance of Ti4+-doped LiFePO4 synthesized by co-precipitation and post-sintering method [J]. Transactions of Nonferrous Metals Society of China, 2010, 20(5): 814-818.
[8] LU Jun-biao, TANG Zi-long, ZHANG Zhong-tai, JIN Yong-zhu. Influence of Mg ion doping on the battery properties of LiFePO4/C [J]. Acta Physico-Chimica Sinica, 2005, 21(3): 319-323.
[9] FISHER C A J, ISLAM M S. Surface structures and crystal morphologies of LiFePO4: Relevance to electrochemical behaviour [J]. J Mater Chem, 2008, 18(11): 1209-1215.
[10] LI Y D, ZHAO S X, NAN C W, LI B H. Electrochemical performance of SiO2-coated LiFePO4 cathode materials for lithium ion battery [J]. J Alloys and Compounds, 2011, 509(3): 957-960.
[11] YAO J, WU F, QIU X, LI N, SU Y. Effect of CeO2-coating on the electrochemical performances of LiFePO4/C cathode material [J]. Electrochimica Acta, 2011, 56(16): 5587-5592.
[12] CUI Y, ZHAO X. Enhanced electrochemical properties of LiFePO4 cathode material by CuO and carbon co-coating [J]. J Alloys and Compounds, 2010, 490(1-2): 236-240.
[13] CUI Y, ZHAO X, GUO R. High rate electrochemical performances of nanosized ZnO and carbon co-coated LiFePO4 cathode [J]. Materials Research Bulletin, 2010, 45(7): 844-849.
[14] WANG M, YANG Y, ZHANG Y. Synthesis of micro-nano hierarchical structured LiFePO4/C composite with both superior high-rate performance and high tap density [J]. Nanoscale, 2011, 3(10): 4434-4439.
[15] VERMA A, KHAN F, KUMAR D, KAR M, CHAKRAVARTY B C, SINGH S N, HUSAIN M. Sol–gel derived aluminum doped zinc oxide for application as anti-reflection coating in terrestrial silicon solar cells [J]. Thin Solid Films, 2010, 518(10): 2649-2653.
[16] XU Z Q, DENG H, LI Y, HUANG C. Al-doping effects on structure, electrical and optical properties of c-axis-orientated ZnO:Al thin films [J]. J Materials Science in Semiconductor Processing, 2006, 9(1-3): 132-135.
掺铝氧化锌包覆LiFePO4的合成与性能
汤 昊1,谭 龙2,许 军1
1. 复旦大学 材料系,上海 200433;
2. 江苏恒益锂电池制造有限公司,无锡 214028
摘 要:以简单的固相法合成了橄榄石结构LiFePO4,并以导电掺铝氧化锌材料(AZO)对其表面进行包覆。充放电结果显示,表面包覆大幅度改善了LiFePO4材料的倍率和低温性能。在20C高倍率条件下,AZO包覆LiFePO4的放电比容量可达100.9 mA·h/g;在低温-20 °C时进行0.2C充放电,未包覆LiFePO4和AZO包覆LiFePO4的放电比容量分别为50.3 mA·h/g和119.4 mA·h/g。经分析,这可能是由于采用导电AZO包覆措施而增加了LiFePO4材料的电导率,从而极大地提高了其比容量。另外,导电AZO包覆措施还增加了LiFePO4材料的振实密度。这些结果表明AZO包覆LiFePO4材料是一种很好的适用于锂离子动力电池的正极材料。
关键词:锂离子电池;LiFePO4;包覆;正极材料;掺铝氧化锌
(Edited by Hua YANG)
Corresponding author: Jun XU; Tel/Fax: +86-21-55664563; E-mail: junxu@fudan.edu.cn
DOI: 10.1016/S1003-6326(13)62484-X