Trans. Nonferrous Met. Soc. China 22(2012) s645-s649
Effect of bonding interface on delamination behavior of drawn Cu/Al bar clad material
Sangmok LEE1, Min-Geun LEE2, Sang-Pill LEE3, Geun-Ahn LEE1, Yong-Bae KIM1, Jong-Sup LEE1, Dong-Su BAE2
1. Advanced Forming Technology Center, Korea Institute of Industrial Technology, Incheon 406-840, Korea;
2. Department of Advanced Materials Engineering, Dong-Eui University, Busan 614-714, Korea;
3. Department of Mechanical Engineering, Dong-Eui University, Busan 614-714, Korea
Received 21 May 2012; accepted 27 September 2012
Abstract: Cu/Al bar clad material was fabricated by a drawing process and a subsequent heat treatment. During these processes, intermetallic compounds have been formed at the interface of Cu/Al and have affected its bonding property. Microstructures of Cu/Al interfaces were observed by OM, SEM and EDX Analyser in order to investigate the bonding properties of the material. According to the microstructure a series of diffusion layers were observed at the interface and the thicknesses of diffusion layers have increased with aging time as a result of the diffusion bonding. The interfaces were composed of 3-ply diffusion layers and their compositions were changed with aging time at 400 °C. These compositional compounds were revealed to be η2, (θ+η2), (α+θ) intermetallic phases. It is evident from V-notch impact tests that the growth of the brittle diffusion layers with the increasing aging time directly influenced delamination distance between the Cu sleeve and the Al core. It is suggested that the proper holding time at 400 °C for aging as post heat treatment of a drawn Cu/Al bar clad material would be within 1 h.
Key words: drawn Cu/Al bar clad material; aging; bonding interface; intermetallic compound; diffusion layer; delamination
1 Introduction
Needs for clad materials classified as metallic composite materials are continuously increasing in various industries since products or parts made by single metal is not easy to possess combination of required characteristics such as, for instance, high mechanical strength with high corrosion resistance for chemical applications, high mechanical strength with low density for structural applications or high electrical conductivity with low density for electrical applications etc. Several processes including rolling [1-6], extrusion [7], overlay welding [8], high magnetic field [9] and explosive welding [10,11] are utilized for production of the clad materials.
One of the representative applications in clad materials is electric wires. Replacement of pure Cu with the combination of Al core (inner material) with Cu sleeve (outer material) makes it possible for the wires to be much lighter due to the lower effective density with the electrical conductivity still maintained. In this regards a drawn Cu/Al bar clad materials for electric wire have received much attention compared to Cu wire materials [3,7,8].
However, it is difficult to fabricate the Cu/Al bar clad materials because brittle intermetallic compounds are inevitably formed at the interface and brittle copper oxides are easily produced at the Cu surface during drawing and post heat treatment. The brittleness of newly formed phases cause the weakening of the bonding strength at the interface when the thickness of the layers reaches beyond a certain critical thickness [3,5]. It is crucial to improve the bonding strength of Cu/Al bar clad material by controlling the interface properties with post heat treatment.
The aim of this work is to investigate the effect of diffusion layers on delamination properties in deriving optimum cladding conditions of a drawn Cu/Al bar clad materials in terms of post aging time to have a proper bonding strength.
2 Experimental
Bar type of Cu/Al clad material was fabricated using copper (Oxygen Free Copper) and Al1050 by a drawing and subsequent heat treatment processes. Additional aging treatments were carried out at 400 °C for 1, 5 and 10 h in a heating furnace.
Microstructures of the aging treated specimens were observed using an optical microscope (OM), a scanning electron microscope (SEM, Quanta 200 FEG) and point analyses were conducted across the interfaces of the specimens by an energy dispersed X-ray analyzer (EDX, Genesis XM2) in order to examine the bonding interface properties of Cu/Al bar clad materials. Image analyses were employed to measure the thickness of the diffusion layer.
V-notched impact tests were performed at room temperature to observe the delamination behavior of Cu/Al interface and then delaminated distances of Cu/Al interfaces were measured by image analysis.
3 Results and discussion
3.1 Thickness of diffusion layer in bonding interface
Figures 1(a)-(d) show the optical microscopic images showing the change of diffusion layer thickness of a drawn Cu/Al bar clad material aged at 400 °C for 0, 1, 5 and 10 h, respectively. The thicknesses of the layers were plotted in terms of aging time as shown in Fig. 1(e).
The thicknesses of the layers were plotted in terms of aging time as shown in Fig. 1(e). The thickness of the diffusion layer increased rapidly up to 1 h and showed almost linear relationship with aging time up to 10 h. The thickness of diffusion layer was 2.0 μm without the additional aging and 18.2 μm for 10 h at 400 °C. The thickness of the diffusion layer increased about 900% for 10 h on aging.
3.2 Intermediate phase and diffusion bonding in Cu/Al interfaces
Figure 2 shows the results of the EDX analyses for bonding layer formed at the interface of a drawn Cu/Al bar clad material aged at 400 °C for 0 and 10 h. A series of diffusion layers were observed at the interface of Cu/Al.
It is evident in the micrographs that bonding interfaces were formed as 3-ply diffusion layers. Points marked as C, D, E in Fig. 2(a) were identified as (α+θ) phase. And those marked as D, E, F in Fig. 2(b) were turned out to be η2, (θ+η2), (α+θ) phases which can be confirmed from the Al-Cu binary phase diagram [12]. The thicknesses of diffusion layers formed at bonding interface increased and the intermetallic phases in diffusion layers were changed from (α+θ) phase to η2, (θ+η2), (α+θ) phases with aging time.

Fig. 1 Thickness of diffusion layer of drawn Cu/Al bar clad material aged at 400 °C for 0 h (a), 1 h (b), 5 h (c), 10 h (d) and thickness changes of diffusion layer with aging time (e)
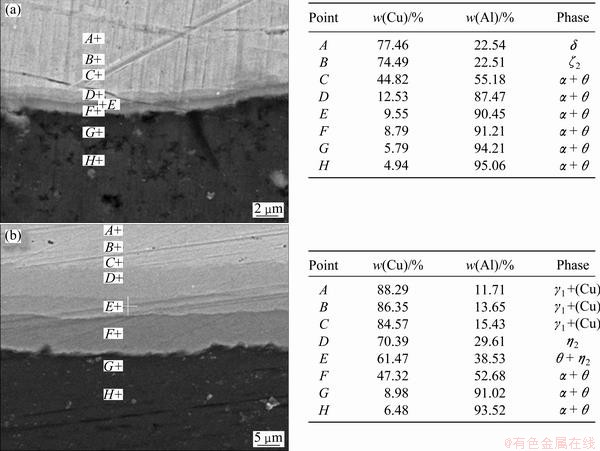
Fig. 2 Point and intermediate phase analysis results of drawn Cu/Al bar clad material aged at 400 °C for 0 h (a) and 10 h (b)
It is noted in Fig. 2 that the shapes of bonding interfaces were smooth along the interface. This type of bonding interface is a little different in shapes of bonding interface with serrated or rough type in roll cladding interface [5,6] or waved type in explosive bonding interface [10,11]. The manufacturing process and mechanical properties of cladding and base materials would affect the shapes of bonding interfaces.
Figure 3 shows the distribution of Cu and Al compositions near Cu/Al interface aged at 400 °C for 0, 1, 5 and 10 h. The Cu composition near Cu/Al interface decreased rapidly to Al side for non-aged condition, as shown in Fig. 3(a). However, the Cu composition near Cu/Al interface decreased gradually to Al side for 1 h aged condition, as shown in Fig. 3(b).
The Cu composition near Cu/Al interface decreased gradually and smoothly to Al side and also Al composition showed the same tendency to Cu side in a 10 h aged specimen, as shown in Fig. 3(d), as a result of interdiffusion from Al to Cu and vice versa [2,5,11].
It is also noted that distances from the interface to 80%Cu-20%Al (mass fraction) composition point were continuously increased from less than 10 μm without aging, to more than 10 μm for 1 h, to about 15 μm for 5 h and finally reached about 22 μm for 10 h, respectively. This was anticipated because exposure of the sample for longer time in heating environment provides the atomic species to have more possibility to jumping events to enhance diffusion activity.
3.3 Delamination behavior in bonding interface
Figures 4(a)-(d) show fractured interfaces of a drawn Cu/Al bar clad material aged at 400 °C for 0, 1, 5 and 10 h, respectively, from V-notched impact tests to observe the delamination behavior in bonding interface [1,4,5] of a drawn Cu/Al bar clad material.
Figure 4(e) shows the changes of delaminated distances between inner surface of Cu and outer surface of Al with the thickness of diffusion layer formed at Cu/Al bonding interface.
Delamination was not observed at bonding interface of a drawn Cu/Al bar clad material with aged at 400 °C for 0 h and 1 h holding time. Large delamination, however, was inspected at bonding interface of a drawn Cu/Al bar clad material with aged at 400 °C for 5 h and 10 h holding time, as shown in Figs. 4(a)-(d). It is recognized that delaminated distance at the bonding interface of a drawn Cu/Al bar clad material was affected directly by the increased thickness of diffusion layer with aging time, as shown in Fig. 4(e). It is speculated that although certain amount of diffusion layer is required for good bondability, largely grown diffusion layers at the interface act as easily breakable bands due to their brittle characteristics.

Fig. 3 EDX analysis results of drawn Cu/Al bar clad material aged at 400 °C for 0 h (a), 1 h (b), 5 h (c) and 10 h (d)

Fig. 4 Fracture surface of drawn Cu/Al bar clad material aged at 400 °C for 0 h (a), 1 h (b), 5 h (c), 10 h (d) and changes of delaminated distances with thickness of diffusion layer (e)
From the above results, it is recommended that the proper holding time for additional aging treatment at 400 °C for the drawn Cu/Al bar clad material would be within 1 h taking into account the delamination behavior at the bonding interface in the aspect of good bondability.
4 Conclusions
1) Diffusion bonding was observed at the interface of Cu/Al and bonding interfaces were formed as 3-ply diffusion layers.
2) The thicknesses of diffusion layers formed at bonding interface increased and the intermetallic phases in diffusion layers were changed from (α+θ) phase to η2, (θ+η2), (α+θ) phases with aging time.
3) Increased thickness of diffusion layer with aging time led directly to the increase of delaminated distance at the bonding interface of a drawn Cu/Al bar clad material.
4) The proper holding time for additional aging at 400 °C for the drawn Cu/Al bar clad material is recommended to be within 1 h taking into account the delamination characteristics.
References
[1] BAE D H, CHOI Y J, CHUNG W S, BAE D S, CHO Y R. Effect of tension-test temperature on fracture behavior and mechanical properties in STS/Al/Cu clad materials [J]. J Kor Ins Met Mater, 2009, 47: 811-818.
[2] LI X, ZU G, DING M, MU Y, WANG P. Interfacial microstructure and mechanical properties of Cu/Al clad sheet fabricated by asymmetrical roll bonding and annealing [J]. Mater Sci Eng A, 2011, 529: 485-491.
[3] ABBASI M, TAHERI A K, SALEHI M T. Growth rate of intermetallic compounds in Al/Cu bimetal produced by cold roll welding process [J]. J Alloys Compounds, 2001, 319: 233-241.
[4] SUN X J, TAO J, GUO X Z. Bonding properties of interface in Fe/Al clad tube prepared by explosive welding [J]. Transactions of Nonferrous Metals Society of China, 2011, 21: 2175-2180.
[5] LI D G, WANG Q, LIU T, LI G J, HE J C. Growth of diffusion layers at liquid Al-solid Cu interface under uniform and gradient high magnetic field conditions [J]. Mater Chem Phys, 2009, 117: 504-510.
[6] RAGHUKANDAN K. Analysis of the explosive cladding of Cu-low carbon steel plates [J]. J Mater Proc Tech, 2003, 139: 573-577.
[7] BAE D S, KIN S K, LEE S P, SHIBAYAMA T, BAE D H. Interface properties of copper/aluminum/stainless steel clad materials [J]. Key Eng Mater, 2007, 345-346: 1497-1500.
[8] MANESH A D, TAHERI A K. Bond strength and formability of an aluminum-clad steel sheet [J]. J Alloys Compounds, 2003, 361: 138-143.
[9] RHEE K Y, HAN W Y, PARK H J, KIM S S. Fabrication of aluminum/copper clad composite using hot hydrostatic extrusion process and its material characteristics [J]. Mater Sci Eng A, 2004, 384: 70-76.
[10] BAE D H, JUNG S J, CHO Y R, JUNG W S, JUNG H S, KANG C Y, BAE D S. Effect of pre-heat treatment on bonding properties in Ti/Al/STS clad materials [J]. J Kor Ins Met Mater, 2009, 47: 573-579.
[11] LEE S, KIM S M, WE S N, BAE D H, LEE G A, LEE J S, KIM Y B, BAE D S. Effect of post heat treatment temperature on interface diffusion layer and bonding force in roll cladded Ti/Mild steel/Ti material [J]. J Kor Ins Met Mater, 2012, 50: 316-323.
[12] OKAMOTO H. Phase diagrams for binary alloys [M]. Ohio, USA: ASM International, 2000: 29.
(Edited by YANG You-ping)
Foundation item: Project supported by the Fundamental Materials Development funded by the Korean Ministry of Knowledge Economy
Corresponding author: Dong-Su BAE; Tel/Fax: +82-51-8902288; E-mail: dsbae@deu.ac.kr
DOI: 10.1016/S1003-6326(12)61779-8