J. Cent. South Univ. Technol. (2008) 15(s1): 453-456
DOI: 10.1007/s11771-008-398-8

Effect of holes on in-plane shear (Mode Ⅱ) crack sub-critical propagation of rock
XIE Hai-feng(谢海峰), RAO Qiu-hua(饶秋华), XIE Qiang(谢 强),
LI Zong-yu(黎纵宇), WANG Zhi(王 志)
(School of Civil Engineering and Architecture, Central South University, Changsha 410083, China)
Abstract: Shear-box (i.e. compression-shear) test and newly designed electrically conductive adhesive method were used to measure shear crack sub-critical propagation time and rate of sandstone specimen. Different cubic specimens with and without holes were tested to study the effect of holes on the shear crack sub-critical propagation. Numerical and experimental results show that three independent variables of hole, the interval distance S, the distance between the center of hole and the crack tip L, and hole radius R, have different contribution to the ratio of stress intensity factor of the specimen with holes to that of the specimen without hole, KII/KII0. Increasing S and decreasing L and R will result in the decrease of KII/KII0 and help crack arrest. The weight relation of the independent variables for KII/KII0 is S>L>R. The specimen DH3 with the largest value of S and the smallest values of L and R has the longest sub-critical crack propagation time and the smallest sub-critical crack propagation rate. Adding two suitable holes symmetrically to the original crack plane in rock specimen is considered to be a potential method for crack arrest of rock.
Key words: sub-critical crack propagation; hole; shear (Mode II) fracture; electrically conductive adhesive; rock
1 Introduction
In mining, geotechnical and civil engineering, rock mass is mostly subjected to shear (Mode Ⅱ) and compression-shear (mixed ModeⅠ-Ⅱ) loading. It is of significance to study not only the shear crack growth, including the crack initiation, crack stable (sub-critical) propagation and unstable propagation, but also the shear crack arrest for the assessment of safety and control of disasters in rock mass structure.
At present, two methods are mainly used for crack arresting, by improving material toughness[1] (e.g. increasing material thickness) and structure[2-4] (e.g. adding arrest strip, loop and arranging bolts). For defected materials, addition of voids, micro-cracks and other inclusions at crack tip can decrease crack-tip stress and help crack arresting[5-6]. In practice, for the rock materials, drilling holes at the crack tip easily result in new cracks. If crack-stopping hole is better arranged closed to the crack tip, it can prevent the crack propagation[7-9].
In this study, shear-box (i.e. compression-shear) test of red sandstone was used to obtain the shear (Mode Ⅱ) fracture[10]. A new electrically conductive adhesive method was proposed to measure the shear crack growth characters, including the crack initiation time, crack stable (sub-critical) propagation and unstable propagation rate. Different cubic specimens with and without holes were tested for studying the effect of holes on the shear sub-critical crack propagation of rock.
2 Numerical calculation
The red sandstone was employed in this study. According to the test standards of the International Society for Rock Mechanics(ISRM), its mechanical properties tested at room temperature are listed in Table 1.
Table 1 Mechanical properties of sandstone at room temperature

The cubic specimen with length L=50 mm, width W=50 mm, and height H=50 mm, is subjected to compression-shear loading, as shown in Fig.1. The notch length a is 25 mm and the notch width t is 1 mm. The
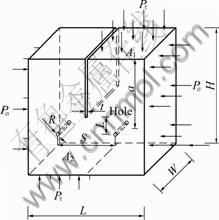
Fig.1 Schematic diagram of compression-shear specimen
ratio of shear stress Pτ to compressive stress Pσ depends on the inclined angle of the beveled die, a. In this study, a=70?.
For the sake of simplicity and machinability, two equal-diameter holes were applied symmetrically to the original crack plane in the specimen, with different interval distances (S=13, 19 and 25 mm), different distances between the center of hole and the crack tip (L=7.5, 12.5 and 17.5 mm), and different hole radii (R=
1.5, 2.5 and 4 mm).
Finite element software MSC.Marc2005 was used to calculate stress field in the specimen and study the effect of holes on shear fracture of rock. Eight-node hexahedron elements were adopted with isotropic properties. Since the distribution of the stress applied to the surface of specimen in shear-box test was unknown, the specimen and loading setup were modeled as a whole (Fig.2). The applied load was assumed to be unit load 1 N.
Shear stress intensity factors(SIF) of both the specimens with holes, KII, and the specimens without hole, KII0, were derived by displacement extrapolation method[9] for comparison.
Fig.3 shows the stress distribution of the specimen with holes and without hole. It can be seen that suitable holes added around the crack tip can release the crack-tip stress and thus decrease the value of SIF.
Table 2 shows the results of KII/KII0 in the specimens with different distances and sizes of holes. The holes added in the specimen can decrease the original stress intensity factor at crack tip and favor the crack arrest only when the value of KII/KII0 is smaller than 1. The smaller the KII/KII0, the easier the crack arrest.
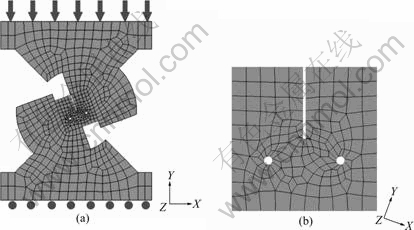
Fig.2 Finite element meshing configuration: (a) Global meshing; (b) Local meshing
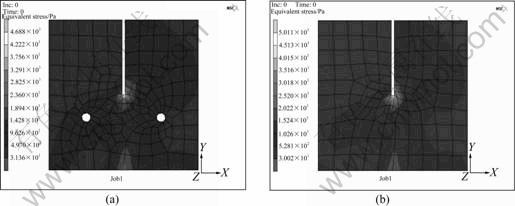
Fig.3 Stress distribution of specimens with and without holes: (a) Specimen DH3 with holes; (b) Specimen S1 without hole
Table 2 Results of KII/KII0 in specimens with different distances and sizes of holes
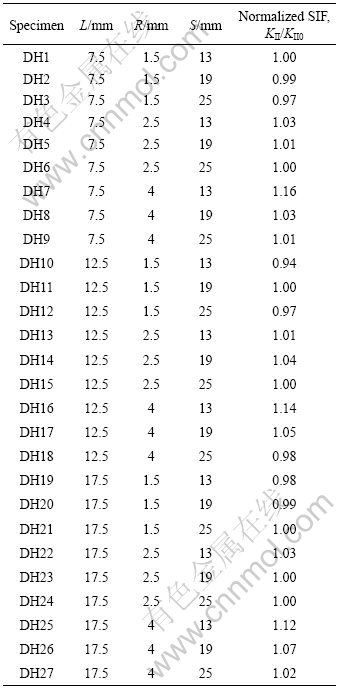
The relationship between the normalized SIF of shear (Mode Ⅱ) crack and distances and sizes of holes is derived by multiple linear regression method, as shown in Eqn.(1), which is similar to that of tensile (ModeⅠ) crack:
(1)
The coefficients of the independent variables, L, R and S, may be positive or negative, and have different contribution to the value of KII/KII0. Increasing S and decreasing L and R will result in the decrease of KII/KII0 and help crack arrest. The weight relation of the independent variables for KII/KII0 is S>L>R.
It is also found that the specimen DH3, with the largest value of S and the smallest values of L and R, has the best effect of holes on shear crack arrest. The specimen DH14, with medium values of L, R and S may be better for the shear crack arrest.
3 Experimental
In order to study the effects of holes on shear sub-critical crack propagation of rock, five typical cubic specimens were adopted in shear-box test based on numerical analysis. There were the specimen DH3 with the largest value of S and the smallest values of L and R, the specimen DH8 with the largest value of R, the specimen DH14 with medium values of L, R and S, the specimen DH22 with the largest value of L, as well as the specimen S1 without any hole.
The initial crack was prepared by a diamond saw blade with the thickness of 0.8 mm. The crack length a is 25 mm and the crack width t is 1 mm. The vertical derivations and the parallelism of specimen surface must be less than 0.25? and 0.05 mm, respectively.
All the compression-shear tests were performed by the INSTRON1346 electro-hydraulic servo testing system (Fig.4), under a displacement control. The loading rate is 0.5 mm/min and the inclined angle of the beveled die, a, is 70?. The shear crack growth characters, including the crack initiation time, crack stable and unstable propagation (sub-critical crack propagation) rate were measured by newly-designed electrically conductive adhesive method.
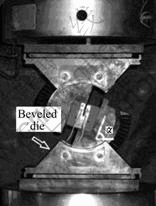
Fig.4 Compression-shear box
4 Results and analysis
It is found that all specimens have crack initiation and propagation almost in the original planes, i.e. shear (Mode Ⅱ) fracture occurs in these specimens.
Table 3 lists the test results of shear crack sub- critical propagation time and rate of the specimens with different double holes (DH3, DH8, DH14, DH22) and the specimen without any hole (S1), respectively. It can be seen that the sub-critical crack propagation time is about 28-36 s and the sub-critical crack propagation rate is about (1.0-2.5)×10-4 m/s for red sandstone.
Table 3 Test results of specimens with and without holes
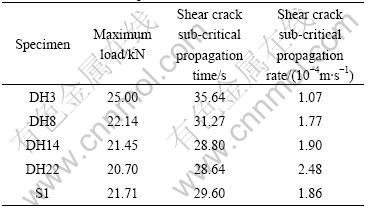
Compared with the specimen without any hole, S1, the specimens with double holes, DH3 and DH8, have longer sub-critical crack propagation time and smaller sub-critical crack propagation rate, while the specimens with double holes, DH14 and DH22, are opposite. Especially, specimen DH3 with the largest value of S and the smallest values of L and R has prolonged by more than 20% sub-critical crack propagation time and reduced sub-critical crack propagation rate by more than 40%. It is proved again that the weight relation of the independent variables for crack arrest is S>L>R. Adding two suitable holes symmetrically to the original crack plane in the specimen is considered to be a potential method for crack arrest of rock.
5 Conclusions
1) Three independent variables of hole, the interval distance S, the distance between the center of hole and the crack tip L, and the hole radius R, have different contribution to the ratio of stress intensity factor of the specimen with holes to that of the specimen without hole, KII/KII0. Increasing S and decreasing L and R will result in the decrease of KII/KII0 and help crack arrest. The weight relation of the independent variables for KII/KII0 is S>L>R.
2) Adding different holes in specimens may be for or against the crack arrest. The specimen with the largest value of S and the smallest values of L and R has the longest sub-critical crack propagation time and the smallest sub-critical crack propagation rate, which favors the crack arrest.
3) Adding two suitable holes symmetrically to the original crack plane in the specimen is considered to be a potential method for crack arrest of rock.
References
[1] CHEN Fu-lai, SHUAI Jian. Arrest structure and ductile determine methods of ductile fracture for gas transportation pipeline [J]. Pressure Vessel Technology, 2006, 23(7): 39-43. (in Chinese)
[2] TSAMASPHYROS G, DIMOU G. Stress intensities in a strip reinforced by stiffeners at the edges [J]. Engineering Fracture Mechanics,1995, 51(6): 897-914.
[3] SETHURAMAN R, MAITI S K. Determination of mixed mode stress intensity factors for a crack-stiffened panel [J]. Engineering Fracture Mechanics, 1989, 33(3): 355-369.
[4] HE Yun-shu, CHEN Li-jun, DU Hong-zeng. Effectiveness varying in dimension of crack-stopping holes [J]. Journal of Civil Aviation University of China, 2004, 22(3): 29-31. (in Chinese)
[5] HU K X, CHANDRA A, HUANG Y. Multiple void-crack interaction [J]. International Journal of Solids and Structures, 1993, 30(11): 1473-1489.
[6] YUAN Long-wei. Rheology on defective object [M]. Beijing: National Defence Industry Press, 1994. (in Chinese)
[7] GONG S X, HORII H. General solution to the problem of microcracks near the tip of a main crack [J]. Journal of the Mechanics and Physics of Structures, 1989, 37: 27-46.
[8] ZHOU Zeng-guo, LI Zhi-da, Experimental research on influence of voids on COD [J]. Journal of Wuhan University of Technology (Transportation Science & Engineering), 2001, 25(3): 326-328. (in Chinese)
[9] HAN Jian-Jun, CHEN Yi-Heng. On the contribution of a microhole in the near-tip stress field to the J-integral [J]. International Journal of Fracture, 1997, 85: 169-183.
[10] RAO Q H. Pure shear fracture of brittle rock—A theoretical and laboratory study [D]. Sweden: Lule? University of Technology, 1999.
(Edited by LI Xiang-qun)
Foundation item: Project(50374073) supported by the National Natural Science Foundation of China; Project(1343-77239) supported by the Graduate Education Innovation Project of Central South University, China
Received date: 2008-06-25; Accepted date: 2008-08-05
Corresponding author: RAO Qiu-hua, Professor; Tel: +86-731-8836001; E-mail: raoqh@mail.csu.edu.cn