文章编号:1004-0609(2015)-11-3033-07
Al-Cu-Mg-Ag新型耐热铝合金的抗腐蚀性能
齐 浩,刘晓艳,梁顺星,张喜亮,崔好选,高 飞,陈啟怀
(河北工程大学 装备制造学院,邯郸 056038)
摘 要:通过晶间腐蚀、剥落腐蚀、电化学和透射电镜等方法研究热处理制度对Al-Cu-Mg-Ag耐热铝合金组织与抗腐蚀性能的影响。结果表明:随着时效时间的延长,合金晶内和晶界析出相逐渐长大,晶界析出相由连续分布转变为不连续分布,无沉淀析出带(PFZ)逐渐变宽,合金的抗晶界腐蚀性能和抗剥落腐蚀性能逐渐降低。基体腐蚀电位φmatrix、PFZ腐蚀电位φPFZ和晶界析出相腐蚀电位φθ在晶间腐蚀液和剥落腐蚀液中符合φmatrix>φθ>φPFZ。具有最低腐蚀电位的PFZ决定了合金的抗腐蚀性能。随着时效时间的延长,晶界析出相的粗化使得PFZ变宽,Cu原子减少,电位负移,PFZ与基体的电位差变大,腐蚀通道变宽,合金的耐蚀性降低。不同时效状态的Al-Cu-Mg-Ag耐热铝合金的抗腐蚀能力由强至弱的顺序为:欠时效的,峰时效的,过时效的。
关键词:Al-Cu-Mg-Ag;耐热铝合金;晶间腐蚀;剥落腐蚀;无沉淀析出带
中图分类号:TG174.3 文献标志码:A
Corrosion resistance of Al-Cu-Mg-Ag new heat-resistant Al alloy
QI Hao, LIU Xiao-yan, LIANG Shun-xing, ZHANG Xi-liang, CUI Hao-xuan, GAO Fei, CHEN Qi-huai
(College of Equipment Manufacture, Hebei University of Engineering, Handan 056038, China)
Abstract: The effects of the aging treatment on the microstructure and the corrosion resistance of Al-Cu-Mg-Ag heat-resistant aluminium alloy were studied by intergranular corrosion, exfoliation corrosion, electrochemical analysis and transmission electron microcopy. The results show that with increasing aging time, the precipitations both in the grains and on the grain boundaries grow, the distribution of the precipitations on the grain boundaries transforms from continuous to discontinuous, and the precipitation free zone (PFZ) widens, the intergranular corrosion resistance and the exfoliation corrosion resistance decrease. The self-corrosion potential of the matrix φmatrix, precipitations on the grain boundaries φθ and the PFZ tested φPFZ both in the intergranular corrosion solution and exfoliation corrosion solution satisfy φmatrix>φθ>φPFZ. The corrosion resistance of Al-Cu-Mg-Ag alloy is determined by PFZ with the lowest self-corrosion potential. With increasing aging time, the PFZ widens with less Cu solution atoms, leading to lower potential and wider corrosion passageway. This results in the larger potential difference between the matrix and the PFZ, and the corrosion resistance correspondingly decreases. The corrosion resistance of Al-Cu-Mg-Ag heat-resistant aluminium alloy changing from high to low are as follows: under-aged, peak-aged, over-aged.
Key words: Al-Cu-Mg-Ag; heat-resistant alloy; intergranular corrosion; exfoliation corrosion; precipitation free zone
铝合金以其较低的密度、较高的比强度、良好的耐蚀性和成型性、较低的成本等优点被广泛应用于航空工业。现代飞机正向大型、高速、多载方向发展,对铝合金的强度、耐热性、可靠性和高寿命等提出了更高的要求。Al-Cu-Mg-Ag合金是在传统变形耐热铝合金基础上发展起来的一种新型航空铝合金材料。研究发现,在2014、2219和2519等高Cu/Mg比传统变形耐热铝合金中添加微量Ag后,合金中析出了一种新相即Ω相。该时效析出相有优良的热稳定性,在200 ℃长时间暴露时,片层长大速度非常缓慢,1000 h后厚度仍小于6 nm[1],合金的高温性能得到大幅度提高[2-4]。与2618和2219合金相比,含Ag的Al-Cu-Mg合金的室温抗拉强度分别提高30%和43%,300 ℃时合金的抗拉强度均提高200%以上[5]。因此,Al-Cu-Mg-Ag新型耐热铝合金有望满足新一代飞机的强度、耐热性和经济性要求,在航空领域有广阔的应用前景[6-7]。
目前国内外研究主要针对Al-Cu-Mg-Ag合金的显微组织与力学性能,对于该体系合金的腐蚀性能研究很少。腐蚀是铝合金一种主要失效形式,为此对该系合金腐蚀性能的研究具有重要的科学和工程意义。对于变形铝合金,腐蚀主要类型是晶间腐蚀和剥落腐蚀。晶间腐蚀是材料在特定的腐蚀环境中沿着晶界发生的腐蚀。这种腐蚀从材料表面开始,沿着晶界向基体内部发展,使晶粒间的结合力大幅度降低甚至丧失。因此晶间腐蚀是一种危害性极大的局部腐蚀。剥落腐蚀是一种特殊形式的晶间腐蚀,一般发生在轧制或锻压形成的型材,也会导致材料的强度和塑性大幅度降低。晶间腐蚀和剥落腐蚀均属于电化学腐蚀,一般都用阳极溶解来解释铝合金晶间腐蚀与剥落腐蚀机理[8-12]。为此,本文作者根据晶界附近化学成分与结构的不同,制备了模拟PFZ、晶界析出相和基体的材料,并对其开路电位进行测试,结合Al-Cu-Mg-Ag合金的显微组织与晶间腐蚀和剥落腐蚀试验结果,对其腐蚀机理进行阐释,为提高Al-Cu-Mg-Ag基耐热铝合金的耐蚀性提供了理论依据。
1 实验
1.1 样品制备
采用工业纯铝、纯镁和纯银与Al-Cu、Al-Mn和Al-Zr中间合金,利用铸锭冶金的方法制备Al-5.3Cu-0.8Mg-0.5Ag-0.3Mn-0.15Zr(质量分数,%)合金铸锭。铸锭在500 ℃下均匀化处理24 h后,在460 ℃下热轧至6 mm厚,经过(400 ℃,2 h)中间退火后,冷轧至3 mm厚的薄板。将冷轧板于515 ℃下固溶处理1.5 h后在185 ℃下进行时效处理,取不同时效时间的试样进行腐蚀性能测试。根据前期研究结果[13],该合金在185 ℃的峰值时效时间为4 h,所以在研究时效时间对合金抗腐蚀性能的影响时,时间点分别取1 h(欠时效)、4 h(峰时效)和24 h(过时效)。
1.2 性能测试与组织观察
晶间腐蚀试验参照国标GB/T7998-2005,每组3个试样,腐蚀液为3%NaCl+10 mL/L H2O2,试样表面积与试验溶液体积之比小于20 mm2/mL,在(35±2) ℃下腐蚀6 h。腐蚀结束后在垂直于主变形方向切去5 mm,用蒸馏水冲洗干净后重新镶样,再进行机械抛光,最后用Olympus DSX500型全自动光学数码显微镜观察,测量晶间腐蚀最大深度,并根据标准得出晶间腐蚀等级。
剥落腐蚀试验参照国际标准ASTM/G 34-01,EXCO溶液中NaCl、KNO3、HNO3的浓度分别为4.0、0.5和0.l mol/L,试验溶液体积与试样表面积之比为20 mL/cm2。用恒温水浴箱在(25±3) ℃下腐蚀96 h。腐蚀结束用流水冲洗干净并拍照,最后根据标准对试样进行腐蚀评级。
利用电化学工作站分别测试试样在晶间腐蚀液和剥落腐蚀液中的极化曲线。采用三电极体系,试样为工作电极,饱和甘汞为参比电极,铂片为辅助电极。极化曲线扫描速率为1 mV/s。
采用纯铝模拟PFZ、Al2Cu铸锭模拟θ相,淬火态Al-Cu-Mg-Ag合金模拟基体。采用电化学工作站对3种材料在晶间腐蚀液和剥落腐蚀液中的开路电位进行测量,扫描范围是1.0 V~-1.0 V,扫描速率为1 mV/s。
在 TECNAI G2 20型TEM上进行试样晶界组织观察。透射电镜试样经机械预减薄后电解双喷穿孔而成,电解液为硝酸和甲醇(体积比为1:3),温度控制在-20 ℃以下。
2 结果与分析
2.1 晶间腐蚀
图1所示为Al-Cu-Mg-Ag耐热铝合金晶间腐蚀后的截面形貌。由图1可知,合金经欠时效处理后,晶间腐蚀深度较浅(见图1(a)),说明此时合金的抗晶间腐蚀性能比较好。合金经峰时效处理后,腐蚀深度加深,有部分晶粒已经脱落(见图1(b))。经过时效后,腐蚀深度进一步加深(见图1(c))。从低倍照片中可以看出,过时效态合金腐蚀严重,有大量晶粒从基体表面脱落(见图1(d))。
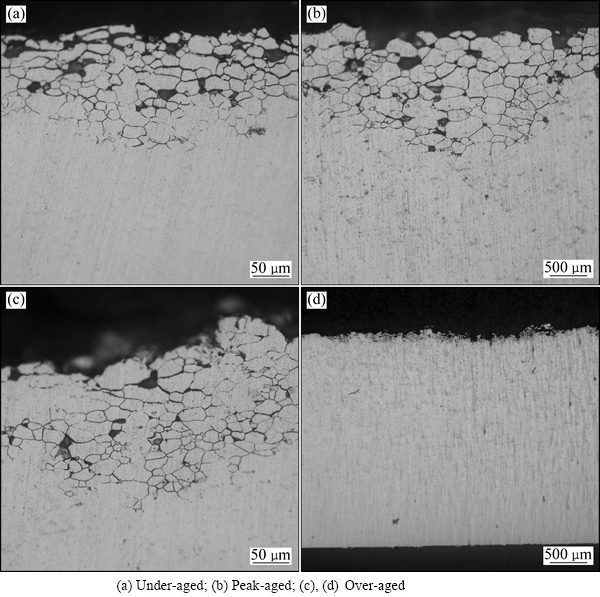
图1 不同时效制度Al-Cu-Mg-Ag合金晶间腐蚀后横截面形貌
Fig. 1 Cross-section morphologies of aged Al-Cu-Mg-Ag alloy after intergranular corrosion
利用金相显微镜对Al-Cu-Mg-Ag合金腐蚀深度进行定量测量,并根据国标对腐蚀等级进行评价,结果列于表1。由表1可知,尽管欠时效、峰时效、过时效试样的晶间腐蚀等级均为4,但不同时效状态合金的最大腐蚀深度差异较大。随着时效时间的延长,腐蚀深度依次增大,从欠时效态的104.257 μm到过时效态的214.992 μm。由晶间腐蚀实验结果可知,不同热处理后的合金抗晶间腐蚀能力由大到小的顺序如下:欠时效的、峰时效的、过时效的。
表1 不同时效态Al-Cu-Mg-Ag合金晶间腐蚀深度和腐蚀等级
Table 1 Maximum IGC corrosion depth and corrosion level of different aged Al-Cu-Mg-Ag alloys

2.2 剥落腐蚀
图2所示为不同时效处理后Al-Cu-Mg-Ag合金在剥落腐蚀液中浸泡不同时间后的宏观形貌。由图2可见,热处理状态对合金的抗剥落腐蚀性能影响很大。浸泡12 h后,欠时效态合金腐蚀不明显(见图2(a)),峰时效态合金发生了轻微点蚀(见图2(c)),过时效态合金点蚀严重(见图2(e))。浸泡96 h后,不同时效状态的合金均发生了剥蚀,欠时效态合金有少量的腐蚀产物已经发生脱落(见图2(b)),随着时效时间的延长,合金表面腐蚀产物大面积的脱落(见图2(d)),过时效态合金有部分位置已经出现多层剥落(见图2(f))。
根据ASTM标准对不同热处理状态的Al-Cu-Mg-Ag合金进行剥落腐蚀评级,结果列于表2。由表2可见,欠时效态合金的剥落腐蚀发展较为缓慢,随着时效时间的延长,剥落速率逐渐增大。剥落腐蚀试验结果表明,不同时效状态Al-Cu-Mg-Ag合金的腐蚀敏感性由强至弱的顺序如下:过时效的、峰时效的、欠时效的。
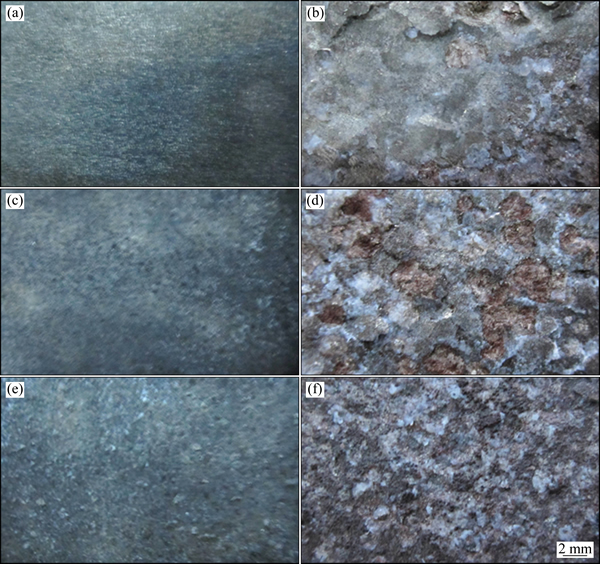
图2 Al-Cu-Mg-Ag合金在剥落腐蚀液中浸泡不同时间后的宏观形貌
Fig. 2 Macrographs of aged Al-Cu-Mg-Ag alloy immersion in exfoliation solution for 12 h (a) and 96 h (b) for under-aged sample, 12 h (c) and 96 h (d) for peak-aged sample, 12 h (e) and 96 h (f) for over-aged sample
表2 Al-Cu-Mg-Ag合金在剥蚀腐蚀液中浸泡不同时间后的腐蚀等级评价结果
Table 2 Corrosion evaluation results of Al-Cu-Mg-Ag alloy immersion in EXCO solution for different time
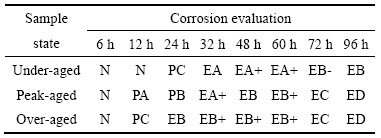
2.3 电化学分析
不同热处理状态Al-Cu-Mg-Ag合金在晶间腐蚀液中的极化曲线如图3所示。由图3可知,随着时效时间的延长,Al-Cu-Mg-Ag合金的极化电位逐渐降低,而自腐蚀电流逐渐增大,相应的极化电阻逐渐减小,说明合金的抗腐蚀能力随着时效时间的延长逐渐减弱。不同时效态合金抗晶间腐蚀能力由大到小的顺序如下:欠时效、峰时效的、过时效的,这与晶间腐蚀实验结果一致。
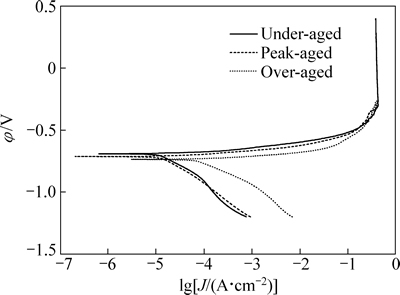
图3 Al-Cu-Mg-Ag合金在晶间腐蚀液中的极化曲线
Fig. 3 Polarization curves of aged Al-Cu-Mg-Ag alloy tested in IGC solution
图4所示为Al-Cu-Mg-Ag合金在剥落腐蚀液中测得的极化曲线。结果显示,合金在剥落腐蚀液中各腐蚀参数的变化规律与晶间腐蚀液中所得结果一致,随着时效时间的延长,合金极化电位逐渐降低,而自腐蚀电流逐渐增大,合金的抗剥落腐蚀能力逐渐减弱。Al-Cu-Mg-Ag合金抗剥落腐蚀能力由大至小的顺序如下:欠时效的、峰时效的、过时效的。这与剥落腐蚀实验所得到的结果一致。
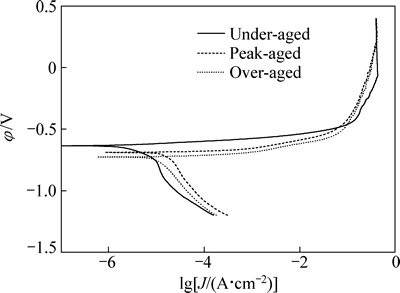
图4 Al-Cu-Mg-Ag合金在剥落腐蚀液中的极化曲线
Fig. 4 Polarization curves of aged Al-Cu-Mg-Ag alloy tested in EXCO solution
2.4 显微组织
图5所示为Al-Cu-Mg-Ag合金经不同时效处理后的TEM像。由图5可知,时效处理对合金显微组织影响很大。时效处理1 h后,合金中晶内析出了大量细小的Ω相,尺寸约为5 nm(见图5(a))。与晶内析出相相比,晶界析出相明显粗大,这些析出相沿晶界连续分布(见图5(b))。随着时效时间的延长,晶内与晶界上的析出相逐渐长大。由图5(c)可见,峰时效态试样晶内析出了大量弥散的Ω相,尺寸约为80 nm,晶界上的析出相与欠时效态试样的相比更加粗大,并且不连续分布。同时可以观察到峰时效态试样在晶界附近出现了明显的无沉淀析出带(PFZ),宽度约为90 nm。对于过时效态试样,晶内和晶界析出相进一步粗化,晶界析出相更加不连续,PFZ宽度增加到120 nm(见图5(d))。
3 讨论

图5 不同热处理状态下Al-Cu-Mg-Ag合金的TEM像
Fig. 5 TEM images of aged Al-Cu-Mg-Ag alloys
由以上实验结果可知,时效制度对Al-Cu-Mg-Ag合金组织与腐蚀性能影响很大。随着时效时间的延长,合金晶内和晶界析出相逐渐长大、粗化,晶界上的析出相由连续逐渐变得不连续,PFZ逐渐变宽,合金的耐蚀性逐渐降低。晶间腐蚀与剥落腐蚀均属于电化学腐蚀,一般发生在电位较低的晶界附近。晶界附近不同结构的腐蚀电位决定合金的耐蚀性。对于Al-Cu-Mg-Ag合金,晶界附近不同的组织主要有晶界析出相、PFZ和晶内基体。但是由于这些结构均为纳米级,很难测出其腐蚀电位。LI等[14]采用TEM对Al-4%Cu在NaCl溶液中浸蚀2 h后的显微组织进行观察,发现晶内一些粗大的θ相附近已被腐蚀,而θ相本身并未被腐蚀。为了解释该现象,他们采用纯铝模拟铝合金基体或PFZ,采用Al2Cu模拟θ相,研究了二者的电位,发现θ相的腐蚀电位明显高于纯铝的。为此,在电化学腐蚀中,θ相附近区域作为阳极优先溶解,而θ相作为阴极,不会受到腐蚀。根据这一研究思路可知,PFZ、晶界析出相和基体的腐蚀电位的比较可直接用来阐释本试验结果。
Al-Cu-Mg-Ag合金的主要强化相是Ω相和少量的θ′相[15],其时效脱溶序列可表示为[16]
SSS→Mg cluster/Mg-Ag co-cluster→
Ω(Al2Cu)→θ(Al2Cu)
SSS→Cu cluster (GPⅠ)→
GPⅡ/θ″→θ′ (Al2Cu)→θ(Al2Cu)
所以Al-Cu-Mg-Ag合金的晶内和晶界的平衡相均为θ(Al2Cu)。为此本实验采用铸态Al2Cu模拟晶界析出相-θ相,采用纯铝模拟PFZ,采用淬火态Al-Cu-Mg-Ag合金模拟基体,分别在晶间腐蚀液和剥落腐蚀液中对这3种材料的开路电位进行测试,结果列于表3。
由表3可知,尽管不同材料在晶间腐蚀液和剥落腐蚀液中的自腐蚀电位数值不同,但变化规律均一致,为φmatrix>φθ>φPFZ。其中基体电位最高,在电化学腐蚀中作为阴极,而PFZ电位最低,在电化学腐蚀中作为阳极,优先腐蚀。因此,Al-Cu-Mg-Ag系耐热铝合金的电化学腐蚀性能主要取决于PFZ。
表3 θ相、PFZ及Al基体在不同介质中的开路电位
Table 3 Open circuit potential of θ, PFZ and matrix tested in different solutions
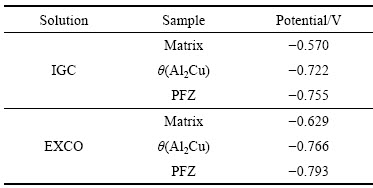
对于欠时效态合金,由于晶界析出相较小,PFZ不明显,晶界附近还有大量的Cu溶质原子,此时晶界附近结构的电位较高,与基体的电位差较小,合金的耐蚀性良好。随着时效时间的延长,晶界上的析出相逐渐粗化,使得晶界附近溶质原子大幅度减小,峰时效态试样中形成了一定宽度的PFZ,并且由于PFZ内的Cu原子减少,其电位负移[17],与基体的电位差增大,电化学腐蚀性能降低。进一步延长时效时间,晶界析出相更加粗化,PFZ内的溶质原子Cu进一步减少,电位降低,与基体的电位差进一步增大,导致合金腐蚀敏感性增加。另一方面,过时效态合金中较宽的PFZ在电化学腐蚀中提供了更宽的腐蚀通道,导致合金的耐蚀性大幅度降低。综上所述,不同时效态Al-Cu-Mg-Ag合金抗腐蚀能力大小为:欠时效的>峰时效的>过时效的。
4 结论
1) 随着时效时间的延长,Al-Cu-Mg-Ag合金晶内和晶界析出相逐渐长大,晶界析出相的粗化速率明显高于晶内析出相的,晶界析出相由连续分布逐渐变得不连续,PFZ宽度逐渐增大。
2) 随着热处理时间的延长,Al-Cu-Mg-Ag合金的极化电压逐渐减小,极化电流逐渐增大,抗腐蚀能力逐渐减弱。不同热处理后的Al-Cu-Mg-Ag抗晶间腐蚀和剥落腐蚀能力由大至小的顺序如下:欠时效的、峰时效的、过时效的。
3) 基体、PFZ和晶界析出相的在晶间腐蚀液和剥落腐蚀液中的自腐蚀电位符合φmatrix>φθ>φPFZ。PFZ在电化学腐蚀中作为阳极优先腐蚀。
REFERENCES
[1] HUTCHINSON C R, FAN X, PENNYCOOK S J, SHIFLET G J. On the origin of the high coarsening resistance of Ω plates in Al-Cu-Mg-Ag alloys[J]. Acta Materialia, 2001, 49(14): 2827-2841.
[2] ZHANG J B, ZHANG Y A, ZHU B H, LIU R Q, WANG F, LIANG Q M. Characterization of microstructure and mechanical properties ofAl-Cu-Mg-Ag-(Mn/Zr)alloywith highCu:Mg[J]. Materials & Design,2013, 49: 311-317.
[3] LIU X Y, PAN Q L, ZHANG X L, LIANG S X, GAO F, ZHENG L Y, LI M X. Creep behavior and microstructural evolution of deformed Al-Cu-Mg-Ag heat resistant alloy[J]. Materials Science and Engineering A, 2014, 599: 160-165.
[4] BAI S, ZHOU X W, LIU Z Y, XIA P, LIU M, ZENG S M. Effects ofAgvariations on the microstructures and mechanical properties ofAl-Cu-Mg alloysat elevated temperatures[J]. Materials Science and Engineering A,2014,611: 69-76.
[5] 肖代红. 微合金化对Al–Cu–Mg基耐热铝合金的显微组织和力学性能的影响[D]. 上海: 上海交通大学, 2004.
XIAO Dai-hong. Effects of microalloyed on the microstructure and mechanical properties of Al-Cu-Mg based heat-resistant aluminium alloy[D]. Shanghai: Shanghai Jiao Tong University, 2004.
[6] 张 坤, 戴圣龙, 杨守杰, 黄 敏, 颜鸣皋. Al–Cu–Mg–Ag系新型耐热铝合金研究进展[J]. 航空材料学报, 2006, 26(3): 251-257.
ZHANG Kun, DAI Sheng-long, YANG Shou-jie, HUANG Min, YAN Ming-gao. Development of a new creep resistant Al-Cu-Mg-Ag type alloy[J]. Journal of Aeronautical Materials, 2006, 26(3): 251-257.
[7] 宋艳芳, 潘清林, 丰 雷, 王 迎, 李 晨. Mg含量对Al-Cu-Mg-Ag合金组织与力学性能的影响[J]. 中国有色金属学报, 2013, 23(7): 1812-1818.
SONG Yan-fang, PAN Qing-lin, FENG Lei, WANG Ying, LI Chen. Effects of Mg content on microstructure and mechanical properties of Al-Cu-Mg-Ag alloy[J]. The Chinese Journal of Nonferrous Metals, 2013, 23(7): 1812-1818.
[8] MENG C, ZHANG D, CUI H, ZHUANG L, ZHANG J. Mechanical properties,intergranular corrosionbehavior and microstructure of Zn modifiedAl-Mgalloys[J]. Journal ofAlloysand Compounds,2014, 61: 925-932.
[9] WANG Z, LI H, MIAO F, SUN W, FANG B, SONG R, ZHENG Z. Improving theintergranular corrosion resistance of Al-Mg-Si-Cu alloys without strength loss by a two-step aging treatment[J]. Materials Science and Engineering A,2014,590: 267-273.
[10] LI H, MAO Q, WANG Z, MIAO F, FANG B, SONG R, ZHENG Z. Simultaneously enhancing the tensile properties and intergranular corrosion resistance of Al-Mg-Si-Cu alloys by a thermo-mechanical treatment[J]. Materials Science and Engineering A, 2014, 617: 165-174.
[11] FANG H C, CHAO H, CHEN K H. Effect of recrystallization on intergranular fracture and corrosion of Al-Zn-Mg-Cu-Zr alloy[J]. Journal of Alloys and Compounds, 2015, 622: 166-173.
[12]
, ANDRIEU E, ODEMER G, ALEXIS J, BLANC C. Effect of varying conditions of exposure to an aggressive medium on the corrosion behavior of the 2050 Al-Cu-Li alloy[J]. Corrosion Science, 2014, 85: 455-470.
[13] LIU X Y, PAN Q L, ZHENG L Y, FU Q R, GAO F, LI M X, BAI Y M. Effect of aging temper on the thermal stability of Al-Cu-Mg-Ag heat-resistant alloy[J]. Materials & Design, 2013, 46: 360-365.
[14] LI J F, ZHENG Z Q, LI S C, CHEN W J, REN W D, ZHAO X S. Simulation studyonfunction mechanismof some precipitates in localized corrosion of Al alloys[J]. Corrosion Science,2007,49 (6): 2436-2449.
[15] LIU X Y, PAN Q L, LU C G, HE Y B, LI W B, LIANG W J. Microstructure and mechanical properties of Al-Cu-Mg-Mn-Zr alloy with trace amounts of Ag[J]. Materials Science and Engineering A, 2009, 525: 128-132.
[16] RINGER S P, HONO K. Nucleation of precipitates in aged Al-Cu-Mg-(Ag) alloys with high Cu:Mg ratios[J]. Acta Materialia, 1996, 44(5): 1883-1898.
[17] KHIRECHE S, BOUGHRARA D, KADRI A, HAMADOU L, BENBRAHIM N. Corrosion mechanism of Al, Al-Zn and Al-Zn-Sn alloys in 3wt.% NaCl solution[J]. CorrosionScience, 2014, 87: 504-516.
(编辑 王 超)
基金项目:河北省自然科学基金资助项目(E2013402056);河北省高等学校科学技术研究项目(QN2014002);邯郸市科学技术研究与发展计划项目(1321110085-4)
收稿日期:2015-04-19;修订日期:2015-08-28
通信作者:刘晓艳,副教授,博士;电话:0310-8577971;E-mail:x918y@126.com