
Microstructure and magnetic properties of rapidly solidified Sm(CobalFe0.11Cu0.10Zrx)7 alloys
LI Li-ya(李丽娅), YI Jian-hong(易健宏), GE Yi-cheng(葛毅成)
State Key Laboratory of Powder Metallurgy, Central South University, Changsha 410083, China
Received 15 July 2007; accepted 10 September 2007
Abstract: Effects of Zr content on the structural, morphological, and magnetic properties of rapidly quenched Sm(CoFe0.11Cu0.10Zrx)7 (x=0-0.04) alloys were investigated. The Zr-free ribbon crystallizes with the 1?7H structure as a major phase while the ribbons with Zr addition adopts the 2?17R structure type. The ribbons with x=0.03 exhibits a highest coercivity, Hci=933.7 kA/m, because a smaller uniform cellular structure along with a lamellar phase is formed. The decrease of Hci above x>0.03 is mainly related to the formation of 2?7 phase.
Key words: rapid solidification; annealing; coercivity; nanocrystalline microstructure; SmCo
1 Introduction
Precipitation hardened Sm(Co, Fe, Cu, Zr)z permanent magnets are very promising candidates for high temperature applications up to 500 ℃[1-3]. The microstructure of magnets consist of rhomhedral 2?17 cells, Cu-rich hexagonal 1?5 cell boundary phase and lamellar phase[4-6]. The lamellar phase appears as a Zr-rich thin plate, and initially has been only observed in the Zr-substituted Sm2Co17 type magnets[7]. But ZHANG et al[8] have reported a lamellar phase in a Zr-free Sm(Co0.45Fe0.15Cu0.4)5 alloy with a Be3Nb structure. Among the three elements added to Sm2Co17-type magnets (Zr, Fe, and Cu), Zr is the most important one since it relates to the structural modification and stabilization of the 2?17 hexagonal phase. TANG et al[9] have showed that the amount of lamellar phase increases with increasing Zr content, and the existence of Zr can stabilize a uniform cellular structure. Recently, melt-spinning has opened a new route in processing high coercive Sm(Co, Fe, Cu, Zr)z magnets[10-11]. Some studies have also shown that by applying to ribbons an annealing process similar to that of sintered magnets an analogous cellular and lamellar microstructure can be obtained[12-13]. Despite all of these researches, the role of Zr on the microstructure and coercivity of melt-spinning Sm2Co17 type magnets is not yet clear. In this paper, we report the microstructure and magnetic properties of Sm(CobalFe0.11Cu0.10Zrx)7 with increasing Zr content. The formation of the cellular structure and the role of the lamellar phase are also discussed.
2 Experimental
Samples of Sm(CobalFe0.11Cu0.10Zrx)7 alloys with x=0, 0.01, 0.02, 0.03 were prepared by induction arc melting using raw material with purity of at least 99.9%. Before arc melting 5% extra Sm was added to the sample to compensate for the mass loss due to Sm vaporization during arc melting. The ingots were then inserted into a 10 mm diameter quartz tube with a nozzle of 0.8 mm in diameter. The chamber was evacuated to a vacuum of 10-2 Pa and then filled with high purity argon. The sample was induction melted and ejected through the nozzle using a pressure difference of 80 Pa. The surface velocity of Cu wheel was 30 m/s. For hardening, the ribbons were first wrapped in tantalum foil and then sealed in quartz capsules after repeated evacuations under ultra-high purity Ar. The samples were then annealed at 800 ℃ for 30 min, followed by slow cooling to 400 ℃ at a rate of 0.5 ℃/min. The microstructures of the ribbons were characterized using a Philips CM 200 transmission electron microscope(TEM). Phase identification of the heat-treated ribbons was done by X-ray diffraction(XRD) using the Cu Kα radiation. Magnetic properties of the samples were measured in the plane direction of the ribbon samples using a vibrating sample magnetometer(VSM).
3 Results
3.1 Magnetic properties
The magnetic behavior strongly depends on the Zr content. Increasing x in Sm(CobalFe0.11Cu0.10Zrx)7 results in a general increase in intrinsic coercivity and a decrease in saturation magnetization. Fig.1 shows the demagnetization curves for the rapidly solidified Sm(CoFe0.11Cu0.10Zrx)7 heat-treated samples. The hysteresis curves show smooth demagnetization behavior, indicating single-phase behavior.
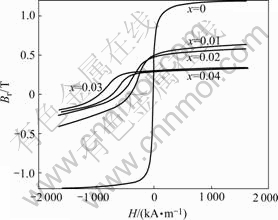
Fig.1 Magnetic hysteresis loops for Sm(CoFe0.11Cu0.10Zrx)7 heat-treated ribbons
The dependence of coercivity and saturation magnetization on the Zr content x is shown in Fig.2. It can be seen that Hci dramatically increases with increasing Zr content from 0 to 0.03. The maximum Hci of around 933.7 kA/m can be obtained at x=0.03, respectively. When the Zr content is increased to 0.04, Hci starts decreasing significantly. This suggests that the addition of Zr is very significant in improving coercivity. On the other hand, the samples with x=0.01-0.03 shows values of the magnetization significantly lower than that of the sample without Zr over the entire range of applied magnetic fields. Ms decreases from 1.19 T to 0.33 T with increasing Zr content x from 0 to 0.04.
3.2 Structural characterizations
Fig.3 shows the X-ray diffraction patterns of the Sm(CoFe0.11Cu0.10Zrx)7 annealed ribbons with x=0, 0.01, 0.02, 0.03, and 0.04. It can be seen that the Zr-free ribbon crystallizes with the 1?7H structure as the main phase while the ribbons with Zr addition adopts the 2?17R (Th2Zn17-rhombohedral type) structure type. The
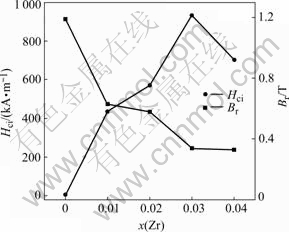
Fig.2 Relationship between Zr content x and intrinsic coercivity and saturation magnetization for Sm(CoFe0.11Cu0.10Zrx)7 heat-treated ribbons
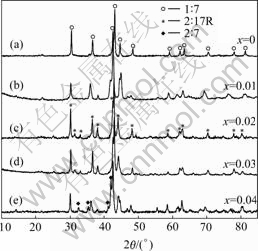
Fig.3 XRD diffraction patterns for Sm(CoFe0.11Cu0.16Zrx)7 heat-treated ribbons
formation of the 2?17R phase is confirmed from the presence of the (204) superlattice refection that appears at approximately 37.8? (2θ). Other phases can not be detected because their amount is too small. With increasing Zr content up to 0.04, other minor phases, mainly Sm2Co7 (2?7) with the hexagonal Ce2Ni7 structure, appears with the 2?17R type structure. The presence of Sm2Co7 is unexpected considering the equilibrium phase diagram.
The addition of Zr results in the significant increase of the coercivity, suggesting that Zr would introduce microstructure changes. Fig.4 shows the TEM bright field micrograph of the ribbons after annealing. The microstructure is strongly dependent on the Zr content. For example, by increasing x from 0 to 0.03, the grain size decreases dramatically from >300 nm to 50
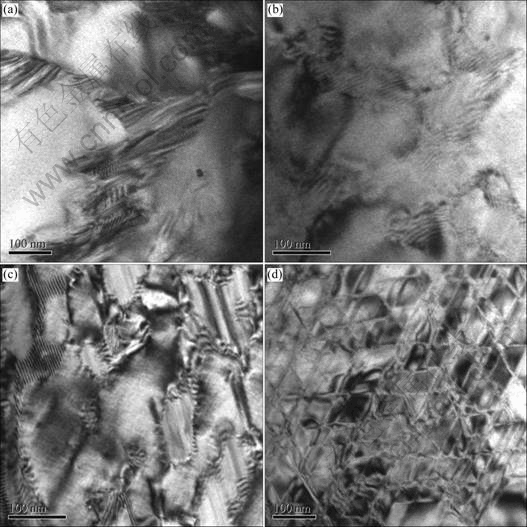
Fig.4 TEM bright field micrographs of Sm(CoFe0.11Cu0.10Zrx)7 alloys with x=0 (a), 0.01 (b), 0.02 (c) and 0.03 (d)
nm, while the lamellar phase density increases sharply. The cellular and lamellar microstructures have not been observed in the Zr-free ribbon. A Cu-rich phase is found to be distributed in the boundary of 1?7H matrix phase instead (Fig. 4(a)). When x=0.01, it is seen from Fig.4(b) that the ribbon exhibits a detectable cellular microstructure with an average cell size of about 100-150 nm (Fig.4(b)). With increasing Cu content (Figs.4(c) amd (d)), a cellular precipitation structure and a platelet structure, similar to that of the bulk Sm(Co, Fe, Cu, Zr)z sintered magnets is obtained. The ribbon for x=0.02 exhibits an inhomogeneous cellular microstructure with an average cell diameter of 60-150 nm. When a uniform cellular structure along with a lamellar phase is formed. The cell size decreases to about 50 nm and the density of the lamellar phase is also much higher. Analysis of electron diffraction patterns shows that the cellular precipitation structure consists of a 2?17R cell matrix phase, a 1?5 cell boundary phase and a Zr-rich platelet phase.
4 Discussion
From the XRD and TEM results (Figs.3 and 4), we observe that three microstructural changes occur in the ribbons when Zr content is increased. The first one is the grain size reduction with the increase of Zr content. The second one is the transformation from 1?7H phase to 2?17R phase. The third one is the appearance of the lamellar phase with the increase of Zr content. The grain size is larger than 300 nm when x=0, while it is 30-60 nm when x=0.03. In the Sm-Co system, the 2?17 phase can exist in three crystal structure types, viz hexagonal 2?17H, hexagonal 1?7H, and rhombohedral 2?17R based on Sm concentration and heat treatment[14]. The difference in the structure arises from the positions of the pare of substituted Co atoms. The melt-spinning at a higher wheel surface speed results in the random occupation of Co-atoms, which is found to promote the formation of the 1?7H structure[15]. The formation of 1?7H structure plays an important role in developing 2?17 magnets with a large Hci. However, the grain size of the Zr-free ribbon is too large for a strong rigid exchange coupling. The intrinsic coercivity of the sample is just about 5.58 kA/m.
The cellular structure as well as 1?7H structure can provide large coercivity by the pinning at the cell boundary phase. The driving force for such a pinning originates from the domain wall energy difference
between 2?17 and 1?5 phase, where K1 is the first anisotropy constant and A the exchange constant[16]. High Cu content in the cell boundary is beneficial for the development of high coercivity in Sm2Co17-based magnets since there is more Cu in the 1?5 cell boundary phases and a larger domain wall energy difference[17]. With a fixed Cu content, the Cu content in the 1?5 phases is determined by the density of the lamellar phase[18]. The lamellar phase would provide easy diffusion paths for Cu segregation. Zr substitution leads to a decrease of the cell size, increase of the density of the lamellar phase, and a better chemical redistribution of Cu at the cell boundaries, and therefore to a higher coercivity of the ribbon. On the other hand, the addition of Zr also results in the decrease of the cell size, especially after x>0.02. More domain wall pinning sites would be helpful to obtain a higher coercivity. The dramatic decrease of intrinsic coercivity above x>0.03 is mainly related to the formation of 2?7 phase (Fig.3).
5 Conclusions
1) The microstructure of the Zr-free Sm(CoFe0.11- Cu0.10)7 heat-treated ribbons with high saturation of 1.19T is composed of 1:7H surrounded by Cu. While the microstructure of the Sm(CoFe0.11Cu0.10Zr0.03)7 sample with high coercivity of 933.7 kA/m is composed of 2?17R cells surrounded by 1:5 cell boundaries and intersected by the lamella phase. A Sm2Co7 phase is observed in the heat-treated ribbons when the Zr content increases to 0.04. The lamellar phase can be observed in the sample with x≥0.02 and its amount increases with increasing Zr content.
2) While the Zr content is increased from 0 to 0.04, saturation magnetization of the heat-treated ribbons decreases from 1.19 T to 0.33 T, and the intrinsic coercivity increases from 5.58 kA/m to 933.7 kA/m. The highest intrinsic coercivity, Hci=933.7 kA/m, is obtained in the ribbon with Zr content of 0.03.
References
[1] GUO Z H, PAN W, LI W. Sm(Co, Fe, Cu,Zr)z sintered magnets with a maximum operating temperature of 500 ℃ [J]. J Magn Magn Mater, 2006, 303(1): e396-e401.
[2] LIU J F, ZHANG Y, DIMITROV D, HADJIPANAYIS G C. Microstructure and high temperature magnetic properties of Sm(Co, Cu, Fe, Zr)z (z=6.7-9.1) permanent magnets [J]. J Appl Phys, 1999, 85(5): 2800-2804.
[3] CORFIELD M R, WILLIAMS A J. Study of solid-state reactions in Sm(Co, Fe, Cu, Zr)z 2?17-type alloys by means of in situ electrical resistivity measurements [J]. Journal of Magnetism and Magnetic Materials, 2007, 316(1): 59-66.
[4] OKABE F, PARK H S, SHINDO D, PARK Y G, OHASHI K, TAWARA Y. Microstructures and magnetic domain structures of sintered Sm(Co0.720Fe0.200Cu0.055Zr0.025)7.5 permanent magnet studied by transmission electron microscopy [J]. Mater Trans, 2006, 47(1): 218-223.
[5] GOPALAN R, OHKUBO T, HONO K. Identification of the cell boundary phase in the isothermally aged commercial Sm(Co0.725- Fe0.1Cu0.12Zr0.04)7.4 sintered magnet [J]. Scripta Mater, 2006, 54(7): 1345-1349.
[6] GOLL D, KRONMULLER H, STADELMAIER H H. Micromagnetism and the microstructure of high-temperature permanent magnets [J]. J Appl Phys, 2004, 96(11): 6534-6545.
[7] DE Campos M F, NEIVA A C, ROMERO S A, MURAKAMI R K, RECHENBERG H R, MISSELL F P. The (SmZr)Co3 phase in Sm(CoFeCuZr)z magnets [J]. IEEE Trans on Magn, 2006, 42(11): 3770-3772.
[8] ZHANG Y, GABAY A M, HADJIPANAYIS G C. Observation of the lamellar phase in a Zr-free Sm (Co0.45Fe0.15Cu0.4)5 alloy[J]. Appl Phys Lett, 2005, 87(14): 141910.
[9] TANG W, ZHANG Y, HADJIPANAYIS G C. Effect of Zr on the microstructure and magnetic properties of Sm(CobalFe0.1Cu0.088Zrx)8.5 magnets [J]. J Appl Phys, 2000, 87 (1): 399-403.
[10] GOPALAN R, OHKUBO T, HONO K. Platelet microstructure and magnetic properties in rapidly solidified Sm20.8Co63.4Fe7.9Cu2.4Zr1.6B4 ribbons [J]. Scripta Mater, 2005, 53(3): 367-371.
[11] AICH S, RAVINDRAN V K, SHIELD J E. Highly coercive rapidly solidified Sm-Co alloys [J]. J Appl Phys, 2006, 99(8): 08B521.
[12] YAN A, GUTFLRISCH O, HANDSRWEIN A, GEMMING T, M?LLER K H. Microstructure, microchemistry, and magnetic properties of melt-spun Sm(Co, Fe, Cu, Zr)z magnets [J]. J Appl Phys, 2003, 93(103): 7975-7977.
[13] PLUGARU N, RUBIN J, BARTOLOME J. Structural and magnetic investigation of Co-rich Sm-Co unidirectionally solidified alloys [J]. J Alloys Compd, 2007, 433(1/2): 129-139.
[14] TANG H, LIU Y, SELLMYER D J. Nanocrystalline Sm12.5(Co,Zr)87.5 magnets: Synthesis and magnetic properties [J]. J Magn Magn Mater, 2002, 241(2/3): 345-356.
[15] GOPALAN R, XIONG X Y, OHKUBO T, HONO K. Nanoscale microstructure and magnetic properties of melt-spun Sm(Co0.725- Fe0.1Cu0.12Zr0.04B0.015)7.4 ribbons [J]. J Magn Magn Mater, 2005, 295(1): 7-20.
[16] LIVNGSTON J D, MARTIN D L. Microstructure of aged (Co, Cu, Fe)7Sm magnets [J]. J Appl Phys, 1977, 48(3): 1350-1354.
[17] XIONG X Y, OHKUBO T, KOYAMA Y, OHASHI K, YAWARA Y, Hono K. The microstructure of sintered Sm(Co0.72Fe0.20- Cu0.055Zr0.025)7.5 permanent magnet studied by atom probe [J]. Acta Mater, 2004, 52(3): 737-748.
[18] ZHANG Y, CORTE-REAL M, HADJIPANAYIS G C. Magnetic hardening studies in sintered Sm(Co, Cux, Fe, Zr)z 2?17 high temperature magnets [J]. J Appl Phys, 2000, 87(9): 6722-6724.
(Edited by PENG Chao-qun)
Foundation item: Project(04JJ6029) supported by the Natural Science Foundation of Hunan Province, China
Corresponding author: LI Li-ya; Tel: +86-731-8877328; E-mail: llylucky@163.com