Trans. Nonferrous Met. Soc. China 20(2010) s1022-s1028

AlTiN and AlTiON-coated hot work tool steels for tooling in steel thixoforming
Y. BIROL1, D. ISLER2
1. Materials Institute, Marmara Research Centre, Gebze, Kocaeli, Turkey;
2. Department of Metallurgy and Materials Engineering, Istanbul Technical University, Istanbul, Turkey
Received 13 May 2010; accepted 25 June 2010
Abstract:X32CrMoV33 hot work tool steel samples coated with AlTiN and AlTiON were submitted to thermal cycling under conditions that approximate thixoforming of steels and to sliding wear tests at 750 ℃, measured to be the cavity surface temperature shortly after the steel slurry is forced into the thixoforming die. AlTiN and AlTiON coatings provide adequate protection against oxidation of the tool steel substrate, but fail to avoid thermal fatigue cracking. This is attributed to the extensive softening of the substrate, the thermal expansion mismatch between the hot work tool steel and the coatings and residual compressive stresses inherited from the deposition process. The impact of AlTiN and AlTiON coatings on the high temperature wear resistance, on the other hand, is favourable. The improved wear resistance is attributed to the stable, protective surface oxide films.
Key words: thixoforming; physical vapor deposition; coating; tooling; steels; thermal fatigue; wear
1 Introduction
Thermal fatigue, wear and oxidation at elevated temperatures produce a very hostile environment which disapproves conventional hot work tool steels for tooling applications in semi-solid processing of steels[1-6]. Tooling materials superior to those available today are thus needed. Several replacements for conventional tool steels with superior performance have been identified in recent years[7-15]. However, cost considerations favour coating hot work tool steels over employing high temperature alloys for tooling applications. Such coatings must offer thermal and chemical stability as well as adequate resistance to thermal fatigue, oxidation and abrasion by the slurries. Thin hard coatings employed to reduce friction and wear of tools for cutting, forming and die casting processes deserve attention [16-21]. Physical vapor deposition (PVD) is employed to extend die life in metal processing since it is capable of depositing such coatings below the temper softening temperature of most common tool steels[22-25]. PVD coatings offer an attractive combination of high hardness, good wear resistance and chemical stability and have thus been widely employed on forming and cutting tools and to a relatively less extent in thixoforming tools for high temperature alloys in recent years[26-30]. AlTiN type PVD coatings are particularly identified for high temperature use owing to an excellent oxidation resistance[31-39]. The potential of AlTiN and AlTiON coatings deposited on X32CrMoV33 hot work tool steel via cathodic arc physical vapour deposition (CAPVD) process under steel thixoforming conditions was investigated in the present work.
2 Experimental
CAPVD process was employed to deposit AlTiN and AlTiON coatings on X32CrMoV33 hot work tool steel (Table 1), which was austenized at 1 025 ?C for 30 min, quenched in circulating air and finally tempered twice at 625 ?C for 2 h, yielding a hardness of HRC 45. The coating process parameters are listed in Table 2.
Table 1 Chemical composition of X32CrMoV33 hot work tool steel used as substrate (mass fraction, %)

The thermal fatigue test involved cyclic heating and cooling of coated prismatic tool steel samples (25 mm ×25 mm×20 mm) between 750 ?C and 450 ?C (Fig.1). These temperatures are the maximum and the minimum temperatures that the die cavity surface has to endure in steel thixoforming experiments. Only the front coated face of the samples was heated to establish the thermal gradients that prevail across the section of the die during steel thixoforming. The thermal fatigue tests are described in detail elsewhere [3].
Table 2 Parameters employed in CAPVD deposition of AlTiN and AlTiON coatings (CrN is bond coat)
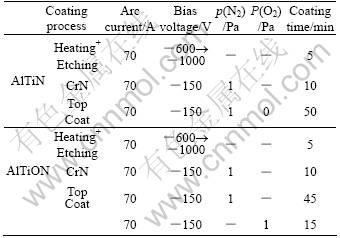
Wear properties of the coatings were evaluated with a commercial ball-on-disc type sliding wear tribometer. A 9.5mm diameter 440C stainless steel ball was used as the counterface, considering that the die material is worn out by solid a-Fe globules during the thixoforming of steel parts. Wear tests were carried out at 750 ?C with a sliding speed of 0.1 m/s, under 5 N load for 60 min. The disc surfaces were ground with 1000 grit sandpaper and were ultrasonically cleaned in acetone and dried before each test. Morphology of the wear track after each sliding experiment was investigated with a 3D profiling system, an optical and a scanning electron microscope. Both thermal fatigue and wear tests were repeated in exactly the same fashion with uncoated tool steel samples to identify the impact of AlTiN and AlTiON coatings on the thermal fatigue performance of X32CrMoV33 tool steel.
Fig.1 Thermal fatigue test set-up: (a) heating; (b) cooling cycle
3 Results and discussion
AlTiN and AlTiON coatings revealed two- and three-layer architectures, respectively, with an inner CrN layer which serves to improve adhesion of the coatings to the substrate. The thickness and hardness of the coatings are listed in Table 3. Oxygen in the AlTiON coating evidently played a softening role as reported for other transition metal oxy-nitride coatings[40-42]. Both coatings maintain the same NaCl structure with a fraction of the Ti atoms substituted by Al atoms[43].
Table 3 Thickness and hardness values of AlTiN and AlTiON coatings

The typical temperature vs time curves for AlTiN and AlTiON-coated and uncoated X32CrMoV33 samples are shown in Fig.2. The rear face temperature in the coated samples seems to have been slightly reduced, implying a barrier effect of the AlTiN and AlTiON coatings on heat transfer. This effect is believed to be due to the relatively lower thermal conductivity of the PVD coatings and is very small as both AlTiN and AlTiON coatings are very thin.
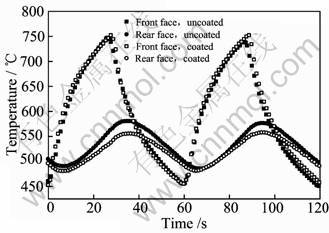
Fig.2 Change in temperature with time at front and rear faces of AlTiN-coated and uncoated hot work tool steel samples
The surface of the hot work tool steel deteriorated very rapidly as soon as thermal cycling started. Thick oxide scales were produced at the front face of the X32CrMoV33 hot work tool steel, which eventually started to spall off upon continued thermal cycling, due to a thermal expansion mismatch (Fig.3). The surface damage thus introduced facilitated crack initiation. The damage features noted in the X32CrMoV33 tool steel sample were clearly absent in the AlTiN and AlTiON coatings. Both coatings retained their integrity for at least 300 cycles. The contrast change after 300 cycles was taken to imply Al2O3 formation. Blisters and small scores-streaks, running more or less parallel to each other, were noted upon further thermal cycling. Finally, small cracks were noted after 425 and 768 cycles in AlTiN and AlTiON coatings, respectively (Fig.3). The thermal fatigue tests of the coated samples were terminated at this point in spite of a superior surface quality with respect to the uncoated tool steel samples. It is hard, in view of the foregoing, to claim an improvement in the thermal fatigue performance of tool steel when coated with AlTiN and AlTiON.
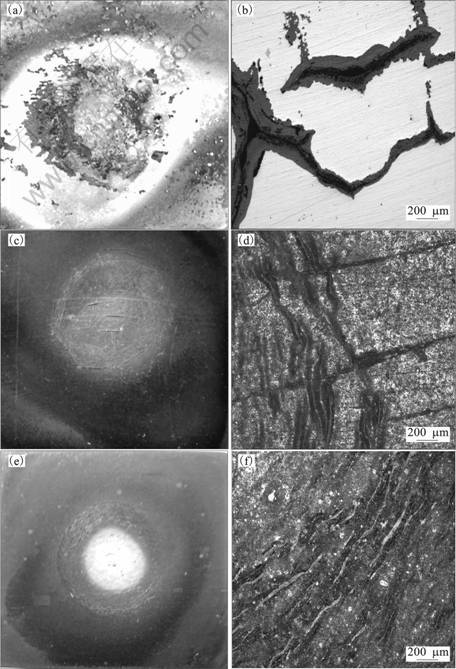
Fig.3 General view of front faces (a, c, e) and thermal fatigue cracks on front faces (b, d, f) of X32CrMoV33 steel (a, b), AlTiN- (c, d) and AlTiON-coated (e, f) samples after 1500, 425 and 768 cycles, respectively (Fig.3(b) shows a metallo-graphically polished section approximately 1 mm from front face)
The poor thermal fatigue performance of AlTiN and AlTiON coatings under steel thixoforming conditions can be attributed to a number of factors. The stresses produced by the thermal expansion mismatch between the hot work tool steel and the nitride and oxy-nitride coatings are believed to play a key role. The CAPVD process is known to cause high compressive stresses in coatings due to its high ionisation rate and bias voltage applied to the substrate. High compressive stresses reduced the adhesive strength of the coating on the substrate, produced blistering and eventually led to spalling[29]. Micro-cracking was thus inevitable with increasing number of thermal cycles. The integrity of the coatings might have also been impaired due to a lack of sufficient substrate support as suggested in Refs.[16, 44-46]. The hardness of the front face of the uncoated steel sample, which was HV 442 before the thermal fatigue test, dropped to approximately HV 275 after only 400 cycles[3]. This situation was aggravated further when the tool steel substrate underwent further softening with increasing number of thermal cycles.
Two- and three-dimensional topographies of the tested surfaces are illustrated in Fig.4. Abrasive wear with deep grooves along the sliding direction, a very thick oxide layer and an appreciable quantity of debris accumulated at the edges of the track are the typical features of the hot work tool steel submitted to wear test at 750 ℃. A nearly 40
deep wear track and a volume loss of 5.8×10-12 m3, occurred in the hot work tool steel. Oxide build up on the disc surface was confirmed by EDS analysis which showed a high and uniform level of oxygen across the wear track(Fig.5). The surface oxides were shown by XRD to be Fe2O3 and Fe3O4. Oxidation, fresh surface generation via fracture and removal of the surface oxides inside the wear track and re-oxidation of the fresh surface are responsible for the substantial wear loss suffered by the hot work tool steel. Wear resistance of the X32CrMoV33 tool steel is impaired at high temperatures also via loss of mechanical strength. X32CrMoV33 tool steel disc sample responded to thermal exposure at 750 ?C with a sharp hardness drop, from over HV 450 to below HV 250 within 1 h.
The sliding wear conditions which produced a deep wear scar on the surface of the tool steel, hardly made an impression on the AlTiN and AlTiON coatings (Figs. 4-6). The wear track features of the AlTiN and AlTiON coatings suggest that the steel ball was smeared onto the PVD coatings rather than digging them as evidenced by the EDS analysis of the wear tracks which were found to contain as much as 1.79% and 0.94% Fe(mass fraction) for the AlTiN and AlTiON coatings, respectively (Fig.5). This is typical of adhesive wear and is likely to occur when a relatively soft ball is rubbed against a much harder surface[47]. AlTiN and AlTiON coatings are indeed much harder than the steel ball which softens further upon thermal exposure during the test, promoting the adhesive wear conditions.
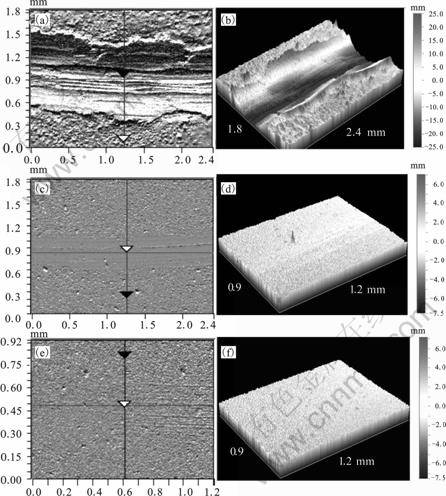
Fig.4 2- and 3-D topographies of tested surfaces of hot work tool steel (a, b), AlTiN (c, d) and AlTiON-coated (e, f) disc samples submitted to sliding wear test at 750℃

Fig.5 SEM micrographs and EDS analysis (mass fraction) inside (1) and outside (2) of wear tracks of hot work tool steel (a), AlTiN- (b) and AlTiON-coated (c) wear test samples
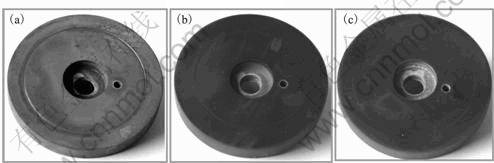
Fig.6 Hot work tool steel (a), AlTiN-(b) and AlTiON-coated (c) disc samples submitted to wear test at 750 ℃
The EDS analysis of the AlTiN- and AlTiON-coated samples revealed an increase in the oxygen content inside the wear track (Fig.5). Al- and Ti-based oxides are believed to have formed at the test temperature owing to the high affinity of Al and Ti to oxygen, as reported in Refs.[48-49]. The debris originating from the steel ball is also believed to have oxidized under the present conditions. The oxy-nitride coating is more resistant to oxidation as it was obtained by the intentional oxidation of an AlTiN coating and is thus somewhat saturated with oxygen. The higher resistance to oxidation provided a higher resistance to sliding wear. The AlTiON coating is thus judged to be the better of the two highly wear-resistant coatings. The smooth wear track features suggest high debris removal efficiency for both coatings with the debris easily being removed from the contact surface.
4 Conclusions
AlTiN and AlTiON coatings provide adequate protection against oxidation of the hot work tool steel samples, but fail to avoid thermal fatigue cracking. Extensive softening of the substrate, thermal expansion mismatch between the hot work tool steel and the nitride and oxy-nitride coatings, compressive residual stresses inherited from the CAPVD process are held responsible. The stable and protective oxide surface layer on AlTiN and AlTiON coatings provide an enhanced resistance to high temperature wear. The latter is relatively more resistant to oxidation and is thus the better of the two coatings tested in the present work. It is fair to conclude that coating solutions for steel thixoforming tools must involve duplex coatings via plasma nitriding followed by physical vapour deposition. The plasma nitride of sufficient thickness is expected to provide the required substrate hardness and thus the substrate support which is clearly absent when thin hard coatings are applied directly on tool steel samples. The tool steel substrate is relatively softer and softens further upon thermal cycling at steel thixoforming temperatures and risks the integrity of the PVD coating.
Acknowledgements
F. ALAGEYIK and O. CAKIR are thanked for their help in the experiments. Prof. M. URGEN is thanked for the provision of the laboratory facilities at ITU. This work was funded by TUBITAK.
References
[1] MUENSTARMAN S, UIBEL K, TONNESEN T, TELLE R. Development of a self-heating ceramic tool for the thixoextrusion of high melting point alloys [J]. Solid State Phenomena, 2006, 116/117: 696-699.
[2] LUGSCHEIDER E, BOBZIN K, BARIMANI C, BARWULF St, HORNIG Th. PVD hard coatings protecting the surface of thixoforming tools [J].Adv Eng Mater, 2000, 2: 33-37.
[3] BIROL Y. Thermal fatigue testing of Inconel 617 and Stellite 6 alloys as tooling materials for thixoforming of steels [J]. Mater Sci Eng A, 2010, 527: 1938-1945.
[4] BIROL Y. Response to thermal cycling of tool materials under steel thixoforming conditions [J]. Ironmak Steelmak, 2010, 37: 41-46.
[5] OMAR M Z, PALMIERE E J, HOWE A A, ATKINSON H V, KAPRANOS P. Thixoforming of a high performance HP9/4/30 steel [J]. Mater Sci Eng A, 2005, 395: 53-61.
[6] TELLE R, MUENSTERMANN S, BEYER C. Design, construction and performance of silicon nitride tool parts in steel thixoforming [J]. Solid State Phenomena, 2006, 116/117: 690-695.
[7] BIROL Y. A CrNiCo alloy as a potential tool material in semi-solid Processing of Steels [J]. Steel Res Int, 2009, 80: 165-171.
[8] BIROL Y. Thermal fatigue testing of tooling materials for semi-solid processing of steels [J]. Steel Res Int, 2009, 80: 588-592.
[9] BIROL Y. Ni-based superalloy as a potential tool material for thixoforming of steels [J]. Ironmak Steelmak, 2009, 36: 555-560.
[10] KAPRANOS P, KIRKWOOD D H, SELLARS C M. Semi-solid processing of aluminium and high melting point alloys [J]. J Eng Manuf, 1993, 207B: 1-8.
[11] BIROL Y. The use of CrNiCo-based superalloy as die material in semi-solid processing of steels [J]. Solid State Phenomena, 2008, 141/142/143: 289-294.
[12] RILEY F L. Silicon nitride and related materials [J]. Journal of the American Ceramic Society, 2000, 83: 245-265.
[13] BIROL Y. Effect of bulk die temperature on die cavity surface strains in thixoforming of steels [J]. Ironmak Steelmak, 2009, 36: 397-400.
[14] BIROL Y. Response to thermal cycling of tool materials under steel thixoforming conditions [J]. Ironmak Steelmak, 2010, 37: 41-46.
[15] BIROL Y. Testing of a novel CrNiCo alloy for tooling applications in semi-solid processing of steels [J]. Int J Mater Form, 2010, 3: 65-70.
[16] DOBRZANSKI L A, POLOK M, ADAMIAK M. Structure and properties of wear resistance PVD coatings deposited onto X37CrMoV5-1 type hot work steel [J]. J Mater Process Tech, 2005, 164/165: 843-849.
[17] HARRY E, IGNAT M, PAULEAU Y, ROUZAUD A, JULIET P. Mechanical behaviour of hard PVD multilayered coatings [J]. Surf Coat Tech, 2000, 125: 185-189.
[18] LEE S Y, KIM G S, HAHN J H. Effect of the Cr content on the mechanical properties of nanostructured TiN/CrN coatings [J]. Surf Coat Tech, 2004, 177/178: 426-433.
[19] BJORK T, WESTERGARD R, HOGMARK S, BERGSTROM J, HEDENGVIST P. Physical vapour deposition duplex coatings for aluminium extrusion dies [J]. Wear, 1999, 225/229: 1123-1130.
[20] NAVINSEK B, PANJAN P, URANIAN I, CVAHTE P, GORENJAK F. Improvement of hot-working processes with PVD coatings and duplex treatment [J]. Surf Coat Tech, 2001, 142/143/144: 1148-1154.
[21] AHN S H, LEE J H, KIM J G, HAN J G. Localized corrosion mechanisms of the multilayered coatings related to growth defects [J]. Surf Coat Tech, 2004, 177/178: 638-644.
[22] KNOTEK O, LOFFLER F, BOSSERHOFF B. PVD coatings for diecasting moulds [J]. Surf Coat Tech, 1993, 62: 630-634.
[23] SRIVASTAVA A, JOSHI V, SHIVPURI R, BHATTACHARYA R, DIXIT S. A multilayer coating architecture to reduce heat checking of die surfaces [J]. Surf Coat Tech, 2003, 163/164: 631-636.
[24] WANG Y. A study of PVD coatings and die materials for extended die-casting die life [J]. Surf Coat Tech, 1997, 94/95: 60-63.
[25] ROSSO M, UGUES D, TORRES E, PERUCCA M, KAPRANOS P. Performance enhancements of die casting tools through PVD nano-coatings [J]. Int J Mater Forming, 2008, 1: 1259-1262.
[26] HARRIS S G, DOYLE E D, VLASVELD A C, AUDY J, QUICK D. A study of the wear mechanisms of Ti1-xAlxN and Ti1-x-yAlxCryN coated high-speed steel twist drills under dry machining conditions [J]. Wear, 2003, 254: 723-734.
[27] PALDEY S, DEEVI S C. Single layer and multilayer wear resistant coatings of (Ti,Al)N: A review [J]. Mater Sci Eng A, 2003, 342: 58-79.
[28] LEE S Y, LEE S Y. Application of PVD coatings for improvement of die performance in copper semi-solid processing [J]. Solid State Phenomena, 2006, 116/117: 64-87.
[29] LUGSCHEIDER E, BOBZIN K, HORNIG Th, MAES M. Investigation of the residual stresses and mechanical properties of (Cr,Al)N arc PVD coatings used for semi-solid metal (SSM) forming dies [J]. Thin Solid Films, 2002, 420/421: 318-323.
[30] BOBZIN K, BAGCIYAN N, IMMICH P. Deposition of oxides as tool protection for large thixoforming dies by using the pulsed MSIP-PVD process [J]. Solid State Phenomena, 2008, 141/142/143: 249-254.
[31] YOON S Y, KIM J K, KIM K H. A comparative study on tribological behavior of TiN and TiAlN coatings prepared by arc ion plating technique [J]. Surf Coat Tech, 2002, 161: 237-242.
[32] MO J L, ZHU M H. Tribological oxidation of PVD hard coatings[ J]. Tribol Int, 2009, 42: 1758-1764.
[33] STAIA M H, D’ALESSANDRIA M D, QUINTO D T, ROUDET F ASTORT M. High temperature tribological characterization of commercial TiAlN coatings [J]. J Phys: Condens Matter, 2006, 18: 1727-1736.
[34] RODRIGUEZ-BARACALDO R, BENITO J A, PUCHI- CABRERA E S, STAIA M H. High temperature wear resistance of (TiAl)N PVD coating on untreated and gas nitrided AISI H13 steel with different heat treatments [J]. Wear, 2007, 262: 380-389.
[35] DOBRZANSKI L A, POLOK M, PANJAN P, BUGLIOSI S, ADAMIAK M. Improvement of wear resistance of hot work steels by PVD coatings deposition [J]. J Mater Process Technol, 2004, 155/156: 1995-2001.
[36] MUNZ W D. Titanium aluminum nitride films—A new alternative to TiN films[J]. J Vac Sci Technol, 1986, A4: 2717-2725.
[37] KAWATE M, HASHIMOTO A K, SUZUKI T. Oxidation resistance of Cr1-xAlxN and Ti1-xAlxN films [J]. Surf Coat Tech, 2003, 165: 163-167.
[38] ENDRINO J L, FOX-RABINOVICH G S, GEY C. Hard AAlTiN, AlCrN PVD coatings for machining of austenitic stainless steel J]. Surf Coat Tech, 2006, 200: 6840-6845.
[39] FOX-RABINOVICH G S, BEAKE B D, ENDRINO J L, VELDHUIS S C, PARKINSON R, SHUSTER L S. Effect of mechanical properties measured at room and elevated temperatures on the wear resistance of cutting tools with TiAlN and AlCrN coatings [J]. Surf Coat Tech 2006, 200: 5738-5742.
[40] SJOLEN J, KARLSSON L, BRAUN S, MURDEY R, HORLING A, HULTMAN L. Structure and mechanical properties of arc evaporated Ti-Al-O-N thin films [J]. Surf Coat Tech, 2007, 201: 6392-6403.
[41] URGEN M, EZIRMIK V, SENEL E, KAHRAMAN Z, KAZMANLI K. The effect of oxygen content on the temperature dependent tribological behavior of Cr-O-N coatings [J]. Surf Coat Tech, 2009, 203: 2272-2277.
[42] ISLER D, BIROL Y, URGEN M. PVD coated hot work tool steels for tooling applications in semi-solid processing of steels [J]. Int J Mater Formin, 2010,3 (suppl): 745-750. doi: 10.007/s/2289- 010-0878-x.
[43] KNOTEK O, LEYENDECKERS T. On the structure of (Ti, Al) NPVD coatings [J]. J Solid State Chem, 1987, 70: 318-322.
[44] LUGSCHEIDER E, BOBZIN K, HORNIG Th, MAES M. Proc. 6th International Tooling Conference. Karlstad, Sweden, 2002: 979-990.
[45] LESKOVSEK V, PODGORNIK B, JENKO M. A PACVD duplex coating for hot-forging applications [J]. Wear, 2009, 266: 453-460.
[46] STARLING C M D, BRANCO J R T. Thermal fatigue of hot work tool steel with hard coatings [J]. Thin Solid Films, 1997, 308/309: 436-442.
[47] WILSON S, ALPAS A T. Tribo-layer formation during sliding wear of TiN coatings [J]. Wear, 2000, 245: 223-229.
[48] REBOUTA L, VAZ F, ANDRITSCHKY M, da SILVA M F, Oxidation resistance of (Ti,AlZr,Si)N coatings in air [J]. Surf Coat Tech, 1995, 76/77: 70-74.
[49] MCINTYRE D, GREENE J E, HAKANSSON G, SUNDGREN J E, MUNZ W D. Oxidation of metastable single-phase polycrystalline Ti0.5Al0.5N films: Kinetics and mechanisms [J]. J Appl Phys, 1990, 67: 1542-1553.
(Edited by YUAN Sai-qian)
Corresponding author: Y. BIROL; Tel: +90-262-6773084; E-mail: yucel.birol@mam.gov.tr