文章编号:1004-0609(2012)06-1718-07
镀TiC金刚石/铝复合材料的界面及热膨胀性能
王新宇,于家康,朱晓敏
(西北工业大学 凝固技术国家重点实验室,西安 710072)
摘 要:采用气压浸渗法制备高体积分数的镀TiC金刚石/铝复合材料,通过SEM和EDS等手段对复合材料的断口形貌进行分析,并研究TiC镀层对复合材料界面和热膨胀性能的影响。结果表明:TiC镀层改善金刚石颗粒与铝合金基体之间的选择性粘结现象,断裂方式以基体断裂为主。部分TiC会被氧化成TiO2并与铝合金基体反应生成Al2O3,从而实现金刚石颗粒与铝合金基体之间良好的界面结合;TiC镀层有效地降低复合材料的热膨胀系数(CTE),增强复合材料热膨胀性能的稳定性。在体积分数相同的情况下,CTE随金刚石颗粒尺寸的减小而减小。
关键词:复合材料;气压浸渗;镀层;界面;热膨胀
中图分类号:TB333 文献标志码:A
Interface and thermal expansion properties of TiC-coated diamond/Al composites
WANG Xin-yu, YU Jia-kang, ZHU Xiao-min
(State Key Laboratory of Solidification Processing, Northwestern Polytechnical University, Xi’an 710072, China)
Abstract: The TiC-coated diamond/Al composites with high volume fraction were fabricated by gas pressure infiltration. The fracture surface of the composites was analyzed by SEM and EDS, and the influence of titanium carbide coating on the interfacial bonding and thermal expansion of the composites was investigated. The results show that the TiC coating is proved to improve the selective interfacial bonding between diamond particles and Al alloy matrix, and the ductile rupture of the matrix is the main facture mechanism. Part of the TiC coating is oxidized to TiO2 and then reacts with Al to produce Al2O3 and thus to achieve the better interfacial bonding between diamond particles and Al alloy matrix. The coefficient of thermal expansion (CTE) of composites is decreased and stabilized due to the TiC coating. For the same volume fraction, the CTE of composites decreases with the decrease of the particle diameter.
Key words: composites; gas pressure infiltration; coating; interface; thermal expansion
随着电子技术的不断发展,在电子封装领域,电子器件和电子装置中元器件的复杂性和密集性日益提高,导致器件产生的热量越来越多,微处理器及半导体器件在应用过程中常常因为温度过高而无法正常工作,散热问题在电子信息产业发展中已经受到广泛的关注[1-3]。金刚石具有高热导率和低热膨胀系数的特征:Ia型金刚石(含氮)的热导率为600 W/(m·K),高纯IIa型金刚石的热导率大约为2 200 W/(m·K),通过高温高压法制备的Ib型金刚石的热导率在1 200~2 000 W/(m·K)之间(和氮含量相关),金刚石的热膨胀系数在0.8×10-6~1.5×10-6 K-1范围[4]。所以,将金刚石颗粒作为增强体与金属基体(Al、Cu、Ag等)制备成复合材料,就可以使金刚石优异的热学性能很好地利用在封装材料中。同时,铝和铝合金具有较高的比强度、优异的耐腐蚀性和较低的密度,再加上较低的制造成本和材料价格,使得其成为金属基复合材料中应用较广的基体材料。因此,金刚石/铝复合材料是一种具有广阔应用前景的新型电子封装材料[5]。
尽管如此,金刚石/铝复合材料的界面结合问题已经成为制约这种新型电子封装材料得以应用的主要难题。金刚石与铝合金基体之间的润湿性较差,铝合金基体只能选择性的与金刚石{001}晶面粘结,而很难粘附于{111}晶面上[6]。针对此问题,通过在金刚石颗粒表面进行镀层处理可以有效地改善铝合金基体与 {111}晶面的界面结合。SCHUBERT等[7-8]的研究结果表明,在金刚石表面镀上一层较薄的Cr3C2可以提高增强体与基体间的界面结合。WEBER和TAVANGAR[9]则是在基体中加入如Cr和B等活性元素,利用这些活性元素与基体之间的化学反应来实现金刚石和基体间的界面结合。
目前,国内外对于金刚石增强金属基复合材料的研究已经成为了热点,但是主要的研究集中在复合材料的热导率方面[10-11]。XUE等[12]通过改变增强体的 体积分数,对复合材料热导率的实验结果和理论模型进行了对比与分析。而在复合材料的热膨胀性能方面,关于镀层对复合材料热膨胀性能影响的研究则较 少[13-14]。因此,本文作者采用气压浸渗法制备高体积分数和低热膨胀系数的金刚石/铝复合材料,应用SEM和EDS分析试样的显微组织、断口形貌及界面反应,测试热膨胀性能,深入研究金刚石颗粒表面的TiC镀层以及金刚石颗粒粒径变化对复合材料的界面结合和热膨胀性能的影响。
1 实验
选用AlSi7Mg合金作为基体材料,其化学成分为7%Si,0.35%Mg(质量分数),其余为Al。选用MBD4型平均粒径分别为70、150、300 μm的未镀层与镀TiC的金刚石颗粒作为增强体。表面镀层采用气相沉积法,工艺参数为:在750 ℃和6~7 Pa 的真空度下微镀钛30 min。通过气相沉积的钛和金刚石表面碳反应生成碳化钛镀层。镀覆后金刚石颗粒的质量大约增加了1%,厚度为2 μm。
采用气压浸渗方法制备体积分数为65%的金刚 石/铝复合材料。如图1所示,首先将金刚石颗粒装在石墨模具中振动、压实使其密实化并放入上炉炉腔 内,然后将铝合金液放入下炉炉腔,设定上炉的温度为750 ℃,下炉的温度为800 ℃,将设备腔内的真空度抽到4 000 Pa以下,保温20 min达到热平衡,最后在1.45 MPa的压力条件下浸渗,浸渗后的凝固时间约为3 min。
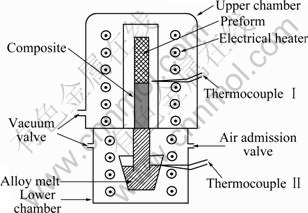
图1 气压浸渗设备示意图
Fig.1 Schematic diagram of gas pressure infiltration apparatus
采用Zeiss SUPRA 55型扫描电子显微镜(SEM)和Oxford INCA型能谱仪(EDS)观察复合材料的显微组织和断口形貌;采用 Philips X’ Pert MPD Pro型自动X射线衍射仪(XRD)分析该复合材料的物相组成;采用德国NETZSCH DIL402C热膨胀仪测量试样的热膨胀系数,测试的试样为d 6 mm×25 mm的圆柱体,测试温度范围为30~200 ℃,升温速度为5 ℃/min,用流速为50 mL/min的氩气保护。
2 结果与讨论
2.1 金刚石颗粒形貌
金刚石的物理性能优异,但由于与铝合金基体润湿性差,需在其表面镀覆一层涂层,图2所示为表面有镀层的金刚石颗粒的SEM像。可以看到,金刚石颗粒呈规则十四面体形状,颗粒表面镀层均匀、致密。
通过XRD分析(见图3(a))可知,金刚石颗粒表面的镀层为TiC。由于金刚石颗粒与铝合金之间的润湿性较差,且铝合金基体在金刚石{001}晶面和{111}晶面上的粘附情况有很大差异,所以金刚石颗粒表面的TiC镀层不仅可以改善金刚石增强体与铝合金基体之间的润湿性,而且可以消除铝基体在金刚石表面选择性粘结现象,达到增强界面结合的作用。图3(b)所示为镀TiC金刚石颗粒在浸渗前经过加热后的XRD谱。由图3(b)中可以看出,镀TiC金刚石颗粒中的物相除了TiC以外还发现了TiO2,TiO2的形成有利于在界面反应中生成Al2O3,从而很好地改善了金刚石颗粒与铝合金基体之间的界面结合。
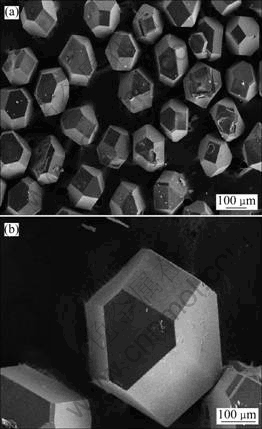
图2 镀TiC金刚石颗粒的表面形貌
Fig. 2 Surface morphologies of TiC coating on diamond particles: (a) 150 μm; (b) 300 μm
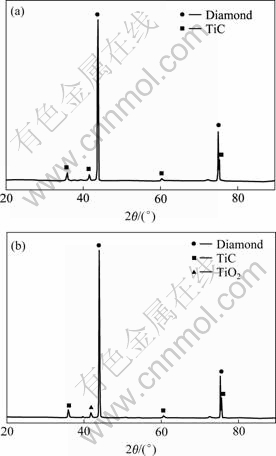
图3 镀TiC金刚石颗粒的相组成
Fig. 3 Phase composition of TiC-coated diamond particles: (a) After disposition; (b) Before infiltration
2.2 复合材料的界面特征
图4所示为金刚石/铝复合材料的断口形貌。从图4(a)中可以看出,未镀TiC的金刚石颗粒与铝合金基体之间的润湿性差,存在明显的选择性粘结现象,铝基体容易粘附在金刚石的{001}晶面上,却难以与金刚石的{111}晶面实现良好的界面结合,所以界面结合不均匀,铝基体不能完全填充到金刚石颗粒之间,从而严重影响复合材料的界面结合。选择性粘结现象是由金刚石不同晶面上的碳原子排布不同造成的。在金刚石{111}晶面上,每个碳原子周围有3个最邻近的碳原子,而在金刚石{001}晶面上,碳原子只与周围临近的两个碳原子相连,金刚石表面的碳原子和铝基体发生化学反应必须实现C—C键的断裂。COLTTERS[15]的研究结果表明,金刚石{001}晶面上的碳原子比{111}晶面上的碳原子更容易实现化学键的断裂,有利于金刚石{001}面上的碳原子和铝基体发生反应,加强铝 基体与金刚石{001}晶面的结合,而与{111}晶面上的结合则较差。
图4(b)所示为镀TiC后金刚石和铝之间的界面结合情况。可以看到,TiC镀层能有效提高金刚石与铝基体之间的界面结合。由于铝基体与TiC镀层之间的润湿性很好,铝基体几乎粘附在金刚石颗粒的所有表面,选择性粘结现象不再出现,从而使金刚石颗粒通过铝基体有效地连接在一起,形成一个金刚石颗粒的骨架结构,没有明显的空隙。

图4 金刚石/铝复合材料断口的SEM像
Fig. 4 SEM images of fracture of diamond /Al composite: (a) Uncoated; (b) Coated
为了确定复合材料界面处的化学元素,将试样表面浸没在浓度为20%的盐酸中进行腐蚀,充分反应掉金刚石颗粒表面的铝合金。图5(a)和表1所示为未镀TiC金刚石/铝复合材料界面区域的SEM像和EDS点扫描分析结果。由图中可以看到,未镀层的金刚石颗粒表面光滑,粘附的铝合金基体几乎都被腐蚀,有效反应界面和残余物质较少,其界面处的化学成分主要有硅、碳和氧元素。
表1 EDS点扫描分析未镀TiC金刚石/铝复合材料界面区域的化学元素组成
Table 1 EDS dates of interfacial element composition of diamond/Al composite with TiC-uncoated diamond (Mole fraction, %)

采用EDS点扫描分析镀TiC金刚石/铝复合材料界面部分的化学成分,结果见表2。由图5(b)中看到,镀TiC的金刚石颗粒表面比较粗糙,出现了一些块状和片状的显微组织。表2显示,界面区域明显出现铝、碳和钛峰位,结合图中出现的显微组织分析推测,TiC和铝合金之间发生了化学反应。在750 ℃的高温条件下,TiC与铝合金之间的反应[16-17]如下:
4Al+3TiC→Al4C3+3Ti (1)
反应证明,TiC镀层不仅很好地防止了金刚石颗粒在高温条件下受热损伤,而且也提高了金刚石颗粒的热稳定性,使其不发生石墨化现象,对金刚石颗粒起到了保护作用,从而保证了金刚石优异的热学性能不发生改变。
表2的扫描结果证实,镀TiC金刚石/铝复合材料界面除含铝、碳、钛和硅元素外,还含有大量的氧元素,与表1相比较可以得出,镀TiC金刚石颗粒表面的氧元素含量明显高于未镀层的含量,经分析认为,虽然浸渗在抽真空的条件下进行,但真空度无法达到很高,设备中仍有部分残留的氧气,这就可能导致在高温的情况下会发生TiC被氧化的反应:
TiC+2O2→TiO2+CO2 (2)
此反应中的TiO2可以在图3(b)中得到证实。此 外,对原位合成TiC/Ti-6Al复合材料的氧化行为研究发现,这种复合材料首先发生TiC颗粒的氧化,因为TiC颗粒和氧气之间具有更高的反应活性,所以在浸渗之前金刚石表面由TiC层和部分被氧化生成的TiO2层组成[18]。TiO2和铝合金在高温下发生如下反应[19]:
3TiO2+4Al→2Al2O3+3Ti (3)
该反应说明,在基体与增强体之间的界面处有部分Al2O3生成,Al2O3在一定程度上能提高界面结合强度,避免铝合金基体直接与金刚石颗粒发生反应,对促进界面结合起到很好的作用。
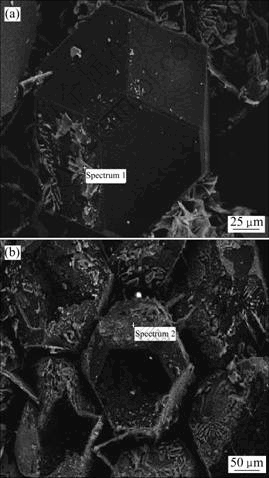
图5 腐蚀后金刚石/铝复合材料SEM像
Fig. 5 SEM images of diamond/Al composite after etching: (a) Uncoated; (b) Coated
表2 EDS点扫描分析镀TiC金刚石/铝复合材料界面区域的化学元素组成
Table 2 EDS data of interfacial element composition of diamond/Al composite with TiC-coated diamond (mole fraction, %)

以上的化学反应的进行实现了金刚石和铝基体之间的界面结合,尤其是金刚石{111}面上的结合,对于复合材料性能的提高具有重要的意义。
2.3 热膨胀性能
在复合材料中,界面对复合材料热膨胀性能的影响至关重要。界面结合强度越高,其发挥的协调作用也就越好。在界面结合较差的情况下,随着温度的升高,复合材料中基体与增强体颗粒就会因热膨胀系数的不匹配而产生热应力,当热应力累积到一定程度便会释放,从而导致材料的热稳定性下降。而对于界面结合较好的情况,界面对于复合材料的协调作用则较强,可以有效地减少基体与增强体之间的热应力现象的发生,从而提高复合材料的热膨胀性能。
图6所示为不同金刚石颗粒尺寸的复合材料CTE值随温度的变化曲线。从图6中可以看出,对于3种不同尺寸的金刚石颗粒,镀TiC金刚石/铝复合材料的CTE值明显小于未镀TiC的,这表明TiC镀层对该复合材料的CTE值的减小起到显著作用。图4中的断口形貌可以解释其原因:未镀TiC的复合材料断裂方式主要以界面断裂为主,说明其界面结合较差,当铝合金基体发生膨胀时,金刚石颗粒对基体不能起到很好的抑制作用。而镀TiC的复合材料的断裂方式则主要为基体断裂,界面结合紧密,这主要是因为金刚石颗粒的TiC镀层和部分被氧化生成的TiO2改善了金刚石颗粒和铝合金基体之间的润湿性,铝合金基体可以同时粘附在金刚石的{001}晶面和{111}晶面上,提高界面结合面积,加强增强体对铝合金基体的束缚作用,从而降低镀TiC复合材料的CTE值。
对于封装材料而言,除了要有与芯片或者基片材料相匹配的热膨胀系数以外,还需要满足热膨胀性能稳定的目的。从图6中复合材料CTE值的变化可以看出,镀TiC金刚石/铝复合材料的CTE值变化比较平稳,随温度的增加,其CTE值增加幅度较小。说明金刚石颗粒通过镀TiC处理后,使其与铝合金基体之间形成了相对稳定的界面,界面对增强体和基体之间的热膨胀差异起到协调作用。随着这种界面强度的提 高,其发挥的协调作用也随之增强。
对比分析图6可以得出:在体积分数相同的条件下,复合材料的CTE值随金刚石颗粒尺寸的减小而减小,而颗粒尺寸的大小对CTE的影响主要体现在界面区域。随着温度的升高,由于基体和增强体间热膨胀系数的差异,导致两种热应力,基体受到压应力作用而增强体受到拉应力作用,冷却时则相反。复合材料主要是靠界面约束基体膨胀的,所以当体积分数相同时,颗粒尺寸越小,界面的总面积就越大,对基体的约束能力就越强,从而使复合材料的CTE值降低。在另一方面,根据VAIDYA和CHAWLA[20]的理论,假定颗粒微球形并被金属均匀的包围着,则
(4)
(5)
(6)
式中:a为颗粒半径;r为颗粒中心到铝基体外端距 离;σr是径向应力;σθ是周向应力;
是泊松比;E是弹性模量;p是界面压力;
是体积分数;p和m分别代表颗粒和基体。那么,界面处的应力为
(7)
从式(7)中可以分析出在体积分数相同的情况下,复合材料界面处的应力取决于颗粒粒径,随着颗粒粒径的减小,界面处产生的应力减小,在温度变化的情况下释放的应力也随之减小,产生较小的应变,从而降低复合材料的热膨胀系数。

图6 不同金刚石颗粒尺寸的复合材料CTE值随温度的变化曲线
Fig. 6 CTE values of composite with different sizes of diamond particles versus temperature rise: (a) 70 μm; (b) 150 μm; (c) 300 μm
3 结论
1) 应用气压浸渗工艺成功制备70、150、300 μm的未镀层与镀TiC的金刚石/铝复合材料。采用的MBD4型金刚石颗粒形貌规则,表面镀层均匀、致密,能够很好地改善金刚石颗粒与铝合金基体之间润湿 性能。
2) 镀TiC的金刚石颗粒与铝合金基体之间明显存在消除选择性粘结现象,铝合金基体几乎粘附在金刚石颗粒的所有表面,界面结合良好,断裂方式主要以基体断裂为主,同时存在少量的界面断裂。TiC镀层的存在实现金刚石颗粒和铝合金基体之间良好的界面结合,尤其是金刚石{111}面上的结合,对于复合材料性能的提高具有重要意义。
3) TiC镀层能有效地改善金刚石颗粒与铝合金基体间的界面结合,降低复合材料的热膨胀系数,提高复合材料热膨胀性能的稳定性。在相同体积分数的情况下,CTE随金刚石颗粒尺寸的减小而减小。
REFERENCES
[1] 李婷婷, 彭超群, 王日初, 王小锋, 刘 兵.电子封装陶瓷基片材料的研究进展[J]. 中国有色金属学报, 2010, 20(7): 1365-1374.
LI Ting-ting, PENG Chao-qun, WANG Ri-chu, WANG Xiao-feng, LIU Bing. Research progress in ceramic substrate material for electronic packaging[J]. The Chinese Journal of Nonferrous Metals, 2010, 20(7): 1365-1374.
[2] 于家康, 周尧和. 混杂2D-C/Al电子封装复合材料的设计与制备[J]. 中国有色金属学报, 2000, 10(S1): 1-5.
YU Jia-kang, ZHOU Yao-he. Design and fabrication of hybrid 2D-C/Al composites for electronic packaging[J]. The Chinese Journal of Nonferrous Metals, 2000, 10(S1): 1-5.
[3] 冯 曦, 郑子樵, 李世晨, 杨培勇. 热压法制备Si-Al电子封装材料及其性能[J]. 稀有金属, 2005, 29(1): 11-15.
FENG Xi, ZHENG Zi-qiao, LI Shi-chen, YANG Pei-yong. Electronic packaging materials fabricated by hot pressing[J]. Chinese Journal of Rare Metals, 2005, 29(1): 11-15.
[4] YAMAMOTO Y, IMAI T, TANABE K, TSUNO T, KUMAZAWA Y, FUJIMORI N. The measurement of thermal properties of diamond[J]. Diamond and Related Materials, 1997, 6(8): 1057-1061.
[5] 梁雪冰, 褚 克, 贾成厂. 放电等离子烧结制备Diamond/Al复合材料[J]. 复合材料学报, 2008, 6(12): 192-197.
LIANG Xue-bing, CHU Ke, JIA Cheng-chang. Diamond/Al composites fabricated by spark plasma sintering[J]. Acta Materiae Compositae Sinica, 2008, 6(12): 192-197.
[6] RUCH P W, BEFFOR O, KLEINER S. Selective interfacial bonding in Al(Si)-diamond composites and its effect on thermal conductivity[J]. Composites Science and Technology, 2006, 66(15): 2677-2685.
[7] SCHUBERT T, CIUPINSKI L, ZIELINSKI W, MICHALSKI A, WEISGARBER T, KIEBACK B. Interfacial characterization of Cu/diamond composites prepared by powder metallurgy for heat sink applications[J]. Scripta Materialia, 2008, 58(4): 263-266.
[8] SCHUBERT T, TRINDADE B, WEIGARBER T, KIEBACK B. Interfacial design of Cu-based composites prepared by powder metallurgy for heat sink applications[J]. Materials Science and Engineering A, 2008, 475(1/2): 39-44.
[9] WEBER L, TAVANGAR R. On the influence of active element content on the thermal conductivity and thermal expansion of Cu-X (X=Cr, B) diamond composites[J]. Scripta Materialia, 2007, 57(11): 988-991.
[10] MOLINA J M, RHEME M, CARRON J, WEBER L. Thermal conductivity of aluminum matrix composites reinforced with mixtures of diamond and SiC particles[J]. Scripta Materialia, 2008, 58(5): 393-396.
[11] TAVANGAR R, MOLINA J M, WEBER L. Assessing predictive schemes for thermal conductivity against diamond-reinforced silver matrix composites at intermediate phase contrast[J]. Scripta Materialia, 2007, 56(5): 357-360.
[12] XUE C, YU J K, ZHU X M. Thermal properties of diamond/SiC/Al composites with high volume fractions[J]. Materials and Design, 2011, 32(8/9): 4225-4229.
[13] HUBER T, DEGISCHER H P, LEFRANC G, SCHMITT T. Thermal expansion studies on aluminum-matrix composites with different reinforcement architecture of SiC particles[J]. Composites Science and Technology, 2006, 66(13): 2206–2217.
[14] FENG H, YU J K, TAN W. Microstructure and thermal properties of diamond/aluminum composites with TiC coating on diamond particles[J]. Materials Chemistry and Physics, 2010, 124(1): 851-855.
[15] COLTTERS R G. Thermodynamics of binary metallic carbides: A review[J]. Materials Science and Engineering A, 1985, 76(1/2): 1-50.
[16] KENNEDY A R, WYATT S M. Characterising particle-matrix interfacial bonding in particulate Al-TiC MMCs produced by different methods[J]. Composites Part A: Applied Science and Manufacturing, 2001, 32(3/4): 555-559.
[17] KENNEDY A R, WESTON D P, JONES M I. Reaction in Al-TiC metal matrix composites[J]. Materials Science and Engineering A, 2001, 316(1/2): 32-38.
[18] QIN Y X, ZHANG D, LU W J, PAN W. Oxidation behavior of in situ synthesized (TiB+TiC)/Ti-Al composites[J]. Materials Letter, 2006, 60(19): 2339-2345.
[19] FLAQUER J, RIOS A, MARTIN A, NOGALES S, BOHM H. Effect of diamond shapes and associated thermal boundary resistance on thermal conductivity of diamond-based composites[J]. Computational Materials Science, 2007, 41(2): 156-163.
[20] VAIDYA R U, CHAWLA K K. Thermal expansion of metal matrix composites[J]. Composite Science and Technology, 1994, 50: 13-22.
(编辑 李艳红)
基金项目:国家自然科学基金资助项目(60776019)
收稿日期:2011-06-02;修订日期:2011-11-14
通信作者:于家康,教授,博士;电话:029-88494987;E-mail: jkyu@nwpu.edu.cn