网络首发时间: 2017-03-02 14:21
稀有金属 2018,42(04),421-428 DOI:10.13373/j.cnki.cjrm.XY16100008
含钛高炉碳化渣中TiC的超重力富集与分离的研究
高启瑞 宋波 郭占成 杨玉厚 宋高阳 蔡泽云
北京科技大学冶金与生态工程学院钢铁冶金新技术国家重点实验室
摘 要:
攀钢含钛高炉渣高温下经碳还原后得到有价组元碳化钛, 碳化钛晶粒细小且均匀分布在碳化渣中, 利用常规的选矿方法很难将其富集来提高品位。本文将超重力技术引入到攀钢含钛高炉碳化渣中, 探讨碳化钛在超重力场下的富集与分离规律。研究结果表明:经过超重力富集后试样出现了明显的分层, 碳化钛全部富集在试样的下部, 而在试样的上部几乎找不到碳化钛相, 并且在富集的试样中碳化钛的面积分数沿着超重力方向逐渐增加。重力系数越大, 富集时间越长, 碳化钛的富集效果越好。预处理渣在重力系数G=300于1320℃等温富集20 min后, 下部富集渣中碳化钛的含量由常重力下的11.6%提高到了18.8%。另外, 经超重力场过滤分离后, 碳化钛全部被截留在碳毡上部的精矿中, 脉石相则被分离到下部坩埚中。预处理渣在重力系数G=300于1320℃等温分离20 min后, 上部精矿中碳化钛的含量提高到了23.8%, 而脉石中则找不到任何碳化钛。
关键词:
超重力;富集;分离;碳化渣;碳化钛;
中图分类号: TQ134.11;X757
作者简介:高启瑞 (1988-) , 男, 山西忻州人, 硕士研究生, 研究方向:有价资源的综合利用;E-mail:gaoqirui9011@126.com;;宋波, 教授;电话:010-62332208;E-mail:songbo@metall.ustb.edu.cn;
收稿日期:2016-10-10
基金:国家自然科学基金项目 (51234001) 资助;
Enrichment and Separation of Ti C Phase from Carbonized Titanium-Bearing Blast Furnace Slag by Super Gravity
Gao Qirui Song Bo Guo Zhancheng Yang Yuhou Song Gaoyang Cai Zeyun
State Key Laboratory of Advanced Metallurgy, School of Metallurgical and Ecological Engineering, University of Science and Technology Beijing
Abstract:
The valued phase TiC was obtained from titanium-bearing blast furnace slag of PZH steel after carbonized at high temperature.However, the mass fraction of TiC could hardly be increased by traditional separating technique because of the fine size and dispersed distribution in carbonized slag.In this study, super gravity technology was introduced to investigate the enriching and separating behaviors of TiC in carbonized titanium-bearing blast furnace slag.The results showed that the obvious layered samples were obtained and all the TiC phase gathered at the second half of the sample without finding any TiC phase at the first half of the sample after super gravity treatment.What's more, the area fraction of TiC increased with the position approaching the bottom of the sample along the direction of super gravity field and the enriching effect of TiC increased with the gravity coefficient and treatment time increasing.With the gravity coefficient of G = 300 and T = 1320 ℃ for 20 min, the mass content of TiC in the enriched slag increased from 11.6% of normal gravity to 18.8%.In addition, TiC phase was intercepted on the carbon fiber felt and the gangue phase was separated to the bottom of the crucible by super gravity filtration method.After separation at the gravity coefficient of G = 300 and T = 1320 ℃ for 20 min, the mass fraction of TiC was up to 23.8% in the concentrate and no TiC phase could be found in the gangue phase.
Keyword:
super gravity; enrichment; separation; carbonized slag; titanium carbide;
Received: 2016-10-10
我国攀枝花地区蕴藏丰富的钒钛磁铁矿, 其中已探明的伴生钛资源保有储量达4.28亿吨, 居世界第一位。钒钛磁铁矿中约53%左右的钛以铁精矿的形式经高炉冶炼后, 生成含钒铁水和含钛高炉渣, 高炉渣中所含的Ti O2的量一般在20%以上, 钛铁精矿也可以用来生产金红石等。由于高炉渣中钛资源的价值巨大, 许多学者对此进行了大量的研究和探索, 在一定程度上扩展了高炉渣的利用途径[1,2,3,4]。其中一种较有前景的工艺为:高温碳化处理含钛高炉渣使其中的钛组分富集于碳化钛相中, 对碳化高炉渣中的碳化钛进行富集, 再制取碳化钛精矿进行后处理[5,6,7]。由于碳化还原生成碳化钛晶粒细小, 粒度仅为几微米, 用常规的选矿方法无法将其有效分离。考虑到高温熔体中固相在超重力作用下会呈现有规律的分布[8]及高温下超重力技术可以除去金属熔体中的杂质和成功制备功能梯度材料[9,10,11,12,13], 可以将超重力技术引入到碳化高炉渣中碳化钛的富集分离中。本文利用碳化高炉渣中碳化钛相与脉石熔体之间存在的密度差异, 其中碳化钛的密度为4.93 g·cm-3, 脉石熔体的密度约为3.05 g·cm-3, 在超重力作用下可以强化碳化高炉渣中碳化钛相与脉石熔体之间的相对运动, 实现碳化钛相与脉石熔体在高温下的高效分离, 开辟一条可行的富集分离碳化高炉渣中碳化钛的利用途径, 提高资源的综合利用率[14,15]。
1 实验
1.1 原料
攀枝花钢铁公司 (攀钢) 含钛高炉渣经高温碳化还原后得到碳化渣, 碳化渣主要化学成分见表1。为了降低碳化渣的熔点和粘度, 本研究加入添加剂B2O3。把碳化渣与B2O3按质量100:8混合均匀, 再装入高纯石墨坩埚中置于硅钼炉中升温至1500℃, 整个过程中通入氩气提供保护气氛, 保温0.5 h使渣样充分熔化, 然后迅速取出石墨坩埚放入水中淬冷, 以保留试样在高温时的物相组成。实验中采用铂铑10-铂热电偶测温, 测温最大误差为±3K, 该过程所得的渣称为预处理碳化渣 (简称预处理渣) , 预处理渣的主要化学成分见表2。
表1 碳化高炉渣的主要化学成分Table 1Major chemical composition of carbonized blast furnace slag (%, mass fraction) 下载原图

表1 碳化高炉渣的主要化学成分Table 1Major chemical composition of carbonized blast furnace slag (%, mass fraction)
表2 预处理渣的主要化学成分Table 2Major chemical composition of pre-treated slag (%, mass fraction) 下载原图

表2 预处理渣的主要化学成分Table 2Major chemical composition of pre-treated slag (%, mass fraction)
1.2 设备
实验设备为自行改装设计的高温超重力冶金实验设备, 主要由高温加热部分与离心旋转部分构成[14,15,16]。其中, 定义重力系数G为表征超重力大小的参数, 表达公式如式 (1) 所示。

式中ω为离心机的角速度 (r·s-1) ;N为转速 (r·min-1) ;R为试样距转轴的距离 (m) ;g为常重力加速度 (9.8 m·s-2) 。当转速N=0时, G=1, 即常重力下重力系数为1。
1.3 过程与分析检测
实验过程包括两部分的内容: (1) 超重力条件下对预处理渣进行富集实验; (2) 在超重力条件下对预处理渣进行分离实验。
(1) 称量30 g预处理渣置入到内径为19 mm的高纯石墨坩埚中, 将该坩埚放到离心机加热炉中加热到1320℃后保温30 min, 然后立即开启离心机, 调整离心机转速使重力系数达到设定值, 在1320℃恒温条件下离心富集20 min后关闭离心机, 迅速取出坩埚水淬。沿超重力方向将水淬试样纵剖, 一半经过镶样、精磨和抛光后在扫描电子显微镜 (SEM) 下进行观察和分析物相;在光学显微镜 (OM) 放大倍数100×, 试样不同位置随机采集20张金相图片, 并用Image 6.0软件统计金相照片中碳化钛的面积分数。另一半沿着试样黑色与灰色分界线切开后用电磁制样粉碎机磨成粉末分别在日本理学Ultima IV衍射仪 (XRD) 与XRF-1800X荧光光谱分析仪上进行XRD与荧光分析, 并进行碳化钛含量的测量。
另取等量的预处理渣按上述实验步骤进行对照试验, 在加热到目标温度后, 不开启离心机, 即未进行超重力实验, 得到水淬样称为对比样。
(2) 称量15 g的预处理渣置于内径为19 mm的底部开孔且铺有过滤碳毡的高纯石墨坩埚中, 石墨坩埚底部放置另一个坩埚, 用来盛放从预处理渣中分离出来的脉石。将这一整套坩埚置于离心机加热炉中升温至1320℃后保温30 min, 然后立即开启离心机, 调整离心机转速使重力系数达到设定值, 超重力分离20 min后关闭, 迅速取出坩埚水淬。超重力分离过程中温度控制在1320℃恒定。将截留在过滤毡上的精矿与漏至底部石墨坩埚中的尾渣纵剖, 一半进行扫描电镜 (SEM) 观察与能谱分析 (EDS) , 另一半进行XRD与XRF分析, 并进行碳化钛含量的测量。
另取等量的预处理渣按上述实验步骤进行对照试验, 在加热到目标温度后, 不开启离心机, 即未进行超重力实验, 得到水淬样称为对比样。
2 结果与讨论
2.1 超重力富集试样的宏观与微观形貌
图1为预处理渣超重力富集试样与对比样的宏观形貌图。图1 (a) 为未经超重力富集的对比样纵剖面形貌图, 可看出渣中物相均匀分布在整个试样中, 没有明显界线。如图1 (b) 为预处理渣在重力系数G=300于1320℃超重力富集20 min后试样纵剖面。可以看出在试样纵剖面上出现了明显的分层, 试样上面部分呈黑亮色, 下部部分为灰色。试样纵剖面不同部分呈现不同的颜色, 主要与试样不同区域的物相组成有关。
在试样不同位置进行扫描电镜的观察和能谱分析, 结果如图2, 在试样上部黑色区域图2 (a) 主要为低熔点的脉石相, 由复合的硅酸盐矿物组成;试样下部区域图2 (b) 中分散的颗粒状灰色物质为碳化钛的晶粒, 尺寸约为几微米。
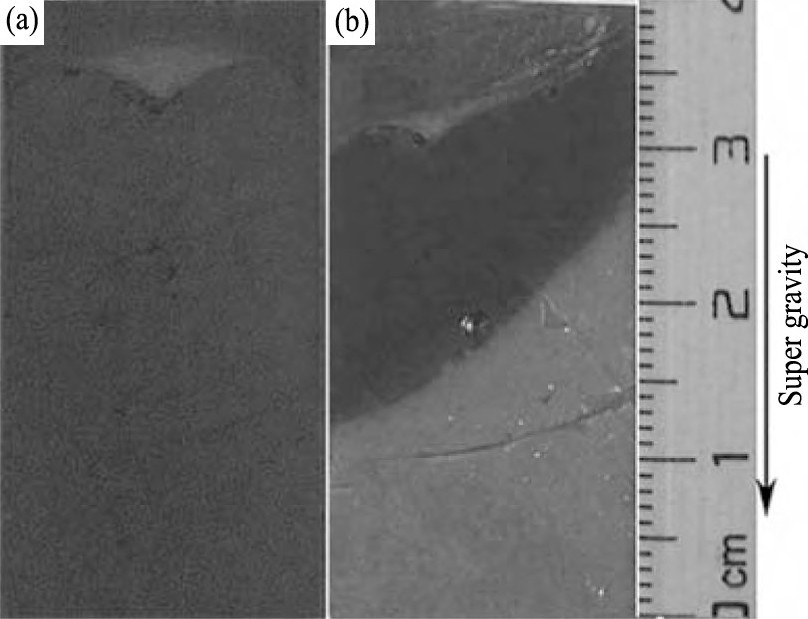
图1 超重力富集试样与对比样宏观形貌图Fig.1 Macro-structure of sample obtained by super gravity en-richment and contrast sample
(a) G=1; (b) G=300
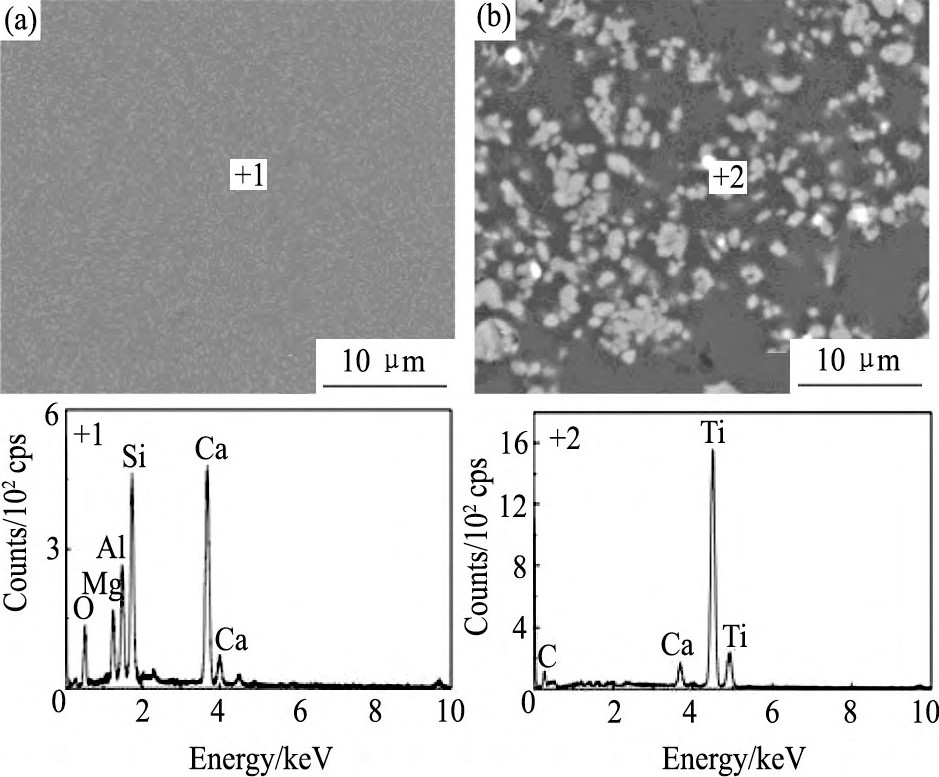
图2 超重力富集后试样的扫描电镜图片和能谱图Fig.2SEM images and EDS results obtained by super gravity enrichment
(a) Upper sample; (b) Lower sample
选择试样的不同部位进行金相显微形貌观察, 观察位置示意图如图3所示。观察结果如图4所示, 在上部黑色区域A中几乎没有碳化钛的晶粒。灰黑相交区域B为过渡带, 该区域上部与A一致, 下部为分散的碳化钛晶粒。在下部灰色区域C~E, 碳化钛全部聚集在该部分区域, 且沿着超重力方向碳化钛的分布越来越密集, 呈梯度分布趋势。
对试样不同位置的碳化钛进行统计分析, 表3给出了预处理渣在T=1320℃下以不同重力系数富集T=20 min后试样不同位置碳化钛的面积分数, 表4给出了预处理渣在G=300, T=1320℃条件下富集不同时间后试样不同位置碳化钛的面积分数。由表3, 4可知, 在试样上部 (如图3黑灰分界线B以上的区域) 几乎找不到碳化钛相, 故该区域碳化钛的面积分数趋于0。然而在试样的下部 (黑灰分界线B以下的区域C~E) 碳化钛的面积分数随着位置接近试样底部而递增。在试样底部碳化钛颗粒富集的最密集, 在该区域碳化钛的面积分数达到最大。
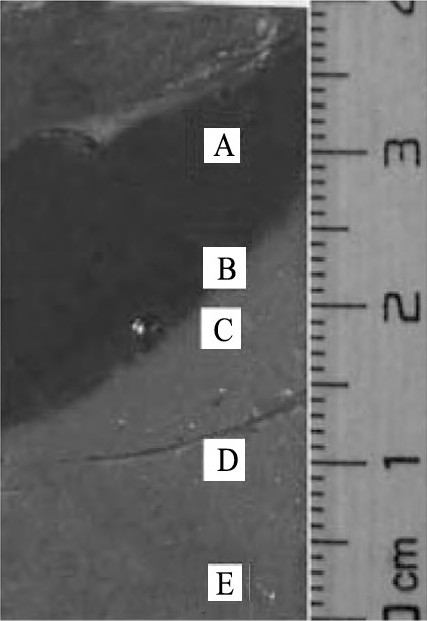
图3 超重力富集试样进行金相观察位置示意图Fig.3Schematic diagram of areas characterized by metallo-graphic microscopy after super gravity enrichment
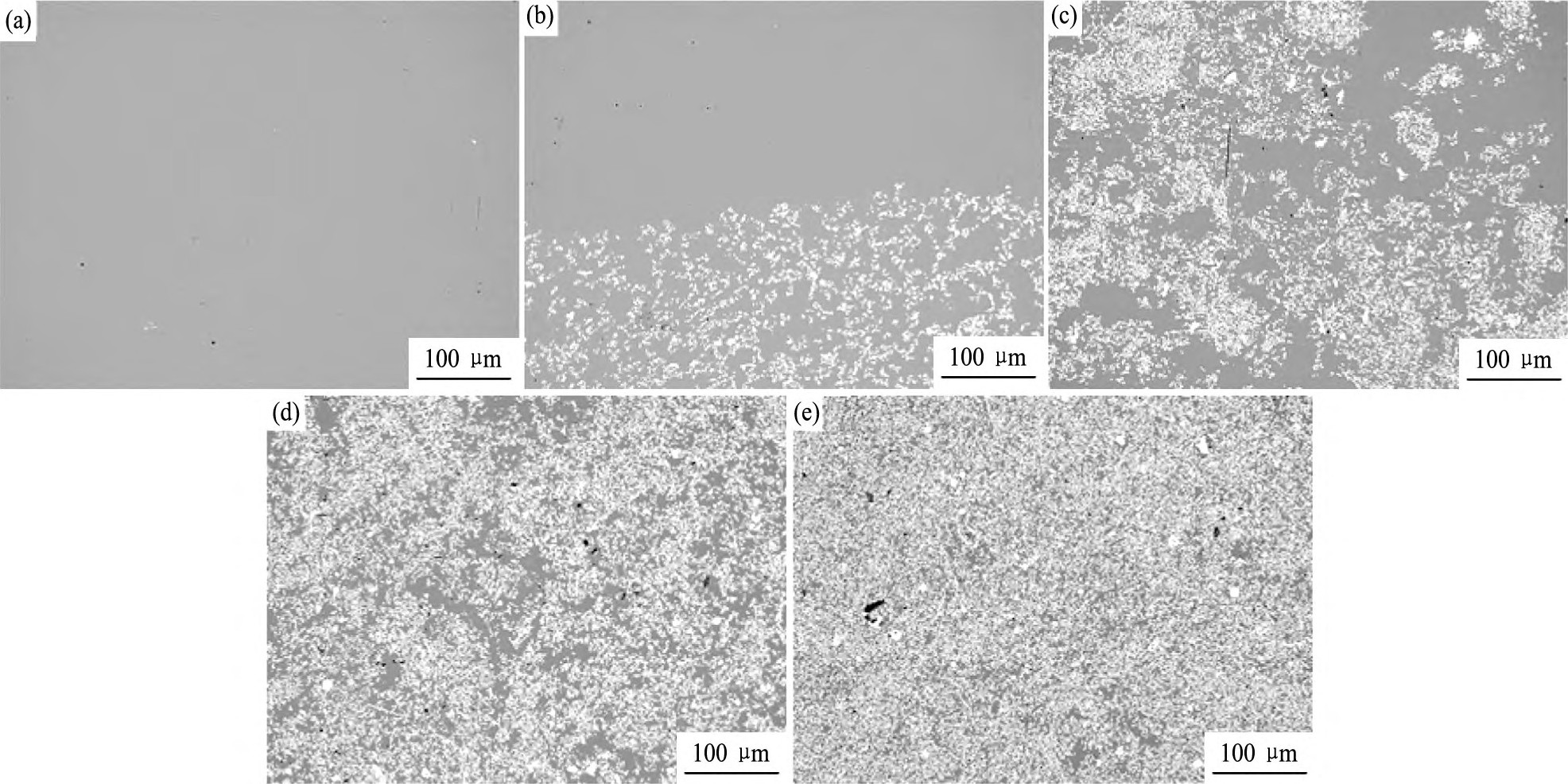
图4 超重力富集试样中碳化钛在不同位置的微观形貌和分布图Fig.4 Micro-morphology and distribution of Ti C at different positions of sample obtained by super gravity enrichment
(a) Area A; (b) Area B; (c) Area C; (d) Area D; (e) Area E
表3 不同重力系数试样不同位置碳化钛的面积分数Table 3 Area fraction of Ti C phase at different positions of sample with different gravity coefficients (T=20 min, T=1320℃) 下载原图
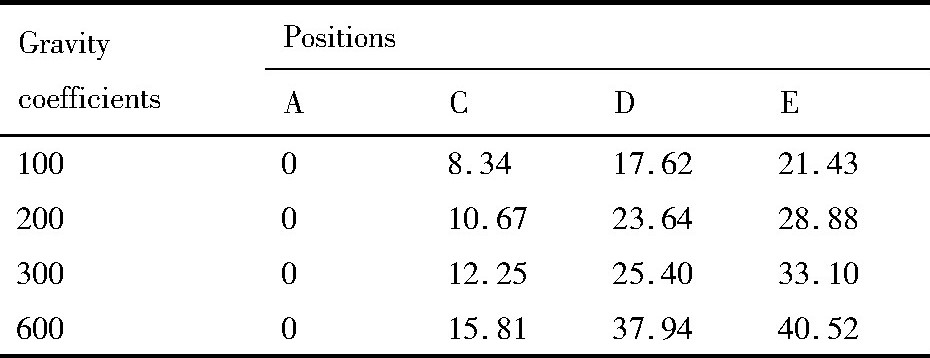
表3 不同重力系数试样不同位置碳化钛的面积分数Table 3 Area fraction of Ti C phase at different positions of sample with different gravity coefficients (T=20 min, T=1320℃)
表4 不同时间试样不同位置碳化钛的面积分数Table 4 Area fraction of Ti C phase at different positions of sample with different time (G=300, T=1320℃) 下载原图
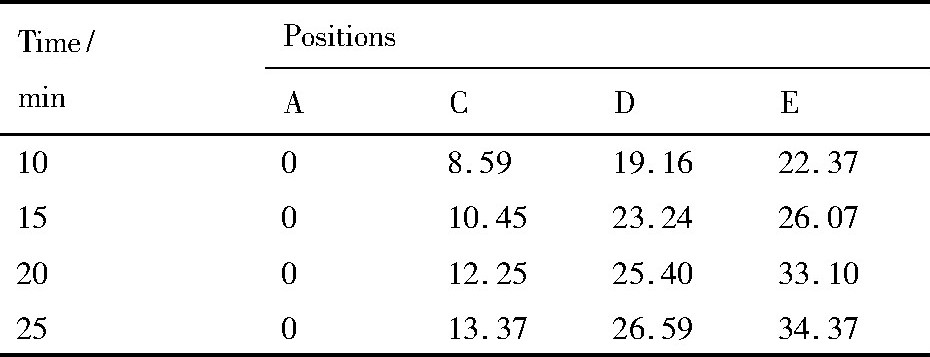
表4 不同时间试样不同位置碳化钛的面积分数Table 4 Area fraction of Ti C phase at different positions of sample with different time (G=300, T=1320℃)
图5, 6分别给出了预处理渣熔体T=1320℃以不同重力系数富集T=20 min后, 以及G=300, T=1320℃条件下以不同的时间富集后试样不同位置的碳化钛的面积分数。由此可见, 预处理渣经不同重力系数、不同时间富集后试样中碳化钛晶粒的面积分数沿着重力方向呈现梯度分布, 即越接近试样底部, 碳化钛晶粒的分布越密集, 并且重力系数越大、处理时间越长, 试样相似部位处碳化钛的分布也越密集。
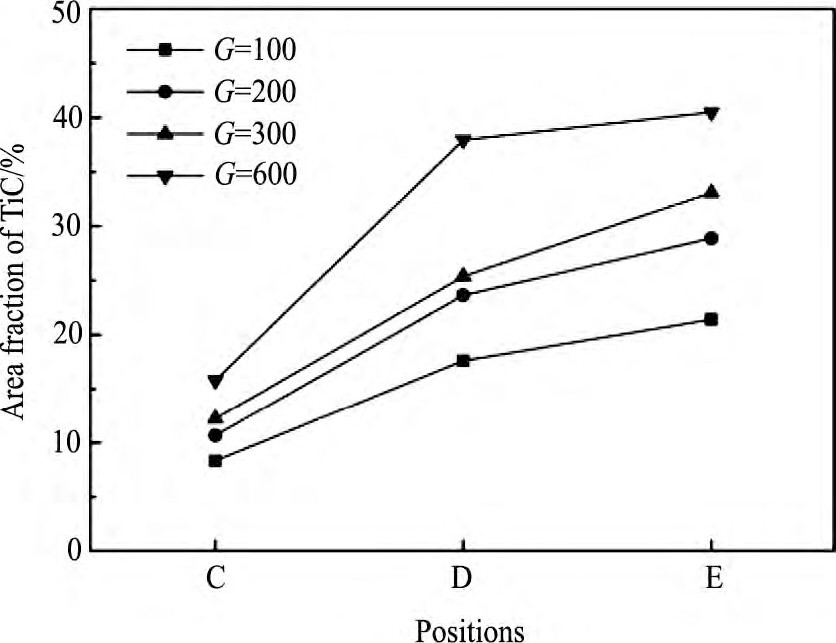
图5 不同重力系数试样不同位置碳化钛的面积分数Fig.5 Area fraction of Ti C phase at different positions of sam-ple with different gravity coefficients (T=20 min, T=1 3 2 0℃)
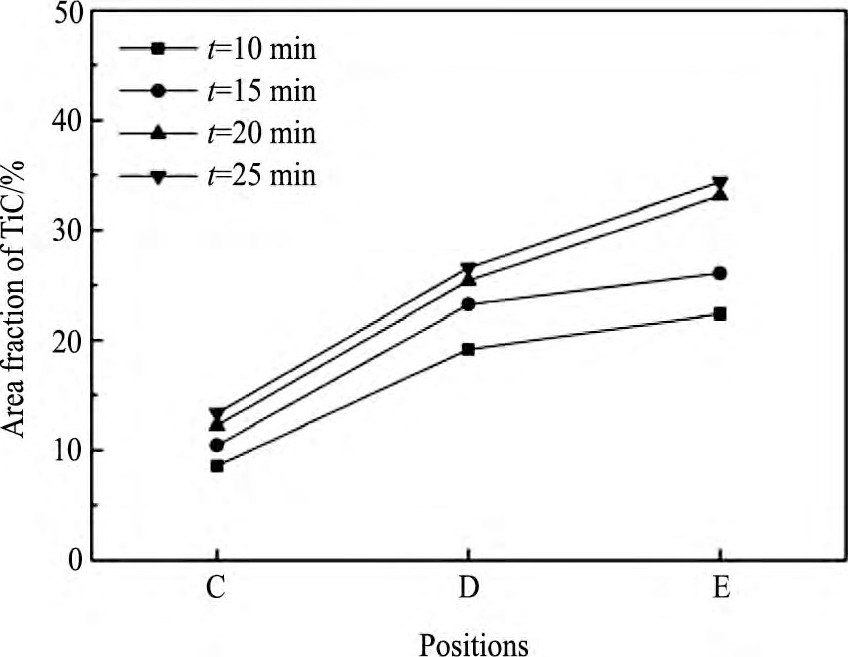
图6 不同时间试样不同位置碳化钛的面积分数Fig.6 Area fraction of Ti C phase at different positions of sam-ple with different time (G=300, T=1320℃)
该现象可由方程 (2) 进行解释[16]:

式中Vr为碳化钛晶粒在超重力场中的运动速度 (m·s-1) ;d为碳化钛颗粒的等积圆直径 (m) ;ρt为碳化钛的密度 (g·cm-3) ;ρm为脉石的密度 (g·cm-3) ;ω为离心机角速度 (r·s-1) ;r为径向距离 (m) ;η为熔体的粘度;G为重力系数;g为常重力加速度 (9.8 m·s-2) 。
由式 (2) 可知, 当ρt-ρm>0, Vr>0, 由于碳化钛的密度为4.93 g·cm-3, 脉石熔体密度约为3.05 g·cm-3, 碳化钛密度大于脉石的密度, 在超重力的作用下, 碳化钛晶粒会沿超重力方向运动到下部试样中, 最后碳化钛颗粒会迁移聚集到试样底部, 且越到试样的底部富集越多。随着超重力系数的增大, 碳化钛的运动速率也增大, 会更快地富集在试样的底部。由于碳化钛的颗粒尺寸非常小 (1~5μm) , 并且熔渣粘度很大, 碳化钛在常重力几乎不可能自发沉降, 所以在常重力条件下碳化钛颗粒很难运动富集, 因此常重力下均匀分布在试样上。
2.2 超重力富集后碳化钛的富集率
将图7中的试样沿着黑灰分界线分割成两部分, 分别进行XRD与XRF的分析。图7为预处理渣在重力系数G=300, 温度T=1320℃超重力富集20 min后试样不同部分XRD图谱。预处理渣未经超重力处理的对比样中主要的物相为碳化钛。
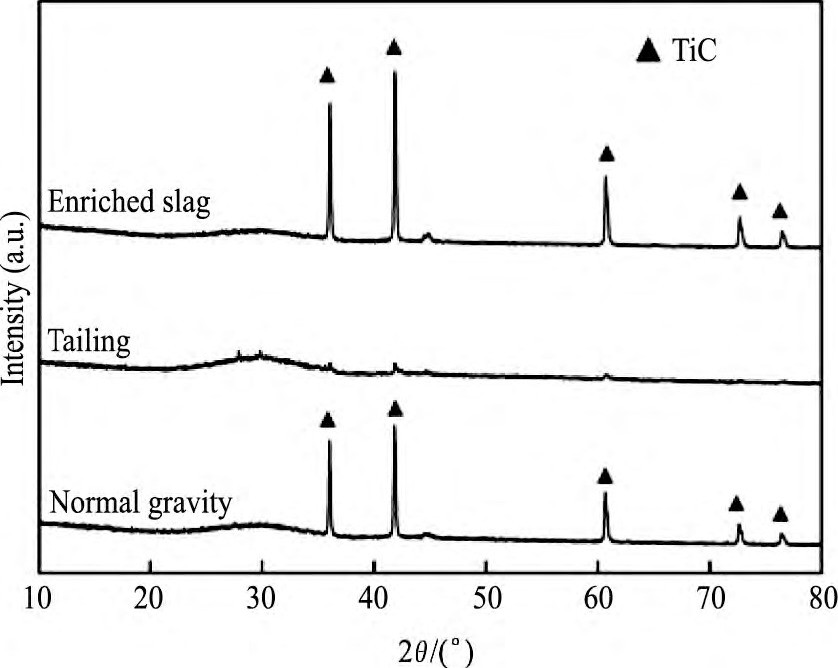
图7 对比样与超重力富集试样的XRD图谱Fig.7 XRD patterns of samples obtained by super gravity en-richment compared with contrast sample
当超重力富集后试样下部富集渣中主要物相为碳化钛, 但碳化钛的衍射峰强度比对比样中明显增强, 试样上部尾渣中只有低熔点的玻璃相, 衍射图谱中几乎找不到碳化钛的衍射峰, 说明碳化钛几乎全部聚集到了试样下部富集渣中。
表5为预处理渣熔体在重力系数G=300、温度T=1320℃超重力富集20 min后试样不同部分XRF分析结果, 从表中可以看出未进行超重力富集的预处理渣中Ti C的含量为11.6%, 当预处理渣超重力富集后, 试样下部富集渣中Ti C的含量提高到18.8%。通过超重力技术手段可使有价组元碳化钛的含量提高62%。
2.3 超重力分离试样的宏观与微观形貌
图8为预处理渣超重力分离试样与对比样的剖面宏观形貌图, 图8 (a) 为未经超重力分离的对比样, 可看出渣样全部留在碳毡上面, 试样纵剖面结构单一。当预处理渣在重力系数G=300于1320℃下超重力分离20 min后, 试样纵剖面如图8 (b) 所示, 截留在过滤毡上部的试样呈现灰黑色, 且为多孔状, 而过滤毡下部坩埚中的试样为黑色的玻璃态物相。试样上下两部分呈现不同形貌特征, 主要与组成其的物相有关。对经超重力分离后的试样不同部分进行扫描电镜观察, 如图9所示, 图9 (a) 为对比样, 碳化钛分散的分布在整个试样纵剖面上, 图9 (b) 为超重力分离后在碳毡上部的精矿, 碳化钛均匀地富集在试样中, 图9 (c) 为经超重力分离后被聚集在下部坩埚的低熔点脉石相。
表5 富集渣与尾渣的XRF结果Table 5 XRF result of enriched slag and tailing slag (%, mass fraction) 下载原图
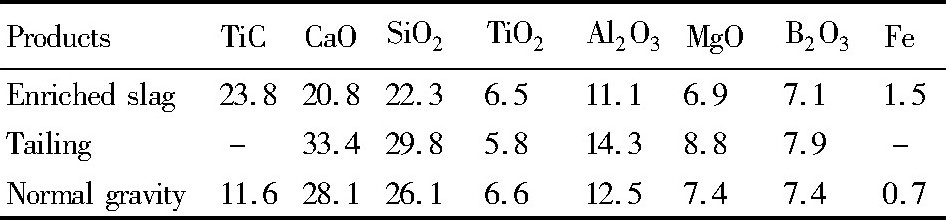
表5 富集渣与尾渣的XRF结果Table 5 XRF result of enriched slag and tailing slag (%, mass fraction)
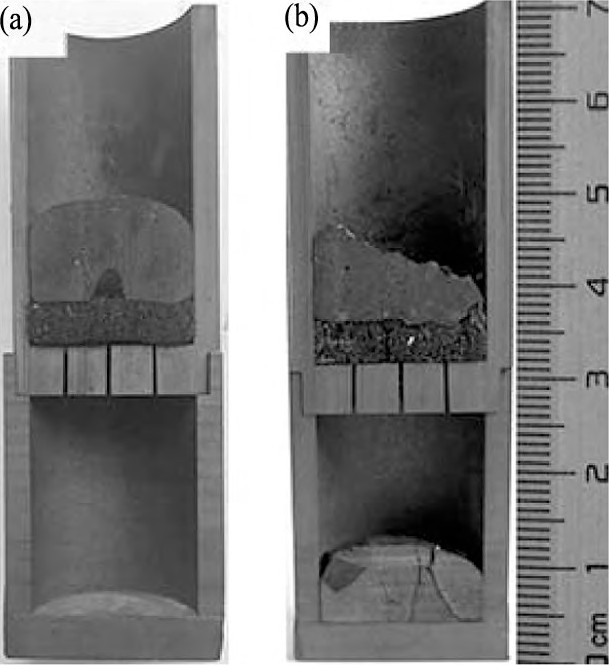
图8 超重力富集试样与对比样宏观形貌面Fig.8Macro-structure of sample obtained by super gravity separation and contrast sample
(a) G=1; (b) G=300
2.4 超重力分离后碳化钛的富集率
将截留在过滤碳毡上部和下部的试样进行XRD分析, 其结果如图10所示, 未经超重力分离的预处理渣中晶体相为Ti C相, 当预处理渣在重力系数G=300于1320℃超重力分离20 min后, 截留在碳毡上部的精矿中晶体相为Ti C相, 而下部尾渣中无明显衍射峰, 以玻璃相存在。显而易见, 碳化钛几乎全部被富集到精矿中。
对过滤碳毡上下两部分的试样进行XRF分析, 其结果如表6所示, 未经超重力分离的预处理渣中Ti C的含量为11.6%, 经过超重力分离后, 截留在碳毡上部的精矿中Ti C含量提高到23.8%, 下部尾渣中几乎没有碳化钛, 与前边XRD的测试结果一致。
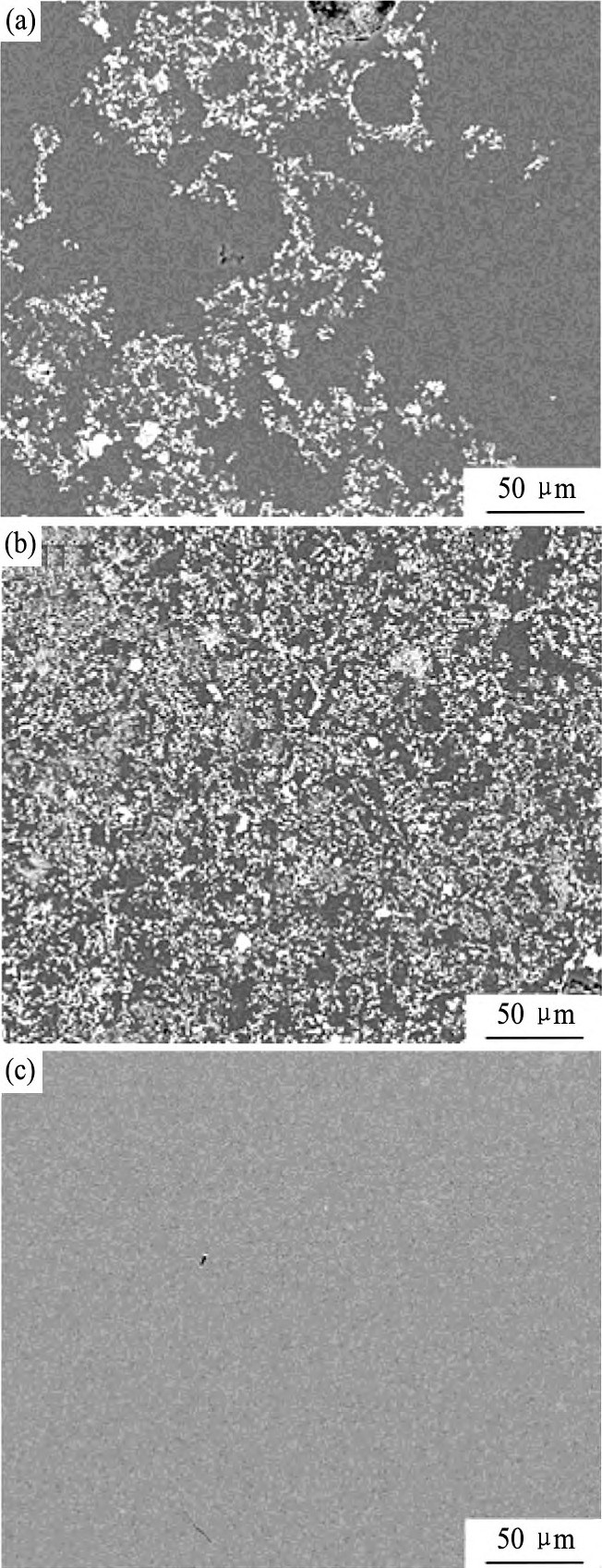
图9 对比样与超重力分离后试样的扫描电镜图Fig.9SEM images obtained by super gravity separation and contrast sample
(a) Contrast sample; (b) Concentrate; (c) Tailing
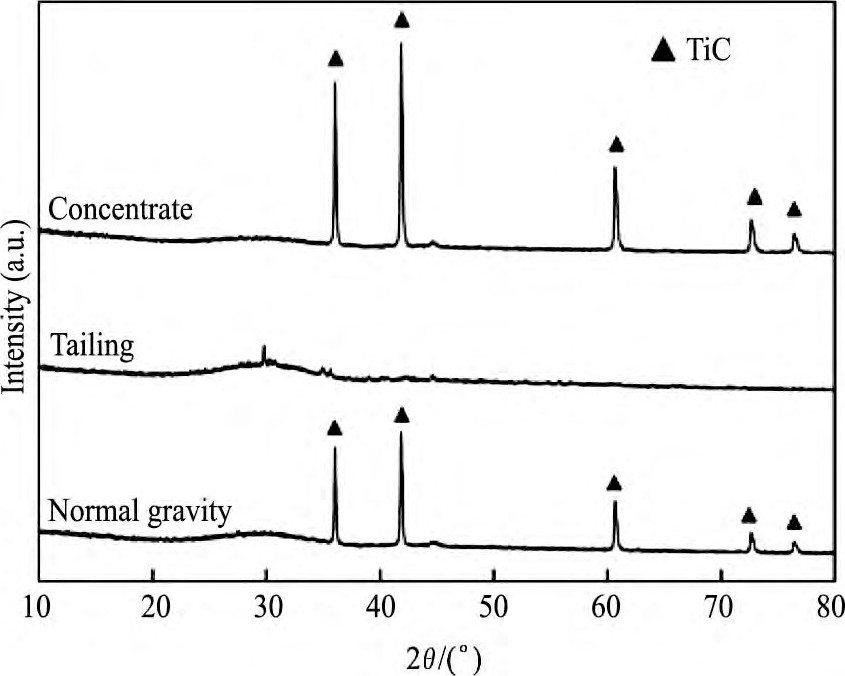
图1 0 对比样与超重力分离试样的XRD图谱Fig.10XRD patterns of samples obtained by super gravity separation compared with contrast sample
表6 精矿与尾渣的XRF结果Table 6XRF result of concentrate and tailing slag (%, mass fraction) 下载原图
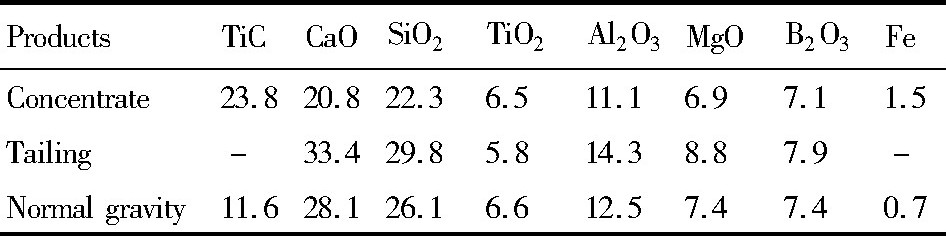
表6 精矿与尾渣的XRF结果Table 6XRF result of concentrate and tailing slag (%, mass fraction)
3 结论
1.在等温条件下经过超重力富集后, 预处理渣熔体中有价组元碳化钛实现了定向富集, 试样出现明显分层, 在试样的上部区域几乎找不到碳化钛相, 熔体中的碳化钛全部富集到下部试样中。随着重力系数的提高和处理时间的增大, 试样中碳化钛的富集程度也逐渐增大。
2.当预处理渣以重力系数G=300, T=1320℃等温富集20 min后, 富集渣中碳化钛的含量由常重力下的11.6%提高到了18.8%, 提高了熔渣中碳化钛的品位。
3.当预处理渣以重力系数G=300, T=1320℃等温分离20 min后, 碳化钛相全部被分离在碳毡上部的精矿中, 试样下部为脉石相。碳毡上部精矿中的碳化钛的含量由常重力下的11.6%增大到了23.8%。
参考文献
[1] Du H G.Theory of Smelting V and Ti-Magnetite by Blast Furnace[M].Beijng:Science Press, 1996.20. (杜鹤桂.高炉冶炼钒钛磁铁矿原理[M].北京:科学出版社, 1996.20.)
[2] Feng C J, Zhang J S.Preparation of Ti C from panzhihua blast furnace slags containing Ti O2[J].Mineral Utilization, 1997, (6) :34. (冯成建, 张建树.采用攀钢高炉渣制取碳化钛的试验研究[J].矿产综合利用, 1997, (6) :34.)
[3] Lu P.Progress and prospect of industrialization of comprehensive utilization of Pangang blast furnace slag[J].Iron Steel Vanadium Titanium, 2013, (3) :33. (陆平.攀钢高炉渣综合利用产业化研究进展及前景分析[J].钢铁钒钛, 2013, (3) :33.)
[4] Wang L, Che X K, Chen S Z, Wang X F, Xiang J, Deng Q J.Leaching ilmenite from Panxi ilmenite by using HCL and chloride slat solutions[J].Chinese Journal of Rare Metals, 2017, 41 (8) :912. (王雷, 车小奎, 陈树忠, 王雪飞, 向俊, 邓巧娟.盐酸加盐浸出攀西钛铁矿的研究[J].稀有金属, 2017, 41 (8) :912.)
[5] Liu X H.Study on High-Temperature Carbonization and Low-Temperature Chlorination on Modified Titanium Bearing Blast Furnace Slag[D].Shenyang:Northeastern University, 2009.21. (刘晓华.改性含钛高炉渣高温碳化低温氯化的研究[D].沈阳:东北大学, 2009.21.)
[6] Li C Y, Li Y W, Gao Y M, Yang D B, Li Y B, Nie J H.Research on extracting Ti (C, N) from high-titanium slag[J].Iron Steel Vanadium Titanium, 2006, 27 (3) :5. (李慈颖, 李亚伟, 高运明, 杨大兵, 李远兵, 聂建华.高钛渣提取碳氮化钛的研究[J].钢铁钒钛, 2006, 27 (3) :5.)
[7] Yi X X, Li Y W, Yang D B.Research of titanium carbonitride from panzhihua Ti-bearing blast furnace slag using magnetic separation[J].Mining Metallurgy, 2008, 17 (3) :46. (易小祥, 李亚伟, 杨大兵.攀钢含钛高炉渣碳氮化后磁选提钛研究[J].矿冶, 2008, 17 (3) :46.)
[8] Yoshimi Watanable, Akihiro Kawamotol, Koichi Matsuda.Partical size distribution in functionally graded materials fabricate by the centrifugal solid-particle method[J].Composites Science and Technology, 2002, 62:881.
[9] Kim S W, Im U H, Cha H C, Kim S H, Jiang J E, Kim K Y.Removal of primary iron rich phase from aluminum-silicon melt by centrifugal separation[J].China Foundry, 2013, 10 (2) :112.
[10] Zhao L X, Guo Z C, Wang Z, Wang M Y.Removal of low-content impurities from Al by super-gravity segregation[J].Metall.Mater.Trans.B, 2010, 41 (3) :505.
[11] Li J W, Guo Z C, Tang H Q, Wang Z, Sun S T.Si purification by solidification of Al-Si melt super gravity[J].Trans.Nonferrous Met.Soc.China, 2012, 22 (4) :958.
[12] Xie Y, Liu C M, Zhai Y B, Wang K, Li X D.Centrifugal casting processes of manu facturing in situ functionally gradient composite materials of Al-19Si-5Mg alloy[J].Rare Metals, 2009, 28 (4) :405.
[13] Chirita G, Soares D, Silva F.Advantages of the centrifugal casting tech nique for the production of structural components with Al-Si alloys[J].Materials&Design, 2008, 29 (1) :20.
[14] Li J C, Guo Z C, Gao J T.Isothermal enriching perovskite phase from Ca O-Ti O2-Si O2-Al2O3-Mg O system by super gravity[J].ISIJ International, 2014, 54 (4) :743.
[15] Li J C, Guo Z C, Gao J T.Laboratory assessment of isothermal separa tion of V containing spinel phase from vanadium slag by centrifugal casting[J].Ironmaking and Steelmaking, 2014, 41 (9) :710.
[16] Rahimipour M R, Sobhani M.Evaluation of centrifugal casting pro cess parameters for in situ fabricated functionally gradient Fe-Ti C composite[J].Metall.Mater.Trans.B, 2014, 44B:1120.