
Rapid electroplating of Cu coatings by mechanical attrition method
NING Zhao-hui(宁朝晖), HE Ye-dong(何业东)
Beijing Key Laboratory for Corrosion, Erosion and Surface Technology,
University of Science and Technology Beijing, 100083 Beijing, China
Received 20 November 2007; accepted 12 June 2008
Abstract: The compact Cu coating with smooth surface and refined grain was prepared at high current density by mechanical attrition enhanced electroplating(MAEE) process. The mechanical attrition(MA) action was supplied by the vertical movement of glass balls on the sample surface with a special vibrating frequency. The plating bath was CuSO4 and H2SO4. It is demonstrated from field emission scanning electron microscopy(FESEM) results that the new coating shows smooth and refined surface morphology in high speed MAEE process. The further studies show that the spherical grain or pillar-shape grain can be obtained by traditional electroplating process at the current density of 200-600 mA/cm2. And the coatings are loosen, porous and easy to brush off. The pyramid-shape grain with diameter of less than 1 μm was obtained by MAEE process under the same condition. And the coatings are compact and pore-free. The rapid electroplating process can be obtained by MA action.
Key words: mechanical attrition; electroplating; Cu coating
1 Introduction
The Cu coating was widely used as pre-treatment and intermediate coating for its good corrosion resistance and anticarburizing performance. Much attention has been paid to high speed plating for a long time. A high speed plating process with mechanical action was reported in 1970s[1-4]. In this process, hard particles with porosity were contracted on the cathode surface. It was suggested that the high porosity of the coatings could allow the access of electrolyte to the electrode surface. Consequently, the thickness of the depletion layer decreased and the plating speed increased. However, this technique was generally not successful because the deposit was severely damaged and in some cases was detached very fast.
Surface modification techniques associated with mechanical action attract much attention recently. For example, the microstructure in the surface layer of metals and alloys can be refined to the nanometer scale by means of surface mechanical attrition treatment(SMAT) [5-6], ball milling(BM)[7] and ultrasonic shot peening (USP)[8-10]. It is interesting that the subsequent surface chemical treatments, such as nitriding and chromizing, can be enhanced by SMAT[11-12]. In our previous work, nano-crystallized alumina coatings can be prepared at a relatively low temperature with a high rate by a mechanical attrition enhanced aluminizing technique[13]. Furthermore, a novel ultrasonic-based dry mechanical process has been proposed for armouring and/or coating metallic surface with other metal or ceramic materials[14].
In our previous work, a novel method for preparing Ni coating was reported, using mechanical attrition to enhance electroplating of Ni alloys[15]. The new coating shows smooth surface morphology, refined grain size, is pore-free, and possesses increased micro-hardness and excellent corrosion resistance.
In this work, Cu coating was prepared using mechanical attrition enhanced electroplating(MAEE) method. In order to enhance the MA action, vertical vibrator was used for MAEE process instead of horizontal vibrator. It is believed that the better peen or cold weld action will be obtained when the glass balls bump the sample surface vertically compared with previous horizontal bumping. Therefore, the modified mechanical attrition method may affect the electroplating process and leads to new properties of coating.
2 Experimental
The device of MAEE Cu coating is shown schematically in Fig.1. A plastic tank filled with plating solution was placed on the top of a vibrator, and the vibrator moved vertically at frequencies of 3.0, 4.0 and 5.0 Hz with an amplitude of 1 mm. A Cu plate was used as anode located horizontally on the top of the plating bath. The carbon steel samples with dimensions of 20 mm×10 mm×2 mm, ground with SiC papers to 1200-grit finish and mounted in epoxy resin, were used as cathode. A CuSO4 based solution was used as the plating solution. The composition was 180 g/L CuSO4·5H2O and 60 g/L H2SO4. Glass balls with diameters of 1, 3, 5 and 7 mm were used on the cathode surface to provide mechanical impact. All the electroplating experiments were carried out in the baths at room temperature for 20 min. The current density was 50, 100, 200, 300, 400 or 500 mA/cm2. Field emission scanning electron microscope(FESEM) (JSM-6700F) was used to observe the morphology of coating surface.
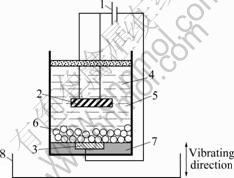
Fig.1 Schematic diagram of mechanical attrition electroplating device: 1 DC power; 2 Anode; 3 Cathode (Carbon steel sample); 4 Plating solution; 5 Plastic bath; 6 Glass ball; 7 Plastic bottom plate; 8 Vibrator
3 Results
Fig.2 shows the surface morphology of Cu coatings deposited at a current density of 100 mA/cm2 with or without supplying MA. From Fig.2(a), it can be seen that many pyramid-like crystals with size of 1-7 mm form uniformly on the surface of Cu coating after traditional electroplating(TEP). The surface is rough and uneven. While, from Fig.2(b), it can be seen that, with MAEE process, pyramid-like crystals disappear from the surface of Cu coating; and the surface of Cu coating is composed of many crystals with size less than 1 mm. The surface is smooth and flat. Therefore, MA action can affect the electroplating process and lead to a finer surface morphology of the Cu coating.
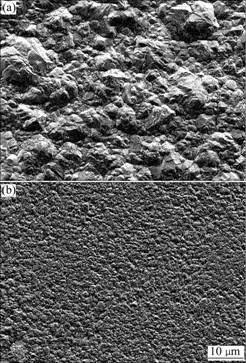
Fig.2 Surface morphologies of Cu coatings deposited at current density of 100 mA/cm2 for 20 min, showing effect of MA action on surface refinement: (a) Without MA; (b) With MA at 5.0 Hz
Fig.3 shows the influence of vibrating frequency on the surface morphology of Cu coatings deposited by MAEE at a current density of 100 mA/cm2. It can be seen that the grain size decreases with increasing vibrating frequency. For the TEP process, Cu coating ismainly composed of the grains with a diameter of 1-7 mm, surrounded by a little small grains (Fig.3(a)). With the MAEE process, as the vibrating frequency increases from 3.0 to 5.0 Hz, the size of the largest grains in Cu coatings is about 1 mm, and the amount of small grains increases (Figs.3(b)-(d)).
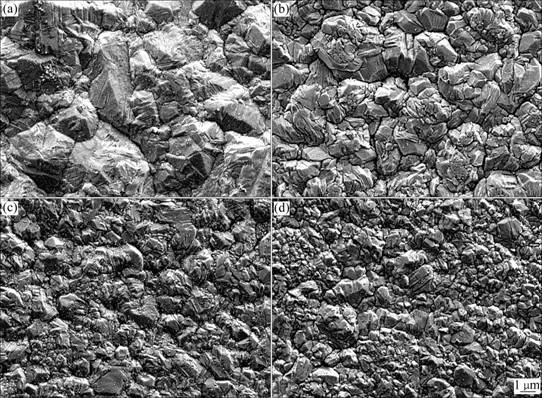
Fig.3 Morphologies of Cu coatings deposited at current density of 100 mA/cm2, showing effect of vibrating frequency on surface refinement: (a) Without MA; (b-d) With MA under different frequency; (b) 3.0 Hz; (c) 4.0 Hz; (d) 5.0 Hz
Fig.4 shows the influence of diameter of glass balls, used to generate MA, on the morphology of Cu coatings deposited at a current density of 100 mA/cm2 and under vibrating frequency of 5.0 Hz. It can be seen that the amount of small grains on Cu coatings increases as the diameter of glass balls increases from 1 mm to 3 mm and 5 mm. However, as shown in Fig.4(d), the amount of the big grains increases when the glass balls with diameter of 7 mm are used. So, the best effect of MA action on the refinement of Cu coating with uniform and fine grain size is obtained when the diameter of glass balls is 5 mm.
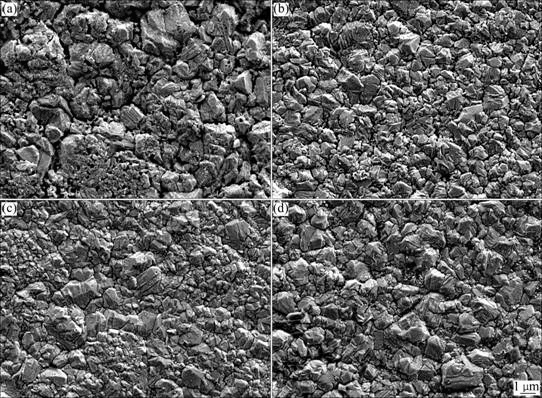
Fig.4 Morphologies of Cu coating deposited at current density of 100 mA/cm2, showing effect of diameter of glass balls on surface refinement with MA action: (a) 1 mm; (b) 3 mm; (c) 5 mm; (d) 7mm
Fig.5 and Fig.6 show the influence of current density on the surface morphology of Cu coatings deposited without and with MA action, respectively. By comparing Figs.5(a) and 5(b) with Figs.6(a) and 6(b), it can be seen that, at lower current densities of 50 and 100 mA/cm2, MA action makes the Cu coatings changed from a structure mainly composed of micro-size grains to a structure mainly composed of nano-size grains. By comparing Figs.5(c)-(f) with Figs.5(a) and 5(b), it is found that the spherical grains or pillar-shape grains form on the surface and the surface of coatings becomes loose and easy to remove without MA when the current density is higher. By comparing Figs.5(c)-(e) and Figs.6(c)-(e), it can be seen that with high current densities, MA changes the Cu coatings from a loose, dentritic structure with many gaps to a compact structure with fewer porosity. Even for the current density of 500 mA/cm2 (Fig.6(f)), the coatings are dense and composed of small grains. Therefore, the rapid electroplating is obtained by MAEE process.

Fig.5 Morphologies of Cu coating by traditional electroplating process at different current density: (a) 50 mA/cm2; (b) 100 mA/cm2; (c) 200 mA/cm2; (d) 300 mA/cm2; (e) 400 mA/cm2; (f) 500 mA/cm2
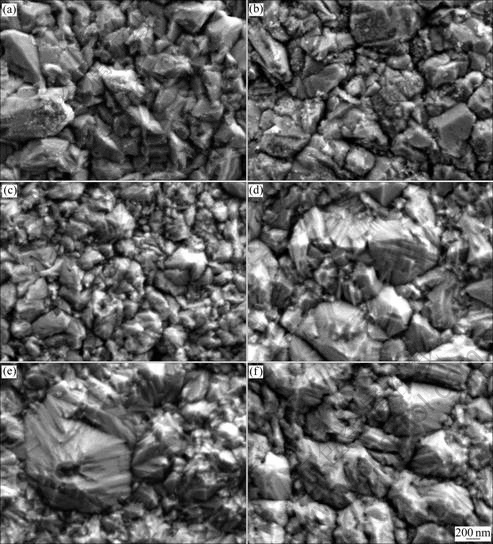
Fig.6 Morphologies of Cu coating by mechanical attrition electroplating process at different current density: (a) 50 mA/cm2; (b) 100 mA/cm2; (c) 200 mA/cm2; (d) 300 mA/cm2; (e) 400 mA/cm2; (f) 500 mA/cm2
4 Discussion
According to the electroplating theory, there are four important steps in the formation of electroplating coating: mass transportation, interface reaction, nucleation and grain growth. We will analyze the effect of MA treatment on the above steps to explain the formation of excellent Cu coatings prepared by MAEE process at high current density.
Fig.7 demonstrates schematically the structure of Cu coating deposited by electroplating under traditional condition with MA. It can be seen that this Cu coating consists of two layers: a fine grain layer (or the grain nucleation zone) and a large grain layer (or the grain growth zone)[16]. The two-layer structure is related to the mass transportation, interface reaction, nucleation and grain growth. Prior to plating, the solution composition in the boundary layer is the same as that in the bulk solution. As a potential is applied to the substrate, current is distributed uniformly on the cathode surface, and Cu ions are immediately reduced at the cathode surface and nucleated to form a fine-grained Cu film (the grain nucleation zone shown in Fig.7(a)). At the same time, the concentration of Cu ions at the cathode surface decreases, and a concentration gradient of Cu ions is established in the boundary layer. As plating goes on, the Cu grains grow. Since the size and shape of the grains are irregular, the current distribution on the cathode surface is no longer uniform. Current density tends to be higher on larger grains, leading to a preferential growth of big grains (as shown in the grain growth zone in Fig.7(b)).
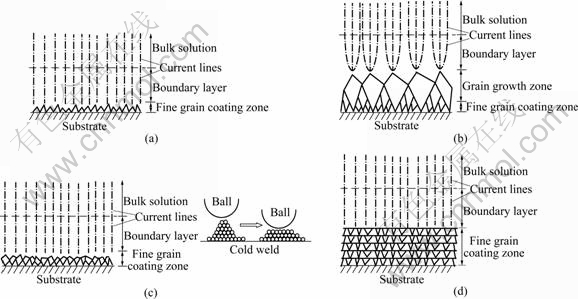
Fig.7 Model on formation of Cu coating: (a) Initial stage of TEP process; (b) Grain growth stage of TEP process; (c) Initial stage of MAEE process; (d) Grain growth stage of MAEE process
According to the electrochemical theory, overpotential is the drive of reaction from metal ion to metal atom and is formed by the polarization. There are two important polarizations at the interface of cathode and boundary layer: electrochemical polarization and concentration polarization. The concentration polarization is related with the thickness of boundary layer[17]. The thickness of the boundary layer is affected by the degree of convection in the bulk solution. Generally, the stronger the convection, the smaller the thickness of boundary layer is. It is obviously that the concentration polarization could be decreased by increasing the convection. There exists a limited current density, IL, which is determined by concentration polarization. When the current density is below IL, the electroplating process is controlled by electrochemical polarization. And the grain size in the growth zone increases, as shown in Figs.5(a) and 5(b). As the current density is equal to or above IL, Cu plating is completely controlled by the concentration polarization. In this case, Cu ions tend to discharge preferentially at the tips of the protrusions, and the Cu nucleus are difficult to grow, resulting in the formation of dendrites, as shown in Figs.5(c)-(f).
Agitation is the easy way to increase the convection in the bulk solution and decrease the thickness of the boundary layer. High porosity of hard particles is used as agitator to increase the convention in the earlier work of high speed plating. The concentration polarization decreases and the limited current density increases. So the electroplating can be done at high current density. But the high atom deposition rate makes the coating become loose and easy to remove.
As MA action is applied to Cu plating, three effects should be considered. Firstly, MA process can decrease the thickness of boundary layer by enhancing the convection in the bulk solution, which can accelerate the diffusion in the boundary layer and increase the limited current density, IL. Therefore, the critical current density to form dendrite during Cu plating increases under MA action. This effect can be confirmed by comparing the microstructures in Figs.5(c)-(e) and Figs.6(c)-(e), in which the Cu dendrite formed in traditional plating at a high current density does not form; and compact Cu coatings are obtained under MA action.
Secondly, the surface of Cu coating becomes smoother and more active under plastic deformation and abrasion by MA, so the current distribution on the surface of Cu coating keeps uniform, and the nucleation of Cu grains processes at a high rate, as shown in Fig.7(d). Therefore, under MA action, the condition for grains to grow larger is hindered, resulting in a fine microstructure of Cu coatings. By comparing Fig.6 with Fig.5, it can be seen that the grain size decreases when the MA action is applied in MAEE process. From Figs.6(c)-(e), the grain size keeps small even at high current density.
Thirdly, the loose Cu coating deposited at high current density can be peened or cold-welded together by the moving glass balls to form compact Cu coatings. Thus, the Cu coatings can be plated at a high current density and deposition rate. Compared with our work at a high current density and the work of high speed plating reported earlier[1-4], it can be seen that the hard particles used are different. We use solid glass balls with diameter of 1-7 mm to peen the cathode surface, so the loose Cu coatings deposited at a high current density can be cold-welded together to form compact coatings. This action was also described in the mechanical plating process[14]. On the other hand, the hard particles used in the earlier work of high speed plating were small and porous, so the coatings were loose and easy to remove.
5 Conclusions
1) The compact Cu coating with smooth surface and refined grain could be prepared at high current density and electroplating rate by MAEE process.
2) The spherical grain or pillar-shape grain could be obtained by traditional electroplating process at the current density of 200-600 mA/cm2. The coatings are loose, porous and easy to brush off. The pyramid-shape grain with diameter less than 1 μm can be obtained by MAEE process. The coatings are compact and pore-free. The rapid electroplating process can be obtained by MA action.
3) When MA action is applied to Cu plating, three effects should be considered. The mass transfer in the boundary layer is affected by MA action. The surface of Cu coating becomes smoother and more active under the effect of plastic deformation and abrasion. The cold-weld action can make the loose coating at high current density transform into compact coatings.
References
[1] EISNER S. Electroplating accompanied by controlled abrasion of the plate (1) [J]. Plat (USA), 1971, 58(10): 993-999.
[2] WISDOM N E, EISNER S. Electroplating accompanied by controlled abrasion of the plate (2) [J]. Plat (USA), 1971, 58(11): 1099-1101.
[3] EISNER S, WISDOM N E. Electroplating accompanied by controlled abrasion of the plate (3) [J]. Plat (USA), 1971, 58(12): 1183-1186.
[4] EISNER S. Ultra high speed plating process utilizing small hard particles [J]. Trans Inst Met Fin, 1973, 51: 13-16.
[5] SATO M, TSUJI N, MINAMINO Y, KOIZUMI Y. Formation of nanocrystalline surface layers in various metallic materials by near surface severe plastic deformation [J]. Sci Technol Adv Mater, 2004, 5: 145-152.
[6] TAO N R, WANG Z B, TONG W P, SUI M L, LU J, LU K. An investigation of surface nanocrystallization mechanism in Fe induced by surface mechanical attrition treatment [J]. Acta Mater, 2002, 50: 4603-4616.
[7] UMEMOTO M, TODAKA K, TSUCHIYA K. Formation of nanocrystalline structure in carbon steels by ball drop and particle impact techniques [J]. Mater Sci Eng A, 2004, 375: 899-904.
[8] TAO N R, SUI M L, LU J, LU K. Surface nanocrystallization of iron induced by ultrasonic shot peening [J]. Nanostruct Mater, 1999, 11: 433-440.
[9] LIU G, LU J, LU K. Surface nanocrystallization of 316L stainless steel induced by ultrasonic shot peening [J]. Mater Sci Eng A, 2000, 286: 91-95.
[10] AKAMATSU H, IKEDA T, AZUMA K, FUJIWARA E, YATSUZUKA M. Surface treatment of steel by short pulsed injection of high-power ion beam [J]. Surf Coat Technol, 2001, 136: 269-272.
[11] TONG W P, TAO N R, WANG Z B, LU J, LU K. Nitriding iron at lower temperatures [J]. Science, 2003, 299: 5607-5609.
[12] GU J F, BEI D H, PAN J S, LU J, LU K. Improved nitrogen transport in surface nanocrystallized low-carbon steels during gaseous nitridation [J]. Mater Lett, 2002, 55: 340-343.
[13] ZHAN Z L, HE Y D, WANG D R, GAO W. Low-temperature processing of Fe-Al intermetallic coatings assisted by ball milling [J]. Intermetallics, 2006, 14: 75-81.
[14] ALLISON G W. Mechanical plating [J]. Metal Finish, 2002, 100: 384-393.
[15] NING Z H, HE Y D, GAO W. Mechanical attrition enhanced Ni electroplating [J]. Surf Coat Technol, 2008, 202: 2139-2146.
[16] WATANABE T. Nano Plating—Microstructure control theory of plated film and data base of plated film microstructure [M]. Singapore: Chemical Industry Press and Elsevier (Singapore) Ltd, 2007: 23-30.
[17] FLUMUJIN. Kinetics of electrode process [M]. Russia: Science Press, 1965: 59-65.
Foundation item: Project(50671006) supported by the National Natural Science Foundation of China
Corresponding author: HE Ye-dong; Tel: +86-10-62332715; E-mail: htgroup@mater.ustb.edu.cn
(Edited by YANG Bing)