
Diffusion bonding of g-TiAl alloy to Ti-6Al-4V alloy under hot pressure
WANG Xiu-feng(王秀锋)1, MA Mo(马 蓦)1, LIU Xue-bin(刘学斌)1, WU Xue-qing(吴学庆)1, TAN Chao-gui(檀朝桂)1, SHI Rong-kai(石荣凯)1, LIN Jiang-guo(林建国)1,2
1. Faculty of Material & Photoelectronic Physics, Xiangtan University, Xiangtan 411105, China;
2. Key Laboratory of Low Dimensional Materials and Application Technology of Ministry of Education,
Xiangtan University, Xiangtan 411105, China
Received 8 December 2005; accepted 20 April 2006
Abstract: The diffusion bonding of g-TiAl alloy to Ti-6Al-4V alloy at different temperatures ranging from 1 073 to 1 173 K under an applied stress of 100 MPa for 2 h was studied. The observation of the microstructure reveals that sound joints between the g-TiAl alloy and the Ti-alloy without any pores or cracks can be achieved through diffusion bonding at temperatures over 1 073 K under the applied stress of 100 MPa for 2 h. The bond is composed of two zones, and its width increases with the increase of bonding temperature. The EDS chemical composition profiles indicate that there is a diffusion flux of Al atoms from g-TiAl alloy towards the Ti alloy and of Ti atoms in the opposite direction. The three point-bending of the joints bonded under different conditions was tested and the fracture mode was analyzed by SEM observation.
Key words: g-TiAl alloys; Ti-6Al-4V alloys; diffusion bonding; microstructure
1 Introduction
Alloys based on the g-TiAl intermetallic compounds have been of much interest in recent years as light-mass structural materials for elevated temperature aerospace applications[1-5]. Successful joining and cost effective fabrication methods for these materials will increase their utility in engineering applications. Encouraging results have been obtained in a few studies by using fusion welding techniques, including gas tungsten arc welding [6], laser welding[7] and electron beam welding[8]. However, the largest challenge for fusion welding is the high residual stress and rapid cooling rate. In comparison with fusion welding processes, diffusion bonding(DB) has the advantage that no melting of the base material occurs, which produces a drastic local change of the microstructure and related mechanical properties. In comparison with fusion welding processes, diffusion bonding(DB) has the advantage that no melting of the base material occurs, and couldn’t produce a drastic local change of the microstructure and related mechanical properties. Furthermore, it can avoid some typical fusion welding defects, such as hot cracking and stress cracking susceptibility. Thus, DB is a good approach for the bonding of g-TiAl alloys. To date, a number of literatures have demonstrated the possibility to join both g-TiAl alloys and Ti-alloys either to themselves or to other special materials by diffusion bonding[9-17].
In the present study, the diffusion bonding of a g-TiAl alloy to a Ti-6Al-4V alloy at different tempera- tures, ranging from 1 073 to 1 173 K, under an applied stress of 100 MPa for 2 h is presented and the relations between bonding parameters and microstructural features are demonstrated. Furthermore, the three point-bending of the BD joints is tested and the fracture mode is analyzed by SEM observation.
2 Experimental
A Ti-6Al-4V rolled bar in the annealed condition, and an as cast titanium aluminide alloy with the nominal composition Ti-46.5Al-2.5V-2Cr-1.5Nb (mole fraction, %) were selected as experimental materials. The TiAl alloy was hot-isostatic-pressed(HIP) under the conditions of 1 523 K, 172 MPa, 4 h. Specimens with the size of 8 mm×6 mm×4 mm were cut for DB experiments. Prior to joining, the g-TiAl samples were heat-treated at 1 353 K for 16 h, and then cooled in the furnace.
DB was conducted with a Gleeble thermal-imitation
machine, and the working chamber was evacuated to 1.33×10-2 Pa at room temperature. The mating surfaces of the specimens were ground with SiC-paper down to grit 1200 and finally cleaned in a reagent consisting of 1%HF, 6%HNO3 and 93%H2O (volume fraction) for 10 s. The mating specimens were put inside a stainless steel rectangle tube with an inner dimension of 6 mm×4 mm and a wall thickness of 3 mm, as schematically illustrat- ed in Fig.1. DB was carried out at 1 073, 1 153 and 1 173 K with an applied stress of 100 MPa for 2 h.
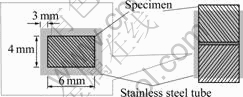
Fig.1 Schematic diagram of g-TiAl/Ti-6Al-4V alloy diffusion bonding mode
To determine the bonding quality, the three-point bending strength of the joints was tested in comparison with that of the base g-TiAl alloy.
The microstructures of the base alloys and the interfaces resulting from joining were characterized by optical microscopy(OM) and scanning electron microscopy(SEM). The chemical composition of the diffusion bond was determined quantitatively by energy dispersive spectrometry(EDS). The fracture morphology after three-point bending testing was analyzed by SEM observation.
3 Results and discussion
Fig.2 illustrates the microstructures of the base materials. It can be seen that the microstructure of Ti-6Al-4V alloy in the annealed condition consists of two phases: the equiaxed primary α phase, with a size of 20-30 μm, and the intergranular regions of transformed β(Fig.2(a)). The g-TiAl alloy after HIP and heat treatment at 1 353 K for 16 h exhibits a near γ micro- structure, with some α2 particles or lamellar colonies at grain boundaries. The size of the equiaxed grains is in the range of 30-50 μm (Fig.2(b)).
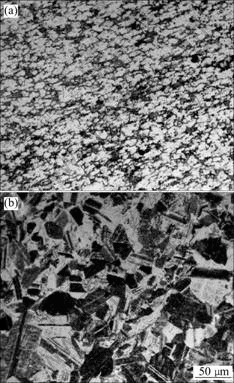
Fig.2 Microstructures of two base materials in annealed condition: (a) Ti-6Al-4V; (b) g-TiAl alloys
The development of the interfacial microstructure during diffusion bonding under the different processing conditions used in this investigation is illustrated in Fig.3. Many micro-voids can be observed at the interface after DB at 1 073 K for 0.5 h. However, these micro-voids are eliminated by increasing the dwelling stage to 2 h, as it can be observed in Figs.3(b)-(d). Therefore, sound bonds between g-TiAl and Ti alloys can be achieved when joining is carried out at temperatures of 1 073 K and over, under an applied stress of 100 MPa for 2 h. The bond width increases with the increase of bonding tem- perature, and it is measured to be 5.5, 11 and 15 μm for the samples bonded at 1 073, 1 153 and 1 173 K, respectively. Furthermore, it is clearly visible that the joining temperature induces microstructural alterations in both g-TiAl and Ti-6Al-4V base alloys, i.e. the grains of these base alloys grow up when the bonding temperature is elevated.

Fig.3 SEM microstructures of bond interfaces of g-TiAl alloy/Ti-6Al-4V alloy bonded under applied stress of 100 MPa: (a) 1 073 K for 0.5 h; (b) 1 073 K for 2 h; (c) 1 153 K for 2 h; (d) 1 173 K for 2 h
Fig.4 shows a back-scattered electron(BSE) image of the bond produced under the conditions of 1 173 K, 100 MPa, 2 h. It is clearly seen that the interface can be divided into two zones. Zone 1, which is located close to the g-TiAl alloy, is generally wider than Zone 2, which is near the Ti alloy. No evident boundary can be detected between the two zones, but the transition from the g-TiAl parent alloy to Zone 1 seems to be more distinct than that between Zone 2 and the Ti parent alloy. The concentration profiles across the interfaces resulting from joining at the different temperatures are shown in Fig.5. The concentration profiles indicate that there is a diffusion flux of Al atoms from g-TiAl alloys towards Ti alloy and of Ti atoms in the opposite direction. The diffusion causes enrichment in Ti and depletion in Al in Zone 1, leading to some increase in the amount of the α2 phase. In contrast to Zone 1, the net diffusion fluxes of Al and Ti atoms in Zone 2 cause both its enrichment in Al and depletion in Ti, leading to the nucleation of the α2 phase in the original α-Ti grain structure. These are similar to the results reported by HOLMQUIST et al[16, 17], in which Zone 1 is composed of large g+α2 grains, while Zone 2 is composed of smaller α+α2 grains.
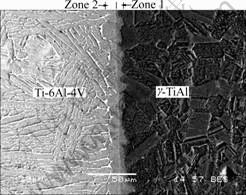
Fig.4 Back-scattered electron(BSE) image of bond interface of g-TiAl alloy/Ti-6Al-4V alloy bonded under applied stress of 100 MPa at 1 173 K for 2 h
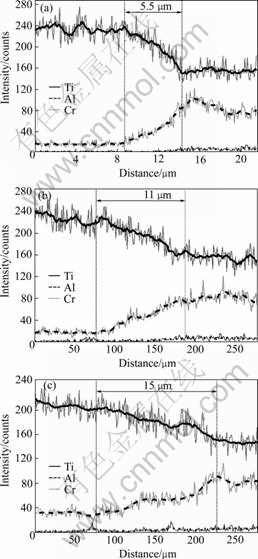
Fig.5 EDS line scanning of Ti, Al and Cr in bond interface of g-TiAl alloy/Ti-6Al-4V alloy bonded under applied stress of 100 MPa: (a) 1 073 K for 2 h; (b) 1 153 K for 2 h; (c) 1 173 K for 2 h
The Vickers microhardness across the interface resulting from joining at the conditions of 1 173 K, 100 MPa, 2 h was measured. The test results are shown in Fig.6. It can be seen that the microhardness of the diffusion bond is in the range of HV310 to HV450, and increases monotonously from the g-TiAl alloy towards the Ti alloy. The variation of the microhardness across the interface can be an explanation of the formation of fine a2 phase in the bond.
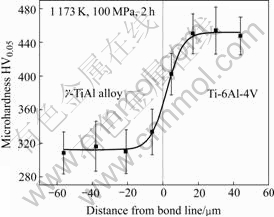
Fig.6 Variation of microhardness HV0.05 as function of distance from bond line
To determine the bonding quality, the three-point bending strength of the joints was tested in comparison with that of the base g-TiAl alloy. The results of the ratio of bending strength of the joints to that of base g-TiAl alloy (BSR) are summarized in Table 1. The fracture of joints bonded under an applied stress of 100 MPa at 1 073 K for 0.5 h occurs at the interface of the g-TiAl and Ti-6Al-4V, as shown in Fig.7(a). And some voids can be found on the fracture surface. The flat fracture morphology indicates that the joint is in mechanical joining fracture mode. While, the joint bonded under the conditions of 1 00 MPa at 1 073 K for 2 h exhibits two fracture modes, as seen in Fig.7(b), one is the cleavage fracture, which occurs in g-TiAl alloy side, the other is the mechanical joining fracture, which occurs at the bonding interface. To the joint bonded at 1 153 K for 2 h, the fracture occurs in g-TiAl alloy in typical clearage mode, which implies that sound metallurgy joining has been achieved, resulting in high fracture strength, as seen in Fig.7(c).
Table 1 Results of three-point bending strength of joint
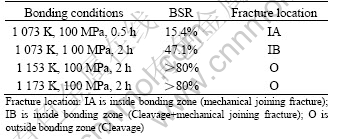
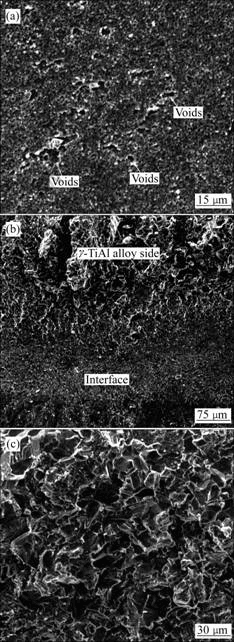
Fig.7 SEM fractographs of typical fracture modes observed in three-point bending of g-TiAl bonds: (a) Mechanical joining fracture; (b) Cleavage+mechanical joining fracture; (c) Clea- vage joining fracture
4 Conclusions
1) Joints between g-TiAl alloy and Ti alloy without any pores or cracks are achieved through diffusion bonding performed in the temperature range of 1 073 to 1 173 K under the applied stress of 100 MPa for 2 h.
2) The interface is composed of two zones, and its width increases with the increase of the bonding temperature. The EDS chemical composition profiles show a diffusion flux of Al atoms from the g-TiAl alloy towards the Ti alloy and of Ti atoms in the opposite direction.
3) In the bonding process, the diffusion of Ti atoms in interface is mainly controlled by grain boundary diffusion.
4) When the joint is bonded at 1 153 K for 2 h, a sound metallurgy joining with high fracture strength is achieved. Its fracture is in cleavage mode.
References
[1] KIM Y W. Intermetallic alloys based on gamma titanium aluminide [J]. JOM, 1989, 41(7): 24-30.
[2] KIM Y W, DIMIDUK D M. Progress in the understanding of gamma titanium aluminides[J]. JOM, 1991, 43 (8): 40-47.
[3] YAMAGUCHI M, UMAKOSHI Y. The deformation behaviour of intermetallic superlattice compounds [J]. Prog Mater Sci, 1990, 34(1): 1-148.
[4] HE Yue-hui, HUANG Bai-yun, ZHOU Ke-cao, OU Wei-pei, CHENG Xiao-qun. Influence of microstructure of TiAl based alloy on the mechanical properties at elevated temperature [J]. The Chinese Journal of Nonferrous Metals, 1997, 7(1): 75-79. (in Chinese)
[5] LIN Jian-guo, ZHANG Yong-gang, CHEN Chang-qi. Effects of lamellar boundaries on creep behavior of pst crystals of TiAl alloys [J]. Trans Nonferrous Met Soc China, 1998, 8(4): 562-566.
[6] ACOFF V L, WILKERSON S, ARENAS M. The effect of rolling direction on the weld structure and hardness of gamma-TiAl sheet material [J]. Mater Sci Eng A, 2002, 329/331: 763-767.
[7] UENISHIA K, KOBAYASHIA K F. Processing of intermetallic compounds for structural applications at high temperature [J]. Intermetallics, 1996, 4(Suppl.1): 95-101.
[8] CHATURVEDI M C, RICHARDS N L, XU Q. Electron beam welding of a Ti-45AI-2Nb-2Mn+0.8vol.% TiB2 XD alloy [J]. Mater Sci Eng A, 1997, 239/240: 605-612.
[9] LIN J G, YU G S, HUANG Z, WU G Q. A novel approach to the solid bonding of a TiAl alloy [J]. J Mater Sci Lett, 2001, 20(18): 1671-1673.
[10] CAM G, KOCAK M. Diffusion bonding of investment cast g-TiAl [J]. J Mater Sci, 1999, 34(14): 3345-3354.
[11] GLATZ W, CLEMENS H. Diffusion bonding of intermetallic Ti-47Al-2Cr-002Si sheet material and mechanical properties of joints at room temperature and elevated temperatures [J]. Intermetallics, 1997, 5(6): 415-423.
[12] HE Peng, FENG Ji-cai, QIAN Yi-yu, ZHANG Bing-gang. Microstructure and strength of TiAi/40Cr joint diffusion bonded the vanadium-copper filler metal [J]. Trans Nonferrous Met Soc China, 2002, 12(5): 811-813.
[13] HE Peng, FENG Ji-cai, ZHANG Bing-gang, QIAN Yi-yu. Interface microstructure and formation mechanism of diffusion-bonded joints of TiAl to steel 40Cr [J]. Trans Nonferrous Met Soc China, 2002, 12(6): 1069-1071.
[14] WANG X F, LUO Z C, YU G S, LIN J G. Application of a diffusion bonding model to superplastic g-TiAl alloys [J]. Mater Sci Technol, 2006, 22(2): 186-192.
[15] WU G Q, HUANG Z, CHEN C Q, RUAN Z J, ZHANG Y. Superplastic diffusion bonding of g-TiAl-based alloy [J]. Mater Sci Eng A, 2004, 380(1-2): 402-407.
[16] HOLMQUIST M, RECINA V, OCKBORN J, PETTERSSON B, ZUMALDE E. Hot isostatic pressing diffusion bonding of titanium alloy Ti-6A1-4V to Gamma titanium aluminide IHI alloy OIA [J]. Scripta Mater, 1998, 39(8): 1101-1106.
[17] HOLMQUIST M, RECINA V, PETTERSSON B. Tensile and creep properties of diffusion bonded titanium alloy IMI 834 to gamma titanium aluminide IHI alloy 01A [J]. Acta Mater, 1999, 47(6): 1791-1799.
Foundation item: Project(50371072) supported by the National Natural Science Foundation of China
Corresponding author: LIN Jian-guo; Tel: +86-732-8292195; Fax: +86-732-8292468; E-mail: lin_j_g@xtu.edu.cn
(Edited by YUAN Sai-qian)