
Surface treatment to improve corrosion resistance of
Al plate heat exchangers
Jong-Soon KIM, Tae-Ho KANG, In-Kwan KIM
Department of Mechanical Engineering, Pukyong National University, Busan, Korea
Received 2 March 2009; accepted 30 May 2009
Abstract:The correlations between thermal and physical properties were studied through thermal conductivity measurements, hardness tests, salt spray tests (AASS) among the surface treatment samples named K20, K40 with thickness of 20, 40 μm respectively and raw sample named K00. In thermal conductivity measurements, there are little differences among the samples as K00, K20 and K40, they exhibit 153.39, 150.69 and 149.76 W/(m?K), respectively. According to hardness tests, K00, K20 and K40 exhibit 87.9, 259.7 and 344.8 in Vickers values. In the result of salt spray tests to examine the effects on corrosion resistance, K00, K20 and K40 exhibit the grade of 3-5, 2.0-9.8 and 10, respectively. The mutual relation of the above results was analyzed. It is found that the surface treatments do not affect the thermal conductivity of aluminum and result in the improvement of physical properties. As a result of the technology, the surface improvement of aluminum alloy specimen is achieved without thermal degradation. It validates the ability of the aluminum plate heat exchangers with surface treatment to enhance the corrosion resistance. Present work is performed as the first fundamental threshold in the process of aluminum plate heat exchangers development to check out its possibility, therefore the next step-experimental and numerical study of practical aluminum plate heat exchangers will be made.
Key words: salt water spray test; corrosion resistance; plate heat exchanger; thermal conductivity; Vickers hardness
1 Introduction
Plate heat exchanger has been employed in various industry fields such as foodstuff industries, dairy product, heavy industries, seawater plant, chemical industry and power generation plant since its invention. Especially, surface corrosion of plate heat exchangers for seawater plant (OTEC equipment) and chemical fields might be causative of low performance for every kind of leakages. It results from exposure to various kinds of chemical steam and saline environment. Also it lets down durability and feasibility[1-2]. To fix them, titanium material was employed as plate heat exchanger element. The titanium is relatively more expansive than other light metal, so it is too difficult to be adapted to plate heat exchangers. Hence, low cost as well as high efficiency can be achieved through plate heat exchanger made with aluminum material. To accomplish these goals, it is necessary to improve the corrosion resistance of aluminum material to adapt various suitable methods such as surface treatment. A kind of ceramic surface treatment technologies was employed which has the excellent physical properties[3].
Measured thermal conductivities of PEO coatings were found to be at least an order of magnitude lower than typical values for corresponding bulk material. For coatings on Al and Mg, measured values are 1.6 W/(m?K) and 0.8 W/(m?K), respectively, which may be compared with corresponding expected bulk values of about 30 W/(m?K), and about 20 W/(m?K)[4]. This is similar to previously reported values for dense alumina[5]. The above studies were focused on the thermal resistance of only coating layer. A sealing of the coating via PEO process appears absolutely necessary to enable long term exposure in aggressive environment[6]. The synthesis of oxides in a low-temperature electrolytic plasma allows to cover the surface of magnesium and its alloys with multifunctional oxide-ceramic coatings in the same manner as aluminum alloys shown previously[7]. Using diffusion coating method, there were trial to improve corrosion resistance of AZ91D alloy[8-9]. For 2024 aluminum alloy, MA et al[10-11] studied relationship between anodic film and the boric acid-containing mixed electrolyte. Also, for corrosion behavior of 2024-T3 aluminum alloy, there were results of influence on NaCl solution containing HQS[10].
In the present study, plate heat exchanger was developed with aluminum material, the fundamental stage was performed to show whether it had reasonable feasibility or not. A nano ceramic coating technology was performed to aluminum specimens, and then the thermal conductivity, AASS and so on were tested and measured. Finally, referring those results, correlations between the coating properties and thermal properties was attempted to establish.
2 Experimental
2.1 Thermal conductivity measurements
The thermal conductivity was measured using the LFA 447 apparatus shown in Fig.1. It conforms to ASTM E 1461, a kind of standard test method for thermal diffusivity by the flash methods. In this method, the front side of a plane-parallel sample was heated by a short light pulse.
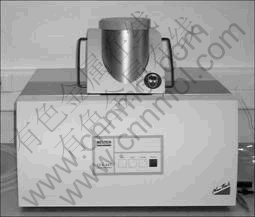
Fig.1 Thermal conductivity test equipment (LFA447)
The resulting temperature on the rear surface was measured using an infrared detector. By analysis of the resulting temperature versus time curve, the thermal diffusivity can be determined. By measuring thermal diffusivity (α) of a material, its thermal conductivity (λ) can be determined if specific heat (cp) and density (ρ) are known:
λ(T)=α(T)cp(T)ρ(T) (1)
The specimens for thermal conductivity measurement were the plates with 8 mm in width, 8 mm in height and 2 mm in thickness. For the sake of convenience, the samples were named as follows: “K00” without coating, “K20” with 20 μm coating layer and “K40” with 40 μm coating layer. The thermal conductivity of each specimen were measured and the results are as follows: 153.39 W/(m?K) in “K00”, 150.69 W/(m?K) in “K20” and 149.76 W/(m?K) in “K40”. The thermal conductivities exhibit the slight decrease with the increase of coating’s thickness.
2.2 AASS test result
To estimate the corrosion resistance of coating layer, AASS test conforming to Korean standard—KS D 9502 was made. Also it conforms to ISO 9227. The acetic acid salt spray (AASS) test is a kind of generally well-known methods to examine anodized coating layer on aluminum. The specimens with 150 mm×100 mm×20 mm in dimension in 168 h (1 week) was examined. And test conditions were as follows: test solvent is (5±1)% sodium chloride(pH 6.8±0.3), test temperature is (35±2) ℃, spray quantity is (2.5±0.5) mL/(h?m2).
The morphologies of specimens are shown in Figs.2-4 as rating number of KS D 9502. The several pits and vast range stain occur on the specimen surface without coating, but little pits and stain occur on “K20” and “K40”.
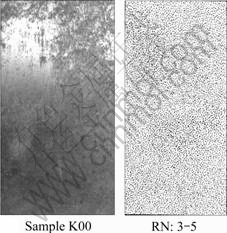
Fig.2 AASS test result for K00
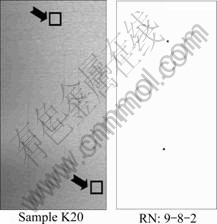
Fig.3 AASS test result for K20
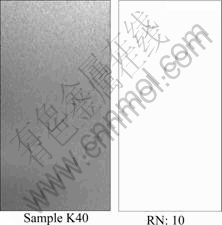
Fig.4 AASS test result for K40
2.3 Hardness measurements
To estimate the coating layer hardness, micro Vickers hardness tester, FM 700 was used. The Vickers hardness denotes to a value from a test load, applied to a specimen to form an indentation on it with a square-based pyramidal diamond indenter which has face angle of 136?. The surface area of the permanent indentation can be obtained from its diagonal length using the following equation.
HV=0.102F/S=0.189 1 F/d2 (2)
where HV is Vickers hardness; F is test load, N; S is surface area of an indentation, mm2; D is average diagonal length of an indent, mm.
3 Results and discussion
In present study, above 3 tests and measurements were accomplished to reveal the correlation between corrosion resistance and heat transfer performance for aluminum plate heat exchanger.
Firstly, according to the thermal conductivity measurements results, “K20” and “K40” show a downward tendency to decrease than “K00”. However, if the value of “K00” is fixed as 100% to compare, the values converted to percentage have 98.23% in the case of “K20”, 97.63% in the case of “K40”. Moreover, these values mean that the thermal conductivity drop is much slight. The thickness of coating layer is only a few 1% of thickness of overall samples, therefore it cannot affect the thermal conductivity. Moreover, the each sample has two coating layers-tops and bottom sides. It means that “K20” and “K40” have the real thickness of over 2 mm. And it shows that the coating layer scarcely results in degradation thermal conductivity.
Secondly, the suitable rating numbers 3.5 in the case of “K00”, 2.0-9.8 in the case of “K20” and 10 in the case of “K40” can be obtained from the photographs of salt spray tests as shown in Figs.4-5. Also they are converted to percentage values. The values and figures mean that there are the distinct contrasts among “K00” and “K20”, ”K40”.
Lastly, the Vickers hardness values were converted into percentages and they are as follows: 87.9(100%) in the case of “K00”, 259.7(295.44%) in the case of “K20” and 344.8(392.26%) in the case of “K40”. The Vickers hardness values were measured at 3 points on the same line and these values show that “K40” are improved three or four times than “K00”.
The correlations between samples from above results are shown in Fig.5 and Table 1.
Table 1 Conversion values of test results
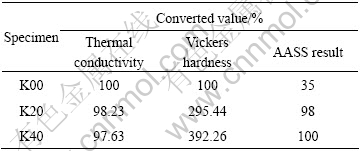
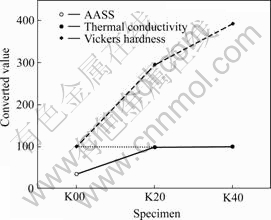
Fig.5 Correlation graph of converted results
According to above results, it can be concluded that, to produce the aluminum plate heat exchangers with enhanced corrosion resistance properties on salt water environments, the surface with minimum 20 μm over coating layer must be treated. The coating layer up to 40 μm has less influence on the thermal conductivity properties.
Hereafter, the various corrosion resistance tests on the samples with various coating layer thickness will be studied.
4 Conclusions
1) The coating layer thickness has little influence on thermal conductivity.
2) The Vickers hardness is furtherly dependent on coating thickness.
3) According to the AASS result, it can be predicted that the applied surface treatment has possibility to enhance the corrosion resistance, but the additional test with longer test time must be made.
4) Based upon this study, to apply this surface treatment technology to aluminum plate heat exchangers, several issues must be considered. Actual heat exchangers are greatly influenced by plate thickness although plate material has excellent thermal property, and its influence may be proportional to the number of stacked plates. Consequently, the optimum plate thickness without minimum thermal effect must be designed. Likewise, after assembly, the structural strength with inter-plate can operate at the maximum operating pressure of (25-30)×105 Pa and it must be carefully considered whether aluminum is able to be manufactured easily.
References
[1] CHUN W G, KANG S H. A study of the application of plate type heat exchanges for OTEC plants[J]. Journal of Res Inst Ind Tech, 2000, 11: 47.
[2] KIM N S, YOON S M, SEO T B, KIM C B. Effect of polymer additives on drag reduction for a plate type heat exchanger in OTEC applications[J]. Sol Energy, 1999, 19(2): 37-44.
[3] WOOD J K. Erosion-corrosion interactions and their effect on marine and offshore materials[J]. Wear, 2006, 261(9): 1012-1023.
[4] CURRAN J A, CLYNE T W. The thermal conductivity of plasma electrolyte oxide coatings on aluminium and magnesium[J]. Surface and Coatings Technology, 2005, 199(2/3): 177-183.
[5] CURRAN J A, CLYNE T W. Thermo-physical properties of plasma electrolyte oxide coatings on aluminium[J]. Surface and Coatings Technology, 2005, 199(2/3): 168-176.
[6] BLAWERT C, HEITMANN V, DIETZEL W, NYKYFORCHYN H M, KLAPKIV M D. Influence of electrolyte on corrosion properties of plasma electrolytic conversion coated magnesium alloys[J]. Surface and Coatings Technology, 2007, 201(21): 8709-8714.
[7] KLAPKIV M D, NYKYFORCHYN H M, POSUVAILO V M. Properties of synthesized oxide-ceramic coatings in electrolyte plasma on aluminium alloys[J]. Surface and Coatings Technology, 1998, 100/101: 21-22.
[8] HUO Hong-wei, LI Ying, WANG Fu-hui. Improvement on the corrosion resistance of AZ91D magnesium alloy by aluminum diffusion coating[J]. Journal of Material Science and Technology, 2007, 25(2): 225-229.
[9] WANG L, SUNDEN B, MANGLIK R M. Plate heat exchangers: Design, applications and performance[M]. WIT Press, 2007: 23-24.
[10] MA Song-jiang, LUO Peng, ZHOU Hai-hui, FU Chao-peng, KUANG Ya-fei. Preparation of anodic films on 2024 aluminum alloy in boric acid-containing mixed electrolyte[J]. Trans Nonferrous Met Soc China, 2008, 18(4): 825-830.
[11] LI Song-mei, ZHANG Hong-rui, LIU Jian-hua. Corrosion behavior of aluminum alloy 2024-T3 by 8-hydroxy-quinoline and its derivative in 3.5% chloride solution[J]. Trans Nonferrous Met Soc China, 2007, 17(2): 318-325.
Corresponding author: In-Kwan KIM; Tel: +82-51-6297548; E-mail: inkwan@pknu.ac.kr
(Edited by CHEN Can-hua)