Trans. Nonferrous Met. Soc. China 24(2014) 2408-2413
Effect of electromagnetic field on microstructure and macrosegregation of flat ingot of 2524 aluminium alloy
Yu-bo ZUO, Jian-zhong CUI, Dan MOU, Qing-feng ZHU, Xiang-jie WANG, Lei LI
Key Laboratory of Electromagnetic Processing of Materials, Ministry of Education, Northeastern University, Shenyang 110819, China
Received 17 October 2013; accepted 30 April 2014
Abstract: Low frequency electromagnetic casting (LFEC) process with the application of an induction coil outside the conventional direct chill (DC) casting mould was used to prepare the flat ingot of 2524 alloy and the effect of electromagnetic field on the microstructure and macrosegregation of this alloy was systematically studied. The results show that the flat ingot prepared by the LFEC process has a finer and more uniform as-cast microstructure and the grain morphology is transformed from dendrite and rosette-like to equiaxed structure. The LFEC process also shows a significant effect on macrosegregation, and with the application of electromagnetic field during casting process, the segregation in the centre of the ingot is obviously reduced. The mechanism of these effects was also discussed.
Key words: 2524 aluminium alloy; grain refinement; solidification; microstructure; macrosegregation; low-frequency electromagnetic casting
1 Introduction
2524 aluminum alloy as a newly developed 2xxx series Al-Cu alloys has been widely used as aerospace materials. So far, 2524 aluminum alloy could be one of the best materials for the fuselage skin. The use of 2524-T3 aluminum has become widespread because it has the same strength properties as 2024-T3, but higher fracture toughness and better damage tolerance and creep resistance [1,2]. 2524 aluminum alloy is heat treatable and responds to precipitation hardening with GPB zones and S phase as the strengthening precipitates [3]. The commercial 2524 alloy is normally solution heat treated, quenched and then artificially aged. The study on the heat treatment of this alloy has been well carried out. It is well known that the as-cast microstructure has a significant effect on the microstructure and properties of semi finished and final finished products. It is therefore very important to get a uniform and fine as-cast microstructure. However, the information on the control of as-cast microstructure of 2524 alloy is still limited.
Based on the electromagnetic casting process (EMC) [4] and CREM [5,6], a low frequency electromagnetic casting (LFEC) process has been developed [7-9], in which the low frequency electromagnetic field was used to control the fluid flow and temperature field. The LFEC process shows a significant advantage of elimination or reduction of hot tearing [9] which is a key problem for the direct chill (DC) casting process [10-12] especially when casting large sized ingot of high strength alloys. It has been also demonstrated by both experimental work and simulation work that the LFEC process can make the temperature field in the sump very uniform and significantly refine microstructure of Al-Zn-Mg-Cu alloys [13,14]. The mechanism of the grain refinement by the LFEC process was also studied [15]. The application of LFEC process could be an effective method to modify the as-cast microstructure of 2524 aluminium alloy.
The aim of this work is to prepare flat ingot of 2524 aluminium alloy by the LFEC process and present its effect on the microstructure and composition distribution.
2 Experimental
The chemical composition of 2524 aluminium alloy used in the present work is shown in Table 1. The high- pure aluminum was melted in a 45 kW resistance furnace. Pure Cu, Mg and addition agent of Mn were added to the melted aluminum at 750 °C. The melt was degassed by C2Cl6, and then was poured into a DC casting mould through a filter tank and a launder. A 90-turn induction coil was arranged outside the mould and a graphite ring was set in the mould. Flat ingots with the cross section of 350 mm×160 mm were then cast by the conventional DC casting and the LFEC process, respectively, under the following conditions: casting temperature (melt temperature in the furnace), 710-720 °C; casting speed, 75 mm/min; temperature of cooling water, 17 °C; cooling water flow rate, 110 L/min. During LFEC process the frequency was kept at 25 Hz and the current was set as 0, 20, 40, 50, 60, 80 and 100 A, respectively.
Table 1 Chemical composition of 2524 aluminium alloy (mass fraction, %)

The sampling positions are shown in Fig. 1. Samples for metallographic examinations were ground, polished and then etched. Samples for microstructure examination were etched with Keller’s reagent (2 mL HF, 3 mL HCl, 5 mL HNO3 and 190 mL H2O). Microstructures of these samples were observed under optical microscope(Leica DMR). The grain size analyses were carried out by software SISCIA S8.0. The chemical composition was measured by a direct-reading spectrometer.
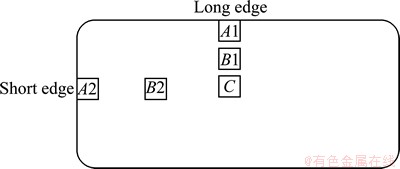
Fig. 1 Cross section of flat ingot and schematic of sampling positions
3 Results and discussion
3.1 Microstructure of 2524 alloy prepared by DC and LFEC process
Figure 2 shows the microstructure of the ingots prepared by the conventional DC and LFEC (25 Hz, 50 A) process. In general, the microstructure of the DC cast ingot shows a non-uniform microstructure with grain size increasing from the edge to the centre of the ingot; with the application of the LFEC process the microstructure becomes much finer and more uniform. Under the influence of the LFEC process the grain morphology is transformed from dendrite and rosette-like to equiaxed structure, especially in the centre of the ingot.
In order to clearly understand the uniformity of the grain structure, the average grain size was quantified. Figure 3 shows the grain size distribution from the long edge to the centre of the ingot (from A1 to C as shown in Fig. 1). It can be seen that the grain size of LFEC cast ingot is smaller than that of the DC cast ingot and also the difference of the grain size between the edge and the centre of the LFEC ingot is also smaller. For the conventional DC cast ingot, in the edge the grain size is around 100 μm and in the centre it is about 190 μm. While, for the LFEC cast ingot, in the edge the grain size is around 70 μm and in the centre it is about 90 μm. Figure 4 shows the grain size distribution from the short edge to the centre of the ingot (from A2 to C as shown in Fig. 1). The variation of the grain size from the edge to the centre shows the same trend as Fig. 3.
In the LFEC process the alternative current generates a time varying magnetic field in the melt, which, in turn, gives rise to an induced current in the melt and ingot. Therefore, the melt is subjected to electromagnetic body forces caused by the interaction of the induced current and the magnetic filed. The Lorentz force (F) can be expressed as [5,6]
(1)
where B and J are the magnetic induction intensity and current density generated in the melt, μ is the permeability of the melt. The first term on the right hand of Eq. (1) is a rotational component which results in a forced convection in the melt.
The forced convection could directly increase the fragmentation and make important contribution to the final structure [16]. The modification of temperature field in the melt induced by the LFEC process could play more important roles in the grain refinement. It has been confirmed that during LFEC casting a Al-Zn-Mg-Cu alloy [15], there is a forced convection and the temperature in the entire melt is quite uniform and 3-6 °C below liquidus. Once the new melt from the launder enters the sump, it is fast cooled down directly to the semi-solid state with a very high cooling rate, resulting in a large undercooling and a significant increase of nucleation rate. The nucleation happens throughout the entire melt. The lower temperature in the melt remarkably reduces the remelting of nuclei and most nuclei can survive and make contributions to the refinement of final microstructure. The nuclei are well dispersed and distributed uniformly in the entire melt by the forced convection and the nuclei grow spherically in a uniform and isotropic condition in the entire melt.
Therefore, with the application of the low-frequency electromagnetic field the microstructure of 2524 alloy flat ingot is finer and more uniform than that of conventional DC cast ingot and the grain morphology is also transformed from dendrite and rosette-like to equiaxed structure.
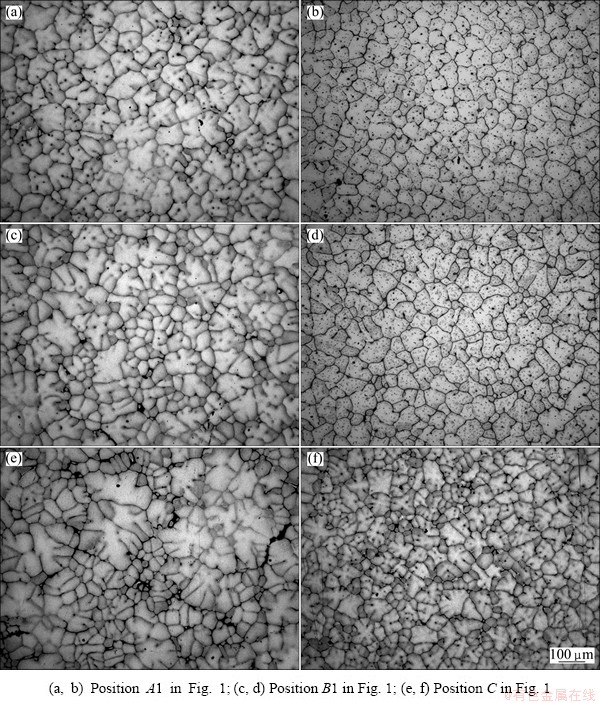
Fig. 2 Comparison of microstructure between ingots made by DC (a, c, e) and LFEC (b, d, f)
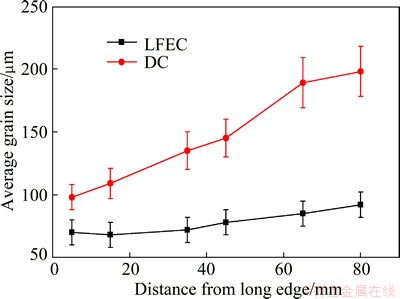
Fig. 3 Average grain size distribution from long edge to centre of DC and LFEC cast ingots
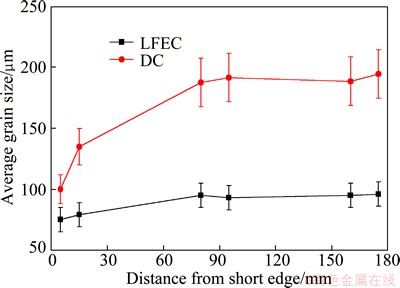
Fig. 4 Average grain size distribution from short edge to centre of DC and LFEC cast ingots
3.2 Variation of microstructure as function of current intensity
The microstructure of the centre of the flat ingots prepared with different current intensities is shown in Fig. 5 and the variation of average grain size as a function of current intensity is plotted in Fig. 6.
Based on Figs. 2(e,f) and Fig. 5, it is clear with increasing the current from 0 to 20 A, the grains change from coarse equiaxed and dendritic grains to finer and more uniform equiaxed grains. When increasing the current from 20 to 40 and then to 50 A, the grains become further fine and more uniform. While, with increasing current from 50 to 100 A, the grain size decreases very slowly. The proper current range for LFEC casting 2524 alloy flat ingot is 50-100 A.
With the increase of current intensity, the electromagnetic field intensity in the melt becomes stronger and consequently the forced convection becomes stronger, which results in more uniform temperature field and the formation of more fragmentation by nucleation on the mould, the liquid surface, remelting of the root of dendrite arms. Therefore, with the increase of current intensity the microstructures become finer and more uniform, as shown in Figs. 5 and 6. Under electromagnetic fields, both the temperature fields and solute fields become uniform and the constitutional supercooling near the liquid-solid interface is decreased, so the grains grow in a uniform and isotropic condition. If there is a little fluctuation at the interface it will disappear when it encounters superheat melt. Under low frequency electromagnetic fields the grains grow spherically, so the grains of LFEC treated ingot are equiaxed or nearly equiaxed.
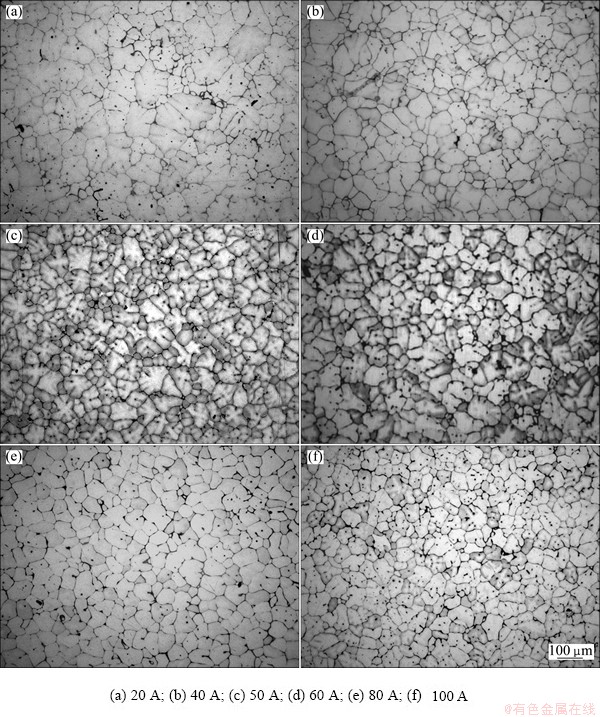
Fig. 5 Effect of current intensity on microstructure in centre of 2524 alloy ingot
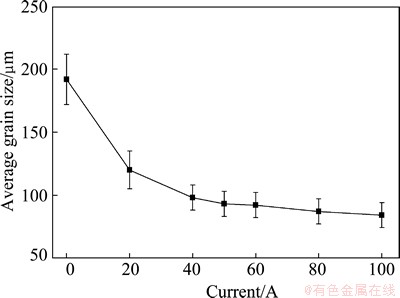
Fig. 6 Variation of average grain size as function of current intensity
3.3 Distribution of chemical composition of 2524 alloy prepared by DC and LFEC process
The chemical composition was measured by a direct-reading spectrometer. Figure 7 shows a preliminary result of the distribution of Cu from the long edge to the centre of the ingot. As shown in Fig. 7, both the ingots prepared with DC and LFEC process have an obvious segregation near to the surface and the LFEC process does not show significant effects on it. However, in the centre of the ingots, the segregation is evidently reduced by the LFEC process. The surface segregation is not crucial for the 2524 alloy ingot because the surface layer will be scalped before hot rolling. Therefore, the reduction of the centre segregation by the LFEC process is very significant for the 2524 alloy. The mechanism of the reduction of macrosegregation by the LFEC process is not completely understood yet. It is believed to be related to the forced convection. Further work about this will be carried out later on.
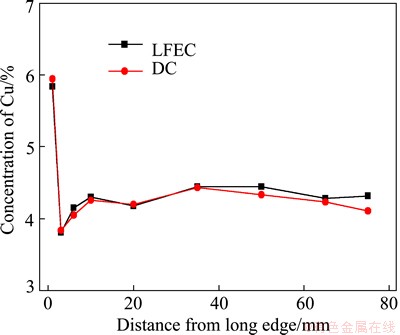
Fig. 7 Distribution of Cu from long edge to centre of ingot
4 Conclusions
1) The LFEC process has a significant grain refining effect on flat ingots of 2524 aluminium alloy. It can reduce the grain size from 190 to 90 μm in the centre of the ingot. The ingot prepared by the LFEC process shows a fine and uniform as-cast equiaxed structure.
2) Current intensity plays a very important role in the grain refining. With increasing the current intensity, the grain size becomes smaller. The proper current range for LFEC casting 2524 alloy flat ingot is 50-100 A.
3) The LFEC process has a significant effect on the chemical composition distribution. It can reduce the centre macrosegregation of the 2524 alloy flat ingot.
References
[1] SMITH BERT L, FLORES TANYA L Z, HIJAZI ALA L. Link-up strength of 2524-T3 and 2024-T3 aluminum panels with multiple site damage [J]. Journal of Aircraft, 2005, 42(2): 535-541.
[2] ZHENG Z Q, CAI B, ZHAI T, LI S C. The behavior of fatigue crack initiation and propagation in AA2524-T34 alloy [J]. Materials Science and Engineering A, 2011, 528(4-5): 2017-2022.
[3] QUAN Li-wei, ZHAO Gang, GAO Sam, MUDDLE BARRY C. Effect of pre-stretching on microstructure of aged 2524 aluminium alloy [J]. Transactions of Nonferrous Metals Society of China, 2011, 21(9): 1957-1962.
[4] GETSELEV Z N. Casting in an electromagnetic mold [J]. J Met, 1971, 10: 38-43.
[5] VIVES C. Electromagnetic refining of aluminum alloys by the CREM process: Part I. Working principle and metallurgical results [J]. Metallurgical and Materials Transactions B, 1989, 20(5): 623-629.
[6] VIVES C. Electromagnetic refining of aluminum alloys by the CREM process: Part II. Specific practical problems and their solutions [J]. Metallurgical and Materials Transactions B, 1989, 20(5): 631-643.
[7] ZHANG Bei-jiang, CUI Jian-zhong, LU Gui-min. Effect of low-frequency magnetic field on macrosegregation of continuous casting aluminum alloys [J]. Materials Letters, 2003, 57(11): 1707-1711.
[8] DONG Jie, ZHAO Zhi-hao, CUI Jian-zhong, YU Fu-xiao, BAN Chun-yan. Effect of low-frequency electromagnetic casting on the castability, microstructure, and tensile properties of direct-chill cast Al-Zn-Mg-Cu alloy [J]. Metallurgical and Materials Transactions A, 2004, 35(8): 2487-2494.
[9] ZUO Yu-bo, CUI Jian-zhong, ZHAO Zhi-hao, ZHANG Hai-tao, QIN Ke. Effect of low frequency electromagnetic field on casting crack during DC casting superhigh strength aluminum alloy ingots [J]. Materials Science and Engineering A, 2005, 406(1-2): 286-292.
[10] ESKIN D G. Physical metallurgy of direct chill casting of aluminum alloys [M]. Boca Raton: CRC Press, 2008.
[11] RAPPAZ M, DREZET J, GREMAUD M. A new hot-tearing criterion [J]. Metallurgical and Materials Transactions A, 1999, 30(2): 449-455.
[12] NAGAUMI H, UMEDA T. Prediction of internal cracking in a direct-chill cast, high strength Al-Mg-Si alloy [J]. Journal of Light Metals, 2002, 2: 161-167.
[13] ZHANG Hai-tao, NAGAUMI H, CUI Jian-zhong. Coupled modeling of electromagnetic field, fluid flow, heat transfer and solidification during low frequency electromagnetic casting of 7xxx aluminum alloys: Part II: The effects of electromagnetic parameters on casting processes [J]. Materials Science and Engineering A, 2007, 448(1-2): 177-188.
[14] ZUO Yu-bo, NAGAUMI H, CUI Jian-zhong. Study on the sump and temperature field during low frequency electromagnetic casting a superhigh strength Al-Zn-Mg-Cu alloy [J]. Journal of Materials Processing Technology, 2008, 197(1-3): 109-115.
[15] ZUO Yu-bo, CUI Jian-zhong, ZHAO Zhi-hao, ZHANG Hai-tao, LI Lei, ZHU Qing-feng. Mechanism of grain refinement of an Al-Zn-Mg-Cu alloy prepared by low-frequency electromagnetic casting [J]. Journal of Materials Science, 2012, 47(14): 5501-5508.
[16] ZUO Yu-bo, CUI Jian-zhong, DONG Jie, YU Fu-xiao. Effects of low frequency electromagnetic field on the as-cast microstructures and mechanical properties of superhigh strength aluminum alloy [J]. Materials Science and Engineering A, 2005, 408: 176-181.
电磁场对2524铝合金扁铸锭微观组织和宏观偏析的影响
左玉波,崔建忠,牟 丹,朱庆丰,王向杰,李 磊
东北大学 材料电磁过程研究教育部重点实验室,沈阳 110819
摘 要:采用在常规结晶器上布置线圈而开发的低频电磁半连续铸造技术(LFEC)制备2524铝合金扁铸锭并系统研究其对微观组织和宏观偏析的影响。结果表明,采用低频电磁半连续铸造技术制备的扁铸锭具有更加细小、均匀的铸态组织,而且组织由枝晶和蔷薇型转变为等轴晶组织。低频电磁半连续铸造技术对铸锭宏观偏析具有重要的影响,施加磁场后铸锭中心部分的反偏析明显减弱了。同时,对这些作用的机理进行了探讨。
关键词:2524铝合金;晶粒细化;凝固;微观组织;宏观偏析;低频电磁铸造
(Edited by Xiang-qun LI)
Foundation item: Projects (51104043, 51374067) supported by the National Natural Science Foundation of China; Project (2012CB619506) supported by the National Basic Research Program of China; Project (N120409002) supported by the Fundamental Research Funds for the Central Universities, China
Corresponding author: Jian-zhong CUI; Tel: +86-24-83681738; E-mail: zuoyubo@126.com
DOI: 10.1016/S1003-6326(14)63364-1