J. Cent. South Univ. (2012) 19: 1341-1345
DOI: 10.1007/s11771-012-1147-6
Advanced run-out table cooling technology based on ultra fast cooling and laminar cooling in hot strip mill
LIU En-yang(刘恩洋), PENG Liang-gui(彭良贵),YUAN Guo(袁国),
WANG Zhao-dong(王昭东), ZHANG Dian-hua(张殿华), WANG Guo-dong(王国栋)
State Key Laboratory of Rolling and Automation, Northeastern University, Shenyang 110819, China
? Central South University Press and Springer-Verlag Berlin Heidelberg 2012
Abstract: In order to meet the severe requirements of market and reduce production costs of high quality steels, advanced run-out table cooling based on ultra fast cooling (UFC) and laminar cooling (LC) was proposed and applied to industrial production. Cooling mechanism of UFC and LC was introduced first, and then the control system and control models were described. By using UFC and LC, low-cost Q345B strips had been produced in a large scale, and industrial trials of producing low-cost dual phase strips were completed successfully. Application results show that the ultra fast cooling is uniform along the strip width and length, and does not affect the flatness of strips. The run-out table cooling system runs stably with a high precision, and makes it possible for the user to develop more high quality steels with low costs.
Key words: hot strip mill; ultra fast cooling; laminar cooling; run-out table cooling; control model; control system
1 Introduction
Run-out table cooling is one of the important parts of thermo-mechanical control process (TMCP), and the desired metallurgical structure and mechanical properties can be achieved by controlling the cooling rates and temperature of strips on the run-out table. Nowadays, the intension to both increase product quality and reduce product costs results in high demands on TMCP, so advanced cooling technology based on ultra fast cooling (UFC) and laminar cooling (LC) was proposed [1-4].
In 1990s, the ultra fast cooling system for hot strip mill was first developed by CRM of Belgium, which could realize cooling rates in the range of 250-500 °C/s for hot strip thicknesses between 6 mm and 3 mm [5-6]. These cooling rates were more than 5 times larger than that obtained by the classical run-out table cooling, such as laminar cooling [7]. In 2002, NKK’s Fukuyama Works completed installation of the Super-OLAC H (on-line accelerated cooling for hot strip mill) system at the run-out cooling zone of its No. 1 hot strip mill. The Super-OLAC H system could attain a cooling rate of 700 °C/s for a sheet thickness of 3 mm, which is close to the theoretical limit of cooling rate [8-9].
In China, simple ultra fast cooling system for hot strip mill was developed and installed at the compact strip production (CSP) line of Baotou Iron and Steel (Group) Co., and it has enabled stable production of 500 MPa and 600 MPa dual phase steel strips [10]. In recent years, ultra fast cooling equipments were installed in a hot strip mill, and the cooling rate can reach 300 °C/s for strips with thickness of 3 mm. Cooling mechanism, control system, control models and application results of run-out table cooling, including ultra fast cooling and laminar cooling, are described in this work.
2 Cooling mechanism of run-out table cooling
2.1 Laminar cooling
Laminar cooling is one of the most common cooling ways in hot strip mill. Several modes of heat transfer occur during laminar cooling and have been previously classified by ZUMBRUNNEN et al [11], including single phase forced convection, nucleate/transition boiling, and forced convection film boiling, etc. These modes occur in two hydrodynamic zones: the impingement zone (under the spray nozzle in the vicinity of the stagnation point) and the parallel flow zone (at a certain distance from the beneath of spray nozzle). Because of high orientation of the spray nozzle, which prevents development of inefficient film boiling, the impingement zone has the highest cooling efficiency. Outside the impingement zone, cooling water usually rides on the strip surface in the direction of strip traveling. Then, the film boiling phenomenon, which occurs from the residual water, is the most frequently occurring mechanism in laminar cooling, although the magnitude is much smaller than that within the impingement zone [12-14].
During laminar cooling process, the top side cooling water remains on the strip until it is blown off by cross sprays. At the start of cooling, the strip surface is high and film boiling is predominant. However, as the strip temperature decreases, transition boiling even nucleate boiling takes place. Because heat flux density changes significantly when the cooling proceeds, laminar cooling becomes unstable and results in unstable strip quality [15]. In order to solve this problem and get the higher cooling rates, the ultra fast cooling system was developed.
2.2 Ultra fast cooling
The ultra fast cooling equipments are installed at the exit of the last finishing mill, in front of the laminar cooling equipments, and the total length is about 10 m. Bottom spray headers are installed between rollers of run-out table. The distance between top side headers and surface of rollers is 300-600 mm, much smaller than that of laminar cooling. The diameter of UFC spray nozzles is reduced, and much more nozzles are densely arranged on the cooling banks than laminar cooling. In order to break up steam film on the surface of strips effectively, spray headers are inclined to an angle in the direction of strip motion and cooling water is impinged out at a pressure of 0.3-1.0 MPa, which can be tuned according to cooling strategies.
Ultra fast cooling system avoids transition boiling and achieves a nucleate boiling over the entire strip surface almost with the start of cooling, and realizes a high cooling capacity on both the top and bottom sides of strips. It is possible to obtain a uniform surface temperature distribution after ultra fast cooling and the flatness is not affected.
3 Control system of run-out table cooling
The structure of run-out table cooling control system which includes UFC and LC is shown in Fig. 1. Three pyrometers are installed on the run-out table to measure real temperatures of strips. PY401 is used to measure entry temperature of UFC, which is the same as the finishing delivery temperature (FDT). The intermediate temperature (MT) can be obtained by PY402. When the strip leaves the cooling zone and goes to the down coiler, coiling temperature (CT) can be obtained by PY403. Air sweeps are located after or before each pyrometer to facilitate accurate temperature measurement.
From the control point of view, the cooling section can be divided into two parts: ultra fast cooling and laminar cooling. The last three spray headers of UFC are used for feedback control and others for main cooling. Laminar cooling consists of main cooling section and trimming section, and trimming section is used for trimming and feedback control. The control system of run-out table cooling comprises process automation (Level 2) and basic automation (Level 1). Nearly all of the functions, such as feedforward control, feedback control, and self learning, are realized in process automation. Basic automation is responsible for data collection and executing the setup results of process automation. The structure of the run-out table cooling control system is similar to that of the laminar cooling control system described in Refs. [16] and [17].
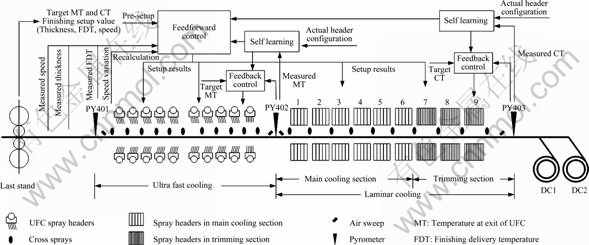
Fig. 1 Structure of run-out table cooling control system (UFC + LC)
4 Control models of run-out table cooling
Heat transfer process is extremely complex during run-out table cooling, mainly including radiative heat transfer, convective heat transfer with the ambient and cooling water, conductive heat transfer between strip and run-out table, and latent heat when strip is cooled.
4.1 Air cooling model
When the strip on the run-out table is not cooled by water, it loses heat through radiation, convection with the ambient and conduction with run-out table rollers. As finishing delivery temperature is usually very high (more than 850 °C), radiation is predominant. According to the law of STEFAN-BOLTZMANN [18], heat transferred by radiation during time dτ is
(1)
where ε is strip emissivity, which depends on the thickness of the oxide layer that forms during cooling, and its value is usually between 0.7 and 0.9; σ is Stefan-Boltzmann constant, 5.67×10-8 W/(m2·K4); F is radiating area of top surface, which is equal to that of bottom surface (side area of strip is neglected), m2; T is absolute temperature of strip, K; Ta is absolute temperature of the ambient, K.
On the other hand, as strip dissipates heat to the ambient, strip temperature decreases at the same time. If strip temperature decreases dT during time dτ, the heat loss is
(2)
where ρ is density of the strip, kg/m3; cp is specific heat, J/(kg·K); h is strip thickness, m.
Combining Eqs. (1) and (2), air cooling model can be obtained as
(3)
where αa is equivalent heat transfer coefficient of air cooling, W/(m2·K).
(4)
4.2 Water cooling model
Water cooling process is particularly complicated. Forced convection occurs during water cooling. According to Newton’s law of cooling [18], there is
(5)
where Tw is absolute temperature of cooling water, K; αw is heat transfer coefficient, W/(m2·K).
Water cooling model can be obtained from Eq. (5) and expressed as
(6)
Heat transfer coefficient αw is closely related to cooling water temperature, flow rate, pressure and strip speed, etc. It can be determined by empirical formula and must be modified by self learning using real time data. Flow rate and pressure of ultra fast cooling can be tuned, and they are usually much higher than those of laminar cooling. The heat transfer coefficient of ultra fast cooling is about 2-6 times that of laminar cooling.
Taking phase transformation heat into consideration, the final run-out table cooling control model can be expressed as
(7)
where q is the internal heat generation per unit time and per unit volume, J/(m3·s).
5 Results of application
The run-out table cooling system (including ultra fast cooling and laminar cooling) was installed and applied online in 2009, and then a series of industrial trial productions were conducted. Ultra fast cooling capacity was tested and its effect on mechanical properties of C-Mn steels was compared. In a trial production, two kinds of cooling processes were used for Q235B slabs: laminar cooling only and ultra fast cooling combined with laminar cooling. Strips are of the same specifications (with thickness of 7.5 mm) and chemical compositions, and two of them under different cooling processes were decoiled for sampling along the strip length. Table 1 gives chemical compositions of strips. Ten samples in all were taken on the positions of 6, 24, 186, 276 and 322 m from the strip tail end. On each position, two samples were taken, one on the operating side and the other on the driving side. The average yield strength, tensile strength, and elongation of each position are shown in Fig. 2, and the deviation of mechanical properties of samples on the operating side and driving side is shown in Fig. 3.
Table 1 Chemical compositions of strips (mass fraction, %)

As shown in Fig. 2, mechanical properties of the strip cooled by UFC and LC are relatively uniform along the strip length. The yield strength and tensile strength of the strip cooled by UFC and LC are about 70-100 MPa larger than those cooled by LC only, and the elongation reduces a little. Figure 3 shows that deviations of yield strength and tensile strength along strip width are within 16 MPa, and the elongation deviation is very small, which demonstrates that UFC is uniform along the strip width.
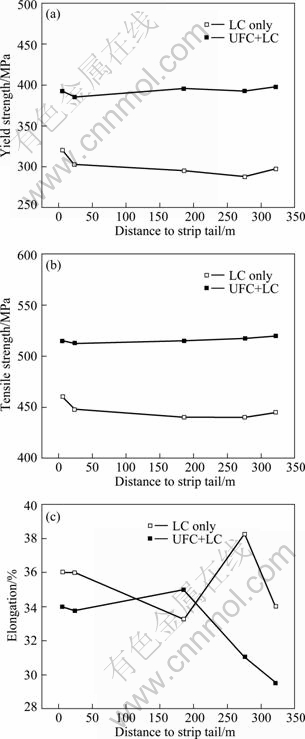
Fig. 2 Mechanical properties of strips under different cooling processes: (a) Yield strength; (b) Tensile strength; (c) Elongation
After tuning and optimization for several months, the run-out table cooling system runs stably with a high precision. Table 2 shows mechanical properties of a strip during normal production, whose chemical compositions are close to those in Table 1 and the thickness is 5.5 mm. During normal production, manganese content can be decreased by about 60% for Q345B strips if UFC is used, and production costs can be reduced by 150 RMB Yuan per ton. In addition, industrial trials of producing low-cost dual phase strips are completed successfully, which makes it possible for users to develop more high quality steels with low costs.
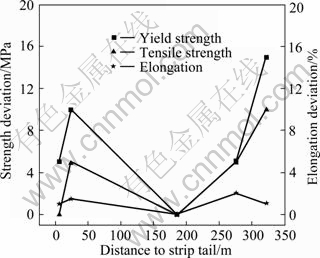
Fig. 3 Deviation of mechanical properties of strip cooled by UFC and LC
Table 2 Mechanical properties during normal production
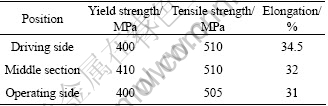
6 Conclusions
1) Cooling mechanism of run-out table cooling is introduced, including laminar cooling and ultra fast cooling, then control system and control models are described.
2) Application results show that the ultra fast cooling is homogeneous and does not affect the flatness of strips. Low-cost Q345B strips have been produced in a large scale by ultra fast cooling, and economic benefits are obtained.
3) The run-out table cooling system runs stably with a high precision, which lays a foundation for the user to develop new products with low costs by combining appropriate chemical compositions and cooling modes.
References
[1] SHIKANAI N, MITAO S, ENDO S. Recent development in microstructural control technologies through the thermo-mechanical control process (TMCP) with JFE steel’s high-performance plates [J]. JFE Technical Report, 2008, 11: 1-6.
[2] OMATA K, YOSHIMURA H, YAMAMOTO S. Leading high performance steel plates with advanced manufacturing technologies [J]. NKK Technical Review, 2003, 88: 73-80.
[3] WANG Guo-dong. New generation TMCP and innovative hot rolling process [J]. Journal of Northeastern University: Natural Science, 2009, 30(7): 913-922. (in Chinese)
[4] WANG Guo-dong. The new generation TMCP with the key technology of ultra fast cooling [J]. Shanghai Metals, 2008, 30(2): 1-5. (in Chinese)
[5] SIMON P, RICHE P. Ultra fast cooling in the hot strip mill [C]// Proceedings of 6th International Rolling Conference, Düsseldorf: VDEh, 1994: 179-183.
[6] HOUYOUX C, HERMAN J C, SIMON P, de BEEK M O, RICHE P. Metallurgical aspects of ultra fast cooling on a hot strip mill [J]. Revue de Metallurgie, 1997, 97: 58-59.
[7] SIMON P, FISCHBACH J P, RICHE P. Ultra fast cooling on the run-out table of the hot strip mill [J]. Revue de Metallurgie, 1996, 93(3): 409-415.
[8] Super-OLAC H introduced at hot strip mill for automotive steel sheet production [EB/OL]. [2002-06]. http://www.jfe-holdings.co.jp/ en/release/ nkk/42-5/art06.html.
[9] KAGECHIKA H. Production and technology of iron and steel in Japan during 2005 [J]. ISIJ International, 2006, 46(7): 939-958.
[10] WANG Guo-dong, LIU Xiang-hua, SUN Li-gang, LIU Zhe, LIU De-qin. Ultra fast cooling on Baotou CSP line and development of 590 MPa grade C-Mn low-cost hot-rolled dual phase steel [J]. Iron and Steel, 2008, 43(3): 49-52. (in Chinese)
[11] ZUMBRUNNEN D A, INCROPERA F P, VISKANTA R. Convective heat transfer distributions on a plate cooled by planar water jets [J]. Journal of Heat Transfer, 1989, 111(4): 889-896.
[12] GUO R M. Heat transfer of laminar flow cooling during strip acceleration on hot strip mill run-out tables [J]. Trans ISS-AIME, 1993, 8: 49-59.
[13] FILIPOVIC J, VISKANTA R, INCROPERA F P, VESLOCKI T A. Cooling of a moving steel strip by an array of round jets [J]. Steel research, 1994, 65(12): 541-547.
[14] COX S D, HARDY S J, PARKER D J. Influence of run-out table operation setup on hot strip quality, subject to initial strip condition: Heat transfer issues [J]. Ironmaking and Steelmaking, 2001, 28(5): 363-372.
[15] FUJIBAYASHI A, OMATA K. JFE steel’s advanced manufacturing technologies for high performance steel plates [J]. JFE Technical Report, 2005, 5: 10-15.
[16] XIE Hai-bo, ZHANG Zhong-ping, LIU Xiang-hua, WANG Guo-dong. System optimization and self-adaptation of model parameters in laminar cooling of hot rolling strip [J]. Journal of Central South University: Science and Technology, 2006, 37(2): 317-323. (in Chinese)
[17] LIU En-yang, PENG Liang-gui, ZHANG Dian-hua, CHEN Hua-xin, WANG Feng-xiang, GUO Hong-wei, YANG Gui-ling, WU Zong-liang. Research and application of laminar cooling control system under non-constant speed rolling [C]// Proceedings of the 10th International Conference on Steel Rolling. Beijing: Metallurgical Industry Press, 2010: 513-517.
[18] KARLEKAR B V, DESMOND R M. Engineering heat transfer [M]. New York: West Publishing Company, 1977: 215-247.
(Edited YANG Bing)
Foundation item: Project(50634030) supported by the National Natural Science Foundation of China
Received date: 2011-03-14; Accepted date: 2011-05-19
Corresponding author: LIU En-yang, PhD Candidate; Tel: +86-24-83686415; E-mail: enyangliu@126.com