
Formation of composites fabricated by exothermic dispersion reaction in Al-TiO2-B2O3 system
ZHU He-guo(朱和国)1, WANG Heng-zhi(王恒志)1, GE Liang-qi(葛良琦)1,
CHEN Shi(陈 湜)1, WU Shen-qing(吴申庆)2
1. Department of Materials Science and Engineering, Nanjing University of Science and Technology,
Nanjing 210094, China;
2. Department of Materials Science and Engineering, Southeast University, Nanjing 210096, China
Received 29 May 2006; accepted 22 January 2007
Abstract: The formation of aluminum matrix composites fabricated by exothermic dispersion reaction in Al-TiO2-B2O3 system was investigated. The thermal analysis results show that the reactions are spontaneous and exothermic. The Gibbs free energy of α-Al2O3 is the lowest among all the combustion products, followed by TiB2 and Al3Ti. It is noted that when the B2O3/TiO2 mole ratio is below 1, the reaction products are composed of particle-like α-Al2O3, TiB2 and rod-like Al3Ti. The α-Al2O3 crystallites, resulting from the reaction between Al and TiO2 or B2O3, are segregated at the grain boundaries due to a lower wettability with the matrix. SEM micrographs show that rod-like Al3Ti phase distributes uniformly in the matrix. When the B2O3/TiO2 mole ratio is around 1, the Al3Ti phase almost disappears in the composites, and the distribution of α-Al2O3 particulates is improved evidently.
Key words: aluminum matrix composite; reaction mechanism; mole ratio; exothermic dispersion reaction
1 Introduction
In situ synthesis techniques are derived from the self-propagating combustion, which is used for fabricating metal or ceramic matrix composites. As the reinforcements are generated directly from chemical reaction within the matrix, the composites are of many excellent advantages, such as clean reinforcement-matrix interface, fine and thermodynamically stable reinforcements, good compatibility and high bond strength between reinforcements and the matrix, and low fabrication costs. It is eventual and critical to select a suitable reaction system and corresponded reaction method. There are several methods reported previously, such as self-propagating high temperature synthesis (SHS), direct metal oxidation method (DIMOX), exothermic dispersion(XD), mechanical alloying(MA), and pressureless metal infiltration(PRRIMX)[1-3]. Recently, the XD method has been focused extensively for it can produce fine ceramic particles (<1 mm) and the volume frication of the reinforcement can vary in a wide range. Among these reinforcements, titanium diboride (TiB2) is compatible with aluminum matrix, and does not react with aluminum. In this case, it provides a method to avoid the formation of brittle products at the particles/matrix interface, which improves the interface bonding strength. Furthermore, TiB2 exhibits very high stiffness and hardness. Considering such excellent characteristics, TiB2 phase has been used increasingly as reinforcements in aluminum-based metal matrix composites(MMCs)[4-5].
Researchers have chosen the reaction systems like Al-Ti, Al-B, Al-Ti-C, Al-Ti-B and Al-Zr-O[6-10], for the fabrication of Al-based MMCs. To decrease the processing cost, the Ti and B were substituted with the compounds of TiO2 and B2O3 respectively. Therefore, the Al-TiO2-B2O3, Al-TiO2-B and Al-TiO2-C reaction systems were highlighted recently. This work aims to investigate the formation of Al2O3, Al3Ti and TiB2 in the Al-based MMCs fabricated by XD method in Al-TiO2-B2O3 system.
2 Experimental
The titanium dioxide TiO2 powder (98% purity, manufactured by Guangdong Guanghua Chemistry Factory Co., Ltd., Guangdong, China), and pure aluminum Al powder (99.6% puring, supplied by Shanghai Refined Chemistry Industry Science & Technology Co., Ltd. Shanghai, China), and Boric oxide B2O3 powder (98.0% purity, made by Shanghai Tongya Refined Chemistry Industry Factory, Shanghai, China) with an average size of 3-5 mm, 30-50 mm and 20-30 mm, respectively, were used as raw materials. According to stoichiometric calculation, the mixed powders with 30% (volume fraction) reinforcements whose B2O3/TiO2 mole ratios were 0, 0.5 and 1.0 respectively were mixed by a ball-milling in the stainless steel vacuum jar for 2 h, and then cold compacted into green billets with a diameter of 30 mm. When the compacts were heated in vacuum furnace one by one at about 1 073 K, the combustion reaction occurred and held for about 10 min, and then the combusted compacts were cooled down to room temperature in the furnace. The three samples A (r(B2O3/TiO2)=0), B (r(B2O3/TiO2)=0.5) and C (r(B2O3/TiO2)=1) made from the reacted compacts were mechanically polished and then investigated by X-ray diffraction(XRD), scanning electron microscope(SEM) and energy dispersive spectrum(EDS).
3 Result and discussion
3.1 Thermodynamic analysis
When the temperature of furnace is increased to about 1 073 K, the B2O3 and Al powders in the compact are melted firstly, and then Al-TiO2 liquid-solid and Al-B2O3 liquid-liquid interfaces are formed. The reactions occur as follows:
The above reactions are exothermic and their theoretical combustion temperature can be calculated by the following formula:

where T is the preheating temperature; Tad is the theoretic combustion temperature, n is the amount of substance, p is the products and R is the reactants.
The Tad of the reactions (1) and (2) is 2 036 K and 2 213 K if not considering the aluminum matrix absorb- ing thermal. In fact, the Tad of the reactions are 1 856 K and 2 045 K respectively which are lower than the previous figures. Therefore, the Tad of the reactions (1) and (2) are all higher than the critical temperature 1 800 K that makes the combustion self- maintained. Due to the above reactions, an Al-Ti-B-α-Al2O3 reaction system is formed. Because the α-Al2O3 phase is very steady due to its low Gibbs free energy, the Al-Ti-B-α-Al2O3 quaternary system is equal to Al-Ti-B ternary system and the following reactions (3)-(8) are likely to occur in the compact:
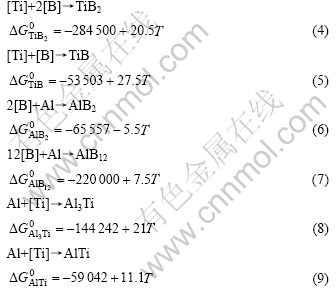
Fig.1 shows the curves of the Gibbs free energy vs temperature of the above reactions. It is indicated that all the reactions can take place spontaneously due to their negative
. It is also indicated that the stability of these products is in the following order: α-Al2O3> TiB2>AlB12>Al3Ti>TiB>AlB2>TiAl. As shown in the Al-Ti phase diagram (see Fig.2), it can be inferred that Al and Ti can form many different kinds of products. But when the content of Ti is less than 36.5% (mass fraction) in the aluminum matrix, Ti will react with Al to form Al3Ti. In this experiment, the content of Ti is much less than 36.5% (mass fraction), therefore, Al3Ti is formed.
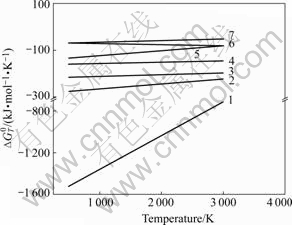
Fig.1 Gibbs free energies of possible combustion products vs temperature in Al-TiO2- B2O3 system: 1 Al2O3; 2 TiB2; 3 AlB12; 4 TiB; 5 Ti3Ti; 6 AlTi; 7 AlB2
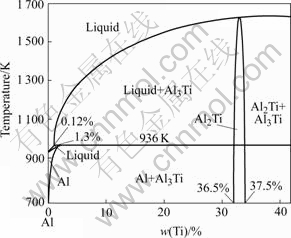
Fig.2 Al-Ti binary phase diagram
In the Al-TiO2-B2O3 system, the reaction equations vary with the B2O3/TiO2 mole ratios as follows:
When r(B2O3/TiO2)=0,
13Al+3TiO2→2α-Al2O3+3Al3Ti;
When r(B2O3/TiO2)=0.5,
23Al+6TiO2+3B2O3→7α-Al2O3+3Al3Ti+3TiB2;
When r(B2O3/TiO2)=1,
10Al+3TiO2+3B2O3→5α-Al2O3+3TiB2
From the above thermodynamic analysis, it can be concluded that when the B2O3/TiO2 mole ratio is 0, the combustion results are composed of α-Al2O3 and Al3Ti. With the increase of B2O3/TiO2 mole ratio, the amount of Al3Ti phase will decrease, and finally as the B2O3/TiO2 mole ratio increases to 1, the Al3Ti phase will disappear.
3.2 Results and analysis
Fig.3(a) displays that the reaction products in sample A are composed of fine particles and rod-like phase, and Fig.3(b) shows that the reaction products are α-Al2O3 and Al3Ti. Figs.3(c) and (d) are their EDS patterns for the rod-like phase and the particle, respectively, which confirm that the rod-like phase is Al3Ti and the particle is α-Al2O3. Each of Al3Ti phase can act as an nuclei in the matrix during the solidification due to its good orientation relationships within aluminum matrix [11]: <110>
//<110>{111}Al; <210>
//<110>{111}Al. The preferential growing direction of the Al3Ti is <110>[12], and then it grows into rod-like of several tens microns in length.
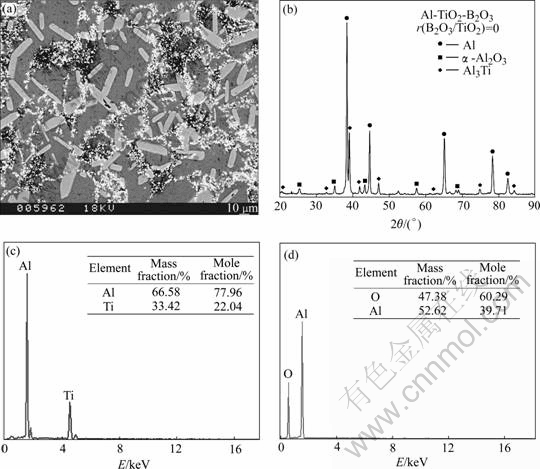
Fig.3 SEM micrograph (a) and XRD pattern (b) of produced sample A as well as EDS patterns (c, d) of rod-like phase and particle, respectively
Owing to the small fraction of Al3Ti phase, it is hard to refine the matrix considerably. The α-Al2O3 particles are formed directly from reactions (1) and (2). They segregated on the grain boundaries because of the following three reasons: 1) the size of α-Al2O3 particles is 2-3 mm and it is difficult for the α-Al2O3 particles to enter the matrix during the solidification; 2) the viscosity of matrix increases quickly due to the reaction temperature decreasing rapidly after combustion; 3) the low wettability between the α-Al2O3 and aluminum matrix. The needed outer work for the α-Al2O3 particles entering into matrix is reported previously as[13]

where W is the outer work; fP is the particle volume fraction; R is the particle radius; σlg is the liquid-solid interface energy; θ is the wetting angle. Here θ is 118? [14], therefore W of α-Al2O3 particles is very high, which makes α-Al2O3 particles hard to enter into Al matrix.
As adding B2O3 powders, B2O3 powders will be melt at the temperature of 633 K and then enter into the aluminum powders by the capillary force. Reaction (2) will occur at the temperature of about 1 000 K and produce active B atoms. Then the active B will react with active Ti atoms produced by reaction (1) to form TiB2 particles. When the B2O3/TiO2 mole ratio is 0.5(sample B), the SEM micrograph of the combustion results indicates that the amount of Al3Ti sticks decreases, as shown in Fig.4(a), which is consistent with the XRD result in Fig.4(c). When the B2O3/TiO2 mole ratio is 1 (sample C), the Al3Ti phase disappears, as shown in Fig.4(b), and the corresponding XRD spectrum in Fig.4(d) also shows that there is no diffraction peaks of Al3Ti, which is in agreement with the conclusion of above thermodynamic analysis.
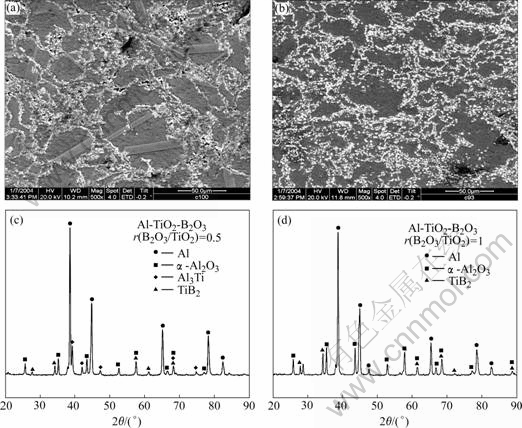
Fig.4 SEM micrographs and XRD patterns of reaction products: (a), (c) Sample A; (b), (d) Sample B
In the Al-TiO2-B reaction system, YANG et al[15] suggested that B powder can be combined directly with liquid Al to form AlB12, and then AlB12 is decomposed as following equation: AlB12→12[B]+Al, to form active B and Al. At the same time, TiO2 powder reacts with Al to produce active Ti. The active B atoms react with Ti atoms to form TiB2. But in the Al-TiO2-B2O3 reaction system, Al reacts with TiO2 and B2O3 respectively to form active B and active Ti, then the active Ti will be combined with the active B to form thermodynamically steady phase TiB2, and there are no intermediate phases AlB12. When the B2O3/TiO2 mole ratio is below 1, the active Ti atoms are excess in the reaction, and then the remained Ti atoms will react with Al to form Al3Ti. With the increase of B2O3/TiO2 mole ratio, the amount of remained Ti atoms decreases. And when the B2O3/TiO2 mole ratio is 1, there is no remained Ti atom to combine with Al to form Al3Ti. Therefore the reaction route in the Al-TiO2-B2O3 system can be shown as follows:
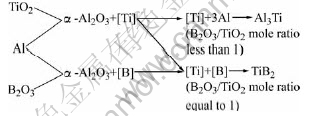
It can be noted that the SEM micrographs of Al3Ti and the reaction process of TiB2 in the Al-TiO2-B2O3 are different from those in the Al-TiO2-B system. In the Al-TiO2-B system, when the B/TiO2 mole ratio is less than 2, the products consist of α-Al2O3, Al3Ti and TiB2, and firstly B will react with Al to form Al12B and then Al12B will decompose to produce active B. The active B will diffuse to the surfaces of Al3Ti and react with Al3Ti to form TiB2, whereas the active B is not enough to reduce all the Al3Ti. Therefore, the surfaces of the remained Al3Ti are not smooth[13]. When the B/TiO2 mole ratio is increased to 2, the Al3Ti sticks are reduced entirely and no Al3Ti is observed in the results. According to the previous analysis, the formation time of TiB2 is later than that of Al3Ti, and the surfaces of the remained Al3Ti are not smooth in the Al-TiO2-B system. However, in the Al-TiO2-B2O3 system, Al can react with TiO2 and B2O3 simultaneously, and then produce active Ti and active B atoms in the matrix. Therefore they can form TiB2 directly by diffusion. When the B2O3/TiO2 mole ratio is below 1, the remained Ti atoms will react with Al to form Al3Ti phase, which is smooth surface as shown in Fig.4(a). Therefore, the formation time of TiB2 is prior to that of Al3Ti, and the surfaces of the remained Al3Ti are smooth in the Al-TiO2-B2O3 system.
4 Conclusions
1) In the Al-TiO2-B2O3 reaction system, when the B2O3/TiO2 mole ratio is below 1, the combustion results are composed of α-Al2O3, TiB2 and Al3Ti. The α-Al2O3 phase is the most stable due to its lowest Gibbs free energy in the products.
2) The α-Al2O3 particles can not enter Al-based grains and segregate in the matrix grain boundaries. The Al3Ti phase distributes uniformly in the matrix. The TiB2 particles are compatible with the matrix and can become the nuclei of the matrix during the solidification, and as a result, the matrix grains can be refined with uniform distribution of the α-Al2O3 particles in the matrix.
3) As the B2O3/TiO2 mole ratio increases, the fraction of Al3Ti will decrease, and if the ratio reaches 1, the Al3Ti phase disappears in the composites.
4) In the Al-TiO2-B2O3 reaction system, the active Ti and B produced by reactions (1) and (2) respectively can form TiB2 directly by diffusion. When the B2O3/TiO2 mole ratio is less than 1, there are still some active Ti atoms remained, and then these active Ti atoms will react with Al to form Al3Ti phases whose surfaces are smooth.
References
[1] MERZHANOV A G. Review paper: History and recent development in SHS [J]. Ceramic International, 1995, 21: 371-379.
[2] TIONG S C, MA Z Y. Microstructural and mechanical characteristic of in situ metal matrix composites [J]. Materials Science and Engineering, 2000, 29: 49-113.
[3] WEN G, LI S B , ZHANG B S, GUO Z X. Reaction synthesis of TiB2-TiC composites with enhanced toughness [J]. Acta Mater, 2001, 49: 1463-1470.
[4] LIU Y H, YIN S, GUO Z M, LAI H Y. Aluminum boride in the combustion synthesis of alumina/boride composite [J]. Journal of Materials Research. 1998, 13(7): 1749-1752.
[5] MEYERS M A, OLEVSKY E A, MA J, JAMET M. Combustion synthesis/densification of an Al2O3-TiB2 composite [J]. Materials Science and Engineering A, 2001, 311: 83-99.
[6] ISIL K. Production of TiC reinforced aluminum composite with the addition of elemental carbon [J]. Materials Letters, 2005, 59: 3795-3800.
[7] LI H, SRIHARAN T, LAM Y M, LENG N Y. Effects of processing parameters on the performance of the Al grain refinement master alloys Al-Ti and Al-B in small ingot [J]. Journal of Materials Processing Technology, 1997, 66: 253-257.
[8] NASSIK M, CHRIFI-ALAOUI F Z, MAHDOUK K, GACHCN J C. Calorimetric study of the aluminum-titanium system [J]. Journal of Alloys and Compounds, 2003, 350: 151-154.
[9] EMAMY M, MAHTA M, RASIZADEH J. Formation of TiB2 particles during dissolution of Al3Ti in Al-TiB2 metal matrix composites using an in situ technique [J]. Composites Science and Technology, 2006, 26: 1063-1066.
[10] ZHAO Y T, DAI Q X, CHEN X N. Microstructure characterization of reinforcements in in situ synthesized compound of Al-Zr-O system [J]. Trans Nonferrous Met Soc China, 2005, 15(1): 109-112.
[11] MARKE E, DAVID S. Grain refinement of aluminum alloys (Part 1): The nucleant and solute paradigms [J]. Metallurgical and Materials Transactions A, 1999, 30(6): 1613-1623.
[12] MOORE J. Review self-propagating high-temperature combustion synthesis of powder compacted materials [J]. Journal of Materials Science, 1990, 25: 1159-1168.
[13] STEFANESCU D M, DHINDAW B K, KACAR S A, MOITRA A. Behavior of ceramic particles at the solid-liquid metal interface in metal matrix composites [J]. Metallurgical Transaction A, 1992, 23: 2847-2855.
[14] KSIAZEK M, SOBCZAK N, MIKULOWSKI B, RADZIWILL W, SUROWIAK I. Wetting and bonding strength in Al/Al2O3 system [J]. Materials Science and Engineering A, 2002, 324: 162-167.
[15] YANG B, WANG Y Q, ZHOU B L. The mechanism of formation of TiB2 particles prepared by in situ reaction in molten aluminum [J]. Metallurgical and Materials Transactions B, 1998, 29: 635-640.
Foundation item: Project(BK2006207) supported by the Natural Science Foundation of Jiangsu Province, China
Corresponding author: ZHU He-guo; Tel: +86-25-84315979; E-mail: zhg1200@sina.com
(Edited by YUAN Sai-qian)